
книги / Технологические процессы и технические средства для глубинно-насосной эксплуатации нефтяных скважин
..pdfПо результатам выполненных исследований образцов из стали 20Н2М установлено следующее:
–закономерной связи между величиной остаточной пластической деформации и величиной остаточных макронапряжений не обнаружено;
–установлена тенденция, заключающаяся в изменении величины остаточных макронапряжений от пластической деформации образца как для штанг из стали 20Н2М, так и из 15Х2НМФ.
Реализация данного способа была осуществлена в НГДУ «Кунгурнефть» ПО «Пермнефть» с использованием устройства для правки насосных штанг из никелесодержащих сталей, например 20Н2М, 15ХНМФ, растяжением и технических средств для магнитоиндукционного контроля протяженных изделий [8, 5]. За счет использования данных технических решений, реализующих способ холодной правки
иконтроля штанг растяжением за период 1992–1994 гг. была снижена обрывность вдвое по фонду скважин, оборудованных штангами, бывшими в эксплуатации после холодной правки, контроля растяжением
имагнитоиндукионного неразрушающего контроля. При этом снижение обрывности было достигнуто за счет: устранения кривизны длинномерных изделий, например насосной штанги; изменения по величине
изнаку остаточных макронапряжений по внешней поверхности штанги; перемещения остаточных макронапряжений. Данное положение установлено при многократном пластическом деформировании образцов.
Устройство, реализующее способ холодной правки, относится к обработке металлов давлением, в частности к оборудованию для правки растяжением длинномерных изделий, насосных штанг, и может быть использовано в металлургической, машиностроительной отраслях промышленности и на предприятиях нефтяной промышленности, ведущихремонт и контрольнефтепромыслового оборудования [8].
Холодная правка, например насосной штанги, достигается за счет того, что устройство для правки изделий растяжением (содержащее установленные на основании подвижную и неподвижную каретки с захватами для концов изделия, связанный с источником питания основной гидроцилиндр, шток которого жестко соединен с подвижной
71
кареткой, и блок управления, включающий закрепленную на основании неподвижную часть со шкалой и размещенную на подвижной каретке подвижную часть с пластиной, периодически взаимодействующей со шкалой, и возвратной пружиной) снабжено двумя дополнительными гидроцилиндрами, закрепленными на основании параллельно основному гидроцилиндру и связанными с источником питания. При этом подвижная часть блока управления выполнена в виде расположенных на подвижной каретке и последовательно шарнирносвязанных между собой толкателя, подпружиненного в направлении неподвижной каретки, промежуточного звена, двуплечего рычага, упора, установленного с возможностью перемещения по пластине, и закрепленного на последней датчика, электрически связанного с источником питания и периодически контактирующего с упором, а штоки дополнительных гидроцилиндров расположены с возможностью периодического взаимодействия с подвижной кареткой и толкателем.
На рис. 1.26 схематично представлен общий вид устройства для правки (вид сверху); на рис. 1.27 – разрез А-А рис. 1.26 (исходное положение элементов датчика контроля величины удлинения изделия); на рис. 1.28 – разрез А-А рис. 1.26 (положение элементов датчика контроля величины удлинения изделия в начале ее пластического удлинения).
Устройство для правки изделий растяжением (см. рис. 1.26–1.28), например насосных штанг, содержит основание 1, нагружающее приспособление, включающее жестко установленные на основании 1 три гидроцилиндра – первый дополнительный 2, основной 3 и второй дополнительный 4, неподвижную 5 и подвижную 6 каретки с захватами 7 и 8 для высаженных концов насосной штанги 9 и датчик 10 контроля величины удлинения насосной штанги.
Шток 11 основного гидроцилиндра 3 жестко связан с подвижной кареткой 6, штоки 12 и 13 гидроцилиндров 2 и 4 соответственно имеют возможность поступательного движения до контакта штока 12 с толкателем 14 датчика 10 контроля величины удлинения насосной штанги и последующего контакта этих штоков 12 и 13 с подвижной кареткой 6. Датчик 10 контроля величины удлинения насосной штанги
72
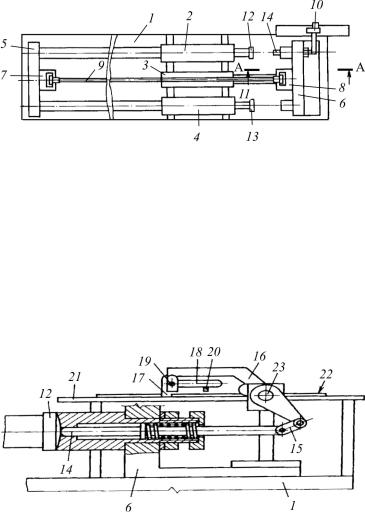
Рис. 1.26. Общий вид устройства для правки изделий растяжением: 1 – основание устройства; 2 – первый (дополнительный) гидроцилиндр; 3 – основной гидроцилиндр для предварительной правки насосной штанги; 4 – второй (дополнительный) гидроцилиндр; 5 – неподвижная каретка устройства; 6 – подвижная каретка устройства; 7, 8 – захваты
для высаженных концов насосной штанги; 9 – штанга насосная (длинномерное изделие); 10 – датчик контроля величины удлинения насосной штанги (изделия); 11 – шток основного гидроцилиндра; 12 – шток гидроцилиндра; 13 – шток гидроцилиндра; 14 – толкатель датчика контроля величины удлинения насосной штанги (изделия)
Рис. 1.27. Разрез А-А рис. 1.26 (при исходном положении элементов датчиков контроля величины удлинения изделия): 15 – промежуточное звено; 16 – двуплечий рычаг; 17 – пластина; 18 – продольный паз пластины 17; 19 – упор в виде стержня; 20 – исполнительный элемент; 21 – опорная площадка; 22 – шкала для определения длины насосной
штанги; 23 – ось рычага 16
73
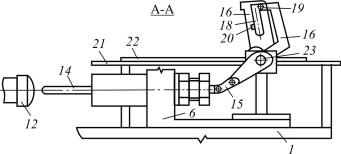
Рис. 1.28. Разрез А-А рис. 1.26 (при положении элементов датчиков контроля величины удлинения изделий в начале ее пластического удлинения)
включает подпружиненный толкатель 14, промежуточное звено 15, двуплечий рычаг 16, пластину 17 с продольным пазом 18, упор 19, выполненный в виде стержня, и исполнительный элемент 20. Исполнительный элемент 20 установлен на пластине 17. Толкатель 14 установлен на подвижной каретке 6 и связан посредством промежуточного звена 15 и двуплечего рычага 16 с упором 19. Упор 19 связан с двуплечим рычагом 16 и установлен в продольном пазу 18 пластины 17 так, что имеет возможность перемещаться при движении подвижной каретки 6 вдоль паза 18 до контакта с исполнительным элементом 20. При этом пластина 17 установлена с возможностью углового перемещения до соприкосновения с жестко связанной с основанием 1 устройства опорной площадной 21, на которой закреплена шкала 22, предназначенная для определения длины насосной штанги при достижении величины эксплуатационного нагружения в скважине.
Схема работы устройства
Штангу насосную 9, поднятую на поверхность из скважины при ремонтных работах и предназначенную для правки, укладывают в захваты 7 и 8 устройства. Включают главный электродвигатель привода гидростанции (не показано), обеспечивая тем самым подачу масла в основной гидроцилиндр 3. Шток основного гидроцилиндра 3 и жестко связанная с ним каретка 6 с захватами 8 начинают движе-
74
ние. При достижении нагружения насосной штангой 9 величины, соответствующей эксплуатационному нагружению штанги в скважине, происходит упругая деформация насосной штанги, в результате которой осуществляется ее предварительная правка. После этого через определенное время осуществляется подача масла в дополнительные гидроцилиндры 2 и 4, и штоки 12 и 13 этих гидроцилиндров начинают поступательное движение. Шток 12 входит в контакт с подпружиненным толкателем 14 датчика 10, конструкция которого представлена на рис. 1.26 и 1.27, в результате чего происходит поворот рычага 16 относительно оси 23 и упор 19 датчика 10 начинает перемещаться по дуге окружности. Вместе с ним совершает угловое перемещение пластина 17 датчика 10. В момент, когда упор 19 достигает своего минимального расстояния до горизонтальной опорной площадки 21, пластина 17 выходит из связи с упором 19 и боковой поверхностью ложится на опорную площадку 21. По положению пластины 17 на опорной площадке 21 устанавливают начало отсчета величины удлинения данной штанги при пластической деформации. Также по положению пластины 17 на опорной площадке 21 и с помощью шкалы 22 определяют длину насосной штанги при ее эксплуатационном нагружении. По величине длины насосной штанги при эксплуатационной нагрузке, по типоразмеру и техническим характеристикам насосной штанги определяется величина требуемого пластического удлинения этой штанги, тем самым определяется положение исполнительного элемента 20 на пластине 17 датчика 10. Поскольку подвижная каретка 6 под действием штоков 12 и 13 продолжает свое поступательное движение, то вместе с кареткой 6 через подпружиненный толкатель 14 промежуточное звено 15 двуплечий рычаг 16 упор 19 начинает перемещаться в продольном пазу 18 пластины 17 датчика 10 контроля величины удлинения насосной штанги, которая к этому моменту лежит на опорной площадке 21 до контакта с исполнительным элементом 20. Исполнительный элемент 20 формирует сигнал на прекращение подачи масла в гидроцилиндры 2, 3 и 4 и возвращение их штоков 11, 12 и 13 в исходное положение,
75
тем самым прекращается пластическое удлинение насосной штанги в процессе правки. При снятии нагрузки толкатель 14 под действием пружины возвращается в исходное положение. В исходное положение возвращаются двуплечий рычаг 16, упор 19 и пластина 17. Насосная штанга 9, прошедшая правку, из захватов 7 и 8 подается на позицию консервации и упаковки. В захваты 7 и 8 устройства укладывается новая штанга, и процесс правки повторяется.
Таким образом, устройство позволяет в результате холодной правки изделий растяжением вернуть в производство до 15 % годового объема поднятых на поверхность при ремонтных работах насосных штанг, которые ранее списывались как непригодные для повторного использования.
1.8. Исследованиевозможностиупрочнениядлинномерных цилиндрических изделийдействиемпродольной растягивающейнагрузкиикручения
Из технологических методов, повышающих эксплуатационную надежность изделий, наиболее применима поверхностная пластическая деформация (ППД), а именно – обкатка роликами, дробеструйная обработка поверхности, пластическая деформация изделия под действием продольной растягивающей нагрузки, одновременном воздействии продольной растягивающей нагрузки и кручения [38, 39, 40].
В результате ППД существенно повышается сопротивление усталости изделий, уменьшается отрицательное воздействие различных поверхностных концентраторов напряжений, причем применяемые методы ППД не используют весь резерв прочности материала изделия. Благодаря работам, выполненным научными коллективами под руководством В.Д. Садовского, М.Л. Бернштейна, Д.А. Прокошкина, А.Г. Рахштадта, А.П. Гуляева, К.Ф. Стародубова, В.С. Ивановой, Л.И. Тушинского, О.Н. Романова и других, предложены комплексные методы температурно-силового воздействия на металл – термомеханическая (ТМО), механико-термическая (МТО) обработки, ба-
76
зирующиеся на создании в металле оптимального для эксплуатации характера структуры и свойств [41, 42, 43]. В сталях после термомеханической и механико-термической обработки повышаются характеристики вязкости разрушения, сопротивление усталостному разрушению, сопротивление контактному разрушению и износу, временное сопротивлениеи предел текучести при статических нагрузках.
Впервые предложенный исследуемый процесс упрочнения при нормальной температуре длинномерных цилиндрических изделий, осуществляемый действием продольной растягивающей нагрузки и кручения, касающийся способов упрочнения насосных штанг, как новых, в процессе их изготовления, так и бывших в эксплуатации, используемых в механизированной глубинно-насосной нефтедобычи, также может быть использован в машиностроении для упрочнения валов, стержней и других длинномерных цилиндричесикх изделий при их изготовлении либо перед их повторным ис-
пользованием [42, 43, 44, 45, 46].
Целью проведенных исследований является обеспечение качества упрочнения длинномерного изделия за счет повышения его усталостной прочности путем установления оптимальных режимов технологического процесса при пластическом деформировании изделия под действием продольной растягивающей нагрузки и кручения
[44, 45, 46, 47, 48].
Поставленная цель достигается тем, что в способе упрочнения длинномерных цилиндрических изделий, включающем упругую и пластическую деформацию продольным нагружением и контроль величины удлинения изделия, существенным является то, что после пластической деформации длинномерного изделия продольным нагружением производят деформацию изделия кручением, при этом продольное нагружение изделия ведут со скоростью в диапазоне 0,12–12,0 мм/с до величины удлинения, в 0,5–9,0 раза превышающего удлинение, соответствующее пределу пропорциональности для новых изделий, или до величины удлинения, в 1,5–5,0 раза превышающего удлинение, соответствующее пределу пропорциональности для изделий, бывших в эксплуатации. После этого фиксируют вели-
77
чину продольного нагружающего усилия и величину пластического удлинения и через паузу продолжительностью в пределах 0,25–60,0 с осуществляют деформацию изделия кручением со скоростью в диапазоне 0,002–1,8 об/с с одновременным контролем величины продольного нагружающего усилия, при уменьшении которого относительно зафиксированной величины в 1,25–4,0 раза заканчивают деформацию кручением и через паузу продолжительностью 0,25–30,0 с производят полное разгружение изделия от действия продольной растягивающей нагрузки со скоростью в пределах диапазона 0,12–14,0 мм/с и через паузу продолжительностью 0,25–30,0 с снимают полностью крутящий момент со скоростью в пределах диапазона 0,01–1,8 об/с.
Поскольку продольное нагружение ведут со скоростью в диапазоне 0,12–12,0 мм/с, создается возможность плавного нагружения изделия (а не интенсивное пластическое деформирование), обеспечивающего постоянное приращение продольной нагрузки, позволяющей изменить величину межатомных расстояний в кристаллической решетке металла в пределах всего объема изделия и при достижении напряжения в теле изделия выше предела пропорциональности обеспечить пластическую деформацию в кристаллах металла путем плавного скольжения частей кристалла относительно друг друга.
Вследствие плавного скольжения происходит взаимный сдвиг частей кристалла по определенным кристаллографическим плоскостям и направлениям, образующим системы скольжения, причем взаимный сдвиг зависит от величины приращения продольной нагрузки в единицу времени и направления приложения продольной растягивающей нагрузки.
Нагружение изделия с предложенной скоростью позволяет вести продольное нагружение изделия в области пластической деформации до величины удлинения, в 0,5–9,0 раза превышающего удлинение, соответствующее пределу пропорциональности для новых изделий, или до величины удлинения, в 0,1–5,0 раза превышающего удлинение, соответствующее пределу пропорциональности для изделий, бывших в эксплуатации. Таким образом достигается упрочнение длинномерного изделия и исключается возможность превысить пре-
78
дел прочности материала изделия. При таком нагружении в указанных пределах обеспечивается взаимный сдвиг частей кристаллов, охватывающий весь объем изделия без образования преимущественной ориентировки кристаллов в объеме изделия, что позволяет повысить усталостную прочность материала изделия. На этой стадии снимаются остаточные напряжения, которые, возможно, имели место в теле штанги до начала упругой и пластической деформации под действием продольной растягивающей нагрузки.
Исходя из того, что при достижении указанной величины деформации изделия величину продольного нагружающего усилия и величину пластического удлинения изделия фиксируют, представляется возможным наложить на фиксированную упругопластическую деформацию изделия деформацию кручением и тем самым дополнительно повыситьусталостную прочностьизделия.
Наличие перед проведением операции кручения паузы продолжительностью 0,25–60,0 с при фиксированной величине продольного нагружающего усилия и фиксированной величине пластического удлинения обеспечивает условия для завершения процесса скольжения частей кристаллов по кристаллографическим плоскостям и, как следствие, для завершения пластической деформации изделия. Это объясняется тем, что разные зерна в структуре металла или разные системы скольжения в зернах по мере увеличения напряжения в них включаются в процесс скольжения последовательно по мере достижения в них критического напряжения сдвига.
Исходя из того, что пластически деформированное длинномерное изделие продольным нагружением подвергают дополнительно деформации кручением, обеспечивается дальнейший процесс упрочнения изделия. В результате деформации кручением каждое элементарное поперечное сечение изделия сдвигается, вращаясь относительно смежных сечений. Действие крутящего момента приводит к увеличению межатомных расстояний кристаллической решетки металла изделия, и при достижении приложенного напряжения, вызванного действием крутящего момента, выше напряжения, соответствующего пределу пропорциональности материала, происходит взаимный сдвиг
79
частей кристалла по кристаллографическим плоскостям в направлении действия крутящего момента. Деформация кручением приводит к образованию неоднородных по сечению касательных напряжений, при этом нормальные напряжения в сечении изделия уменьшаются, перераспределяясь в эпюру куполообразной формы с максимумом в центре тяжести сечения изделия. Присутствие при этом сжимающих напряжений приводит кувеличению усталостной прочности материала изделия.
Поскольку деформацию кручением ведут с постоянной скоростью из предложенного диапазона 0,002–1,8 об/с, появилась возможность изменить величину межатомных расстояний в кристаллической решетке металла в приповерхностном тонком слое металла без нарушения этих связей по всей длине длинномерного изделия.
Поскольку при деформации изделия кручением с фиксированной упругопластической деформацией происходит уменьшение напряжений в сечении изделия, уменьшается и величина деформации продольным нагружением. В результате в приповерхностном слое изделия образуются остаточные сжимающие напряжения, а в центральной части изделия – остаточные растягивающие напряжения. Остаточные сжимающие напряжения в приповерхностных слоях также приводят к повышению усталостной прочности материала изделия. Деформацию изделия кручением заканчивают при уменьшении величины продольного нагружающего усилия в процессе кручения в 1,25–4,0 раза. Установленные пределы позволяют осуществлять технологический процесс упрочнения длинномерных изделий без их разрушения для широкого диапазона марок сталей, имеющих многообразие механических свойств, например сталей 40, 30ХМА, 20Н2М, 15Н3МА, 15Х2НМФ, 15Х2ГМФ, 14Х3ГМЮ производства
СССР и СНГ, а также импортного производства.
Наличие паузы продолжительностью 0,25–30,0 с после прекращения деформации кручением обеспечивает дальнейшее последовательное скольжение частей кристаллов по кристаллографическим плоскостям, благодаря чему обеспечивается механизм однородной сдвиговой деформации в пределах длины изделия и поверхностном слое.
80