
874
.pdf
чертеж будет сопровождать развертка детали. Последовательность построения модели изображена на рисунке 5 (а, б, в, г).
а) |
б) |
в) |
г) |
Рис. 5. Листовое тело
Второй способ. Используем операцию создания обечайки с заданными переменными радиусами и зазором под сварку. На рабочем чертеже обечайки будет развертка с разметкой под гибку. Днище создаем отдельно из листового тела копируя нижнюю кромку обечайки для эскиза с помощью листового тела. Обечайку соединяют с днищем с помощью сварки, а значит нужно создать новый документ – сборку и соединить две детали совпадением объектов. На рабочем чертеже обозначаем сварные швы. Последовательность построения модели изображена на рисунке 6(а, б, в, г, д).
а) |
б) |
в) |
г) |
д) |
Рис. 6. Обечайка
261
Таким образом, возможности КОМПАС-3Dпозволяют выбрать рациональные приемы тонкостенного моделирования, обеспечивая правильное изготовление детали и качественное исполнение конструкторской документации.
Литература
1. Инженерная 3D-компьютерная графика: учебник и практикум для академического бакалавриата [Электронный ресурс] /А.Л. Хейфец [и др.]. - 3-е изд., перераб. и доп - Москва:
Юрайт, 2015. – Режим доступа: http://www.biblio-online.ru
УДК 678.012
С.В. Скачков – студент 4 курса; Е.Н. Перетягин – научный руководитель, ст. преподаватель,
ФГБОУ ВО Пермская ГСХА, г. Пермь, Россия
УВЕЛИЧЕНИЕ РЕСУРСА УЗЛОВ ТРАНСПОРТНЫХ И ТЕХНОЛОГИЧЕСКИХ МАШИН ПРИ ПОМОЩИ НАНОМАТЕРИАЛОВ
Аннотация. В статье изложены основные сведения о наноматериалах (трибопрепаратах), предназначенных для продления ресурса узлов транспортных и технологических машин. Приведены результаты лабораторных триботехнических исследований наноматериалов и эффективность их использования в условиях штатной эксплуатации машин.
Ключевые слова: трибосостав, наноматериал, ресурс, двигатель, мощность, расход топлива, эксплуатация.
До 80% износа является причиной отказа силовых агрегатов и агрегатов трансмиссии, что обусловливает материальные затраты, достигающие 2% ВВП развитых стран. Достижения машиностроения и нефтехимии обеспечили высокую износостойкость узлов трения машин и оборудования, но возможности дальнейшего прогресса требуют нерациональных затрат. Некоторым решением повышения износостойкости узлов трения является создание антифрикционных покрытий триботехническими методами в процессе эксплуатации, что позволяет в 2…3 раза увеличить срок службы агрегатов, до 20% уменьшить расход топлива, и до 50% – эксплуатационные затраты. Доказано, что введение в трибосреду, кроме присадок, нетрадиционных химически активных веществ, растворов органических солей мягких металлов, суспензий высокодисперсных порошков, природных и искусственных минеральных частиц, создающих пленочные покрытия, или повышающих адгезию смазки, или модифицирующих поверхности трения, технически и экономически оправдано[1].
По назначению, способам действия трибосоставы можно сгруппировать
на [2]:
- профилактические, применяемые в постгарантийный период работы машин, после обкатки отремонтированных агрегатов, после их безразборного ремонта; эти составы модифицируют поверхности трения на небольшую глубину или покрывают их мультимолекулярным ворсом, или полимерными пленками, или углеродной алмазоподобной, или аморфной углеводородной, структурированной
262
наноалмазами, или комплексными пленками с металлами, углеводородными соединениями и минералами, или хемосорбцией образуют галогениды железа;
-ремонтно – восстановительные (РВС), применяемые при исчерпании доремонтного (межремонтного) ресурса, образующие пленочные покрытия. Они действуют на поверхностях трения в силу физической, химической адсорбции, трибополимеризации, электролитического осаждения, активации ионообменных процессов в трибосреде, или же каталитически пленкообразуют органику. Продлевается ресурс изношенных узлов, агрегатов. Вместо текущего (капитального) ремонта РВС восстанавливают и функционирование агрегатов: мощность ДВС до номинальной и несколько выше, уменьшают изнашивание, расход ТСМ, выбросы вредных веществ, стуки и перегрев агрегатов трансмиссии, повышают КПД гидронасосов, давление и подачу ими смазки, рабочей жидкости, уменьшают утечки
вгидроприводах;
-притирочные, обеспечивающие выравнивание контакта сопряжений, уменьшение шероховатости и удельных давлений, а некоторые – и модифицируют поверхности, повышают их антифрикционные свойства и ресурс. Если составы просто разделяют поверхности без физикохимического действия, то притирочный эффект после смены смазки с трибосоставом не сохраняется.
Трибоматериалы по составу и механизму действия можно разделить на [2]:
-порошки природных минералов (графита, талька, каолина, монтмориллонита, гексагонального нитрида бора («белой сажи»), сернистых соединений и окислов некоторых металлов и т.п.), а также пудры резины, полимеров и опилок твердых пород дерева. Они не создают пленок, в основном только разделяют детали как «третье тело». Эти временные трибокомпоненты, удерживаемые физической адсорбцией, которая на два порядка слабее атомарных связей (хемосорбции), удаляются при смене трибосреды и требуют возобновления;
-масляные суспензии высокодисперсных порошков мягких металлов, их сплавов. Они без процессов трения на основе химического и физического осаждения образуют мягкие, выдавливаемые пленки на стальных деталях, которые отслаиваются, действуя коррозионно, а триботехника заметно ухудшается;
-масляные растворы органических солей мягких металлов (олеаты, пальметаты, стеараты и др.), которые действуют аналогично масляным суспензиям;
-фторорганические растворы политетрафторэтилена и его аналогов, образующие физической адсорбцией без трения временные пленки: осаждаются и в масляных каналах, закупоривая их, что негативно влияет на эффективность смазки ДВС;
-химически активные составы – галогенированные производные углеводородов, которые проникают на небольшую глубину поверхности деталей, придавая им высокие антифрикционные свойства;
-фторкарбонатные смолы с высокой адгезией к поверхностям снижающие износ на два порядка;
-трибополимеробразующие добавки, которые образуют антифрикционную
пленку;
-комплексные составы: органические добавки и серпентины, соли меди и серпентины и т.п.
263
Врезультате анализа большого количества источников установлено, что существенно продлить ресурс агрегатов, в режиме штатной эксплуатации, предположительно можно с помощью специальных нанопрепаратов – восстановительных антифрикционных и противоизносных добавок (ВАФПИД) к смазочным материалам. Нанодобавки к трансмиссионным и другим маслам отличаются от многочисленных присадок тем, что присадки ―работают‖ на масло, улучшая эксплуатационные свойства масел, в том числе и противоизносные, а нанопрепараты ВАФПИД ―работают‖ на металл, улучшая эксплуатационные свойства рабочих поверхностей деталей, причем эти препараты не реагируют с маслами и не ухудшают их качество[3].
Исследования, проведенные в ГОСНИТИ, показали, что ремонтновосстановительные составы целесообразно применять после 50 – 70% - ной наработки доремонтного или послеремонтного ресурса. В этом случае можно увеличить доремонтный ресурс более чем в 2 раза[4].
Вподтверждение этого были проведены исследования по количественной оценке повышения износостойкости пары трения за счет применения 6 типов препаратов с использованием машины трения. Исследовались нанопрепараты: РВС, ХАДО, Реагент-2000, СУПРОТЕК, ФОРСАН, АВТОКОМФОРТ [4].
Результаты исследования противоизносных свойств указанных препаратов по сравнению с чистым моторным маслом показали, что все препараты, предназначенные для увеличения ресурса двигателей, на машине трения проявили снижение величины износа образцов по сравнению с износом тех же образцов на чистом моторном масле в 2 раза и более [4].
Можно с уверенностью утверждать, что все препараты дают существенный положительный эффект по снижению износа образцов, а следовательно, и по замедлению скорости изнашивания деталей ресурсных сопряжений двигателя [4].
Испытания, проведенные в ГОСНИТИ на двигателях Д – 240 и в полевых условиях ЯМЗ – 240 показали, что потеря мощности на механическое трение в сопряжениях механизмов двигателей снизилась на 5,2% и в связи с этим существенно снизился часовой расход дизельного топлива на 15,5% и, соответственно, повысился индикаторный КПД на 15,2% [5].
Таким образом, благодаря использованию нанопрепаратов увеличивается межремонтный ресурс, снижается расход топлива, а также сокращаются убытки в связи с уменьшением простоя на устранение последствий отказов.
Литература
1.Пустовой И.Ф. 14-летний опыт Питерской РВС-технологии // Труды ГОСНИТИ. Т. 107, ч. 2 – М.: 2011 – с. 38-40.
2.Зуев В.В. Конституция, свойства минералов и строение земли. (Энергетические аспекты). – СПб.: Наука, 2005. – 400 с.: ил.
3.Лялякин В.П. Наноматериалы для продления послеремонтного ресурса тракторных трансмиссий и экономии топлива / В. П. Лялякин. А. К. Ольховацкий, Д. А. Гительман. А. П. Шавкунов // Труды ГОСНИТИ. Т. 105. – М.: 2010 – с. 53-57
4.Черноиванов В. И. Перспективы применения нанотехнологий как прорывного фактора повышения качества обслуживания и ремонта машин // Сельскохозяйственная техника: обслуживание и ремонт. – 2011. - №2. – с. 7-8
5.Наноматериалы в техническом сервисе сельскохозяйственных машин: Учеб. пособие для вузов. / под ред. Черноиванова В.И. – М: ГОСНИТИ., 2010. – 67 с.
264

УДК 621.3
В.А. Улитин – студент ФГБОУ ВО Пермской ГСХА; С.М. Боровских – научный руководитель, ст. преподаватель, ФГБОУ ВО Пермской ГСХА, г. Пермь Россия
ВЫБОР ЭЛЕКТРОДВИГАТЕЛЯ ДЛЯ МЕХАНИЗМОВ С ПЕРЕМЕННОЙ НАГРУЗКОЙ
Аннотация. Правильность подбора электродвигателя, учитывающая специфику приводного механизма, условия работы и окружающей среды, определяет длительность безаварийной работы и надежность системы «двигатель – нагрузка». В данной статье рассмотрен выбор электродвигателя для механизмов с переменной нагрузкой, методом эквивалентных величин.
Ключевые слова: Кратковременная перегрузка, нагрев двигателя, допустимая мощность.
Введение. Нагрузка электродвигателя в процессе работы может изменяться различным образом. Рассмотрим выбор электродвигателя, работающего с переменной нагрузкой.
При выборе мощности электродвигателя для привода механизма с продолжительной переменной нагрузкой используют метод эквивалентных величин – тока, момента и мощности. Метод основан на предположении, что потери электродвигателя при его работе с продолжительной переменной нагрузкой равны потерям в этом двигателе при его работе с продолжительной постоянной нагрузкой, значение которой эквивалентно фактической переменной нагрузке.
При расчѐте эквивалентной величины какого-либо параметра электродвигателя необходимо располагать нагрузочной диаграммой электродвигателя. Такая диаграмма представляет собой зависимость потребляемого тока I, полезного момента M или полезной мощности P от времени t. Из нагрузочной диаграммы мощности P = f(t) следует (рис. 1), что в течение времени t1 электродвигатель потребляет мощность P1, в течение времени t2 – мощность P2, в течение времени t3 – мощность P3, а в течение времени t4 – мощность P4. Диаграммы электродвигателя по моменту и току имеют аналогичный вид.
Рис. 1. Нагрузочная диаграмма по мощности при продолжительной переменной нагрузке
265

Расчѐт эквивалентной мощности электродвигателя, работающего с продолжительной переменной нагрузкой, ведут по формуле:
√ |
|
(1) |
|
где P1, P2, …, Pn – значения полезной мощности электродвигателя в соответствующие периоды переменной нагрузки (t1, t2, …, tn).
Приведѐнная выше формула справедлива, если участки нагрузочной диаграммы представляют собой прямоугольники, как на рис. 1.
При выборе мощности электродвигателя следует эквивалентные значения величин сравнить с номинальными данными электродвигателя.
Необходимо, чтобы эквивалентная величина была немного меньше номинальной или равна ей.
Предварительно выбранный электродвигатель при работе в заданном режиме не будет перегреваться, если:
(2)
где Pнаиб – наибольшее значение мощности на нагрузочной диаграмме, Н·м; Pном – номинальная мощность выбранного электродвигателя, Н·м.
Для проверки по нагреву используют постоянную времени нагрева:
|
|
(3) |
|
|
|
где m – масса электродвигателя, кг; |
|
– установившееся превыше- |
ние температуры электродвигателя при номинальной нагрузке, ; - номинальные потери двигателя, идущие на нагрев, Вт.
Если постоянная времени нагрева укладывается в значение Т=22-28 мин, то электродвигатель подобран верно. Если значение постоянной времени нагрева меньше заданного, то двигатель нагревается быстрее положенного, что свидетельствует о недостаточной мощности электродвигателя. Если постоянная времени нагрева больше заданного, то двигатель имеет избыточную мощность. В обоих случаях следует подобрать электродвигатель с подходящими параметрами мощности или подходящим классом изоляции по нагревостойкости так, чтобы постоянная времени нагрева укладывалась в заданные параметры.
Выбор установочной мощности электродвигателя, прежде всего, сказывается на кпд электропривода – двигатель при работе с нагрузкой меньше номинальной имеет и меньше кпд и коэффициент мощности.
Коэффициент полезного действия электропривода определяется как отношение полезной механической энергии Амех и затраченной электрической Аэл:
(4)
Метод эквивалентных величин выбора мощности электродвигателя при продолжительной переменной нагрузке даѐт достаточно точные результаты лишь при условии, что изменение нагрузки влияет лишь на величину переменных потерь, а постоянные потери (магнитные и механические) остаются практически неизменными. Поэтому метод эквивалентных величин можно с успехом приме-
266
нять к электродвигателям, у которых изменение нагрузки не вызывает значительных изменений частоты вращения и основного магнитного потока. Это относится к асинхронным электродвигателям и электродвигателям постоянного тока с параллельным возбуждением, работающим в режиме естественной механической характеристики, т.е. без добавочного сопротивления в цепи ротора (якоря).
Нагрузочная диаграмма двигателя служит основой для проверки предварительно выбранного двигателя по перегрузочной способности и по нагреву.
Проверка по перегрузочной способности сводится к проверке выполнения условия:
(5)
где Pмакс – максимальная мощность из нагрузочной диаграммы двигателя; Pдоп – допустимая по перегрузке мощность двигателя.
Выводы. Рассмотрен выбор электродвигателя для механизмов с переменной нагрузкой методом эквивалентных величин по мощности и проверку выбора электродвигателя постоянной времени нагрева.
Литература
1.Назаров Г.И., Олейник Н.П. и др. электропривод и применение электрической энергии в сельском хозяйстве. – М.: Колос, 1972.
2.http://edu.dvgups.ru/METDOC/GDTRAN/DEPEN/ELMASH/ELEKTROP
3.http://studopedia.org/1-22594.html
4.http://electrono.ru/
УДК 631.362
А.Ф. Федосеев, Р.Г. Сединин, Р.Э. Калимуллин – аспиранты; Р.А. Кылосов – студент; В.Д. Галкин – научный руководитель, д-р техн. наук, профессор,
ФГБОУ ВО Пермская ГСХА, г. Пермь, Россия
ВЛИЯНИЕ ЧАСТОТЫ КОЛЕБАНИЯ ДЕКИ УСОВЕРШЕНСТВОВАННОЙ КОНСТРУКЦИИ НА ПОКАЗАТЕЛИ РАБОТЫ ВИБРОПНЕВМОСЕПАРАТОРА
Аннотация. В статье представлены закономерности изменения показателей работы вибропневмосепаратора от частоты колебания деки. Опытами установлено, что средние значения степени выделения овсюга при 500 об/мин изменяется: от 92… 98% ( для первой и второй фракций) до 55% (для третьей фракции), а среднее значение потерь семян пшеницы в отходы не превысило 6,4%.
Ключевые слова: семена, вибропневмосепаратор, степень выделения примесей, потери в отходы.
Цель исследований – выявить закономерности изменения основных показателей качества работы вибропневмосепаратора усовершенствованной конструкции в зависимости от частоты колебания деки.
Применение для посева высококачественных семян является одним из важнейших факторов увеличения урожайности зерновых культур. Важнейшей же
267

операцией в подготовке семян является их окончательная очистка, которая в настоящее время проводится на вибропневмосепараторах.
Опыты проведены на семенах пшеницы сорта Баженка урожая 2015г. при следующих условиях: средние значения массы 1000 зерен – 37 г, всхожести – 96%, энергии прорастания – 88%, влажности – 13,7%, объемной массы – 712 г/куб.дм, засоренности овсюгом – 120 шт./кг. Семена прошли предварительную очистку, сушку, очистку на двух воздушно-решетно-триерных машинах K531.
Опыты проведены на вибропневмосепараторе усовершенствованной конструкции кафедры сельскохозяйственных машин Пермской ГСХА [1]. Установка позволяла изменять частоту колебания деки в пределах от 460 до 540 мин -1. Продольный угол наклона деки составлял 6°, поперечный 0°. Скорость воздушного потока измеряли анемометром и поддерживали в пределах 1,5 – 1,6 м/с без слоя зерна.
Опыты проведены при среднем значении подачи 1000 кг/ч при частотах колебания 460, 480, 500, 520 и 540 мин-1.
1 – вентилятор, 2 – дека, 3 – приемники фракций, 4 – шатун, 5 – зона расслоения, 6 – зона транспортирования, 7,8 – стенки деки
Рис. 1. Технологическая схема вибропневмосепаратора
Отбор проб производили на установившемся режиме в течение 10 секунд в трехкратной повторности из четырех приемников фракций. Каждую фракцию взвешивали на весах с точностью до 1 грамма. Затем из каждой первых трех фракций отбирали средний образец для оценки на засоренность. После этого рассчитывали степень выделения примесей и потери семян в отходы.
Степень выделения примесей рассчитывали по формуле:
где – начальная засоренность, шт/кг;
– засоренность очищенных семян, шт/кг. Потери семян в отходы рассчитывали по формуле:
268

где – масса четвертой фракции без примесей;
–подача семян в машину, кг/ч.
Врезультате проведенных опытов получены графические зависимости
(рис.2).
Рис. 2. Потери семян в отходы и степень выделения примесей в зависимости от частоты колебания деки
Из графиков следует, что средние значения степени выделения примесей при 500 об/мин изменяется: от 92…98% ( для первой и второй фракций) до 55% (для третьей фракции), а среднее значение потерь семян в отходы не превысило 6,4%.
Литература 1. Галкин, В.Д. Вибропневмосепаратор семян с усовершенствованной декой. /В.Д. Галкин,
К.А. Грубов. //Тракторы и сельхозмашины. №4, 2011.-С.12-13.
УДК 631.3
А.Ф. Федосеев, Р.Г. Сединин – аспиранты; П.С. Серебренников –магистрант; Р.А. Кылосов, Е.В. Мазеина – студенты; В.Д. Галкин – научный руководитель, д-р техн. наук, профессор,
ФГБОУ ВО Пермская ГСХА, г. Пермь, Россия
УСОВЕРШЕНСТВОВАННАЯ ЛИНИЯ ПОДГОТОВКИ СЕМЯН
Аннотация. В статье приведена усовершенствованная линия подготовки семян, реализующая двухступенчатую предварительную очистку, двухэтапную технологию сушки и фракционную технологию очистки. Технико-экономическая
269
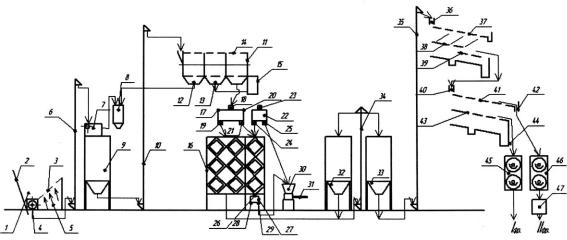
оценка линии показала, что при обработке около 5 тыс. т влажного зернового вороха, годовой экономический эффект составит не менее 1 млн. рублей за счет использования предложенных технологических операций.
Ключевые слова: зерно, технология, очистка, сушка, техникоэкономическая оценка.
Целью работы является разработка технологической схемы линии подготовки семян.
Анализ известных поточных линий для подготовки семян из влажного комбайнового вороха, показал, что они имеют высокие затраты на сушку зернового вороха и низкий выход семян с требуемыми показателями качества при их очистке от трудноотделимых примесей [1]. В этой связи разработка усовершенствованных линий, позволяющих снизить затраты и потери семян в отходы, является важной и актуальной задачей.
В основу линии положены разработки кафедры сельскохозяйственных машин Пермской ГСХА и ООО «Техноград» Пермского края [2, 3].
Устройство линии подготовки семян показано на рисунке 1.
Рис.1 Схема технологическая усовершенствованной линии подготовки семян: 1,2,3,4,5 – приемник зернового вороха и его элементы; 6,10,34,35 – нории, машина предварительной очистки; 8 – бункер неиспользуемых отходов; 9 – бункер временного хранения влажного зерна; 11,12,13,14,15 – зерносепарирующая приставка и ее элементы; 16 – зерносушилка; 17,18,19,20,21,22,23,24,2526,27,28,29 –
распредельтели зерновых потоков; 30 – приемный бункер; 31 – экструдер; 32,33 – бункеры; 36,37,38,39,40,41,42,43,44 – воздушно-решетная машина и ее элементы; 45,46 – триеры; 47 – вибропневмосепаратор
Линия работает следующим образом. Зерно поступает от комбайнов в приѐмник - 1, из которого норией - 6 оно направляется в зерноочистительную машину - 7 предварительной очистки. Из бункера зерно, очищенное от лѐгких, крупных и мелких сорных примесей подаѐтся в норию -10, которая направляет его в зерносепарирующую приставку – 11. На первой секции приставки отделяются оставшиеся мелкие сорные примеси, которые направляются в бункер – 8. На вто-
270