
909
.pdf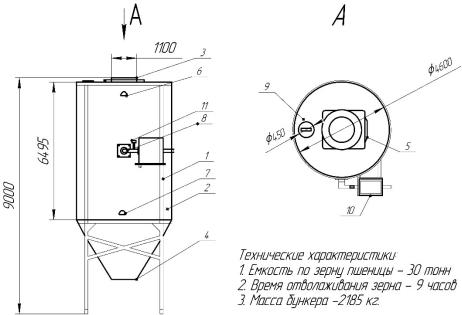
пульсатор давления 7 соединенный каналом 8 с внутренней полостью 9 корпуса 2. На корпусе размещены датчики максимального 10 и минимального 11 уровня зерна, предохранительный клапан 12. Вертикальный корпус закрыт герметичной крышкой 13.
Процесс отволаживания в бункере происходит следующим образом. Увлажненное зерно подается через горловину 3 в бункер отволаживания
зерна, состоящий из вертикального корпуса 2, с конической нижней частью 4 и выгрузной горловиной 5, размещенный на раме 1. Затем горловина 3 закрывается герметичной крышкой 13. Далее оператор включает в работу пульсатор давления 7, соединенный каналом 8 с внутренней полостью 9, который периодически создает давление в бункере и также его сбрасывает. В результате чего процесс отволаживания ускоряется. Если максимальное давление начинает превышать установленный предел срабатывает предохранительный клапан 12. По окончанию процесса отволаживания давление опускается до атмосферного, и сырье далее, через шлюзовый затвор 6 выводится из бункера. Количество сырья в корпусе 2 бункера контролируется датчиками максимального 10 и минимального 11 уровня.
На рисунке 2 представлена предлагаемая конструкция бункера для отволаживания зерна.
Рис. 2. Предлагаемая конструкция бункера для отволаживания зерна
Сократить срок отволаживания зерна, при этом сохранить его качество и необходимое количество влаги в зерне – одна из главных проблем любого мельничного производства. В данной работе предлагается сократить продолжительность отволаживания путем повышения давления внутри бункера. Частицы влаги на поверхности зерновки будут испытывать нагнетающее давление выше атмосфернного, вследствие чего будет происходить более интенсивное ее проникновение. Результатом послужит ускоренное ослабление связи между оболочкой и эндоспермом.
При этом действии вода создает напряженное состояние капилляров набухших оболочек, которому сопутствует концентрация местных напряжений на отдельных участках, а также заполнению влагой микротрещин. Все это в сово-
241
купности облегчает отделение оболочек с минимальными потерями эндосперма. Для достижения данной цели предлагается использовать пневматический пульсатор давления, применяемый в горном деле.
Конструкция предлагаемого бункера для отволаживания зерна наиболее удачна, так как смотровое отверстие, находящееся в середине конструкции возможно использовать для подачи сжатого воздуха, установленный в трубопроводе регулятор давления будет выводить данные на компьютер в диспетчерской.
Выводы. В результате внедрения предлагаемой конструкции бункера для отволаживания зерна в процессе его гидротермической обработки, а именно создания избыточного давления в бункере, интенсивность проникновения влаги в зерновку резко возрастет, что позволит сократить время отволаживания. С этой целью мы включили в технологическую схему бункер, с установленным в его конструкцию пневматическим пульсатором давления. Данная техническая сущность положительно повлияет на объемы производства линии переработки зерна в муку.
Литература
1.Кайшев, В.Г. Состояние и развитие продовольственного комплекса России // Пищевая промышленность. - 2016. - №3. – С. 6-19.
2.Гордеев, А.В. Россия - зерновая держава / А.В. Гордеев, В.А. Бутковский. - М.: Пищепромиздат, 2003. - 508 с
3.Бутковский, В.А. Технология зерноперерабатывающих производств: учебник/ В.А. Бутковский, Л.И Мерко. - М.: Интеграф сервис, 1999 – 472 с.
4.Бузоверов, С.Ю. Технология и оборудование элеваторной промышленности: учебное пособие / С.Ю. Бузоверов, В.И. Лобанов. – Барнаул: РИО АГАУ, 2013. – 85с.
5.Пат. №174380. Бункер для отволаживания зерна / Российская Федерация МПК В65D
88/00 (2006.01) / Бузоверов С.Ю., Балабов А.А., Лобанов В.И.; заявитель и патентообладатель Балабов А.А. - № 2017112559; заявл. 12.04.2017; опубл. 11.10.2017, Бюл. №29.
6.Бузоверов, С.Ю. Разработка устройства для увлажнения и отволаживания зерна пшеницы // Вестник Алтайского государственного аграрного университета. – 2019. - № 2(172). – С.
161-167.
УДК 631.362
В.Д. Галкин, А.Д. Галкин, В.А. Хандриков, К.А. Грубов, А.Ф. Федосеев, ФГБОУ ВО Пермский ГАТУ, г. Пермь, Россия
Е-mail: engineer@pgsha.ru
АНАЛИЗ ДВИЖЕНИЯ СЕМЯН ПО ПЕРФОРИРОВАННОЙ ПОВЕРХНОСТИ ПОД ДЕЙСТВИЕМ ВИБРАЦИИ И ВОЗДУШНОГО ПОТОКА,
И ОЦЕНКА ИХ РАЗДЕЛЕНИЯ ПО КОМПЛЕКСУ СВОЙСТВ
Аннотация. Исследования проведены на кафедре сельскохозяйственных машин и оборудования. Целью работы является повышение удельной производительности и снижение энергоемкости процесса очистки семян в вибропневмоожиженном слое. Выявлены закономерности изменения средней скорости движения семян по деке в зависимости от режима ее работы и скорости воздушного потока. Опытами установлено, что использование усовершенствованной машины с декой площадью 0,27 м2, при очистке семян пшеницы от овсюга, по сравнению с
машинами производительностью до 1,5 т/ч, позволяет увеличить удельную
242
нагрузку и снизить удельные энергозатраты при требуемом качестве очистки и допустимых потерях семян в отходы.
Ключевые слова: семена, очистка, вибропневмоожиженный слой.
Постановка проблемы. В нашей стране для очистки семян по комплексу их свойств разработаны, использовались и применяются в настоящее время пневматические сортировальные столы [1,2], технические характеристики которых приведены в таблице 1.
Таблица 1
Технические характеристики отечественных пневмосортировальных столов
|
Производитель- |
Установ- |
|
Удельные энер- |
Удельная |
||
Модель ма- |
Масса, |
гоемкость, |
|||||
ность, т/ч (на пше- |
ленная |
металло- |
|||||
кВт.ч/т/ |
|||||||
шины |
нице)/ |
|
мощность, |
кг |
емкость, |
||
|
производитель- |
||||||
|
площадь деки, м |
2 |
кВт |
|
кг.ч/т |
||
|
|
|
ность, т/ч* м2 |
||||
ПСС-1 |
1,0/0,46 |
|
3.75 |
500 |
3,75/2,17 |
500 |
|
ССП-1,5 |
1,5/1,8 |
|
7,1 |
750 |
4,75/0,83 |
500 |
|
БПС-3 |
3,0/2,0 |
|
5,5 |
740 |
1,83/1,5 |
246,7 |
|
ПСС-2,5 |
2,5/1,08 |
|
6,6 |
650 |
2,64/2,3 |
260 |
|
СПС-5 |
5,0/1,56 |
|
11,75 |
837 |
2,35/3,2 |
167,4 |
|
МОС-9 |
6,0/2,05 |
|
16,1 |
990 |
2,68/2,92 |
165 |
Из таблицы 1 следует, что при производительности столов от 1,0 до 6,0 т/ч, их удельная нагрузка на деку изменяется в пределах 0,83…3,20 т/ч*м2 , а удельная энергоемкость - 1,83…4,75 кВт.ч/т. Машины компании «Westrup» (Дания) при
производительности от 1,5 до 18т/ч, имеют удельную нагрузку на деку 2,63…3,53 т/ч*м2 , а удельная энергоемкость этих столов составляет 1,79…5,50 кВт.ч/т, причем для машины производительностью 1,5 т/ч этот показатель - 5,50 кВт.ч/т [1].
Отечественные и зарубежные машины, разделяющие компоненты зерновой смеси по комплексу свойств семян, являются достаточно сложными в настройке и имеют высокую металлоемкость. Поэтому, повышение удельной производительности, снижение удельной металлоемкости и энергоемкости машин, упрощение их настройки на заданные условия работы при требуемом качестве очистки семян и допустимых их потерях в отходы, является важной и актуальной задачей, решение которой позволит снизить эксплуатационные затраты на использование пневмосортировальных столов в составе поточных линий.
Методы проведения исследований. При исследовании движения семян по поверхности использовали методы классической механики. Показатели качества очистки определяли экспериментальны путем.
Результаты теоретических исследований. Для увеличения удельной производительности, а, следовательно, снижения удельной энергоемкости, необходимо повысить среднюю скорость перемещения материала по деке. Для ее определения рассмотрим силы, действующие на материал, движущийся по деке.
На частицу, находящуюся на колеблющейся, перфорированной деке, имеющей продольный угол наклона (Рис. 1 и 2), действуют: сила веса G=m·g; сила инерции U=j·m; сила трения F=N·tg ; сила N, действующая перпендикулярно деке; сила воздушного потока Pв, направленная вдоль силы инерции. Дифференциальные урав-
243
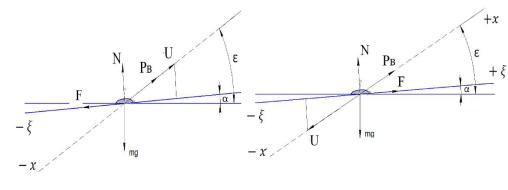
нения, составленные для правого и левого интервалов будут иметь вид:
Рис.1.Силы, действующие на ча- |
Рис.2. Силы, действующие на |
стицу, находящуюся на перфорирован- |
частицу, находящуюся на перфориро- |
ной деке (правый интервал) |
ванной деке (левый интервал) |
|
∙ |
2 вв |
= U ∙ − − ∙ |
|
|
− |
( ) |
+ ∙ − |
|
||||||||||||||||||||||||
|
где: |
m2 |
мас |
; |
|
( |
− |
ускорение) |
; |
|
( |
|
)сила инерции( ) |
; |
в |
|
|
( |
|
|
) |
||||||||||||
|
|
|
|
|
− |
|
|
|
|
|
|
|
|
|
|
U − |
|
|
|
|
|
|
− |
|
|
|
|
|
|||||
|
|
|
|
|
|
|
|
|
|
2 вв |
|
|
|
- продольный угол наклона деки; |
|
|
|||||||||||||||||
угол |
направленности |
|
2 |
|
|
|
− |
||||||||||||||||||||||||||
|
|
|
|
|
|
|
|
|
|
колебаний; |
|
|
|
|
|
|
|
|
|
|
|
|
|
|
|
|
|||||||
угол трения материала о поверхность деки. |
|
|
+ |
|
∙ |
|
|
|
|
|
|
||||||||||||||||||||||
|
|
|
∙ |
( − − ) |
= ∙ ( ) − ∙ ( − − ) |
|
|
, |
|
|
|
|
|||||||||||||||||||||
|
2 вв |
|
|
|
|
|
|
|
|
|
|
|
|
|
|
|
|
|
(+) |
|
|
|
|
|
|
|
|
|
|||||
|
После преобразований уравнения (1), получим: |
|
|
|
|
2 |
|
|
|
|
|
||||||||||||||||||||||
|
|
|
|
п |
|
|
|
|
|
|
|
2 |
|
|
|
|
|
|
|
|
|
|
|
|
|
|
|
|
|
|
|
||
|
∙ |
|
|
= ∙ ( ) − U ∙ ( − ) |
+ ∙ ( + ) − ∙ |
||||||||||||||||||||||||||||
|
|
2 |
|
||||||||||||||||||||||||||||||
|
|
|
|
|
|||||||||||||||||||||||||||||
|
|
вн |
|
|
( ) |
|
|
|
|
|
|
|
|
|
|
|
|
|
|
|
|
|
|
потока. |
|||||||||
|
где2: |
|
|
|
- |
коэффициент парусности; Vв – скорость воздушногоп |
|||||||||||||||||||||||||||
|
|
|
∙ ( − + ) = ∙ ( ) − ∙ ( − + ) − |
∙ |
|
|
|
|
|
|
|||||||||||||||||||||||
|
2 вн |
|
|
|
|
( ) |
|
|
|
|
|
|
|
|
|
|
|
( −) |
|
|
|
|
|
|
|
|
|
|
|||||
|
После |
2преобразований, уравнение (3) приметв |
вид: |
|
|
|
2 |
|
|
|
|
|
|||||||||||||||||||||
|
|
|
|
|
|
|
|
|
|
|
|
|
2 |
|
|
|
|
|
|
cos( − + ) , |
|
|
п |
|
|
|
|
|
|
||||
|
Обозначив2 |
: |
|
|
|
|
|
|
|
|
= |
|
|
|
|
|
|
|
|
||||||||||||||
|
|
|
|
|
|
|
|
|
|
cos( ) , |
|
|
|
|
|
|
|
|
|||||||||||||||
|
|
|
|
|
|
|
|
|
|
|
|
|
|
|
= |
cos( − − ) |
|
|
|
|
|
|
|
|
|
|
|
||||||
|
|
|
|
|
|
|
2 |
|
|
(4) |
с учетом |
|
|
cos( ) |
|
|
+ п |
∙ , |
|
|
|
|
|
||||||||||
|
|
|
|
|
|
|
∙ = ∙ cos( ) − ∙ cos( − − ) |
|
|
|
|
|
|||||||||||||||||||||
|
|
|
|
|
|
|
2 вв |
1 |
|
|
|
|
|
|
|
|
|
|
sin( + ) |
|
|
|
|
|
|
|
|
|
|
||||
|
уравнения (2) и |
|
|
2 |
|
обозначений (5) и (6) примут вид : |
|
|
|||||||||||||||||||||||||
|
|
|
|
|
|
|
2 |
|
|
|
|
|
|
|
|
|
|
|
|
|
|
|
|
|
2 |
|
|
|
|
|
|||
|
|
|
|
|
|
|
∙ = ∙ cos( ) − ∙ cos( − + ) − п ∙ . |
|
|
|
|
|
|||||||||||||||||||||
|
|
|
|
|
|
|
2 вн |
1 |
|
|
|
2 |
|
|
|
|
|
|
|
sin(− ) |
|
|
|
2 |
|
|
|
|
|
||||
|
|
|
|
|
|
|
|
|
|
|
|
|
|
|
|
|
|
|
|
|
|
|
|
|
|
|
|
|
|
|
(1)
(2)
(3)
(4)
(5)
(6)
(7)
(8)
Проинтегрировав дважды уравнения (7) и (8) и, получив уравнения для
перемещения частиц по деке, рассчитали средние скорости |
ср |
перемещения ма- |
|||||
териала по деке по выражению: |
вн+ вв , |
|
|||||
|
|
|
|
ср = |
|
(9) |
|
где |
вв |
и |
вн |
|
|
|
|
вверх и |
|
|
|
|
|
||
|
|
|
|
- величины перемещений частиц материала, соответственно, |
вниз за период колебаний .
244
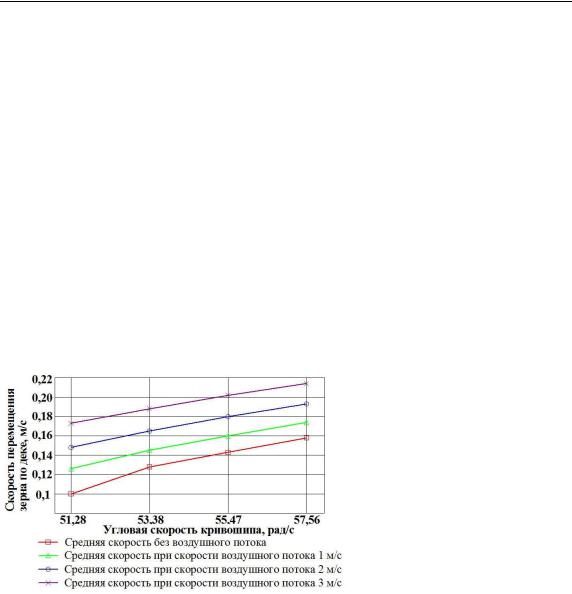
При этом использовали следующие параметры и режимы, обеспечивающие процесс движения материала по деке: угол наклона деки α=00 при угле направленности колебаний ε=300; углы трения частиц о поверхность: 1=350; 2=450; радиус кривошипа r=0,0075м при различных угловых скоростях; коэффициент парусности частиц kп=0,1м-1, скорости воздушных потоков Vв – 1,2,3 м/с, которые
приведены в таблице 2.
Таблица 2
Расчетные величины средней скорости перемещения сыпучего материала по деке
Vв,м/c |
Vср, м/c |
, м |
,м |
α0 |
ε0 |
10 |
20 |
ω, рад/с |
|
0 |
0,108489 |
0,001474вн |
0,011818вв |
|
|
|
|
|
|
1 |
0,126205 |
0,001454 |
0,014008 |
0 |
30 |
35 |
45 |
51,28 |
|
|
|
|
|
||||||
2 |
0,148078 |
0,001500 |
0,016641 |
||||||
|
|
|
|
|
|||||
|
|
|
|
|
|
|
|
|
|
3 |
0,172683 |
0,001599 |
0,019556 |
|
|
|
|
|
|
|
|
|
|
|
|
|
|
|
|
0 |
0,127568 |
0,001682 |
0,013333 |
|
|
|
|
|
|
|
|
|
|
|
|
|
|
|
|
1 |
0,144882 |
0,001653 |
0,015400 |
0 |
30 |
35 |
45 |
53,38 |
|
|
|
|
|
||||||
2 |
0,165428 |
0,001674 |
0,017798 |
||||||
|
|
|
|
|
|||||
|
|
|
|
|
|
|
|
|
|
3 |
0,188484 |
0,001737 |
0,020449 |
|
|
|
|
|
|
|
|
|
|
|
|
|
|
|
|
0 |
0,143695 |
0,001835 |
0,014441 |
|
|
|
|
|
|
|
|
|
|
|
|
|
|
|
|
1 |
0,160464 |
0,001793 |
0,016382 |
0 |
30 |
35 |
45 |
55,47 |
|
|
|
|
|
||||||
2 |
0,180144 |
0,001793 |
0,018611 |
||||||
|
|
|
|
|
|||||
|
|
|
|
|
|
|
|
|
|
3 |
0,201751 |
0,00182 |
0,021031 |
|
|
|
|
|
|
|
|
|
|
|
|
|
|
|
|
0 |
0,157718 |
0,001943 |
0,015271 |
|
|
|
|
|
|
|
|
|
|
|
|
|
|
|
|
1 |
0,174404 |
0,001895 |
0,01714 |
0 |
30 |
35 |
45 |
57,56 |
|
|
|
|
|
||||||
2 |
0,193547 |
0,001878 |
0,019247 |
||||||
|
|
|
|
|
|||||
|
|
|
|
|
|
|
|
|
|
3 |
0,214253 |
0,001879 |
0,021506 |
|
|
|
|
|
|
|
|
|
|
|
|
|
|
|
По расчетным данным построены графические зависимости (Рис.3).
Рис.3. Закономерности
изменения скорости перемещения зерна по деке, в зависимости от режима ее работы и скорости наклонного воздушного потока
Результаты экспериментальных исследований. На кафедре сельскохо-
зяйственных машин и оборудования ФГБОУ ВО Пермский ГАТУ изготовлен экспериментальный вибропневмосепаратор семян [3]. При настроечном значении подачи 1,2 т/ч семян пшеницы, засоренной овсюгом, при поперечном угле наклона 0о, амплитуде колебаний – 0,015 м достигнута степень выделения примесей не менее 98% при потерях семян в отходы не превышающих 10%. При площади деки
245
0,27 м2, удельная производительность сепаратора превысила 4,4 т/ч*м2, а удель-
ная энергоемкость составила 3,1 кВт.ч/т.
Вывод. Выявлены закономерности изменения средней скорости движения семян по деке в зависимости от режима ее работы и скорости наклонного воздушного потока. Опытами установлено, что использование усовершенствованной машины с декой площадью 0,27 м2, при очистке семян пшеницы от овсюга, по
сравнению с машинами производительностью до 1,5 т/ч, позволяет увеличить удельную нагрузку и снизить удельные энергозатраты при требуемом качестве очистки и допустимых потерях семян в отходы.
Литература 1.Технологические основы применения пневматических сортировальных столов в сель-
ском хозяйстве/ В.М. Дринча, С.А. Павлов, В.Д. Бабченко и др.-М: Росельхозакадемия, 2003.- 98с.
2.Галкин, А.Д. Машины и оборудования послеуборочной обработки зерна и подготовки семян из влажного комбайнового вороха: рекомендации./ А.Д. Галкин, В.Д. Галкин. МСХ РФ, Пермский ГАТУ. Пермь: ИПЦ «Прокростъ».2020.-47 с.
3.Пат. РФ № 190119. Вибропневмосепаратор /В.Д.Галкин, А.Д.Галкин, В.А. Хандриков, А.Ф. Федосеев, М.С. Накаряков. Опубл. 14.06.2019. Бюл. №17.
УДК 621.869
В.А. Елтышев, Ю.А. Барыкин,
ФГБОУ ВО Пермский ГАТУ, г. Пермь, Россия e-mail: detali@pgsha.ru
ОПРЕДЕЛЕНИЕ МОЩНОСТИ ПРИВОДА ФРЕЗ БУРОРЫХЛИТЕЛЬНОЙ МАШИНЫ БРМ-80/110 ПРИ ПРЕДЕЛЬНОМ ИЗНОСЕ
РЕЖУЩЕГО ИНСТРУМЕНТА
Аннотация. Статья посвящена расчету мощности привода фрез бурорыхлительной машины БРМ-80/110 с рациональным сочетанием значений геометри-
ческих параметров режущего инструмента фрез при установленном предельном износе резца по высоте.
Ключевые слова: мощность, бурорыхлительная машина, многорезцовая
фреза, добавочная сила сопротивления резанию, производительность.
Мощность привода многорезцовых рабочих органов является одним из важнейших технико-экономических показателей технологического оборудования. Бурорыхлительная машина БРМ-80/110 [5] оснащена двумя электродвигателями,
которые приводят во вращение многорезцовые фрезы. Каждый электродвигатель приводит во вращение две фрезы. Суммарная мощность, которая расходуется на разрыхление смерзшегося дисперсного материала, рассчитывается на основании баланса мощности
P P1 P2 P3 P4 P5 , |
(1) |
где |
P |
1 |
фрезами, кВт;
мощность, затрачиваемая на резание мерзлого материала двумя
P2 мощность, затрачиваемая на преодоление добавочных сил сопротив-
ления резанию, которые действуют на площадки износа резцов, кВт;
246

P3
мощность, затрачиваемая на преодоление трения разрыхленного мерз-
лого материала о стенку выработки, кВт;
P4 P5
мощность, затрачиваемая на подъем разрыхленного материала, кВт; мощность, затрачиваемая на преодоление трения разрыхленного ма-
териала о винтовую поверхность фрезы, кВт.
В проведенных исследованиях [2] при ограничении по мощности для одно-
го резца
Pc.1
1,5
кВт, получено рациональное сочетание значений геометриче-
ских параметров режущего инструмента фрез: угол резания α = 70º, задний угол β
= 40º, а также значение предельного износа резца по высоте
h |
|
i |
|
3,8 мм. Этим
параметрам соответствуют значение силы сопротивления резанию на режущей
кромке Fс.р 340 Н
на площадку износа
и
Fс.р'
добавочной силы сопротивления резанию, действующей
260 Н.
Составляющие мощности рассчитываем при следующих исходных данных
[4, 5]:
80/110
мощность
P |
55 |
э.д |
|
электродвигателей базовой бурорыхлительной машины БРМ-
кВт;
производительность одной фрезы при резании и транспортировании мерзлого материала Q = 40…45 т/ч;
средняя скорость резания |
v |
р |
|
2,5 м/с; |
|
|
|
|
|
||||||
|
|
|
|
|
|
|
|||||||||
число резцов на |
одной |
фрезе одновременно участвующих в резании |
|||||||||||||
смерзшегося материала |
Z |
р |
|
11; |
|
|
|
|
|
|
|
|
|
|
|
|
|
|
|
|
|
|
|
|
|
|
|
|
|||
высота подъема Н = 2,4 м; |
|
|
= 680 мм; |
|
|
|
|
|
|||||||
диаметр фрезы по резцам |
D |
р |
|
|
|
|
|
||||||||
|
|
|
|
|
|
|
|
|
|
|
|
|
|
||
диаметр фрезы по виткам D = 580 мм; |
|
|
|
|
|
|
|||||||||
диаметр вала фрезы d = 260 мм; |
|
|
|
|
|
|
|
||||||||
шаг винтовой поверхности t = 500 мм; |
|
|
|
|
|
||||||||||
|
|
|
|
|
|
|
|
|
|
т/м |
|
|
|
|
|
объемный вес каменного угля ρ = 1,1 |
|
3 |
; |
|
|
|
|||||||||
|
|
|
|
|
|||||||||||
коэффициент трения материала о сталь f = 0,5; |
|
|
|
||||||||||||
коэффициент трения разрыхленного материала о стенку скважины |
f |
1 |
|
||||||||||||
|
|
||||||||||||||
0,8; |
|
|
|
|
|
|
|
|
|
|
|
|
|
|
|
коэффициент заполнения ψ = 0,3; |
|
|
|
|
|
|
угол трения материала о сталь φ = 26 30'.
Угол подъема винтовой поверхности фрезы по наружной кромке [1, 3]
|
|
tgα |
|
|
|
1 |
|
||
tgα1 |
|
500 |
|
|
3,14 580 |
||||
|
|
π
t |
, |
|
|
||
D |
0,274, α1 15,3 .
(2)
Угол подъема винтовой поверхности фрезы по внутренней кромке (по ва-
лу) [1, 3]
247
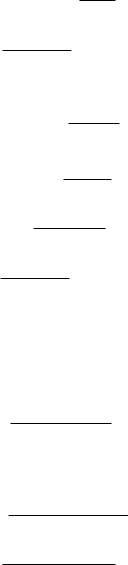
tg α |
0 |
|
|
tgα |
0 |
|
|
|
|
|
||
|
500 |
|
|
|
3,14 260 |
||||
|
t π d ,
0,612
,
α |
0 |
|
31,5
.
(3)
Угол подъема винтовой поверхности фрезы по среднему диаметру [1, 3]
tgα |
|
|
t |
, |
|
ср |
π D |
||||
|
|
||||
|
|
|
|
||
|
|
|
ср |
|
D |
|
D d |
|
, |
|||
ср |
|
||
|
|
2 |
Dср 580 260 420 мм; 2
(4)
(5)
tgαср
|
500 |
||
3,14 |
420 |
||
|
0,379
,
αср
20,7
.
Мощность, затрачиваемая на резание мерзлого материала двумя фрезами, рассчитывается [1, 3]
P1 |
2 |
Fс.р vр Zp |
|
|
|
|
, |
(6) |
|
|
1000 |
|||
|
|
|
|
P1
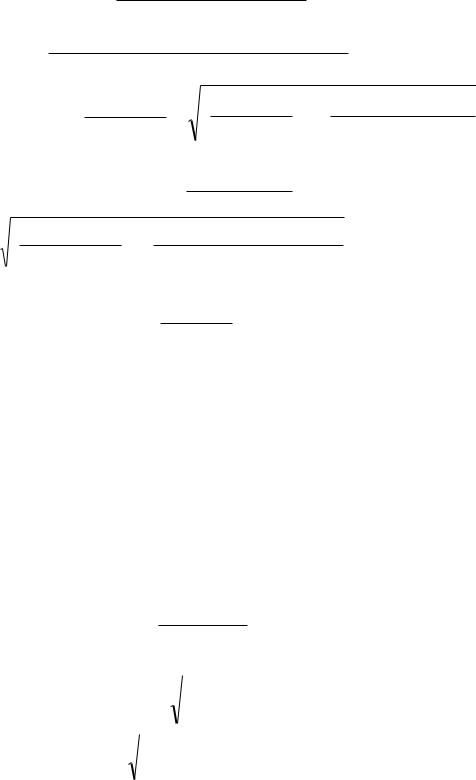
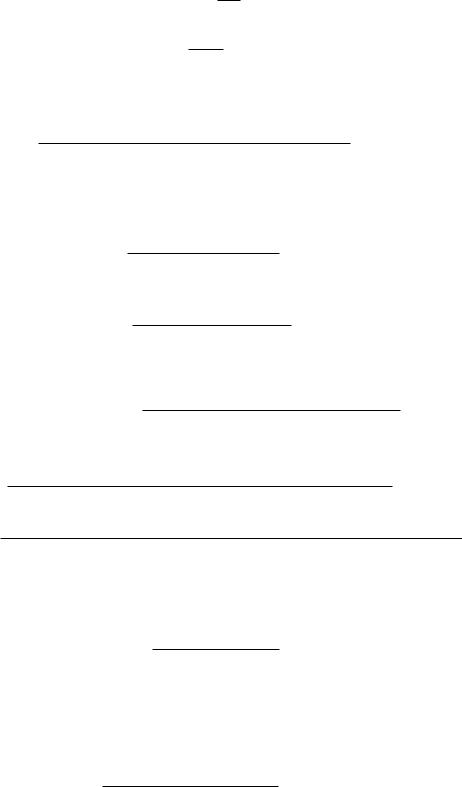