
Учебное пособие 2170
.pdfОсобенность дисперсно-упрочненных композиционных материалов – изотропность свойств, определяемая модулями упругости и податливости.
Используя представление единичного тензора в виде суммы объемной и девиаторной составляющих можно представить тензоры модулей упругости c и податливости s изотропной среды в виде
c 3KV 2 D, |
s 3pV 2qD |
(2) |
|
где |
К – объемный модуль упругости; |
|
|
|
- сдвиговый модуль упругости. |
|
Иногда вместо (2) удобнее пользоваться следующими
представлениями: |
|
|
c 3 V 2 I, |
s 3sV 2qI |
(3) |
где =К – 2/3 - постоянная Ламе; V – единичный объемный тензор;
I – единичный тензор четвертого ранга;
q – податливость, связанная со сдвиговым дефор-
мированием.
Из соотношения (2) и (3) находим, что податливости s, p и q выражаются через объемный и сдвиговый модули упругости при помощи соотношений
s |
1 |
|
1 |
, |
p |
1 |
, |
q |
1 |
(4) |
9K |
|
|
4 |
|||||||
|
|
6 |
|
9K |
|
|
По известным модулям упругости К и могут быть вычислены другие постоянные упругости.
Обозначив модули упругости, полученные осреднением тензора c через Кv и v, а осреднением тензора s через КR и R, можно получить следующие неравенства
KR K* KV , |
R * V |
(5) |
90
где K* - эффективный объемный модуль упругости;* - эффективный сдвиговый модуль упругости.
Эти величины связывают осредненные напряжения и деформации и именно эти модули измеряются экспериментально на образцах, размеры которых существенно превышают средний размер зерна.
В связи с вышеизложенным, получение математических зависимостей, позволяющих аналитически определять модули упругости и податливости реальных композитных сред, является весьма ценным.
Литература
1.Жачкин С.Ю. Холодное гальваноконтактное восстановление деталей. Воронеж: ВГУ, 2002. 138 с.
2.Жачкин С.Ю. Моделирование механического воздействия инструмента при получении гальванических композитных покрытий / С.Ю. Жачкин, М.Н. Краснова, Н.А. Пеньков, А.И. Краснов // Труды ГОСНИТИ. – 2015. – Т. 120. – С. 130 – 135.
3.Жачкин С.Ю. Нанесение размерных композитных хромовых покрытий методом гальваноконтактного осаждения / С.Ю. Жачкин // Упрочняющие технологии и покрытия. – 2006. - № 7. - С. 44 – 48.
4.Жачкин С.Ю. Расчет напряжений в дисперсноупрочненных композитных гальванических покрытиях / С.Ю. Жачкин, Н.А. Пеньков, О.А. Сидоркин, С.В. Нелысов // Наука в центральной России. – 2016. - № 2. - С. 32 – 37.
5.Жачкин С.Ю. Аналитическая оценка свойств дисперсноупрочненных гальванических композитных многослойных покрытий / С.Ю. Жачкин, Н.А. Пеньков, А.И. Краснов, К.А. Манаенков
//Вестник Мичуринского государственного аграрного университета. – 2015. - № 1. - С. 142 – 150.
6.Жачкин С.Ю., Пеньков Н.А., Краснова М.Н., Сидоркин О.А. Восстановление гидроцилиндров дисперсно-упрочненным гальваническим композитным покрытием на основе хрома. Воронеж, ВГТУ, 2017. 162 с.
Воронежский государственный технический университет
91
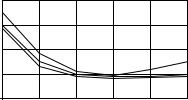
УДК 621.9.047
С.Ю. Жачкин, д-р техн. наук, проф., Н.А. Пеньков, канд. техн. наук, нач. лаб., М.Н. Краснова, канд. техн. наук, доц.
УПРАВЛЕНИЕ КАЧЕСТВОМ КОМПОЗИТНЫХ ГАЛЬВАНИЧЕСКИХ ПОКРЫТИЙ
ПРИ ВОССТАНОВЛЕНИИ ДЕТАЛЕЙ МАШИН
Рассматриваются вопросы получения качественных хромовых гальванических композитных покрытий в зависимости от давления инструмента на обрабатываемую поверхность детали. Приведены качественные и количественные характеристики процесса.
Ключевые слова: композитный материал, упрочение, покрытие.
Наиболее важным параметром процесса, влияющим на высоту шероховатости, является сила прижима инструмента. Зависимость шероховатости поверхности от силы прижима инструмента, как показала практика, качественно одинакова для различных материалов (рис. 1) [1, 4].
-ти, мкм |
0,08 |
|
|
|
|
|
0,06 |
1 |
|
|
|
|
|
пов |
|
|
2 |
|
|
|
Шероховатость |
0,04 |
|
|
|
|
|
0,02 |
|
|
|
|
|
|
0 |
|
3 |
|
|
|
|
|
|
|
|
|
|
|
|
0 |
1 |
2 |
3 |
4 |
5 |
|
|
|
Давление инструмента, МПа |
|
|
Рис. 1. Зависимость шероховатости поверхности
От давления инструмента при iк; 1 – 14 кА/м2; 2 – 10 кА/м2; 3 – 8 кА/м2
График зависимости шероховатости от усилия обработки можно разделить на три характерных участка: 1) участок уменьшения шероховатости от исходной до минимальной; 2) участок минимальной шероховатости; 3) участок последующего увеличе-
92
ния шероховатости по сравнению с минимальной.
При изменении силы прижима инструмента в пределах первого участка наблюдается уменьшение шероховатости, но все более медленное, а по достижении определенной величины силы уменьшение шероховатости прекращается [2, 3]. Это объясняется тем, что при малых силах контакт инструмента с обрабатываемой поверхностью происходит по вершинам неровностей, опорная площадь которых мала. Вследствие этого на площадях контакта развиваются значительные давления, превышающие предел текучести материала и вызывающие интенсивную пластическую деформацию неровностей. По мере роста силы прижима инструмента увеличивается глубина внедрения и растет площадь контакта инструмента с обрабатываемой поверхностью. Кроме того, в процессе пластической деформации поверхностный слой металла сильно упрочняется. Все это увеличивает сопротивление поверхности пластической деформации, и уменьшение шероховатости с увеличением давления замедляется.
При определенных значениях силы прижима инструмента происходит полное сглаживание исходных неровностей и образуется шероховатость, обусловленная только самим процессом контакта инструмента с обрабатываемой поверхностью — скоростью относительного перемещения инструмента по детали и пластических искажений. Увеличение силы прижима инструмента в пределах второго участка графика не вызывает поэтому существенного изменения шероховатости.
При осаждении покрытий методом ГКО пластическая деформация вызывает упрочнение поверхностного слоя металла: увеличиваются твердость, предел упругости и предел текучести, но уменьшается его пластичность. Упрочнение поверхностного слоя связано с изменением тонкой кристаллической структуры металла при пластической деформации. В этом случае наблюдается дробление зерен и образование мелкодисперсной структуры. Раздробление зерен вызывается скольжением отдельных частей кристаллов по плоскостям сдвигов. При этом увеличивается количество искажений кристаллической решетки — дислокации. Современная теория объясняет упрочнение металла при пластической деформации увеличением числа дислокаций, которые пре-
93
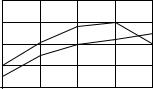
пятствуют перемещению отдельных частей кристаллов по плоскостям скольжения. Преодоление сопротивления дислокаций требует приложения значительно больших напряжений, чем необходимо в неупрочненном металле. Поэтому возрастает прочность пластически деформированного металла [5].
Упрочнение осаждаемого покрытия зависит от соотношения скорости осаждаемого слоя и величины силы прижима инструмента. Степень пластической деформации в наибольшей степени влияет на характеристики упрочнения покрытия. Поверхностная микротвердость с увеличением силы прижима инструмента возрастает (рис 2) и достигает максимума при давлении 2,5 — 3,0 МПа. Дальнейшее увеличение силы вызывает падение поверхностной микротвердости вследствие исчерпания способности материала тонкого поверхностного слоя к упрочнению и его перенаклепа [6].
При увеличении силы прижима инструмента выше расчетной происходит упрочнение все более глубоко залегающих слоев осаждаемого металла. При приложении чрезмерно больших нагрузок при общем росте глубины упрочненного слоя начинается разрушение тонкого поверхностного осаждаемого слоя, вызванного перенаклепом. Это прояляется в появлении микротрещин на поверхности и снижении микротвердости.
, МПа |
10000 |
|
|
|
|
9000 |
|
2 |
|
|
|
покрытия |
8000 |
1 |
|
|
|
|
|
|
|
|
|
Твердость |
7000 |
|
|
|
|
6000 |
|
|
|
|
|
|
|
|
|
|
|
|
1,5 |
2 |
2,5 |
3 |
3,5 |
|
|
давление инструмента, МПа |
|
Рис. 2. Влияние давления инструмента на упрочнение покрытия:
1 – макротвердость; 2 – микротвердость
Важной характеристикой упрочненного поверхностного слоя является градиент изменения микротвердости по толщине
94
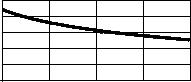
осажденного покрытия ( ) рис.3.
Величина , характеризует интенсивность изменения механических свойств металла по толщине осажденного покрытия. При слишком большой разнице в свойствах различных слоев осаждаемого металла возможно их отслаивание и зарождение подповерхностных трещин. Для метода ГКО характерно плавное изменение микротвердости по толщине слоя. Градиент микротвердости уменьшается с увеличением давления инструмента.
Увеличение числа проходов увеличивает кратность нагрузки и вызывает некоторое увеличение упрочнения.
При контакте инструмента с деталью происходит механическая обработка поверхностных слоев, и в них возникают остаточные напряжения, которые влияют на эксплуатационные качества обработанной поверхности. Появление остаточных напряжений вызывается пластической деформацией в процессе обработки. В результате действия пластической деформации возникают сжимающие остаточные напряжения.
градиент микротвердости, МПа х мкм
50
40
30
20
10
0
1,5 |
2 |
2,5 |
3 |
3,5 |
давление инструмента, МПа
Рис. 3. Зависимость градиента микротвердости от давления инструмента
При осаждении покрытия методом ГКО поверхностный слой обрабатываемой детали испытывает интенсивную пластическую деформацию, нагрев же его невелик. Все это должно обусловливать появление в поверхностном слое сжимающих остаточных напряжений. Однако, как показали многочисленные проведенные эксперименты, на поверхности покрытия наблюдалось некоторое уменьшение напряжений. Исходя из общей научной концепции, наличие спада напряжений на поверхности покрытия
95
автор объясняет, во-первых, схемой деформации. При контактной схеме деформации, когда максимум касательных напряжений находится в некоторой глубине, величина остаточных напряжений на поверхности должна уменьшаться; переход к контактносдвиговой схеме пластической деформации, когда наряду с радиальной силой начинает действовать и сдвигающая, приводит к уменьшению глубины залегания максимальных остаточных напряжений и к уменьшению спада напряжений к поверхности. Вовторых, уменьшение сжимающих напряжений на поверхности тонкого поверхностного слоя покрытия в процессе деформирования можно объяснить нагревом. Хотя температура, развиваемая при методе ГКО, невелика, можно предполагать, что она вызывает снижение величины сжимающих напряжений в тонком поверхностном слое, т.к. ее увеличение вызывает увеличение пластичности осажденного металла.
Структура покрытий, получаемых методом ГКО, как указывалось ранее, представляет собой металлическую основу с равномерно распределенными твердокомпонентными дисперсными включениями инструментального материала. С увеличением их содержания повышаются прочность, твердость, и уменьшается пластичность наносимого покрытия. Высокая прочность объясняется большой дисперсностью фазы включений, малым расстоянием между ее частицами. Нерастворимость в материале матрицы и отсутствие склонности к коагуляции мелкодисперсных частиц обеспечивает стабильность структуры и высокую прочность получаемых покрытий.
Литература
1.Жачкин С.Ю. Холодное гальваноконтактное восстановление деталей. Воронеж: ВГУ, 2002. 138 с.
2.Жачкин С.Ю. Моделирование механического воздействия инструмента при получении гальванических композитных покрытий / С.Ю. Жачкин, М.Н. Краснова, Н.А. Пеньков, А.И. Краснов // Труды ГОСНИТИ. – 2015. – Т. 120. – С. 130 – 135.
3.Жачкин С.Ю. Нанесение размерных композитных хромовых покрытий методом гальваноконтактного осаждения / С.Ю. Жачкин // Упрочняющие технологии и покрытия. – 2006. - № 7. -
96
С. 44 – 48.
4.Жачкин С.Ю. Расчет напряжений в дисперсноупрочненных композитных гальванических покрытиях / С.Ю. Жачкин, Н.А. Пеньков, О.А. Сидоркин, С.В. Нелысов // Наука в центральной России. – 2016. - № 2. - С. 32 – 37.
5.Жачкин С.Ю. Аналитическая оценка свойств дисперсноупрочненных гальванических композитных многослойных покрытий / С.Ю. Жачкин, Н.А. Пеньков, А.И. Краснов, К.А. Манаенков
//Вестник Мичуринского государственного аграрного университета. – 2015. - № 1. - С. 142 – 150.
6.Жачкин С.Ю., Пеньков Н.А., Краснова М.Н., Сидоркин О.А. Восстановление гидроцилиндров дисперсно-упрочненным гальваническим композитным покрытием на основе хрома. Воронеж, ВГТУ, 2017. 162 с.
Воронежский государственный технический университет
УДК 621.9.047 С.Ю. Жачкин, д-р техн. наук, проф., Н.А. Пеньков, канд.
техн. наук, нач. лаб., М.Н. Краснова, канд. техн. наук, доц., Ю.С. Гончарова, студент
КАЧЕСТВО СИСТЕМЫ РУЧНОГО УПРАВЛЕНИЯ МАНИПУЛЯЦИОННЫМИ СИСТЕМАМИ
ПРИ ОБРАБОТКЕ ДЕТАЛЕЙ АВИАЦИОННОЙ ТЕХНИКИ
Приведены данные по применению ЭВМ для расчета оптимальной траектории движения манипуляторов различных автоматизированных систем. Приводится количественная оценка меры информационной трудности решения поставленной задачи
Ключевые слова: ЭВМ, качество, манипуляционная система, деталь
Качество физического труда — ручного, механизированного, частично автоматизированного — во многих случаях можно достаточно полно охарактеризовать двумя показателями: точностью и производительностью. Нормы точности и нормы времени
97
в той или иной форме содержатся в любом задании, которое дается человеку, участвующему в рабочем процессе.
Производственные нормы обычно не оговаривают ни точной структуры рабочих движений, ни распределения времени при выполнении каждой отдельной операции либо даже в течение всего рабочего дня. В этом смысле они не подавляют человеческую индивидуальность и лишь согласуют различные индивидуальности, позволяют их соизмерить, количественно оценить результаты труда, определить необходимые его затраты, обеспечить коллективность действий.
Точность и производительность — два ключевых критерия, по которым оценивается также качество подавляющего большинства новых машин, станков, приборов, производственного оборудования. Таким образом, эти критерий используют как для оценки человеческого труда, так и для оценки качества машин. Естественно их применить также и для оценки качества систем «человек — машина», разнообразных систем ручного управления, в том числе устройств робототехники.
Следует сказать, что в различных видах труда тот или иной критерий может в зависимости от содержания задания играть определяющую роль либо носить подчиненный характер. Так, например, во всех задачах ручного отслеживания процессов, развертывающихся во времени, оператору фактически предъявляется задание в функции времени. При этом качество работы биотехнической системы оценивается точностью отработки задания.
В других случаях жестко задаются нормы точности, несоблюдение которых ведет к браку. При этом качество биотехнической системы оценивается по затратам времени на движения и действия, сопряженные с выдачей годного по точности результата.
Исследованию систем «человек — машина», в которых оператор отрабатывает задание, предъявляемое в функции времени, посвящено большое число работ, в том числе [1, 2, 3]. Методики и результаты этих исследований могут представлять интерес при формировании оценок качества копирующих устройств робототехники применительно, например, к решению двигательных задач динамического характера.
98
Другую группу составляют исследования вопросов ручного управления, когда задание формируется в виде некоторой функции координат системы. При этом режим работы определяет сам оператор, а в процессе исследования выявляется связь между сложностью задания и временем его выполнения. Ряд подобных исследований базируется на результатах, полученных в [4, 5]. Авторы этих работ рассматривают выполняемую вручную одномерную двигательную задачу точного позиционирования. В результате была установлена опытным путем закономерность, связывающая точность выполнения операции с временем ее выполнения. Она определяет информационную меру трудности выполнения указанной задачи и обычно записывается так:
Id |
ln |
2A |
(1) |
|
D |
||||
|
|
|
где Id — величина, измеряемая в битах информации и называемая индексом трудности, А — амплитуда движения (расстояние от начальной точки до цели), D — диаметр цели.
В результате исследований оказалось, что время выполнения такой операции в среднем прямо пропорционально ее индексу трудности. В дальнейшем было высказано предположение о том, что эти результаты могут быть обобщены применительно к работе оператора, управляющего манипуляционными системами (МС). При этом открылась возможность оценивать качество систем ручного управления, сопоставляя времена выполнения операции вручную и с помощью МС.
На рис. 1, а в качестве примера показана схема одной из подобных двигательных задач — взятие валика в точке О и сопряжение его с втулкой, находящейся на расстоянии А от точки О. Индекс трудности здесь выписывается так:
Id |
ln |
2A |
(2) |
|
B C |
||||
|
|
|
На рис. 1, б показаны результаты опытов по выполнению этой задачи вручную (прямая 1), а также с помощью двух разных
99