
- •Введение
- •1. Аналитический обзор. Выбор направления исследований
- •1.1. Флотация, электрофлотация, электрофлотокоагуляция, современные направления извлечения взвешенных веществ, цветных, редкоземельных металлов и органических веществ. Научные школы
- •2. Методическая часть
- •2.3. Определение характеристик дисперсной фазы
- •2.4. Информация об использованных в работе ПАВ, флокулянтах и коагулянтах
- •2.5. Характеристика некоторых образцов дисперсной фазы
- •4. Новые области применения электрофлотационных процессов. Основные научные результаты
- •5.2. Роль дисперсной фазы в эффективности электрофлотацинного процесса
- •Заключение
- •Список сокращений и условных обозначений
- •Список литературы
- •Приложение 1
- •Акты и протоколы опытно-промышленных и промышленных испытаний установок для очистки сточных вод
- •Приложение 2
132
4. Новые области применения электрофлотационных процессов. Основные научные результаты
4.1. Основные закономерности электрофлотационного извлечения высокодисперсных углеродных материалов (порошки ОУ-А, ОУ-Б) из
водных растворов электролитов
Одним из методов очистки сточных вод от вредных органических веществ является сорбция, определяющую роль в эффективности которой играет выбор сорбента. Наиболее эффективными сорбентами для сорбционной очистки считают порошкообразные углеродные материалы [285], в том числе активированные угли различных марок и производителей [235, 237, 286, 287].
В последнее время все более распространенной становится технология
«углевания» – это порционное введение углеродного материала в виде суспензии для сорбционной очистки воды [282, 284]. Однако применение такой технологии подвергает опасности загрязнения сточных вод частицами углеродных материалов малых размеров,
на которых сорбированы органические и неорганические вещества различной природы.
Вкрупномасштабных производствах порошкообразные углеродные материалы обычно разделяются двухступенчатым процессом, состоящим из стадии седиментации и стадии фильтрации. Оптимальные системы разделения угля чаще всего конструируются
сцелью уменьшения стоимостей производства и дозировки добавок. В соответствии с этим, наиболее часто применяемыми технологиями извлечения являются седиментация и фильтрация, в основном в сочетании с коагуляцией и флокуляцией. Однако данными методами можно извлечь только крупные частицы (от 50 до 500 мкм), кроме того они не выгодны для производства в силу своей длительности (60–120 минут) и
дороговизны [248].
Внастоящее время в зарубежных странах [282, 288] и РФ проводят фундаментальные исследования процессов флотации и электрофлотационного извлечения высокодисперсных углеродных материалов из водных растворов в присутствии различных загрязняющих веществ.
Учитывая вышеизложенное, проведение электрофлотационных исследований порошкообразных углеродных материалов и определение факторов, влияющих на высокую эффективность и интенсификацию процессов, позволит расширить
133
технологические возможности применения активированных углей на промышленных предприятиях для обеспечения снижения угроз загрязнения водных сред опасными отходами.
В работе исследования проводили, используя водные растворы сульфата и хлорида натрия, содержащие высокодисперсные углеродные материалы (порошки) ОУ-А, ОУ-Б и другие порошки ВДУМ.
Для интенсификации ЭФ процесса использовали ПАВ:
-анионной природы – додецилсульфат натрия (NaDDS), додецибензолсульфонат натрия (NaDBS), алкилбензолсульфонат натрия (А-40);
-катионной природы – алкилбензилдиметиламмоний хлорид (Катамин АБ,
КатаПАВ), |
алкилдиметил |
(2-гидроксиэтил) |
аммоний |
хлорид (Катинол), |
дидецилдиметиламмоний хлорид (СептаПАВ);
-неионогенной природы – синтанол АЛМ-10, препарат ОС-20 и полиэтиленоксид ПЭО-1500;
атакже флокулянты, коагулянты и композиции:
-флокулянты: С-494(к), А-130(а), N-300(н);
-коагулянты: соли Al3+, Fe3+, Al(OH)2Cl;
-композиции Fe(OH)3 – ПАВа, Al(OH)3 – ПАВа, Al(OH)2Cl – ПАВа.
Проведены исследования по ЭФ извлечению порошков углей ОУ-А, ОУ-Б из водных растворов электролитов на основе NaCl, Na2SO4 в диапазоне pH = 4–11.
Характеристика образцов представлена в подразделе 2.5. Экспериментальные данные ЭФ процесса извлечения порошков углей в различных растворах представлены в таблице 4.1.
Установлено, что в растворах NaCl (мг/л) для ОУ-А и ОУ-Б степень извлечения не превышает 10–15 %. Низкая величина α связана с малым размером частиц ≤ 10 мкм и высокими отрицательными значениями величины электрокинетического потенциала, что неблагоприятно сказывается на формировании флотокомплекса пузырек H2
(отрицательный заряд) и порошок ВДУМ (отрицательный заряд).
Относительно высокие значения степени извлечения для ОУ-Б при рН 4–10 в
растворах Na2SO4 связаны со специфической адсорбцией сульфат-аниона на порошках
углеродного материла, вероятно по реакции ионного обмена групп 2OH- |
→ |
SO42-, что |
→ |
ведет к увеличению гидрофобности поверхности и, как следствие, росту степени извлечения дисперсной фазы.
134
Таблица 4.1 – Влияние рН раствора и природы электролита на степень
электрофлотационного извлечения порошков углей различных марок
рН |
|
|
Степень извлечения, α, % |
|
|
|
|
NaCl |
|
|
Na2SO4 |
||
|
ОУ-А* |
|
ОУ-Б |
ОУ-А* |
|
ОУ-Б |
4 |
13 |
|
15 |
11 |
|
76 |
5 |
10 |
|
10 |
12 |
|
60 |
6 |
9 |
|
12 |
13 |
|
58 |
7 |
8 |
|
14 |
10 |
|
56 |
8 |
10 |
|
10 |
13 |
|
67 |
9 |
10 |
|
8 |
12 |
|
59 |
10 |
4 |
|
6 |
10 |
|
56 |
11 |
4 |
|
5 |
8 |
|
23 |
Условия эксперимента: c электролита – 1 г/л; c угля – 100 мг/л; c* – 200 мг/л;
Jv – 0,4 А/л; τ– 20 мин, рН – 4–11.
Известно, что важный фактор, влияющий на степень извлечения дисперсной фазы
– это размер и заряд частиц. Экспериментальные результаты по измерению ξ±-потенциала представлены в таблице 4.2.
Таблица 4.2 – Влияние рН раствора на электрокинетический потенциал частиц высокодисперсных углеродных материалов различной природы
|
|
Электрокинетический потенциал, ξ±, мВ |
||||
рН |
|
УНМ [231] |
|
|
ВДУМ |
|
|
УНВ |
УНВ окисл |
УНЧ |
ОУ-А |
|
ОУ-Б |
0,5 |
–3 |
+2 |
–4 |
–5 |
|
–23 |
2,0 |
–9 |
–3 |
–10 |
–10 |
|
–23 |
3,0 |
–9 |
–10 |
–16 |
–14 |
|
–27 |
5,0 |
–10 |
–14 |
–18 |
–20 |
|
–28 |
6,0 |
–16 |
–14 |
–18 |
–19 |
|
–36 |
7,0 |
–17 |
–16 |
–20 |
–24 |
|
–33 |
9,0 |
–19 |
–19 |
–23 |
–28 |
|
–29 |
10,0 |
–20 |
–21 |
–25 |
–35 |
|
–29 |
11,0 |
–20 |
–21 |
–25 |
–19 |
|
–27 |
Условия эксперимента: c NaCl – 1 г/л; c ВДУМ – 100 мг/л; рН – 0,5–11.
Экспериментально показано, что порошки углеродных материалов при рН 2–11 в
сточных водах в растворах NaCl и NaNO3 имеют высокий отрицательный заряд
ξ±-потенциала от –20 до –35 мВ.
135
Порошки ОУ-Б достаточно сложно извлекаются в растворах хлорида натрия концентрацией от 1 до 100 г/л даже в присутствии коагулянтов Fe3+ и Al3+ и ПАВ. В
разбавленных растворах высокие значения степени извлечения (80–90%) наблюдаются при добавлении композиции AlCl3–ПАВа, композиция с ПАВ–FeCl3 работает неэффективно. Экспериментальные данные по кинетике ЭФ извлечения порошка ОУ-Б
представлены в таблице 4.3.
Таблица 4.3 – Зависимость кинетики электрофлотационного извлечения активированного угля ОУ-Б от концентрации фонового электролита NaCl при добавлении композиции анионного ПАВ и коагулянтов AlCl3 и FeCl3
|
Степень электрофлотационного извлечения активированного угля ОУ-Б, α, % |
||||||||
|
|
|
|
|
|
|
|
||
Время, |
1 г/л NaCl |
10 г/л NaCl |
|
100 г/л NaCl |
|||||
τ, мин |
|
|
|
|
|
|
|
|
|
AlCl3 |
FeCl3 |
AlCl3 |
|
FeCl3 |
|
AlCl3 |
|
FeCl3 |
|
|
|
|
|
||||||
|
+ ПАВа |
+ ПАВа |
+ ПАВа |
|
+ ПАВа |
|
+ ПАВа |
|
+ ПАВа |
5 |
81 |
9 |
31 |
|
3 |
|
19 |
|
2 |
10 |
90 |
10 |
30 |
|
6 |
|
16 |
|
2 |
20 |
89 |
10 |
28 |
|
16 |
|
13 |
|
4 |
30 |
79 |
13 |
31 |
|
21 |
|
10 |
|
5 |
Условия эксперимента: c электролита – |
1 г/л; c угля – |
100 мг/л, |
c ПАВ – 5 мг/л; |
с AlCl3/FeCl3 – 10 мг/л; Jv – 0,4 А/л; рН – 7; ПАВ – NaDDS
Установлено, что с ростом концентрации NaCl степень извлечения снижается до
15%, что обусловлено реакцией разряда Cl- и накоплением окислителя в растворе (ClO-).
Все это ведет к окислению поверхностных групп и повышению гидрофильности дисперсной фазы. Большие сложности возникают при ЭФ извлечении дисперсной фазы ОУ-Б при его повышенных концентрациях – 100, 200, 300 мг/л. Экспериментальные результаты представлены в таблице 4.4.
136
Таблица 4.4 – Зависимость кинетики электрофлотационного извлечения активированного угля ОУ-Б от концентрации коагулянта AlCl3 в присутствии фонового электролита NaCl
и анионного ПАВ NaDDS
|
|
Степень электрофлотационного извлечения |
|||
Концентрация |
Время, |
активированного угля ОУ-Б, α, % |
|||
ОУ-Б, мг/л |
мин |
|
Концентрация AlCl3 |
|
|
|
|
40 мг/л |
60 мг/л |
|
80 мг/л |
|
5 |
11 |
18 |
|
30 |
300 |
10 |
23 |
32 |
|
45 |
20 |
34 |
46 |
|
58 |
|
|
|
||||
|
30 |
60 |
67 |
|
72 |
|
|
|
Концентрация AlCl3 |
|
|
|
|
20 мг/л |
30 мг/л |
|
40 мг/л |
200 |
5 |
10 |
74 |
|
41 |
10 |
19 |
91 |
|
61 |
|
|
|
||||
|
20 |
37 |
88 |
|
75 |
|
30 |
51 |
87 |
|
74 |
|
|
|
Концентрация AlCl3 |
|
|
|
|
5 мг/л |
10 мг/л |
|
20 мг/л |
100 |
5 |
22 |
81 |
|
40 |
10 |
14 |
90 |
|
84 |
|
|
|
||||
|
20 |
16 |
89 |
|
85 |
|
30 |
21 |
79 |
|
87 |
Условия эксперимента: c электролита – 1 г/л; c ПАВ – 5 мг/л; Jv – 0,4 А/л; рН – 7
Установлено, что электрофлотационное извлечение порошка ОУ-Б при высоких концентрациях до 300 мг/л требует увеличения дозы коагулянта до 30–60 мг/л.
Анализируя экспериментальные данные, представленные в таблице 4.4, и ранее отмеченные результаты сорбционной активности ОУ-Б и Al(OH)3 такая система, как ОУ-Б – Al(OH)3 – ПАВа в соотношении (100–200):(10–40):(5–10) представляет практический интерес для очистки сточных вод. Извлечение высоких концентраций ОУ-
Б (200 мг/л) возможно при совмещении двух процессов – седиментации и электрофлотации.
На рисунке 4.1 показано влияние флокулирующих композиций AlCl3+ПАВ, AlCl3
+ флокулянт на степень извлечения порошка ОУ-Б. Высокие значения α наблюдаются
(кривая 5,6) в присутствии флокулирующей композиции Al(OH)3–ПАВа,
Al(OH)3–флокулянт. Степень извлечения достигает 80–90%, что связано в первую очередь с увеличением размера флотируемых частиц 40–50 мкм и изменением заряда поверхности в сторону более низких положительных значений.
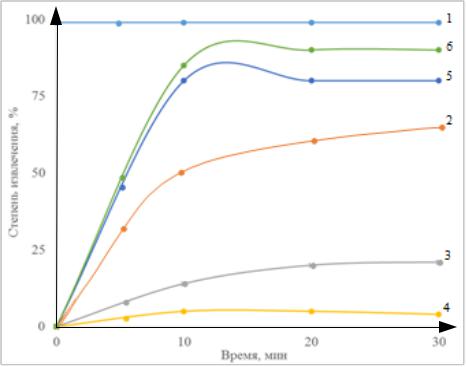
137
Рисунок 4.1 – Влияние флокулирующих добавок на электрофлотационное извлечение ОУ-Б: 1 – фильтрация ОУ-Б; 2 – Na2SO4 без коагулянта; 3 – NaCl без коагулянта;
4 – Na2SO4 + Al2 (SO4)3; 5 – NaCl + AlCl3 + ПАВа; 6 – Na2SO4 + AlCl3 + Флок.а: условия эксперимента: c NaCl/Na2SO4 – 1 г/л; c ПАВ/флокулянт – 5 мг/л; c ОУ-Б – 100 мг/л;
Jv – 0,4 А/л; рН – 7,0
Проведена оценка степени извлечения ОУ-Б с учетом размера и заряда дисперсной фазы ОУ-Б+Fe(OH)3; ОУ-Б+Al(OH)3; ОУ-Б+ПАВ; ОУ-Б+флокулянт. Экспериментальные данные приведены в таблице 4.5.
Установлено, что введение в раствор катионного флокулянта FO 4190 марки SNF Floerger способствует смене знака заряда частиц на положительный, однако размер частиц существенно уменьшается и при этом степень извлечения не превышает 6%.
Добавление в раствор флокулянта анионной природы способствует незначительному росту степени извлечения дисперсной фазы до 60%, в то же время
ξ-потенциал частиц не изменяется, а средний гидродинамический радиус частиц снижается до 10 мкм.
Такие компоненты, как поверхностно-активные вещества анионной и неионогенной природы способствуют значительному снижению ξ -потенциала частиц до –35 мВ, что также существенно подавляет процесс электрофлотационного извлечения дисперсной фазы.
138
Как показали исследования, в присутствии коагулянтов Al3+, Fe3+ наблюдается не только увеличение размера частиц, но и снижение величины электрокинетики потенциала
(таблица 4.5), все это способствует росту степени извлечения ОУ-Б. Флокулянты и ПАВ не дают увеличения размера частиц ОУ-Б ввиду того, что адсорбция крупных органических молекул на ОУ-Б осложняется размерами пор. В ряде случаев наблюдается снижение размера частиц в присутствии ПАВ, что связано с диспергацией частиц.
Таблица 4.5 – Влияние добавок на ξ±-потенциал, средний диаметр и степень электрофлотационного извлечения частиц ОУ-Б в растворе Na2SO4
|
|
|
Показатель |
|
|
Добавка |
|
|
|
|
|
|
ξ±, мВ |
Øср, мкм |
|
α, % |
|
|
|
|
|||
|
|
|
|
|
|
|
Однокомпонентная система |
|
|
|
|
|
|
|
|
|
|
Без добавок ОУ-Б |
|
–19 |
25 |
|
56 |
|
|
|
|
|
|
Fe (III) + ОУ-Б |
|
–7 |
55–60 |
|
98 |
|
|
|
|
|
|
А1 (III) + ОУ-Б |
|
–5 |
35–40 |
|
97 |
|
|
|
|
|
|
|
Двухкомпонентная система |
|
|
|
|
|
|
|
|
|
|
|
ОУ-Б + флокулянт |
|
|
|
|
|
|
|
|
|
|
FO4190 (к) |
|
+12 |
4 |
|
6 |
|
|
|
|
|
|
FA 920 (н) |
|
–18 |
7 |
|
23 |
|
|
|
|
|
|
AN 905 (а) |
|
–19 |
10 |
|
60 |
|
|
|
|
|
|
|
ОУ-Б + ПАВ |
|
|
|
|
|
|
|
|
|
|
Катинол (к) |
|
–19 |
19 |
|
28 |
|
|
|
|
|
|
ОксиПАВ (н) |
|
–34 |
12 |
|
37 |
|
|
|
|
|
|
NaDDS (а) |
|
–35 |
14 |
|
26 |
|
|
|
|
|
|
Условия эксперимента: c Na2SO4 –1 г/л; c ОУ-Б – 100 мг/л; c ПАВ / флокулянт – 5 мг/л;
Jv – 0,4 А/л; рН – 7,0; τ – 20 мин.
139
Таблица 4.6 – Влияние природы ПАВ и коагулянта на электрофлотационное извлечение
порошка ОУ-Б из водного раствора электролита Na2SO4
|
|
Степень извлечения ОУ-Б, % |
|||
Система |
|
|
|
|
|
|
|
|
время, мин |
|
|
|
5 |
|
10 |
20 |
30 |
Анионный ПАВ NaDBS* (без коагулянта) |
1 |
|
2 |
2 |
3 |
|
|
|
|
|
|
+ А13+ |
22 |
|
25 |
35 |
36 |
+ Fe3+ |
15 |
|
18 |
19 |
20 |
+ Zn2+ |
29 |
|
30 |
30 |
30 |
Катионный ПАВ СептаПАВ* (без коагулянта) |
9 |
|
50 |
52 |
52 |
+ А13+ |
14 |
|
43 |
59 |
81 |
+ Fe3+ |
71 |
|
71 |
98 |
98 |
+ Zn2+ |
72 |
|
89 |
97 |
97 |
Неионогенный ПАВ ПЭО-1500* |
2 |
|
4 |
4 |
4 |
|
|
|
|
|
|
+ А13+ |
21 |
|
27 |
68 |
86 |
+ Fe3+ |
58 |
|
77 |
92 |
97 |
+ Zn2+ |
58 |
|
93 |
99 |
99 |
Условия эксперимента: c Na2SO4 – 1 г/л; c Me2+ – 10 мг/л; c ПАВ – 100 мг/л; c ОУ-Б – 100 мг/л; Jv – 0,4 А/л, рН –7, рН для Zn2+ – 9,5.
* – система без коагулянта
При высоких концентрациях ПАВ (100 мг/л) ЭФ извлечение ОУ-Б затруднено.
Степени извлечения ОУ-Б в присутствии NaDBS(а) не превышает 3%. Аналогично для неионогенного ПАВ низкое значение α связано с (таблица 4.6) процессами мицеллообразования на поверхности ОУ-Б-ПАВ. Для катионного ПАВ мицелообразование наблюдается при концентрациях более 200 мг/л и в связи с тем, что электрокинетический потенциал-ОУ-Б отрицательный, для ЭФ создаются благоприятные условия при росте ξ±-потенциала.
Отмеченное выше приводит к гидрофобизации поверхности ОУ-Б. Степень извлечения ВДУМ достигает 52%. Добавление гидроксидов в качестве коагулянтов не приводит к значительному росту степени извлечения в присутствии высокой концентрации NaDBS, так как частицы коагулянта заряжены отрицательно, как порошок ОУ-Б. В присутствии катионных и неионогенных ПАВ коагулянты Fe3+, Al3+ и Zn2+
работают эффективно, возрастает размер частиц, повышается ξ±-потенциал,
увеличивается степень извлечения.

140
Необходимо отметить, что кинетика процесса ЭФ извлечения зависит от состава раствора, наличия ПАВ, коагулянтов и композиций. Стационарные значения α достигаются за время ЭФ не более 10 мин (кривая 4) Все это свидетельствует об эффективном формировании флотокомплекса «частица – композиция – пузырек (H2, O2)»
и, как следствие, сокращения времени ЭФ.
Рисунок 4.2 – Влияние ПАВ на степень электрофлотационного извлечения ОУ-Б:
1 – неионогенный ПАВ; 2 – анионный ПАВ; 3 – катионный ПАВ; 4 – ОУ-<+катионный ПАВ+Fе3+(10мг/л); 5 –ПАВк + Fe3+ (5 мг/л): условия эксперимента: с ОУ-Б – 100 мг/л; с ПАВ – 5мг/л; рН – 7,0; Jv – 0,2 А/л; с Na2SO4 – 1г/л
Установлено, что частицы ОУ-Б эффективно извлекаются при добавлении промышленного коагулянта UltraPAC и ПАВ. Влияние концентрации коагулянта
(Al(OH)2Cl) и ПАВ (NaDDS) на степень извлечения ОУ-Б представлено на рисунке 4.3.
Для достижения высоких значений α необходим подбор концентрации ОУ-Б: коагулянт:
ПАВ = 1:0,3:0,2–0,25.
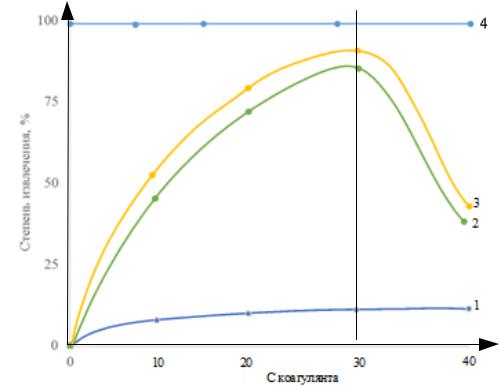
141
Рисунок 4.3 – Влияние концентрации коагулянта UltraPAC на ЭФ извлечения ОУ-Б: 1 – с ПАВ 0 мг/л; 2 – с ПАВ 5 мг/л; 3 – с ПАВ 10 мг/л; 4 – фильтрация: условия эксперимента: с Al3+ – 0–50 мг/л; ПАВ – NaDDS; с NaCl – 1 г/л; Jv – 0,2 А/л; pH – 7,0;
с ОУ-Б – 100 мг/л
Применение высоких концентраций коагулянта UltraPAC более 30 мг/л приводит к интенсификации процессов седиментации. Все это требует использовать ЭФ аппараты с камерой седиментации, разработанные в РХТУ им. Д.И. Менделеева.
Электрофлотационное извлечение другого порошка ОУ-А в растворах NaCl
протекает так же неэффективно, как и ОУ-Б, степень извлечения составляет 5–10%.
Экспериментальные данные представлены в таблице 4.7 для разных систем.
142
Таблица 4.7 – Влияние коагулянта FeCl3, ПАВ и флокулянта на ЭФ извлечение порошка угля ОУ-А
|
|
|
|
Степень извлечения, α, % |
|
|||
Система |
|
|
|
|
|
|
|
|
|
рН - 4 |
|
рН - 5 |
рН - 6 |
||||
|
|
|
||||||
|
|
|
|
|
|
|
|
|
|
|
5 мин |
20 мин |
5 мин |
20 мин |
5 мин |
20 мин |
|
|
|
|
|
|
|
|
|
|
без коагулянта и ПАВ |
2 |
5 |
|
5 |
9 |
3 |
9 |
|
|
|
|
|
|
|
|
|
|
+ FeCl3 25 мг/л |
31 |
96 |
|
65 |
30 |
25 |
12 |
|
|
|
|
|
|
|
|
|
|
+ FeCl3 15 мг/л |
35 |
89 |
|
17 |
10 |
10 |
12 |
|
|
|
|
|
|
|
|
|
|
+ FeCl3 35 мг/л |
59 |
97 |
|
42 |
14 |
7 |
9 |
|
+ FeCl3 25 мг/л ПАВа 5 мг/л |
92 |
96 |
|
65 |
17 |
3 |
2 |
|
|
|
|
|
|
|
|
|
|
+ FeCl3 25 |
мг/л ПАВк 5 мг/л |
87 |
89 |
|
92 |
60 |
26 |
5 |
+ FeCl3 25 |
мг/л ПАВк 10 мг/л |
29 |
96 |
|
48 |
11 |
60 |
25 |
|
|
|
|
|
|
|
|
|
+ FeCl3 25 |
мг/л флокулянт 5 мг/л |
81 |
71 |
|
25 |
13 |
- |
- |
Условия эксперимента: с NaCl – 1 г/л; с ОУ-А – 200 мг/л; Jv – 0,4 А/л; c ПАВ – 0–10 мг/л; c FeCl3 – 25 мг/л; рН = 4 – 6; ПАВа – NaDDS; ПАВк – СептаПАВ ХСВ-50.
Рост степени электрофлотационного извлечения наблюдается в присутствии коагулянтов Fe3+и композиции Fe3+ – ПАВа, наиболее эффективно электрофлотационный процесс протекает при рН 4,0, остаточное содержание Fe3+ < 0,1 мг/л.
Для анализа причин высокой эффективности ЭФ извлечения ОУ-А в слабокислых растворах (pH=4,0) проведено измерение размера и заряда частиц флотокомплекса ОУ-А
– Fe(OH)3. Экспериментальные данные приведены в таблице 4.8.
Таблица 4.8 – Влияние кислотности среды на физико-химические свойства
(электрокинетический потенциал и размер частиц) дисперсной фазы ОУ-А в присутствии коагулянта Fe3+ и без добавок
|
Электрокинетический потенциал, мВ. |
Размер частиц, мкм |
||
pH |
|
|
|
|
|
Без добавок |
+ FeCl3 |
Без добавок |
+ FeCl3 |
|
|
|
|
|
4 |
–23 |
–2 |
10 |
20 |
|
|
|
|
|
5 |
–23 |
–9 |
13 |
16 |
6 |
–27 |
–9 |
13 |
16 |
7 |
–28 |
–21 |
13 |
16 |
8 |
–36 |
–22 |
13 |
16 |
9 |
–33 |
–22 |
11 |
14 |
10 |
–29 |
–23 |
11 |
12 |
Условия эксперимента: c Na2SO4 – 1 г/л; c Fe3+ – 10 мг/л; c ОУ-Б – 100 мг/л.
143
Высокие значения степени извлечения для ОУ-А при рН 1,0 связано с размером флотокомплекса ОУ-А – Fe(OH)3 и низким значением ξ-потенциала.
Фундаментальные исследования по ЭФ извлечению порошков углеродных материалов разных производителей (10–12 образцов), роли поверхности групп,
сорбционные свойства порошков и их влияние на процессы разделения проводятся в РХТУ им. Д.И. Менделеева канд.хим.наук доцентом кафедры технологии неорганических веществ и электрохимических процессов А.М. Гайдуковой В рамках данной работы решались технологические задачи извлечения органических соединений из сточных вод гальванохимических производств.
4.2.Электрофлотационное извлечение труднорастворимых соединений титана
(TiO2, Ti3N4, Ti(OH)4, карбида кремния, карбида железа и оксида скандия
Материалы на основе диоксида титана распространены в различных отраслях промышленности: лакокрасочной, пищевой, химической, фармакологической,
машиностроительной, в производстве косметики и бумаги. Причиной тому является широкий набор специфических физико-химических свойств диоксида титана [289, 290].
Наряду с оксидами титана находят практическое применение керамические материалы на основе его нитридов и карбидов, которые обладают высокой прочностью,
твердостью, высокими температурами плавления и износостойкостью, что определяет их использование в специальных областях промышленности, в частности в авиации.
В сточные воды диоксид титана может попадать различными путями (в
зависимости от назначения в рассматриваемой технологии): вместе с растворителями,
после разложения катализатора, при уносе катализатора с потоком сырья и реагентов, при обработке поверхности титана и его сплава, промывки оборудования и т. п.
Порошки труднорастворимых соединений титана TiO2, TiC, TiN, Ti(OH)4 попадают в сточные воды при использовании золь-гель технологий для получения композиций,
изделий специального назначения, а также при промывке реакторов, уборке помещений,
где работают с мелкодисперсными порошками (1–10 мкм). Соединения TiCl4, Ti(OH)2Cl, Ti(OH)3Cl, Ti(OH)4 применяются как эффективные коагулянты в процессе очистки сточных вод [291–295].
Публикуются обзоры по коллоидно-химическим свойствам TiO2 в водных растворах электролитов [296, 297], их электрокинетическим потенциалам и
144
изоэлектрическим точкам (ζ=0). Указанная информация представляет практический интерес для электрофлотационных процессов.
Отдельно следует упомянуть, что диоксид титана в больших количествах содержится в виде твердых отходов. Так, красные шламы, в зависимости от состава применяемых бокситов, содержат 12–30% TiO2 (нередко в виде перовскита). Разработаны методы концентрирования различных компонентов красных шламов, включая диоксид титана и соединения скандия [298, 299].
Рассмотрим результаты ЭФ извлечения порошков неорганических материалов таких как TiO2, Ti3N4, Ti(OH)4, Sc2O3, а также SiC и оксидов из водных растворов электролитов в присутствии флокулянтов, ПАВ, коагулянтов и композиций коагулянт– ПАВ.
Проведено исследование электрофлотационного извлечения порошков оксида и нитрида титана из водных растворов. Установлено, что в растворе сульфата натрия максимальное значение степени извлечения 25–30% наблюдается в присутствии NaDDS
рН 2–11. В хлоридном растворе степень извлечения TiO2 10–15%, в присутствии NaDDS 43–45%. В таблице 4.9. представлены ξ-потенциал и размер частиц TiO2
Таблица 4.9 – Влияние рН раствора на ξ-потенциал и размер частиц TiO2
Параметр |
NaCl, pH |
|
|
|
Na2SO4, pH |
|
|
|
|||
3 |
5 |
7 |
9 |
11 |
3 |
5 |
7 |
9 |
11 |
||
|
|||||||||||
ξ±, мВ |
+16 |
+7 |
–14 |
–40 |
–44 |
–12 |
–15 |
–30 |
–36 |
–39 |
|
Ø, мкм крупн, |
5,5 |
7,2 |
11 |
10 |
8 |
32 |
19 |
15 |
28 |
22 |
|
% |
76 |
85 |
80 |
72 |
98 |
59 |
52 |
69 |
52 |
56 |
|
Ø, мкм мелк., |
0,5 |
0,2 |
0,4 |
0,3 |
0,1 |
0,6 |
0,4 |
0,6 |
0,6 |
0,4 |
|
% |
14 |
15 |
20 |
28 |
2 |
41 |
48 |
31 |
78 |
44 |
Условия эксперимента: с электролита –1 г/дм3; с TiO2 – 50 мг/ дм3.
Установлено, что величина ξ±-потенциала дисперсной фазы Ti(IV) зависит от рН.
Низкая эффективность извлечения в NaCl связана с малым размером частиц, в Na2SO4
торможение процесса электрофлотации связано с высокими отрицательными значениями
ξ±-потенциала (от –12 до – 40 мВ) и большим процентом частиц размером менее 1 мкм.
Эффективность процесса существенно возрастает в области рН 7±0,5 при добавлении коагулянтов Fe3+ и Al3+ степень извлечения возрастает до 85–90% ввиду малого размера частиц (10-15 мкм).

145
Экспериментальные данные приведены в таблице 4.10. Коагулянт TiCl4 работает неэффективно.
Таблица 4.10 – Влияние коагулянтов Fe3+, Al3+, Ti4+ на электрофлотационное извлечение диоксида титана в растворах с различным значением рН
|
без |
|
|
Степень извлечения, α, % |
|
|
|||
рН |
FeCl3, мг/л |
|
AlCl3, мг/л |
|
TiCl4, мг/л |
||||
коагулянта |
|
|
|||||||
|
5 |
10 |
|
5 |
10 |
5 |
|
10 |
|
|
|
|
|
||||||
3,0 |
45 |
|
|
- |
|
5 |
|
14 |
|
6,5 |
14 |
86 |
53 |
|
90 |
86 |
20 |
|
11 |
7,5 |
14 |
34 |
53 |
|
27 |
79 |
17 |
|
8 |
9,5 |
10 |
18 |
13 |
|
42 |
44 |
6 |
|
26 |
Условия эксперимента: с NaCl – 1 г/ дм3; с TiO2 – 50 мг/ дм3; Jv – 0,4 А/дм3; τ – 30 мин.
Эффективность процесса электрофлотационного извлечения диоксида титана (IV)
возрастает до 96–98% при добавлении в раствор композиции Fe3+ – ПАВ. Результаты экспериментов приведены в таблице 4.11.
Установлено, что при добавлении композиции Fe(OH)3–ПАВ эффективность извлечения TiO2 возрастает в широком диапазоне pH до 90–96%. В щелочной области рН в связи с отрицательным зарядом дисперсной фазы, эффективность возрастает в присутствии катионного флокулянта Zetag 8737.
Таблица 4.11 – Влияние флокулянтов, коагулянта, ПАВ и рН на степень извлечения TiO2
из водных растворов NaCl
|
|
|
|
Степень извлечения, α, % |
|
||||
рН |
Без |
|
FeCl3 + |
FeCl3 |
+ |
FeCl3 |
|
|
|
FeCl3 |
+СЕПТ |
Флокулянты |
|
||||||
|
добавок |
NaDBS |
ПЭО-1500 |
|
|||||
|
|
АПАВ |
|
|
|
||||
|
|
|
|
|
|
|
|
|
|
5 |
5 |
74 |
94 |
92 |
|
90 |
М345 (а) |
|
63 |
7 |
7 |
14 |
96 |
98 |
|
92 |
Ferocryl 8737 (н) |
|
31 |
9 |
4 |
8 |
97 |
90 |
|
94 |
Zetag 8737 (к) |
|
95 |
Условия эксперимента: с TiO2 – 50 мг/л; с NaCl – 1 г/л; с флокулянта – 10 мг/л;
с ПАВ – 5 мг/л; с FeCl3 – 10 мг/л; Jv = 0,2 А/л.
* фильтрация без добавок – 60%; ** – фильтрация с добавками – 99–99,9%.
При введении ПАВ и коагулянтов показано расширение диапазона концентраций
TiO2, который можно извлекать в ЭФ процессе с 50–100 мг/л до 300–400 мг/л. Указанный
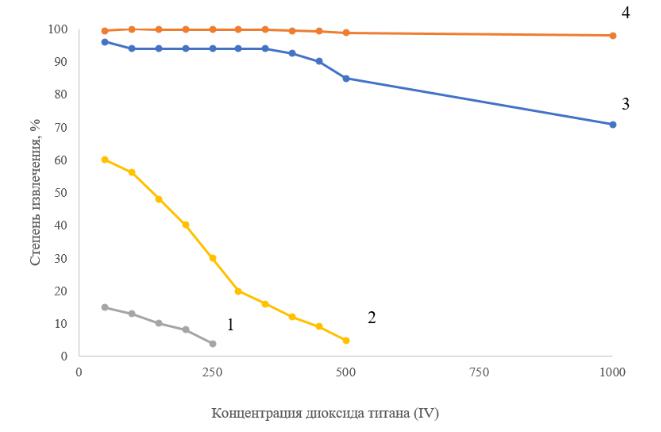
146
эффект связан с увеличением размера флотокомплекса TiO2–коагулянт–ПАВ и гидрофобизацией поверхности коагулянта Fe(OH)3 за счет адсорбции молекул ПАВ.
Рисунок 4.4 – Влияние исходной концентрации TiO2 на степень электрофлотационного и фильтрационного извлечения дисперсной фазы: 1 – без добавок; 2 – FeCl3;
3 – FeCl3 + ПАВ (а); 4 – фильтрация: условия эксперимента: с NaCl – 1 г/л;
с ПАВ – 5 мг/л; с FeCl3 – 10 мг/л; рН = 7; τ – 20 мин; 1 – Jv – 0,2 А/л; 2 – 4 – Jv – 0,4 А/л
На примере порошка TiO2 разных концентраций проведено исследование по влиянию объемной плотности тока на степень извлечения TiO2. Как и для большинства ранее исследованных систем (гидроксиды металлов), для более высокой концентрации взвешенных веществ необходима более высокая величина газонасыщения, что ведет к росту оптимальных значений объемной плотности тока в лабораторных аппаратах в 2–3
раза при изменении концентраций от 100 до 500 мг/л. Экспериментальные зависимости представлены на рисунке 4.5.
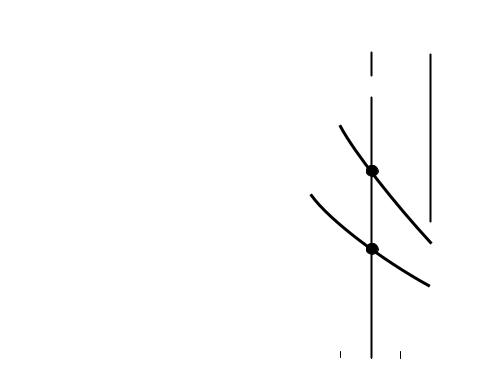
147
0,8 |
А/л |
Рисунок 4.5 – Зависимость степени извлечения ВВ (TiO2) от объемной плотности тока при различных концентрациях осадка: 1 – с ВВ – 100–150 мг/л; 2 – с ВВ – 200–250 мг/л;
3 – с ВВ – 400–500 мг/л: условия эксперимента: pH = 7,0; с ПАВа – 10 мг/л;
с Fe3+ – 25 мг/л
Изучен электрофлотационный процесс извлечения нитрида титана (порошок
10–15 мкм) в двух растворах электролитов – NaCl и Na2SO4. Установлено, что процесс протекает неэффективно, степень извлечения 5–8%. В присутствии коагулянта Fe(OH)3
степень извлечения возрастает до 80–85%. При введении композиции «Fe3+–ПАВ» степень извлечения в сульфате натрия возрастает до 93%, в хлориде натрия до 98%.
Экспериментальные данные представлены в таблице 4.12.
Таблица 4.12 – Влияние композиции «коагулянт Fe3+ – ПАВ» на электрофлотационное извлечение нитрида титана
|
|
|
|
Степень извлечения, α, % |
|
|||
Время, |
|
|
Na2SO4 |
|
|
|
NaCl |
|
мин |
без |
Fe3+ |
Fe3+ |
Fe3+ |
без |
Fe3+ |
Fe3+ |
Fe3+ |
|
АЛМ-10 (н) |
NaDBS (а) |
АЛМ-10 (н) |
NaDBS (а) |
||||
|
|
|
|
|
||||
5 |
4 |
88 |
3 |
63 |
3 |
76 |
46 |
56 |
10 |
5 |
82 |
4 |
79 |
5 |
87 |
25 |
63 |
20 |
8 |
85 |
3 |
93 |
5 |
80 |
28 |
98 |
Условия эксперимента: с TiN – 50 мг/л; с электролита – 1 г/л; с ПАВ – 5 мг/л;
с FeCl3 – 10 мг/л; Jv – 0,2 А/л; рН – 7±0,5
148
Более низкие значения степени извлечения в Na2SO4 связаны со специфической адсорбцией ионов SO42- на дисперсной фазе Fe(OH)3 на местах, где адсорбируется анионный ПАВ.
Анализ зависимости электрокинетического потенцаила от кислотности среды для для неорганической дисперсной фазы порошка нитрида титана показывает, что ионы
H3O+ (OH-) являются потенциалопределяющими и формируют двойной электрический слой, точно так же, как и на оксидах и гидроксидах металла (см. Ti(OH)4)
изоэлектрическая точка (ξ± = 0) в инактивном электролите NaCl составляет рН0 = 3,5±0,2.
Экспериментальные данные по размеру частиц и электрокинетическому потенциалу представлены в таблице 4.13.
Таблица 4.13 – Электрокинетический потенциал и средний размер частиц нитрида титана в растворах электролитов
рН |
|
NaCl |
|
Na2SO4 |
|
|
ξ±, мВ |
Ø, мкм |
ξ±, мВ |
|
Ø, мкм |
||
|
|
|||||
3 |
+4 |
16 |
0 |
12 |
|
65% |
0,8 |
|
35% |
||||
|
|
|
|
|
||
4 |
–6 |
18 |
-10 |
14 |
|
59% |
0,8 |
|
41% |
||||
|
|
|
|
|
||
6 |
–13 |
18 |
-18 |
11 |
|
55% |
0,6 |
|
45% |
||||
|
|
|
|
|
||
8 |
–19 |
19 |
-36 |
12 |
|
75% |
0,6 |
|
25% |
||||
|
|
|
|
|
||
10 |
–19 |
20 |
-36 |
16 |
|
30% |
0,6 |
|
70% |
||||
|
|
|
|
|
||
11 |
–20 |
18 |
-37 |
13 |
|
45% |
0,6 |
|
55% |
||||
|
|
|
|
|
Условия эксперимента: с электролита – 1 г/дм3; с TiN – 50 мг/ дм3.
В растворе NaCl средний диаметр частиц 18–20 мкм; в Na2SO4 размер частиц меньше, 40–60% частиц имеют размер 12–15 мкм, и ~50% частиц размером 0,6–0,8 мкм.
Фотографии осадка в увеличении показывают, что структура TiN состоит из мелких округлых частиц разных размеров. Отметим, что частица TiO2 имеет хлопьевидную структуру, с развитой поверхностью, более приемлемую для захвата пузырьками H2 и O2
в процессе электрофлотации.
Исследован электрофлотационный процесс извлечения карбида кремния из водных растворов Na2SO4, NaNO3 без флокулянтов и при добавлении флокулянтов различной природы (анионной, катионной, неионогенной).
149
Установлено, что в растворах электролитов pH=2–12, степень извлечения низкая и составляет после 30 мин электрофлотации 5–15%. В таблице 4.13 представлен средний размер и заряд частиц в электролитах NaCl и NaNO3. Установлено, что в системе присутствуют крупные частицы размером 15–25 мкм (70–80%) и мелкие частицы размером 0,1–0,6 мкм (20–30%). Вследствие гидратации поверхности SiC ионы H3O+
являются потенциалопределяющими. Величина ζ-потенциала снижается в NaCl с –3 мВ
(pH=3) до –28 мВ (pH=11). В Na2SO4 наблюдается специфическая адсорбция сульфат анионов на дисперсной фазе SiC. С учетом величины и знака ζ-потенциала исследовано влияние добавок ПАВ на ЭФ процесс. Установлено положительное воздействие ПАВ в растворе Na2SO4 (таблица 4.14). Для карбида кремния характерно наличие как крупных
(более 10 мкм), так и мелких (менее 0,5 мкм) частиц, доля которых не менее 20%.
Таблица 4.14 – Размер и электрокинетический потенциал частиц SiC в хлоридных и сульфатных растворах электролитов с различным значением рН
pH |
|
|
Na2SO4 |
|
|
|
|
NaCl |
|
||
|
R, мкм |
% |
|
ξ±, мВ |
|
R, мкм |
|
% |
|
ξ±, мВ |
|
|
|
|
|
|
|
||||||
3 |
|
0,5 |
22 |
|
–12 |
|
0,3 |
|
13 |
|
–3 |
|
|
30 |
78 |
|
|
26 |
|
87 |
|
||
|
|
|
|
|
|
|
|
||||
5 |
|
0,4 |
27 |
|
–20 |
|
0,3 |
|
26 |
|
–15 |
|
|
13 |
73 |
|
|
16 |
|
74 |
|
||
|
|
|
|
|
|
|
|
||||
7 |
|
0,3 |
33 |
|
–26 |
|
0,1 |
|
3 |
|
–23 |
|
|
20 |
67 |
|
|
19 |
|
97 |
|
||
|
|
|
|
|
|
|
|
||||
9 |
|
0,3 |
42 |
|
–28 |
|
0,3 |
|
19 |
|
–26 |
|
|
14 |
58 |
|
|
22 |
|
81 |
|
||
|
|
|
|
|
|
|
|
||||
11 |
|
0,5 |
44 |
|
–37 |
|
0,3 |
|
34 |
|
–28 |
|
|
19 |
56 |
|
|
26 |
|
66 |
|
||
|
|
|
|
|
|
|
|
||||
11 + Септапав |
|
0,7 |
20 |
|
–6 |
|
0,4 |
|
21 |
|
–23 |
|
|
19 |
80 |
|
|
28 |
|
79 |
|
||
|
|
|
|
|
|
|
|
||||
11+ С-496 |
|
0,5 |
70 |
|
–34 |
|
0,4 |
|
26 |
|
–20 |
|
|
8,0 |
30 |
|
|
26 |
|
74 |
|
||
|
|
|
|
|
|
|
|
||||
Условия эксперимента: с электролита – 1 г/л; с SiC – 50 мг/л; с добавка – 5 мг/л. |
|||||||||||
Относительно |
высокая |
степень |
извлечения |
наблюдается |
во всем |
диапазоне |
pН 2–11, максимальное значение 50–70% при рН 6–7. Высокие степени извлечения SiC в
растворах Na2SO4 в присутствии ПАВ связаны с гидрофобизацией поверхности карбида кремния, а именно замена ОН- на ионы SO42- и замена Н2О ↔ ПАВн (а), а также адсорбцией катионного ПАВ на отрицательно заряженных участках поверхности SiC.
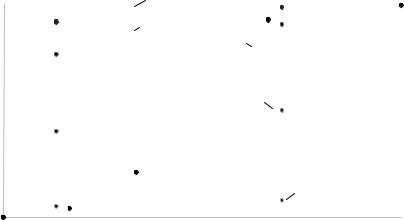
150
Таблица 4.15 – Влияние рН раствора и природы поверхностно-активных веществ на
эффективность электрофлотационного процесса извлечения карбида кремния в присутствии различных фоновых электролитов
pH |
Na2SO4 |
ПАВ + |
NaNO3 |
ПАВ + |
NaCl |
ПАВ + |
Природа ПАВ |
|
Na2SO4 |
NaNO3 |
NaCl |
||||||
|
|
|
|
|
||||
2 |
13 |
29 |
11 |
19 |
10 |
24 |
NaDBS (а) |
|
3 |
4 |
31 |
11 |
25 |
3 |
31 |
||
|
||||||||
6 |
8 |
66 |
6 |
6 |
6 |
26 |
АЛМ-10 (н) |
|
7 |
8 |
46 |
6 |
6 |
5 |
25 |
||
|
||||||||
11 |
5 |
35 |
2 |
4 |
2 |
1 |
СЕПТАПАВ |
|
12 |
2 |
10 |
2 |
2 |
2 |
4 |
ХСВ.50 (к) |
Условия эксперимента: с фон – 1 г/л; с SiC – 50 мг/л; с ПАВ – 5 мг/л; Jv – 0,4 А/л; τ – 30 мин.
Фильтрация во всех случаях позволяет достичь степени извлечения SiC – 99%. При добавлении коагулянтов Al3+, Fe3+ эффективность ЭФ SiC возрастает до 40% в
присутствии AlCl3 и 80% FeCl3. Экспериментальные данные представлены на рисунке 4.6.
Наиболее эффективно процесс протекает при добавлении флокулирующей композиции Al3+ – ПАВа, Fe3+ – ПАВ (кривая 5, 6). Стационарные значения степени извлечения устанавливаются за 10 мин. Степень извлечения достигает 95–98%.
Остаточное содержание Fe, Al не более 0,1 мг/л.
Степень извлечения, %
100 |
|
|
5 |
|
|
|
|
|
|
|
|
|
|
90 |
|
3 |
|
|
|
|
80 |
|
|
|
2 |
|
|
70 |
|
|
|
|
|
|
60 |
|
|
|
|
|
|
|
|
|
|
4 |
|
|
50 |
|
|
|
|
|
|
40 |
|
|
|
|
|
|
30 |
|
|
|
|
|
|
20 |
|
|
|
|
|
|
10 |
|
|
|
|
1 |
|
|
|
|
|
|
|
|
0 |
|
|
|
|
|
|
0 |
5 |
10 |
15 |
20 |
25 |
30 |
|
|
|
Время, |
мин |
|
|
Рисунок 4.6 – Влияние добавок коагулянтов, ПАВ на кинетику процесса электрофлотационного извлечения карбида кремния: 1 – без добавок; 2 – АЛМ-10; 3 – FeCl3; 4 – AlCl3; 5 – композиция аПАВ + AlCl3; 6 – аПАВ + FeCl3: условия эксперимента: с Na2SO4 – 1 г/л; с SiC – 50 мг/л; с ПАВ – 5 мг/л; с AlCl3 – 5 мг/л;
с FeCl3 – 5 мг/л; Jv – 0,4 А/л; pH = 6
151
Проведены исследования по ЭФ извлечению порошка карбида железа. Состав порошка представлен в подразделе 2.4. Микрофотографии карбида железа на конфокальном микроскопе представлены в подразделе 5.2.
Проведенные исследования ЭФ процесса показали, что степень извлечения порошка карбида железа не превышает 10% в растворах NaCl и 20% в растворах сульфата натрия. Влияние коагулянтов и ПАВ представлено в таблицах 4.16 и 4.17 для двух растворов электролитов.
Таблица 4.16 – Влияние коагулянтов Al+3, Fe+3, UltraPAC и композиции коагулянт – ПАВа на ЭФ извлечение порошка карбида железа
τ, |
|
|
Степень извлечения α, % |
|
|
|||
|
Al+3 |
Al+3+П |
UltraPAC+ |
UltraPAC+ |
Fe+3 |
Fe+3+ПАВ |
||
мин |
Без коаг. |
|||||||
коаг. |
АВ |
Al+3 |
ПАВ |
|||||
|
|
|
|
|||||
5 |
6 |
12 |
55 |
59 |
10 |
75 |
68 |
|
10 |
7 |
15 |
91 |
69 |
79 |
88 |
87 |
|
20 |
9 |
16 |
93 |
81 |
80 |
83 |
76 |
|
30 |
10 |
18 |
95 |
85 |
78 |
80 |
76 |
Условия эксперимента: с NaCl – 1 г/л; с Fe3C – 50 мг/л; с коагулянта – 50 мг/л; с ПАВNaDDS – 5 мг/л; Jv – 0,2 А/л; pH – 7,0.
Таблица 4.17– Влияние коагулянтов Al+3, Fe+3, UltraPAC и композиции коагулянт – ПАВА на ЭФ извлечение порошка карбида железа
|
|
|
|
Степень извлечения α, % |
|
|
|||
τ, |
Без |
Al+3 |
Al+3+П |
|
UltraPAC+ |
UltraPAC+ |
|
Fe+3 |
Fe+3+ПАВ |
мин |
коаг. |
коаг. |
АВ |
|
Al3+ |
ПАВ |
|
||
|
|
|
|
||||||
5 |
12 |
15 |
52 |
|
5 |
41 |
|
66 |
52 |
10 |
18 |
11 |
93 |
|
21 |
71 |
|
82 |
70 |
20 |
20 |
10 |
95 |
|
28 |
80 |
|
65 |
80 |
30 |
22 |
7 |
96 |
|
45 |
90 |
|
54 |
90 |
Условия эксперимента: с Na2SO4 – 1 г/л; с Fe3C – 50 мг/л; с |
коагулянта – 50 мг/л; |
с ПАВNaDDS – 5 мг/л; Jv – 0,2 А/л; pH – 7,0.
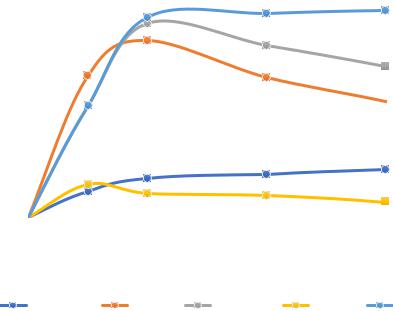
152
Степень извлечения α, %
100
5
80
3
60
2
40
1
20
4
0
0 |
5 |
10 |
15 |
20 |
25 |
30 |
35 |
τ, мин
1 - Без коаг |
2 - Fe+3 |
3 - Fe+ПАВ |
4 - Al+3 |
5 - Al+ПАВ |
Рисунок 4.7 – Влияние коагулянтов Al+3, Fe+3, UltraPAC и композиции коагулянт – ПАВА на ЭФ извлечение порошка карбида железа: условия эксперимента:
с Na2SO4 – 1 г/л; с FeC – 50 мг/л; с коагулянта – 50 мг/л; с ПАВNaDDS – 5 мг/л; Jv – 0,2 А/л; pH = 7,0; 1 – без коагулянта, 2 – Fe3+, 3 – Fe3+ + ПАВа, 4 – Al3+, 5 – Al3++ ПАВа
Проведены исследования ЭФ процесса извлечения оксидов скандия Sc2O3 –
товарного продукта. Оксиды скандия представлены в виде порошка белого цвета. В
сточных водах Sc2O3 встречается в процессах производства, а также при термической обработке гидроксида скандия. Проведенные исследования показали, что в растворах
NaCl, NaNO3 и Na2SO4 в интервале pH = 2–12 содержание оксида скандия составляет
96–97 % в нерастворимом виде, который может быть извлечен из сточных вод фильтрацией, флотацией и декантацией.
Полученные результаты ЭФ извлечения Sc2O3 показывают, что максимальные значения степени извлечения достигают 50–55 %. Низкие значения величины α связаны в первую очередь с размером частиц Sc2O3. В основном извлекаются частицы размером
20–25 мкм, более мелкие частицы не извлекаются. Природа электролита, pH раствора не оказывают существенного значения на электрофлотационный процесс.
Экспериментальные данные представлены в таблице 4.18.
153
Таблица 4.18 – Влияние природы электролита, размера частиц и ξ±-потенциала на степень извлечения Sc2O3
Электролит |
|
Параметры |
|
|
ξ±, мВ |
Øср, мкм |
α20, % |
||
|
||||
NaCl |
-2 |
38 |
96 |
|
NaNO3 |
+4 |
31 |
99 |
|
Na2SO4 |
-6 |
39 |
93 |
|
Na2CO3 |
-6/-8* |
29/33* |
56/90* |
Условия эксперимента: с электролита – 1 г/л; Jv – 0,4 А/л; τ – 20 мин;
с Sc – 50, 100 мг/л; pH – 7±0,5; *с ПАВ – 5 мг/л NaDDS.
Необходимо отметить, что высокие значения степени извлечения Sc(OH)3 связаны с большим размером частиц и небольшим значением ζ-потенциала, что характерно для большинства исследованных объектов, гидроксидов металлов. Установлено, что для порошка оксида Sc2O3 ионы H3O+, OH- являются потенциалопределяющими и приводят к изменению величины и знака заряда поверхности (ζ-потенциала) от pH.
Экспериментальные данные приведены в таблице 4.19.
Таблица 4.19 – Влияние pH раствора на величину ζ-потенциала Sc2O3
Электролит |
|
|
pH, ζ-потенциал |
|
|
|
3 |
5 |
7 |
|
9 |
11 |
|
|
|
|||||
Na2SO4 |
+6 |
–7 |
–12 |
|
–16 |
–40 |
NaCl |
+12 |
+2 |
-5 |
|
–15 |
–35 |
Условия эксперимента: с Sc2O3 – 50 мг/л; pH = 3 – 11; с электролита – 1 г/л.
Низкие значения величины α при pH = 12 связаны с поверхностными свойствами порошка, в частности с формированием высокого отрицательного заряда поверхности
(ζ = 35-40 мВ), что приводит к низкой эффективности ЭФ процесса.
Добавление в водный раствор электролитов и ПАВ (СептаПАВ – катонный) ведет к повышению степени извлечения до 82%, катионный ПАВ типа КатоПАВ оказывает положительное влияние, повышая степень извлечения до 60–70%. Экспериментальные данные представлены в таблице 4.20.
154
Таблица 4.20 – Электрофлотационное извлечение порошка Sc2O3 в присутствии различных ПАВ в растворах электролитов NaCl, NaNO3, Na2SO4
Электролит |
|
|
α, % |
|
|
|
без ПАВ |
NaDDS (а) |
СептаАПВ (к) |
КатаПАВ (к) |
АЛМ-10 (н) |
||
|
||||||
NaCl |
55 |
90 |
82 |
66 |
36 |
|
Na2SO4 |
37 |
92 |
82 |
56 |
31 |
|
NaNO3 |
17 |
90 |
64 |
60 |
22 |
Условия эксперимента: с Sc2O3 – 50 мг/л; с электролита – 1 г/л; с ПАВ – 5 мг/л; Jv – 0,2
А/л; pH – 8; τ – 20 мин.
Положительное влияние катионных ПАВ связано с изменением заряда частиц
Sc2O3 в сторону положительных значений, что благоприятно сказывается на ЭФ процесс.
Влияние неионогенного ПАВ АЛМ-10 в ЭФ процессе не проявляется.
Известно, что анионные ПАВ часто используются для гидрофобизации поверхности оксидов и гидроксидов, что ведет к повышению эффективности в ЭФ процессе.
Положительный эффект обнаружен для порошка Sc2O3, степень извлечения повышается до 90–92% в присутствии ПАВ.
Таблица 4.21 – Электрофлотационное извлечение порошка Sc2O3 в водных растворах различного состава и значения pH
pH |
|
|
|
α, % |
|
|
|
NaCl |
* |
NaNO3 |
* |
Na2SO4 |
* |
||
|
|||||||
2 |
6 |
- |
27 |
- |
54 |
- |
|
4 |
29 |
93 |
33 |
90 |
32 |
88 |
|
6 |
34 |
96 |
19 |
95 |
36 |
90 |
|
8 |
45 |
96 |
17 |
95 |
37 |
90 |
|
10 |
40 |
- |
15 |
- |
16 |
|
|
12 |
30 |
- |
7 |
- |
16 |
- |
Условия эксперимента: с Sc2O3 – 50 мг/л; с электролит – 1 мг/л; τ – 20 мин; Jv – 0,2 А/л;
αфильт – 96 %; pH = 2–10
В присутствии композиций Fe(OH)3–ПАВа, Al(OH)3–ПАВа, как и в случае других порошков, наиболее высокие степени извлечения 90–96% достигаются при добавлении композиции гидроксидов (Fe, Al)–ПАВ.
Рассмотрим результаты ЭФ извлечения труднорастворимых соединений Ti(IV)
хлоридных растворах в широком диапазоне pH.
155
Анализ растворов, проведенных после фильтрации осадков на основе Ti(IV),
показал, что в диапазоне рН 2–12 98–99% титана находится в дисперсной фазе и может быть удалено фильтрацией, седиментацией и электрофлотацией. В указанном диапазоне
Ti(IV) существует в виде [Ti(OH)2Cl]2+; [Ti(OH)3Cl]+; [Ti(OH)4·nH2O]0; [Ti(OH)5]-Na+.
Установлено, что процесс осаждения осадка Ti(OH)4 протекает медленно и неэффективно. За 180 мин степень осаждения при рН 4,0 (вблизи изоэлектрической точки) 60%. При рН 7–10 степень осаждения 45–50%. Для использования Ti(IV) в
качестве коагулянта, необходимо добавление флокулянта анионного типа при рН 2–4,
неионогенного при рН 4–8, катионного рН 8–12.
Исследован процесс электрофлотации труднорастворимых соединений Ti(IV) в
широком диапазоне рН 2–12.
Зависимость α = f(pH) представлена на рисунке 4.8. Установлено, что максимальная степень извлечения наблюдается при рН 3±0,5. Величина степени извлечения 92–98%.
В нейтральной области рН 5–7 степень извлечения не превышает 10–15%, при рН 8–9 степень извлечения 60–80%. Низкие значения α в нейтральной области рН связаны с высокой гидрофильностью поверхности Ti(OH)4·nH2O, что затрудняет электрофлотационный процесс.
Добавление анионного ПАВ (кривая 3) приводит к росту степени извлечения за счет гидрофобизации поверхности гидроксида титана. Катионный ПАВ оказывает положительное влияние в области рН 8–11, где создаются благоприятные условия для его адсорбции (кривая 2).
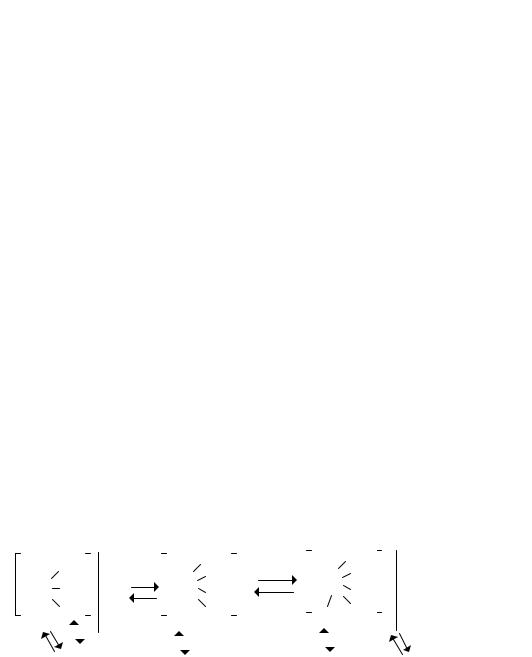
156
Степень извлечения, %
100 |
|
|
|
|
|
|
|
|
|
|
|
|
|
90 |
|
|
|
|
|
|
|
|
|
|
|
|
|
80 |
|
|
|
|
|
|
|
|
|
|
|
3 |
|
|
|
|
|
|
|
|
|
|
|
|
|
|
|
70 |
|
|
|
|
|
|
|
|
|
|
|
|
|
|
|
|
|
|
|
|
|
|
|
|
|
2 |
|
60 |
|
|
|
|
|
|
|
|
|
|
|
|
|
50 |
|
|
|
|
|
|
|
|
|
|
|
|
|
40 |
|
|
|
|
|
|
|
|
|
|
|
|
|
30 |
|
|
|
|
|
|
|
|
|
|
|
1 |
|
|
|
|
|
|
|
|
|
|
|
|
|
|
|
20 |
|
|
|
|
|
|
|
|
|
|
|
|
|
10 |
|
|
|
|
|
|
|
|
|
|
|
|
|
0 |
|
|
|
|
|
|
|
|
|
|
|
|
|
0 |
1 |
2 |
3 |
4 |
5 |
6 |
7 |
8 |
9 |
10 |
11 |
12 |
13 |
|
|
|
|
|
|
pH |
|
|
|
|
|
|
|
|
|
|
1 |
без ПАВ |
|
2 |
Катинол |
|
3 |
NaDDS |
|
|
|
Рисунок 4.8 – Влияние pH на ЭФ извлечение труднорастворимых соединений титана: 1 – без ПАВ; 2 – ПАВ катионный (Катинол); 3 – ПАВ анионный (NaDDS): условия эксперимента: τ – 20 мин; с NaCl – 1 г/л; с Ti (IV) – 50 мг/л; Jv – 0,4 А/л; с ПАВ – 5 мг/л
Схематично процесс адсорбции ПАВ на гидроксиде титана представлен на рисунке 4.9.
|
|
|
|
|
|
+ σ |
|
|
|
|
|
|
|
0 |
|
|
|
|
+ σ |
|
|
|
|
OH |
|
|
|
|
|
|
OH |
|
|
|
|
|
OH |
|
|
||||
Ti |
|
|
|
Ti |
|
OH |
|
|
|
Ti |
O |
|
+ |
||||||||
OH |
|
- |
|
|
OH |
|
|
|
OH |
|
|||||||||||
.. |
|
|
|
|
Cl |
|
.. |
|
|
|
|
|
|
|
OH |
|
Na |
||||
H O |
OH |
|
|
|
H O |
OH |
|
|
|
H O |
|
|
|||||||||
|
|
|
|
|
|
|
|
|
|||||||||||||
|
|
|
|
|
|
|
|
|
|
|
|
|
|||||||||
2 |
|
|
|
|
|
|
|
|
|
|
|
|
|
|
|||||||
|
|
|
|
|
|
|
|
|
|
|
2 |
|
|
|
|||||||
|
|
|
|
|
|
|
2 |
|
max |
|
|
|
|
|
|
|
|
|
|||
|
|
|
|
|
|
|
|
|
|
|
|
|
|
|
|
|
|
|
|
|
|
|
|
|
|
|
|
|
|
|
|
|
|
|
|
|
|
||||||
|
|
ПАВа |
ПАВа |
|
|
|
ПАВа |
ПАВк |
|||||||||||||
|
|
|
|
|
|
|
|
|
|
|
|
|
|
|
|
|
|
|
|
|
|
рН < pH0 |
|
|
pH0 |
|
|
|
рН > pH0 |
|
|
|
|||||||||||
|
|
|
|
|
|
|
|
|
|
|
|
||||||||||
pH 3 - 4 |
|
|
pH 6 - 7 |
|
|
|
pH 8 - 9 |
|
|||||||||||||
ξ |
+ |
|
|
|
|
|
|
ξ |
0 |
|
|
|
|
|
ξ - |
|
|
|
|||
|
|
|
|
|
|
|
|
|
|
|
|
|
|
|
|
|
|
|
|
Рисунок 4.9 – Схема процесса адсорбции ПАВ на гидроксиде титана Исследовано влияние pH и добавок ПАВ на кинетику ЭФ процесса извлечения
дисперсной фазы Ti (IV). Экспериментальные данные представлены в таблице 4.22.
157
Таблица 4.22 – Влияние pH среды на степень извлечения дисперсной фазы Ti(IV)
τ, мин |
|
|
|
pH |
|
|
|
2 |
3 |
4 |
5 |
6 |
7 |
||
|
|||||||
5 |
0 |
91 |
8 |
0 |
0 |
0 |
|
10 |
17 |
97 |
20 |
1-2 |
1-2 |
1-2 |
|
20 |
30 |
98 |
60 |
5 |
5 |
5 |
|
фильтрация |
99 |
99 |
99 |
99 |
99 |
99 |
Условия эксперимента: с Ti4+ – 200 мг/л; с NaCl – 0,5 г/л; Jv – 0,4 А/л.
Из данных таблицы видно, что степень извлечения практически на всем интервале pH не превышает 5%, однако степень электрофлотационного извлечения ионов Ti4+ в
растворе с pH = 3 достигает 91% за 5 мин обработки.
Анализ показывает, что кинетика процесса извлечения дисперсной фазы Ti(IV)
существенно зависит от pH среды, наиболее эффективно процесс протекает при pH = 3±0,5. В этом же диапазоне pH положительное влияние на ЭФ процесс оказывает анионный ПАВ – NаDDS, NaDBS, вследствие гидрофобизации поверхности дисперсной фазы Ti (IV). Некоторые экспериментальные данные представлены в таблице 4.23.
Таблица 4.23 – Влияние pH среды и природы ПАВ на степень извлечения дисперсной фазы Ti(IV)
pH |
τ, мин |
|
|
α, % |
|
|
|
Без ПАВ |
Катинол |
NaDDS |
NaDBS |
СептаПАВ |
|||
|
|
||||||
|
5 |
74 |
78 |
83 |
95 |
90 |
|
2,5 |
10 |
95 |
97 |
96 |
99 |
92 |
|
|
20 |
99 |
99 |
99 |
99 |
96 |
|
|
5 |
91 |
89 |
93 |
90 |
88 |
|
3,0 |
10 |
97 |
97 |
96 |
97 |
96 |
|
|
20 |
97 |
99 |
98 |
97 |
98 |
|
|
5 |
2 |
10 |
18 |
12 |
16 |
|
3,5 |
10 |
20 |
12 |
22 |
18 |
55 |
|
|
20 |
60 |
12 |
32 |
26 |
99 |
Условия эксперимента: с Ti4+ – 200 мг/л; с Cl- – 0.6 г/л; с ПАВ – 5 мг/л, Iv– 0,4А/л.
Исследовано влияние pH на ЭФ процесс извлечения Sc3+ в растворах NaCl, NaNO3, Na2SO4 в диапазоне pH = 3–7. Экспериментальные данные представлены в таблице 4.24.
158
Таблица 4.24 – Степень ЭФ извлечения Sc(OH)3 при различных значениях pH
Электролит |
|
|
α, %, pH |
|
|
|
3 |
4 |
5 |
6 |
7 |
NaCl |
0 |
2 |
12 |
68 |
98 |
NaNO3 |
0 |
1 |
6 |
20 |
99 |
Na2SO4 |
0 |
1 |
3 |
8 |
92 |
Условия эксперимента: τ – 20 мин; Jv – 0,4 А/л; с электролита – 1 г/л; с Sc3+ – 100 мг/л;
рН = 3–7
Результаты исследования показывают, что дисперсная фаза при рН = 3–4
практически не формируется, что важно для возможности селективного разделения.
Исследован электрофлотационный процесс селективного разделения гидроксида металла (Ti(IV)), который формируется при pH = 2–5, и металлов Me(III), которые находятся в ионном виде в растворах электролитов и не извлекаются в виде осадка.
Основной подход к повышению селективности процесса: повысить эффективность извлечения дисперсной фазы за счет применения флокулянтов и ПАВ и снизить соосаждение Me (III) за счет сорбции гидроксидом Me (IV).
Основная задача исследования – определить условия максимального извлечения
Me(OH)4 (электролит, рН раствора, ПАВ, флокулянт) и минимального соосаждения
Me(OH)3 или сорбции Мe (III) на свежесформированном осадке.
Анализ влияния pH на степень извлечения Ti(IV) и Sc(III) показывает, что в кислых растворах при низких концентрациях Sc осадки Sc(OH)3 не формируются. В то же время, Ti(IV) формирует в кислых растворах при pH = 3–6 дисперсную фазу Ti(OH)2Cl2, Ti(OH)3Cl, Ti(OH)4, которая может быть извлечена в ЭФ процессе. Для селективного разделения выбран электролит NaCl как наиболее часто встречаемый для систем Ti(IV) и pH=3, где степень извлечения Ti(IV) достигает 90–95 %. Соотношение компонентов Ti:Sc
выбрано из расчета 1:1; 1:0,5; 1:0,25, максимальная концентрация Ti составляет 100 мг/л.
Необходимо отметить, что для высоких концентраций (более 1000 мг/л) для процессов разделения используют центрифугирование, седиментацию и фильтрацию. В
таблице 4.25 представлены экспериментальные данные по ЭФ в 2-компонентных систем
Ti(IV) – Sc(III).
159
Таблица 4.25 – Влияние ПАВ на степень извлечения Ti(IV) и Sc(III) в составе
2-компонентной смеси
Ti-Sc |
|
|
|
Ti |
|
|
Sc |
|
α10, % |
|
α20, % |
α10, % |
|
α20, % |
|
|
|
|
|
||||
Без добавок |
|
64 |
|
89 |
30 |
|
34 |
+Катинол (к) 5 мг/л |
|
45 |
|
89 |
30 |
|
35 |
+NaDBS (а) 5 мг/л |
|
10 |
|
74 |
10 |
|
15 |
+ПЭО-1500 (н) 5 мг/л |
|
89 |
|
97 |
13 |
|
15 |
+NaDBS (а) 10 мг/л |
|
6 |
|
12 |
2 |
|
5 |
+Катинол (к) 10 мг/л |
|
1-2 |
|
7 |
2 |
|
14 |
+ПЭО-1500 (н) 10 мг/л |
|
20 |
|
65 |
2 |
|
5 |
Условия эксперимента: |
с Ti4+ – 100 |
мг/л; с Sc3+ |
– 25 мг/л; |
pH – 3; τ – 20 мин, |
с ПАВ – 5–10 мг/л; NaCl – 1 г/л.
Анализ показывает, что наибольший положительный эффект извлечения Ti(IV)
наблюдается в присутствии неионогенного ПАВ (ПЭО-1500). Степень извлечения Ti(IV)
достигает 90–97 %, степень извлечения Sc(III) составляет 5–15%. Положительный эффект отмечается при добавлении неионогенного флокулянта N300 в концентрациях 2–5 мг/л.
При высокой концентрации флокулянта (или ПАВ) процесс ЭФ протекает неэффективно из-за преобладания процессов седиментации.
Часто в сточных водах соединения титана присутствуют совместно с ионами алюминия (III). По своим физико-химическим свойствам Al(III) и Sc(III) достаточно близки. Проведены исследования по извлечению соединений Ti(IV) и Al(III) при их совместном присутствии. Экспериментальные данные представлены в таблице 4.26.
Таблица 4.26 – Влияние ПАВ и флокулянтов на степень извлечения Ti(IV) и Al(III)
|
|
|
|
α, % |
|
|
|
Система |
|
Ti(IV) |
|
|
Al(III) |
||
|
10 |
|
20 |
|
10 |
|
20 |
без ПАВ |
16 |
|
45 |
|
0 |
|
2 |
NaDBS (а) |
66 |
|
80 |
|
1 |
|
3 |
NaDDS (а) |
64 |
|
76 |
|
1 |
|
3 |
ПАВ(к) |
2 |
|
5 |
|
12 |
|
30 |
ПАВ(н) |
2 |
|
5 |
|
19 |
|
40 |
флокулянт N300 (а) |
88 |
|
90 |
|
39 |
|
60 |
флокулянт Preastol 5230 (а) |
86 |
|
93 |
|
40 |
|
55 |
Условия эксперимента: с Ti – 10 мг/л; pH = 3; Jv – 0,4 А/л; с NaCl – 0,5 г/л; с ПАВ / флок – 5 мг/л.

160
Анализ показывает, что максимальная степень извлечения Ti (IV) наблюдается в присутствии анионного флокулянта N300, Preastol 5230, анионного ПАВ NaDDS, NaDBS.
В то же время, максимальная селективность извлечения титана 80% наблюдается только для ПАВ анионной природы.
Указанные эффекты влияния ПАВ связаны с гидрофобизацией поверхности дисперсной фазы (Ti (IV), что ведет к росту степени извлечения. Аналогичные эффекты наблюдаются для системы Ti (IV) – Fe (III). Экспериментальные данные представлены в таблице 4.27.
Таблица 4.27 – Влияние природы и концентрации ПАВ на степень извлечения Ti(IV) и
Fe(III)
Добавки |
|
Ti |
|
Fe |
|
α10, % |
|
α20, % |
α10, % |
α20, % |
|
|
|
||||
Без добавок |
5 |
|
40 |
49 |
50 |
NaDBS (а) 5 мг/л |
40 |
|
70 |
1 |
3 |
NaDBS (а) 10 мг/л |
35 |
|
59 |
21 |
23 |
Катинол (к) 5 мг/л |
52 |
|
60 |
0 |
5 |
Катинол (к) 10 мг/л |
3-7 |
|
10 |
0 |
7 |
ПЭО-1500 (н) 5 мг/л |
1-2 |
|
7 |
0 |
2 |
ПЭО-1500 (н) 10 мг/л |
5 |
|
5 |
2 |
10 |
Условия эксперимента: с Fe3+ – 25 мг/л; pH – 3; τ – 20 мин; с NaCl – 0,5 г/л.
Из представленных экспериментальных данных можно сделать вывод, что оптимальной добавкой для данной системы является анионы ПАВ – NaDBS с
концентрацией 5 мг/л. В данных условиях титан извлекается на 70%, а железо практически не извлекается.
Проведены исследования по селективному разделению двухкомпонентной системы Ti(IV) и Me(III) (Ce, Sc, Y, La). Гидроксиды титана хорошо флотируются в области pH = 3±0,5, где ионы Ce, Sc, Y, La в растворах NaCl осадков не образуют.
Для систем Ti (IV) – Me (III) определены максимальные степени извлечения дисперсной фазы Ti (IV) и минимальные степени извлечения Me(III).
На основании анализа концентраций Ti (IV) и Me (III) в исходном растворе и после ЭФ процесса проведены расчеты коэффициента К по формуле:
Kраз Me1 / Me2 = D1/D2, (13)
где D1 и D2 – коэффициенты распределения для каждого металла, D = (сисх – скон)/скон.
161
4.3. Основные закономерности электрофлотационного извлечения труднорастворимых соединений редкоземельных элементов из промывных
вод и технологических растворов. Селективное разделение двухкомпонентных систем: Сe(IV) – Me (III), Ti(IV) – Me (III)
Уникальные физико-химические свойства РЗЭ делают их привлекательными для использования во многих отраслях промышленности. При переработке редкоземельного сырья любого типа первоначально выделяют смесь РЗЭ в виде сульфатов, оксалатов,
карбонатов или гидроксидов, которая затем поступает на разделение с целью получения индивидуальных элементов. Экстракционные процессы являются основными в схемах разделения РЗМ [300–303]. Для извлечения микроколичества РЗЭ из растворов сложносолевого состава, а также разделения [304–306] предложено использование ионообменных смол.
В настоящее время для извлечения и разделения ионов редкоземельных металлов широко внедряются методы поверхностного разделения веществ. В работах [307–315]
проведены исследования разделения и извлечения РЗМ с помощью ионной флотации с использованием поверхностно-активного вещества – додецилсульфата натрия. В
процессе флотации ионы лантаноидов извлекаются додецилсульфатом натрия в форме основных додецилсульфатов. Максимальное извлечение РЗМ в слабокислых,
нейтральных и слабощелочных средах составляет 95%, при этом концентрация ПАВ в растворе должна быть не менее 0,5 г/л.
Описанные выше методы извлечения РЗМ имеют свои преимущества и недостатки.
Для извлечения микроколичеств РЗМ практикуют сорбционные методы, однако к недостаткам можно отнести использование дефицитных материалов и необходимость регенерации сорбентов. Применение ионной флотации требует добавок ПАВ в достаточно больших концентрациях.
Для реализации дополнительной ступени извлечения РЗМ из растворов сложносолевого состава, а также для регенерации реэкстрагирующих растворов после процесса экстракции может быть использована электрофлотационная технология,
которая зарекомендовала себя не только в очистке сточных вод [316–322], но и для извлечения ценных элементов из водных растворов [323–326].
Основными минералами, где содержатся РЗМ, являются бастнезит, монацит,
лопарит и ионно-абсорбционные глины [327]. Существующие технологии получения
162
редкоземельной продукции представляют собой комплексную переработку рудных материалов, включающую вскрытие руды кислотами (серной, соляной, азотной и др.) с
получением хлоридов, сульфатов, нитратов редкоземельных элементов. После проводят обработку полученных растворов содой или щавелевой кислотой для получения малорастворимых карбонатов или оксалатов редкоземельных элементов. Полученный осадок фильтруют и промывают водой [300–302; 328]. В результате чего с промывными водами теряется часть целевого продукта. Процесс разделения РЗМ с использованием данных методов требует дополнительного технологического оборудования и весьма трудоемок [303].
При переработке и добыче металлических руд образуется большое количество отходов, в том числе водных растворов, в которых содержатся редкоземельные металлы в значительных объемах. Поэтому создание технологии обезвреживания жидких отходов с наиболее полным выходом ценных компонентов является актуальной задачей.
Анализ существующих технологий по получению карбонатов редкоземельных металлов из кислых растворов РЗМ показывает, что процесс состоит из нескольких стадий осаждения, промывки (для удаления хлоридов) и трех стадий фильтрации осадка
(целевой продукт). Принципиальная схема получения карбонатов редкоземельных металлов после вскрытия руды соляной кислотой представлена на рисунке 4.10.
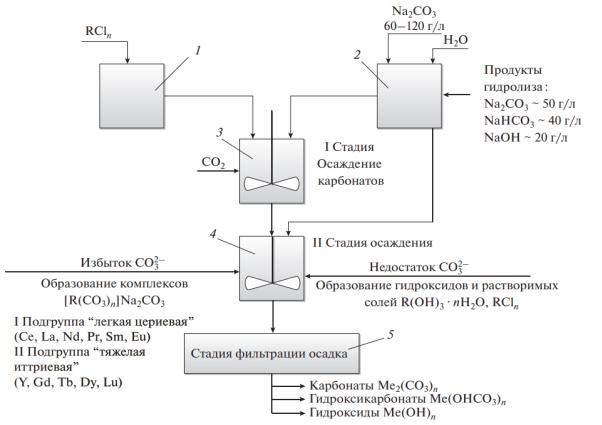
163
Рисунок 4.10 – Принципиальная схема получения карбонатов из растворов HCl:
1 – емкость технологического раствора хлоридов РЗМ; 2 – емкость для приготовления раствора осадителя (карбонат натрия); 3 – реактор I стадии осаждения с дополнительной дозировкой CO2; 4 – реактор II стадии осаждения осадка РЗМ; 5 – фильтрационные модули
В процессе реализации данной технологии возникает ряд проблем:
1.Для получения осадка в виде карбонатов РЗМ, как правило, требуется избыток осадителя (карбонат-иона), с другой стороны, избыток Na2CO3 приводит к комплексообразованию в первую очередь подгруппы II (тяжелая иттриевая).
2.В связи с тем, что Na2CO3 в водном растворе гидролизуется, раствор для осаждения содержит Na2CO3, NaHCO3, NaOH. Таким образом, на стадии фильтрации реально фильтруются Me2(CO3)3, Me(OH)CO3, Me(OH)3. Для исключения процессов комплексообразования реальное мольное соотношение Me:CO3 должно составлять 1:0,95.
Для снижения гидролиза в раствор дополнительно вводят CO2.
3. Раствор для осаждения после нейтрализации имеет значение pH 4,5–5,0, что оптимально с точки зрения осаждения карбонатов, с другой стороны, до 5% РЗМ находится в виде ионов и остается в растворе. Для формирования осадков гидроксидов РЗМ необходимое значение pH как минимум 6–6,5, где формируются гидроксиды РЗМ.
164
Растворимость осадков РЗМ (карбонаты, гидроксиды) возрастает с увеличением концентрации фонового электролита (NaCl ≈ 100–120 г/л) и уменьшается размер частиц дисперсной фазы.
С целью удаления коррозионно-агрессивных ионов хлора осадки карбонатов на стадии фильтрации дополнительно промывают горячей водой (50 °С), что приводит к частичному растворению дисперсной фазы и потере мелкодисперсной фракции осадка
(<10 мкм).
Таким образом, для повышения эффективности работы стадии фильтрации раствора и извлечения редкоземельных металлов из промывных вод необходимы новые технологические решения. Одним из перспективных направлений извлечения малорастворимых соединений РЗМ из водных растворов является электрофлотация.
Рассмотрим экспериментальные данные по ЭФ извлечению ∑РЗМ из водных растворов.
В таблице 4.28 представлены данные по степени извлечения фильтрацией осадка карбонатов РЗМ в диапазоне рН 4–10 и соотношении Na2CO3:∑РЗМ – 1:0,3
Установлено, что максимальное количество дисперсной фазы образуется при рН 7 – 10 и достигает 40–60% в зависимости от природы металла.
Таблица 4.28 – Зависимость степени извлечения дисперсной фазы редкоземельных металлов от рН раствора в присутствии осадителя Na2CO3 1 г/л фильтрацией осадка
pH |
|
Процент дисперсной фазы, % |
|
d, мкм |
|
ξ±, мВ |
||
La3+ |
Ce4+ |
Pr3+ |
Nd3+ |
Sm3+ |
|
∑РЗМ |
||
|
|
|||||||
4 |
0 |
30 |
0 |
19 |
33 |
>0,1 |
|
–1 |
5 |
0 |
32 |
0 |
21 |
33 |
0,1 |
|
–6 |
6 |
0 |
35 |
20 |
26 |
33 |
0,3 |
|
+7 |
7 |
36 |
55 |
40 |
55 |
67 |
8,0 |
|
+9 |
8 |
36 |
59 |
40 |
64 |
67 |
9,0 |
|
+10 |
9 |
38 |
66 |
40 |
69 |
67 |
10 |
|
+11 |
10 |
36 |
34 |
40 |
36 |
33 |
>200 |
|
–4,0 |
9* |
89 |
90 |
86 |
88 |
91 |
- |
|
- |
Условия эксперимента: с Ce4+ – 146 мг/л; с La3+ – 80,2 мг/л; с Nd3+ – 41,8 мг/л;
с Pr3+ – 15,5 мг/л; с Sm3+ – 3 мг/л; с Na2CO3 – 1 г/л; αmax фильтрации – 40–60%. * – электрофлотация.
165
Было исследовано влияние концентрации ионаосадителя на эффективность электрофлотационного процесса извлечения малорастворимых соединений редкоземельных металлов при различных значениях pH.
Таблица 4.29 – Влияние концентрации иона-осадителя и pH раствора на эффективность электрофлотационного процесса извлечения соединений редкоземельных металлов
|
|
|
|
|
C(Na2CO3), г/л |
|
|
|
||
Элемент |
0 |
|
|
|
0,25 |
|
|
0,5 |
|
|
|
5 |
|
7 |
9 |
5 |
7 |
9 |
5 |
7 |
9 |
La |
29 |
|
80 |
89 |
19 |
78 |
58 |
15 |
34 |
16 |
Ce |
23 |
|
84 |
92 |
22 |
79 |
48 |
16 |
24 |
9 |
Pr |
25 |
|
85 |
92 |
15 |
78 |
52 |
15 |
37 |
19 |
Nd |
26 |
|
85 |
91 |
14 |
78 |
56 |
10 |
36 |
23 |
Sm |
8 |
|
87 |
91 |
28 |
77 |
55 |
14 |
37 |
23 |
Gd |
30 |
|
82 |
88 |
21 |
76 |
45 |
10 |
34 |
17 |
Условия эксперимента: с∑ РЗМ – 200–250 мг/л; с NaCl – 1 г/л; Jv – 0,4 А/л; τ – 30 мин.
Установлено, что гидроксиды и гидрокарбонаты РЗМ хорошо извлекаются при pH ≥ 7,0. При увеличении концентрации Na2CO3 степень извлечения падает. В таблице
4.28 представлены экспериментальные данные по средним размерам частиц ∑РЗМ и величинам ξ±-потенциалов.
В кислой области pH размер частиц < 1мкм и за счет избытка ионов CO32-
ξ±-потенциал отрицательный. Формирование карбонатов, гидроксикарбонатов размер частиц возрастает до 10 мкм, ξ±-потенциал положительный, за счет формирования осадка с избытком Me3+ по отношению к ионам CO32- в твердой фазе.
При электрофлотационной обработке раствора при рН 9,0 и Jv – 0,4 А/л, степень извлечения повышается до 90%. В процессе электрофлотации происходит укрупнение частиц, и максимальное значение α достигается за 20 мин флотации. Флотошлам неустойчив и плохо держится на границе раздела жидкость – воздух.
При электрофлотационном извлечении ∑РЗМ в присутствии реагента-осадителя
Na2CO3 степень извлечения сильно зависит от концентрации Na2CO3. В таблице 4.29
представлены данные по электрофлотационному извлечению ∑РЗМ из раствора 1 г/л
NaCl.
Анализ показывает, что степень извлечения в растворе 1 г/л Na2CO3 невелика и не превышает 10–15%, для Ce(III) + Ce(IV) – 25%. В то же время фильтрация раствора
166
показала, что 95–98% ионов металлов РЗМ присутствуют в виде осадков,
комплексообразование в этом случае минимально. Низкие степени извлечения при концентрации карбоната натрия 1 г/л связаны с высоким отрицательным значением
ξ-потенциала (–25 ÷ –30 мВ). Указанные системы флотируются неэффективно. При снижении концентрации Na2CO3 величина ξ-потенциала возрастает и растет степень извлечения до 35%, а при концентрации 0,25 г/л степень извлечения увеличивается до
78%.
Проведенные ранее исследования по электрофлотационному извлечению РЗМ,
таких как La3+, Ce3+, Ce4+ показали, что эффективность процесса возрастает в присутствии ПАВ и флокулянтов и зависит от рН и природы электролита. Определены условия, когда труднорастворимые соединения La3+, Ce3+, Ce4+ извлекается на 95–98% при рН 7–9.
Таблица 4.30 – Электрофлотационное извлечение карбонатов (гидроксикарбонатов) РЗМ из промывных вод отмывки осадков
|
|
Степень извлечения, α, % |
|
|
|||
Me |
1 г/л Na2CO3 |
0,5 г/л Na2CO3 |
|
0,25 г/л Na2CO3 |
|||
без доб. |
+СептаПАВ |
без доб. |
+ NaDDS |
|
без доб. |
+ NaDDS |
|
|
|
||||||
|
|
ХСВ.50 |
|
|
|
|
|
La |
7 |
94 |
34 |
89 |
|
78 |
96 |
Ce (IV, III) |
5 |
93 |
24 |
87 |
|
79 |
96 |
Pr |
5 |
93 |
37 |
88 |
|
78 |
97 |
Nd |
8 |
94 |
36 |
88 |
|
78 |
97 |
Sm |
6 |
96 |
37 |
84 |
|
77 |
97 |
Eu |
10 |
96 |
35 |
98 |
|
77 |
96 |
Gd |
12 |
98 |
34 |
87 |
|
76 |
96 |
Tb |
8 |
98 |
34 |
98 |
|
76 |
98 |
Dy |
4 |
98 |
34 |
98 |
|
76 |
98 |
Y |
6 |
99 |
34 |
98 |
|
74 |
98 |
Условия эксперимента: с NaCl – 1 г/л; с добавки – 5 мг/л; Jv – 0,4 А/л; рН –7,0; τ – 20 мин
Проведен комплекс исследований по воздействию ПАВ и флокулянтов на эффективность электрофлотационного процесса. Результат ввода наиболее эффективных добавок и именно ПАВ NaDDS(a) и СептаПАВ(к) приведен в таблице 4.30. Степень извлечения РЗМ при концентрации ПАВ – 5 мг/л возрастает до 95–98%. Влияние катионного ПАВ связано с изменением ξ-потенциала дисперсной фазы, который возрастает на 10–15 мВ, что благоприятно сказывается на электрофлотационном
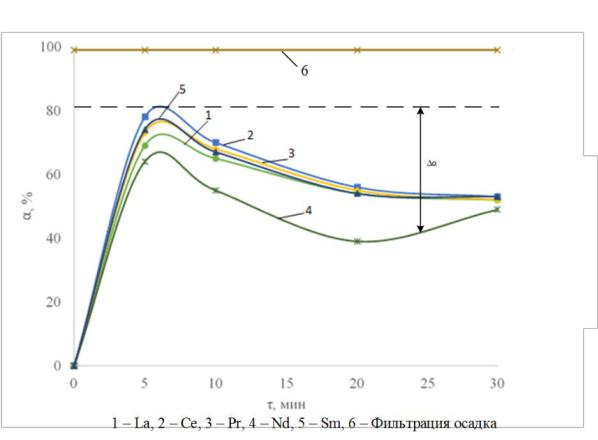
167
процессе. Действие анионного ПАВ связано с заменой молекул воды и гидрофобизацией поверхности осадка, что положительно отражается на формировании флотокомплекса.
Отмечено, что при электрофлотации дисперсной фазы РЗМ пенный продукт неустойчив, степень извлечения падает во времени на 30–40%. Экспериментальные результаты представлены на рисунке 4.11.
Рисунок 4.11 – Кинетика ЭФ извлечения ∑РЗМ (без ПАВ): условия эксперимента:
с NaCl – 1г/л; с Na2CO3 – 0,5 г/л; pH – 7,0
Эффективность процесса возрастает при добавлении катионного ПАВ (СептаПАВ)
и катионного флокулянта С-496. Экспериментальные данные приведены на рисунке 4.12.
Максимальное значение степени извлечения достигается в присутствии ПАВ за 5–10 мин обработки, что связано в первую очередь с гидрофобизацией поверхности и изменением
ξ-потенциала, о чем упоминалось выше.
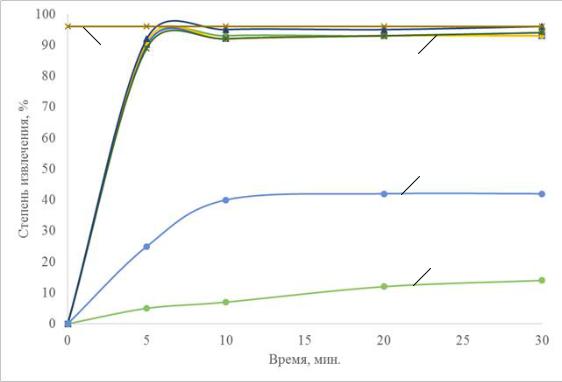
168
8 |
– |
|
2
1
Рисунок 4.12 – Влияние катионного ПАВ СептаПАВ ХСВ.50 и флокулянта С-496 на извлечение смеси РЗМ в присутствии осадителя Na2CO3: 1 – ∑РЗМ (Ce, La, Pr, Nd, Sm и
др.); 2 – ∑РЗМ (Ce, La, Pr, Nd, Sm и др.) + С-496 (флокулянт катионный);
3–7 – ∑РЗМ (Ce, La, Pr, Nd, Sm и др.) + СептаПАВ (катионный);
8 – фильтрация осадка (α = 98%): условия эксперимента: с NaCl – 1 г/л; с Na2CO3 – 1 г/л;
Jv – 0,4 А/л; рН – 9.0; с ПАВ – 5 мг/л; с флокулянта – 5 мг/л; с∑ РЗМ – 0,25 г/л
Проведенные исследования показали, что в технологических растворах Na2SO4 100
г/л эффективное извлечение La3+ происходит при рН – 10, в присутствии СептаПАВ степень извлечения составляет 97%.
Труднорастворимые осадки Nd в растворе Na2SO4 извлекаются эффективно в присутствии флокулянтов Praestol 825(к), 2530(а) и 2500(н), степень извлечения 75–85%.
Необходимо отметить, что 12–15% Nd3+ находится в виде растворимого комплекса
[Nd·(SO4)x]n- и в осадок не попадает.
В растворе 100 г/л NaNO3 карбонаты ∑РЗМ извлекается при рН – 9 на 85–90%. При добавлении катионного флокулянта С-496 степени извлечения достигают 93–95% в связи с тем, что выход по току водорода в концентрированных растворах нитрата натрия ниже
100% за счет восстановления NO3- иона, время газонасыщения возрастает до 30 мин.
Электрофлотация кислорода протекает эффективно.
169
Как показали результаты исследования ЭФ процесса извлечения ∑РЗМ без добавок в растворах 10 г/л NaCl, эффективность металлов цериевой группы около 20 %, натриевой
1–3%. Положительное влияние оказывает анионный ПАВ. Экспериментальные данные приведены в таблице 4.31.
Таблица 4.31 – Влияние ПАВ NaDDS (А) различной концентрации на эффективность электрофлотационного процесса извлечения малорастворимых соединений редкоземельных металлов при рН=7
ПАВ |
|
|
|
|
|
α, % |
|
|
|
|
с, мг/л |
|
|
|
|
|
|
|
|
|
|
La |
Ce |
Pr |
Nd |
Sm |
Eu |
Gd |
Tb |
Dy |
Y |
|
0 |
20 |
18 |
11 |
14 |
18 |
23 |
1 |
2 |
1 |
3 |
|
|
|
|
|
|
|
|
|
|
|
5 |
92 |
95 |
96 |
96 |
97 |
83 |
96 |
97 |
98 |
97 |
10 |
52 |
62 |
65 |
66 |
71 |
71 |
71 |
71 |
64 |
68 |
20 |
11 |
12 |
11 |
12 |
12 |
14 |
10 |
11 |
10 |
9 |
Условия эксперимента: с Na2CO3 – 1 г/л; с NaCl – 10 г/л; Jv – 0,4 А/л; рН – 7.
Введение в раствор анионного ПАВ NaDDS при небольших концентрациях (5
мг/л), необходимых для гидрофобизации поверхности осадка ∑РЗМ степень извлечения возрастает до 92 – 98%.
При реализации электрофлотационного процесса в концентрированных растворах электролитов наиболее эффективной добавкой показал себя неионогенный флокулянт N-
300. Для удобства анализа результаты представлены по цериевой (таблица 4.32) и
иттриевой группам (таблица 4.32 и 4.33).
Таблица 4.32 – Влияние концентрации флокулянта на электрофлотационное извлечение суммы РЗМ цериевой группы в фильтрате NaCl (100 г/л)
Флокулянт |
|
|
Степень извлечения, α, % |
|
|
||
N-300 |
La |
Ce |
Pr |
Nd |
|
Sm |
Eu |
0 |
21 |
16 |
18 |
15 |
|
18 |
20 |
2,5 |
56 |
58 |
48 |
56 |
|
59 |
60 |
5,0* |
94 |
96 |
95 |
96 |
|
96 |
97 |
10,0* |
90 |
89 |
91 |
90 |
|
91 |
90 |
Условия эксперимента: с NaCl – 100 г/л; с Na2CO3 – 1 г/л; с∑ РЗМ – 0,25 г/л; Jv – 0,4 А/л;
* Jv – 0,6 А/л; рН = 7,0; τ – 20 мин.
170
Таблица 4.33 – Влияние концентрации флокулянта на электрофлотационное извлечение
суммы РЗМ иттриевой группы в фильтрате NaCl (100 г/л)
Флокулянт |
|
Степень извлечения, α, % |
|
||
N-300 |
Eu |
Gd |
Tb |
Dy |
Y |
0 |
23 |
1 |
2 |
1 |
3 |
2,5 |
96 |
92 |
94 |
96 |
94 |
5,0* |
98 |
98 |
99 |
99 |
98 |
10,0* |
90 |
93 |
91 |
92 |
89 |
Условия эксперимента: с NaCl – 100 г/л; с Na2CO3 – 1 г/л; с∑ РЗМ – 0,25 г/л; Jv – 0,4 А/л;
* – Jv – 0,6 А/л; рН = 7,0; τ– 20 мин.
Без добавок металлы цериевой группы извлекаются на 15–20%, иттриевой группы
– 3%. Низкое значение степени извлечения связаны в первую очередь с размером дисперсной фазы менее 10 мкм.
Влияние ξ±-потенциала невелико, так как в концентрированных растворах ξ-
потенциал не превышает ±2 мВ. В связи с этим действие неионогенного флокулянта N-
300 и ПАВ ПЭО-1500 наиболее эффективно. Установлено, что смесь гидроксидов РЗМ может быть извлечена из концентрированных растворов NaNO3, которые обычно образуются при нейтрализации азотнокислых растворов выщелачивания или реэкстракции (таблица 4.34).
Таблица 4.34 – Влияние pH раствора на электрофлотационное извлечение малорастворимых соединений редкоземельных металлов в 100 г/л NaNO3
pH |
|
|
Степень извлечения, α, % |
|
||
La3+ |
Ce4+ |
|
Pr3+ |
Nd3+ |
Sm3+ |
|
|
|
|||||
5 |
0 |
3 |
|
2 |
3 |
3 |
7 |
13 |
22 |
|
26 |
28 |
60 |
9 |
89 |
90 |
|
86 |
88 |
91 |
9* |
94 |
93 |
|
95 |
94 |
95 |
Условия эксперимента: с Ce4+ – 146 мг/л; с |
La3+ – 80,2 мг/л; с Nd3+ – 41,8 мг/л; |
с Pr3+ – 15,5 мг/л; с Sm3+ – 3 мг/л; с Na2CO3 – 1 |
г/л; с NaNO3 – 100 г/л; с С-496к - 5 мг/л; |
Jv – 0,4 А/л. |
|
Проведенные исследования показали, что электрофлотационный процесс позволяет эффективно извлекать малорастворимые соединения смеси РЗМ как из промывных вод при отмывке осадков РЗМ от ионов хлора, так и из солевых растворов
171
(NaCl) фильтратов. Место и роль электрофлотационных процессов показано на схеме получения карбонатов РЗМ (рисунок 4.13).
Базовая схема выделения ∑РЗМ включает три стадии фильтрации и промывку осадков. В связи с отмеченными проблемами схема дополнена двумя электрофлотационными установками 9 и 10. Электрофлотатор 9 обеспечивает извлечение из промывной воды редкоземельных элементов в виде карбонатов и гидроксидов.
Электрофлотатор 10 обеспечивает высокоэффективную очистку фильтрата, содержащего до 100 г/л NaCl, от дисперсной фазы карбонатов и гидроксидов РЗМ. Указанный подход позволяет предотвращать потери редкоземельных элементов с промывными водами и в фильтрате после технологических операций.
Для реализации указанного процесса созданы электрофлотационные установки производительностью 5 и 10 м3/ч с нерастворимыми анодами на основе ОРТА. Затраты электроэнергии для обработки воды – до 1 кВт/м3, для очистки фильтрата 0,2–0,5 кВт/м3.
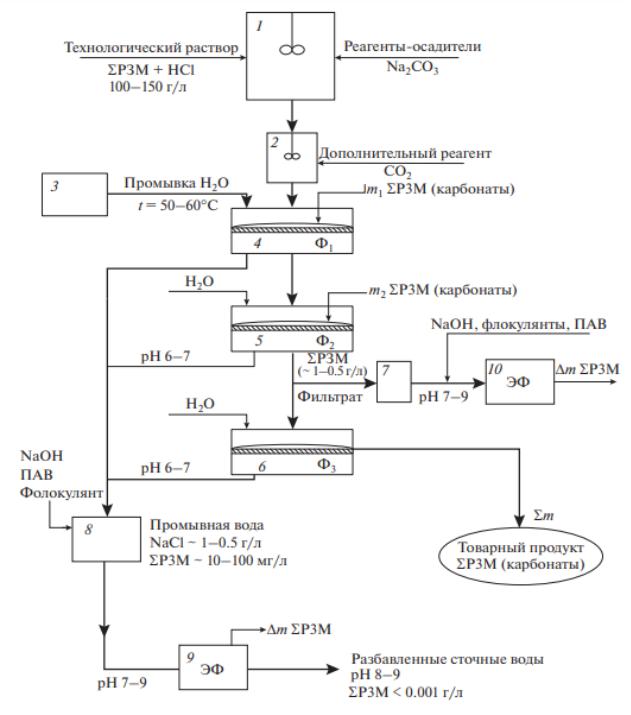
172
Рисунок 4.13 – Схема выделения карбонатов РЗМ из хлорсодержащего технологического раствора: 1 – реактор образования карбонатов редкоземельных металлов; 2 – реактор для ввода дополнительного реагента СO2 для снижения скорости гидролиза Na2CO3; 3 – промывная вода (очищенная);
4–6 – фильтры (Ф1 – крупнопористый (~500 г/м2), Ф2 – среднепористый (~750 г/м2),
Ф3 – мелкопористый (~1000 г/м2); 7 – емкость для сбора фильтрата; 8 – накопитель промывной воды; 9 – электрофлотатор для очистки промывной воды;
10 – электрофлотатор для очистки фильтрата
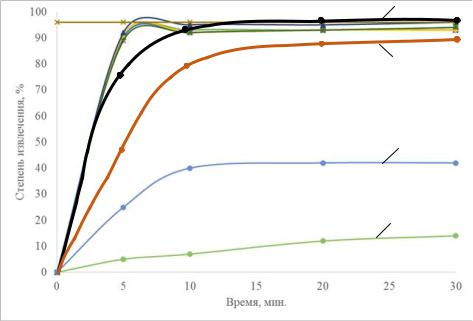
173
Исследован электрофлотационный процесс селективного разделения гидроксида металлов (Ce(IV), Ti(IV)), формирующих гидроксиды при pH = 3–5 и металлов Me(III),
которые находятся в ионном виде в растворах электролитов и не извлекаются в виде осадка. Основной подход к повышению селективности процесса: повысить эффективность извлечения дисперсной фазы за счет применения флокулянтов и ПАВ и снизить соосаждение Me (III) и сорбцию гидроксида Me (IV) в осадках. Типичные зависимости степени извлечения гидроксидов Me (IV) и Me (III) представлены на рисунке
4.14.
Основная задача исследования: определить условия максимального извлечения
Me(OH)4 (электролит, рН раствора, ПАВ, флокулянт) и минимального соосаждения
Me(OH)3 или сорбции Мe (III) на свежесформированном осадке. Рассмотрим экспериментальные результаты электрофлотационного разделения двухкомпонентных систем. Для выбора оптимальных значений рН использованы литературные данные по рН гидратообразования в разбавленных растворах редкоземельных металлов, а также Ti, Sc, Fe, Al, установленных в данной работе.
1
2
3
4
Рисунок 4.14 – Кинетика ЭФ процесса извлечения гидроксида Ce(IV) и ионов металлов
Me(III): 1 – извлечение Me(OH)4 + ПАВ; 2 – извлечение Me(OH)4 + ПАВ (флокулянт); 3 –
извлечение Me(III); 4 – извлечение Me(III) + ПАВ (флокулянт): условия эксперимента: JV – 0,4 А/л; с Na2SO4 – 1 г/л; с ПАВ – 10 мг/л; с флокулянт – 1 мг/л; рН = 5
174
Для дальнейшего исследования выбраны растворы с рН = 5,0, где Ce(IV)
присутствует в дисперсном виде, а осадки Me(III) практически не образуются.
Экспериментальные результаты для системы Ce(IV) – Nd(III) – раствор Na2SO4
представлены в таблице 4.35.
Таблица 4.35 – Электрофлотационное извлечение и разделение Ce4+ и Nd3+ в условиях сульфатного фона
|
|
|
|
Степень извлечения, α, % |
|
|
|
|
||||
Время, мин |
Без добавок |
СептаПАВ |
С-496 |
|
NaDDS |
|||||||
|
Ce |
|
Nd |
Ce |
|
Nd |
Ce |
|
Nd |
Ce |
|
Nd |
5 |
54 |
|
48 |
90 |
|
44 |
80 |
|
32 |
88 |
|
94 |
10 |
62 |
|
59 |
92 |
|
42 |
75 |
|
33 |
95 |
|
85 |
20 |
35 |
|
33 |
81 |
|
44 |
58 |
|
24 |
98 |
|
89 |
K |
|
1,1 |
|
16 |
8,5 |
|
|
2,0 |
Условия эксперимента: JV – 0,4 А/л; с Се4+ – 50 мг/л; с Nd3+ – 12,5 мг/л; с Na2SO4 – 1 г/л;
с ПАВ – 10 мг/л; с флокулянта – 1 мг/л; рН = 5.
K (NaDDS) – 8 К (А-137) – 3 К (PEO–1500) – 2 К (N–300) – 1,2.
Можно видеть, что без добавок селективного разделения Ce(IV) – Nd(III) не происходит, величина К = 1,1. Добавление флокулянтов, ПАВк приводит к росту коэффициента распределения до 8,5, 16. Катионный ПАВ (СептаПАВ) способствует извлечение осадка Ce(IV) до 90–92%.
Для повышения эффективности электрофлотационного извлечения соединений
Ce4+, La3+, Y3+ и Nd3+ исследованы ПАВ различной природы:
Таблица 4.36 – Влияние ПАВ различной природы на степень извлечения труднорастворимых соединений Ce4+ и Y3+ в условиях сульфатного фона
Время, |
|
|
|
|
|
Степень извлечения, % |
|
|
|
||||
|
Без добавок |
|
NaDDS |
|
PEO-1500 |
СептаПАВ |
|||||||
мин |
|
|
|
||||||||||
|
Ce |
Y |
|
Ce |
Y |
|
Ce |
|
Y |
Ce |
|
Y |
|
|
|
|
|
|
|
||||||||
5 |
|
5 |
9 |
|
14 |
24 |
|
14 |
|
33 |
39 |
|
49 |
10 |
|
36 |
21 |
|
11 |
15 |
|
10 |
|
19 |
44 |
|
48 |
20 |
|
41 |
22 |
|
25 |
40 |
|
18 |
|
20 |
39 |
|
49 |
Условия |
эксперимента: JV |
– 0,4 |
А/л; |
с Се4+ – |
50 мг/л; |
с Y3+ |
– 12,5 мг/л; |
с Na2SO4 – 1 г/л; с добавки – 10 мг/л; pH = 5.
175
Таблица 4.37 – Электрофлотационное извлечение и разделение Ce4+ и Y3+ в условиях
сульфатного фона
|
|
|
Степень извлечения, α, % |
|||
Время, мин |
|
Без добавок |
|
PEO–1500 |
||
|
Ce |
|
Y |
Ce |
|
Y |
5 |
5 |
|
9 |
14 |
|
33 |
10 |
36 |
|
21 |
10 |
|
19 |
20 |
41 |
|
22 |
18 |
|
20 |
K |
|
2,5 |
|
3 |
|
Условия эксперимента: JV – 0,4 А/л; с Се4+ – 50 мг/л; с Y3+ – 12,5 мг/л; с Na2SO4 – 1 г/л;
с ПАВ – 10 мг/л; с флокулянта – 1 мг/л; рН = 5.
Рассчитанные значения коэффициентов разделения в сульфатных растворах
(максимум – 2,0) показали, что селективного разделения в растворах Na2SO4 для системы
Ce (IV) – Y (III) не происходит. Низкие значения степени извлечения и коэффициента разделения без добавок, и увеличенные за счет введения анионного ПАВ NaDDS
представлены в таблице 4.38.
Таблица 4.38 – Электрофлотационное извлечение и разделение Ce4+ и La3+ в условиях сульфатного фона
|
|
|
Степень извлечения, α, % |
|||
Время, мин |
|
Без добавок |
|
NaDDS |
||
|
Ce |
|
La |
Ce |
|
Y |
5 |
12 |
|
7 |
60 |
|
16 |
10 |
9 |
|
27 |
46 |
|
17 |
20 |
16 |
|
32 |
41 |
|
17 |
K |
|
3 |
|
8 |
|
Условия эксперимента: IV – 0,4 А/л; с Се4+ – 50 мг/л; с Y3+ – 12,5 мг/л; с Na2SO4 –1 г/л;
с ПАВ – 10 мг/л; с флокулянт – 1 мг/л; рН = 5
Примечание: К (А-137) – 6; К (СептаПАВ) – 4; К (С-496) – 3; K (PEO-1500) – 4,5;
К (N–300) – 2.5
Основной вывод из работ по электрофлотационному разделению Ce(IV) – Me(III) в
растворах Na2SO4 – они показывают, что получить высокие значения коэффициента разделения невозможно, ввиду присутствия дисперсной фазы гидроксисульфатов лантана, иттрия и неодима, которые извлекаются вместе с дисперсной фазой Ce(OH)4 и
Cе(OH)3·SO4.

176
Анализ литературы [313] показал, что селективное флотационное разделение с более высокими значениями К наблюдаются в растворах NaCl и NaNO3. Некоторые экспериментальные результаты даны в таблицах 4.39 и 4.40.
Таблица 4.39 – Электрофлотационное извлечение и разделение Ce4+ и La3+ в условиях хлоридного фона
Время, |
|
|
|
|
|
Степень извлечения, α, % |
|
|
|
|
||||
Без добавок |
NaDDS |
PEO-1500 |
СептаПАВ |
|
С-496 |
|||||||||
мин |
|
|||||||||||||
Ce |
|
La |
Ce |
|
La |
Ce |
|
La |
Ce |
|
La |
Ce |
La |
|
|
|
|
|
|
||||||||||
5 |
82 |
|
31 |
77 |
|
10 |
58 |
|
6 |
51 |
|
2 |
23 |
3 |
10 |
90 |
|
45 |
80 |
|
8 |
64 |
|
8 |
62 |
|
6 |
25 |
1 |
20 |
92 |
|
79 |
82 |
|
10 |
47 |
|
7 |
62 |
|
3 |
30 |
6 |
K |
|
11 |
|
46 |
|
21 |
|
52 |
|
32 |
Условия эксперимента: JV – 0,4 А/л; с Се4+ – 50 мг/л; с La3+ – 12,5 мг/л; с NaCl – 1 г/л;
с ПАВ – 10 мг/л; с флокулянта – 1 мг/л; рН = 5.
Из данных анализа следует, что без добавок в системе Ce(IV) – La(III) – NaCl
происходит селективное разделение, хотя величина К невелика и достигает значений
10–11. Эффективность процесса резко возрастает в присутствии ПАВ, причем как для анионного, так и для катионного коэффициент разделения возрастает до значений 46 – 52. Установлено, что ПАВ за счет гидрофобизации поверхности дисперсная фаза Ce(OH)4
увеличивает степень извлечения осадка и не влияет на извлечение ионов лантана.
Таблица 4.40 – Электрофлотационное извлечение и разделение Ce4+ и Nd3+ в условиях хлоридного фона
|
|
|
Степень извлечения, α, % |
|
|
|
||
Время, мин |
Без добавок |
|
PEO-1500 |
|
N-300 |
|||
|
Ce |
Nd |
Ce |
|
Nd |
Ce |
|
Nd |
5 |
37 |
5 |
83 |
|
11 |
57 |
|
3 |
10 |
18 |
5 |
85 |
|
12 |
69 |
|
3 |
20 |
19 |
7 |
80 |
|
10 |
79 |
|
8 |
K |
|
11 |
|
42 |
|
43 |
Условия эксперимента: JV – 0,4 А/л; с Се4+ – 50 мг/л; с Nd3+ – 12,5 мг/л; с NaCl – 1 г/л;
с ПАВ – 10 мг/л; с флокулянта – 1 мг/л; рН = 5.
Для системы Ce(IV) – Nd(III) ПАВ и флокулянты также оказывают положительное влияние. Наиболее высокие значения коэффициента разделения наблюдаются для неионогенного ПАВ ПЭО-1500 и неионогенного флокулянта N-300, величины K
177
достигают значений 42–43. Для анионного ПАВ NаDDS величина К = 5, для катионного
ПАВ СептаПАВ) К = 2,0 и флокулянта С-496 – 9,0.
Эффект влияния неионогенного ПАВ и флокулянта вероятно связан с адсорбцией дисперсной фазы Ce(OH)4 в присутствии Nd(III), поверхность которого не заряжена и реализуются условия близкие к изоэлектрической точке рН 5±0,5 для системы H2O – NaCl
– Ce(OH)4 – Nd3+.
Проведены исследования по селективному разделению Ce(IV) – Me(III) в
нитратных растворах. Экспериментальные результаты по степени извлечения и
коэффициенту разделения Ce(IV) – Y(III) представлены в таблице 4.41.
Таблица 4.41 – Электрофлотационное извлечение и разделение Ce4+ и Y3+ в условиях нитратного фона
|
|
|
Степень извлечения, α, % |
|
|
|
|
||||
|
|
|
|
|
|
|
|
|
|
||
Время, мин |
Без добавок |
СептаПАВ |
С-496 |
|
NaDDS |
||||||
|
|
|
|
|
|
|
|
|
|
|
|
|
Ce |
Y |
Ce |
|
Y |
Ce |
|
Y |
Ce |
|
Y |
|
|
|
|
|
|
|
|
|
|
|
|
5 |
35 |
5 |
73 |
|
3 |
73 |
|
8 |
44 |
|
5 |
|
|
|
|
|
|
|
|
|
|
|
|
10 |
39 |
22 |
75 |
|
4 |
74 |
|
7 |
76 |
|
10 |
|
|
|
|
|
|
|
|
|
|
|
|
20 |
47 |
23 |
71 |
|
4 |
75 |
|
11 |
75 |
|
12 |
|
|
|
|
|
|
|
|
|
|
|
|
K |
|
10 |
|
74 |
38 |
|
|
29 |
|||
|
|
|
|
|
|
|
|
|
|
|
|
Условия эксперимента: JV – 0,4 А/л; с Се4+ – 50 мг/л; с Y3+– 12,5 мг/л, с NaNO3 – 1 г/л;
с ПАВ – 10 мг/л; с флокулянт – 1 мг/л; рН = 5.
Примечание: K (A-137) – 21; К (СептаПАВ) – 12.
Анализ показал, что внесение в раствор добавок ПАВ или флокулянта способствуют значительному увеличению значения коэффициента разделения К.
Максимальным эффектом обладает катионный ПАВ СептаПАВ, величина К составляет 74, в то время как без ПАВ – 10. Указанный эффект можно объяснить сильным влиянием ПАВ на ЭФ извлечение дисперсной фазы Ce(OH)4 и блокированием адсорбции
Y(III) катионным ПАВ на свежесформированном осадке гидроксида. Результаты селективного разделения Ce(IV) – La(III) в растворе NaNO3 представлены в таблице 4.42.
178
Таблица 4.42 – Электрофлотационное извлечение и разделение Ce4+ и La3+ в условиях
нитратного фона
|
|
|
Степень извлечения, α, % |
|
|
|
|
||||
Время, мин |
Без добавок |
|
NaDDS |
PEO-1500 |
С-496 |
|
|||||
|
Ce |
La |
Ce |
|
La |
Ce |
|
La |
Ce |
|
La |
5 |
39 |
6 |
73 |
|
7 |
69 |
|
10 |
77 |
|
9 |
10 |
55 |
7 |
80 |
|
10 |
57 |
|
17 |
77 |
|
12 |
20 |
52 |
9 |
80 |
|
11 |
55 |
|
11 |
75 |
|
9 |
K |
|
12 |
|
36 |
20 |
|
34 |
|
Условия эксперимента: JV – 0,4 А/л; с Се4+ – 50 мг/л; с La3+ – 12,5 мг/л;
с NaNO3 –1 г/л; с ПАВ – 10 мг/л; с флокулянта – 1 мг/л; рН = 5.
Определено, что коэффициент разделения возрастает при добавлении ПАВ и флокулянтов до 34–36, однако их влияние значительно ниже, чем для системы Ce(IV) – Y(III).
В таблице 4.43 представлены экспериментальные результаты ЭФ извлечения дисперсной фазы Ce(OH)4 в присутствии Nd(III) в растворе NaNO3.
Таблица 4.43 – Электрофлотационное извлечение и разделение Ce4+ и Nd3+ в условиях нитратного фона
|
|
|
|
Степень извлечения, α, % |
|
|
|
|
|||||
Время, мин |
Без добавок |
NaDDS |
PEO-1500 |
СептаПАВ |
С-496 |
||||||||
|
Ce |
Nd |
Ce |
|
Nd |
Ce |
|
Nd |
Ce |
|
Nd |
Ce |
Nd |
5 |
34 |
6 |
73 |
|
8 |
56 |
|
2 |
55 |
|
5 |
71 |
5 |
10 |
33 |
6 |
79 |
|
9 |
61 |
|
3 |
66 |
|
10 |
70 |
6 |
20 |
23 |
7 |
81 |
|
8 |
49 |
|
5 |
62 |
|
4 |
71 |
13 |
K |
|
8 |
|
50 |
|
49 |
|
39 |
|
46 |
Условия эксперимента: JV – 0,4 А/л; с Се4+ – 50 мг/л; с Nd3+ – 12,5 мг/л;
с NaNO3 – 1 г/л; с ПАВ – 10 мг/л; с флокулянта –1 мг/л; рН = 5.
Введение в систему Ce(OH)4 – Nd(III) в растворах NaNO3 катионного флокулянта С-496 и ПАВ различной природы интенсифицирует процесс извлечения дисперсной фазы и повышает степень извлечения с 33% до 60–80%. Необходимо отметить, что ионы Nd(III)
извлекаются на 5–12 %. В присутствии ПАВ и флокулянтов коэффициент разделения возрастает с 8 до 40–50.
179
Сравнительное влияние природы ионов Ме(III), электролита и добавок (ПАВ, флокулянт) на селективное разделение двухкомпонентной системы Ce(OH)4 – Ме(III) (La, Y, Nd) представлено в таблице 4.44.
Таблица 4.44 – Влияние природы электролита, ПАВ и флокулянта на коэффициент разделения двухкомпонентой смеси Се(ОН)4 – Me 3+ (– La3+, – Y3+, – Nd3+)
|
|
|
Коэффициент разделения, К |
|
|
||
Система |
Me 3+ |
Электролит |
Без |
ПАВ |
Флокулянт |
||
|
|
|
добавок |
||||
|
|
|
|
|
|
|
|
|
– Nd3+ |
|
11 |
42 (PEO-1500) |
43 |
(N-300) |
|
|
– La3+ |
|
11 |
46 |
(NaDDS |
32 |
(C-496) |
|
NaCl |
52 (СептаПАВ) |
|||||
|
|
|
|
|
|||
|
– Y3 |
|
5 |
9 (NaDDS) |
21 |
(C-496) |
|
|
|
20 |
(PEO-1500) |
||||
|
|
|
|
|
|
||
Се(ОН)4 |
– Nd3+ |
|
8 |
50 (NaDDS) |
46 |
(N-300) |
|
|
|
49 |
(PEO-1500) |
||||
|
|
|
|
|
|
||
|
– La3+ |
NaNO3 |
12 |
36 |
(NaDDS) |
34 |
(C-496) |
|
20 |
(PEO-1500) |
|||||
|
|
|
|
|
|
||
|
– Y3 |
|
10 |
74 |
(PEO-1500) |
38 |
(C-496) |
|
|
29 |
(NaDDS) |
29 |
(N-300 |
||
|
|
|
|
Условия эксперимента: JV – 0,4 А/л; с Се4+ – 50 мг/л; с Me3+ – 12,5 мг/л; с фона – 1 г/л; τ – 20 мин, с ПАВ – 10 мг/л; с флокулянта – 1 мг/л; рН = 5
Установлено, что без добавок для всех ионов металлов коэффициенты разделения в среднем имеет значения 8–12, как в растворах NaCl и NaNO3, что не позволяет использовать такие системы на практике вследствие низкой эффективности.
Максимальный коэффициент разделения для системы Ce(IV) – La(III) в растворе
NaCl в присутствии катионного ПАВ (СептаПАВ) К = 52. Для системы Ce(IV) – Y(III) в растворе NaNO3 в присутствии неионогенного ПАВ К = 74. Для системы Ce(IV) – Nd(III)
максимален в растворах NaNO3 К = 49–50 в присутствии ПАВ.
При расширении объема научных исследований по таким системам (новые ПАВ, флокулянты, температурный режим, концентрации электролитов) можно ожидать рост коэффициентов разделения Ce(OH)4 – Me(III) до значений 80–100.
В рамках выполнения проекта РФФИ по теме: «Создание фундаментальных основ энергоресурсоэффективной экологически безопасной электрофлотомембранной технологии переработки низкоконцентрированных жидких техногенных отходов, содержащих Ti и Sc» (№ 18-29-24010 от 01.11.2018 г.) проведены исследования по селективному разделению двухкомпонентной системы Ti(IV) и Me(III) (Ce, Sc, Y, La).
180
Гидроксиды титана хорошо флотируются в области рН = 3±0,5, где ионы Ce, Sc, Y, La в
растворах NaCl осадков не образуется.
В таблице 4.45 представлены данные по селективному разделению гидроксида титана Ti(OH)4 и ионов металлов Sc3+, Y3+, La3+ и Ce3+ в растворе хлорида натрия при рН
= 3,0.
Таблица 4.45 – Селективное извлечение гидроксида титана из двухкомпонентных систем
ПАВ (а) NaDDS |
Степень извлечения, α, % |
К |
|
|
|
||
|
Ti(IV) |
РЗЭ(III) |
|
|
|
|
|
Ti–Ce |
73 |
3 |
87 |
|
|
|
|
Ti–La |
66 |
7 |
38 |
|
|
|
|
Ti–Y |
58 |
5 |
19 |
|
|
|
|
Ti–Sc |
89 |
11 |
74 |
|
|
|
|
Условия эксперимента: рН = 3; с Ti4+ – 100мг/л; с Y3+, La3+, Ce3+ – 50 мг/л; с ПАВ – 5 мг/л;
Jv – 0,4 А/л; с NaCl – 1 г/л.
Высокий коэффициент разделения наблюдается для систем Ti(IV) – Sc(III) K = 74
и Ti(IV) – Ce(III) K = 87 в присутствии ПАВ NaDDS и ПЭО-1500, которые повышают эффективность извлечения дисперсной фазы Ti(OH)4 за счет гидрофобизации поверхности дисперсной фазы.
Технологическое внедрение процесса селективного разделения Me(IV) – Me(III)
может быть реализовано в рамках полученных патентов: «Способ извлечения ионов церия (IV) из водных растворов» (№ 2610864) и «Способ для селективного извлечения и разделения ионов цветных и редкоземельных металлов с возможным первичным окислением металлов переменной валентности» (№ 2016122112), указанных в приложении 2.
181
5. Общий подход к созданию высокоэффективной технологии очистки сточных вод, загрязненных ИТМ, ВВ, ПАВ, нефтепродуктами, лигандами и
композициям органической природы
5.1. Роль ПАВ в интенсификации и повышении эффективности электрофлотационных процессов извлечения труднорастворимых
соединений цветных и редкоземельных металлов и высокодисперсных углеродных материалов
Рассмотрим влияние поверхностно-активных веществ на электрофлотационный процесс извлечения дисперсной фазы свежесформированного осадка гидроксидов,
фосфатов и сульфидов металлов (Cr, Al, Fe, Ti, Cu, Zn, Ni, Sc), которые имеют различную структуру, размер частиц и заряд поверхности.
Экспериментальные данные представленны в разделе 3 и показывают, что ПАВ адсорбируется на поверхности гидроксидов Fe, Al, Cr при рН 5 – 10, Cu, Ni, Zn, Cd при рН 8–11. Наибольшее значение величины адсорбции наблюдается для катионных ПАВ СептаПАВ ХСВ.50 и ХЭВ.70, что связано с доступностью мест адсорбции по местам атома кислорода в структуре гидроксида за счет десорбции ионов H3O+ в щелочных растворах электролитов [5, 7].
Установлено, что адсорбция ПАВ на гидроксидах протекает в виде полислоев за счет мицеллообразования при концентрации анионных ПАВ более 200 мг/л, катионных более 500 мг/л. Некоторые изотермы адсорбции представлены на рисунках 5.1 – 5.3.
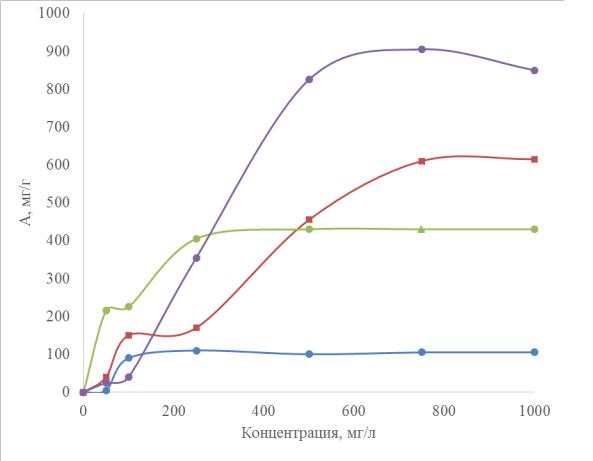
182
1
2
3
4
Рисунок 5.1 – Изотермы адсорбции анионных ПАВ для различных коагулянтов:
1 – Fe(OH)3+ NaDBS; 2 – Fe(OH)3+ NaDDS; 3 – Al(OH)3 + NaDDS; 4 – Аl(OH)3 + NaDBS
На рисунке 5.1 представлена изотерма адсорбции анионных ПАВ NaDDS и NaDBS
на гидроксидах алюминия и железа. Анализ зависимости А = ƒ(cисх) показал, что на кривой имеются два участка. I – низкая концентрация до 100 мг/л ПАВ, кривая 2, 3, 4, где формируется первый адсорбционный слой и II – участок, где формируются полислои ассоциаты, происходит мицелообразование (более 200 мг/л). Аналогичные зависимости получены на Al2O3, SiO2 и других оксидах.
С технологической точки зрения важно, что величины адсорбции в расчете на 1 г
гидроксида составляет 100, 400, 600, 800 мг/г в зависимости от природы органического сорбата в воде, что можно эффективно использовать в процессах водоочистки для извлечения ПАВ.
Характер изотерм адсорбции для неионогенного ПАВ АЛМ-10 отличается от изотерм адсорбции анионного ПАВ. Экспериментальные данные представлены на рисунке 5.2 (кривые 1, 3, 4). На кривой имеется I участок, в случае гидроксида железа определены предельные значения величины адсорбции Аmax, предельные значения
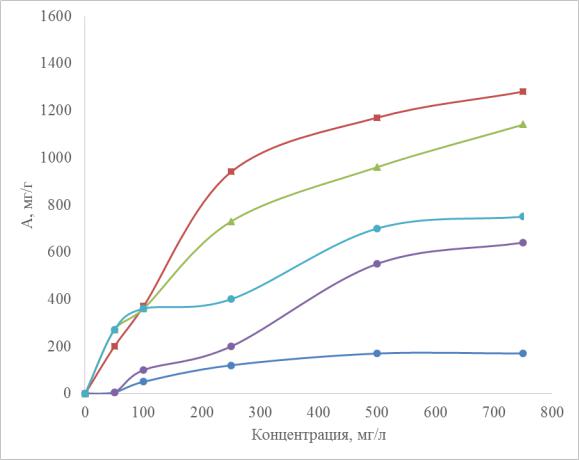
183
наблюдаются при концентрации 800–1000 мг/л, для Al(OH)3 составляет 1000–1200 мг/л.
Влияние мицелообразования при данной концентрации не проявляется до 400 мг/л.
3
4
5
2
1
Рисунок 5.2 – Изотермы адсорбции неионогенных ПАВ для различных сорбентов:
1 – Fe(OH)3 + АЛМ-10; 2– Fe(OH)3 + ОС-20; 3 – Al(OH)3 + АЛМ-10; 4 – ОУ-Б + АЛМ-10; 5 – ОУ-Б + ОС-20*
Для неионогенного ПАВ ОС-20Б кривые имеют два явно выраженных участка.
Первый участок наблюдается в диапазоне концентрации до 400 мг/л. Второй участок характерен для области концентраций, где наблюдается мицелообразование и формирование полислоев и ассоциатов, величина адсорбции увеличивается в 1,5–3 раза.
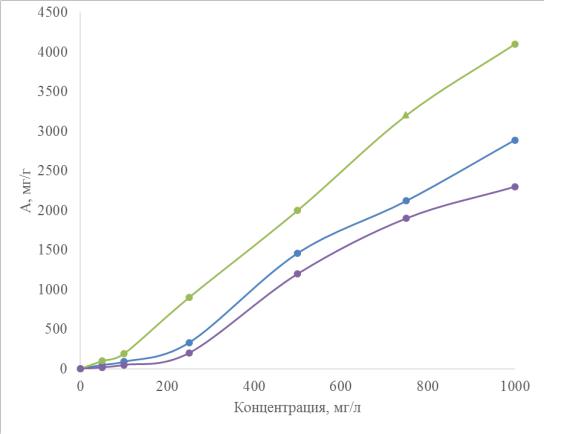
184
1
2
3
Рисунок 5.3 – Изотермы адсорбции катионных ПАВ для различных сорбентов: 1 – Al(OH)3; 2– ОУ-Б; 3 – Fe(OH)3;*СептаПАВ ХСВ.50
Зависимость А = ƒ(cисх) носит S-образный характер. Причем величина адсорбции при концентрации 200–300 мг, 500–1000 мг/л. Все это свидетельствует о формировании полислоев на поверхности осадков, включая порошки углей ОУ-Б.
Сравнение величины адсорбции ПАВ на осадках Al(OH)3 и порошках углей ОУ-Б
показывает, что величины адсорбции в первом случае значительно выше, чем на углеродных сорбентах, что связано с затруднением проникновения ПАВ в микропоры углей. Основные места для адсорбции ПАВ – мезопоры, то есть на поверхности углей.
Суммарный объем пор исследованных углей: ОУ-Б 0,8 см3/г, ОУ-А 1,4 – 1,5 см3/г, в том числе микропор 0,2 см3/г, 0,28 см3/г и 0,45 см3/г соответственно.
При разработке технологии очистки сточных вод от органических загрязнений с помощью порошков углеродных материалов ОУ-А, ОУ-Б или дисперсной фазы гидроксидов металлов (Al, Fe, Cr и др.) используют изотермы адсорбции, удельные сорбционные характеристики, а также кинетику адсорбции процесса. При этом возникает ряд противоречий и сложностей. Первое – это низкие удельные величины адсорбции (А,
мг/гадс) при низких исходных концентрациях. Второе – это низкие значения ПДК для
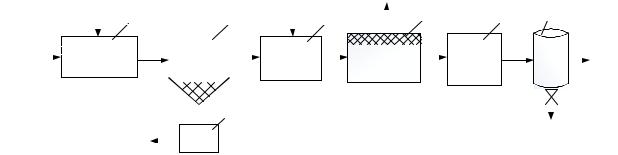
185
большинства органических загрязнений, включая ПАВ (0,1–0,01 мг/л). Третье – это большой расход сорбентов порошка ОУ-А, ОУ-Б либо коагулянтов и сорбентов (Al, Fe, Ti). Четвертое – это массоперенос и интенсификация процессов адсорбции за счет перемешивания выделяющимися газами H2, O2. С другой стороны, извлечение органических соединений происходит не только за счет адсорбции на дисперсной фазе,
но и в результате адсорбции на пузырьках H2, O2. «Пенная флотация», концентрация ПАВ–газ в 10–20 раз выше, чем ПАВ–жидкость. Эмульсии и дисперсную фазу органической природы извлекают флотационно, снижая концентрацию органических загрязнений, подаваемых на сорбционные фильтры.
Положительный эффект (увеличение удельных адсорбционных характеристик)
достигается дополнительно за счет ассоциации молекул ПАВ или мицелл при концентрации больше ККМ и формировании полислоев на поверхности дисперсной фазы, на осадках гидрофильной природы (гидроксиды, оксиды металлов).
Дополнительные эффекты возникают в растворах с разными значениями pH из-за изменения величины и знака ζ-потенциала, что приводит к росту адсорбционных характеристик осадков за счет электростатической адсорбции ассоциатов ПАВ.
Большинство авторов при использовании порошков-углей для извлечения органических загрязнений предлагают проводить дозировку сорбента в 2–3 стадии, используя аппараты удаления осадков. По оценке автора работы, при 2-стадийной обработке расход порошка угля сокращается на 80%. Многостадийный подход с использованием ЭФ технологий и двух типов сорбентов (порошки углей и гидроксидов металлов), а также сорбционных модулей с БАУ представлен на рисунке 5.4.
|
|
|
|
|
|
|
|
|
|
|
|
|
|
Флотоконцентрат |
|
|
|
|
|
|
|
|||
|
|
|
|
|
|
|
|
|
|
|
|
|
m = α m3+(1-α) (m1+m2) |
|
|
|
|
|
|
|
||||
|
m2 |
|
|
|
|
|
|
m3 |
|
|
|
|
|
|
|
|
|
|
|
|
||||
|
|
|
|
|
|
|
|
|
|
|
|
|
|
|
6 |
7 |
|
|
|
|||||
|
|
1 |
|
2 |
|
4 |
|
|
5 |
|
|
|
|
|||||||||||
|
|
|
|
|
|
|
|
|
|
|
|
|
|
|
|
|||||||||
H2Oсточная |
|
|
|
|
|
|
|
|
|
|
|
|
|
|
|
|
|
|
|
|
|
|||
|
|
|
|
|
|
|
|
|
|
|
|
|
|
|
|
|
|
|
|
|
||||
|
|
|
|
|
|
|
|
|
|
ЭФ |
|
|
|
|
|
|
|
|
|
|||||
m1 |
|
|
|
О.О. |
|
|
|
|
|
|
|
МФ |
|
|
|
|
|
m4 |
||||||
|
|
|
|
|
|
|
|
|
|
|
|
|
|
|||||||||||
|
|
|
|
|
|
|
|
|
|
|
|
|
|
|
|
|
|
|||||||
|
|
|
|
|
|
|
|
|
|
|
|
|
|
|
|
|
|
|
|
|
|
|
|
|
|
|
|
|
|
|
|
|
|
|
|
|
|
|
|
|
|
|
|
|
|
|
|||
|
|
|
|
|
|
|
|
|
|
|
|
|
|
|
|
|
|
|
|
|
||||
|
|
|
|
|
|
3 |
|
|
|
|
|
|
|
|
|
|
|
|
|
|
|
|||
|
|
|
|
|
|
|
|
|
|
|
|
|
на утилизацию |
|||||||||||
|
|
|
|
|
|
|
|
|
|
|
|
|
|
|
|
|
|
|
||||||
|
|
|
|
|
|
|
|
|
|
|
|
|
|
|
|
|
|
|
||||||
|
осадок α (m1+m2) |
|
|
|
ФП |
|
|
|
|
|
|
|
|
|
|
|
|
|
|
|
||||
|
|
|
|
|
|
|
|
|
|
|
|
|
|
|
|
|
|
Рисунок 5.4 – Схема многостадийной очистки сточных вод от органических загрязнений с использованием сорбентов: 1 – емкость для перемешивания; 2 – тонкостенный отстойник; 3 – фильтр-пресс; 4 – емкость для перемешивания; 5 – электрофлотатор;
6 – микрофильтр; 7 – колонна с активированным углем

186
Сорбенты:
m1 → гидроксиды Me2+/3+ (Fe, Al, Cr, Cu, Zn, Ni и др.); m2 → ОУ-А (ОУ-Б), Al3+, Fe3+;
m3 → ОУ-А(ОУ-Б) + Al3+; m∑ = α∙m3+(1-α)∙(m1+m2);
m4 – сорбционная загрузка фильтр (БАУ).
Дозировка сорбентов производится на стадиях 1,4,7.
Как отмечается в литературе [5, 7], адсорбция неионогенных и анионных ПАВ протекает на поверхности гидроксидов за счет замены молекул воды, сорбированной на атоме металла по схеме:
+n |
. |
|
|
{ Ме |
H2O |
||
|
|||
OH |
|
|
{+ тв
ПАВнр-р
{
+n Ме .
OH
ПАВ{+ тв
H2O |
р-р |
|
Адсорбция таких ПАВ приводит к гидрофобизации поверхности и изменению краевого угла смачивания, что ведет к росту степени электрофлотационного извлечения и интенсификации процесса.
Наиболее масштабно указанный эффект наблюдается для дисперсной фазы
Cr(OH)3, Al(OH)3, Al(OH)3-x(SO4)x; Fe(OH)3, Al(OH)2Cl и других гидроксидах степень извлечения возрастает до 95–98%. За счет наличия на поверхности гидроксидов мест для адсорбции на гидроксидах имеются места для адсорбции и катионных ПАВ, и в реальных системах, где присутствуют различные гидроксиды, с разным значением заряда поверхности и ξ-потенциала. Экспериментальные данные представлены в разделах 3 – 4.
Например, при рН 9–10 ξ-потенциал Fe(OH)3, Al(OH)3 имеет отрицательное значение, так как ИЭТ находится при рН 6–7, в то время как для Ni(OH)2 pH 10–10,5
соответствует ИЭТ и ξ-потенциал стремится к нулю. В этом случае, как часто используют в обогащении минералов, целесообразно для очистки сточных вод сложного состава использовать смеси двух ПАВ различной природы, ПАВа – ПАВк, например, (МТМх)а 80% + (Флон-1) к 20% или СептаПАВк 20% – NaDDSа 80%.
Анализ влияния ПАВ на величину ξ-потенциала частицы (заряд поверхности),
показал, что для всех изученных объектов тенденции к влиянию ξ-потенциала идентичны:
анионные ПАВ снижают ξ-потенциал, катионные ПАВ повышают величину
ξ-потенциала. Влияние неионогенного ПАВ невелико и обычно изменяется на ±5 мВ в зависимости от того, как молекула ориентирована на поверхности, положительной или
187
отрицательной частью в раствор. Экспериментальные данные представлены в разделах 3–4.
Влияние ПАВ на размер частиц дисперсной фазы, в отличии от флокулянта, где всегда наблюдается увеличение размера, не так однозначно. Например, для Ni(OH)2
размер частиц возрастает незначительно, в присутствии анионного ПАВ размер частиц находится на уровне 40–50 мкм. Гидроксид цинка имеет достаточно большой размер частиц (150–180 мкм), влияние ПАВ практически отсутствует. Для Cu(OH)2 увеличение размера частиц наблюдается при добавлении катионного ПАВ с 60 до 100 мкм. На осадках фосфатов Ni, Cu, Zn (отрицательно заряженных) наблюдается увеличение размера частиц с 10–12 до 30–40 мкм при добавлении катионного ПАВ.
Для использования ПАВ в ЭФ технологии очистки сточных вод для извлечения ВВ,
гидроксидов (до 200 мг/л) необходимая концентрация добавки – 5–10 мг/л.
Положительное влияние изменение поверхностных характеристик связано с сорбцией. В случае ионной флотации концентрация ПАВ значительно выше и соответствует стехиометрии реакции типа:
Me3+ (р-р) + 3R– (Ан) → MeR3↓ (осадок)
При концентрации анионных ПАВ более 100 мг/л и при низкой концентрации металлов 5–20 мг/л, в первую очередь комплексообразователей (Cu, Zn, Fe, Al, Cd),
отмечаются эффекты растворения осадка и формирования растворимых комплексов, что исключает возможность извлечения дисперсной фазы. Для ряда систем при введении ПАВ установлено изменение структуры осадка (Cu(OH)2 – СептаПАВ).
В литературе [14] отмечается, что присутствие ПАВ в растворе стабилизирует газовую фазу, в частности размер пузырьков H2, величина которых составляет 20–25 мкм.
Кривые распределения пузырьков H2 и O2 по размерам в присутствии ПАВ показываю более монодисперсный состав, что ведет к повышению степени извлечения частиц и интенсификации процесса электрофлотации.
Положительное действие ПАВ отмечается при стабилизации пенного слоя (см.
подраздел 4.3), в первую очередь для гидроксидов РЗМ, состав осадка содержит до 8
молекул воды (Me(OH)3·8H2O). Все это делает осадок сильно гидрофильным и плохо извлекаемым во флотационном процессе и нестабильным на границе раздела H2О – воздух. Добавление ПАВ гидрофобизирует поверхность, что ведет к росту степени извлечения. С электрохимической точки зрения анионный ПАВ анодно-устойчивый.
188
Процессы окисления практически не протекают при адсорбции ПАВ на электродах,
за счет роста перенапряжения реакции выделения водорода на катоде и кислорода на аноде, размер пузырьков незначительно может уменьшаться, о чем часто пишут в литературе.
Флокулянты широко используются в очистке сточных вод, в первую очередь для укрупнения частиц дисперсной фазы с последующим отделением флотацией,
фильтрацией, седиментацией. Во всех случаях при правильно подобранных флокулянтах с учетом знака ξ±-потенциала размер частицы укрупняется.
Необходимо отметить, что тенденция изменения ζ-потенциала при добавлении анионных ПАВ и флокулянта – снижение ζ-потенциала идентичны. Добавление катионных ПАВ и флокулянта – рост ζ-потенциала. Указанные эффекты свидетельствуют о том, что места для адсорбции на гидроксидах идентичны, а именно для катионных – это кислородные группы, для анионных – это ионы металлов.
Me-О ↔ Флок (кат) (ПАВк) Me-H2O ↔ Флок (ан) (ПАВа)
Обычно для флотации количество добавления флокулянта 2–10 мг/л на 150–200
мг/л ВВ, при более высоких концентрациях 10–20 мг/л взвешенные вещества коагулируют, образуя в нижней части аппарата осадок. При длительном хранении (более
2–3 ч) осадок «желируется» и плохо фильтруется на фильтр-прессах и вакуум-фильтрах.
На основании проведенных исследований определены факторы интенсификации и подавления электрофлотационного процесса извлечения гидроксидов металлов.
Высокую эффективность процесса извлечения смеси гидроксидов (Cu, Zn, Ni, Co, Cd, Fe) обеспечивают промышленные ПАВ: МТМх, МТМл или их смесь 80% + 20%,
применяемые при извлечении Al2O3. Особенно в тех случаях, когда наблюдается образование комплексов, например, Cu–NH4OH, Zn–NH4OH, Ni–NH4OH.
Экспериментальные данные по ЭФ извлечению многокомпонентной системы гидроксидов (Cu, Zn, Ni, Co, Fe) в аммиачных средах в присутствии промышленного ПАВ представлены в подразделе 6.1 и разделе 4.
В присутствии ПАВ эффективность процесса возрастает с 15–60% до 92–94 % в
течении 5 мин электрофлотации, что несомненно положительно влияет на энергозатраты и производительность установок.
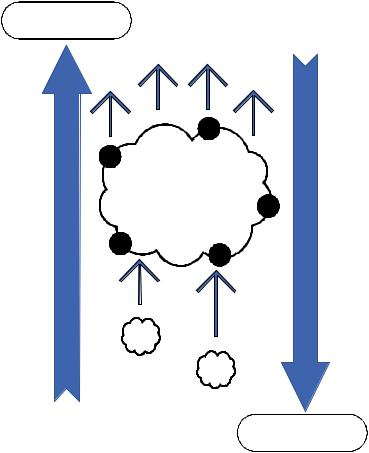
189
Среди факторов подавления ЭФ процесса следует выделить присутствие органических веществ, способных формировать растворимые комплексы с Cu2+, Ni2+, Cd2+ и другими металлами.
|
|
|
На рисунке 5.5 представлены факторы интенсификации и подавления ЭФ процесса, |
||||||||||||||||||||
которые учитываются при разработке технологии водоочистки. |
|
|
|
|
|
|
|
|
|
||||||||||||||
|
|
|
|
|
|
|
|
|
|
|
α(max) = 95–98 % |
|
|
|
|
|
|
|
|
|
|
|
|
|
α |
5 |
= 90% |
|
|
|
|
|
|
|
|
|
|
|
|
|
|
|
|
|
|
|
|
|
|
|
|
|
|
|
|
|
|
|
|
|
|
|
|
|
|
|
|
|
|
|
|
|
ПАВа(80%)+ ПАВк(20%) |
|
|
|
α |
5 |
= 25% |
|
|
||||||||||||||
|
|
|
|
|
|
|
|
|
|
|
|
|
|
|
|
||||||||
|
|
|
|
|
|
|
|
|
|
|
|
|
|
|
|
|
|
|
|
|
|
||
|
С(ПАВа) = 5–10 г/м |
3 |
|
|
|
|
|
|
|
|
|
|
|
|
|||||||||
|
|
|
рост С(эл-та) с 1 до 100 г/л |
||||||||||||||||||||
|
|
|
|
|
|
|
|
|
|
|
|
|
|
||||||||||
|
С(ПАВк) = 5–10 г/м |
3 |
|
|
|
|
|
|
|
|
|
|
|
|
|||||||||
|
|
|
R < 10 мкм |
|
|||||||||||||||||||
|
|
|
|
|
|
|
|
|
|
|
|
|
|
|
|||||||||
|
С(Флок = 5–20 г/м |
3 |
|
|
|
|
|
|
|
|
|
|
|
|
|
|
|||||||
|
|
|
|
|
ζ = –20 мВ (отриц.) |
||||||||||||||||||
|
|
|
|
|
|
|
|
|
|
|
|
|
Ме(OH) |
||||||||||
|
|
|
|
|
|
|
|
|
|
|
|
|
|
|
|
|
|
|
|
|
|
|
|
|
ПАВн |
|
|
|
|
|
|
|
|
|
3 |
|
|
|
|
2– |
|
3– |
2– |
2– |
|||
|
|
|
|
|
|
|
|
|
+ |
X |
|
||||||||||||
|
|
|
|
|
|
3+ |
|
|
3+ |
|
|
– PO4 |
|
, S |
, CO3 |
||||||||
|
Коагулянт Fe |
|
|
|
|
|
|
|
– |
|
|
|
|
|
|||||||||
|
, Al |
|
|
|
Me(OH)2 |
|
L |
– ЭДТА. Тартрат, NH |
|||||||||||||||
|
|
|
|
|
|
|
|
|
|
|
|
(взвешенные вещества) |
|
|
|
|
|
|
|
|
|
3 |
|
|
Композиция Fe |
3+ |
– ПАВа |
|
орг.в-ва – комплексообр-е |
||||||||||||||||||
|
|
|
|||||||||||||||||||||
|
|
|
|
|
|
|
|
|
|
|
|
|
|
||||||||||
|
Композиция Al |
3+ |
– ПАВа |
|
|
|
|
|
|
|
|
|
|
|
|
||||||||
|
|
|
Jv > 0.6 А/л |
|
|||||||||||||||||||
|
|
|
|
|
|
|
|
|
|
|
|
|
|
|
|||||||||
|
ζ = ±5 мВ |
|
|
|
|
|
|
|
|
|
|
С(веществ) > 500 мг/л |
|||||||||||
|
|
|
|
|
|
|
|
|
|
|
|
|
|
||||||||||
|
Rчаст ~ 40–50 мкм |
|
|
|
|
|
τ |
преб |
< 10 мин |
|
|||||||||||||
|
|
|
|
|
|
|
|
|
|
|
|
|
|
|
|||||||||
|
Jv = 0,2–0,4 А/л |
|
|
|
|
|
|
|
|
|
|
|
3 |
|
|
|
3 |
||||||
|
|
|
|
|
|
|
|
|
|
|
|
|
|
1 м (ап) |
|
>5 м /H O(тех) |
|||||||
|
|
|
|
|
|
|
|
|
|
|
|
O |
|
|
|
|
|
|
|
|
|
|
2 |
|
Rпуз (+ПАВ) = 20–40 мкм |
|
|
|
|
|
|
|
|
|
|
|
|||||||||||
2 |
|
|
|
|
|
|
|
|
|
|
|
||||||||||||
|
τ |
|
|
15 мин |
|
|
|
|
|
|
|
|
|
|
|
|
|
|
|
|
|
|
|
|
преб |
|
|
|
|
|
|
|
|
ζ < 0 |
H2 |
|
|
|
|
|
|
|
|
|
|
||
|
|
|
3 |
|
|
3 |
|
|
|
|
|
|
|
|
|
|
|
|
|
|
|||
1 м (ап) |
4 м /H O(тех) |
|
|
|
|
|
|
|
|
|
|
|
|
||||||||||
|
|
|
|
|
|
|
|
2 |
|
|
pH = 7–11 |
|
|
|
|
|
|
|
|
|
|
||
|
|
|
|
|
|
|
|
|
|
|
|
|
|
|
|
|
|
|
|
|
|
||
|
|
|
|
|
|
|
|
|
|
|
|
|
|
α(min) = 10–25 % |
|
|
|
|
|
Рисунок 5.5 – Факторы интенсификации и подавления ЭФ процесса извлечения гидроксидов металлов
При электрофлотации ряда частиц дисперсной фазы TiO2, TiN, SiC, Sc2O3, SiO2,
углеродных порошков (ОУ-А, ОУ-Б, МеКс-О) и углеродных наноматериалов (УНВ, УНЧ,
УНТ) отмечена низкая эффективность ЭФ процесса, степень извлечения 10–15%, время флотации 30–60 мин. Добавление флокулянтов и ПАВ различной природы не приводит к росту степени извлечения ввиду слабой адсорбции на указанных порошках. Причины – это различные структуры осадка, наличие пор (угли), недоступных для больших молекул,
физико-химические свойства и электронные характеристики металлов в структуре компонентов. Как показали проведенные исследования, степень извлечения существенно возрастает при добавлении коагулянтов на основе солей Fe3+ и Al3+, в области рН 4–10
формирует осадки гидроксидов, которые захватывают частицы (оксиды, карбиды, ОУ-Б
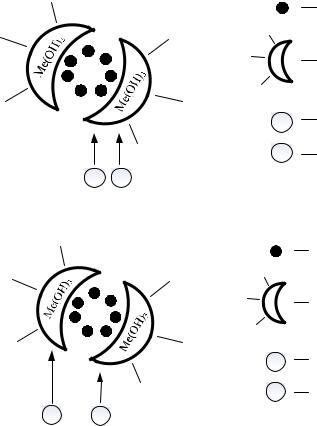
190
и др.), увеличивая их размер, что в конечном итоге интенсифицирует процесс флотации,
седиментации. С другой стороны, электрофлотация такой системы, как Me(OH)3·nH2O – TiO2, Me(OH)3·nH2O – SiC, Me(OH)3·nH2O – ОУ вследствие увеличения размера порошков с 10–15 до 50–60 мкм протекает достаточно эффективно. В ряде случаев степени извлечения достигают 90–95%. С другой стороны, при высокой дозе коагулянта скорость флотационного процесса снижается, пенный продукт неустойчив, наблюдаются эффекты осаждения крупных частиц размером 1–10 мм.
Отмеченные ранее эффекты влияния анионных ПАВ на электрофлотацию гидроксидов железа, алюминия и титана стали научным заделом для создания флокулирующей композиции «коагулянт – ПАВ» для извлечения мелкодисперсных порошкообразных материалов и взвешенных веществ.
В присутствии флокулирующей композиции степень извлечения частиц возрастает до 90–98% при времени извлечения не более 5–10 минут. Схематично механизм флокуляции частиц для электрофлотационного извлечения представлен на рисунке 5.6.
H O |
|
|
|
|
|
|
|
|
2 |
|
|
|
|
|
|
|
|
|
|
|
|
|
частица |
|
|
|
H O |
|
|
H O |
H O |
|
|
|
|
|
|
2 |
|
|
|
|
||
2 |
|
|
2 |
|
|
|
|
|
|
|
|
|
H O |
Коагулянт |
|
||
|
|
|
|
2 |
(Me(OH) |
|
nH |
O) |
|
|
|
|
|
3 |
|||
|
|
|
|
|
|
2 |
|
|
|
|
|
|
H O |
|
|
|
|
|
|
|
|
2 |
|
|
|
|
H O |
|
|
H O |
|
|
|
|
|
|
|
2 |
|
|
|
|
|
|
2 |
|
|
|
|
пузырек H |
|
||
|
|
|
|
H |
|
|||
|
|
|
|
|
|
2 |
|
|
|
|
|
|
2 |
|
|
|
|
|
|
H O |
|
O |
пузырек О |
|
||
|
|
2 |
|
2 |
|
|
2 |
|
|
H |
O |
|
|
|
|
|
|
|
2 |
2 |
|
|
|
|
|
|
|
|
Вариант А |
|
|
|
|
||
ПАВ |
|
|
|
|
|
|
|
|
|
|
|
|
|
частица |
|
|
|
ПАВ |
|
|
ПАВ |
ПАВ |
|
|
|
|
|
|
|
|
ПАВ |
флотокомпозиция |
|||
|
|
|
|
|
||||
|
|
|
|
ПАВ |
|
|
|
|
ПАВ |
|
|
ПАВ |
|
|
|
|
|
|
|
|
|
пузырек H2 |
|
|
||
|
|
|
|
H2 |
|
|
||
|
|
|
|
|
|
|
|
|
|
|
ПАВ |
|
O2 |
пузырек О2 |
|
|
|
O2 |
H2 |
|
|
|
|
|
|
|
Вариант Б Рисунок 5.6 – Механизм флокуляции частиц для ЭФ процесса извлечения
191
При реализации механизма по варианту А происходит укрупнение извлекаемой частицы (TiO2, ОУ-Б, SiC), однако поверхность вновь сформированной дисперсной фазы
Me(OH)3 – частица остается гидрофильной. Рост степени извлечения в основном связан с увеличением размеров флотокомплекса.
При реализации механизма по варианту Б происходит укрупнение извлекаемой частицы за счет коагулянта Me(OH)3. Добавление ПАВ снижает смачиваемость гидрофильного осадка, делая поверхность более гидрофобной, все это приводит к росту степени извлечения до 98–99% и скорости всплытия флотокомплекса гидроксид – пузырьки H2 и O2.
Экспериментальные доказательства двух механизмов флокуляции для электрофлотационного процесса получены при проведении лабораторных исследований.
Анализ литературы показал, что для различной дисперсной фазы ПАВ ведет себя по-разному, обеспечивая функции собирателя, смачивателя и пенообразователя [12].
Для исследования объектов в рамках выполнения данной диссертационной работы ПАВ является скорее собирателем, снижая смачиваемость поверхности гидрофильного материала, делая поверхность более гидрофобной, в первую очередь для гидроксидов
Me(OH)2, Me(OH)3. В этом случае величина краевого угла смачивания θ увеличивается
(cos θ < 0).
Для высокодисперсных углеродных материалов БАУ, ОУ-А, ОУ-Б, УНЧ,
добавление ПАВ приводит к эффекту смачивания поверхности гидрофобного материала,
делая его более гидрофильным. В этом случае величина краевого угла смачивания θ уменьшается, cos θ увеличивается. С увеличением концентрации ПАВ эффект смачивания возрастает, электрофлотация протекает неэффективно.
Анализ литературы по применению ПАВ и, в частности, МТМх и Флон-1 показал,
что введение ПАВ в систему H2O – нефелин (Al2O3) – МТМх приводит к снижению краевого угла смачивания θ со 110o до 80о при концентрации анионного ПАВ – 0,1 г/л.
Для катионного ПАВ Флон-1 краевой угол смачивания θ изменяется со 110о до 68о .
Указанные эффекты связаны с ростом гидрофильности поверхности оксида алюминия, что ведет к реализации процесса обратной флотации, гидрофильная дисперсная фаза остается в растворе, в пенный продукт извлекается гидрофобная дисперсная фаза примесей (SiO2, Fe2O3).
192
Добавление промышленного ПАВ МТМх(ан) использовано совместно с коагулянтом Al(OH)2Cl и флокулянтами ПАА(а) и Superfloc.
Для случая очистки фильтрата ТБО от ВВ в присутствии коагулянта Al(OH)2Cl,
дисперсная фаза будет гидрофильно-гидрофобной (при добавлении ПАВ).
Максимальные степени извлечения составляют для напорной флотации 50–70%,
электрофлотации 85–90%. Прогноз специалистов РХТУ им. Д.И. Менделеева для системы ВВ – Al(OH)2Cl – флокулянт, α=80–85%, для системы ВВ – Al(OH)2Cl –
флокулянт – ПАВ, α=90–95%.
В работах профессора Б.С. Ксенофонтова отмечается, что эффективность флотационного извлечения дисперсной фазы сильно зависит от гидрофильно-
гидрофобных свойств поверхности и способа газонасыщения жидкости (типа машины).
Сравнительные данные представлены в таблице 5.1.
Таблица 5.1 – Сравнительная оценка эффективности извлечения гидрофобных и гидрофильно-гидрофобных загрязнений из сточных вод в различных флотационных машинах комбинированного типа и обычного исполнения [11]
Тип |
флотационных |
Эффективность извлечения загрязнений, % |
||
машин и аппаратов |
гидрофобных |
гидрофильно-гидрофобных |
||
Механические |
|
60–70 |
10–15 |
|
Пневматические |
|
55–65 |
10–15 |
|
Напорные |
|
|
90–95 |
50–70 |
Электрофлотационные |
90–98 |
85–95 |
||
Флотационные |
|
|
|
|
механические |
машины |
45–55 |
5–10 |
|
обычного исполнения |
|
|
Электрофлотация обеспечивает максимальную эффективность извлечения ВВ из водных растворо и является высокоэффективным процессом извлечения высокодисперсных порошков материалов (оксиды, карбиды, ВДУМ) из сточных вод в присутствии флокулирующей композиции: «Fe(OH)3 – ПАВа», «Al(OH)3 – ПАВа».
Объекты, где композиция работает эффективно представлены на схеме на рисунке 5.7.
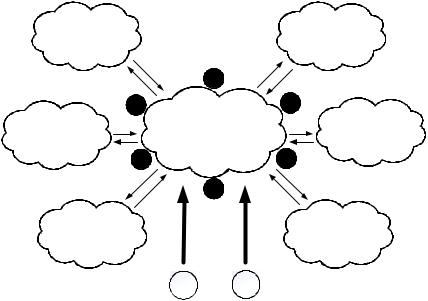
|
|
|
193 |
|
|
|
|
TiO |
, Ti(OH) |
|
|
ВДУМ |
|
|
|
4 |
|
(ОУ-А, ОУ-Б, МЕКС-О) |
|
||||
2 |
|
|
|
||||
|
|
|
ПАВ |
|
|
|
|
|
ПАВ |
|
|
ПАВ |
|
|
|
|
|
|
|
|
|
|
|
? |
|
|
|
|
|
MeS |
|
|
Me(OH) |
|
Me (PO ) |
||||
|
|
|
3 |
4 2 |
|||
|
|
3-x |
(Zn, Cu, Ni) |
||||
|
|
|
|||||
|
ПАВ |
|
|
ПАВ |
|
|
|
|
|
|
|
|
|
|
|
|
TiC |
|
ПАВ |
Se O |
3 |
|
|
|
|
|
|
2 |
|
|
|
|
SiC |
|
|
La O |
3 |
|
|
|
|
|
|
2 |
|
|
|
|
TiN |
|
|
SiO |
|
|
|
|
|
|
|
|
2 |
|
|
|
|
H |
O |
|
|
|
|
|
|
2 |
2 |
|
|
|
|
Рисунок 5.7 – Схема применения флокулирующей композиции для ЭФ извлечения дисперсной фазы
Наиболее эффективно применение флокулирующей композиции коагулянт – ПАВ.
Применение флокулирующей композиции позволяет интенсифицировать процесс.
Снизить энергозатраты, время нахождения жидкости в ЭФ аппарате, увеличить степень извлечения порошков, осадков, стабилизировать пенный продукт и уменьшить количество осадка, формируемом на дне ЭФ аппарата.
В таблице 5.2 представлены экспериментальные результаты, где, применяя определенные технологические приемы, процесс ЭФ извлечения протекает с высокой эффективностью.
Таблица 5.2 – Объекты с высокой эффективностью электрофлотационного процесса извлечения дисперсной фазы
Параметр |
|
|
|
|
|
Объекты |
|
|
|
||
TiO2 |
TiN |
SiC |
ОУ-А |
ОУ-Б |
ВВ (ТБО) |
Sc2O3 |
|
МеКс-О |
|||
|
|
|
|||||||||
K |
|
0,25 |
0,25 |
015 |
0,27 |
|
0,2 |
0,2 |
0,26 |
|
|
|
|
|
|
|
|
|
|
|
|
|
|
α5 |
|
85 |
85 |
70 |
92 |
|
75 |
80 |
90 |
|
|
|
|
|
|
|
|
|
|
|
|
|
|
α30 |
|
98 |
95 |
92 |
96 |
|
98 |
92 |
96 |
|
|
|
|
|
|
|
|
|
|
|
|
|
|
Добавка |
|
|
|
|
|
|
Fe- |
|
|
|
|
|
|
Fe- |
Al- |
Fe- |
Fe- |
|
ПАВ |
Al-ПАВ – |
Fe-ПАВ |
|
|
|
|
ПАВ |
ПАВ |
ПАВ |
ПАВ |
|
Al- |
флок. |
Al-ПАВ |
|
|
|
|
|
|
|
|
|
ПАВ |
|
|
|
|
Условия |
эксперимента: |
с ВВ |
≤ 100 |
мг/л; с |
коагулянт |
– 5–10 |
мг/л; с ПАВ, |
с флокулянта – 5–10 мг/л; рН = 6–8; с электролит – 1 г/л; Композиция Ме(OH)3 – ПАВа;
ПАВ – NaDDS, МТМх, NaDBS.
194
На основании проведенных лабораторных исследований и опытно-промышленных испытаний можно утверждать, что, используя различные технологические приемы,
можно увеличивать эффективность электрофлотационного процесса до приемлемых значений величины степени извлечения, времени процесса, энергозатрат и себестоимости очистки, что расширяет области практического применения. Среди технологов,
работающих на установках водоочистки, и проектировщиков, использующих рекомендации ученых, в последние 10 лет ведется дискуссия, что лучше применять для интенсификации процессов водоочистки. Автором на основании опыта работы проведена оценка по ряду параметров использования флокулянтов и ПАВ в ЭФ процессе.
Сравнение, что лучше флокулянт или ПАВ для электрофлотационного процесса очистки представлено в таблице 5.3.
195
Таблица 5.3 – Сравнение «флокулянт – ПАВ. Что лучше для ЭФ процесса водоочистки на
промышленных объектах»
№ |
Параметры |
|
ПАВ |
Флокулянт |
|
|
(промышленный) |
(промышленный) |
|||
|
|
|
|||
1. |
Эффективность ЭФ процесса |
Высокая |
Высокая |
||
(α=95–99%) |
(α=90–95%) |
||||
|
|
|
|||
2. |
Изменение размера частиц |
Незначительно |
Увеличение в 2–3 раза |
||
3. |
Изменение |
ζ-потенциала |
Да |
Да |
|
частицы |
|
||||
|
|
|
|
||
4. |
Гидрофобность |
|
Увеличение |
Нет изменений |
|
5. |
Стабильность пены |
Да |
Нет |
||
6. |
Распределение частиц |
Пена – 90–95% |
Пена – 20–30% |
||
Осадок – 5–10% |
Осадок – 70–80% |
||||
|
|
|
|||
7. |
Фильтрация осадка |
Эффективно |
Проблемно |
||
(Фильтр-пресс) |
|
||||
|
|
|
|
||
8. |
Микрофильтрация взвешенных |
Эффективно |
Проблемно |
||
веществ |
|
||||
|
|
|
|
||
9. |
Приготовление |
растворов |
Простое |
Сложное |
|
длительного хранения добавки |
30–60 дней |
До 5 дней |
|||
|
|||||
10. |
Норма дозирования (г/м3) |
5–10 |
10–20 |
||
11. |
Универсальность |
(катионный, |
Высокая |
Средняя |
|
анионный, неионогенный) |
|||||
|
|
|
|||
12. |
ЭФ (α5) – интенсивность (%) |
85–90 |
70–85 |
||
13. |
Сорбция на гидроксильных |
высокая |
Флокуляция |
||
осадках |
|
||||
|
|
|
|
||
|
|
|
МТМх – 35 |
|
|
14. |
Цена продукта (руб/кг) |
МТМл – 17 |
ПАА – 200–300 |
||
Флок – 250 |
Superfloc – 200–300 |
||||
|
|
|
|||
|
|
|
NaDDS – 250 |
|
|
15. |
Остаточное содержание в воде, |
Минимальное |
Минимальное |
||
мг/л |
|
1–0,1 (<ПДК) |
1–0,1 (<ПДК) |
||
|
|
Представленные характеристики по большинству параметров показывают перспективность применения ПАВ в процессах водоочистки. Необходимо отметить важный фактор – ПАВ часто присутствует в сточных водах, ввиду широкого технологического применения и специально добавлять 1–10 мг/л нет необходимости,
флокулянт всегда надо добавлять для повышения эффективности.