
- •Введение
- •1. Аналитический обзор. Выбор направления исследований
- •1.1. Флотация, электрофлотация, электрофлотокоагуляция, современные направления извлечения взвешенных веществ, цветных, редкоземельных металлов и органических веществ. Научные школы
- •2. Методическая часть
- •2.3. Определение характеристик дисперсной фазы
- •2.4. Информация об использованных в работе ПАВ, флокулянтах и коагулянтах
- •2.5. Характеристика некоторых образцов дисперсной фазы
- •4. Новые области применения электрофлотационных процессов. Основные научные результаты
- •5.2. Роль дисперсной фазы в эффективности электрофлотацинного процесса
- •Заключение
- •Список сокращений и условных обозначений
- •Список литературы
- •Приложение 1
- •Акты и протоколы опытно-промышленных и промышленных испытаний установок для очистки сточных вод
- •Приложение 2
196
5.2. Роль дисперсной фазы в эффективности электрофлотацинного процесса
Проанализировано влияние природы дисперсной фазы, заряда и размера частиц на электрофлотационный процесс извлечения взвешенных веществ из водных растворов электролитов NaCl, Na2SO4, NaNO3, Na3PO4. Экспериментальные данные представлены в разделе 3 и подразделах 4.1 и 4.2. Некоторые сводные данные приведены в таблице 5.4.
Анализ показывает, что низкие степени извлечения наблюдаются в первую очередь для частиц размер которых 10–15 мкм, что связано со сложностью формирования флотокомплексов с пузырьками H2 и O2, размер которых 20–40 мкм.
Высокая эффективность формирования флотокомплекса (α5) и максимально высокие степени извлечения (α30) > 90% наблюдается для частиц, размер которых
50–100 мкм, обладающих рыхлой, хлопьевидной структурой (гидроксиды металлов) и
имеющих небольшой заряд поверхности (ξ ±10 мВ). Для сильно гидратированной поверхности порошков, несмотря на достаточно большой размер частиц, степень извлечения невелика.
Таблица 5.4 – Влияние природы дисперсной фазы, размера частиц и электрокинетического потенциала ее поверхности на степень извлечения взвешенных веществ
Система |
pH |
Ø, сред |
ξ, |
|
α5, |
|
α30, |
|
|
мкм |
мВ |
|
% |
|
% |
Ni3(PO4)2 |
|
12 |
–35 |
|
40 |
|
75 |
Ni(OH)2 |
|
50 |
+10 |
|
45 |
|
92 |
Cu3(PO4)2 |
10 |
50 |
–43 |
|
75 |
|
93 |
Cu(OH)2 |
60 |
–20 |
|
70 |
|
98 |
|
|
|
|
|||||
Zn3(PO4)2 |
|
10 |
–35 |
|
11 |
|
62 |
Zn(OH)2 |
|
180 |
–12 |
|
77 |
|
97 |
TiO2 |
|
11 |
–14 |
|
5 |
|
14 |
TiN |
|
18 |
–15 |
|
5 |
|
10 |
Ti(OH)4 |
|
10 |
–10 |
|
5 |
|
25 |
ОУ-Б |
|
25 |
–36 |
|
30 |
|
50 |
ОУ-А |
7 |
13 |
–28 |
|
3 |
|
10 |
SiC |
|
19 |
–23 |
|
5 |
|
11 |
Al(OH)3 – NaCl |
|
15 |
30 |
|
25 |
|
50 |
Al(OH)3 – Na2SO4 * |
|
10 |
–2 |
|
10 |
|
25 |
Fe(OH)3 – NaCl |
|
60 |
10 |
|
65 |
|
92 |
Условия эксперимента: |
с NaCl – 1 г/л; * с Na2SO4 |
– 1 г/л; Jv |
– 0,4 А/л; τ – 30 мин; |
без ПАВ и флокулянтов.
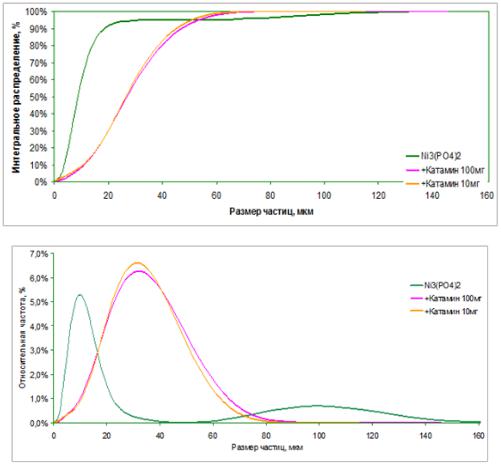
197
Отмечено, что при малых размерах частиц (5–15 мкм) осложняется электрофлотационный процесс формирования флотокомплекса в первую очередь для отрицательно заряженных частиц (ξ<0) и пузырьков водорода, сформированных на катоде и имеющих небольшие отрицательные заряды поверхности.
При размерах частиц > 50 мкм электростатические факторы влияют минимально,
т.к. формирование флотокомплекса происходит, вероятно, за счет механического захвата
«пузырек – частица» как в обычной (классической) флотации.
Молекулы ПАВ при высоких концентрациях вызывают классическую гидрофобную флотацию частиц. На рисунке 5.8 приведен пример влияния ПАВ катионного типа (Катамин АБ) на дифференциальное и интегральное распределение размера частиц фосфата никеля в водном растворе при концентрации ПАВ 10 и 100 мг/л.
Размер частиц увеличивается в 4 раза, что создает хорошие условия для электрофлотационного извлечения Ni3(PO4)2.
1
2,3
1
2
3
|
|
1 |
|
2,3 |
2 |
|
3 |
|
1 |
|
|
|
|
Рисунок 5.8 – Дифференциальное и интегральное распределение по размерам частиц фосфата никеля в присутствии катионного ПАВ различной концентрации
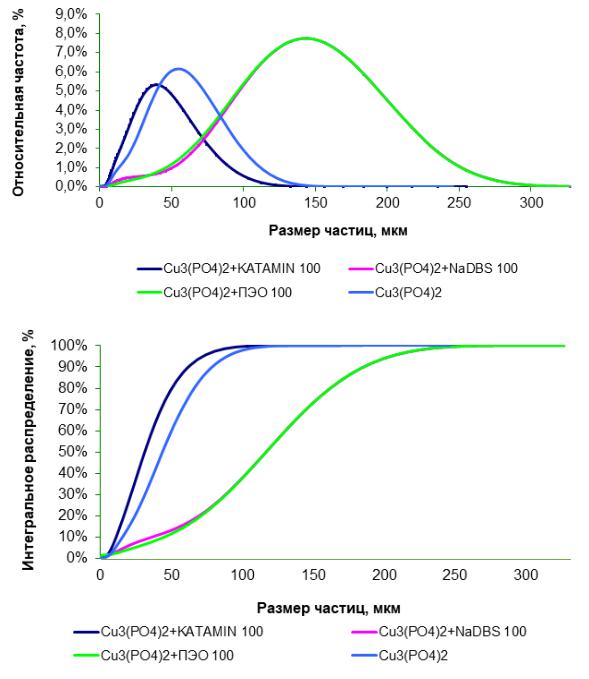
198
Влияние катионного ПАВ связано с адсорбцией на дисперсной фазе Ni3(PO4)2,
имеющей отрицательный заряд и величину ζ-потенциала – 35 мВ при pH=10. Влияние ПАВ различной природы на интегральное и дифференциальное распределение частиц дисперсной фазы Cu3(PO4)2 по размерам в присутствии анионного ПАВ NaDDS,
катионного ПАВ Катамин АБ и неионогенного ПАВ ПЭО-1500 представлено на рисунке
5.9.
2 3,4
1
2 |
4 |
3 |
1 |
1 |
2 |
3,4 |
|
|
2 |
4 |
3 |
1 |
Рисунок 5.9 – Интегральное и дифференциальное распределение частиц дисперсной фазы фосфата меди по размерам: условия эксперимента: с Сu2+ –50мг/л; с PO43- – 55мг/л; с ПАВ – 100 мг/л; с Na2SO4 – 1 г/л; рН = 9,5
199
Анализ показывает, что в присутствии катионного ПАВ происходит агрегирование частиц, размер увеличивается с 40 до 60 мкм. Более сильное влияние оказывают анионный и неионогенный ПАВ, средний размер частиц возрастает до 150 мкм, что способствует протеканию процессов коагуляции в больше мере, чем флотации.
Указанный эффект связан с высокой концентрацией ПАВ, формированием полислоев на поверхности Cu3(PO4)2. Приведенные два примера показывают, что в реальных системах дисперсная фаза в присутствии ПАВ может существенно изменить распределение частиц по размерам.
Методом электронной микроскопии проведено исследование свежесформированных осадков гидроксидов железа, никеля, меди и цинка в фоновых растворах электролитов NaCl, Na2SO4 и NaNO3. Процессы формирования осадков ионов металлов происходят при очистке сточных вод гальванохимических производств. Во всех осадках раствора Na2SO4 имеются примеси гидроксисульфатов. В образцах №1 наряду с гидроксидом железа (III) присутствует фаза оксидов железа (магнетит – гоетит).
Обобщенные данные результатов исследования экспериментальных образцов методом электронной микроскопии приведены в таблице 5.5.
200
Таблица 5.5 – Морфология, размеры частиц и структура осадков
№ |
|
Фоновый |
Размер |
|
|
|
Структура |
п/п |
Вещество |
электро- |
Форма частиц |
|
|||
частиц, нм |
|
осадка |
|||||
|
|
лит |
|
|
|
||
|
|
|
|
|
|
|
|
1 |
|
NaCl |
40–80 |
Частицы |
сферической |
|
|
|
|
формы |
|
|
|
||
|
Гидроксид |
|
|
|
|
|
|
|
NaNO3 |
d = 40–80; |
Частицы |
сферической |
Рыхлая |
||
|
железа (II) |
||||||
|
Na2SO4 |
|
и пластины игольчатой |
|
|||
|
|
|
|
||||
|
|
300-500 |
формы |
|
|
|
|
|
|
|
|
|
|
||
2 |
|
NaCl |
d = 100; |
Хлопьевидные |
|
|
|
|
|
l = 12–18 |
|
|
|||
|
|
|
|
|
|
|
|
|
Гидроксид |
NaNO3 |
d = 120; |
Хлопьевидные |
|
Плотная |
|
|
никеля (II) |
l = 12–18 |
|
||||
|
|
|
|
|
|
||
|
|
Na2SO4 |
d = 150-200; |
Хлопьевидные |
|
|
|
|
|
l = 20 |
|
|
|||
|
|
|
|
|
|
|
|
3 |
|
NaCl |
d = 600–900; |
Хлопьевидные |
|
|
|
|
|
l = 15–20 |
|
|
|||
|
|
|
|
|
|
|
|
|
Гидроксид |
|
d = 700–1500; |
Хлопьевидные |
с |
Менее |
|
|
NaNO3 |
примесью |
аморфной |
||||
|
цинка (II) |
l = 25–30 |
плотная |
||||
|
|
фазы |
|
|
|||
|
|
|
|
|
|
|
|
|
|
Na2SO4 |
d = 1500–2300; |
Хлопьевидные |
|
|
|
|
|
l = 30 |
|
|
|||
|
|
|
|
|
|
|
|
4 |
|
NaCl |
d =1070–2700; |
Хлопьевидные |
|
Ячеистая |
|
|
|
l = 60–110 |
|
||||
|
|
|
|
|
|
|
|
|
Гидроксид |
NaNO3 |
d = 276–392; |
Хлопьевидные |
|
Ячеистая |
|
|
кобальта |
l = 25–35 |
|
||||
|
|
|
|
|
|
||
|
(II) |
|
d = 1200–1400 |
Хлопьевидные |
с |
|
|
|
|
Na2SO4 |
l = 40–80 |
примесью агломератов |
Ячеистая |
||
|
|
|
d =25 |
из сферических частиц |
|
||
5 |
|
NaCl |
d = 600–1500; |
Пластинчатые |
|
|
|
|
|
l = 52 |
|
Слоисто- |
|||
|
|
|
|
|
|
||
|
|
NaNO3 |
d = 500–1000; |
Пластинчатые |
|
столбчатая |
|
|
Гидроксид |
l = 30–50 |
|
|
|||
|
|
|
|
|
|
||
|
меди (II) |
|
|
Друзы из пластинчатых |
|
||
|
|
Na2SO4 |
d = 450–550; |
кристаллитов, |
|
Рыхлая |
|
|
|
l = 50–60 |
стремящиеся |
к |
|||
|
|
|
|
||||
|
|
|
|
глобулярной структуре |
|
Методика исследования представлена в разделе 2.
Микроанализ полученных образцов, выполненный методом сканирующей электронной микроскопии, позволяет разделить их по морфологии на три типа: частицы сферической формы (образец №1 а), а также сочетание частиц сферической и пластин игольчатой формы, тонкие (образцы №2, 3, 4) и толстые хлопья (образец № 5), соответственно. Согласно результатам исследования, образцы осажденной фазы

201
гидроксида железа (№1) представлены в виде частиц сферической формы, объединенных в агломераты (рисунок 5.10 и 5.11), что является характерным для материалов, формирующихся в жидких средах.
а |
б |
Рисунок 5.10 – Осажденная фаза гидроксида железа на фоне хлорида натрия: |
|
|
а – х20000; б – 50000 |
Наряду с частицами |
сферической формы (на микрофотографиях гидроксида |
железа, на фоне сульфата натрия), отмечаются кристаллы игольчатой формы длиной
300–500 нм, доля которых выше в образце, полученном на фоне сульфата натрия.
а б
Рисунок 5.11 – Осажденная фаза гидроксида железа на фоне сульфата натрия:
а – х20000; б – х50000
Размеры кристаллитов, образующих агрегаты, варьируют в диапазоне 40–80 нм, большая часть которых имеет размеры ~ 50 нм, наряду с ними имеются также включения частиц размером 120 нм. По визуальной оценке, осадок сравнительно рыхлый.
Образцы № 2 (гидроксид никеля) представлены тонкими хлопьями. Судя по микрофотографиям, фоновый электролит не оказывает влияния на морфологию осадка,

202
но влияет на размер частиц, который растет с увеличением заряда кислотного остатка.
Так, хлопья на фоне хлорида натрия имеют диаметр ~100 нм и толщину 12-18 нм, на фоне нитрата натрия: ~120 нм х 12–18 нм, на фоне сульфата натрия их толщина составляет ~20 нм, а их диаметр варьируется от 150 до 250 нм. Визуально, осадок плотный.
а б
Рисунок 5.12 – Осажденная фаза гидроксида никеля на фоне хлорида натрия: а – х20000; б –х50000
а |
б |
Рисунок 5.13 – Осажденная фаза гидроксида никеля на фоне сульфата натрия: |
а – х20000; б – х50000
Морфология образцов № 3 (гидроксид цинка) аналогична образцам № 2, но при
этом хлопья отличаются более крупными размерами. Хлопья гидроксида цинка на фоне хлорида натрия имеют диаметр от 600 до 900 нм и толщину 15–20 нм; на фоне нитрата натрия: от 700 нм до 1,5 мкм и толщину 25 – 30 нм, на фоне сульфата натрия их толщина составляет ~30 нм, а диаметр варьируется от 1,5 до 2,3 мкм (рисунок 5.14). Осадок представлен в виде объемных изометричных ячеек из хлопьев.
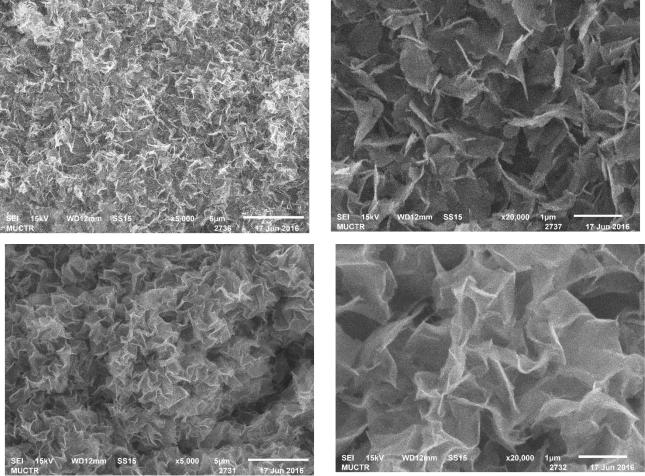
203
а |
б |
Рисунок 5.14 – Осажденная фаза гидроксида цинка на фоне сульфата натрия: а – х5000; б – х20000
Хлопья образцов № 4 (гидроксид кобальта) на фоне хлорида натрия имеют диаметр
1,07–2,7 мкм и толщину 60–110 нм, на фоне нитрата натрия отмечается более узкое распределение по размерам: их диаметр составляет 276–392 нм, а толщина 25–35 нм, большая жесткость частиц обеспечивает им меньшую деформацию в процессе осаждения. Осажденная фаза на фоне сульфат-иона представлена сочетанием агломератов из частиц сферической формы диаметром 25 нм и хлопьев размером 1,2–1, 4 мкм х 40–80 нм.
Образцы № 5 (гидроксид меди) на фоне хлорида натрия имеют вид толстых пластинок фиксированной толщины, похожих на монокристаллы, которые располагаются слоями. Диаметр частиц изменяется в диапазоне 600 нм -1,5 мкм, толщина составляет 52 нм (рисунок 5.15), осажденная фаза на фоне сульфат-иона представлена агломератами частиц, стремящимися к глобулярной форме и отличаются самым узким распределением по размерам, их диаметр составляет 450–550 нм, а толщина 50–60 нм (рисунок 5.15).
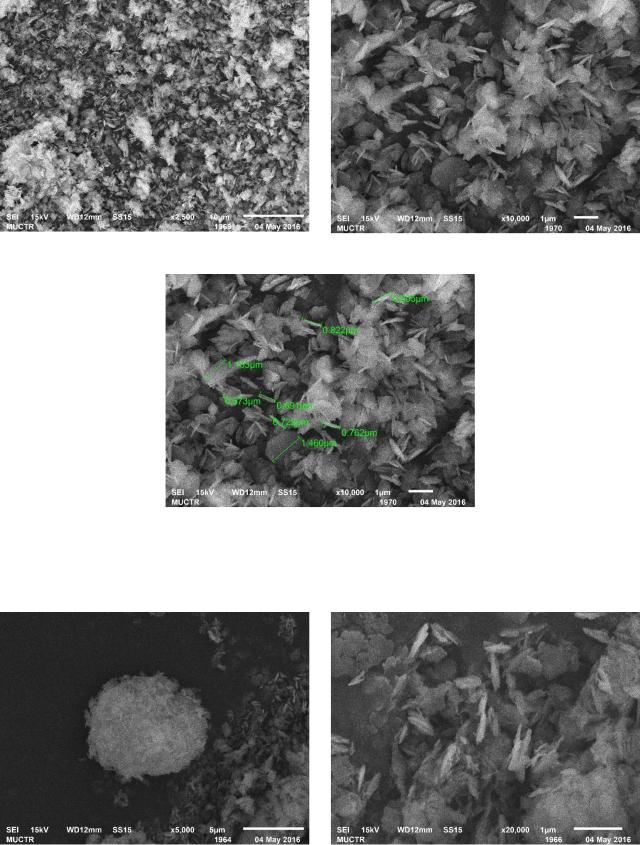
204
а |
б |
в
Рисунок 5.15 – Осажденная фаза гидроксида меди на фоне хлорида натрия:
а – х2500; б – х5000 в – х10000
а б
Рисунок 5.16 – Осажденная фаза гидроксида меди на фоне сульфата натрия:
а – х5000; б – х20000
205
Экспериментальные исследования свежеосажденных образцов фаз методом электронной микроскопии позволяют установить влияние физико-химических факторов на характеристики осажденной фазы и выявить некоторые закономерности, имеющие практическое значение для процессов флотации и фильтрации. Так как коллоидные системы с моно- и тонкодисперсными частицами обладают большей устойчивостью, судя по микрофотографиям исследуемых осадков можно предположить, что системы с цинком, никелем, железом будут более устойчивы по сравнению с кобальт-и медьсодержащими системами. При этом, сопутствующие примесные фазы, отличающиеся от основной фазы морфологией, будут снижать устойчивость коллоидных систем. Осадки серии образцов № 2–4 идентичной морфологии имеют вид хлопьев, диаметр которых увеличивается в ряду: Ni–Zn–Co (за исключением гидроксида кобальта с фоновым электролитом нитрата натрия). После сушки хлопьевидные осадки приобретали вид ячеек с различной долей свободного сечения, которую предположительно определяет интермицеллярное содержимое.
Полученные данные представляют технологический интерес для процессов фильтрации (обезвоживании) полученных флотошламов на фильтр-прессах.
Проведены исследования структуры порошков TiO2, Ti3N4, Fe4C3, углеродных материалов ОУ-А, ОУ-Б с помощью конфокального микроскопа. Некоторые фотографии образцов при увеличении от 108 до 2147 представлены ниже. Исследованию подвергались порошки до использования их в процессах электрофлотационного извлечения. Фотографии на конфокальном микроскопе приведены на рисунках 5.17 – 5.20
и результаты рентгенофлуоресцентной спектрометрии на рисунках 5.21 и 5.22.
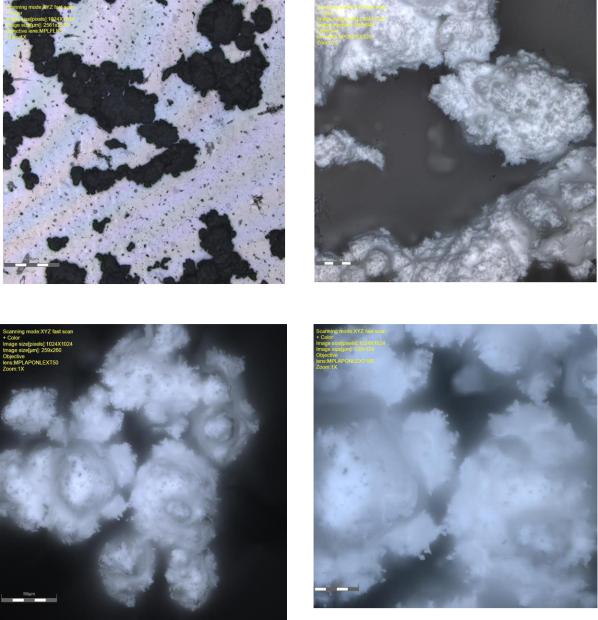
206
а |
б |
в г
Рисунок 5.17 – Фотографии на конфокальном микроскопе оксида титана:
а – х108; б – х429; в – х1069; г – х2147
Исследуя микрофотографии с увеличением 1069 можно отметить, что частицы оксида титана имеют плотную хлопьевидную структуру белого цвета с большим количеством неровностей, кратеров и пиков.
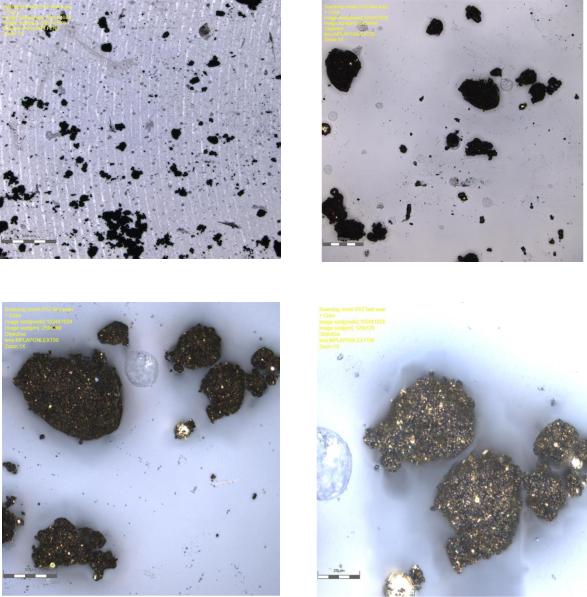
207
а |
б |
в г
Рисунок 5.18 – Фотографии на конфокальном микроскопе нитрида титана:
а – х108; б – х429; в – х1069; г – х2147
Частицы нитрида титана представляют собой сильношероховатые черные самородки с вкраплениями, обладающих золотистым блеском.
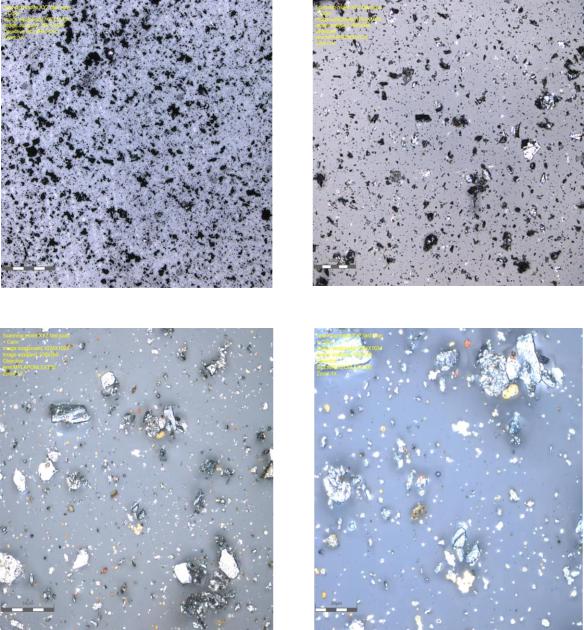
208
а |
б |
в г
Рисунок 5.19 – Фотографии на конфокальном микроскопе карбида железа:
а – х108; б – х429; в – х1069; г – х2147
При анализе микрофотографии с увеличением 1069 выявлено, что частицы карбида железа характеризуются острыми формами и сильно отличающимися размерами.
Присутствует сильный металлический блеск.
Исследование морфологии оксида скандия поверхности осуществляли с помощью сканирующего электронного микроскопа (СЭМ) JEOL 1610LV с энергодисперсионным спектрометром для электронно-зондового микроанализа SSD X-Max Inca Energy (JEOL,
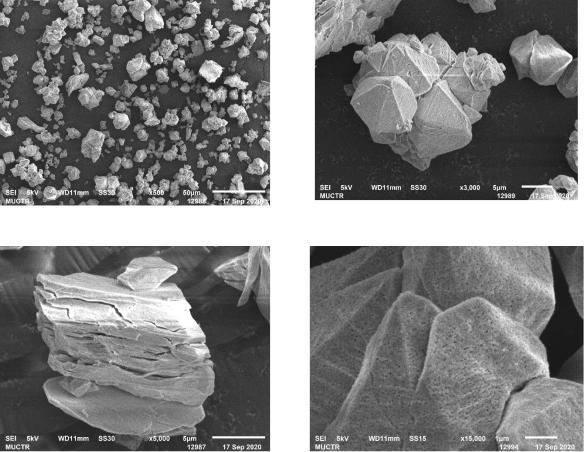
209
Япония; Oxford Instruments, Великобритания) в Центре коллективного пользования
(ЦКП) им. Д. И. Менделеева.
а |
б |
в г
Рисунок 5.20 – Фотографии на конфокальном микроскопе оксида скандия:
а – х100; б – х1000; в – х5000; г – х15000
При 1000-кратном увеличении установлено, что кристаллы оксида скандия имеют четко выраженную пирамидальную форму, преимущественно присутствуют частицы одного размера. При увеличении в 15 000 раз была обнаружена пористая структура пирамидальных частиц.
Представлены результаты рентгенофлуоресцентной спектрометрии неорганических порошков, выполненной на энергодисперсионном спектрометре EDX-
7000, характеризующие химический состав.
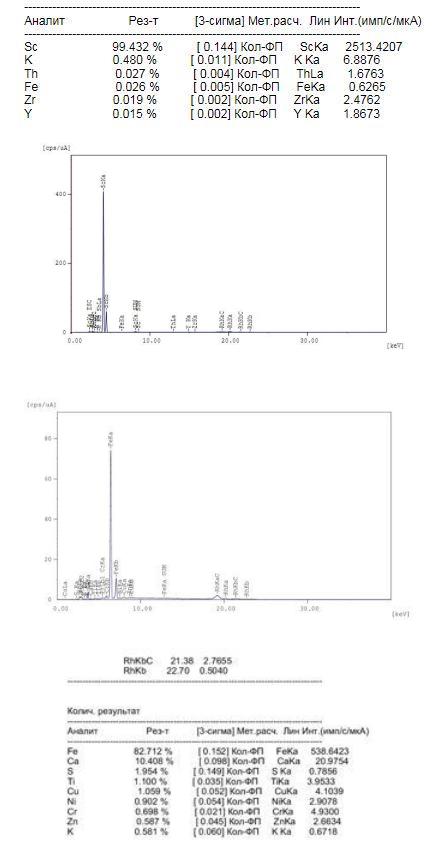
210
Рисунок 5.21 – Результаты рентгенофлуоресцентной спектрометрии оксида скандия
Рисунок 5.22 – Результаты рентгенофлуоресцентной спектрометрии карбида железа
211
Анализ образцов, морфологические исследования TiO2, TiN, FeCx, SiC и Sc2O3
показали, что, в отличие от гидроксидов, структура исследованных порошков – это отдельные частицы, гранулы, спеченные осадки и кристаллы различной формы.
Основной размер частиц 5–10 мкм. Вероятность закрепления пузырьков водорода или кислорода в процессе ЭФ извлечения невысокая, поэтому степень извлечения не превышает 5–15%. На указанных выше порошках наблюдается низкая адсорбция флокулянтов и ПАВ, что не позволяет интенсифицировать процесс электрофлотации.
Положительный эффект достигается если в систему H2O – порошок – электролит вводится дисперсная фаза коагулянта (Fe, Al), имеющая хлопьевидную рыхлую структуру, которая позволяет легко захватывать пузырьками H2 и О2 в ЭФ процессе.
Экспериментальные доказательства приведены в подразделе 4.2.
212
6.Технологический инжиниринг. Опытно-промышленная реализация
6.1.Промышленное испытание электрофлотационных, микрофильтрационных
исорбционных модулей очистки сточных вод гальванических производств
производительностью 1, 5 и 10 м3/ч
Для разработки высокоэффективных систем очистки сточных вод проведен анализ пяти методов разделения, часто применяемых на практике. Подробности применения и работы установок для извлечения взвешенных веществ изложены в обзорах и монографиях [5, 7, 14].
В таблице 6.1 представлены важные для проектировщиков показатели эффективности методов разделения фаз при разработке систем водоочистки от взвешенных веществ, ПАВ и нефтепродуктов.
Таблица 6.1 – Сравнительные данные эффективности очистки сточных вод от взвешенных веществ методами разделения фаз
Показатели |
|
|
|
|
Методы разделения |
|
|||
|
|
ЭФ |
НФ |
ЭК + С |
УФ (МФ) |
С |
|||
|
|
|
|
||||||
Степень |
извлечения, |
% |
|
|
|
|
|
||
взвешенных веществ |
|
95 |
90–95 |
80–90 |
95–99 |
50–70 |
|||
Ø>100 мкм |
|
|
|
|
|
|
|
||
Степень извлечения, % |
|
|
|
95–99 |
|
||||
∑ гидроксидов металлов |
90–95 |
30–50 |
70–80 |
30–60 мин |
|||||
(промывка) |
|||||||||
Ø<50 мкм |
|
|
|
|
|
|
|||
|
|
|
|
|
|
|
|||
Обработка |
объемов |
≥ 10 |
10–100 |
≥ 10 |
без |
1–100 |
|||
воды, м3/ч |
|
|
ограничения |
||||||
Объем |
полученного |
|
|
|
|
|
|||
осадка, % от объема |
0,1–0,5 |
0,5–1,0 |
15–20 |
10–20 |
17–18 |
||||
очищенной воды |
|
|
|
|
|
|
|||
Вторичное загрязнение |
отсутст- |
отсутст- |
коагулянты |
отсутствует |
коагулянты Fe, Al |
||||
вует |
вует |
Fe, Al |
|||||||
|
|
|
|
|
|
||||
Влажность осадка |
|
92–96 |
92–96 |
98–99 |
98–99,8 |
98–99,8 |
|||
Время разделения, мин |
5–10 |
15–30 |
30–40 |
30–40 |
30–120 |
||||
Удельный |
расход |
|
|
|
|
|
|||
электроэнергии, |
|
Q, |
0,1–0,5 |
0,3–0,7 |
1–2 |
1,5–3,0 |
0,1–0,4 |
||
кВт ч/м3 |
|
|
|
|
|
|
|
|
|
Размер пузырьков, мкм |
15 – 40 |
50 – 100 |
30 – 40 |
- |
- |
||||
|
|
|
|
Флоку- |
Коагулянт |
|
|
Флокулянт |
|
|
|
|
|
лянт |
|
|
|||
Вид реагента |
и |
его |
(10 – 30) |
Коагулянт |
Флокулянт |
(5 – 10) |
|||
(1 – 5) |
|||||||||
концентрация, г/м3 |
|
Флок. |
(30 – 50) |
(1 – 5) |
Коагулянт |
||||
|
ПАВ |
||||||||
|
|
|
|
(5 – 10) |
|
|
(30 – 50) |
||
|
|
|
|
(1 – 5) |
|
|
|||
|
|
|
|
|
|
|
|
||
|
|
|
|
Коагу- |
Коагулянт |
|
|
|
|
Новая |
композиция |
лянт |
(20 – 50) |
*Расход |
* Промывка |
*Фильтр-пресс для |
|||
[коагулянт + ПАВ] |
|
(10 – 20) |
ПАВ - 10 |
анода |
фильтра |
осадка |
|||
|
|
|
|
ПАВ – 5 |
|
|
|
|
|
Дополнительное |
|
- |
- |
Отстойник |
Отстойник |
Флокулятор |
|||
оборудование |
|
|
Центрифуга |
Центрифуга |
|||||
|
|
|
|
|
213 * - ЭФ – электрофлотация; НФ – напорная флотация; ЭК + С – электрокоагуляция +
седиментация; УФ (МФ) – ультра (микро) фильтрация; С – Седиментация
К достоинствам флотационных методов следует отнести возможность извлечения загрязняющих компонентов из сточных вод, тогда как мембранные методы (микро- и
ультрафильтрация) концентрируют загрязняющие компоненты и требуют применения дополнительных методов разделения (седиментация, центрифугирование).
Электрофлотационная технология позволяет извлекать более мелкие дисперсные частицы (<50 мкм) по сравнению с напорной флотацией, нет вторичного загрязнения воды и высокая эффективность процесса по сравнению с электрокоагуляцией, невысокий расход реагентов и электроэнергии.
На основании проведенных исследований определены направления, где электрофлотационная технология обеспечивает высокую эффективность извлечения порошков оксидов, нитридов и карбидов титанапорошкообразных углеродных материалов (ОУ-А, ОУ-Б), свежесформированных осадков гидроксидов, фосфатов и сульфидов металлов, а также органических соединений и композиций. Обобщенные данные представлены в таблице 6.2.
214
Таблица 6.2 – Эффективность электрофлотационной очистки сточных вод сложного
состава в присутствии различных добавок
|
|
|
|
|
|
|
Степень извлечения, α, % |
||||
Загрязнение в воде |
|
|
|
|
|
|
|
Коаг. |
композиция «ПАВ |
||
|
|
Флок. |
|
ПАВ |
|
|
+ коаг.» |
||||
|
|
|
|
|
|
(Fe, Al) |
|
||||
|
|
|
|
|
|
|
|
|
|
(Fe, Al, ОУ-Б) |
|
|
|
|
|
|
|
|
|
|
|
|
|
Взвешенные |
вещества |
(оксиды |
50–60 |
|
60–70 |
|
70–80 |
|
95–99 |
||
металлов (Ti, Sc, Y), ОУ-Б) |
|
|
|
|
|||||||
|
|
|
|
|
|
|
|
|
|||
Гидроксиды ∑Ме (Cu, Ni, Zn, Al, Cr, |
90–95 |
|
95–98 |
|
90–92 |
|
98–99 |
||||
Fe, Cd) |
|
|
|
|
|
|
|||||
|
|
|
|
|
|
|
|
|
|
|
|
Фосфаты, сульфиды (Cu, Ni, Zn) |
|
80–90 |
|
80–90 |
|
90–95 |
|
95–98 |
|||
Растворители, |
|
эмульсии, |
|
|
|
|
|
|
|
|
|
нефтепродукты, СОЖ |
|
|
50–60 |
|
50–60 |
|
80–90 |
|
90–95 |
||
(ХПК) |
|
|
|
|
|
|
|
|
|
|
|
Ca2+, Mg2+, Ba2+ PO43-, OH- |
|
70–80 |
|
70–80 |
|
85–95 |
|
90–95 |
|||
Растворимые |
орг. вещества |
+ |
30–40 |
|
50–60 |
|
80–90 |
|
90–95 |
||
∑Me(OH)2 |
|
|
|
|
|
|
|||||
|
|
|
|
|
|
|
|
|
|
|
|
Me – L |
|
|
|
40–60 |
|
80–90 |
|
80–90 |
|
80–95 |
|
Условия эксперимента: |
c |
ВВ ≤ |
300 |
мг/л; |
ХПК ≤ |
2000 мгО/л; |
|||||
c ∑гидроксидов ≤ 300 мг/л; c Ca2+ / Mg2+ / Ba2+ ≤ 200 мг/л. |
|
|
|
||||||||
Из опыта работы на промышленных объектах высокая эффективность процесса |
|||||||||||
наблюдается для соотношений: |
|
|
|
|
|
|
|
|
|
||
ВВ: флокулянт |
|
|
|
- |
|
100 : (5–10) |
|
|
|||
ВВ: ПАВ |
|
|
|
|
- |
|
100 : (1–5) |
|
|
||
ВВ: коагулянт |
|
|
|
- |
|
100 : (5–20) |
|
|
|||
ВВ: коагулянт + ПАВ |
|
|
- |
|
100 : (5–10) : (5–10) |
|
|||||
ВВ: коагулянт + флокулянт |
|
|
- |
|
100 : (5–10) : (1–5) |
|
|||||
ВВ: коагулянт + ПАВ + флокулянт |
- |
|
100 : (10–20) : (5–10) : (1–5) |
Природа коагулянта, флокулянта и ПАВ для различных систем определены в результате тестирования сточных вод на лабораторных установках (состав реагентов представлен в разделе 2).
Как показали результаты исследования, предельная концентрация по взвешенным веществам не более 500 мг/л, в ряде случаев (фильтраты полигонов) достигает
1000–1200 мг/л.
215
В таблице 6.3 представлены результаты исследования применения промышленного анионного ПАВ МТМх в электрофлотационном процессе извлечения смеси гидроксидов металлов из сточных вод. Подробно характеристика ПАВ, МТМх приведена в разделе 2.
Таблица 6.3 – Влияние рН раствора на степень извлечения ∑Ме(ОН)2 из водного раствора
Na2SO4 в присутствии промышленного анионного ПАВ (МТМх)
рН |
|
Степень извлечения ∑Ме(ОН)2, α, % |
|
||
раствора |
|
|
|
|
|
Cu |
Ni |
Zn |
Co |
Fe |
|
|
|
|
|
|
|
8 |
97 |
91 |
95 |
88 |
88 |
|
|
|
|
|
|
9 |
72 |
83 |
98 |
97 |
88 |
|
|
|
|
|
|
10* |
97 |
98 |
98 |
98 |
84 |
|
|
|
|
|
|
11 |
98 |
98 |
99 |
98 |
73 |
|
|
|
|
|
|
Условия эксперимента: c Na2SO4 – 1 г/л; c∑ Ме(ОН)2 – 100 мг/л; с МТМх – 5 мг/л;
Jv – 0,4 А/л; τ– 20 мин.
Проведенные исследования с промышленным ПАВ показали, что при добавлении анионного ПАВ МТМх в соотношении ∑Me:ПАВ – 100:(1–10) эффективность извлечения составляет 98 – 99%, время процесса не более 10 мин (α5 – 90%). Наиболее эффективно процесс протекает при рН = 10, которое часто используют для очистки сточных в гальванохимических производств.
Наиболее сильное влияние ПАВ проявляется в сточных водах в присутствии лигандов, например, аммиачных растворов. Экспериментальные результаты по влиянию промышленных ПАВ на ЭФ извлечение гидроксидов Cu, Ni, Zn, Co, Fe из аммиачных растворов представлены в подразделе 6.2.
Проведена оценка эффективности работы электрофлотационного модуля с различной степенью очистки 1 (α = 0), № 2 (α = 25%), № 3 (α = 50%), №4 (α = 95%) для очистки сточных вод сложного состава. Расчетные данные представлены в таблицах
6.4–6.7.

216
Таблица 6.4 – Основные параметры сточной воды (без электрофлотации). Степень
извлечения, α = 0
Параметр |
Исходная, pH = 7±0,5 |
Подщелачивание, pH = 10±0,5 |
|
|
|
м3/сут |
240,00 |
257,3 |
|
|
|
м3/ч |
10,00 |
10,7 |
|
|
|
температура |
25,0 |
25,0 |
|
|
|
Ni++Fe2+/3+ |
30,00 |
28 |
Ca2+ |
20,00 |
20 |
Mg2+ |
10,00 |
10,00 |
|
|
|
Cd2++Al3+ |
20,00 |
19 |
|
|
|
Na+ |
580,00 |
582,92 |
|
|
|
K+ |
10,8 |
10,80 |
|
|
|
SO42- |
1200 |
1200 |
|
|
|
Cl- |
120 |
120 |
|
|
|
PO43- |
15,00 |
14,3 |
|
|
|
CO32- |
0,00 |
0,00 |
|
|
|
HCO3- |
14,14 |
14 |
|
|
|
ХПК |
700,00 |
707 |
|
|
|
ПАВ |
30,00 |
30 |
|
|
|
oil & grease |
70,00 |
69 |
|
|
|
TSS |
150,00 |
144 |
|
|
|
TDS |
2020 |
2018 |
|
|
|
pH |
5,5 |
5,5 |
|
|
|
cations |
28,705 |
28,7 |
|
|
|
anions |
28,818 |
28,8 |
|
|
|
|
Для расчета использованы данные по усредненному анализу сточных вод одного |
||||
из |
машиностроительных |
предприятий |
г. |
Москвы. |
Производительность |
установки – 10 м3/ч. |
|
|
|
|
217
Таблица 6.5 – Основные параметры сточной воды (минимальная обработка). Степень
извлечения α = 25%
Параметр |
Вход |
Выход |
Шлам |
|
|
|
|
м3/сут |
257 |
244,45 |
12,87 |
|
|
|
|
м3/ч |
10,7 |
10,19 |
0,54 |
|
|
|
|
температура |
25,0 |
25,0 |
25,0 |
|
|
|
|
Ni++Fe2+/3+ |
28 |
5,60 |
453 |
Ca2+ |
20,00 |
20,00 |
20,0 |
Mg2+ |
10,00 |
10,00 |
10,0 |
|
|
|
|
Cd2++Al3+ |
19 |
3,74 |
302 |
|
|
|
|
Na+ |
623 |
623 |
623 |
|
|
|
|
K+ |
10,8 |
10,8 |
10,8 |
|
|
|
|
SO42- |
1200 |
1200 |
1200 |
|
|
|
|
Cl- |
120 |
120 |
120 |
|
|
|
|
PO43- |
14,34 |
10,25 |
92 |
|
|
|
|
CO32- |
43 |
10,65 |
32 |
|
|
|
|
HCO3- |
2,0 |
34,32 |
13 |
|
|
|
|
ХПК |
708 |
506 |
4540 |
|
|
|
|
ПАВ |
29 |
19,74 |
217 |
|
|
|
|
oil & grease |
69 |
49,26 |
441 |
|
|
|
|
TSS |
144 |
96 |
1056 |
|
|
|
|
TDS |
2090 |
2049 |
2877 |
|
|
|
|
pH |
10,65 |
9 |
9 |
|
|
|
|
cations |
30 |
29 |
50 |
|
|
|
|
anions |
30 |
29 |
30 |
|
|
|
|
Расчеты показывают формирование флотошлама при подщелачивании сточной
воды до рН = 10 ±0,5. Эффективность ЭФ невысокая и принята для расчетов α = 25%.
218
Таблица 6.6 – Основные параметры сточной воды (после электрофлотации). Степень
извлечения α = 50%
Параметр |
Вход |
Выход |
Шлам |
|
|
|
|
м3/сут |
244 |
232 |
12,2 |
|
|
|
|
м3/ч |
10,2 |
9,68 |
0,5 |
|
|
|
|
температура |
25,0 |
25,0 |
25,0 |
|
|
|
|
Ni++Fe2+/3+ |
5,60 |
2,80 |
59 |
Ca2+ |
20,00 |
20,00 |
20,0 |
Mg2+ |
10,00 |
10,00 |
10,0 |
|
|
|
|
Cd2++Al3+ |
3,7 |
1,87 |
39 |
|
|
|
|
Na+ |
623 |
623 |
623 |
|
|
|
|
K+ |
10,8 |
10,8 |
10,8 |
|
|
|
|
SO42- |
1200 |
1200 |
1200 |
|
|
|
|
Cl- |
120 |
120 |
120 |
|
|
|
|
PO43- |
10,2 |
5,12 |
107 |
|
|
|
|
CO32- |
10,6 |
6,55 |
20 |
|
|
|
|
HCO3- |
34,3 |
38 |
25 |
|
|
|
|
ХПК |
506 |
253 |
5313 |
|
|
|
|
ПАВ |
19,7 |
9,9 |
207 |
|
|
|
|
oil & grease |
49 |
24 |
517 |
|
|
|
|
TSS |
96 |
48 |
1008 |
|
|
|
|
TDS |
2048 |
2039 |
2234 |
|
|
|
|
pH |
9,13 |
9 |
9 |
|
|
|
|
cations |
30 |
29 |
31 |
|
|
|
|
anions |
30 |
29 |
30 |
|
|
|
|
Повышение степени извлечения в процессе электрофлотации приводит к снижению концентрации взвешенных веществ, гидроксидов и других труднорастворимых соединений металлов, а также органических загрязнений (ХПК).
219
Таблица 6.7 – Основные параметры сточной воды (после электрофлотации). Степень
извлечения α = 95%
Параметр |
Вход |
Выход |
Шлам |
|
|
|
|
м3/сут |
232,2 |
220,6 |
11,61 |
|
|
|
|
м3/ч |
9,7 |
9,19 |
0,48 |
|
|
|
|
температура |
25,0 |
25,0 |
25,0 |
|
|
|
|
Ni++Fe2+/3+ |
2,80 |
0,56 |
45 |
Ca2+ |
20,00 |
20,00 |
20,0 |
Mg2+ |
10,00 |
10,00 |
10,0 |
|
|
|
|
Cd2++Al3+ |
1,87 |
0,37 |
30 |
|
|
|
|
Na+ |
623 |
623 |
623 |
|
|
|
|
K+ |
10,8 |
10,8 |
10,8 |
|
|
|
|
SO42- |
1200 |
1200 |
1200 |
|
|
|
|
Cl- |
120 |
120 |
120 |
|
|
|
|
PO43- |
5,12 |
5,12 |
5,12 |
|
|
|
|
CO32- |
6,55 |
1,19 |
5,61 |
|
|
|
|
HCO3- |
38 |
43 |
39 |
|
|
|
|
ХПК |
253 |
101 |
3137 |
|
|
|
|
ПАВ |
10 |
2,0 |
159 |
|
|
|
|
oil & grease |
24 |
4,9 |
398 |
|
|
|
|
TSS |
48 |
5 |
869 |
|
|
|
|
TDS |
2038,9 |
2035 |
2109 |
|
|
|
|
pH |
9 |
8,35 |
8,35 |
|
|
|
|
cations |
29 |
29 |
31 |
|
|
|
|
anions |
29 |
29 |
29 |
|
|
|
|
При увеличении степени извлечения электрофлотации до 95% в сточной воде в основном остаются растворимые соли, взвешенные вещества и растворимые органические загрязнения присутствуют при низкой концентрации.
В таблице 6.8 приведены экспериментальные расчетные данные по эффективности работы модулей микрофильтрации, ультрафильтрации и сорбции.
220
Таблица 6.8 – Основные параметры сточной воды после микрофильтрации,
ультрафильтрации и сорбции
Параметр |
Микрофильтрация |
|
Ультрафильтр |
|
Сорбционный фильтр |
||||
|
|
|
|
|
|
|
|
|
|
|
вход |
выход |
шлам |
вход |
выход |
шлам |
вход |
выход |
шлам |
|
|
|
|
|
|
|
|
|
|
м3/сут |
220,6 |
209,59 |
11,03 |
209,5 |
203,3 |
6,29 |
203,30 |
193,13 |
10,16 |
|
|
|
|
|
|
|
|
|
|
м3/ч |
9,19 |
8,73 |
0,46 |
8,73 |
8,47 |
0,26 |
8,47 |
8,05 |
0,42 |
|
|
|
|
|
|
|
|
|
|
температ. |
25,0 |
25,0 |
25,0 |
25,0 |
25,0 |
25,0 |
25,0 |
25,0 |
25,0 |
|
|
|
|
|
|
|
|
|
|
Ni++Fe2+/3+ |
0,56 |
0,56 |
0,56 |
0,56 |
0,56 |
0,56 |
0,56 |
0,56 |
0,56 |
Ca2+ |
20,00 |
20,00 |
20,0 |
20,00 |
20,00 |
20,0 |
20,00 |
20,00 |
20,0 |
|
|
|
|
|
|
|
|
|
|
Mg2+ |
10,00 |
10,00 |
10,0 |
10,00 |
10,00 |
10,0 |
10,00 |
10,00 |
10,0 |
Cd2++Al3+ |
0,37 |
0,37 |
0,37 |
0,37 |
0,37 |
0,37 |
0,37 |
0,37 |
0,37 |
|
|
|
|
|
|
|
|
|
|
Na+ |
623 |
623 |
623 |
623 |
623 |
623 |
623 |
623 |
623 |
|
|
|
|
|
|
|
|
|
|
K+ |
10,8 |
10,8 |
10,8 |
10,8 |
10,8 |
10,8 |
10,8 |
10,8 |
10,8 |
SO42- |
1200 |
1200 |
1200 |
1200 |
1200 |
1200 |
1200 |
1200 |
1200 |
|
|
|
|
|
|
|
|
|
|
Cl- |
120 |
120 |
120 |
120 |
120 |
120 |
120 |
120 |
120 |
|
|
|
|
|
|
|
|
|
|
PO43- |
5,12 |
5,12 |
5,12 |
5,12 |
5,12 |
5,12 |
5,12 |
5,12 |
5,12 |
|
|
|
|
|
|
|
|
|
|
CO32- |
1,19 |
1,19 |
1,19 |
1,19 |
1,19 |
1,19 |
1,19 |
1,19 |
1,19 |
|
|
|
|
|
|
|
|
|
|
HCO3- |
43,5 |
43,53 |
43,53 |
43,5 |
43,53 |
43,53 |
43,53 |
43,53 |
43,53 |
|
|
|
|
|
|
|
|
|
|
ХПК |
101 |
101 |
101 |
101 |
40 |
2064 |
40 |
8 |
656 |
|
|
|
|
|
|
|
|
|
|
ПАВ |
1,97 |
0,79 |
24,48 |
0,79 |
0,08 |
23,77 |
0,08 |
0,03 |
0,98 |
|
|
|
|
|
|
|
|
|
|
oil&grease |
4,93 |
1,97 |
61,08 |
1,97 |
0,79 |
40,19 |
0,79 |
0,32 |
9,77 |
|
|
|
|
|
|
|
|
|
|
TSS |
5 |
0 |
87 |
0 |
0 |
14 |
0 |
0 |
1 |
|
|
|
|
|
|
|
|
|
|
TDS |
2034,9 |
2034,9 |
2035 |
2034,9 |
2034,9 |
2035 |
2034,9 |
2034,9 |
2035 |
|
|
|
|
|
|
|
|
|
|
pH |
8,35 |
8,35 |
8,35 |
8,35 |
8,35 |
8,35 |
8,35 |
8,35 |
8,35 |
|
|
|
|
|
|
|
|
|
|
cations |
29,24 |
29,24 |
29,24 |
29,24 |
29,24 |
29,24 |
29,24 |
29,24 |
29,24 |
|
|
|
|
|
|
|
|
|
|
anions |
29,24 |
29,24 |
29,24 |
29,24 |
29,24 |
29,24 |
29,24 |
29,24 |
29,24 |
|
|
|
|
|
|
|
|
|
|
Расчетные данные показывают, что основные загрязняющие воду вещества удалены с использованием ЭФ, МФ, УФ и С. ЭФ модуль при степени извлечения 95%
обеспечил высокую эффективность работы последующих мембранных и сорбционных модулей. Проведен анализ сточной воды после стадии обессоливания.
221
Таблица 6.9 – Основные параметры очищенной воды после обратного осмоса
Параметр |
Вход |
Выход |
Шлам |
м3/сут |
193,1 |
135,1 |
57,9 |
м3/ч |
8,05 |
5,63 |
2,4 |
температура |
25,0 |
25,0 |
25,0 |
Ni++Fe2+/3+ |
0,56 |
0,00 |
1,9 |
Ca2+ |
20,00 |
0,10 |
66,4 |
Mg2+ |
10,00 |
0,05 |
33,2 |
Cd2++Al3+ |
0,37 |
0,00 |
1,24 |
Na+ |
623 |
6 |
2065 |
K+ |
10,8 |
0,09 |
35 |
SO42- |
1200 |
11 |
3975 |
Cl- |
120 |
1,08 |
397 |
PO43- |
5,12 |
0,05 |
17 |
CO32- |
1,19 |
0,00 |
5 |
HCO3- |
43,5 |
0,12 |
142 |
ХПК |
8 |
0 |
27 |
ПАВ |
0,03 |
0,00 |
0,10 |
oil & grease |
0,32 |
0,00 |
1,04 |
TSS |
0 |
0 |
0 |
TDS |
2034 |
17 |
6740 |
pH |
8,35 |
6 |
8,23 |
cations |
29,24 |
0,26 |
96 |
anions |
29,24 |
0,26 |
96 |
Вода, прошедшая очистку с использованием комплекса установок, представленных выше, обеспечивает качество воды по ГОСТ 9.314 3-я категория и может быть возвращена в гальваническое производство, производство печатных плат и на участок анодного оксидирования алюминия.
Проведенные расчеты показывают изменение состава сточной воды на каждой стадии технологического процесса, количество извлекаемых взвешенных веществ
(шлам), количество концентрата солевых компонентов и пермеат для возврата воды в технологический процесс.
Повышение степени извлечения взвешенных веществ в электрофлотационном модуле (на 10–15%) обеспечивает более высокую эффективность работы всех модулей технологической схемы.
В таблице 6.10 представлены расчеты снижения нагрузки на модуль микрофильтрации и модуль сорбции при различных значениях эффективности (α, %)
работы электрофлотационного модуля (50%, 75%, 95%).
222
Таблица 6.10 – Снижение нагрузки на модуль микрофильтрации и модуль сорбции при
различной эффективности работы модуля электрофлотации
|
Микрофильтрация |
|
|
Сорбция |
|
|||||
Параметр |
|
ВВ, скон. мг/л |
|
|
ХПК, скон. мгО/л |
|
||||
|
*100 |
|
50 |
25 |
5 |
|
**500 |
250 |
100 |
50 |
Эффективность |
0 |
|
50 |
75 |
95 |
|
0 |
50 |
80 |
90 |
электрофлотации, α, % |
|
|
||||||||
|
|
|
|
|
|
|
|
|
|
|
Количество промывок в |
8–10 |
4–6 |
2–3 |
1 |
|
– |
– |
– |
– |
|
час |
|
|||||||||
|
|
|
|
|
|
|
|
|
|
|
Замена угля красит. |
|
|
|
|
|
|
|
|
|
|
[0,2 кг/кг] |
– |
|
– |
– |
– |
|
10 |
20 |
50 |
100 |
Периодичность |
|
|
дней |
дней |
дней |
дней |
||||
|
|
|
|
|
|
|||||
1 раз в / дней |
|
|
|
|
|
|
|
|
|
|
Замена угля орг. |
|
|
|
|
|
|
|
|
|
|
[0,4 кг/кг] |
– |
|
– |
– |
– |
|
20 |
40 |
100 |
200 |
Периодичность |
|
|
дней |
дней |
дней |
дней |
||||
|
|
|
|
|
|
|||||
1 раз в / дней |
|
|
|
|
|
|
|
|
|
|
|
Количество загрязнений |
|
|
|
|
|||||
[кг/час] |
1,0 |
|
0,5 |
0,25 |
0,05 |
|
5 |
2,5 |
1,0 |
0,5 |
[кг/сутки] |
24 |
|
12 |
6 |
1,2 |
|
120 |
60 |
24 |
12 |
[кг/10 дней] |
240 |
|
120 |
60 |
12 |
|
1200 |
600 |
240 |
120 |
* - с исх ВВ – 100 мг/л; * – с исх ХПК – 500 мгО/л.
Для расчета использовали следующие заданные параметры: производительность установок 10 м3/ч, 3-сменный режим работы (24 ч), сорбционный фильтр с загрузкой БАУ
2400 кг, максимальная емкость угля по красителю – 0,2 кг/кг угля и растворителя
(0,4 кг/кг угля) (экспериментальные данные). Промывка осуществлялась при давлении
0,8–1,4 бар, при концентрации взвешенных веществ 5–10 мг/л и мутности NTU 20–40 ед. 1 раз в час. Время промывки 45–60 с. При увеличении концентрации загрязняющих веществ частота промывок увеличивается.
Анализ показывает, что в зависимости от эффективности очистки воды (степень извлечения α – 95%) промывка фильтра проводится в стандартном режиме фильтра 1 раз в час; При степени извлечения 75% – 2–3 раза; при α – 50% 4–6 раз в час.
При эффективности очистки от органических загрязнений на ЭФ модуле с добавкой сорбентов (Al(OH)3, ОУ-Б) при степени извлечения 90% замена загрузки угля БАУ при максимальной сорбционной емкости 0,2 кг орг. вещ-ва/кг угля проводится 1 раз в 100 дней; при α – 50% 1 раз в 20 дней. При максимальной сорбции 0,4 г орг. вещ-ва/кг угля время до полной замены возрастает в 2 раза.
223
Полученные результаты использованы при проведении испытаний и промышленной эксплуатации установок для очистки воды.
В период с 2017–2019 гг. изготовлены и проведены испытания комплексных установок производительностью 1 м3/ч, 5 м3/ч и 10 м3/ч. Для испытания разработаны программы и методики:
- проведения лабораторных исследований по очистке промывных и сточных вод, а
также отработанных технологических растворов по сложным, 5–6-компонентным системам в присутствии комплексообразователей, ПАВ и органических растворов
(гальваническое производство); - проведения лабораторных исследований по очистке промывных и сточных вод, а
также отработанных технологических растворов по системам медь, никель, олово, свинец
(производство печатных плат);
-проведения лабораторных исследований поведения дисперсной фазы алюминия и органических красителей;
-проведения лабораторных исследований по межфазным явлениям и их роль в процессах флотации, фильтрации и сорбции (заряд, размер частиц), в том числе с применением лазерных анализаторов характеристик частиц субмикронного и нанодиапазона «Photocor Compact» и «Analysette NanoTec»;
-проведения апробации модулей водоподготовки, водоочистки и обессоливания
воды.
Рассмотрим результаты испытания экспериментальных образцов установок производительностью 1 м3/ч, 5 м3/ч и 10 м3/ч. Для испытания использованы сточные воды,
содержащие взвешенные вещества, ионы тяжелых и цветных металлов, органические загрязнения, неорганические соли, хлориды, сульфаты. Состав сточной воды приведен в таблицах 6.12–6.14. Электрофлотационные аппараты для испытаний представлены на рисунке 6.1.
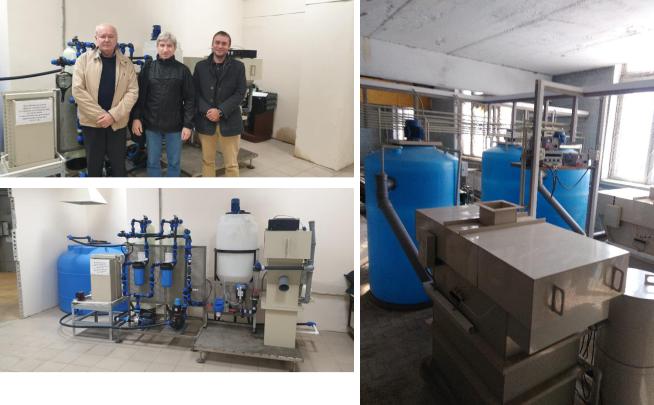
224
Рисунок 6.1 – Электрофлотационные аппараты для испытаний Принципиальная схема экспериментального образца установки для очистки
промывных и сточных вод, производительностью 5 м3/ч и представлена на рис 6.2,
спецификация базового оборудования дана в таблице 6.11. При проведении испытаний готовились растворы с заданными значениями исходных концентраций c0. для 3-х типов,
загрязняющих веществ, суммы ионов тяжелых и цветных металлов (Cu, Fe, Zn, Ni, Cd)
для взвешенных веществ (∑ гидроксидов цветных металлов и органических загрязнений
(СОЖ, масло, ДТ).
Контроль концентраций проводили после ЭФ (с1), после механического фильтра
(с2) и после сорбционного фильтра (с3). Основные параметры очистки представлены в протоколе, приложенном ниже.
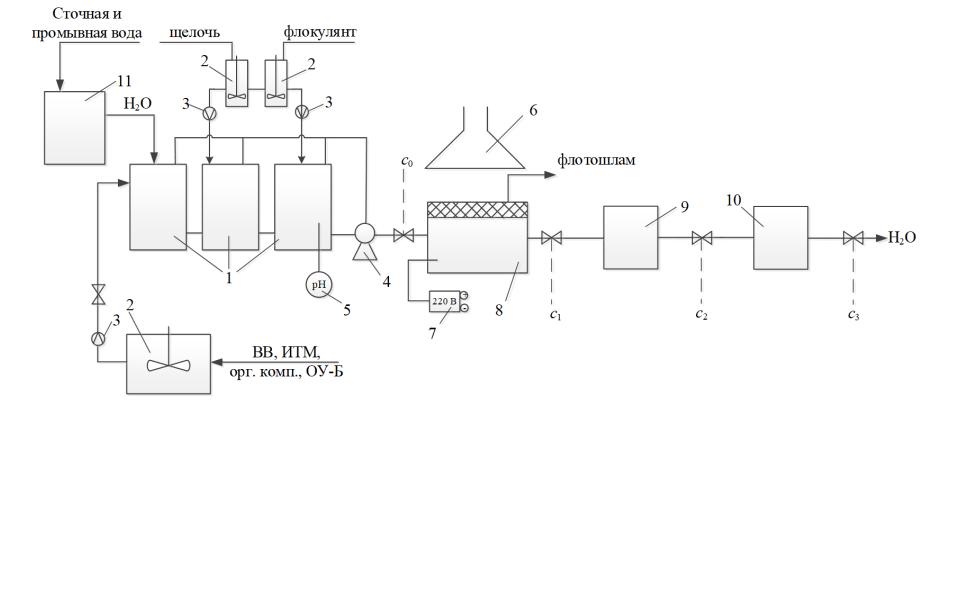
225
Рисунок 6.2 – Принципиальная схема экспериментального образца установки для очистки промывных и сточных вод
производительностью 5 м3/ч: 1 – емкость для воды; 2 – бак приготовления реагентов; 3 – насос-дозаторы; 4 – насос; 5 – рН-метр промышленный; 6 – вытяжной зонт-крышка; 7 – источник постоянного тока; 8 – электрофлотатор;
9 – фильтр механический; 10 – фильтр сорбционный, 11 – усреднитель (приемник) сточных вод п/я; С0,С1,С2,С3 – место отбора проб
|
|
|
|
226 |
|
|
|
Таблица 6.11 – Спецификация базового оборудования |
|
|
|||||
|
|
|
|
|
|||
|
№ по |
Наименование |
Характеристики, комплектация |
Кол-во, |
|||
|
схеме |
оборудования |
|
|
|
||
|
|
|
|
шт. |
|||
|
|
(установки, стенда) |
|
|
|
||
|
|
|
|
|
|
||
|
1 |
Емкость для |
воды |
Объем 1,5 м3, |
диаметр 1100 мм, высота |
3 |
|
|
|
(альтернатива) |
1800 мм |
|
|
||
|
|
|
|
|
|||
|
2 |
Бак приготовления |
Рабочий объем 30–150 л, полный объем |
|
|||
|
|
реагентов |
|
V= 170 л, материал полипропилен, |
3 |
||
|
|
|
|
мешалка 0,25 кВт, 750 об/мин, 650 мм |
|
||
|
3 |
Насос-дозаторы |
Подача 5 л/ч, напор 50 м, Etatron |
|
3 |
||
|
|
|
|
|
|
|
|
|
4 |
Насос |
|
Подача 5–10м3/ч, напор 15–35 м |
|
1 |
|
|
5 |
рН-метр |
|
Диапазон 0–14 рН, щитовое исполнение, |
1 |
||
|
|
промышленный |
релейный выход, выход 0–20 мА |
|
|||
|
|
|
|
||||
|
6 |
Вытяжной |
зонт- |
Для ЭФ аппарата |
|
1 |
|
|
|
крышка |
|
|
|
|
|
|
|
|
|
|
|
|
|
|
7 |
Источник |
|
Напряжение 0–12В (регулируемое), сила |
1 |
||
|
|
постоянного тока |
тока 0–100 А (регулируемая) |
|
|||
|
|
|
|
||||
|
8 |
Электрофлотатор |
Производительность 5 м3/ч (комплект |
|
|||
|
|
|
|
нерастворимых |
электродов, пеносборное |
1 |
|
|
|
|
|
устройство,). |
Габаритные |
размеры |
|
|
|
|
|
|
|||
|
|
|
|
1820 800 1600 мм (д ш в) |
|
|
|
|
9 |
Фильтр |
|
Насыпного типа, 1 колба 30", ручной |
|
||
|
|
механический |
|
управляющий клапан, дренажная система, |
1 |
||
|
|
|
|
фильтрующая |
|
загрузка. |
|
|
|
|
|
|
|
||
|
|
|
|
Производительность 1 колбы 5 м3/ч |
|
||
|
10 |
Фильтр |
|
Насыпного типа, 1 колба 30", ручной |
|
||
|
|
сорбционный |
|
управляющий клапан, дренажная система, |
1 |
||
|
|
|
|
сорбционная |
|
загрузка. |
|
|
|
|
|
|
|
||
|
|
|
|
Производительность 1 колбы 5 м3/ч |
|
||
|
11 |
Усреднитель |
|
Объем – 10 м3. |
|
|
|
|
|
(приемник) |
|
Примечание – находится на предприятии |
1 |
||
|
|
сточных вод п/я |
|
|
|
|
Таблица 6.12 – Экспериментальные результаты анализа сточной воды на содержание ионов тяжелых металлов до и после обработки в пилотном модуле
Время, мин |
|
Концентрация ∑ИТМ, мг/л |
|
|||
С0 |
С1 |
С2 |
С3 |
α,% |
||
|
||||||
0 |
100±10 |
- |
- |
- |
- |
|
30 |
100±10 |
10±2 |
3±0,5 |
1±0,5 |
99 |
|
60 |
100±10 |
7±1 |
2±0,5 |
1±0,5 |
99 |
|
120 |
100±10 |
5±1 |
2±0,5 |
<0,5 |
99 |
Условия эксперимента: τ – 0–120 мин; pH – 10 ± 0,5, c Na2SO4 – 0,5 г/л; c NaCl – 0,2 г/л; c
ПАА – 5 г/м3; I – 25 A; U – 26 В; Расход сточной воды – 5м3/ч.
227
Таблица 6.13 – Экспериментальные результаты анализа сточной воды на содержание
взвешенных веществ до и после обработки в пилотном модуле
Время, мин |
|
|
Концентрация ВВ, мг/л |
|
||
|
|
|
|
|
|
|
|
С0 |
С1 |
|
С2 |
С3 |
α,% |
|
|
|
|
|
|
|
0 |
150±10 |
- |
|
- |
- |
- |
|
|
|
|
|
|
|
30 |
150±10 |
15±2 |
|
2±0,5 |
<1 |
98±1 |
|
|
|
|
|
|
|
60 |
150±10 |
10±2 |
|
1,5±0,5 |
<1 |
99 |
|
|
|
|
|
|
|
120 |
150±10 |
10±2 |
|
1,0±0,5 |
<1 |
99 |
|
|
|
|
|
|
|
Условия эксперимента: τ – 0–120 мин; pH – 10 ± 0,5, c Na2SO4 – 0.5 г/л; c NaCl – 0,2 г/л; c ПАА – 5 г/м3; I – 25 A; U – 26 В; Расход сточной воды – 5 м3/ч.
Таблица 6.14 – Экспериментальные результаты анализа сточной воды на содержание органических соединений до и после обработки в пилотном модуле
Время, мин |
|
Концентрация органических соединений, ХПК, 0/л |
|
||||
|
|
|
|
|
|
|
|
|
С0 |
|
С1 |
С2 |
С3 |
|
α,% |
|
|
|
|
|
|
|
|
0 |
250±10 |
|
- |
- |
- |
|
- |
|
|
|
|
|
|
|
|
30 |
250±10 |
|
120±10 |
65±10 |
>10±2 |
|
96 |
|
|
|
|
|
|
|
|
60 |
250±10 |
|
100±10 |
50±5 |
>5±1 |
|
98 |
|
|
|
|
|
|
|
|
120 |
250±10 |
|
90±10 |
45±5 |
>5±1 |
|
99 |
|
|
|
|
|
|
|
|
Условия эксперимента: τ – 0–120 мин; pH = 10 ± 0,5, c Na2SO4 – 0,5 г/л; c NaCl – 0,2 г/л; c ПАА – 5 г/м3; I – 25 A; U – 26 В; Расход сточной воды – 5м3/ч.
Проведенные испытания показали высокую эффективность процесса очистки по ИТМ, ВВ и органическим загрязнениям.
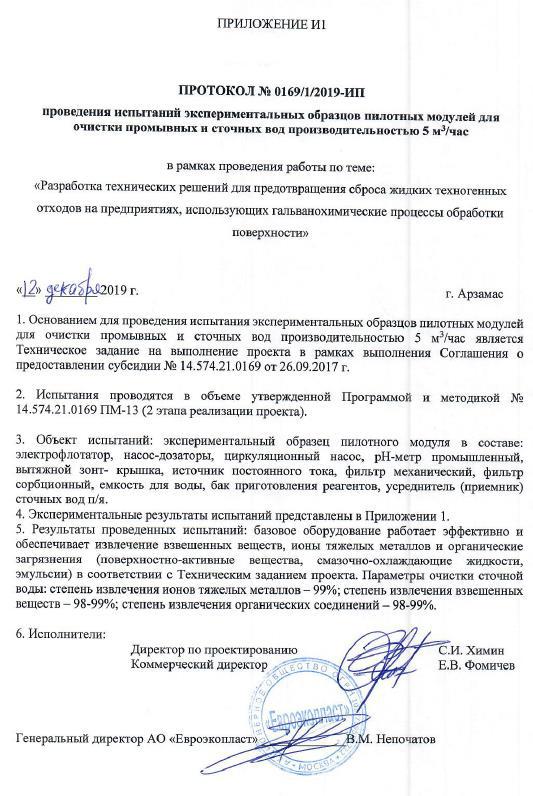
228
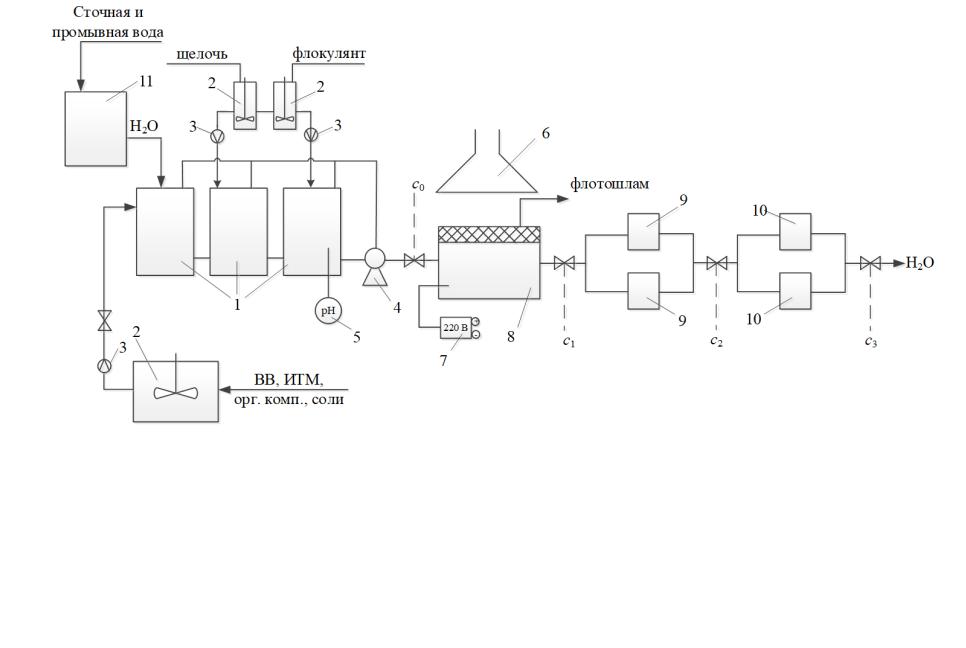
229
Рисунок 6.3 – Принципиальная схема экспериментального образца установки модуля для очистки промывных и сточных вод производительностью 10 м3/ч:
1 – емкость для воды;2 – бак приготовления реагентов; 3 – насос-дозаторы; 4 – насос; 5 – рН-метр промышленный; 6 – вытяжной зонт-крышка; 7 – источник постоянного тока; 8 – электрофлотатор;
9 – фильтр механический; 10 – фильтр сорбционный; 11 – усреднитель (приемник) сточных вод п/я; С0,С1,С2,С3 – место отбора проб
230
Аналогичные исследования проведены для установки производительностью 10 м3/ч. Принципиальная схема экспериментального образца установки модуля для очистки промышленных и сточных вод, производительностью 10 м3/ч представлена на рисунке 6.3. Спецификация базового оборудования установки для очистки сточных вод на 10 м3/ч представлена в таблице 6.15. Экспериментальные результаты очистки воды от ионов тяжелых металлов, взвешенных веществ, а также органических загрязнений представлены в таблице 6.16 – 6.18.
Таблица 6.15 – Спецификация базового оборудования
№ по |
Наименование |
Характеристики, комплектация |
Кол-во, |
|||
схеме |
оборудования |
|
|
|
||
|
|
|
шт. |
|||
|
(установки, стенда) |
|
|
|
||
|
|
|
|
|
||
1 |
Емкость для |
воды |
Объем 1,5 м3, диаметр 1100 мм, высота |
3 |
||
|
(альтернатива) |
1800 мм |
|
|
||
|
|
|
|
|||
2 |
Бак приготовления |
Рабочий объем 30–150 л, полный объем |
|
|||
|
реагентов |
|
V= 170 л, материал полипропилен, |
3 |
||
|
|
|
мешалка 0,25 кВт, 750 об/мин, 650 мм |
|
||
3 |
Насос-дозаторы |
Подача 5 л/ч, напор 50 м, Etatron |
|
3 |
||
|
|
|
|
|
|
|
4 |
Насос |
|
Подача 5–10м3/ч, напор 15–35 м |
|
1 |
|
5 |
рН-метр |
|
Диапазон 0–14 рН, щитовое исполнение, |
1 |
||
|
промышленный |
релейный выход, выход 0–20 мА |
|
|||
|
|
|
||||
6 |
Вытяжной |
зонт- |
Для ЭФ аппарата |
|
1 |
|
|
крышка |
|
|
|
|
|
|
|
|
|
|
|
|
7 |
Источник |
|
Напряжение 0–12 В (регулируемое), сила |
1 |
||
|
постоянного тока |
тока 0–100 А (регулируемая) |
|
|||
|
|
|
||||
8 |
Электрофлотатор |
Производительность 10 м3/ч (комплект |
|
|||
|
|
|
нерастворимых |
электродов, пеносборное |
1 |
|
|
|
|
устройство,). |
Габаритные |
размеры |
|
|
|
|
|
|||
|
|
|
2500 13001600 мм (д ш в) |
|
|
|
9 |
Фильтр |
|
Насыпного типа, 2 колбы 30", ручной |
|
||
|
механический |
|
управляющий клапан, дренажная система, |
2 |
||
|
|
|
фильтрующая |
|
загрузка. |
|
|
|
|
|
|
||
|
|
|
Производительность 1 колбы 5 м3/ч |
|
||
10 |
Фильтр |
|
Насыпного типа, 2 колбы 30", ручной |
|
||
|
сорбционный |
|
управляющий клапан, дренажная система, |
2 |
||
|
|
|
сорбционная |
|
загрузка. |
|
|
|
|
|
|
||
|
|
|
Производительность 1 колбы 5 м3/ч |
|
||
11 |
Усреднитель |
|
Объем – 10 м3 |
|
|
|
|
(приемник) |
|
Примечание – находится на предприятии |
1 |
||
|
сточных вод п/я |
|
|
|
|
231
Таблица 6.16 – Экспериментальные результаты анализа сточной воды на содержание
ионов тяжелых металлов до и после обработки в пилотном модуле
Время, мин |
|
|
Концентрация ∑ИТМ, мг/л |
|
||
С0 |
С1 |
|
С2 |
С3 |
α,% |
|
|
|
|||||
0 |
100±10 |
- |
|
- |
- |
- |
30 |
100±10 |
8±2 |
|
3±0,5 |
1±0,5 |
99 |
60 |
100±10 |
7±1 |
|
2±0,5 |
1±0,5 |
99 |
Условия эксперимента: pH = 10±0,5; c Na2SO4 – 0,5 г/л; c NaCl – 0,2 г/л; c ПАА – 5 г/м3; I – 50 A; U – 30 В; Расход сточной воды – 10 м3/ч.
Таблица 6.17 – Экспериментальные результаты анализа сточной воды на содержание взвешенных веществ до и после обработки в пилотном модуле
Время, мин |
|
|
Концентрация ВВ, мг/л |
|
||
С0 |
С1 |
|
С2 |
С3 |
α,% |
|
|
|
|||||
0 |
150±10 |
- |
|
- |
- |
- |
30 |
150±10 |
20±2 |
|
2±0,5 |
<1 |
98 |
60 |
150±10 |
18±2 |
|
2±0,5 |
<1 |
99 |
Условия эксперимента: pH = 10±0,5; c Na2SO4 – 0,5 г/л; c NaCl – 0,2 г/л; c ПАА – 5 г/м3; I = 50 A; U – 30 В; Расход сточной воды – 10 м3/ч.
Таблица 6.18 – Экспериментальные результаты анализа сточной воды на содержание органических соединений до и после обработки в пилотном модуле
Время, мин |
|
Концентрация органических соединений, ХПК, 0/л |
|
||||
С0 |
|
С1 |
С2 |
С3 |
|
α,% |
|
|
|
|
|||||
0 |
250±10 |
|
- |
- |
- |
|
- |
30 |
250±10 |
|
120±10 |
65±10 |
>5 |
|
98 |
60 |
250±10 |
|
100±10 |
50±5 |
>5 |
|
98 |
Условия эксперимента: pH = 10±0,5; c Na2SO4 – 0,5 г/л; c NaCl – 0,2 г/л, c ПАА – 5 г/м3; I – 50 A; U – 30 В; Расход сточной воды – 10 м3/ч.
Контроль основных параметров С1, С2 и С3 показывает низкие значения остаточных концентраций (высокие значения степени извлечения, α, %. Официальный протокол испытаний представлен ниже.
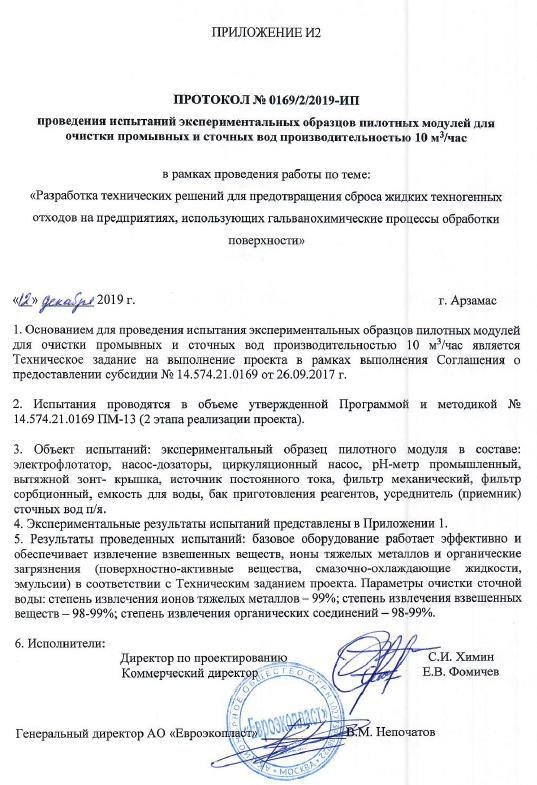
232
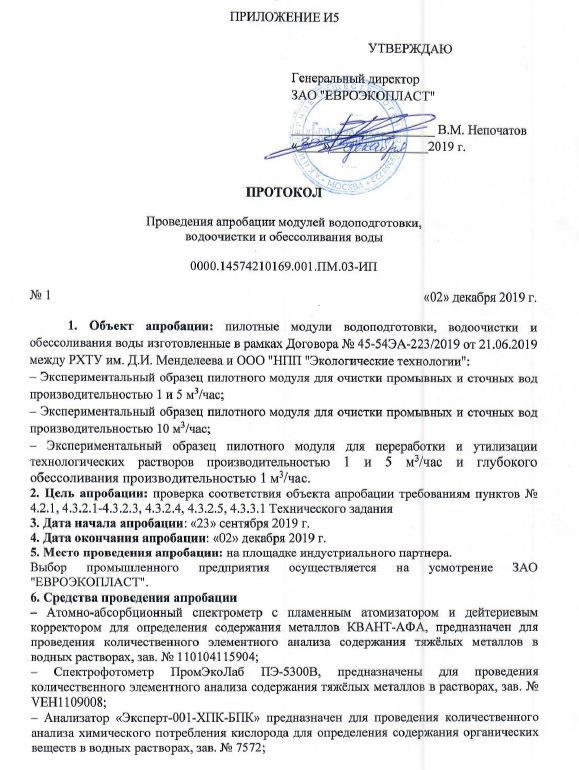
233
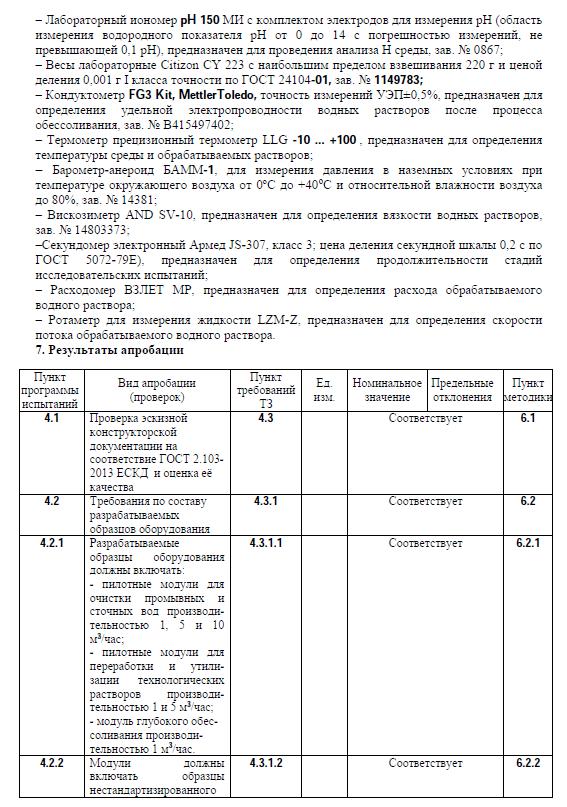
234
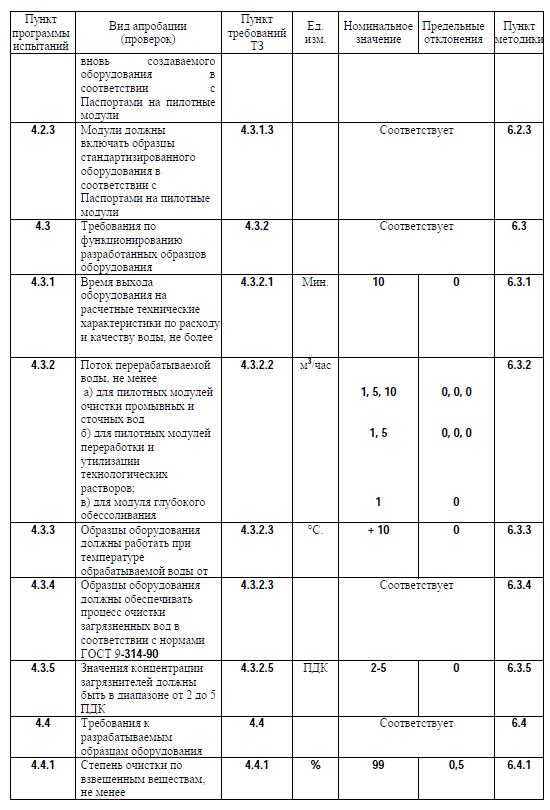
235
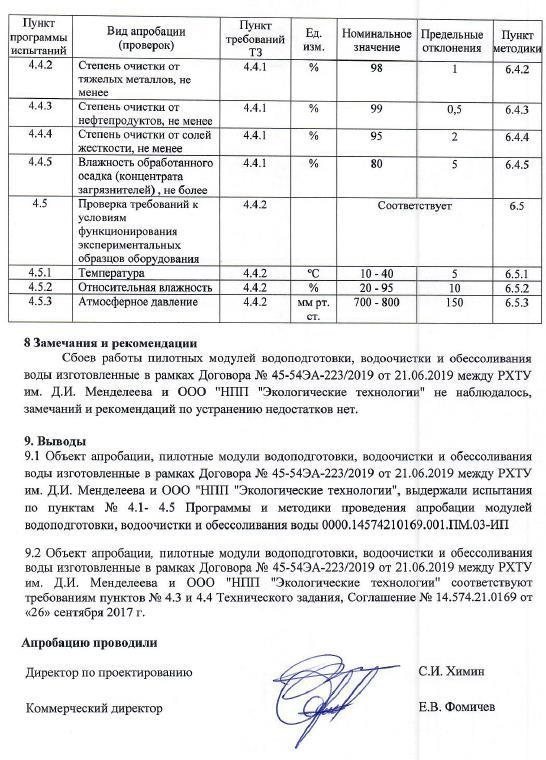
236
237
В приложении 1 представлены акты и протоколы проведения апробации модулей водоподготовки, водоочистки и обессоливания воды, проведенный в РХТУ им.
Менделеева индустриальным партнером АО «Евроэкопласт». От РХТУ им. Д. И.
Менделеева при испытании участвовали А.В. Колесников (автор работы), П.Н.
Кисиленко (изготовитель оборудования).
Результаты апробации по различным программам испытаний при контроле более чем 20 параметров представлены в протоколе и утверждены генеральным директором АО
«Евроэкопласт» Непочатовым В.М.
6.2. Современные очистные сооружения на базе электрофлотационных,
сорбционных и мембранных модулей очистки сточных вод сложного состава
Проведенный анализ сточных вод сложного состава, который часто встречается при гальванохимической обработке поверхности, показал, что наряду с токсичными ионами металлов (Cr, Cu, Zn, Ni, Ti, Al) в сточных водах присутствуют разнообразные органические соединения и, в зависимости от природы, их действия на ЭФ процесс различны.
Соединения, которые плохо растворимы в воде (эмульсии, СОЖ, нефтепродукты,
растворители, экстрагенты), как правило, оказывают положительное влияние на ЭФ процесс, степень извлечения гидроксидов меняется мало, при этом степень извлечения органических веществ достаточна высока (подраздел 3.2).
Вторая группа органических соединений, хорошо растворимая в воде,
адсорбируется на гидроксидных осадках, меняя поверхностные свойства дисперсной фазы. Ввиду высокой гидрофильности (спирты, гидрофильные красители) указанные соединения затрудняют ЭФ процесс извлечения гидроксидов железа, алюминия, меди.
Степень извлечения снижается при увеличении концентрации органического вещества.
более 1000 – 3000 мг/л.
Третья группа органических соединений и композиций типа Vigon, Zestron, Deccordal, Gardostrip и др., которые используются для обработки поверхности, оказывает наиболее сильное влияние на ЭФ процесс извлечения дисперсной фазы Cu, Ni, Fe, Al в
связи с образованием растворимых комплексов, в первую очередь с различными аминами
(моноэтаноламин, диэтиламин). Существенно снижают извлечение гидроксидов Cu, Ni,
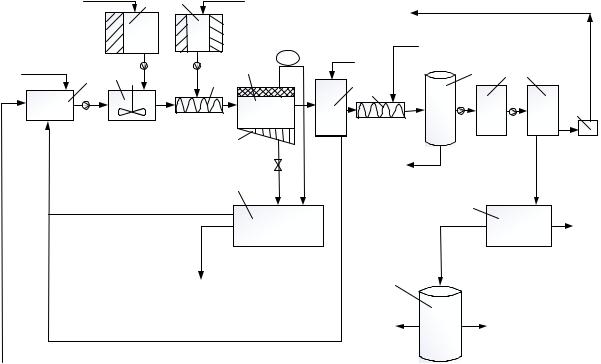
238
Zn, Cd, такие лиганды, как ЭДТА, тартрат, фосфоновая кислота, используемая в электролитах «ЭПИ-бесцианистая медь».
В работе определены два основных подхода к повышению эффективности ЭФ процесса в присутствии лигандов. Первый – это введение добавок катионных ПАВ – СептаПАВ – ХЭВ.50 или ХСВ70, которые увеличивают эффективность ЭФ в указанных системах. В первую очередь для ионов меди.
Второй подход – это сорбционное извлечение лигандов на порошках ОУ-Б, осадках
Al(OH)3 или композиции Al(OH)3 – ОУ-Б (раздел 3).
На рисунке 6.4 представлена базовая схема очистки сточных вод гальванохимического производства.
pH=2-3 |
pH=10-14 |
линия восстановления (Cr(III)), |
Окисление) линия Cu, Zn, Cd, |
Хром(VI) |
(CNЦиан |
|
)( |
|
- |
|
|
NaOH |
3 |
|
ПАВх |
|
Возврат H O (I класс) |
||
|
|
|
|
4 |
|
|
|
2 |
|
1)ВВ |
|
|
|
|
|
|
70-80 % |
||
|
|
|
|
|
|
|
|||
2) |
Me |
|
|
|
|
|
|
(Пермеат) |
|
) ХПК |
|
|
|
|
|
|
HCl |
|
|
4) |
Солей |
|
|
|
|
|
|
|
|
|
|
|
|
|
|
|
|
||
5) эмульсии |
|
|
|
|
ФШ |
H O |
|
|
|
|
|
|
|
2 |
|
|
|||
H O |
|
2 |
|
|
6 |
|
10 |
11 12 |
|
2 |
|
1 |
|
|
5 |
|
|
|
|
|
|
|
|
|
8 |
|
|
||
|
|
|
|
|
|
9 |
|
||
|
|
|
|
|
|
|
|
|
|
|
|
Q |
|
|
|
ЭФ |
|
|
13 |
|
|
|
|
|
|
|
|
||
|
|
|
|
|
|
|
|
|
|
|
|
|
pH=10±0.5 |
|
|
|
pH= ±0.5 |
|
|
|
|
|
|
|
|
|
|
|
|
|
|
|
|
|
|
осадок |
|
|
|
|
|
|
|
|
|
|
|
БАУ |
|
|
|
|
|
|
|
|
|
(обезвреживание) |
|
|
|
|
|
|
|
7 |
|
|
|
|
|
|
Фильтрат |
|
|
|
14 |
Раствор-концентрат |
|
|
|
|
|
|
|
|
|||
|
|
|
1 – 5% H O |
|
Ф.П. |
|
|
солей |
|
|
|
|
|
2 |
|
|
|
|
|
|
|
|
|
|
|
|
|
|
|
|
|
|
|
|
|
|
|
|
IV Класс (40-50 г/л) |
|
|
|
|
|
|
|
|
|
30% Q |
|
|
|
|
|
Гальваношлам |
|
15 |
|
|
|
|
|
|
|
|
|
|
||
|
|
|
|
|
(II Класс опасности |
|
|
|
|
|
|
|
|
|
|
ИТМ) |
Твердый отход |
|
|
|
|
|
|
|
|
|
Концентрат (жидкий отход) |
||
|
|
|
|
|
|
|
|
|
|
|
|
|
|
|
|
|
|
солей |
(100-150 г/л) |
|
|
|
|
|
|
|
|
|
|
|
|
|
|
1-5 % ВВ |
0,1 Q |
|
IV класс |
IV Класс |
|
|
|
|
|
|
|
||||
|
|
|
|
|
|
10% Q |
|||
|
|
|
|
|
|
|
|
|
Рисунок 6.4 – Базовая схема очистки кислотно-щелочных сточных вод гальванических производств с возвратом воды в технологический процесс: 1 – приемная емкость;
2 – реактор-нейтрализатор; 3 – емкость со щелочью; 4 – емкость с ПАВ;
5 – флокулятор; 6 – электрофлотатор; 7 – фильтр-пресс; 8 – микрофильтр; 9 – реактор-
нейтрализатор; 10 – сорбционный фильтр; 11 – установка ультрафильтрации;
12 – обратноосмотический модуль; 13 – емкость очищенной воды; 14 – емкость для концентрата; 15 – выпарная установка
Схема включает несколько основных модулей:

239
Модуль I – ЭФ, МФ и сорбция для удаления ВВ, эмульсий, гидроксидов металлов,
растворимых органических соединений.
Модуль II – обратноосмотический модуль концентрирования солевых компонентов с выпарной установкой для получения концентрата солей (твердых отходов) IV класса опасности (нет ИТМ).
Модуль III – фильтрация флотоконцентрата и суммы гидроксидов металлов
(гальваношлам II класса опасности).
Использование модулей I, II и III, включающих установки 6, 8, 10, 11, 12, 15
обеспечивают возврат воды 80–90% с извлечением солевых компонентов (хлориды,
сульфаты) и осадок гидроксидов, фильтраты с примесями ИТМ возвращаются в емкость
1 для обезвреживания.
С учетом полученных экспериментальных результатов в подразделе 3.2
разработана принципиальная схема очистки сточных вод производства печатных плат электронной техники с возвратом воды в технологический процесс (рисунок 6.5).
|
|
|
|
|
5 |
|
|
|
Осадок Cu, Sn, Pb, Ni, |
|
|
|
|
|
|
|
|
Ф.П. |
|
|
|
|
|
|
|
|
|
|
|
Гидроксиды Al |
|
|
|
|
|
|
|
|
|
|
|
ОУ-Б |
|
ИТМ, орг. компоненты, |
|
ИТМ |
|
|
4 |
(II-III Класс опасности) |
|
|||
|
(Cu, Ni, Sn, Fe, Pb) |
|
Al |
|
|
|||||
NH |
OH, растворители и др. |
|
|
|
|
|||||
|
|
|
|
|
|
|||||
4 |
|
|
|
|
|
|
|
|
|
|
|
|
|
|
|
|
|
Al(OH)2Cl |
ПАВа |
H O |
|
|
|
|
|
|
|
|
2 |
|
||
|
|
|
|
|
|
|
|
|
|
|
сточная вода |
|
NaOH |
2 |
3 |
|
+ |
|
7 |
8 |
|
1 |
6 |
H |
|
9 |
ЭФ1 |
pH=7-8 |
ЭФ2 |
МФ |
pH=9-10
1-5 % ВВ
|
|
Раствор солей |
|
|
(IV Класс опасности) |
ПАВк |
ОУ-Б |
|
СептаПАВ |
|
|
H O Возврат воды в технологический процесс |
||
2 |
|
|
|
0 – |
0% |
|
|
20 % H O |
|
|
2 |
|
|
дистиллят |
|
12 |
Вода очищенная |
|
|
Сор |
pH=7-8 |
|
|
|
|
|
|
|
ХПК<50 |
|
|
|
ИТМ < 1 мг/л |
|
|
pH=7-8 |
солей = 1 – |
г/л |
|
10 |
|
|
30 % |
О.О. |
|
|
(А) |
|
|
|
|
|
30 % |
|
|
концентрат |
|
|
11 |
|
|
|
|
Твердые отходы |
|
|
|
(IV Класс опасности) |
|
|
|
солей |
|
|
Рисунок 6.5 – Принципиальная схема очистки сточных вод производства печатных плат с водооборотом: 1 – емкость приема сточной воды; 2 – реактор-нейтрализатор;
3 – электрофлотатор; 4 – флотошлам; 5 – фильтр-пресс; 6 – емкость для коагуляции;
7 – ЭФ%; 8 – МФ; 9 – сорбционный фильтр; 10 – установка обратного осмоса;
11 – выпарная установка; 12 – емкость для воды
240
Особенность схемы заключается в использовании двух ЭФ аппаратов. Первый нужен для извлечения гидроксидов Cu, Ni, Co, Sn, Pb, Fe и др. ионов тяжелых металлов в присутствии в растворе лигандов NH3, ЭДТА, тартрат, амины и др. при pH=8–10 с
обязательным добавлением ПАВ катионного типа СептаПАВ или промышленного ПАВ ФЛОН-1 или смеси анионный ПАВ МТМх (20%) и катионный Флотон (80%). Степень извлечения гидроксидов достигает 95–98%.
Второй ЭФ служит для удаления флокулирующей композиции Al(OH)2Cl+ОУ-
Б+ПАВ. Указанная композиция обладает высокими параметрами сорбции органических загрязнений Vigon, Zestron, растворителей, спиртов и др., что снижает нагрузку на последующий сорбционный модуль с адсорбентом БАУ. Для модуля обессоливания используется установка обратного осмоса и локальная выпарная установка производительностью 1–2 м3/час.
Режим работы ЭФ1 и ЭФ2 отработан на установке 1, 5 и 10 м3/ч на сточной воде сложного состава. В сточных водах производства печатных плат широко применяются медно-аммиачные растворы травления с высокой концентрацией NH4OH.
При промывке изделий водой, при несанкционированном сбросе части отработанных растворов в сточной воде при концентрации NH4OH 100 – 500 мг/л
формируются аммиачные комплексы меди, цинка и других металлов. В таблице 6.19
приведены результаты влияния промышленного ПАВ МТМх(а).
Таблица 6.19 – Влияние рН раствора на степень извлечения ∑Ме(ОН)2 из водного раствора NH4OH в присутствии промышленного анионного ПАВ (МТМх)
рН |
|
Степень извлечения ∑Ме(ОН)2, α, % |
|
||
раствора |
|
|
|
|
|
Cu |
Ni |
Zn |
Co |
Fe |
|
|
|
|
|
|
|
8 |
98 /83* |
95 |
97 /55* |
94 |
82 |
|
|
|
|
|
|
9 |
97 /84* |
98 |
98/ 79* |
95 |
84 |
|
|
|
|
|
|
10* |
95/ 95* |
96 |
97 / 87* |
98 |
92 |
|
|
|
|
|
|
11 |
98 / 96* |
99 |
98 /98* |
99 |
97 |
|
|
|
|
|
|
Условия эксперимента: c NH4OH – 500 г/л; c∑ Ме(ОН)2 – 100 мг/л; с МТМх – 5 мг/л;
Jv – 0,4 А/л, τ – 20 мин.
* – без ПАВ (Cu, Zn).
Установлено, что в широком диапазоне рН степень извлечения комплексов Cu, Ni, Zn возрастает до 95–98%, что связано с гидрофобизацией поверхности за счет вытеснения
241
молекул воды и NH3. Аммиачные комплексы меди при рН 8–11 заряжены отрицательно,
можно ожидать, что добавление промышленных катионных ПАВ приведет к увеличению степени извлечения.
В таблице 6.20 представлены данные по влиянию промышленного катионного ПАВ Флон-1 на степень извлечения суммы гидроксидов металлов в сточной воде,
содержащей NH4OH.
Таблица 6.20 – Влияние рН раствора на степень извлечения ∑Ме(ОН)2 из водного раствора NH4OH в присутствии промышленного катионного ПАВ (Флон-1)
рН |
|
Степень извлечения ∑Ме(ОН)2, α, % |
|
||
раствора |
|
|
|
|
|
Cu |
Ni |
Zn |
Co |
Fe |
|
|
|
|
|
|
|
8 |
98 /83* |
98 |
98 /55* |
99 |
95 |
|
|
|
|
|
|
9 |
97 /84* |
95 |
91/ 79* |
93 |
94 |
|
|
|
|
|
|
10* |
99/ 95* |
95 |
90 / 87* |
90 |
91 |
|
|
|
|
|
|
11 |
94 / 96* |
98 |
99 /98* |
97 |
93 |
|
|
|
|
|
|
Условия эксперимента: c NH4OH – 500 г/л; c∑ Ме(ОН)2 – 100 мг/л; с МТМх – 5 мг/л;
Jv – 0,4 А/л, τ – 20 мин.
* – без ПАВ (Cu, Zn).
Выявлено, что добавление промышленного ПАВ значительно увеличивает степень извлечения всех металлов в широкой области рН 8–11.
Разработанные модули прошли опытно-промышленную и промышленную проверку с участием индустриальных партнеров (ООО «Глобал СО», ООО НПП
«Экологические технологии», АО «Евроэколпласт», ООО «Экоинжком» и др.).
Сформированы технические решения, оформленные в виде «НОУ-ХАУ» и
патентов, представленые ниже.
«Новые технологические решения по очистке сточных вод от ионов тяжелых,
цветных металлов, поверхностно-активных веществ и композиций»
Цель: Повышение эффективности очистки сточных вод от ионов Fe, Al, Cu, Zn, Cr, ПАВ различной природы и сложных композиций (ПАВ, растворители, кислоты) Gardostrip,
Deccordal, Vigon и Zestron.
242
Решение:
I Этап
Введение в систему высокодисперсных материалов на основе ОУ-А, ОУ-Б (10-20
мкм) и коагулянтов на основе FeCl3, AlCl3 для сорбции органических загрязнений, время контакта при перемешивании: 30–60 минут в зависимости от природы и концентрации органического загрязнения.
Количество сорбента определяется на основании представленных данных по адсорбции органических соединений (Г мг/г адсорбента) для различных значений ХПК в определенной воде. Концентрации ОУ-Б 100, 200 мг/л. Добавление коагулянта FeCl3, AlCl3 – 10–20 мг/л.
II Этап
Электрофлотационное отделение дисперсной фазы ОУ-Б, AlCl3, FeCl3 в аппарате проточного типа при pH – 5–8, объемной плотности тока 0,2–0,4 А/л, времени процесса до 20 минут в присутствии ПАВ (МТМх) при соотношении ОУ-Б:ПАВа:коагулянт – 100: 5–10:10.
Для интенсификации процесса и сокращения времени извлечения используются ПАВ 1–5 мг/л. Доза сорбента до 500 г/м3. При дозе сорбента более 500 г/м3 применяют дополнительно отстойник. Время осаждения до 30 минут. Для обеспечения глубокой степени извлечения взвешенных веществ (1–10 г/м3) используется фильтр с размером пор
≤ 1 мкм. Проведен анализ системы очистки сточных вод предприятия по анодному оксидированию алюминия (ГОСТ 9.301-86 и QUALANOD). В технологическом процессе задействовано 19 технологических стадий, 10 стадий промывок изделий дистиллированной водой. Подготовка воды реализуется на установке ионного обмена
(10 м3/ч). На очистных сооружениях (производительностью 10 м3/ч) практикуют реагентный метод обработки воды серной кислотой (нейтрализация) до pH=7±0,5 и
обработка Ca(OH)2 для удаления гидроксиды алюминия и частично сульфат-ионов.
Результат – постоянный расход воды (40 т/мес.) и дороговизна его утилизации,
большой расход реагентов (Ca(OH)2 – 950 кг/мес., серная кислота – 2300 кг/мес. – 20%,
флокулянт – 50 кг/мес.)
Указанная технология не обеспечивает нормативы по сбросу воды в городской коллектор по ионам SO4-, Ca2+, Al3+.

243
Предложен комплекс технологических решений с использованием базовой
технологии:
-электрофлотация и седиментация;
-электрофлотация, фильтрация, сорбция, обратный осмос;
-обессоливание и обезвоживание концентрата раствора Na2SO4 на выпарной установке с кристаллизацией солей Na2SO4 10H2О) (товарный продукт).
Новый подход базируется на разработанной в работе высокоэффективной технологии извлечения Al(OH)3 и растворов Na2SO4 в присутствии добавки анионного ПАВ. Степень извлечения составляет 95–98%, время обработки – 5–10 мин.
Экспериментальные данные представлены в подразделе 3.1.
Принципиальная схема представлена на рисунке 6.6.
|
|
|
|
|
На 10 операций |
|
|
|
|
|
|
Вода |
|
|
|
|
|
|
|
|
|
|
|
|
|
|
|
||
|
|
|
|
|
|
|
|
|
|
|
|
обессоленная |
|
|
Линия анодного |
|
|
|
|
|
|
|
|
|
|
|
1 |
|
|
оксидирования |
|
|
|
|
|
|
|
|
|
2 |
|
|
|
|
алюминия |
|
|
|
|
|
|
|
|
|
|
|
|
|
|
|
|
|
|
|
|
|
|
|
|
|
|
H O (артез) |
||
|
|
|
|
|
|
|
|
|
|
|
|
|
||
|
|
|
|
|
|
|
|
|
|
|
|
|
2 |
|
|
|
|
|
|
|
|
|
|
|
|
Al |
И.О. |
3 |
/час |
|
|
|
|
|
18 операций |
|
|
|
|
|
|
|
Q=10м |
|
|
|
|
|
|
|
|
|
|
|
|
|
|
|
|
3 |
|
|
|
|
|
|
|
|
|
|
|
|
|
|
Q=10м /час |
|
|
|
|
|
|
|
|
|
|
|
|
|
|
С 10 операций |
промывка |
|
|
|
|
|
|
|
|
|
|
|
||
|
|
|
|
|
9 |
9 |
|
|
|
|
|
пермеат |
0,8 Q |
|
|
|
|
|
|
|
|
|
|
|
|
|
|
||
|
H SO |
|
|
|
|
H O |
|
|
|
|
||||
|
4 |
ФШ |
ФШ |
|
|
|
|
|
|
|||||
pH=10-11 |
2 |
|
|
|
2 |
|
|
|
|
13 |
||||
|
|
|
|
|
|
|
|
|
|
|
|
|||
3 |
|
5 |
|
|
6 |
7 |
|
|
|
10 |
11 |
12 |
|
|
|
|
|
|
|
|
|
|
|
|
|
||||
|
|
pH=7 |
|
|
|
МФ |
Сорб |
|
|
H O |
|
|||
|
|
|
|
ЭФ/К |
ЭФ/К |
|
|
|
|
|||||
|
|
|
|
|
|
|
|
|
|
|
2 |
|
||
4 |
|
|
|
|
|
|
|
|
|
|
|
|
|
|
ПАВ |
|
|
|
|
|
|
|
|
|
|
|
|
|
|
(ан) |
|
|
|
|
ФШ |
|
фильтрат |
|
14 |
|
|
|||
|
|
|
|
|
|
|
|
|
||||||
фильтрат |
|
|
|
|
|
|
|
|
|
|||||
|
|
|
|
|
|
|
|
|
|
|
H O |
|
|
|
|
|
|
|
8 |
|
|
|
|
|
|
|
|
|
|
|
|
|
|
|
|
|
|
|
|
|
2 |
|
|
|
|
|
|
|
|
|
|
|
|
|
|
|
Конденсат |
|
|
|
|
|
|
|
|
|
|
|
|
|
|
.ВУ. |
|
|
|
|
|
|
|
|
|
|
|
|
|
|
0,1 Q |
|
|
Осадок |
|
ФП |
|
|
|
|
|
|
15 |
|
|
|
|
|
Al(OH) -коагулянт |
|
|
|
|
|
|
|
|
|
|
|
|
|
|
3 |
|
|
|
|
|
|
|
|
|
|
|
|
|
|
III Класс опасности |
|
|
|
|
Кристаллизатор |
|
|
|
|
|
|
|
|
|
|
|
|
|
|
|
|
|
|
|
|
|
|
||
|
|
|
|
|
солей |
|
|
|
|
|
|
|
|
|
|
|
|
|
|
|
16 |
|
|
|
|
3 |
|
|
|
|
|
|
|
|
|
|
|
|
|
V=~1м |
|
|
||
|
|
|
|
|
|
Na |
SO |
4 |
10H O |
Раствор солей (Na2SO4) |
|
|
||
|
|
|
|
|
|
2 |
|
|
2 |
|
17~150-200 г/л |
|
|
|
|
|
|
|
|
|
(продукт) твердый |
|
|
|
|||||
|
|
|
|
|
|
|
|
|
|
|||||
|
|
|
|
|
|
|
|
|
|
|
|
IV Класс опасности |
|
|
Рисунок 6.6 – Новый подход к очистке сточных вод анодного оксидирования алюминия: 1 – установка ионного обмена; 2 – технологическая линия оксидирования;
3 – емкость промывной воды; 4 – емкость для ПАВ; 5 – реактор-нейтрализатор;
6, 7 – электрофлотокоагулятор; 8 – фильтр-пресс; 9 – сборник флотошлама;
10 – микрофильтр; 11 – сорбционный фильтр; 12 – обратноосмотическая установка;
13 – емкость для чистой воды (пермеат); 14 – выпарная установка; 15 – кристаллизатор
244
Комплекс технологий, реализующих новый подход, обеспечивает:
-возврат до 90% воды в технологический процесс;
-использование ионообменного метода – на 10% (сокращение забора чистой воды);
-снижения количества элюатов 10% вместо 100% Ca2+, Mg2+, Fe2+/3+;
-сокращение шлама Al(OH)3 – 10% от суммарного объема, нет CaSO4;
-получение сухого вещества Na2SO4 10 H2O – вторичный продукт;
-эффективный режим флотации на Al(OH)3-x(SO4)x, Al(OH)3, NaAlO2 + ПАВ степень извлечения 95%;
-сорбцию органических загрязнений на гидроксиде алюминия – повышение ресурса работы угольного фильтра (БАУ);
-повышение ресурса работы микрофильтра – доочистка 5–10% взвешенных веществ;
-осадок Al(OH)3 – II класс опасности (10% от суммарного объема) – продукт для очистки сточных вод (коагулянт);
-обратноосмотическая установка обеспечивает получение особочистой воды для приготовления растворов и проведения промывки в рамках стандарта Qualicoat (80% от требуемого потребления);
-выпарная установка обеспечивает получение дистиллированной воды (вторичный продукт) 10–15%.
Анализ экологических проблем на машиностроительных предприятиях Роскосмоса показал, что существует 10–12 источников загрязнений сточных вод, помимо гальванических цехов и участков это линии размерной обработки стали и сплавов,
механические и сборочные цеха, участки изготовления композиционных материалов и сбора изделий из них, линии и цеха по производству печатных плат электронной техники,
участки нанесения лакокрасочных покрытий, где отсутствуют локальные очистные сооружения.
Все загрязняющие компоненты (более 200 наименований) поступают в хозяйственно-бытовые сточные воды, где наблюдается превышение по ионам тяжелых и цветных металлов, органическим компонентам (ХПК) и взвешенным веществам в десятки раз.
Указанные стоки попадают в общий колодец сточных вод предприятия, откуда поступают в городскую канализацию, где постоянно контролируются со стороны
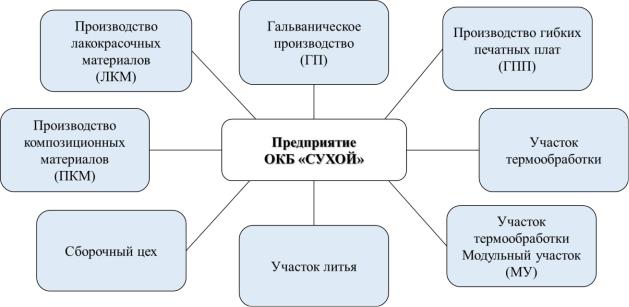
245
водоканалов, которые выставляют существенные штрафы за превышение ПДК достигающие десятки миллионов рублей.
Единственный цех, где всегда есть очистные сооружения, это гальваническое производство (проекты 70–80 хх годов XX века). В состав технологий очистки, как правило, заложен реагентный метод с отстойником, зарытым в землю, где осаждаются гидроксиды металлов.
Основные недостатки таких очистных сооружений:
-Существующая схема очистки сточных вод и применяемое оборудование не всегда обеспечивает очистку сточных вод по ряду компонентов до установленных современных норм предельно-допустимых концентраций (ПДК);
-Как правило, отсутствуют системы автоматического регулирования и контроля параметров очистки (кислотность среды, окислительно-восстановительный потенциал,
химическое потребление кислорода);
-Кислотность очищаемой воды не всегда обеспечивает необходимое снижение концентрации ионов тяжелых и цветных металлов;
-Отсутствуют эффективные системы очистки сточных вод от органических загрязнений и комплексообразователей.
Так, например, для предприятий Филиал ПАО «Компания «Сухой» «ОКБ Сухого» или АО «ММЗ «Вперед» (г. Москва). Источники загрязнение сточных вод приведены на рисунке 6.7 и новый подход к очистке сточных вод на машиностроительном заводе на рисунке 6.8.
Рисунок 6.7 – Источники загрязнение сточных вод
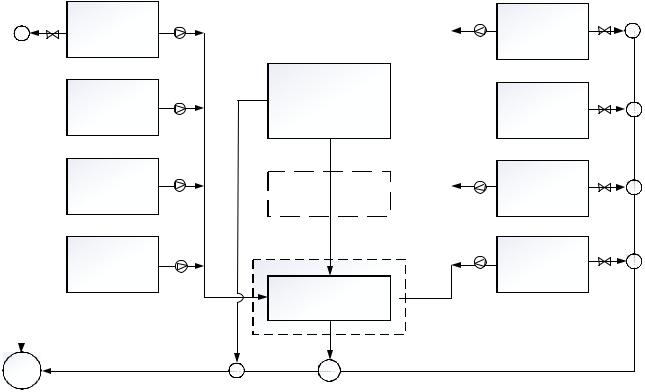
246
Вода хозяйственно-бытового назначения
Лакокрасочное производство
Производство полимерных композиционных материалов
Сборочный цех
Участок литья
Новая линия (промышленные стоки) Вода хозяйственно-бытового назначения
Общий колодец п/я Контроль ИТМ, ХПК, ВВ...
Гальванический цех
Гальваническое производство
Очистные сооружение (гальваническое производство)
Новая линия (промышленные стоки)
Производство печатных плат
Участок термообработки
Модульный участок
ЦЗЛ
Вода хозяйственно-бытового назначения
Вода очищенная
Рисунок 6.8 – Новый подход к очистке сточных вод на машиностроительном заводе
Блок утилизации минерализованных стоков производительностью до 240 м3/сут (до 10 м3/ч)
После предварительной очистки от солей тяжелых металлов и других токсичных соединений образуются сточные воды с повышенной минерализацией, сброс которых в канализацию либо запрещен, либо приводит к дополнительным штрафам.
Для исключения платы за сброс минерализованных сточных вод предлагается использовать блок утилизации на основе метода обратного осмоса. При этом не только исключается сброс минерализованных сточных вод, но и обеспечивается возврат в технологический оборот до 95% сточных вод, очищенных до уровня показателей ГОСТ
9.314 (1 кат.). При эксплуатации блока утилизации минерализованных стоков образуются жидкие отходы (солевые растворы с концентрацией минеральных солей на уровне
200–250 г/л), которые вместе со шламовыми отходами от блока предварительной очистки от солей тяжелых металлов и отработанными технологическими растворами подлежат сдаче в специализированные предприятия.
Основным элементом блока утилизации минерализованных стоков служит установка обратного осмоса. Особенностью данной обратноосмотической установки является работа в режиме глубокого концентрирования. Для исключения образования
247
осадков на поверхности обратноосмотических мембран на входе в установку обратного осмоса монтируются установки ионного обмена и микроультрафильтрации. Для повышения степени концентрирования и уменьшения объема образующихся стоков на выходе обратноосмотической установки располагаются установка выпаривания.
Обессоленная вода после установки обратного осмоса (примерно 95% от объема сточных вод) возвращается в технологический цикл и используется повторно. При этом в 20 раз сокращается потребление свежей водопроводной воды и, соответственно, затраты на водопотребление. Кроме того, качество обессоленной воды после установки обратного осмоса существенно выше качества водопроводной воды, что должно благоприятно сказаться на работе гальванической линии.
Предлагаемая технология позволяет практически полностью утилизировать минерализованные сточные воды, образующиеся после предварительной очистки от солей тяжелых металлов. Получающиеся в результате очистки концентраты имеют малый объем и могут вывозиться на захоронение на специализированных полигонах или нейтрализоваться другим способом.
В состав блока утилизации входят:
Установка ионного обмена (фильтры умягчители);
Установка микроультрафильтрации с мешочным фильтром;
Установка обратного осмоса;
Установка термического испарения;
Система автоматического управления;
Запорно-регулировочная арматура, контрольно-измерительные приборы и трубопроводы.
Перечень основного оборудования и его стоимость приведена в таблице 6.21.
248
Таблица 6.21 – Перечень основного оборудования и его стоимость
№ |
Наименование оборудования |
Стоимость, млн. руб. |
|
|
|
1 |
Установка микро-ультрафильтрации |
2,0–2,5 |
|
|
|
2 |
Установка обратного осмоса |
3,5–3,9 |
|
|
|
3 |
Фильтры для умягчения |
1,0–1,3 |
|
|
|
3 |
Установка термического испарения |
2,5–3,1 |
|
|
|
6 |
Система управления |
0,3–0,7 |
7 |
Обвязка и арматура |
0,1–0,3 |
|
|
|
|
Прочее |
0,1–0,7 |
|
|
|
|
ИТОГО: |
9,5–12,3 |
|
|
|
На 25.06.2021 г. включая НДС) Установка обратного осмоса.
Вода, прошедшая через установку микроультрафильтрации, с расходом подается на двухстадийную очистку в установке обратноосмотического обессоливания.
Обратноосмотическая установка состоит из двух ступеней обратноосмотических элементов типа BW30-400 и SW30-4040. Каждая ступень состоит из корпусов с последовательно соединенными элементами. Общая степень концентрирования составляет до 80–85 %.
При необходимости отключения обратноосмотических фильтров на срок свыше 1 недели производится их консервация раствором пиросульфита натрия.
Срок службы применяемых обратноосмотических мембран не менее 3 лет при условии их регулярного технического обслуживания и периодичности химической промывки не менее 2 раз в год. Полученный концентрат 15–20 % поступает на установку термического испарения пермеат (обессоленная вода). Используется повторно в технологических процессах. Усредненный состав пермеата приведен в таблице 6.22. Для сравнения представлен ГОСТ на воду I категории, используемую в гальванохимических процессах.
Установка термического испарения.
Для сокращения сброса солевого концентрата производится дальнейшее обессоливание воды методом термического испарения и сушки в потоке продуктов горения жидкого или газообразного топлива. В установку термического испарения поступает около 13 м3/сут концентрата после установки обратного осмоса. Степень концентрирования на установке составляет около 8. Концентрат в количестве 1,6 м3/сут (0,07 м3/ч) транспортируется на захоронение или смешивается с отходами блока

249
предварительной физико-химической очистки и флотационной обработки. Опыт разработки, изготовления и эксплуатации выпарных установок имеется в РХТУ им. Д.И. Менделеева (рис. 6.9).
Рисунок 6.9 – Выпарная установка На основании анализа литературы [17, 18, 42, 43] проведена сравнительная оценка
вариантов обессоливания воды методами выпаривания и обратного осмоса. Для качественной оценки за 100% приняты капитальные и эксплуатационные затраты метода выпаривания (таблица 6.22.).
Таблица 6.22 – Технико-экономические показатели вариантов обессоливания
№ |
Наименование |
Выпаривание |
Обратный |
|
|
|
осмос |
1 |
Капитальные затраты, % в том числе: |
100 |
60 |
|
оборудование |
80 |
40 |
|
здания сооружения |
10 |
10 |
|
прочее |
10 |
10 |
|
|
|
|
2 |
Эксплуатационные затраты, % в том числе: |
100 |
25 |
|
энергетические |
90 |
15 |
|
прочие затраты |
10 |
10 |
|
|
|
|
3 |
Себестоимость 1 м3 воды, 2020 г. |
300 руб. |
70–80 руб. |
|
|
|
|
Блок утилизации минеральных стоков после предварительной очистки сточной воды предложен в 2020 году:
-АО ММЗ «Вперед» (г. Москва);
-АО «Туламашзавод» (г. Тула);
-АО ММЗ «Авангард» (г. Москва);
250
-АО «Златмаш» (г. Златоуст);
-ОАО «НПО «Курганприбор» (г. Курган);
-Филиал ОКБ «Сухой» (г. Москва);
-Филиал ОАО РЖД (г. Калуга) (в 2020 г. стадия проектирования);
-Фирма «Экотрак» (г. Подольск, в 2020 г. договор на модернизацию).
При содержании ВВ – 100 мг/л, ХПК – 2170 мгО/л, солесодержание – 4600 мг/л. В
присутствии указанной композиции в лабораторных условиях процесс протекает не более
5 мин, степень извлечения ВВ – 90–95%.
Изменение ХПК на 56–60%, мутность воды, связанная в основном с гуминовыми кислотами, уменьшилась на 72%.
В первую очередь не работает флотатор на 50 м3/ч так, при добавлении коагулянтов
(UltraPAC) и флокулянта Superfloc (А) осадок выпадает на дно аппарата и не поднимается в некий продукт. Неэффективно спроектирована система дозировки реагентов, не предусмотрено оборудование для очистки от ИТМ, органических веществ, минеральных солей.
Для реализации общего подхода к очистке сточных вод на машиностроительном заводе разработана комплексная технология, представленная на рисунке 6.10.
Первый блок данной технологии обеспечивает очистку сточных вод от взвешенных веществ, эмульсий, ПАВ, композиций, восстановление шестивалентного хрома, и
окисление цианид-анион, нейтрализацию кислот и щелочей (рис. 6.11.)
Второй блок обеспечивает глубокую доочистку (5–10%) по взвешенным веществам и органическим компонентам (в том числе растворимым) и обессоливание воды с возвратом 80% подготовленной воды в технологический процесс и получением техногенного отхода IV класса опасности – неорганические соли (хлориды, сульфаты) и
их примеси (рисунок 6.10).
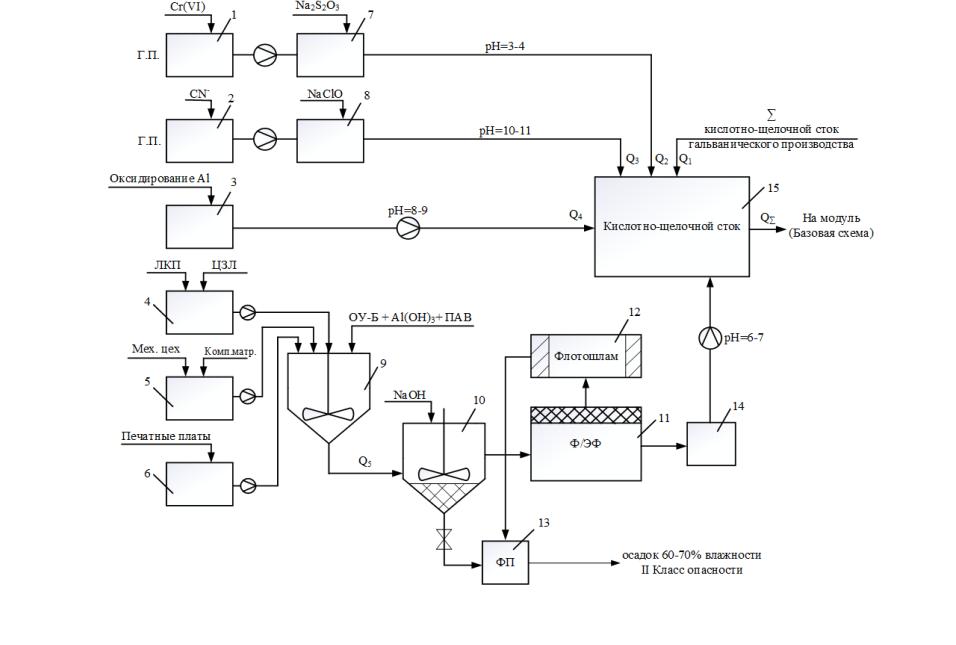
251
Рисунок 6.10 – Комплексная технология очистки сточных вод машиностроительного предприятия: I Блок (водоочистка)
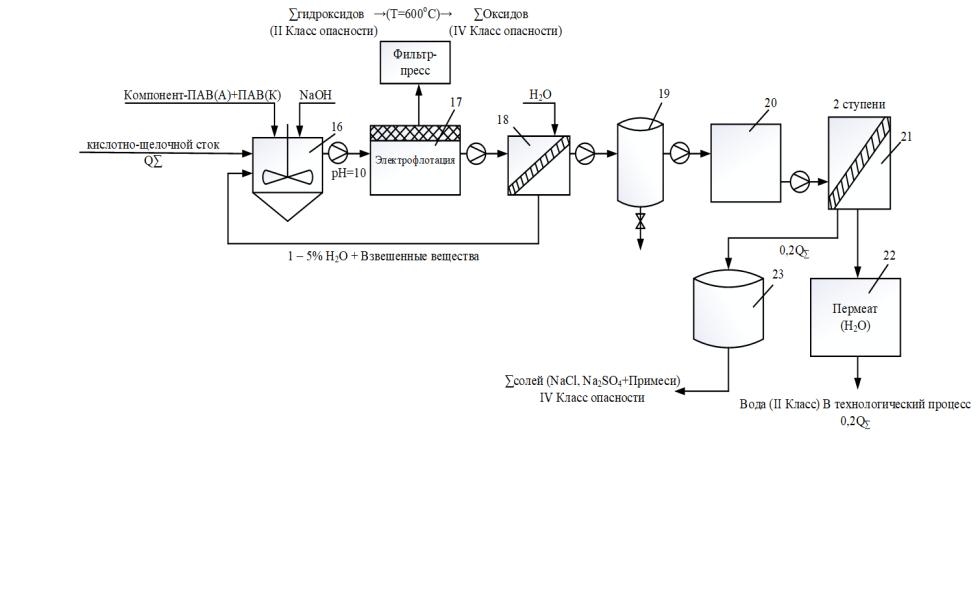
252
Рисунок 6.11 – Комплексная технология очистки сточных вод на машиностроительном предприятии:
II Блок (обессоливание и возврат воды): 1–8 – приемные емкости; 9–10, 16 – реакторы; 11,17 – электрофлотатор; 12 – сборник
флотошлама; 13 – фильтр-пресс; 14,20 – промежуточная емкость; 15 – емкость для кислотно-щелочного стока;18,21 –
обратно-осмотическая установка; 19, 23 – сорбционная установка; 22 – сборник пермеата
253
В последние 2–3 года экологические службы регионов усилили контроль за полигонами ТБО, в том числе за сбросом фильтратов. Реализованы два основных подхода, очистка фильтрата производится на специализированном объекте. В 2018–2019
году в г. Климовск создано предприятие «Экотрак» для обезвреживания фильтратов полигонов Московской области производительностью 1000 м3/ч. Технологическим центром «Экохимпроект» РХТУ им. Д. И. Менделеева и автором работы проведен анализ технических решений объекта и определены причины низкой эффективности функционирования (таблица 6.28).
Проведены исследования ЭФ процесса очистки фильтрата ТБО от ВВ, гуминовых кислот, органических загрязнений. Установлено, что наилучшие результаты
(эффективность осветления фильтрата, извлечения ВВ и частично органических загрязнений) достигается с новой флокулирующей композицией:
UltraPAC (Al(OH)3Cl) – ПААа – ПАВа (МТМх): 100–150 г/м3:10–20г/м3: 10–20 г/м3
Таблица 6.23 – Оценка эффективности электрофлотационной очистки фильтрата ТБО г. Климовск от взвешенных веществ (ХРК, мутность) в РХТУ им. Д.И. Менделеева
№ |
Флоккулирующая композиция |
α ∑, % |
α ∑, % |
|
фильтрат |
концентрат |
|||
|
|
|||
|
|
|
|
|
1 |
UltraPAC (Al) – 100 мг/л |
|
|
|
|
Superfloc (a) – 10 мг/л |
80–85 |
70–75 |
|
|
МТМх – 10 мг/л |
|
|
|
|
|
|
|
|
2 |
UltraPAC (Al) – 125 мг/л |
|
|
|
|
Superfloc (a) – 15 мг/л |
90–95 |
78–83 |
|
|
МТМх – 15 мг/л |
|
|
|
|
|
|
|
|
3 |
UltraPAC (Al) – 150 мг/л |
|
|
|
|
Superfloc (a) – 20 мг/л |
95–98 |
90–95 |
|
|
МТМх – 20 мг/л |
|
|
|
|
|
|
|
Высокая эффективность процесса по снижению концентрации взвешенных веществ, мутности воды и частично ХПК и увеличения производительности флотатора в
5 раз, до 60 м3/ч достигнуто за счет применения композиции «Al(OH)2Cl – флокулянт (А- 100) – ПАВа (МТМх)».
254
Основные загрязняющие компоненты, входящие в состав исследованного фильтрата и извлекаемые в ходе ЭФ процесса – взвешенные вещества, которые обеспечивают высокие значения мутности (600–650 ед.), ХПК = 2000–2200 мгО/л,
концентрация дисперсной фазы 900–1000 мг/л. Состав фильтрата по 20 основным компонентам представлен в приложении 2.
Определен расход реагентов для композиции Al(OH)2Cl – Superfloc A-100 (a) –
МТМх (а) исходя из результатов очистки фильтрата на лабораторной установке в РХТУ им. Д.И. Менделеева. При суточной производительности 1000 м3, расход достаточно большой – коагулянта 180 кг, 24 кг флокулянта и 24 кг ПАВ. При низкой концентрации рабочего раствора флокулянта 0,1% суточный расход 24 м3, что требует значительного реагентного хозяйства. Расчетные данные представлены в таблице 6.24.
Таблица 6.24 – Расход реагентов
|
|
Расход |
|
|
|
|
|
|
|
|
Al(OH)2Cl (А) |
Superfloc (А) |
МТМ (А) |
|
|
UltraPAC |
|
|
|
|
|
|
|
|
в 1 л (лаб) |
150 мг |
20 мг/л |
20 мг |
|
|
|
|
|
|
в 1 м3 |
150 г |
20 г |
20 г |
|
|
|
|
|
|
в 10 м3 |
1500 |
200 |
200 |
|
|
|
|
|
|
в 50 м3 (час) |
7500 г |
1000 |
1000 |
|
|
|
|
|
|
в час 50 м3 |
7,5 кг |
1 кг |
1 кг |
|
|
|
|
|
|
в сутки 1000 м3 |
180 кг |
24 кг |
24 кг |
|
|
|
|
|
|
|
9,3%+ |
0,1%+ |
1% |
|
Исходный раствор |
93 г/л |
1 г/л |
р-р+ |
|
93 кг/м3 |
1 кг/м3 |
10 г/л |
|
|
|
|
|||
|
|
|
10 кг/м3 |
|
|
|
|
|
|
Расход в сутки |
коагулянты |
флокулянт |
ПАВ |
|
~ 2 м3 |
24 м3 |
2,4 м3 |
|
|
|
|
|||
|
|
|
|
|
В рамках выполнения контракта с ООО «ЭКОТРАК» определены основные |
||||
причины низкой |
эффективности |
работы электрофлотационной установки |
производительностью 50 м3/ч. В первую очередь, не отработана технология и не подобран
255
состав флоккулирующей композиции Al(OH)2Cl – флокулянт – ПАВ для очистки фильтрата ТБО.
Предложено два этапа, необходимых для обеспечения работы комплекса производительностью 1000 м3/сут:
I Этап. Модернизация действующего комплекса согласно предложенной схемы рис.6.12 (Предложение – договор РХТУ им. Д.И. Менделеева на 2021 г.)
Основной результат: Повышение эффективности очистки фильтрата от ВВ,
снижение ХПК и мутности раствора.
II Этап. Монтаж второго модуля (рисунок 6.13), обеспечивающего глубокую очистку воды до норм водоотведения г. Подольска и сдачу твердых отходов (∑ солей) IV
класса опасности (вариант А) или концентрата солей (вариант Б).
В рамках II этапа необходимо выполнить технологическую часть.
Предложена схема модернизации комплекса, а именно в части флокуляции осадка
(поз. 3), реагентного хозяйства (поз. 11, 12, 13) ЭФ (поз. 14, 15), концентрации взвешенных веществ (поз. 2). Принципиальная схема приведена на рисунке 6.14.

|
|
|
|
|
256 |
|
|
|
|
|
|
|
|
|
|
|
|
|
17 |
|
|
Концентрат ТБО |
|
|
16 |
|
осадок |
|
|
|
||
|
|
|
|
|
|
|||||
|
|
|
|
|
|
|
||||
|
20 |
|
2 |
14 |
|
* |
|
|
H2O техническая |
|
|
|
|
|
|
|
|||||
|
|
|
|
|
|
15 |
|
0 В +-
фильтрат |
|
3 |
19 |
1 |
21 |
|
|
22 |
0 В |
+- |
5 |
6 |
4 |
|
||
|
|
|
H2O Техническая
ЭФ 18
На стадию II
|
12 |
воздух |
|
|
11 |
13 |
|
9 |
|
|
|
|||
|
|
|
|
Фильтрат ВВ |
|
фильтрат |
|
10% |
8 |
|
|
|
7
10
11 12 13
H2O Техническая
|
|
10% Q |
|
|
Реагентное хозяйство |
1 смена |
|
||
|
H2O Разбавление |
|
||
|
|
|
||
|
|
10 – 0 % |
|
Рисунок 6.12 – Схема модернизации I стадии (ВВ, ХПК) очистки фильтрата ТБО:
1 – Накопитель фильтрата ТБО, V = 50–100 м3; 2 – накопитель концентрата ТБО,
V = 20 м3 *; 3 – Емкость-флокулятор, V = 10 м3 *; 4 – флотатор (электрофлотатор);
5, 6 – напорные фильтры; 7 – Емкость технической воды, V = 10 м3; 8 – емкость для фильтрата промывки фильтров (* емкости с дозаторами t1 коагулянт, t2 флокулянт, t3 ПАВ (2 часа запас), V = 3 м3 *; 9 – компрессор; 10 – участок для приготовления реагентов;11 – емкость коагулянта Al; 12 – емкость флокулянта; 13 – емкость ПАВ
(промышленный)*; 11а – емкость дозирования коагулянта; 12а – емкость дозирования флокулянта; 13а – емкость дозирования ПАВ; 14 – источники тока для модуля электрохимического газонасыщения – 1 блок, на входе мощность 300 А; 15 – источники тока для модуля электрохимического газонасыщения – 2 блока, на выходе мощность 300
А*; 16 – шнековый обезвоживатель флотошлама, приемная емкость; 17 – осадок
(Al(OH)3+ВВ+ХПК); 18 – техническая вода (повышенное солесодержание на стадию II); 19 – фильтрат ТБО, исходная вода (концентрация 1); 21 – блок перемешивания воды,
коагулянтов, флокулянтов и ПАВ; 22 – насосы для перекачки жидкости
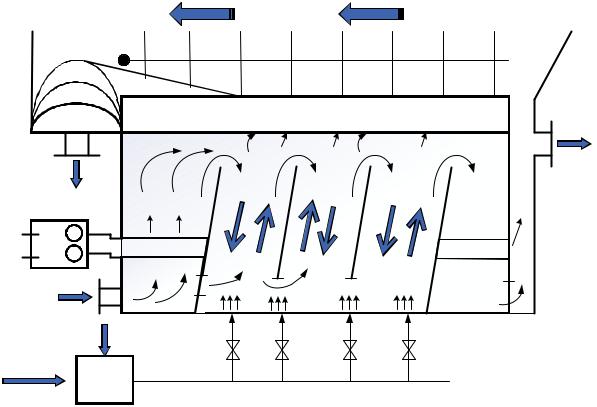
257
В связи с тем, что используемая на очистных сооружениях флотационная установка является комплексом: I камера – ЭФ, II – напорная флотация, III – ЭФ. Проведена работа по повышению эффективности работы установки (объем установки – 12 м3)
производительностью 50 м3/ч. Схема установки приведена ниже на рисунке 6.13.
II к |
II к |
II к |
Вода |
|
|
|
очищенная |
|
Q |
|
эф |
ЭФ |
|
1 |
|
H |
О |
2 |
2 |
+ |
|
220 В |
|
|
|
|
|
|
ЭФ |
- |
|
|
|
|
|
|
2 |
|
|
|
|
|
|
|
III к |
Фильтрат |
|
|
|
|
|
|
|
|
Воздух |
|
|
|
|
|
|
H O~10% |
Q |
Q |
2 |
Q |
3 |
Q |
4 |
1 |
|
|
|
||||
2 |
|
|
|
|
|
|
|
очищенная |
|
|
|
|
|
|
|
Q |
|
Q флотатора |
|
|
|||
|
|
|
|
|
|
|
|
|
|
регулировка |
|
|
Рисунок 6.13 – ЭФ/Флотационный аппарат после модернизации: I камера – ЭФ1;
II камера – Фло; III камера – ЭФ2
Для повышения эффективности работ электрофлотатора / флотатора необходимо иметь нерастворимые аноды Ti / TiO2, оксиды Ме сроком службы 5–10 лет.
Дополнительно на указанных анодах протекает процесс обеззараживания воды
(выделение гипохлорита натрия за счет электролиза NaCl)
В связи с тем, что состав фильтрата ТБО достаточно сложный и I стадия не обеспечивает удаление растворимых солей (NaCl, Na2SO4, ИТМ Fe, Al), растворимых органических соединений заказчику предложен II-й этап модернизации. Схема очистки фильтрата ТБО представлена на рисунке 6.14.
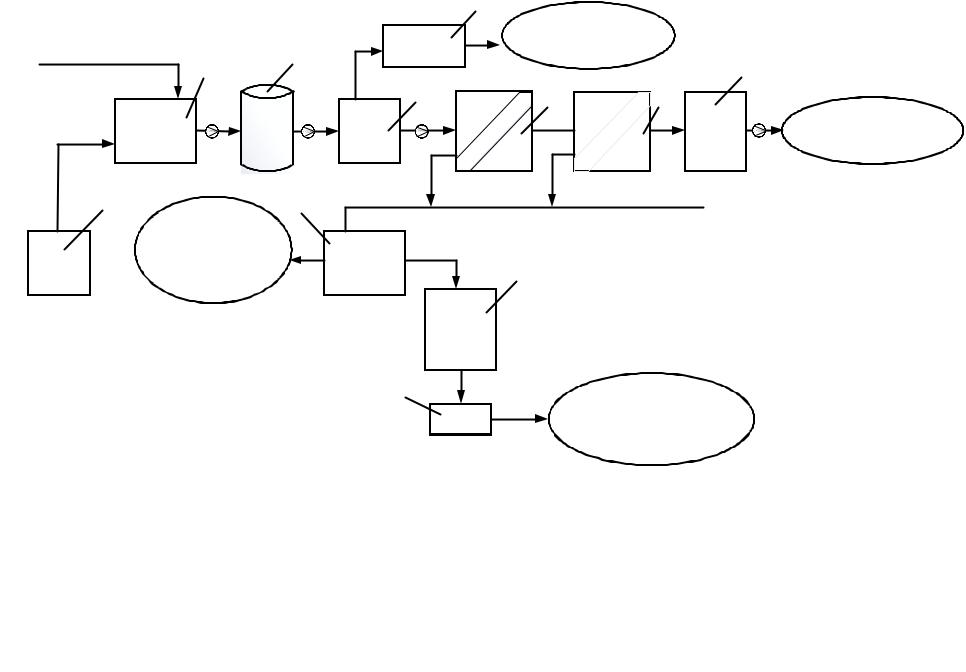
Вода после схемы I
Солей – 5 кг/м3 |
|
pH=7-8 |
|
~50 м3/час Q |
2 |
|
1 |
|
БАУ |
11 |
8 |
|
Технологический раствор
NaCl, Na2SO4 и др.
ОХ IV Класс опасности
~15-20 % Q
Вариант Б
|
4 |
|
|
|
Осадок II-III Класс опасности |
|
|
Элюаты |
|
(Сa, Mg, ИТМ, Fe, Al) |
|
pH=1-2 |
|
– кг/час |
|
1м3/час |
|
7 |
|
|
|
||
3 |
I ступень |
II ступень |
|
|
|
|
5 |
6 |
|
О.О |
||
|
R+
О.О
|
9 |
ВУ |
|
6 - 10 м3/час |
Вариант А |
10 |
Твердый отход |
КР |
NaCl, Na2SO4 И др |
солей IV Класса опасности |
|
|
~2 0 кг/час |
|
~ 000 кг/сутки ( 000м3) |
Вода очищенная (~80% Q потребителю до норм сброса г. Подольска
Рисунок 6.14 – Технологическая схема проекта 2021 г. II этапа (2022 г.): Технологическая часть: 1 – Емкость с водой после I
этапа;
2 – Фильтры с активированным углем (БАУ); 3 – Модуль ионного обмена (катионит) удаление Ca, Mg, ИТМ (Fe, Al, Zn, Cu, Ni, Cr); 4 – Модуль обезвреживания элюатов (нейтрализация – осаждение, ~ 1 м3/ч); 5 – I ступень обратного осмоса;
6 – II ступень обратного осмоса; 7 – Емкость для очищенной воды (пермеат); 8 – Емкость для концентрата от Обратного осмоса; 9 – Выпарная установка; 10 – Кристаллизатор солей; 11 – Емкость для окислителя (H2O2, NaClO)
258
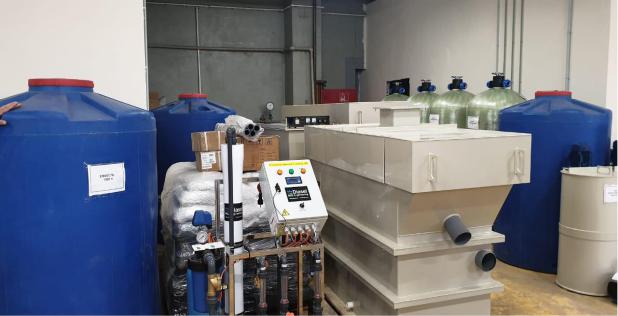
259
Проведенный анализ показывает, что объект «Комплекс локальных очистных сооружений фильтрата полигона твердых бытовых Отходов» мощностью 1000 м3/сутки на производственной площадке Заказчика, расположенной по адресу Московская область, г.о. Подольск, мкр. Климовск, ул. Заводская д. 2, корп. 320, лит. «В»» сегодня обеспечить решение поставленной задачи не может.
Необходимо проводить работы по модернизации комплекса в 2 этапа. I этап – 2021
г., II этап – 2023 г.
РХТУ им. Д.И. Менделеева, ООО «НПП «Экологические технологии», ЗАО
«Экоинжком», АО «Евроэкопалст», ООО «Энергоэкотех» готовы участвовать на всех стадиях выполнения работ по модернизации, проектированию, поставке оборудования,
монтажу, пуско-наладке и обучению персонала.
В настоящий момент РХТУ им. Д.И. Менделеева и ЗАО «Экоинжком» заключили договор на технологическое сопровождение и поставку оборудования.
Полученный опыт очистки фильтратов полигонов захоронения бытовых отходов может быть использован на других объектах, где работают сотрудники РХТУ им. Д.И.
Менделеева.
Некоторые виды созданного в последние 10 лет электрофлотационного оборудования, созданного в РХТУ им. Д. И. Менделеева, в испытаниях которых участвовал автор работы, представлены на фотографиях (рисунки 6.15–6.18).
Рисунок 6.15 – Общий вид с электрофлотационным модулем производительностью
1 м3/ч
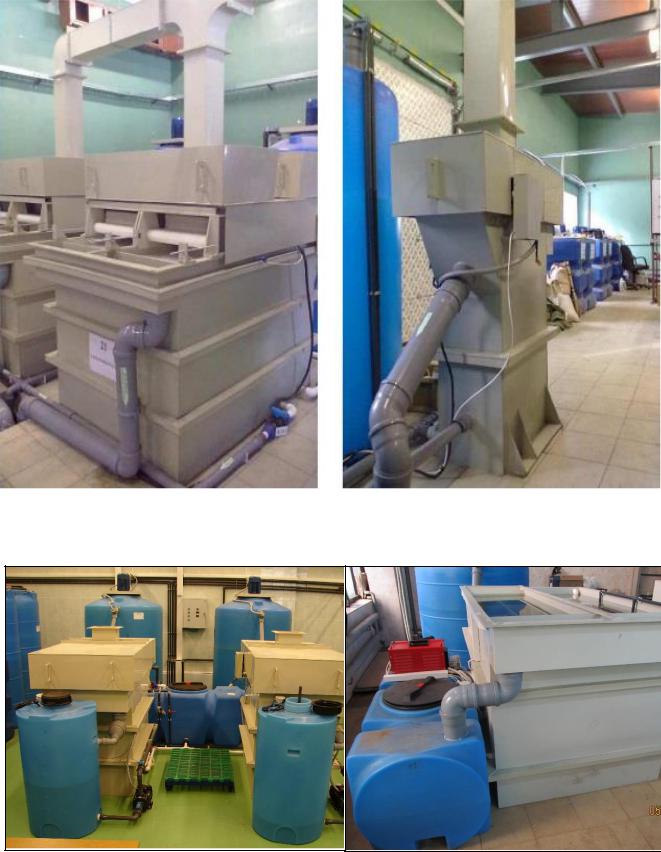
260
Рисунок 6.16 – Электрофлотационные аппараты производительностью
10 м3/ч и 5 м3/ч
Рисунок 6.17 – Фотографии ЭФ модулей
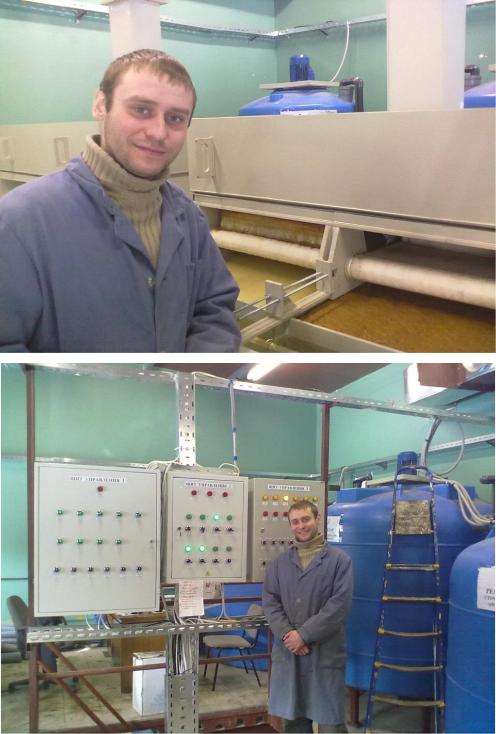
261
Рисунок 6.18 – Очистные сооружения, завод «Рубин», г. Балашиха
Проведена оценка стоимости оборудования для очистки сточных вод сложного состава для комплекса 10 м3/ч. Оценка поставщиков приведена в таблице 6.25. Цены представлены на 1.06.2021 г. с учетом НДС.
262
Таблица 6.25 – Оценка стоимости оборудования для извлечения взвешенных веществ из сточных вод сложного состава производительностью 10 м3/ч
|
Операция |
Цена за ед., млн. |
||
Тип оборудования |
Концентрирование |
Извлечение |
||
руб. |
||||
|
ВВ, % |
ВВ, % |
||
|
|
|||
Электрофлотатор |
99 |
95 |
1,2–1,4 |
|
Напорный флотатор |
50 |
50 |
1,5–2,0 |
|
МФ установка |
96 |
- |
1–1,2 |
|
УФ установка |
99 |
- |
1,5–2,0 |
|
МФ + центрифуга (1м3/ч) |
99 |
95 |
2–2,5 |
|
УФ + центрифуга (1м3/ч) |
99 |
97 |
2,5–3,0 |
|
Декантер центрифуга (10 м3/ч) |
95 |
95 |
> 5,0 |
Представленное выше оборудование используется Технологическим центром
«Экохимпроект» РХТУ им. Д.И. Менделеева при участии автора работы для реализации на промышленных объектах при очистке сточных вод от взвешенных веществ.
Проведенная оценка показывает конкурентоспособность электрофлотационного оборудования для извлечения ВВ органической и неорганической природы.
Разработанные модули прошли опытно-промышленную и промышленную проверку с участием индустриальных партнеров (ООО «Глобал СО», ООО НПП
«Экологические технологии», АО «Евроэколпласт», ООО «Экоинжком» и др.).
Созданы новые технологические решения по повышению эффективности удаления ВВ и снижения ХПК при очистке фильтратов, образующихся на полигонах ТБО Московской области для ООО «Экотрак», на комбинированном аппарате флотатор с ЭФ камерой, объем аппарата – 12 м3/ч. Высокая эффективность процесса по снижению концентрации ВВ, мутности воды и частично ХПК и увеличения производительности флотатора в 5 раз до 60 м3/ч достигнуто за счет применения композиций из трех веществ:
Al(OH)2Cl 100–150 г/м3, флокулянт 10–20 г/м3, ПАВ (МТМх) 10–20 г/м3 при концентрации ВВ 1000–1500 мг/л, ХПК – 4000–5000 ед., мутности до 800 ед.
Комплексы для очистки сточных вод внедрены: ЗАО «НТЦ Элинс» г. Зеленоград,
ОАО «Топаз», г. Москва, АО «Рубин» г. Балашиха. Технологические решения модернизации очистных сооружений переданы: ОКБ «Сухого» г. Москва, ММЗ «Вперед» г. Москва, ПО «Туламашзавод» г. Тула, ООО «Экотрак» г. Подольск, АО «Калужский завод Ремпутьмаш» г. Калуга.