
- •МЕХАНИКА МАШИН
- •1.1. Структура машинного агрегата
- •1.4. Управление движением машинного агрегата
- •СТРОЕНИЕ МЕХАНИЗМОВ
- •2.1. Основные определения
- •2.2. Кинематические пары и соединения
- •2.5. Структурный синтез механизмов
- •2.6. Классификация механизмов
- •КИНЕМАТИЧЕСКИЕ ХАРАКТЕРИСТИКИ МЕХАНИЗМОВ
- •3.1. Основные понятия
- •tgfa
- •3.6. Примеры графического исследования механизмов
- •pc = fivVB\ Р'Ь" = цайв', Ь"Ь'= цаагВ-
- •3.7. Кинематические характеристики плоских механизмов с высшими парами
- •3.8. Кинематические характеристики пространственных механизмов
- •3.9. Метод преобразования декартовых прямоугольных координат
- •4.1. Динамическая модель машинного агрегата
- •4.2. Приведение сил
- •4.3. Приведение масс
- •4.8. Неравномерность движения механизма
- •JTnp,
- •4.10. Динамический анализ и синтез с учетом влияния скорости на действующие силы
- •5.1. Динамическая модель машинного агрегата
- •5.2. Установившееся движение машинного агрегата
- •5.3. Исследование влияния упругости звеньев
- •СИЛОВОЙ РАСЧЕТ МЕХАНИЗМОВ
- •6.1. Основные положения
- •6.4. Силовой расчет механизма с учетом трения
- •6.5. Потери энергии на трение. Механический коэффициент полезного действия
- •ВИБРОАКТИВНОСТЬ И ВИБРОЗАЩИТА МАШИН
- •7.1. Источники колебаний и объекты виброзащиты
- •7.3. Анализ действия вибраций
- •7.6. Статическая и динамическая балансировка изготовленных роторов
- •Щ = у/g sina/<5CT,
- •7.8. Демпфирование колебаний. Диссипативные характеристики механических систем
- •7.9. Динамическое гашение колебаний
- •тт(р - рт) = mjyE.
- •7.11. Ударные гасители колебаний
- •7.12. Основные схемы активных виброзащитных систем
- •ТРЕНИЕ И ИЗНОС ЭЛЕМЕНТОВ КИНЕМАТИЧЕСКИХ ПАР МЕХАНИЗМОВ И МАШИН
- •8.1. Виды и характеристики внешнего трения
- •8.2. Основные понятия и определения, используемые в триботехнике
- •8.3. Механика контакта и основные закономерности изнашивания
- •8.4. Методика расчета износа элементов кинематических пар
- •МЕТОДЫ ПРОЕКТИРОВАНИЯ СХЕМ ОСНОВНЫХ ВИДОВ МЕХАНИЗМОВ
- •МЕТОДЫ СИНТЕЗА МЕХАНИЗМОВ С ВЫСШИМИ ПАРАМИ
- •9.1. Основные понятия и определения
- •9.2. Основная теорема зацепления
- •9.3. Скорость скольжения сопряженных профилей
- •9.4. Угол давления при передаче движения высшей парой
- •9.5. Графические методы синтеза сопряженных профилей
- •9.7. Производящие поверхности
- •МЕХАНИЗМЫ ПРИВОДОВ МАШИН
- •10.1. Основные понятия и определения
- •10.2. Строение и классификация зубчатых механизмов
- •10.4. Планетарные зубчатые механизмы
- •ЦИЛИНДРИЧЕСКАЯ ЗУБЧАТАЯ ПЕРЕДАЧА
- •11.2. Эвольвента, ее свойства и уравнение
- •11.3. Эвольвентное прямозубое колесо
- •11.4. Эвольвентная прямозубая рейка
- •11.5. Эвольвентное зацепление
- •11.8. Подрезание и заострение зуба
- •11.9. Эвольвентная зубчатая передача
- •11.10. Качественные показатели зубчатой передачи
- •11.11. Цилиндрическая передача, составленная из колес с косыми зубьями.
- •11.12. Особенности точечного круговинтового зацепления Новикова
- •ПРОСТРАНСТВЕННЫЕ ЗУБЧАТЫЕ ПЕРЕДАЧИ
- •12.1. Коническая зубчатая передача
- •МЕХАНИЗМЫ С НИЗШИМИ ПАРАМИ
- •13.1. Основные этапы синтеза
- •13.4. Синтез четырехзвенных механизмов по двум положениям звеньев
- •13.5. Синтез четырехзвенных механизмов по трем положениям звеньев
- •13.6. Синтез механизмов по средней скорости звена и по коэффициенту изменения средней скорости выходного звена
- •tijivu) < [tfj]-
- •КУЛАЧКОВЫЕ МЕХАНИЗМЫ
- •14.1. Виды кулачковых механизмов и их особенности
- •14.2. Закон перемещения толкателя и его выбор
- •sinx4
- •sinx2 = [(*2 “ Vj3)/f34]sm03;
- •14.5. Определение габаритных размеров кулачка по условию выпуклости профиля
- •14.6. Определение координат профиля дисковых кулачков
- •14.7. Механизмы с цилиндрическими кулачками
- •МЕХАНИЗМЫ С ПРЕРЫВИСТЫМ ДВИЖЕНИЕМ ВЫХОДНОГО ЗВЕНА
- •15.1. Зубчатые и храповые механизмы
- •15.2. Мальтийские механизмы
- •15.3. Рычажные механизмы с квазиостановками
- •УПРАВЛЕНИЕ ДВИЖЕНИЕМ СИСТЕМЫ МЕХАНИЗМОВ
- •16.2. Циклограмма системы механизмов
- •МАНИПУЛЯЦИОННЫЕ МЕХАНИЗМЫ
- •17.3. Задачи о положениях манипуляторов
- •17.4. Задачи уравновешивания и динамики
- •Glos
ПРОСТРАНСТВЕННЫЕ ЗУБЧАТЫЕ ПЕРЕДАЧИ
Во многих машинах осуществление требуемых движений механизмов связано с необходимостью передать вращение с одного вала на другой при условии, что оси этих валов либо пересекаются, либо скрещиваются. В таких условиях применяют соответственно или коническую, или гиперболоидную зубчатую передачу. Аксоидами колес первой являются конусы, аксоидами второй — однополостные гиперболоиды (см. § 9.1). Обе пере дачи относятся к категории пространственных механизмов. Изложению основ их синтеза (геометрического расчета) по заданному передаточному отношению посвящена данная глава.
12.1. Коническая зубчатая передача
Если угол между осями равен 90°, то коническую зубча тую передачу называют ортогональной. В общем случае в неортогональной передаче угол, дополненный до 180° к углу
между векторами угловых скоростей |
и й 2 звеньев |
1 и 2 , |
называют межосевым углом Е (рис. 12.1, а). |
|
|
Связь между векторами й\ и и 2 угловых скоростей 1 и 2 |
||
характеризуется соотношением |
|
|
W2=Wi+Wi2. |
|
(12-1) |
Положение вектора й>21 относительно векторов |
и и 2 |
|
определяется углами 6W\ и 6W2 , сумма которых равна межосе |
||
вому углу Е: |
|
|
5wl + $w2 — £. |
|
(1 2 .2 ) |
Если через точку О пересечения осей 0\0 и О2О провести вектор CJ21 , то он совпадет с мгновенной осью ОР относитель ного движения ведущего и ведомого звеньев и будет определять
конические поверхности аксоидов, называемых начальными ко нусами. При обозначении параметров, относящихся к началь ному конусу, используют индекс w. Углы 6W\ и 6W2 началь ных конусов вычисляют при решении векторного соотношения ( 1 2 .1) с использованием теоремы синусов (рис. 1 2 .1 , а):
sin $%])\ |
sin |
|
р2\ |
|wi| |
|
Отношение модулей угловых скоростей |tJi| и |а721 пред |
||
ставляет собой передаточное отношение: |
|
|
\ui\ |
sin 6W2 |
(12.3) |
U\2 —- ----- |
— --------- , |
|
|W2 | |
sin ^ i |
|
При заданных межосевом угле Е и передаточном отноше нии и\2 углы начальных конусов определяют, совместно решая
соотношения (12.2) и (12.3): |
|
|
u12 = |
sin ^„,2 |
sin(E -^ «,i) |
— |
= ------:— 7-------- = |
|
|
sin оJJJi |
sin 0UJi |
sin E cos |
—cos E sin £^,1 _ sinE |
cos E.
sin 6W\
Искомые углы 6W\ и 6W2 начальных конусов находят по формулам
( |
sinE \ |
( |
sinE |
\ |
, j4 |
f>w\ = arctg |
----- --------- |
= arctg — |
------------ -- |
; |
(12.4) |
\ui2 + cosE / |
\2 2 |
/^l + cosE / |
|
||
|
f>w2 = S —6wi . |
|
|
(12.5) |
|
Для ортогональной передачи при Е = 90° эти соотношения |
|||||
имеют вид |
|
|
|
|
|
&wl = arctg(l/ui2) = arctg(2i/z2); |
|
g |
|||
6w2 = arctg«12 = arctg(z2/zi). |
|
|
Частным случаем неортогональной передачи является плоская коническая передача, в которой поверхность одного из начальных колес является плоскостью и угол при верши не 6WC = 90° (рис. 12.1, б).
Параметры, относящиеся к плоскому коническому колесу, обозначают с добавлением индекса с (например, число зубьев плоского колеса zc, угловая скорость ис). Формирование колес, размеров зубьев и расположение их элементов проводят отно сительно базовой конической поверхности на каждом колесе, называемой делительным конусом. При проектировании ко нических передач углы 6\ и 62 делительных конусов принима ют совпадающими с углами <5^1 и <5^,2 начальных конусов, что упрощает расчетные соотношения. Зубья образуют на колесе зубчатый венец, который располагается между конусом вер шин с углом 6а и конусом впадин с углом Sf (рис. 1 2 .2 ). При изготовлении заготовок колес используют базовое расстояние А и размеры В до вершины конуса и С — до базовой плос кости. Поверхность, отделяющую зуб от впадины, называют боковой поверхностью зуба. Пересечение боковой поверхности зуба с соосной поверхностью называют линией зуба. Линия зу ба может совпадать с образующей делительного соосного ко нуса (прямые зубья) или иметь угол (3 наклона линии зуба на делительной поверхности. Различают виды конических колес, отличающихся по форме линий зубьев на развертке делитель ного конуса (рис. 1 2 .3 ): а — с прямыми; б — тангенциальными; б — круговыми; г, д, е — криволинейными зубьями. Прямо зубые передачи используют для работы при легких нагрузках и невысоких скоростях (обычно при частоте вращения менее
Рис. 12.2
100 об/мин). Для работы в режиме максимальных нагрузок, при высоких скоростях и для обеспечения максимальной плав ности работы и бесшумности применяют передачи с криволи нейными зубьями.
Образование боковой поверхности зубьев можно просле дить по рис. 12.4. Плоскость П касается основного конуса и перекатывается по нему без скольжения. Любая прямая K L на обкатывающей плоскости П в пространстве опишет кони ческую эвольвентную поверхность, а любая точка (К >L или другая) описывает траекторию, расположенную на сфере опре деленного радиуса и называемую сферической эвольвентой. В каждом сферическом сечении на боковой поверхности зуба можно выделить линию пересечения, называемую профилем зуба. Профили зубьев в сечениях конического колеса разли чаются. Торцовые сечения подразделяют следующим образом: внешнее, среднее, внутреннее и текущее. При обозначении па раметров в том или ином сечении добавляют соответствую щий индекс (см. рис. 1 2 .2 ), например для внешнего сечения — е, для среднего — га, для внутреннего — г, для текущего — х.
Радиус Re внешнего торцового сечения называют внеш ним конусным расстоянием. Расстояние между внешним и
Рис. 12.3
Рис. 12.4
внутренним торцовыми сечениями конического колеса называ ют шириной зубчатого венца и обозначают Ь(см. рис. 1 2 .2 ).
Взаимодействие сопряженных эвольвентных конических поверхностей при заданных начальных конусах представляет собой коническое эвольвентное зацепление (рис. 12.5).
Полюсная прямая РО, лежащая в плоскости N1 ON2 , каса тельной к основным конусам, можно рассматривать как обра зующую боковых поверхностей зубьев. Любые сопряженные сферические эвольвенты имеют линию зацепления, располо женную на сфере (например, N1 PN2 ) и являющуюся дугой большого круга сферы.
Взаимодействие сферических эвольвент описать в анали тической форме довольно сложно. Учитывая, что высотные размеры зубьев невелики по сравнению с радиусом сферы и профили зубьев расположены на узком сферическом поясе, ис пользуют инженерную методику расчета, которая заключается в построении дополнительных конусов (рис. 1 2 .6 ).
Дополнительным делительным конусом называют соос ную коническую поверхность, образующая которого (напри мер, P 0 V1 или Р 0 е2 на рис. 12.6) перпендикулярна образую-
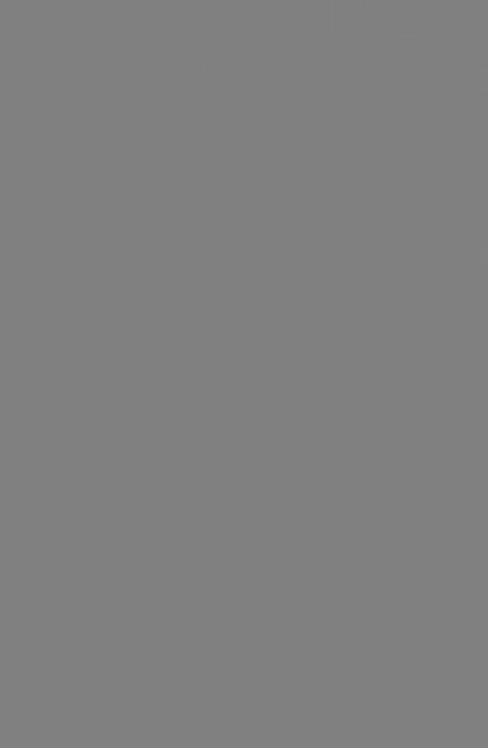
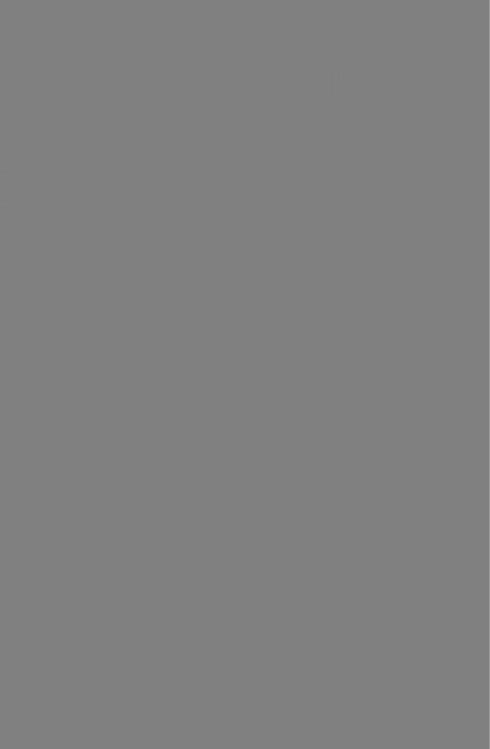
Передаточное отношение эквивалентной цилиндрической передачи определяется следующим соотношением:
z v t 2 |
z2/cos62 |
cos6\ |
/1Л . |
u v l 2 = ------- = |
--- ------ Т ~ |
= u l 2 -----7“ • |
(12.8) |
Zv t l |
Z l / C O S O i |
COS 02 |
|
Угол зацепления awvte эквивалентной цилиндрической пе редачи, радиусы raviei и ravte2 окружностей вершин, радиусы r f v t e l и r f v t e 2 окружностей впадин (см. рис. 1 2 .6 ) рассчитыва ют по формулам, аналогичным выведенным ранее для цилинд рических эвольвентных передач.
При расчете конических передач с криволинейной лини ей зуба (см. рис. 12.3) эквивалентная цилиндрическая переда ча является не прямозубой, а имеет винтовые зубья. Поэтому профили зубьев рассматривают в соответствующих нормаль ных сечениях. Прямозубое цилиндрическое зубчатое колесо, размеры и форма зубьев которого в главном сечении практи чески идентичны размерам и форме зубьев конического зуб чатого колеса с тангенциальными и криволинейными зубьями в сечении, нормальном к средней линии зуба, называют биэквивалентным цилиндрическим колесом, число зубьев кото рого обозначают zvn (соответственно zvn\ и zvn2).
С достаточной для практических расчетов точностью ко эффициент формы зубьев таких конических колес оценивают по аналогии с биэквивалентным цилиндрическим колесом, чис ло зубьев которого
z v n \ = -------с ~ ' з |
Д- ; |
z v n 2 = -------г |
2 3 д " ) |
(12.9) |
COS Oi COS'1 |
р п |
COS 0 2 |
COS'3 p n |
|
где (Зп — угол наклона средней линии зуба, соответствующей внешнему, среднему, внутреннему или другим расчетным нор мальным сечениям зуба конического зубчатого колеса.
Геометрия боковых поверхностей и профилей зубьев тес нейшим образом связана с технологией изготовления кониче ских колес. Способ копирования фасонного профиля инстру мента для образования профиля на коническом колесе не мо жет быть использован, так как размеры впадины конического колеса изменяются по мере приближения к вершине конуса. В связи с этим такие инструменты, как модульная дисковая
фреза, пальцевая фреза, фасонный шлифовальный круг, мож но использовать только для черновой прорезки впадин или для образования впадин колес не выше восьмой степени точности.
Для нарезания более точных конических колес используют способ обкатки в станочном зацеплении нарезаемой заготовки с
воображаемым производящим колесом. Боковые поверхности производящего колеса образуются за счет движения режущих кромок инструмента в процессе главного движения резания, обеспечивающего срезание припуска. Преимущественное рас пространение получили инструменты с прямолинейным лез вием. При прямолинейном главном движении прямолинейное лезвие образует плоскую производящую поверхность. Такая поверхность не может образовать эвольвентную коническую поверхность со сферическими эвольвентными профилями. По лучаемые сопряженные конические поверхности, отличающие ся от эвольвентных конических поверхностей, называют квазиэвольвентными (по старой терминологии — октоидальными).
Производящие колеса могут быть плоскими С 6Woc — 90° (рис. 12.7, а, б) или плосковершинными с 6W0C = 90° — 0fwo\
(рис. 12.7, б) при одном и том же угле Swoj при вершине аксоидного конуса станочного зацепления. В первых двух слу чаях образуемые квазиэвольвентные конические колеса будут сопряженными, поскольку производящие плоские колеса обра зуют совпадающую пару, боковые производящие поверхности зубьев которой могут совпадать при наложении во всех своих точках (как отливка и форма или шаблон и контршаблон). Од нако станок, реализующий схему станочного зацепления в со ответствии с рис. 12.7, а, должен иметь поворотные направля ющие, допускающие установку резцовых направляющих под углом (90° - 0fwoi ), где вj wo\ — угол ножки зуба нарезаемого колеса в станочном зацеплении. Это усложняет конструкцию станка и используется ограниченно.
В случае движения резцов без учета угла Qfwol (см* рис. 12.7, б) высота ножки зуба по мере приближения к верши не конуса остается неизменной, что ослабляет зуб И приводит иногда к подрезу ножки.
Большинство моделей станков построены на использова нии плосковершинного производящего колеса, у которого вер шины зубьев расположены в плоскости, а угол аксоидного ко нуса в станочном зацеплении рассчитывается с учетом угла
O f w o i ножки зуба нарезаемого колеса. Два плосковершинных колеса не образуют совпадающую производящую пару, и по этому нарезаемые квазиэвольвентные колеса будут несопря женными. Эти погрешности обычно являются незначитель ными и ими обычно пренебрегают.
Расчетная схема, приведенная на рис. 12.8, позволяет на базе станочного зацепления конического колеса с производя щим плосковершинным колесом перейти к эквивалентному станочному зацеплению с теоретическим исходным контуром. Исходный контур, совпадающий с реечным контуром, приня тым в качестве базового для определения теоретических форм и размеров зубьев конических колес, регламентирован по ряду параметров: а = 20°; /i* = 1 , 2 ; с* = 0 , 2 ; ру- < 0,3. Однако
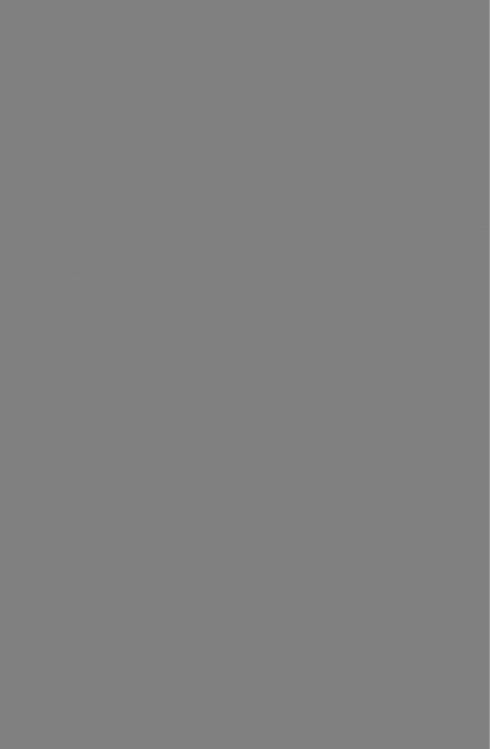
ширина зубчатого венца b < 0,3Ле, или Ъ< 10гае; коэф фициент ширины зубчатого венца кье = b/Rwe = 0 ,2 ... 0,3;
угол делительного конуса
6i — arctg ( |
Z2/ 2I |
^ c o s s ) ’ |
(12.13) |
62 = |
E - |
6 1 ; |
(12.14) |
90° |
|
|
|
<5i = arctg(zi/z2); |
(12.15) |
коэффициент смещения исходного контура х\ = 0 ... 0 , 6 в зависимости от числа зубьев z\ и передаточного отношения передачи (Х2 = —xi)
_ |
^ _ |
1 псо |
0,058*1. |
Мо 1вЧ |
®1 |
—®1 min — 1)068 |
г ) |
(12.16) |
|
|
|
|
COS dl |
|
коэффициент изменения расчетной толщины зуба исход ного контура
хт\ = 0,03 - 0,008(Z2/ZI - 2,5); хТ2 = - х т\. |
(12.17) |
Расчет параметров зубчатых колес проводят с использо ванием следующих расчетных формул, вывод которых основан на расчетной схеме (см. рис. 1 2 .8 ):
внешняя высота головки зуба
hael ~ {ha х\^те, |
hac2 — |
hae\, |
(12.18) |
|
внешняя высота ножки зуба |
|
|
||
hfel = hae2 Н” ^ |
TTiej |
hfe2 —^ael |
^ 777-6) |
(12.19) |
внешняя высота зуба |
|
|
|
|
|
he = hae -f hfe\ |
|
(1 2 .2 0 ) |
|
внешняя окружная толщина зуба |
|
|
||
5ei = (0,б7г + 2ii tga + Жг1)”ге; se2 |
= тгте - sei; |
(12.21) |
||
угол ножки зуба |
|
|
|
|
0 /1 |
= |
arctg(/iyel/J?e); |
(1 2 .2 2 ) |
|
0 / 2 |
= |
arctg(/iye2 / i 2e); |
(12.23) |
|
0al |
< 0/2! &a2 < 0/1 > |
(12.24) |
угол конуса вершин |
|
|
|
|
|
<5ai = <5i + 0ai; |
ba2 = h |
+ @а2; |
(12.25) |
||
угол конуса впадин |
|
|
|
|
|
<S/i = |
- 0 /i; |
<5/2 - |
h |
- 0/2; |
(12.26) |
внешний делительный диаметр |
|
|
|
||
dei = |
m ezi; |
de2 = |
m eZ2; |
(12.27) |
|
внешний диаметр вершин зубьев |
|
|
|
||
dael = del + 2 /iaei cos^i; dae2 = de2 + 2hae2 cosS2. |
(12.28) |
При проверке качества зацепления по геометрическим по казателям рассчитывают коэффициент еа торцового перекры тия, внешнюю окружную толщину зуба sae на поверхности вершин и проверяют отсутствие подрезания зубьев с исполь зованием эквивалентного цилиндрического зацепления.
Рекомендуемые значения показателей следующие: ко эффициент торцового перекрытия еа > 1,3; относительная окружная толщина зуба на поверхности вершин s*e = sae/me > > 0 , 3 — при однородной структуре металла; s*e > 0,4 — при поверхностном упрочнении зубьев.
При выборе исходных данных учитывают заданное пере даточное отношение и\2 и его допустимое отклонение в связи с тем, что числа зубьев — целые числа. Рекомендуется числа зубьев колес назначать в пределах от 12 до 1 0 0 .
Для прямозубой конической пары рекомендуется назна чать передаточные отношения: щ 2 < 5 — для замедляющей, и\2 >0,35 — для ускоряющей передач.
Межосевой угол Е назначают в пределах от 10 до 170°, для ортогональной передачи его назначают равным 90°
Параметры исходного контура стандартизованы. На рис. 12.8 они приведены в соответствии с ГОСТ 13754-81.
Коэффициент ширины зубчатого колеса /tye = b/Rwe реко мендуется выбирать в пределах 0 , 2 ... 0 , 8 . Увеличение длины зуба за эти пределы на практике приводит к краевому кон такту зубьев вследствие погрешностей монтажа и деформаций их под нагрузкой, т.е. не способствует повышению несущей способности передачи.
Рис. 12.9
При проектировании быстроходных передач, работающих при переменных нагрузках, числа зубьев z\ и z<i должны быть взаимно простыми числами, т.е. не иметь общих делителей. Если передача работает при постоянной нагрузке и умеренных линейных скоростях, то стремятся к тому, чтобы числа z\ и Z2 были бы кратны друг другу, или имели возможно большее чис ло общих делителей, что способствует ускоренной приработке рабочих поверхностей зубьев. При расчете соосных кониче ских передач необходимо согласовывать числа зубьев, углы их начальных конусов и углы между осями. Например, для пла нетарного механизма с коническими колесами, схема которого изображена на рис. 1 2 .9 , должны выполняться следующие со отношения:
£ 1 2 + S23 = 180°;
+_ с _ |
sin S 12 |
|
z\ /Z2 + COS 2J 12 |
. , |
sin E23 |
2 |
Z3 /Z2 + COSE23 |
Решая эти соотношения совместно, получают соотноше ние для межосевого угла £ 12:
V, |
*3 - *1 |
cos £12 = |
— ----- . |
|
2 Z 2 |
Из последнего соотношения легко установить нижний пре дел для чисел Z2 IZ2 > 0 , 5 (z3 —z\).
Гиперболоидпой зубчатой передачей называют переда чу со скрещивающимися осями, аксоидами ее зубчатых ко лес являются однополостные гиперболоиды вращения (см. рис. 9.1, в), оси которых не пересекаются.
Для обеспечения точечного касания линий зубьев можно применить более простые по форме поверхности, чем гипербо лоиды вращения, что упрощает изготовление зубчатых колес. Например, круглые цилиндры, соприкасающиеся только в од ной точке, лежащей на линии кратчайшего расстояния между осями колес, или конусы с несовпадающими вершинами.
Гиперболойдную зубчатую передачу, начальные поверх ности зубчатых колес которой — круглые цилиндры, назы вают винтовой зубчатой передачей (см. рис. 2.18, д). Если в качестве начальных поверхностей зубчатых колес выбрать конусы с несовпадающими вершинами, то получим гипоид ную зубчатую передачу (см. рис. 2.18, ж). Червячная переда ча представляет собой гиперболойдную передачу, начальные и делительные поверхности зубчатых колес которой отличны от конических, и шестерня (червяк 1) (см. рис. 2.18, е) имеет винтовые зубья, а звено 2 называется червячным колесом.
Винтовая зубчатая передача (рис. 12.10) представляет собой гиперболойдную передачу, начальные поверхности зуб чатых колес которой сливаются с делительными, а оси скрещи ваются под произвольным межосевым углом £. В большинстве случаев применяют передачи с Е = (5W\ ± (5W2 = 90°, где (3wl и flw2 — углы наклона линий зубьев (винтовых линий) по на чальным цилиндрам; верхний знак соответствует одноименно му направлению винтовых линий, нижний — разноименному.
В отличие от косозубых цилиндрических передач для вин товых зубчатых колес не является обязательным равенство углов наклона винтовых линий и разноименность их напра влений.
На рис. 12.10, a-в показаны три проекции начальных ци линдров винтовой передачи с радиусами rw\ и rW2 и концент ричные им основные цилиндры с радиусами гв\ и гв2 . Вин товые линии на начальных цилиндрах показаны в положении
Рис. 12.10
касания в полюсе Р зацепления, п - п — нормаль к ним. Об щая касательная т—тсоставляет с осями колес соответственно углы (iw\ и /3^2 , сумма которых равна Е.
Через полюс Р зацепления проходят образующие плоско сти Ец и Ei2 , касательные к основным цилиндрам, в которых
расположены прямолинейные образующие, боковые поверхно сти зубьев, составляющие углы /Зц и 2 с осями колес. В пе редачах со скрещивающимися осями производящие плоскости пересекаются по прямой, представляющей собой геометриче ское место точек контакта боковых поверхностей зубьев, на зываемых линией зацепления. Предельные точки N\ и N2 ли нии зацепления отмечены на основных цилиндрах. Активная длина линии зацепления определяется точками В\ и В2 пере сечения линии зацепления поверхностями цилиндров вершин зубьев колес радиусами га\и та2 .
Для колес 1 и 2 , вращающихся соответственно с угловы ми скоростями и\ и ^2 , на рис. 1 2 .1 0 , в представлен план ско ростей, построенный при расположении колеса 1 над колесом 2. Исходя из равенства нормальных составляющих v™2 окруж ных скоростей в точке касания начальных цилиндров,’справед ливо соотношение vn = u\rw\ cosj3w\ = U2rw2cos Pw2> откуда
^ 1 r w2 COS Pw2
(12.29)
Ш2 1*w l COS (3w i
Из этого следует положение, характерное для винто вых передач: заданное передаточное отношение и\2 можно осуществить, выбирая произвольно отношения rw2 /rwi или cos(3W2/ cospwi. Если передача образована винтовыми колеса ми с правым и левым направлением винтовых линий, то знак в равенстве (12.29) будет отрицательным. Формула (12.29) сви детельствует о многозначности решения задачи осуществле ния заданного передаточного отношения. Из множества вари антов следует выбрать тот, который дает лучшие качествен ные показатели зацепления винтовых линий.
В нормальном сечении шаг и модуль колес винтовой пере дачи одинаковы, поэтому для передачи, у которой начальные и делительные цилиндры сливаются, имеем р = pw\ = pw2 = = р = 7Г7п; в торцовых же сечениях модули разные: га/ cos/?i и га/ cos/?2 -
Радиусы делительных и начальных цилиндров определя ются следующими формулами:
mz\
rriZ2 |
(12.30) |
|
&w — Тw\ "1“ Тw2 |
— ( Zl |
. Z2 \ |
(12.31) |
|
2 \COS/?i |
COS /?2 / |
|||
|
|
Все исполнительные размеры определяются по формулам для косозубых колес (см. § 1 1 .6 ). Скорость скольжения боко вых поверхностей зубьев в направлении общей касательной к винтовым поверхностям зубьев для контактной точки, совпа дающей с полюсом (см. рис. 1 2 .1 0 ) можно найти по формуле
|
vi |
rw |
u\mz\ |
V C K |
sin |
sin (3W\ |
(12.32) |
|
2 cos pwi sin (3Wi ' |
Вследствие точечного контакта рабочих поверхностей рас сматриваемых передач в сочетании со значительным скольже нием их нагрузочная способность мала, поэтому винтовые пе редачи применяют большей частью в приборостроении.
Червячную зубчатую передачу, являющуюся частным случаем гиперболойдной, используют для передачи вращения между скрещивающимися осями с постоянным отношением скоростей звеньев. В большинстве случаев угол скрещивания осей выбирается равным 90°.
Известны две разновидности червячного зацепления: а) с цилиндрическим червяком (рис. 1 2 .1 1 , б) (поверхность вит ков такого червяка является геликоидом); б) с глобоидным червяком (рис. 1 2 .1 1 , в), по форме которого зацепление назва но глобоидным. В зависимости от направления линии витка червяка червячные передачи бывают с правым и левым на правлением линии витка. В зависимости от формы винтовой поверхности червяка передачи бывают с архимедовым (архи медова спираль), конволютным (удлиненная или укороченная эвольвента) или эвольвентным червяком. Червячное колесо представляет собой косозубое колесо с зубчатым венцом спе циальной горловидной формы, охватывающим червяк и обра зующим как бы бесконечную гайку. Работу червячной пере дачи можно представить как непрерывное ввинчивание винта
— червяка в бесконечную гайку — червячное колесо. Чер вяк, как правило, является ведущим звеном, а червячное ко лесо — ведомым. Обратная передача движения (за редким исключением) неосуществима из-за эффекта самоторможения.
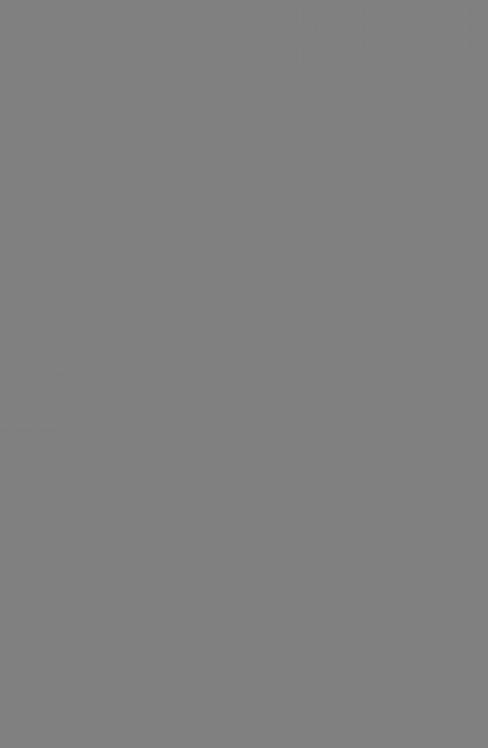
На рис. 12.11, а представлена червячная зубчатая передача с червяком цилиндрической формы.
В отличие от винтовой передачи, составленной из цилинд рических колес с винтовыми зубьями, в червячном зацепле нии поверхности зубьев имеют не точечное, а линейное каса ние, что позволяет использовать такое зацепление для пере дачи значительных нагрузок. Другим важным достоинством червячной передачи является возможность обеспечения пере даточного отношения от 20 до 500. Кроме того, червячная передача, как и другие косозубые передачи, обладает высокой плавностью и бесшумностью вращения.
Червячные передачи имеют и существенные недостатки: 1 ) КПД этих передач по сравнению с КПД других передач
низок и составляет 0 , 5 ... 0 , 7 ; 2 ) повышенное скольжение контактирующих профилей
вызывает их износ и требует применения для венцов червяч ных колес антифрикционных материалов;
3)значительное выделение теплоты в зоне зацепления чер вяка с колесом требует интенсивного охлаждения передачи;
4)большая осевая сила, действующая на червяк, требует постановки его на подшипники, способные воспринимать эти реакции.
Нарезание червяков и червячных колес. В соответ ствии с ГОСТ 18498-73 введены обозначения различных видов червяков. Например, архимедов червяк обозначается как чер вяк ZA, конволютный — червяк ZJV, эвольвентный — червяк ZJ и т.д. Каждый из них требует особого способа нарезания. Нарезание червяков осуществляется либо резцами на токарно винторезных станках, либо модульными фрезами на резьбо фрезерных станках.
Резец, имеющий в сечении форму трапеции (рис. 1 2 .1 2 , а), устанавливают на токарно-винторезном станке так, что верх няя его плоскость А —А проходит через ось червяка (положе ние 7), и при нарезании образует винтовую поверхность, ко торая в сечении, перпендикулярном оси червяка, дает кривую
—архимедову спираль. В этом случае червяк называют архи медовым. Архимедов червяк в осевом сечении имеет прямоли нейный профиль витка, аналогичный инструментальной рейке.
А-А
Рис. 12.12
Угол между боковыми поверхностями профиля витка у стан дартных червяков, согласно ГОСТ 19036-81, а = 20°. Если же резец повернуть на угол подъема винтовой линии червяка 7 (положение 2) так, чтобы верхняя плоскость резца А - А была перпендикулярна винтовой линии, то при нарезании по лучится винтовая поверхность, которая в сечении, перпенди кулярном оси червяка, дает кривую — конволюту, а червяк соответственно называют конволютным.
Для нарезания эвольвентных червяков используют два резца (рис. 1 2 .1 2 , б). Резец 1 с правой режущей кромкой, уста новленный выше оси червяка на расстоянии радиуса основного цилиндра (dj,o/ 2 ), образует левую поверхность витка. Резец 2, установленный ниже оси червяка на расстоянии радиуса основ ного цилиндра, образует правую поверхность витка червяка. Режущие кромки а ^ - Д и а д - /д совпадают с образующими прямыми, а в результате при нарезании получается винтовая поверхность, которая в сечении, перпендикулярном оси червя ка, дает кривую — эвольвенту окружности.
Червячные колеса чаще всего нарезают червячными фре зами, причем червячная фреза должна представлять собой ко пию червяка, с которым будет зацепляться червячное коле со. Станочное зацепление червячного колеса и фрезы воспро изводит рабочее зацепление червячной передачи. Работоспо собность червячной передачи зависит от твердости и чистоты винтовой поверхности червяка, поэтому после нарезания резь бы и термообработки червяки шлифуют, а иногда и полируют.
Кинематические и геометрические соотношения в червячной передаче. Червячная передача характеризуется передаточным числом гб = ^2 /^1 , где Z1 — число зубьев колеса (обычно z\ — 18...300); z<i — число витков червяка (обычно z2 = 1...4).
Геометрические размеры червячной передачи опреде ляются межосевым расстоянием а^, которое зависит от диаметров червяка и колеса (рис. 12.13) и регламентируется ГОСТ 2144-76.
Главными параметрами червяка являются модуль т и ко эффициент диаметра q. Модулем червяка называют линейную величину, в q раз меньшую расчетного шага червяка. Расчет ным шагом червяка является делительный осевой шаг витков.
Рис. 12.13
Расчетным шагом одновиткового червяка является делитель ный ход витка, равный расстоянию между одноименными про филями данного витка по образующей делительного цилиндра. Коэффициент диаметра qравен отношению делительного диа метра червяка к его модулю: q = di/m.
Модули и коэффициенты диаметра регламентируются стандартом в соответствии с ГОСТ 19672-74. Чтобы червяк не был слишком тонким, коэффициент диаметра увеличивают, а модуль уменьшают.
Окружности, определяющие размеры червяка в средней торцовой плоскости, называют средними концентрическими. Различают окружности: делительную, диаметром di, началь ную, диаметром dw1 , вершин витков — da1 , впадин — dyj, при надлежащие соответственно поверхностям делительной, на чальной, вершин витков и впадин.
Диаметр делительного цилиндра червяка выбирают крат ным осевому модулю червяка: d\= mq. Начальный диаметр червяка без смещения dw\равен делительному. Если коэф фициент смещения исходного производящего контура инстру мента при нарезании червячного колеса х ф 0 , то начальный цилиндр червяка не сливается с его делительным цилиндром:
dw1 = m(q+ 2х).
Наклон винтовой линии витка по делительному цилиндру определяют делительным углом подъема 7 и находят его из
соотношения |
^ |
|
|
t g 7 |
~ ird1 ~ |
^ |
q ' |
Высоту ГОЛОВКИ halИ НОЖКИ hfi витков вычисляют по |
|||
формулам |
|
|
|
hai — h*am; |
hfi = |
|
где коэффициент высоты головки h*= 1 , коэффициент высоты ножки для архимедовых и конволютных червяков равен -2, а для эвольвентных (1 + 0 , 2 cos 7 ).
Диаметр вершин витков червяка равен
dal = ™(q + 2Ла);
диаметр цилиндра впадин —
dfi = d\ —2hfi;
п - 11273
толщина витка по делительному цилиндру составляет
жт
51 = ^ - ' На основании ранее выведенных в § 11.3 формул для
эвольвентной цилиндрической зубчатой передачи основные размеры червячного колеса в среднем сечении и червячной пе редачи рассчитывают с использованием следующих формул:
диаметр делительной окружности
d2 = rriZ2\
диаметр окружности вершин зубьев
da2 = rn(z2 + 2х + 2 /i*);
диаметр окружности впадин
df2 = m{z2 + 2х - 2 h*f);
высота зуба
h = m(h* + h*j);
толщина зуба по делительной окружности
S2 = m |
+ 2 a : t g a ) ; |
межосевое расстояние зубчатой передачи
aw = m[(q + ^ ) / 2 + х].
Смещение червяка выполняют с целью вписывания пере дачи в стандартное межосевое расстояние. Коэффициент сме щения х исходного производящего контура инструмента выби рают в пределах ± 1 . Предпочтительно использовать положи тельные смещения, при которых повышается прочность зубьев колеса.
Контрольные вопросы
1.Какую форму имеют сопряженные поверхности прямозубых колес при коническом эвольвентном зацеплении с заданными начальными конусами?
2.В чем заключается сущность метода дополнительных конусов и экви валентной цилиндрической передачи при расчете конической переда чи?
3.Какую форму имеют боковые поверхности производящих плоских и плосковершинных колес в станочном зацеплении?
4.Каковы особенности кинематики и геометрии конической передачи?
5.Расскажите об инженерной методике расчета конической прямозубой передачи.
6.В чем состоит различие между винтовой, гипоидной и червячной зубчатыми гиперболоидными передачами?
7.Для каких случаев используются гиперболоидные передачи?
8.Какие механизмы называют гиперболоидными и каковы их разно видности?
9.Какие виды червячных передач используют в механизмах машин?
10.Какими особенностями кинематики вызвано скольжение зубьев чер
вячной передачи?
11.Расскажите об основных достоинствах и недостатках червячных пе редач.