
книги / Сварка в машиностроении. Т. 3
.pdfПри сборке ферм стремятся обеспечить правильное центрирование стержней в узлах. При малом числе одинаковых изделий в серии используют простейшие приспособления и метод копирования. При достаточно большом числе выпускае мых ферм одного типоразмера экономически целесообразно использовать более сложную и производительную оснастку. Схема приспособления с двумя стендами
1 и 3 и кантующей рамкой 2 приведена на рис. 21. Сборку осуществляют на стенде /. Элементы фермы расклады вают по упорам и фиксаторам, одно временно зажимают включением пневмоприжимов и жестко соединяют швами, оказавшимися в нижнем по-
Рис. 20. Соединение концов труб |
Рис. |
21. Схема приспособления |
||
в |
пространственный |
узел ванной |
для |
сборки ферм |
сваркой |
|
|
|
|
ложеиии. С помощью рамки 2 собранную |
ферму сначала ставят в вертикаль |
|||
ное |
положение, а затем |
передают на стенд 3, причем в каждом из этих поло |
жений выполняют соответствующие швы. Сборку следующей фермы на стенде 1 производят одновременно со сваркой на позициях 2 и 3.
Использованию механизированных поточных методов при изготовлении ферм препятствует не только разнообразие типоразмеров и ограниченное число изделий в серии, но и малая технологичность типовых конструктивных решений. Однако
Рис. 22. Типовая стропильная ферма
эти препятствия преодолимы [16], что можно видеть на примере типовой стропиль ной фермы (рис. 22), разработанной в ЦНИИСКе. Предусмотрены четыре типорс .мера фермы под разную нагрузку, отличающиеся сечением используемых профилей, тогда как размеры / = 12 м и h — 1,5 м остаются неизменными. Верх ний пояс 1 состоит из двух горячекатаных швеллеров, нижние пояса 2 и раскосы 3 — из одиночных гнутых швеллеров. Короткие отрезки таких швеллеров исполь зованы как диафрагмы верхнего пояса 4\ нижний узел объединен косынками 5. Рациональная схема фермы из ограниченного числа элементов позволяет механи зировать сборку и выполнять соединения контактной точечной сваркой непосред ственно в сборочном кондукторе без кантовки фермы, Компоновки из таких ферм
позволяют перекрывать пролеты длиной более |
12 м, что расширяет потребность |
в таких фермах до сотен тысяч в год, обеспечивая эффективность их крупносе- |
|
рийного производства в автоматизированной |
поточной линий. |
В условиях завода арматуру железобетона (сетки, плоские и пространстве^-' ные каркасы) обычно сваривают контактной сваркой в поточных и ароматиче ских линиях. В элементах сборного железобетона жилых зданий предусматривают закладные детали, располагаемые в местах примыкания одного элемента к дру гому. При монтаже эти закладные детали сваривают дуговой сваркой. В про мышленных и энергетических сооружениях из сборного железобетона стыковку элементов осуществляют сваркой арматурных стержней, выступающих из каждого сборного элемента. Сварка может производиться при горизонтальном и вертикаль ном положении стержней или под углом друг к другу. В этом случае, а также и при монтаже каркасов монолитного железобетона применяют электродуговую, ванную или электрошлаковую сварку.
НЕГАБАРИТНЫЕ ЕМКОСТИ И СООРУЖЕНИЯ
При изготовлении емкостей и сооружений больших размеров из листового проката целесообразно возможно больший объем работ выполнять в условиях завода-изготовителя. Для этого каждую конструкцию расчленяют так, чтобы от правочные элем?}п;ц имели возможно большие размеры, но в пределах габарита железнодорожного подвижного состава. Для листовых полотнищ толщиной до 16 ~ lj?JrtM стремление увеличить размеры отправочных элементов привело к раз
работке |
метода рулонирования, получившего |
в нашей стране весьма широкое |
||||||
применение. Крупные узлы конструк |
|
|
|
|
||||
ции в виде полотнищ большого размера |
|
|
|
|
||||
собирают, сваривают |
и |
сворачивают |
|
|
|
|
||
в рулон на специальных установках. |
|
|
|
|
||||
Схема такой установки показана на |
|
|
|
|
||||
рис. 23. |
Необходимость сварки с двух |
|
|
|
|
|||
сторон |
предопределяет |
наличие двух |
|
|
|
|
||
ярусов 1 и 2, а также поворотного кру |
|
|
|
|
||||
жала 3 для передачи полотнища с |
|
|
|
|
||||
одного |
яруса |
на другой |
с поворотом |
Рис. |
23. |
Схема установки для |
сборки |
|
на 180°. Перемещение полотнища и его |
и сварки |
полотнищ |
|
|||||
сворачивание |
обеспечивается рабочим |
|
|
|
|
|||
кружалом 4. |
На двух ярусах 1 и 2 |
|
сварки с одной стороны, |
сварки |
||||
расположены |
четыре рабочих участка: сборки, |
с другой стороны, контроля и исправления дефектов. Сворачивание рулона производят периодически после завершения работ на каждом из участков. При этом полотнище наворачивают на вспомогательный элемент, закрепляемый в ра бочих кружалах. Размеры свариваемого и сворачиваемого в рулон полотнища определяют из условия рационального членения конструкции цилиндрического резервуара в зависимости от размеров емкости с тем, чтобы масса рулона не превышала 40—65 т.
Боковые стенки листовых конструкций башенного типа также выполняют из нескольких полотнищ, каждое из которых имеет длину, равную периметру бо ковой стенки.
Расположение листов в полотнище, их толщина и типы соединений опреде ляются как конструктивными, так и технологическими соображениями. Листы толщиной более 7—8 мм собирают и сваривают встык, а более тонкие — внахле стку.
Для сварки встык кромки листов подвергают механической обработке паке том. Сварку под флюсом осуществляют сварочными тракторами. Первый слой стыковых соединений выполняют на флюсо-медной подкладке либо на весу. Сварка стыковых швов с противоположной стороны на другом ярусе стенда обеспечивает
надежное проплавление всей толщины листа. На последнем рабочем участке двухъярусного стенда предусмотрен контроль внешним осмотром и испытание на плотность вакуум-аппаратом. Обнаруженные дефекты уточняют просвечиванием и исправляют.
Усовершенствованная двухъярусная установка обеспечивает комплексную механизацию процесса изготовления полотнищ. Все соединения сваривают встык. Их расположение и последовательность сварки показаны на рис. 24. Включе нием сворачивающего механизма кромку ранее собранной части полотнища уста навливают над медной подкладкой устройства 4 для сварки поперечного шва (рис. 25) и прижимают к ней рычажными пневмоприжимами. Листы из всех кон тейнеров 1 с помощью вакуумных захватов за один ход кран-балки 2 подают на место 3 сборки. Сборку осуществляют два боковых 6 и один задний 7 толкатели, сдвигающие листы до упора друг в друга и в кромку ранее собранного полотнища. После зажатия второй кромки поперечного стыка его сваривают автоматом под
Секция Ш |
СекцияП |
Секция! |
|
|
|
|
|
:Ш,И< |
: |
( |
|
|
|
Стш |
Рис. 24. Расположение соеди |
||
|
|
|
|
||
|
|
|
|
|
нений и последовательность |
|
|
|
|
|
сварки на двухъярусной уста |
|
|
|
|
|
новке |
|
3000 |
3000 |
|
|
|
6000 |
601W . * |
60LЮ |
|
6000 |
|
mm* Ранее сваренные стыки ш Свариваемые стыки
флюсом. За время сборки и сварки поперечного стыка на рабочем месте 5 свари вают все продольные швы. Для этого катучую балку, несущую направляющие двух сварочных головок и зажимные устройства, последовательно устанавливают над каждой парой продольных швов, прижимают кромки к медной подкладке и осу ществляют сварку. На нижнем ярусе стенда предусмотрены рабочие места 8 и 9 соответственно для сварки поперечного и продольного швов с другой стороны.
При монтаже вертикальных цилиндрических резервуаров рулон элементов днища укладывают на основание и раскатывают в последовательности, определяе мой расположением элементов в рулоне. Элементы днища соединяют сварочным трактором под флюсом с одной стороны. Рулон боковой стенки резервуара ставят
ввертикальное положение и по мере разворота его нижнюю кромку прихватывают
кднищу. Верхнюю кромку развернутой части боковой стенки закрепляют уста новкой элементов щитовой кровли или закрепляют расчалками.
При монтаже цилиндрических сооружений башенного типа из-за наличия кольцевых стыков между монтажными блоками требования к точности изготовле
ния полотнищ и к приемам разворачивания рулонов оказываются более высокими. После заварки замыкающего продольного шва на уровне земли монтажный блок поднимают краном и устанавливают в проектное положение. Сварку кольцевого шва осуществляют с двух сторон: с наружной стороны обечайки— покрытыми электродами вручную, а внутри обечайки — полуавтоматами в углекислом газе.
Для цилиндрических резервуаров вместимостью более 50 тыс. м3 метод рулонирования пока использовать не удается из-за значительной толщины листов нижних поясов. Применение высокопрочных сталей или конструктивных нов шеств, возможно, позволит применить метод рулонирования и для более крупных цилиндрических резервуаров. За рубежом цилиндрические резервуары (вмести мостью 200 тыс. м3) сооружают полистовым методом [5]. Листы толщиной до 40 мм
очищают от окалины, обрезают кромки автоматической кислородной резкой, вальцуют, окрашивают и маркируют. Листы толщиной до 14 мм имеют V -образ- ную разделку кромок, при большей толщине Х-образную. Большинство швов днища выполняют сваркой под флюсом, горизонтальных швов боковой стенки — также под флюсом с флюсоудерживающим устройством или в С02; вертикальные швы боковой стенки преимущественно сваривают с принудительным формирова нием шва дуговой сваркой под флюсом или в СОа.
В нашей стране сооружают сферические резервуары вместимостью 600 и 2000 м3 на внутреннее давление до 18 кгс/см2. Тип раскроя оболочек приведен
Рис. 25. Схема усовершенствованной двухъярусной установки
в табл. 1. Сферическую поверхность листовым заготовкам при толщине до 36 мм придают горячей штамповкой (типы раскроя а и в), при толщине до 28 мм — валь цовкой на специальных гибочных вальцах со сферическими валками (раскрой б). В последнем случае плоскую заготовку предварительно сваривают из листов, вы резают газовой резкой по копиру и затем вальцуют.
При раскрое типа а укрупнение блоков и их сварку под флюсом выполняют на шарнирно-качающихся стендах. Блоки собирают в полусферу на стенде (рис. 26), подварку швов под последующую автоматическую сварку осуществляют вручную. После завершения сборки нижнюю полусферу кантуют и устанавливают на временную опору. На этом же стенде собирают верхнюю полусферу, затем под нимают ее и монтируют на нижнюю. Сборка заканчивается ручной подваркой замыкающего шва.
При раскрое типа б лепестки также предварительно укрупняют в блоки, при чем для сферы вместимостью 2000 м3 каждый меридиональный лепесток собирают
8 И/p . Винокурова В. А., т. 3
из двух заводских элементов (большого и малого). Для этого типа раскроя получил применение «вертикальный» способ сборки сферы. На временной опоре 1 (рис. 27) устанавливают нижнее днище 2, к нему крепят трубчатую монтажную стойку 3
Рис. 26. Схема сборки полу сферы на стенде
с верхним днищем 4 и монтажной люлькой 5. Блоки 6 с распорками жесткости 7 поднимают в вертикальное положение и крепят с помощью сборочных планок и клиньев к днищам и друг к другу, а также временными прихватками к опорам 8, устанавливаемым на фундаменте. Затем блоки соединяют прихваточным швом,
|
а перед установкой последнего блока уда |
|||||||||||
|
ляют трубы жесткости, монтажную стойку |
|||||||||||
|
и люльку. |
|
|
|
|
|
|
|
|
|||
|
Сварку сферических резервуаров вме |
|||||||||||
|
стимостью |
600— 2000 м3 |
выполняют |
ав |
||||||||
|
томатом под флюсом с двух сторон при |
|||||||||||
|
вращении сферы |
на специальном |
манипу |
|||||||||
|
ляторе, |
домкратное |
устройство |
которого |
||||||||
|
приподнимает сферу над опорами после |
|||||||||||
|
удаления временных прихваток. При тол |
|||||||||||
|
щине |
элементов |
16 мм |
разделку |
кромок |
|||||||
|
не осуществляют. При толщине 25 мм |
ис |
||||||||||
|
пользуют V -образную разделку при тол |
|||||||||||
|
щине |
34 |
мм — Х-образную. |
Последова |
||||||||
|
тельность |
выполнения |
швов |
следующая. |
||||||||
|
Сначала выполняют меридиональные швы |
|||||||||||
|
со стороны разделки кромок в несколь |
|||||||||||
|
ко слоев. |
С другой |
(внутренней) сторо |
|||||||||
|
ны подварку корня |
шва |
производят без |
|||||||||
|
вырубки его за счет глубокого проплав |
|||||||||||
|
ления. Затем сваривают широтные и по |
|||||||||||
Рис. 27. Схема сборки сферического |
люсные |
соединения. |
При |
выполнении |
||||||||
сборочных и сварочных работ над резер |
||||||||||||
резервуара |
||||||||||||
вуаром |
целесообразно |
устраивать общее |
||||||||||
|
светопрозрачное |
пленочное |
покрытие. |
В этом случае условия работы лучше, чем под открытым небом, и облегчается сварка в среде защитного газа. За рубежом при сооружении резервуаров больших размеров монтаж осуществляют методом укрупнительной сборки лепестков за водского изготовления в блоки на монтажной площадке и их автоматической сварки под слоем флюса или в среде защитного газа, В проектное положение блоки монтируют последовательным наращиванием, швы между блоками выпол-
няют в основном ручной сваркой покрытыми электродами или автоматами для сварки во всех пространственных положениях проволокой диаметром 1— 1,2 мм в смеси аргон — углекислый газ со свободным формированием шва. Очередность установки блоков при монтаже сферы определяется расположением опор. При раскрое типа в монтаж можно начинать с экваториального пояса. К укрупненным блокам лепестков этого пояса приваривают опорные стойки и, устанавливая их на фундамент, монтируют весь экваториальный пояс. Затем на временный поста мент укладывают нижнее днище и монтируют блоки нижнего пояса. После уста новки временной стойки монтируют верхнее днище и верхний пояс.
При сооружении кожухов домен (толщина листов 40—60 мм) листы, прошед шие заготовительные операции, перед отправкой с завода попарно укрупняют сваркой под флюсом по длинной кромке. При этом в зависимости от мощности ги бочного оборудования завода-изготовителя длинную кромку листа располагают вдоль образующей либо в окружном направлении. Расположение вдоль образую-
Рис. 28. Схема раскроя монтажного блока кожуха домны. Условные обозначения:
-------------- электрошлаковая сварка на монтаже; сварка под ф лю сом :----------- на монтаже; — X — X — X — на заводе
щей является предпочтительным, так как в этом случае (рис. 28, а) все швы мон тажного блока прямолинейны, однотипны и удобны для сборки и электрошлаковой сварки. При расположении длинной кромки листа в окружном направлении (рис. 28, б) сборке монтажного блока с выполнением вертикальных швов электрошлаковой сваркой предшествует укрупнение заводских элементов сваркой под флюсом на качающемся стенде.
Спиральные камеры крупных гидротурбин сложны в изготовлении из-за больших габаритов и высоких требований к точности при значительной толщине листовых элементов. Для наиболее напряженных звеньев спиральной камеры Красноярской ГЭС использовали высокопрочную сталь СК-2 (ап,2 > 50 кге/мм2), менее напряженные звенья изготовляли из сталей 10ХСНД и МСтЗ [10]. Разметку элементов осуществляли с помощью шаблонов, изготовленных по размерам, опре деленным на плазе. После газопламенной резки с одновременным скосом под сварку заготовки подвергали гибке на прессе с помощью универсального гибоч ного штампа. Для предотвращения изменения формы при сварке элементов
взвенья устанавливали временные элементы жесткости. Подгонку звеньев друг
кдругу осуществляли при контрольной сборке.
Порядок монтажной сборки можно проследить на рис. 29. После установки и раскрепления статора турбины устанавливали секции 18 и 2, а также отража тельный лист 19. Затем к каждой из этих секций последовательно подгоняли смежные прилегающие секции. Замыкающим элементом сборки являлась секция 12, изготовленная с некоторым припуском для подгонки. Подтягивание сопряга емых кромок производили с помощью болтовых стяжек и конусных оправок. Регулировку положения каждой секции и всей спиральной камеры по высоте осуществляли домкратами, а форму трубы исправляли растяжками. Для того чтобы меньше применять потолочную сварку, разделку швов в верхней части спирали делали с наружной стороны, а в нижней части — с внутренней. Боковые
части спирали имели Х-образную разделку. Сварку выполняли покрытыми электродами, причем для соединения монтажных элементов из высокопрочной стали применяли электроды аустенитного класса. В первую очередь в каждой
------------
» ■ ■
Заводская сварка Сварка на монтаже
Рис. 29. Схема монтажа спиральной камеры гидротурбины 1—19 — монтажные элементы
секции заваривали продольные швы, затем приваривали звенья к статору, а после этого сваривали кольцевые стыки. Сварку продольных и кольцевых швов спирали выполняли способом последовательного обратноступенчатого исполнения швов иди способом наварки слоев горкой.
СОСУДЫ, РАБОТАЮЩИЕ ПОД ДАВЛЕНИЕМ
Сосудам в большинстве случаев придают цилиндрическую форму, реже форму сферы или тора. Продольные, кольцевые и круговые швы, как правило, выполняют встык. Применительно к технологии изготовления можно выделить следующие четыре группы сосудов: тонкостенные, со стенкой средней толщины, толстостенные и многослойные.
Продольные прямолинейные стыки тонкостенных обечаек собирают в зажим ных приспособлениях клавишного типа. Плотное прижатие кромок к подкладке обеспечивает качественное выполнение односторонней сварки в этом же приспо соблении без прихватки.
При выполнении кольцевых стыков тонкостенных сосудов из материалов, малочувствительных к концентрации напряжений, используют остающиеся под кладные кольца. Подкладные кольца облегчают центровку кромок и их односто роннюю сварку, однако для некоторых высокопрочных материалов они оказы ваются неприемлемыми. В этом случае кольцевые стыки обычно собирают и сва ривают на съемных подкладках разжимных колец. Возможна также сборка с охва том зоны кольцевого стыка жестким бандажом снаружи при расположении сварочной головки внутри обечайки.
Элементы арматуры (фланцы, штуцеры) обычно вваривают в стенки сосудов встык. Для материалов, малочувствительных к концентрации напряжений, иногда допускают приварку таких элементов угловыми швами или рельефной сваркой.
В крупносерийном производстве тонкостенных сосудов (тормозные резер вуары, пропановые баллоны) для выполнения сборочно-сварочных операций нашли применение специальные полуавтоматические установки.
Сосуды со стенками из листов средней толщины (до 40 мм) из низкоуглеро дистых и низколегированных сталей изготовляют преимущественно с помощью автоматической сварки под флюсом. Сосуды, работающие в агрессивных средах, изготовляют из хромоникелевых и хромистых сталей, цветных металлов и их спла вов автоматической сваркой под флюсом и по слою флюса полуоткрытой дугой (алюминиевые сплавы), а также аргонодуговой сваркой. Для экономии дорогосто ящих и дефицитных материалов применяют двухслойные листы. При выполнении сварных соединений таких листов несмешиваемость обоих материалов обеспечи вают использованием для каждого из слоев различных присадочных материалов и приемов сварки.
Цилиндрические сосуды обычно собирают из нескольких обечаек и двух полусферических или эллиптических днищ. Обечайки вальцуют из одиночного листа или из сварной карты при расположении швов вдоль образующей. Днища либо сваривают из отдельных штампованных лепестков, либо штампуют целиком из листа или из сварной заготовки. Продольный стык обечайки собирают на при хватках с помощью стяжных приспособлений. Для сборки кольцевых стыков между обечайками используют специальные устройства. Продольные и кольцевые швы сосудов со средней толщиной стенки выполняют, как правило, с двух сторон. При этом первым укладывают шов изнутри обечайки на флюсовой подушке, а вто рым — шов снаружи по ранее уложенному первому с полным проплавлением всей толщины стенки. При толщине стенки сосуда более 25 мм сварку под флюсом не редко выполняют в несколько слоев. При сборке обечаек с днищами целесообразно использовать центрирующие устройства. Сварку этих кольцевых стыков выпол няют так же, как и стыков между обечайками.
При серийном производстве сосудов используют поточные методы произ водства. Примером может служить изготовление котлов железнодорожных цис терн на Ждановском заводе тяжелого машиностроения [9]. Цилиндрическую часть котла составляют из нескольких листов длиной 9280 мм. На сборочном стенде листы собирают встык на прихватках с постановкой входных и заходных планок. Собранное полотнище приподнимают системой роликов, передают на стенд для сварки, собранными стыками укладывают на флюсовые подушки и сварку всех швов полотнища выполняют одновременно, Затем полотнище передают в канто
ватель, переворачивают и на второй сварочной установке также одновременно сваривают все стыки с другой стороны. Далее полотнище рольгангом подают в 10-метровые гибочные вальцы, где его вальцуют вдоль швов в обечайку. После сборки и двусторонней сварки продольного стыка обечайку подвергают калиб ровке в гибочных вальцах, затем устанавливают на роликовый конвейер, связы
вающий несколько рабочих мест, где вырезают отверстия для горловины и сливного прибора, собирают обечайку с днищами и т. д.
При изготовлении тол стостенных сосудов (толщи ной св. 60 мм) широко ис пользуют электрошлаковую сварку, обеспечивающую надежное проплавление всего сечения за один проход. Про дольные швы толстостенных обечаек, как правило, вы полняют электрошлаковой
сваркой. В зависимости от размеров сосуда и имеющегося в наличии гибочного оборудования листовую заготовку гнут в нагретом состоянии вдоль длинной или вдоль короткой кромки листа. В первом случае уменьшается число более трудоемких кольцевых швов в сосуде, а во втором — менее трудоемких про дольных. Схемы сборки обечаек с одним и двумя продольными стыками приве дены на рис. 30, а и б соответственно. Зазор фиксируется приваркой скоб. Если обечайку после выполнения продольных швов необходимо править, ее нагре вают до 1000— 1050° С, а охлаждение на воздухе при калибровке используют одновременно для нормализации.
Кольцевые швы выполняют много слойными сваркой под флюсом или электрошлаковой сваркой в один про ход. Полное проплавление при много слойной сварке обеспечивают укладкой в разделку нескольких подварочных слоев с внешней стороны (рис. 31), зачисткой корня шва с помощью пнев матического зубила или резака и на ложением внутреннего подварочного шва. После этого производят много слойное заполнение места внешней разделки.
Сборка кольцевого стыка под электрошлаковую сварку должна быть достаточно точной, так как местная деплаиация криволинейных кромок
стыка свыше Змм может привести к нарушению уплотнения и вытеканию шлако вой ванны. Поэтому сборке предшествует обработка внешней и внутренней поверх ности обечаек на участке шириной 70— 100 мм от торца. Сбирают стык с помощью планок, которые устанавливаются на ребро поперек кольцевого стыка и привари вают к поверхности обечаек. Иногда скобы временного крепления дополнительно устанавливают внутри обечаек. При электрошлаковой сварке кольцевых стыков особое внимание уделяют заварке замка. Усадочную раковину либо выводят в специальный прилив в наружном ползуне или в медный кокиль, либо выплавляют и заваривают вручную. При выполнении продольных и кольцевых швов толсто стенных сосудов начинают использовать способ вертикальной газоэлектрической
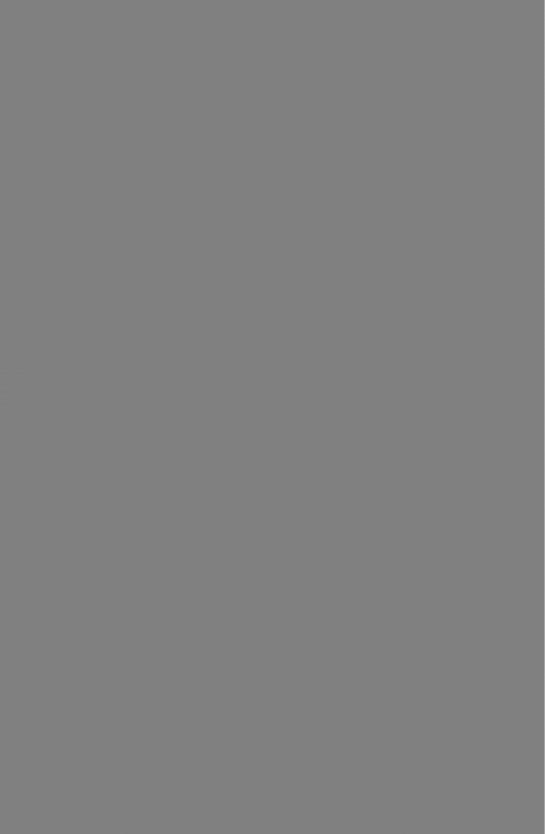