
книги / Надежность и диагностика технологических систем
..pdf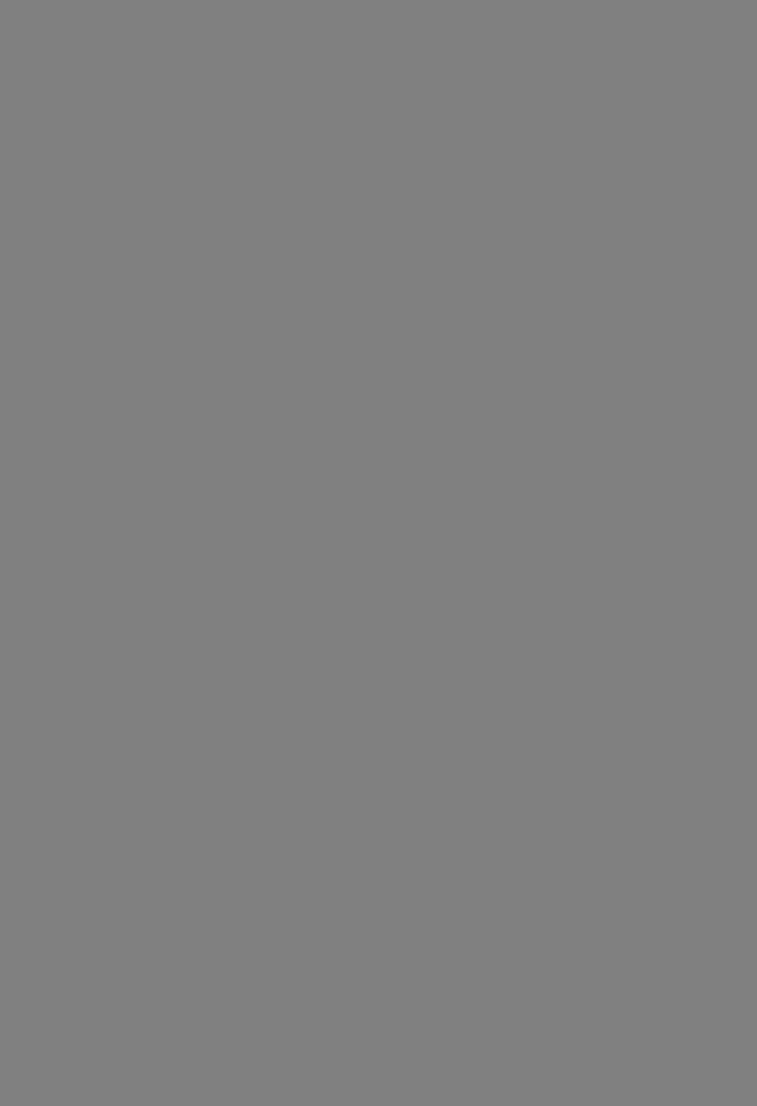
222 |
6. Надежность, производительность и эффективность ТС |
Для точного расчета *шх при изготовлении партии деталей надо пусконаладочное время £пн делить на количество деталей п в партии:
|
*шт = “ П — + £3аг + *х +(*р + *ф+ *р) + *х +*раз* |
(6 .6 ) |
т» |
(*п +*н) |
|
Величину — — — называют подготовительно-заключительным
п
временем.
Из рис. 6.2 и формулы (6.5) видно, что только одна из десяти составляющих времени обработки является производительной — это время формообразования *ф (при этом £ф < fp ). Практически все составляющие времени обработки в конечном счете являются производными от надежности, влияют на производительность и эффективность ТС.
В за и м о с в я зь н а д е ж н о с ти и п р о и з в о д и те л ь н о с ти т е х н о л о г и ч е с к и х
6.2. с и с те м м е т а л л о о б р а б о т к и
Зависимость состояния оборудования технологических систем от уровня надежности. В теории производительности, как уже говорилось, производительным считается только время формо образования. Остальное время относят к различного вида потерям, величина которых определяется общим уровнем надежности ТС и организации процесса изготовления деталей в целом (рис. 6.3). Любая эксплуатируемая ТС металлообработки может находиться
вдвух состояниях:
•бесперебойной работы, когда выдается годная продукция —
период Х ф раб;
• когда по различным причинам не выдается годная продук ция; этот период равен суммарной длительности всех видов про стоев Х Ф пр*
Таким образом, общий фонд времени механической обработ ки заготовок
1 Ф о б щ “ Х Ф раб^’ ^ Ф п р * |
(6.7) |
Период
работы
£Фраб
Время
формо
образо
вания
Полезное
время
Общий фонд времени механической обработки на станках с ЧП УХФ общ
Время холо стых ходов tx
Время вспомо гательное #в
Время
движения
инструмента на рабочей подаче t'p и t ” без резания
Время
работы
станка
Собственные простои ЕФсоб
из-за отказов элементов ТС
Отказы обо рудования
Отказы оснаст ки, приспособ лений
Отказы
инструмента
Остановы станка для контроля, введения коррекции
Период простоев £Ф пр
Организацион но-технические простои £Ф.орг
Несвоевремен ные включение
ивыключение станка, приход
иуход рабочего
Пусконаладоч ные работы на станке
Отсутствие
заготовок,
инструмента,
электроэнер гии, УП
Осмотр и уборка
О б щ и е п о т е р и в р е м е н и
Простои из-за переналадки
ЕФпер
Смена
оснастки
Смена
инструмента
Смена и отладка УП
Рис. 6.3. Виды затрат времени у автоматизированных технологических систем металлообработки
производительности и надежности Взаимосвязь .2.6
NJ
М
OJ
224 |
6. Надежность, производительность и эффективность ТС |
Период работы £ Ф раб включает четыре вида составляющих времени:
•время процесса формообразования *ф, т.е. время снятия стружки — «полезное время»;
•время холостых ходов fx (подвод и отвод режущего инстру мента) — «потерянное время»;
•время выполнения вспомогательных операций tB(установ ка заготовки в приспособление, зажим-разжим заготовки, сня тие заготовки) — «потерянное время»;
•время движения инструмента на рабочей подаче fp до и по сле процесса формообразования — «потерянное время».
Общий период простоев £ Ф пр можно разделить на три вида:
• собственные простои (время 2 Ф СОб);
• |
организационно-технические |
простои (время £ Ф орг); |
• |
простои из-за переналадки (£ |
Ф пер). |
К собственным простоям ]ГФсоб относятся:
•простои оборудования (отказы, поломки, разрегулирование механизмов, устранение неисправностей, настройка механизмов);
•простои из-за оснастки (потеря точности, поломка деталей, неисправности гидропневмосистемы, снижение усилий зажима
уприспособлений ниже допустимых, вибрации);
•простои из-за инструмента (поломка, сколы, повышенный износ, затупление, потеря точности, вибрации, смена, регули ровка, подналадка);
•простои из-за брака (время, когда производится бракован ная продукция, считается простоем). Брак — первый признак (индикатор) и следствие низкой надежности ТС. Собственные простои обусловлены общим уровнем надежности всех элемен тов ТС.
Простои по организационно-техническим причинам ЕФорг не связаны непосредственно с состоянием и уровнем надежности оборудования ТС. Они определяются в основном «человеческим фактором»: несвоевременный приход или уход рабочего; несвое временный пуск или останов станка; отсутствие электроэнергии, заготовок, инструмента или УП; неправильные действия рабо тающих; уборка, осмотр, регламентные функции.
К простоям из-за переналадки оборудования £Ф пер на обра ботку деталей другого типоразмера относятся: замена и наладка приспособлений, комплекта нового инструмента; подготовка УП и обработка пробных деталей; корректировка УП.
6.2. Взаимосвязь надежности и производительности |
225 |
Суммарное время простоев |
|
£ Ф пр = ХФооб + ХФорг + Х ф пер- |
(6 .8 ) |
Вобщем фонде времени простоев ]ГФпр собственные простои
£Ф соб являются превалирующими и обусловлены общим техни ческим уровнем оборудования ТС и уровнем его надежности.
Анализ надежности автоматизированного оборудования ГПС. Как показывает опыт эксплуатации автоматизированных ТС, простои оборудования связаны главным образом с отказами эле ментов электроники систем ЧПУ, элементов электроавтоматики
имеханических узлов.
Основные причины отказов пневматических роботов: некаче ственная регулировка и сборка; попадание посторонних предме тов в механизмы поворота; потеря точности позиционирования в результате износа зубчатых передач; износ уплотнений в пнев моцилиндрах.
Основные причины и виды отказов автоматизированного обо рудования:
1) отказы системы электроники: пробои изоляции; отказы ин терфейса; отказы элементной базы; нарушение регулировок;
2) отказы системы электроавтоматики: нарушение регулиро вок; обрыв проводов; пробой изоляции; нарушение или залипание контактов; короткое замыкание; нарушение контакта щеток элек тродвигателей; отказ блоков питания и датчиков; сгорание, обрыв или межвитковое замыкание обмоток электродвигателей;
3) отказы элементов механической части ТС: срезание или поломка фиксаторов; поломка или предельный износ режущего инструмента; нарушение регулировок и повышенный люфт в при водах; заклинивание подшипников; перегрев гидросистемы, за едание золотников и приводных шестерен; износ (или поломка) упоров, сухарей, кулачков; заклинивание или задиры в направ ляющих; обрыв трубопроводов или их засорение; нарушение уплотнений.
Основные элементы и блоки электроавтоматики, механиче ской части ТС и электронной системы можно диагностировать с целью предотвращения, обнаружения и быстрого устранения отказов.
226 |
6. Надежность, производительность и эффективность ТС |
Производительность и надежность ТС можно оценить по об щему коэффициенту эффективного использования Кэ#и оборудо вания:
(6.9)
где Т0— общий фонд времени работы оборудования за рассмат риваемый период; Тпр — общее время простоев. При высоком уровне надежности показатель Кэ и стремится к единице:
(6.10)
Разработка и оснащение оборудования ГПС системами диаг ностики позволяет не только резко сократить время простоев оборудования Тпр из-за отказов, но и значительно снизить их количество, увеличить наработку на отказ всех видов оборудо вания ГПС.
Параметры и показатели, характеризующие качество обра ботки, надежность и производительность технологических си стем. Технологический процесс на концептуальном уровне сле дует рассматривать как совокупность пяти взаимодействующих информационных потоков (или видов связей): размерных, вре менных, управляющей информации, свойств материалов, эко номических.
Технологический процесс металлообработки и виды связей можно интерпретировать графически с помощью кругов Вена и теории множеств (рис. 6.4). Множество — это совокупность каких-либо элементов. Каждый из пяти видов связи — это мно жество Мi с параметрами:
где Мр — множество, характеризующее размерные связи и содер жащее погрешности обработки Alf Д2, ..., Дл; Мв — множество,
6.2. Взаимосвязь надежности и производительности |
227 |
Рис. 6.4. Параметры, формирующие качество обработки, надежность и производительность технологических систем:
М* — обобщенное множество параметров; Alt ..., Ап — погрешности; |Мпер|— мощность пересечения
характеризующее временные связи и содержащее параметры fH,
*п» *заг> *х» *Р>^раз» *ц* *шт — соответственно время наладки инст румента, пуска ТС, загрузки заготовки, холостых ходов, рабо чих ходов, разгрузки детали, автоматического цикла, штучное; Му.„ — множество, характеризующее элементы и виды управляю щей информации (УП — управляющая программа, L — траек тория режущего инструмента, G — подготовительные команды, М — вспомогательные команды, Э — команды электроавтома тики); Мс<м — множество, характеризующее свойства материа лов, используемых в процессе обработки (СМ!, СМ2, ...» СМП— свойства материала заготовки, режущего инструмента и др.); Мэ — множество, характеризующее экономические связи (Соп, Сшт, Q — себестоимость операции, себестоимость штучная, про изводительность). Совокупность (объединение) множеств Мр, М„, Му.и, Мс.м, Мэ образуют обобщенное множество М*.
Параметры множеств Мр, Ма, Мэ широко используются в мате матических моделях при решении и формализации задач техно
228 6. Надежность, производительность и эффективность ТС
логии, теории производительности, надежности, оценки эффек тивности.
Погрешности обработки (множество Мр) формируются в тече ние всего периода t^ . Однако непосредственно на детали действие погрешностей проявляется реально (физически) только в пери од *р(точнее *ф). Поэтому в период £ф есть пересечение элементов множеств Мр и Мв, т.е. |Мпер Ф0| — «непустое множество».
Из всего баланса времени обработки £шт = производитель ным является только время формообразования £ф (см. рис. 6.2). Качество обработки, уровень надежности, производительность и эффективность — это «конечный продукт», результат дейст вия всех рассмотренных выше факторов и элементов множеств пяти видов связей.
Для оценки производительности ТС (и отдельных машин) ис пользуют ряд специальных критериев (показателей, коэффициен тов). Математическую основу теории производительности состав ляют уравнения, связывающие показатели производительности с технологическими, стоимостными и другими показателями оборудования.
Время — основная категория, через которую выражаются большинство показателей производственной деятельности. При оценке эффективности оборудования можно использовать четыре вида производительности (технологическую, цикловую, техни ческую, фактическую), коэффициенты и показатели производи тельности.
Технологическая производительность:
(6. 11)
откуда ip = 1/К.
Этот вид производительности характеризует максимально дос тижимую («идеальную», теоретическую) производительность.
Цикловая производительность: |
1 |
1 |
|
|
(6.12) |
где Т — время цикла.
Техническая производительность:
1
6.2. Взаимосвязь надежности и производительности |
229 |
Фактическая производительность:
ф пр =
_ ___________________ 1___________________
(6.14)
+ *х) + *в] + ( Х Ф соб+ Х ф орг + Е Ф пер)
Это реальная производительность с учетом всех видов потерь. Все формулы справедливы для случая, когда за рабочий цикл выдается одно изделие.
Между технологической К и цикловой Qn производительно
стью существует связь (при fB= 0): |
|
|
|||
|
1 |
1 |
к |
_ к 1 |
= Кт|. (6.15) |
|
*р+*х |
l/K+tx |
1+Kxix |
1+К£х |
|
|
|
||||
Величина |
1 |
= т\называется коэффициентом производи |
|||
|
1+ К*х тельности. Она характеризует степень непрерывности протекания
ТП. Например, величина Т|= 0,7 означает, что в рабочем цикле 70 % составляют рабочие ходы, а остальные 30 % — холостые, следовательно, возможности ТС используются только на 70 % .
Коэффициент использования Т|исп численно равен доле време ни работы машины Фр в общем плановом фонде времени Фпл:
_ Ф Р ^ |
ф Р |
1 |
1 |
(6.16) |
|
Фпл |
Ф р + 1 Ф п р |
1 + 1 Ф п р /Ф р |
l + 2rfB |
||
|
Показатель
ХФпр
фр
есть величина внецикловых потерь Фпр, приходящихся на еди ницу бесперебойной работы Фр = Z •Т = Z(tp + tx + tB), откуда
Z = Фр/7\ (6.17)
Показатель Х*пот — величина внецикловых простоев (потерь), приходящихся на единицу продукции:
Е < п о т = ^ £ = |
^ % |
= ^ !!Е?’ = Е -вг. |
(6.18) |
Z |
Фр/-* |
Фр |
|
где Z — количество деталей; Т — время цикла.
230 6. Надежность, производительность и эффективность ТС
Коэффициент технического использования Т|тех численно ра вен доле времени работы машины при условии обеспечения ее всем необходимым (т.е. в периоды, исключающие организаци онные простои £ Ф орг).
Коэффициент загрузки Т|загпоказывает, какую долю времени машина обеспечена всем необходимым для бесперебойной работы. Так, значения цтех= 0,7 и = 0,8 означают, что в общем времени машина обеспечена всем необходимым для бесперебойной работы (заготовками, инструментом, электроэнергией) только на 80 % и в этот период машина работает только 70 % (остальное время она простаивает по техническим причинам — из-за отказов обо рудования, смены инструментов, наладки и др.).
Между коэффициентом использования Т)нсп и коэффициента
ми Лтех и Лзаг существует взаимосвязь: |
|
|
|
Лисп = Лтех 'Лзаг* |
(6.19) |
Например, при |
= 0,7 и Т|заг = 0,8 |
коэффициент использо |
вания |
|
|
Лисп = Л«Х Лзаг = 0,7 0,8 = 0,56.
Все виды производительности (К, Q4, Ятех* <?ф) связаны меж ду собой через безразмерные коэффициенты Т|, Лисп» Лтех» Лзаг:
K = l/tp;
Яц =К-Л;
Qrex = 0ц 'Лтех = (К *Л)’Лтех»
Оф = (?’Лисп = (К * Л)(Лтех*Лзаг) = Фц 'Лтех’Лзаг» К >Яц >Qrex >Яф*
Оценить влияние внецикловых простоев на производитель ность можно при помощи рассмотренных выше показателей т\, Лтех» Лисп» Х*п и £В. Численные значения показателей и видов производительности зависят в конечном счете от общего уровня надежности всех элементов ТС.
Влияние надежности технологических систем на производи тельность в условиях серийного производства. Для количествен ной оценки производительности Я необходимо общее количество деталей Z разделить на период их изготовления (общий фонд времени Фобщ):
Я — Z / Ф оьщ . |
(6.20) |