
910
.pdfОбзор литературных источников, анализ приведенных показателей формирует понимание об реальных условиях в процессе пуска ДВС и на этой основе руководство при их эксплуатации.
Ключевые слова: аграрный сектор, техническое обеспечение, двигатель внутреннего сгорания, пусковые качества.
Высокопроизводительную работу аграрного сектора страны во многом обеспечивает современного техническое обеспечение, основанное на инновационных научных разработках [3-5]. Одним из приоритетных направлений в этом аспекте является автотракторная техника основным источником энергии, которой в настоящее время являются поршневые двигатели внутреннего сгорания (ДВС) [1]. Важнейшим показателем функционирования ДВС являются его пусковые качества. Это комплекс свойств мотора, агрегатов, а также устройств, от которых напрямую зависит пуск ДВС, дающих возможность привести мотор в действие.
Основные параметры, с помощью которых оценивают пусковые качества ДВС, представляют собой [2]:
а) значение предельной температуры, гарантирующей надёжный пуск; б) временной период подготовки мотора к принятию нагрузки.
Предельная температура надёжного пуска - это значение наиболее низкой температуры - окружающего воздуха, при которой выполняется пуск ДВС с приемлемыми отклонениями от величины температуры окружающего воздуха: 1°С для температуры узлов, а также деталей мотора, в том числе охлаждающей жидкости и моторного масла; 2°С для применяемого электролита аккумуляторных батарей, но не ниже «-36°С».
Надёжный пуск ДВС – пуск мотора, снаряженного комплектом навесных агрегатов на основном виде горючего с применением штатных АБ (со степенью заряженности 75%) с числом попыток пуска холодного двигателя не более чем 3, а также горячего двигателя не более чем 2 и двигателя предпускового подогрева.
Длительность одной попытки 10 секунд для карбюраторного мотора и 15 секунд для дизельного с промежутком между попытками в 60 секунд. Холодный ДВС – мотор при значении температуры его деталей, а также охлаждающей жидкости, в том числе топлива и масла, отличающейся от величины температуры окружающей воздушной среды не более чем на 1°С. Горячий ДВС - остановленный после функционирования при значении температуры окружающего воздуха до +45°С, а также величине температуры деталей мотора, включая охлаждающую жидкость и масло не ниже рабочей.
nmin – значение минимальных пусковых оборотов; Wmin – значение минимальной угловой скорости.
nmin – наименьшее значение для реальной температуры средней частоты вращения коленчатого вала мотора с помощью стартера, при которой совершается пуск ДВС за 2 попытки (11-15 сек, 60 секунд перерыв).
Действительные пусковые характеристики при среднем значении частоты вращения коленчатого вала ДВС
В случае применения системы специального предпускового подогрева, продолжительность подогрева электролита аккумуляторной батареи по времени не учитывается.
31

Тестирование пусковых качеств выполняется при запуске в производство новых, а также модернизированных ДВС, узлов и приборов моторов и транспортных средств, влияющих на процесс пуска, в том числе серийной продукции с частотой не менее одного раза за три года.
Рисунок. Зависимость времени попытки пуска от частоты вращения коленчатого вала ДВС при различных температурах окружающего воздуха и количественном значении попытки
Точки перегиба на рисунке демонстрируют оптимум процесса запуска. Продолжительность по времени подготовки мотора к принятию рабочей
нагрузки – это суммарное время для приведения в рабочее состояние и функционирование устройства для достижения легкого пуска холодного, а также горячего ДВС, применяемой системы предпускового подогрева; собственно пуск, в том числе продолжительность по времени на пуск двигателя, включая его работу на холостом ходу (х.х.) до достижения состояния применения рабочей нагрузки, т.е. до момента, когда допустимо начало движения транспортного средства.
Процесс надёжного пуска горячего ДВС должен быть обеспечен:
- для моторов транспортных средств общего, в том числе многоцелевого назначения, включая северного варианта исполнения при значении температуры окружающего воздуха не ниже -41°С. - для моторов транспортных средств тропического варианта исполнения не ниже +46 °С при затратах времени на подготовку к выполнению нагрузки не более 3,5 минут.
Таблица 1 Требования к бензиновым моторам по пусковым качествам
Тип двигателя |
Дизель с каме- |
Дизель с камерой в |
Дизель с разделен- |
||||
|
|
ными камерами |
|||||
|
|
рой в поршне |
поршне, ε≥15 |
||||
|
|
ε≥21 |
|||||
|
|
|
|
|
|
||
tmin, °C |
|
- 12 |
- 30 |
- 20 |
-25 |
- 20 |
|
v, мм2 /c |
|
4010 |
6010 |
4010 |
6010 |
5000 |
|
Топливо |
|
зимнее, температура замерзания – 35,5 % |
|
||||
Время, необходимое |
|
|
|
|
|
||
для подготовки мо- |
|
|
|
|
|
||
тора к выполнению |
8 |
10 |
8 |
10 |
10 |
||
рабочей |
нагрузки, |
||||||
|
|
|
|
|
|||
не более минут |
|
|
|
|
|
||
|
|
|
|
32 |
|
|
Таблица 2 Значение предельной температуры надежного запуска мотора после выполнения предпускового подогрева и времени подготовки ДВС к осуществлению рабочей
нагрузки
Назначение |
транс- |
Общее, северное и мно- |
Многоцелевое |
Северный вари- |
||||
портного средства |
гоцелевое назначение |
назначение |
ант исполнения |
|||||
tmin,не более, °C |
|
- 46 |
|
-50 |
-60 |
|||
Сорт масла,мм2 /c -вяз- |
зимнее, класс «8» |
маловязкое загущенное |
||||||
кость |
|
|
4з/6 |
|
4з/8 |
|
5з/8 |
|
|
|
|
|
|
||||
Сорт |
трансмиссион- |
зимнее |
|
|
арктическое |
|||
ного масла |
|
|
|
|||||
|
|
|
|
|
|
|
||
Сорт топлива |
|
бензин, сильное арктическое дизельное топливо |
||||||
Продолжительность |
36 |
|
30 |
45 |
||||
подготовки |
|
|
||||||
|
|
|
|
|
|
|
Требования к бензиновым моторам по пусковым качествам, а также значения предельных температур надежного запуска мотора после выполнения предпускового подогрева и времени подготовки ДВС к осуществлению рабочей нагрузки сведены в таблицу 1 и 2. Анализ приведенных показателей, а также весь представленный материал формирует понимание об реальных условиях в процессе пуска ДВС и на этой основе руководствоваться при их эксплуатации.
Литература
1.Аносова, А.И., Хороших О.Н., Шуханов С.Н. Методика определения безотказности и поиска неисправностей при диагностировании технических средств // Известия Оренбургского государственного аграрного университета. 2021. № 6 (92). С. 181-183.
2.Суркин, В.И. Основы теории и расчёта автотракторных двигателей. СПб: Лань, 2013. -
304 с.
3.Ivanyo Ya., Bendik N., Asalkhanov P. Big data in solving applied problems of agricultural producers and procurers of wild food resources // В сборнике: 2020 International Multi-Conference on Industrial Engineering and Modern Technologies, FarEastCon 2020. 2020. С. 9271362.
4.Kokieva G., Voinash S., Sokolova V., Nuretdinov D., Alekseeva S., Taraban M., Zatenko S. Evaluation and prediction of machine performance in low-volume reduced works // В сборнике: AIP Conference Proceedings. Krasnoyarsk Scientific Centre of the Siberian Branch of the Russian Academy of Sciences. Melville, New York, United States of America, 2021. С. 30004.
5.Medyakov, A.A., Lastochkin D.M., Kamenskih A.D., Anisimov P.N., Ostashenkov A.P. Study of the biogas plant with catalytic heating // В сборнике: IOP Conference Series: Earth and Environmental Science. Krasnoyarsk Science and Technology City Hall of the Russian Union of Scientific and Engineering. Krasnoyarsk, 2021. С. 52060.
УДК 502.36
Е.С. Лопатина – студентка; О. С. Сергеева – научный руководитель, доцент,
ФГБОУ ВО Пермский ГАТУ, г. Пермь, Россия
ЭКОЛОГИЧЕСКАЯ БЕЗОПАСНОСТЬ. ВЫБОР СИСТЕМЫ ОЧИСТКИ ДЛЯ КУЗНЕЧНОГО ЦЕХА
Аннотация. События по охране окружающей среды, прочерчиваемые в кузнечном изготовлении, формируются его особенностью: цехи данного изготовления принадлежат к предметам, оказывающим интенсивное воздействие в находящуюся вокруг среду. В этой статье рассматривается вопрос загрязнения атмосферы такими газами, как углекислый и диоксид серы.
33

Ключевые слова: углекислый газ, диоксид серы, система очистки, загрязнение, адсорбция, абсорбция.
Проблема – Загрязнение атмосферы участка такими газами как SO2 и CO2. Большая концентрация CO2 в воздухе вызывает заражение организма, а так же такую опасную болезнь как гиперкапния (рвота, сильные боли в голове, затруд-
ненное дыхание, обмороки). При длительном воздействии углекислого газа на человека, наступает кислородное голодание, эта болезнь – гипоксия. В атмосфере CO2 оказывает, довольно, значительное влияние на ее состояние: вызывает экстремальные погодные явления, такие как смертельные перепады температуры; увеличивается ареал обитания таких насекомых как москиты и клещи, они в свою очередь являются переносчиками смертельных болезней.
Вдыхание человеком таких паров газов как диоксид серы оказывает много побочных эффектов: появляется кашель, мокрота, хрипота, боль в полости рта и горла. При случайном попадании вещества высокой концентрации на слизистые могут быть вызвано: удушье и трудности с глотанием, случаются расстройства речи, сильная долговременная рвота и отеки легких. Кислород в воздухе вступает в реакцию с помощью света, что приводит к окислению сернистого газа до получения ангидрида серы. Аэрозоль серной кислоты в атмосфере, раствор в дождевых водах приводит к подкислению почвы, а также сжиганию зеленной массы расте-
ний. [1]
Методы очистки воздуха от примесей газов: механические (центробеж-
ная, водой и мокрая очистка); химические (каталитические, сорбционные); физикохимические (абсорбционные, адсорбционные).
Для решения данной проблемы были более подробно изучены и проанализированы такие способы очистки как абсорбция и адсорбция. Абсорбция – промывка загрязняющих примесей жидкими растворами (абсорбентами). Адсорбция – присоединение примесей фильтрами.
Адсорбция
Рисунок 1. Адсорберы
34

Загрязнённый воздух поступает в адсорбер, проходят через фильтр, в котором примеси притягиваются к наполнителю в фильтре. Наружу выходит уже ранее обработанный от примесей воздух. В этом методе используются различные фильтры. (Рис. 1) Например, фильтры наполняют такими материалами как цеолиты, алюмогель, силикагель (кремний). Но самым распространенным материалом является активированный уголь (он на много дешевле). Фильтры на основе угля представляют собой мелкие гранулы. Чем меньше гранулы, тем больше площадь поглощения газа. Но угольный порошок слипается, образовывается в камень – это понижает эффективность работы системы. Поэтому важно, чтобы размеры гранул имели оптимальный объем. В нашем случае не подходят угольные фильтры, так как они не очищаю воздух от углекислого газа, а использование других материалов для фильтров значительно удорожают систему. Фильтры требуется менять или правильно утилизировать.
Преимущества и недостатки адсорбционного метода
+Высокая степень очистки
+Отсутствие жидкостей
+Газы не охлаждаются
+Процесс по очистке может работать непрерывно
-Разрешено очищать только сухие и не загрязненные пылью газы
-Низкая скорость работы системы по очистке газов [2]
Абсорбционный метод. Скруббер – аппарат, где газ и жидкость подаются под давлением.
Рисунок 2. Скруббер-абсорбер: 1 – насадка; 2 – разбрызгиватель
Абсорбент поступает сверху через разбрызгиватели. Газ подается снизу и, проходя через водяной поток, очищается. Из скруббера выходит уже очищенный газ. Сточная жидкость вытекает снизу из скруббера через слив. (Рис. 2).
Для SO2 и для CO2 абсорбентом может являться обычная техническая вода, ведь обе примиси растворяются в воде (это на много упрощает и удешевляет систему по очищению воздуха) (рис. 3).
35

Рисунок 3. Абсорбенты
Преимущества и недостатки абсорбционного метода
+не дорогой способ по очистке воздуха в больших колличествах
+процесс по очистке может работать непрерывно
+универсальность (очищение и газовых примесей и пыли)
+эффективность
-технологические схемы сложны, многоступенчаты и очистные реакторы имеют большие объемы;
-громоздкость аппаратурного оформления;
-сильное понижение температуры воздуха, что влияет на снижение эффективности рассеивания газов в атмосфере;
-много жидких отходов (проблема транспортировки или утилизации шлама). [3]
Выводы
После проведенного анализа, склоняюсь к такому способу очистки как абсорбция. Методика очистки не сложная. Очищает сразу и пылевые и газовые примеси. Возможна непрерывная работа очистительной системы. (рис. 4)
Рисунок 4. Схема по очистке газов: 1 — скруббер; 2 — форсунка; 3 — каплеуловитель; 4, 9 — фильтры; 5 — гидроциклон; 6 — вакуум-фильтр; 7 — насос;
8 — циркуляционный сборник; 10 — гидрозатвор
36
Литература
1.Бадагуев, Б.Т. Экологическая безопасность предприятия. Приказы, акты, инструкции, журналы, положения, планы. 2-е изд., пер. и доп. / Б.Т. Бадагуев. — М.: Альфа-Пресс, 2018. — 568 c.
2.Калыгин, В.Г. Экологическая безопасность в техносфере. Термины и определения / В.Г. Калыгин. — М.: КолосС, 2018. — 368 c
3.Саркисов, О.Р. Экологическая безопасность и эколого-правовые проблемы в области загрязнения окружающей среды: Учебное пособие для студентов вузов, обучающихся по специальности «Юриспруденция» / О.Р. Саркисов. — М.: ЮНИТИ-ДАНА, 2017. — 231 c.
УДК 631.171
Д.Ю. Лычин, И.А. Кривенко–магистранты 2 курса; Н.В. Трутнев – научный руководитель, доцент, ФГБОУ ВО Пермский ГАТУ, г. Пермь, Россия
МЕТОДИКА ИССЛЕДОВАНИЯ СПИРАЛЬНО-ВИНТОВОГО ДОЗАТОРА
ВРЕЖИМЕ СМЕШИВАНИЯ
ИДОЗИРОВАНИЯ КОМПОНЕНТОВ КОМБИКОРМОВ
Аннотация. В сельском хозяйстве качественное и равномерное дозирование является важным аспектом в кормлении животного. В статье было рассмотрено, как диаметр и шаг спирали влияют на точность смешивания и раздачи сухих кормов.
Ключевые слова: спирально-винтовой дозатор, корм, дозатор-смеситель, бункер, спираль.
Включение в рацион крупного рогатого скота комбикормов дает возможность обогатить его всеми необходимыми компонентами для нормального роста животных и высоких удоев. Полнорационные составы содержат сбалансированный комплекс питательных веществ, витаминов, минералов и ферментов, подобранных
сучетом возраста и породы [4].
Внастоящий момент применяемые дозаторы-смесители на фермах крупного рогатого скота имеют ряд существенных недостатков:
Дороговизна;
Плохая однородность смешивания;
Сложность конструкции;
Большая металлоемкость [1].
На основании вышеизложенного следует вывод, что разработка смесителядозатора для смешивания и выдачи сыпучих кормов, обеспечивающего эффективное использование комбикормов, нормальное развитие и рост продуктивности дойных коров, в данный момент времени является актуальной задачей и требует изучения на основе результатов научных исследований.
За основу для изучения процесса смешивания и дозирования сухих кормов был взят спирально-винтовой дозатор, разработанный в ПГАТУ. В процессе исследования он был доработан путем разделения загрузочного бункера на 2 части, его схема изображена на рисунке 1. Основу спирально-винтового смесителя дозатора составляют сменная спираль и кожух, спираль крепится на выходном валу моторредуктора при помощи муфты [2].
37
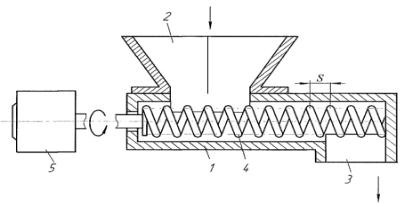
Процесс дозирования протекает следующим образом: загрузочный бункер 2 разделен на две части. Под действием силы тяжести поступает в цилиндрический корпус 1, где под действием вращающейся спирали 4, приводимой во вращение приводом 5 с регулируемой частотой вращения, смешивается и транспортируется к выгрузному окну 3. Привод спирали осуществляется от моторедуктора постоянного тока [3].
Рисунок 1. Конструктивно-технологическая схема экспериментального дозатора
Основным технологическим параметром любого типа раздатчиков является подача (производительность). У спирально-винтового дозатора подача находится в прямой зависимости от межвиткового объема рабочего органа – спирали и ее частоты вращения. В ходе теоретических исследований установлено, что на межвитковой объем спирали влияют: диаметр и шаг спирали, зазор между спиралью и кожухом, коэффициент заполнения, насыпная плотность корма и коэффициент уплотнения. Коэффициент уплотнения является фактором, который невозможно контролировать. В зависимости от вида продукта и динамических характеристик он будет различным.
|
|
|
|
|
|
|
|
|
Таблица |
|
|
|
|
Результаты эксперимента |
|
|
|
||||
|
D, |
ша |
ча- |
|
Об |
масса |
ма |
|
сред- |
|
|
Вр |
степень |
ний % |
|||||||
№ |
спи- |
г |
стота |
щая |
комби- |
сса |
||||
емя, |
однород- |
одно- |
||||||||
опыта |
рали, |
витк |
вра- |
масс |
корма, |
зерн |
||||
с. |
ности, % |
родно- |
||||||||
|
мм. |
а |
щения |
а, кг. |
кг. |
а, кг. |
||||
|
|
|
сти |
|||||||
|
|
|
|
|
|
|
|
|
||
1 |
96 |
1,25 |
41-45 |
10 |
3,3 |
1,98 |
1,32 |
80 |
81,53 |
|
|
96 |
1,25 |
41-45 |
10 |
3,29 |
1,95 |
1,34 |
81,5 |
|
|
|
96 |
1,25 |
41-45 |
10 |
3,3 |
1,93 |
1,37 |
83,03 |
|
|
|
96 |
1,25 |
41-45 |
10 |
3,22 |
1,31 |
1,91 |
81,4 |
|
|
|
96 |
1,25 |
41-45 |
10 |
3,33 |
1,36 |
1,97 |
81,7 |
|
|
2 |
96 |
1,00 |
41-45 |
10 |
3,02 |
1,79 |
1,23 |
81,5 |
81,38 |
|
|
96 |
1,00 |
41-45 |
10 |
2,95 |
1,19 |
1,76 |
80,7 |
|
|
|
96 |
1,00 |
41-45 |
10 |
2,96 |
1,25 |
1,71 |
84,5 |
|
|
|
96 |
1,00 |
41-45 |
10 |
2,99 |
1,78 |
1,21 |
80,9 |
|
|
|
96 |
1,00 |
41-45 |
10 |
3 |
1,19 |
1,81 |
79,3 |
|
|
3 |
96 |
0,75 |
41-45 |
10 |
2,3 |
1,39 |
0,91 |
79,1 |
81,6 |
|
|
96 |
0,75 |
41-45 |
10 |
2,31 |
1,37 |
0,94 |
81,4 |
|
|
|
96 |
0,75 |
41-45 |
10 |
2,36 |
1,37 |
0,99 |
83,9 |
|
|
|
96 |
0,75 |
41-45 |
10 |
2,35 |
0,97 |
1,38 |
82,5 |
|
|
|
96 |
0,75 |
41-45 |
10 |
2,27 |
0,92 |
1,35 |
81,1 |
|
38

Продолжение таблицы
4 |
73 |
1,25 |
41-45 |
10 |
1,22 |
0,64 |
0,58 |
95,1 |
98,02 |
|
73 |
1,25 |
41-45 |
10 |
1,41 |
0,71 |
0,7 |
99,3 |
|
|
73 |
1,25 |
41-45 |
10 |
1,36 |
0,66 |
0,7 |
97,1 |
|
|
73 |
1,25 |
41-45 |
10 |
1,39 |
0,7 |
0,69 |
99,3 |
|
|
73 |
1,25 |
41-45 |
10 |
1,39 |
0,69 |
0,7 |
99,3 |
|
5 |
73 |
1,00 |
41-45 |
10 |
1,12 |
0,58 |
0,54 |
96,4 |
97,9 |
|
73 |
1,00 |
41-45 |
10 |
1,16 |
0,6 |
0,56 |
96,6 |
|
|
73 |
1,00 |
41-45 |
10 |
1,1 |
0,56 |
0,58 |
98,2 |
|
|
73 |
1,00 |
41-45 |
10 |
1,23 |
0,62 |
0,61 |
99,2 |
|
|
73 |
1,00 |
41-45 |
10 |
1,17 |
0,58 |
0,59 |
99,1 |
|
6 |
73 |
0,75 |
41-45 |
10 |
0,91 |
0,46 |
0,45 |
98,9 |
98,08 |
|
73 |
0,75 |
41-45 |
10 |
0,9 |
0,46 |
0,44 |
97,8 |
|
|
73 |
0,75 |
41-45 |
10 |
0,95 |
0,49 |
0,46 |
96,8 |
|
|
73 |
0,75 |
41-45 |
10 |
0,97 |
0,48 |
0,49 |
99 |
|
|
73 |
0,75 |
41-45 |
10 |
0,94 |
0,46 |
0,48 |
97,9 |
|
7 |
49 |
1,25 |
41-45 |
10 |
0,5 |
0,31 |
0,19 |
76 |
77,96 |
|
49 |
1,25 |
41-45 |
10 |
0,46 |
0,29 |
0,17 |
73,9 |
|
|
49 |
1,25 |
41-45 |
10 |
0,48 |
0,2 |
0,28 |
83,3 |
|
|
49 |
1,25 |
41-45 |
10 |
0,47 |
0,18 |
0,29 |
76,6 |
|
|
49 |
1,25 |
41-45 |
10 |
0,45 |
0,18 |
0,27 |
80 |
|
8 |
49 |
1,00 |
41-45 |
10 |
0,38 |
0,23 |
0,15 |
78,9 |
78,16 |
|
49 |
1,00 |
41-45 |
10 |
0,4 |
0,24 |
0,16 |
80 |
|
|
49 |
1,00 |
41-45 |
10 |
0,4 |
0,15 |
0,25 |
75 |
|
|
49 |
1,00 |
41-45 |
10 |
0,4 |
0,24 |
0,16 |
80 |
|
|
49 |
1,00 |
41-45 |
10 |
0,39 |
0,15 |
0,24 |
76,9 |
|
9 |
49 |
0,75 |
41-45 |
10 |
0,33 |
0,2 |
0,13 |
78,8 |
78,22 |
|
49 |
0,75 |
41-45 |
10 |
0,3 |
0,18 |
0,12 |
80 |
|
|
49 |
0,75 |
41-45 |
10 |
0,34 |
0,21 |
0,13 |
76,5 |
|
|
49 |
0,75 |
41-45 |
10 |
0,28 |
0,17 |
0,11 |
75,8 |
|
|
49 |
0,75 |
41-45 |
10 |
0,3 |
0,18 |
0,12 |
80 |
|
На основе методики экспериментальных исследований настоящей работы, ставилась задача изучить влияние независимых факторов на массу материала в межвитковом пространстве спирали (коэффициент уплотнения).
Исследования проводились на двух видах корма – гранулированном и пшеница, после чего данные опытов заносили в регистрационный журнал, обработанные данные сведены в таблицу.
Степень однородности:
= ⁄0,5 ,
где mmin- масса меньшего по массе корма, кг; М – общая масса корма, кг.
Средний процент однородности:
ср = ( 1+ 2+ 3+ 4+ 5) , 5
(1.1)
(1.2)
На основании опытных данных и компьютерных программ STATGRAPHICS Plus и Mathcad получены уравнения регрессии и построены поверхности отклика изменения подачи материала спирально-винтовым дозатором в зависимости от конструктивных параметров (рисунок 2).
39
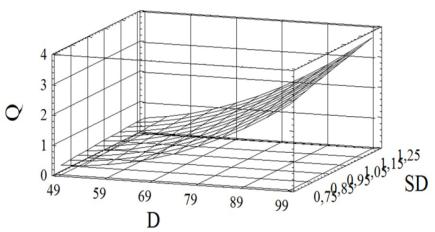
Рисунок 2 – Поверхности откликов, характеризующие подачу кг/мин гранулированного комбикорма и пшеницы от конструктивных параметров: а – диаметра спирали D,
мм и при шаге спирали SD
Уравнение регрессии массовой подачи рассыпного корма:
Q = 3,00474 - 0,1138*D - 0,340979*SD + 0,000966048*D^2 +0,0274894*D*SD - 0,32*SD^2
Анализ поверхностей откликов рисунка 2 показывает, что подача кормораздатчика имеет прямолинейную зависимость от шага спирали s, а также, следует, что при увеличении диаметра спирали от 49 мм до 97 мм подача увеличивается в параболической зависимости.
При проведении опытов замечено, что при наибольшем зазоре b = 7,5 мм гранулированный и рассыпной концентрированный корм перемещается в полное поперечное сечение цилиндрического кожуха, следовательно, объем межвиткового пространства заполнен материалом на 100%.
Можно сделать вывод, что в ходе приведения опытов были рассмотрены спирали диаметром 96, 73, 49 мм шагами витка 1,25; 1 и 0,75. Оптимальным дозирующим органом является спираль диаметром 73 мм, так как степень однородности составляет 98%, а у других не достигает даже 82 %.
Литература
1.Глобин, А.Н., Краснов И.Н. Г54 Дозаторы: монография / А.Н. Глобин, И.Н. Краснов. – Зерноград: ФГБОУ ВПО АЧГАА, 2012. – 348 с.
2.Лялин, Е.А. Обоснование основных конструктивнотехнологических параметров спи- рально-винтового дозатора комбикормов: 2019/ Лялин Евгений Александрович; - Пермь. -175с.
3.Лялин, Е.А. Лабораторная установка для исследования рабочего процесса спиральновинтового дозатора гранулированных и рассыпных кормов / Лялин Е.А., Коньшин С.В., // Молодежная наука 2014: технологии, инновации, Всероссийская науч.-практическая конф. (2014; Пермь).
–2014. с.24-25.
4.Фролов, В.Ю. Машины и технологии в молочном животноводстве: учебное пособие / В.Ю. Фролов, Д.П. Сысоев, С.М. Сидоренко. — 2-е изд., испр. — Санкт-Петербург: Лань, 2017. — 308 с. — ISBN 978-5-8114-2418-4. — Текст: электронный // Лань: электронно-библиотечная си-
стема. — URL: https://e.lanbook.com/book/91875 (дата обращения 16.03.2021).
40