
книги / Технологические процессы и технические средства для глубинно-насосной эксплуатации нефтяных скважин
..pdf
была выявлена трещина у основания штанги, состоящая как бы из двух, суммарной протяженностью 8 мм. При достижении 6 309 800 циклов нагружения фрагмента штанги протяженность трещины увеличилась и составила 11 мм. Далее при достижении 7 032 600 циклов нагружения протяженностьтрещины, представленная на рис. 2.1, составила 16 мм.
Рис. 2.1. Фрагмент насосной штанги Очёрского машзавода (маркировка 19Н2А.28Н1) с поперечным дефектом, нарушающим ее сплошность, выявленным при проведении магнитолюминесцентного контроля
Таким образом, магнитолюминесцентный метод контроля насосной штанги в приложенном поле электромагнита позволяет эффективно диагностировать поверхностные дефекты типа микро-
имакротрещин.
2.2.Неразрушающий контроль состояния поверхности и подповерхностного слоя концевого участка штанги методом измерения шумов Баркгаузена при ее коррозионно-усталостном испытании
Для прогнозирования эксплуатационных возможностей насосных штанг, как новых, так и бывших в эксплуатации, методом измерения шумов Баркгаузена, обладающего высокой чувствительностью к структурным изменениям ферромагнитного материала, были проведены исследования фрагментов насосных штанг с маркировкой 19НЗА 001 и 19Н2А 28Н из стали 20Н2М производства Очёрского машинострои-
131
тельного завода без нагрузки и при циклическом нагружении в коррозионной среде.
Измерение шумов Баркгаузена было осуществлено анализатором напряжений и структуры металлов «Интромет» (разработанным Академией наук Белоруссии НПЦ ИПФ «Диагностика») с чувствительной головкой. Для обеспечения повторяемости получаемой информации был использован цилиндрический протяженный шаблон с четырьмя продольными прорезями со смещением на 90°. Перед проведением коррозионно-усталостных испытаний данных фрагментов штанг были проведены первичные исследования состояния поверхности и подповерхностного слоя, в основу которых был положен метод измерения шумов Баркгаузена.
Характер распределения шумов Баркгаузена вдоль фрагмента штанги с маркировкой 19НЗА001 в четырех продольных сечениях перед проведением коррозионно-усталостных испытаний представлен на рис. 2.2. В связи с этим можно сделать заключение о неоднородности структуры металла фрагмента и о наличии микронесплошностей как на поверхности, так и в подповерхностном слое. Данное положение было подтверждено результатами, полученными при проведении магнитолюминесцентного контроля фрагмента штанги с маркировкой 19Н3А001.
Для установления эксплуатационных возможностей материала насосной штанги в процессе коррозионно-усталостных испытаний ее фрагмента были выполнены измерения шумов Баркгаузена при следующих режимах:
–первый режим нагружения – симметричный;
–величина нагружения 12 кг/мм2;
–цикличность – от 0 до 3 362 000 раз;
–периодичность измерения шумов Баркгаузена – 20 тыс. циклов, 120 тыс. циклов, 600 тыс. циклов;
–второй режим нагружения фрагмента – симметричный;
–величина нагружения 16 кг/мм2;
–цикличность – от 3 362 000 до 5 943 700 раз;
132
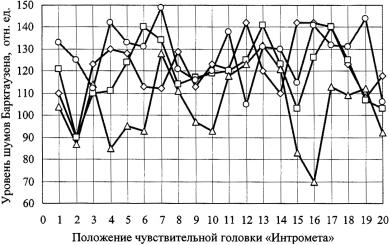
–периодичность измерения шумов Баркгаузена – 50 тыс. циклов, 150 тыс. циклов, 200 тыс. циклов;
–цикличность – от 5 943 700 до 7 234 700 раз.
Рис. 2.2. Характер распределения шумов Баркгаузена вдоль фрагмента насосной штанги Очёрского машзавода (маркировка 19Н3А001) до начала проведения коррозионно-усталостных испытаний:
– шум в пределе 1-го продольного сечения; – шум в пределе 2-го продольного сечения; U – шум в пределе 3-го продольного сечения; { – шум в пределе 4-го продольного сечения. Режим измерения шумов: направление перемагничивания – 90° к продольной оси штанги; частота перемагничивания fпер = 100 Гц; частота селекции fс = 20 кГц; ток перемагничивания Iпер = 100 мА
Характер распределения шумов Баркгаузена вдоль фрагмента штанги с маркировкой 19Н3А 001 в двух продольных сечениях под нагрузкой представлен на рис. 2.3 и 2.4.
При проведении коррозионно-усталостных испытаний фрагментов насосных штанг было установлено устойчивое, многократно повторяемое уменьшение амплитуды шумов Баркгаузена от 4 500 000 циклов и более, включая 7 234 700 циклов нагружения и далее до разрушения, подтвержденное графически на рис. 2.3 и 2.4.
133
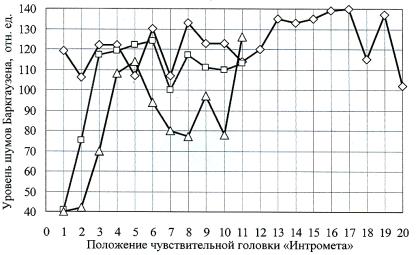
Рис. 2.3. Характер распределения шумов Баркгаузена вдоль фрагмента насосной штанги Очёрского машзавода (маркировка 19Н3А001)
при проведении коррозионно-усталостных испытаний:
– шум в пределе 1-го продольного сечения фрагмента при 3 363 000 циклах его нагружения; – шум в пределе 1-го продольного сечения фрагмента при 5 943 700 циклах его нагружения; U – шум в пределе 1-го продольного сечения фрагмента при 724 700 циклах его нагружения. Режим измерения шумов: направление перемагничивания – 90° к продольной оси штанги; частота перемагничивания fпер = 100 Гц; частота селекции fс = 20 кГц; ток перемагничивания Iпер = 100 мА
В процессе проведенных исследований установлено, что уменьшение амплитуды шумов Баркгаузена связано с разрушением кристаллической решетки материала штанги и зарождением микронесплошностей с наружной поверхности фрагмента, а также с появлением магистральной (магистральных) трещины. Данное положение подкреплено, например, характером распределения шумов Баркгаузена вдоль фрагмента насосной штанги Очёрского машзавода (маркировка 19Н2А 28Н) с магистральной трещиной, уровень шума от которой равен ~60 отн. ед. Данное распределение шумов представлено на рис. 2.5 и подтверждено наличием видимых микро- и макронесплошностей на внешней поверхностифрагментов, выявленных примагнитолюминесцентном контроле.
134
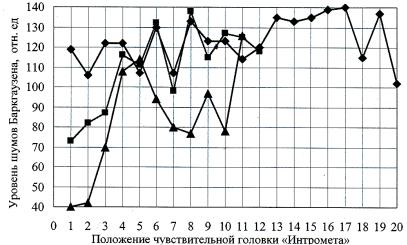
Рис. 2.4. Характер распределения шумов Баркгаузена вдоль фрагмента насосной штанги Очёрского машзавода (маркировка 19Н3А001) при проведении коррозионно-усталостных испытаний:
– шум в пределе 3-го продольного сечения фрагмента при 3 363 000 циклах его нагружения; – шум в пределе 3-го продольного сечения фрагмента при 5 943 700 циклах его нагружения; S – шум в пределе 3-го продольного сечения фрагмента при 724 700 циклах его нагружения. Режим измерения шумов: направление перемагничивания – 90° к продольной оси штанги; частота перемагничивания fпер = 100 Гц; частота селекции fс = 20 кГц; ток перемагничивания Iпер = 100 мА
Видимые макро- и микронесплошности на поверхности фрагментов, обнаруженные при альтернативном магнитолюминесцентном методе контроля, представлены на рис. 2.6.
Так, в зависимости от количества циклов нагружения фрагмента штанги протяженность макронесплошности 1 (см. рис. 2.6) изменялась следующим образом: протяженность 3 мм при 545900 циклах нагружения; протяженность 8 мм при 6 081 500 циклах нагружения; протяженность 14 мм при 6 309 800 циклах нагружения; протяженность 16 мм при 7 234 700 циклах нагружения. При этом процесс разрушения связей кристаллической решетки материала штанги, наличие микронесплошностей и их величина в поверхностном и под-
135

Рис. 2.5. Характер распределения шумов Баркгаузена вдоль фрагмента насосной штанги Очёрского машзавода (маркировка 19Н2А28Н) до начала проведения коррозионно-усталостных испытаний:
– шум в пределе 1-го продольного сечения; – шум в пределе 2-го продольного сечения; U – шум в пределе 3-го продольного сечения; { – шум в пределе 4-го продольного сечения. Режим измерения шумов – направление перемагничивания 90° к продольной оси штанги; частота перемагничивания fпер = 100 Гц; частота селекции fс = 20 кГц;
ток перемагничивания Iпер = 100 мА
Рис. 2.6. Общий вид фрагмента насосной штанги Очёрского машзавода (маркировка 19Н3А 001) с микронесплошностями при 7 234 700 циклах его нагружения: 1 – макронесплошность; 2, 3 – микронесплошности
136
поверхностном слое фрагмента были подтверждены альтернативными методами неразрушающего контроля, а именно – вихретоковым, люминесцентным, магнитолюминесцентным.
Полученные результаты измерения шумов Баркгаузена вдоль фрагмента штанги были продублированы исследованиями, полученными при использовании вихретокового модуляционного дефектоскопа 02.831 фирмы «Ферстер», обладающего максимальным коэффициентом подавлений мешающих факторов.
Выбор дублирующего вихретокового метода был обусловлен двумя обстоятельствами:
–высокая разрешающая способность метода к усталостным трещинам;
–отсутствие искажений с точки зрения остаточных магнитных полей и антикоррозионной обстановки.
Фрагмент насосной штанги был исследован вихретоковым методом при достижении: 4 355 400 циклов нагружения; 4 469 160 циклов нагружения; 5 449 000 циклов нагружения; 5 619 000 циклов нагружения; 5 893 700 циклов нагружения.
При этом сканирование внешней поверхности фрагмента штанги вихретоковым преобразователем было произведено по четырем продольным направлениям: I, II, III, IV. Во всех пяти вариантах вихретокового контроля в боковом сечении по направлениям II и IV выходной сигнал не превышал уровень тревоги. По направлениям I и III амплитуда выходного сигнала превышала пороговое значение, несущее признак дефектности. По направлению I были зарегистрированы сигналы от дефектов на расстоянии от опоры основного зажима 7–12 мм, 20–25 мм, а по линии III – на расстоянии 7–10 мм.
При втором контрольном варианте была сделана попытка оценки параметров трещин с помощью сравнительного определения параметров выходного сигнала от трещин на рабочем образце. Контроль проводился по следующим режимам: фаза – 275; усиление – 22; верхний
фильтр– 3; |
нижний фильтр – 2; частота – 1000 кГц; режим – сигнал |
в квадрате; |
уровень амплитудной селекции – 6; индикация – звуковая, |
световая; отношение параметров сигнала пооси хк осиу равно6.
137
Во втором контрольном варианте было подтверждено наличие трещин, обнаруженных в первом контрольном варианте, кроме того, выявлены дополнительные сигналы в первой и третьей линии. Амплитуда ряда сигналов в указанных зонах была сравнима с амплитудой сигналов от трещин рабочего образца. По линии III также были обнаружены дополнительные сигналы.
При третьем контрольном варианте было выявлено увеличение амплитуды выходного сигнала (приблизительно на 30–40 %) при сканировании по линии I в дефектных зонах. После выполнения контроля вихретоковым методом с шагом сканирования 2 мм представилось возможным оценить протяженность трещин соответственно 5, 7, 8 мм. Измерения по линии III не показали существенного увеличения амплитуды сигналов в ранее обнаруженных дефектных зонах.
Последующие 4-й и 5-й контрольные варианты не внесли изменения в результат текущих измерений. Возможно, это связано с искажением и разрушением кристаллической решетки материала фрагмента штанги при коррозионно-усталостных испытаниях и, как следствие, с появлением и развитием макро- и микронесплошности магистральной трещины.
Таким образом, применение вихретокового, магнитолюминесцентного методов контроля позволило оперативно выявить трещины, установить характер изменения эксплуатационных парамеров изделия на примере насосной штанги, прогнозируемые методом измерения шумов Баркгаузена.
2.3. Магнитоиндукционный контроль насосной штанги при напряжении в ее теле, превосходящем эксплуатационное
Магнитоиндукционный контроль относится к контролю протяженных ферромагнитных изделий неразрушающим методом, в частности к способам и устройствам дефектоскопии насосных штанг, используемых в механизированной нефтедобыче [58, 59, 5, 7, 10, 55, 61], и предназначен для повышения надежности контроля за счет распознавания дефектов несплошности и неоднородности
138
структуры материала. Реализуются технические решения следующим образом [5, 7, 10].
Насосную штангу укладывают на рольганги правочной машины, высаженную часть штанги закрепляют в захваты механизма перемещения насосной штанги и включают электродвигатели привода ведущих рольгангов и механизма равномерного перемещения насосной штанги. В результате насосная штанга, имеющая сложную криволинейную цилиндрическую форму, при прохождении через рольганги в процессе непрерывной объемно-контактной правки приобретает правильную цилиндрическую форму. После правки насосную штангу укладывают в захваты универсальной установки для дефектоскопии насосных штанг. Нагружают штангу до величины минимального нагружения ее в скважине (F = 1000 кГс) при помощи нагрузочного механизма. Продолжают нагружение предварительно растянутой штанги до величины максимального ее нагружения в скважине (F = 3000 кГс), т.е. до напряжения в ее теле, превосходящем эксплуатационное, и одновременно с началом изменения нагрузки начинают намагничивать насосную штангу.
Продольное намагничивание осуществляют путем перемещения на платформе расположенных коаксиально к штанге насосной двух катушек намагничивания от начала штанги до ее конца. Передвижение платформы осуществляют с помощью гибкой тяги, уложенной на барабан. Намагничивание производят постоянным магнитным полем катушек намагничивания до насыщения, при этом магнитное поле в теле штанги от каждой катушки намагничивания совпадает с направлением движения этих катушек. После достижения нагружения насосной штанги величины, соответствующей максимальному ее нагружению в скважине (F = 3000 кГс), т.е. до напряжения в ее теле, превосходящем эксплуатационное, снимают постепенно механическую нагрузку до величины, соответствующей минимальному нагружению штанги в скважине (F = 1000 кГс), при этом процесс перемещения катушек и, следовательно, процесс намагничивания штанги продолжают непрерывно до тех пор, пока платформа не займет конечного положения.
139
Одновременно с процессом намагничивания насосной штанги осуществляют измерение уровня сигнала магнитного поля рассеяния с помощью двух измерительных катушек, выход которых подключен на вход быстродействующего регистратора. Измерительные катушки перемещают вдоль штанги одновременно с катушками намагничивания при указанном нагружении, тем самым получают эксплуатационную дефектограмму насосной штанги с дефектами несплошности и/или неоднородности структуры.
Наличие дефекта типа несплошности в теле насосной штанги (например, усталостная трещина, расслоение металла и т.п.) приводит кперераспределению магнитного потока, пронизывающего насосную штангу в продольном направлении. Изменение длины силовой линии обусловлено геометрическими размерами дефекта, величиной раскрытия дефекта, площадью поперечного сечения и протяженностью дефекта. Поэтому при прохождении зоны дефекта несплошности катушками намагничивающей и измерительной систем с выхода измерительных катушек на вход быстродействующего регистратора поступает однополярный суммарный импульс электродвижущей силы (ЭДС).
Выделение дефектов неоднородности структуры основано на относительном сравнении непрерывно и локально изменяющихся магнитных проводимостей участков, расположенных в зоне первой и второй катушек намагничивания, так как магнитная проводимость участка зависит от объемного содержания феррита, перлита, сорбита, мартенсита в структуре изделия. В случае, если проводимости участков структуры, лежащих в зоне первой и второй катушек намагничивания, отличаются друг от друга, то на выходе измерительных катушек возникает ЭДС. Этот сигнал в процессе перемещения измерительных катушек вдоль штанги поступает на вход быстродействующего регистратора.
После снятия эксплуатационной дефектограммы насосную штангу разгружают и вновь нагружают до величины минимального нагружения штанги в скважине, после чего начинают ступенчатое нагружение штанги с последующим снятием нагрузки до величины минимального нагружения штанги в скважине.
140