
- •Система разработки продукции
- •THE TOYOTA
- •Содержание
- •Предисловие Джима Вумека
- •Благодарности
- •Предисловие авторов
- •Введение
- •Революция в разработке новой продукции
- •Новый рубеж конкурентной борьбы: система разработки продукции
- •Совершенство разработок — важнейшая составляющая потенциала компании
- •Бережливая система разработки продукции: объединить усилия функциональных подразделений и поставщиков
- •Учиться у Toyota
- •Модель бережливой системы разработки продукции
- •Социотехническая система
- •Подсистема «Процесс»: принципы 1-4 LPDS
- •Подсистема «Люди»: принципы 5-10 LPDS
- •Подсистема «Инструменты и технология»: принципы 11-13 LPDS
- •Процесс определения ценности с точки зрения потребителя в North American Car Company
- •Процесс определения ценности с точки зрения потребителя в Toyota
- •Руководство проектом: роль главного инженера
- •Этапы создания ценности для потребителя
- •Конкретная ситуация: Команда разработчиков кузова Lexus уменьшает допустимый предел погрешности вдвое
- •Почему этот принцип стал первым?
- •Правильный старт как фабрика идей: разработка разных продуктов на основе единой платформы
- •Производные модели на основе существующих платформ
- •Долгосрочное технологическое планирование
- •Правильный старт при реализации отдельных проектов: внешний вид автомобиля и техническая осуществимость
- •Параллельное проектирование на базе альтернатив
- •Применение кенто к разработке кузова и каркаса Toyota
- •Пример того, как стандартизация производственных операций обеспечивает быстрое решение проблем
- •Унифицированная компоновка и использование единых комплектующих
- •Анализ базовых целей создания автомобиля и принятие решений
- •Технология производства в Toyota: обязанности инженера по параллельному проектированию
- •Инженеры по параллельному проектированию должны обеспечить достижение плановых показателей по инвестициям и переменным издержкам
- •Мидзен боси и посещение производственных предприятий
- •Обмен информацией со специалистами функциональных групп
- •Инженер по параллельному проектированию представляет план
- •Использование средств автоматизированного проектирования
- •Раннее решение проблем на этапе кенто: конкретная ситуация
- •Кодзокейкаку (К4) — соединить части в единое целое
- •Правильный человек, правильная работа, правильный момент
- •Обеспечить выровненный поток процесса разработки продукции
- •Потенциал потока
- •Разработка продукции как процесс
- •Составление карт потока создания ценности
- •Семь видов потерь в процессе разработки продукции
- •Три типа потерь реально существуют
- •Факторы, способствующие и препятствующие потоку: подход теории очередей
- •Выровненный поток вместо неразберихи: кенто и поток
- •Роль логики процесса
- •Использование общих платформ
- •Скользящий график запуска в производство
- •Завершение разработки продукции
- •Синхронизация работы внутри и между функциональными подразделениями
- •Примеры межфункциональной синхронизации
- •Обеспечение гибкости
- •Детальные (фундоси) графики работы функциональных подразделений
- •Обеспечение потока процесса при несерийном производстве
- •Определение ритма проектно-конструкторских работ и сокращение времени управленческого цикла
- •Вытягивание информации в системе разработки продукции
- •Объединение операций в единый поток
- •Три вида стандартизации
- •Стандартизация конструкции и контрольные листки
- •Стандартизация процесса
- •Стандартизированный процесс организации производства в Toyota
- •Разработка штампов в Toyota
- •Разработка технологического процесса и фиксаторов
- •Производство инструмента и штампов в Toyota
- •Типовые сроки производства штампов и инструментов
- •Станочная обработка штампов в Toyota
- •Сборка штампов в Toyota
- •Разработка технологии сборки автомобиля в Toyota
- •Стандартизация профессиональных знаний и навыков
- •Заключение
- •Развивать систему главных инженеров для интеграции всего процесса разработки
- •Культурная составляющая системы главных инженеров
- •История двух главных инженеров: проекты Lexus и Prius
- •Lexus: главный инженер, который не идет на компромиссы
- •Главный инженер — лидер
- •Руководство разработкой продукции в NAC: от главного инженера к бюрократу
- •Организация групповой работы в Chrysler
- •Система главных инженеров Toyota:
- •избегать компромиссов, порождающих бюрократию
- •Какая структура лучше?
- •Недостатки продуктовой структуры
- •Достоинства и недостатки матричной структуры при управлении процессом разработки продукции
- •Реорганизация матричной структуры Toyota
- •Структура проектных команд Chrysler: сравнение с центрами разработки автомобилей
- •Параллельное проектирование: обея
- •Параллельное проектирование: команды разработки модулей и главные инженеры по организации производства
- •Команды разработки модулей: кузов и организация производства
- •Организационная структура как развивающееся явление
- •Наем, развитие и сохранение персонала
- •Процесс подбора и найма персонала в NAC
- •Процесс отбора и найма в отделе разработки продукции NAC
- •Процесс найма в отделе организации производства NAC
- •Обучение и развитие в NAC
- •Развитие людей в Toyota
- •Наем в Toyota
- •Обучение и развитие в Toyota
- •Обучение и развитие в отделе разработки кузова
- •Обучение и развитие в отделе организации производства
- •Генти генбуцу в процессе разработки
- •Демонтаж продукции конкурентов
- •Сборка опытного образца
- •Ежедневные совещания на сборочном участке
- •Система бережливой разработки продукции должна обеспечивать развитие людей
- •Сделать поставщиков составной частью системы разработки продукции
- •Деталь — не деталь, а поставщик — не поставщик
- •Сила кейрецу
- •Равны ли поставщики между собой?
- •Отбор и развитие поставщиков до уровня партнера в Toyota: пример поставщика автопокрышек из США
- •Партнерские отношения с поставщиками: кому это выгодно?
- •Поставщики работают в тесном контакте с компанией-заказчиком: взаимовыгодные долгосрочные отношения
- •Цена — это не все
- •Упустить заказ
- •Развитие отношений
- •Система инженеров по приглашению
- •Состав группы поставщиков
- •Стратегия аутсорсинга
- •Совершенствование важнейших технологий
- •Освоение новых направлений: гибридный двигатель и средства автоматизированного управления
- •Привлечение аутсорсеров для изготовления аккумуляторных батарей
- •Изменить корпоративные принципы, чтобы сохранить внутренний потенциал
- •Обращаться с поставщиками корректно и разумно
- •Создать систему обучения и непрерывного совершенствования
- •Что такое знание и организационное обучение
- •Передача явного и неявного знания
- •Система обучения разработке продукции в Toyota
- •Обучение на собственном опыте
- •Хансей в Toyota
- •Идзивару — испытания в Toyota
- •Потенциал проблем
- •Решение проблем на месте
- •Цена невежества
- •Ускорить обучение, сократив продолжительность цикла
- •Сформировать культуру постоянного стремления к совершенству
- •Как культура может помешать бережливой разработке продукции
- •Инструмент не решает проблему
- •Приносить пользу потребителям и обществу
- •Высокий профессионализм и непревзойденное качество разработок — интегральная часть культуры
- •Дисциплина и трудовая этика
- •Кайдзен изо дня в день
- •Прежде всего потребитель
- •Стремление учиться, заложенное на генетическом уровне
- •Ответственность и обязательства
- •Организационное единство
- •Правильный процесс дает правильные результаты
- •Культура поддерживает процесс
- •Культура держится на лидерах
- •Адаптировать технологию к потребностям людей и процесса
- •Пять основных принципов отбора инструментов и технологий
- •Технология бережливой разработки продукции
- •Автоматизированное проектирование в Toyota
- •Технология проектирования в Toyota
- •Виртуальное производство и цифровая визуализация в NAC
- •Виртуальная сборка в Toyota
- •Анализ методом конечных элементов в NAC и в Toyota
- •Контрольные листки и инструменты стандартизации в Toyota и NAC
- •Создание трехмерных твердотельных моделей при разработке штампов в NAC и в Toyota
- •Станочная обработка штампов в Toyota и в NAC
- •Прессы для отладки штампов в NAC и в Toyota
- •Сборка без подгонки в NAC и функциональная сборка в Toyota
- •Освоить технологию, чтобы облегчить процесс
- •Концептуальный проект главного инженера как объединяющее начало
- •Межфункциональное взаимодействие посредством обея
- •Инструменты координации
- •Немаваси в Toyota
- •Система ринги в Toyota
- •Коммуникация и координация в Toyota
- •Использовать эффективные инструменты для стандартизации и организационного обучения
- •Как обучается ваша организация
- •База знаний в NAC:
- •поток создания ценности при разработке кузова
- •База данных по ноу-хау в Toyota
- •Инструменты оценки альтернативных решений и обмена информацией
- •Кривые компромиссных характеристик
- •Отчеты по бенчмаркингу конкурентов в NAC
- •Демонтаж автомобилей конкурентов в Toyota и аналитические таблицы
- •Инструменты стандартизации в Toyota: контрольные листки, матрицы качества, сендзу, стандартизированные карты процесса
- •Роль стандартизации и инструментов обучения
- •Целостная система: собираем по частям
- •Интеграция подсистем:
- •люди, процесс, инструменты и технология
- •Определение ценности:
- •создавать ценность с точки зрения потребителя
- •Поток создания ценности: устранение потерь и вариации
- •Устранить или изолировать вариацию
- •Обеспечение вытягивания и потока
- •Составление карт потока создания ценности при разработке продукции (PDVSM)
- •Особенности составления карт потока создания ценности при разработке продукции и на производстве
- •Практические семинары по PDVSM
- •Учитесь видеть разработку продукции как процесс
- •Преобразование культуры: суть бережливой разработки продукции
- •Воспитать внутреннего агента перемен
- •Приобретайте нужные знания
- •Механизмы интеграции (обея/проверки проекта)
- •Роль линейной структуры
- •Начните с потребителя
- •Осмыслите текущее состояние процесса бережливой разработки продукции
- •Подлинное преобразование культуры
- •Люди — ядро системы бережливой разработки продукции
- •Дорожная карта перехода к бережливой разработке продукции
- •Лидерство, обучение и непрерывное совершенствование как интегральная часть процесса
- •Глава 1
- •Глава 2
- •Глава 4
- •Глава 5
- •Глава 6
- •Глава 7
- •Глава 8
- •Глава 9
- •Глава 10
- •Глава 11
- •Глава 12
- •Глава 13
- •Глава 14
- •Глава 16
- •Глава 17
- •Предметный указатель
Конкретная ситуация: Команда разработчиков кузова Lexus уменьшает допустимый предел погрешности вдвое
История Lexus дает простой пример выстраивания иерархии ценности и процесса декомпозиции ценности. Ведущим принципом создания бренда Lexus было неустанное стремление к совершенству. Однако на первых порах данные обратной связи говорили о том, что среди машин класса «люкс» по требители явно предпочитают автомобили BMW и Mercedes, разработанные в Германии и отличающиеся безупречным качеством. Именно эти компании были основными конкурентами для Lexus. Чтобы выйти на новый уровень качества, отвечающий запросам потенциальных покупателей Lexus, коман да поставила цель снизить допустимый предел погрешности вдвое. Чтобы обеспечить достижение этой цели, группа разработки кузова должна была решить конкретную задачу — уменьшить зазоры между панелями кузо ва по отношению к действующему стандарту и вдвое снизить допустимое отклонение от величины зазора. В то время многие считали такой уровень точности изготовления деталей кузова недостижимым.
Команда Lexus понимала, что уменьшение зазоров благотворно скажется на аэродинамике автомобиля и значительно снизит шум при движении. Кроме того, это значительно улучшит внешний вид автомобиля и качество его исполнения, а именно эти параметры имеют решающее значение для вла дельцев машин класса «люкс». Перед командой разработки модулей, которая отвечала за узлы кузова (в частности, капот, двери и крышку багажника), стояла чрезвычайно сложная задача. Помимо уменьшения зазоров и сниже ния вариации, им следовало учитывать удобство открывания и закрывания. Межфункциональная команда первым делом внимательно изучила двери двух главных конкурентов. Члены команды выявили две проблемные зоны, которые видны на графике (рис. 3-1).
Проблемные зоны на графике соответствуют участкам двери, выделен ным на рис. 3-2. Поскольку именно эти зоны определяют различия между изделиями, команда занялась их исследованием.
Как показывает рис. 3-2, верхняя и нижняя секции двери имеют сопоста вимые вариации по зазорам. Максимальные различия между двумя дверьми выявлены на участке А, в зоне передней кромки двери, и на участке Е, в зоне задней кромки двери. В процессе производства периметр двери формируется завальцовкой края внешней панели двери, как показано на рис. 3-3.
Хотя на первый взгляд передние кромки дверей похожи, внимательное изучение позволило выявить несколько важных различий. Острый излом кромки двери Lexus в точке А мог привести к деформации данного участка при завальцовке и стать причиной вариации зазоров между панелями кузова.
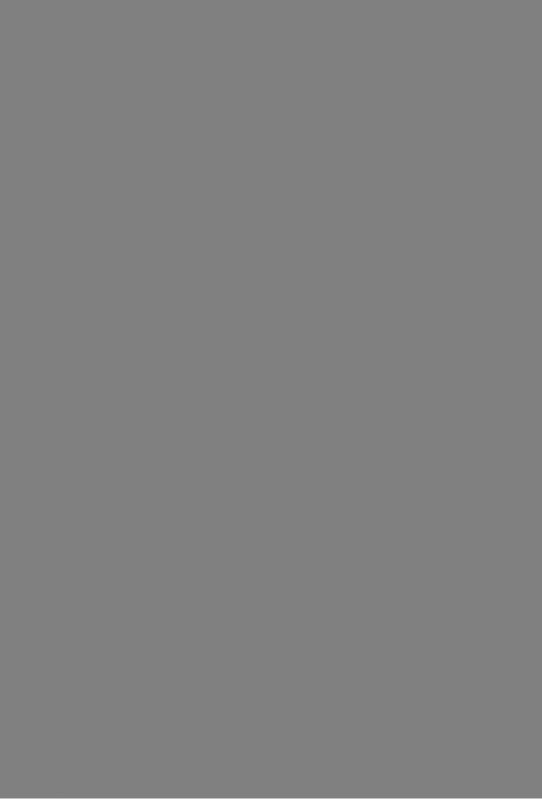
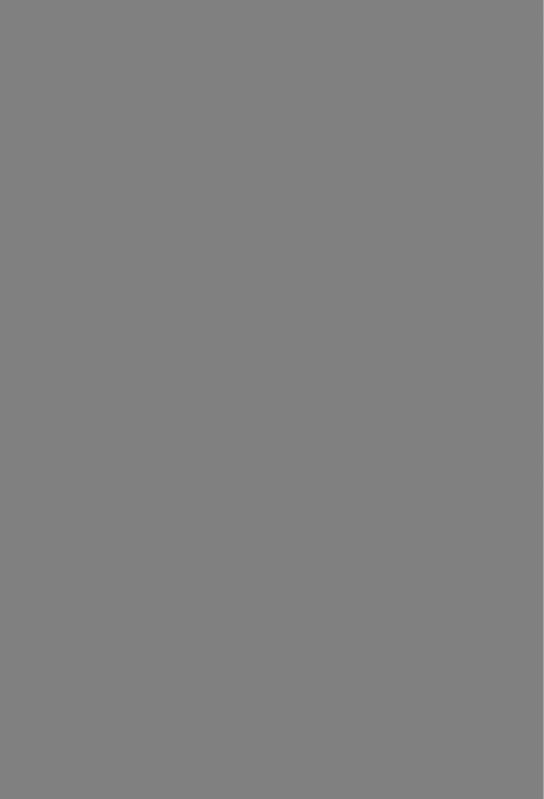
В автомобиле компании-конкурента боковая линия кузова уходила вверх и сливалась с точкой крепления зеркала, не пересекая кромку.
Те же самые факторы команда разработки модулей обнаружила, исследуя заднюю кромку двери: две боковые линии кузова упирались в завальцованный край, а кромка верхней секции двери имела острый излом. Собранная информация позволила команде изменить конструкцию и добиться умень шения зазоров между панелями кузова. Кроме того, команда обратила вни мание на миллиметровый скос кромки по контуру внутренней панели двери (участок Е). Члены команды пришли к выводу, что такая форма кромки повышает качество изготовления дверей, улучшает их прилегание и сни жает вариацию зазоров. На данном этапе было совсем не сложно внести в конструкцию подобное изменение.
Затем команда разработки модулей посетила производственное пред приятие, на котором осуществлялась завальцовка дверных панелей. По наблюдав за происходящим и побеседовав с операторами, разработчики внесли еще одно усовершенствование. Изменив условия выполнения операции и уменьшив ширину припуска наружных панелей, они доби лись более жесткого контроля процесса завальцовки, что позволило сни зить вариацию и уменьшить зазоры между панелями. В ходе дальнейших производственных испытаний команда определила оптимальный размер припуска и наилучшие условия выполнения операции, которые обеспечи вали максимальную эффективность соединения деталей и минимальный постоянный зазор.
Вариация припусков, равномерность зазоров и точность стыковки пане лей отслеживались на протяжении реализации проекта и внимательно прове рялись при поэтапной оценке проекта, а результаты всех проверок докумен тировались. Команда разработала систему измерения целевых показателей (зазор 4 мм и вариация), определила средства решения проблем (изменение конструкции, ширина припуска, условия, предшествующие завальцовке) и на протяжении всего проекта отслеживала результаты и принимаемые меры, вывешивая несложные графики там, где собиралась проектная команда. Отслеживая результаты и принимаемые меры, команда могла оперативно проверить, используются ли соответствующие методы и средства решения проблем и позволяют ли они улучшить результаты. Коллективно решая отдельные задачи добавления ценности для потребителя, команда сумела создать автомобиль класса «люкс», который превзошел стандарты своего времени. Наверняка многие читатели помнят рекламный ролик Lexus, де монстрирующий качественно новый уровень точности изготовления авто мобиля, — по кузову катится шариковый подшипник, беспрепятственно минуя стыки панелей.