
книги / Технологические процессы и технические средства для глубинно-насосной эксплуатации нефтяных скважин
..pdfТаблица 1 . 2 6
Перечень причин разрушения полых штанг насосных
вскважине № 742 Павловского месторождения нефти (19.07.2006 г., в составе оборудования ООРРНЭО)
Датавыхода колонныштанг |
Причиныразрушения |
|
|
насосныхизстроя, местопо- |
Примечание |
||
ложение зоныразрушения |
полых штангнасосных |
||
|
|||
иегохарактеристика |
|
|
|
26.12.2006 г. – |
Перегрузка5-йштангиподдей- |
Расчетным путемуста- |
|
5-яштанга(резьба) |
ствиемвесаколонныполых |
новлено, чтовеличина |
|
|
штангсдобываемойжидкостью, |
напряженияσрвзоне |
|
|
силвязкоготрения, силтрения |
разрушенияштангирав- |
|
|
междусоприкасающимисяпо- |
на128,7 МПа. Получен- |
|
|
верхностями, присутствием |
наявеличинаσр состав- |
|
|
динамическихсоставляющих |
ляет45 % отпредела |
|
|
приотборежидкостидвумя |
текучестиσт штангииз |
|
|
глубинныминасосами. Наработ- |
материаласталь45 |
|
|
канаотказсоставила1 449 360 |
|
|
|
качанийколонныштанг |
|
|
08.2008 г. – 77яштанга |
Циклическая деформация кон- |
Разрушениештангипро- |
|
(резьба). Втораяступень |
цевыхучастковполойштанги в |
изошлоподциклическим |
|
(ШНП32×6,5) |
интервале370–410 м. Надан- |
воздействиям изгибаю- |
|
|
номучасткевеличинарасхож- |
щихсилвинтервале |
|
|
дениямежду Аni+1 – Аni состави- |
370–410 мирастяги- |
|
|
лаот–1,25° до 3,25°. Наработка |
вающихнагрузок |
|
|
наотказсоставила4 594 032 |
|
|
|
качанийштанги |
|
|
29.07.2009 г. – 85яштанга. |
Циклическая деформация кон- |
Разрушениештангипро- |
|
Втораяступень |
цевыхучастковполойштанги в |
изошлоподциклическим |
|
(ШНП33×6,5) |
интервале380–459 м. Надан- |
воздействиемизгибаю- |
|
|
номучасткенаибольшаявели- |
щихсилвинтервале |
|
|
чинарасхождения между |
380–459 мирастяги- |
|
|
Аni+1 – Аni составила3,83°. |
вающихнагрузок |
|
|
Наработка наотказсоставила |
|
|
|
786 240 качанийколонныштанг |
|
121

1.10.4. Оценка коррозионной стойкости фрагментов полых штанг насосных при эксплуатации в нефтяных скважинах
ООО «ЛУКОЙЛ-Пермь»
Для полых штанг насосных после эксплуатации в скважине № 652 Баклановского и скважине № 742 Павловского месторождения нефти характерно поражение наружной поверхности по типу сплошной неравномерной коррозии.
Результаты определения глубины очагов коррозии, замеренные металлографическим методом по ГОСТ 9.502, расчетные величины скорости коррозионного поражения наружной поверхности штанг представлены в табл. 1.27.
Таблица 1 . 2 7
Максимальная глубина очагов коррозии, расчетные величины скорости коррозии
Месторождение, |
Глубина |
Длительность |
Рассчитанная |
Примеча- |
|
выдержки образца |
|||||
очагов |
скорость коррозии, |
||||
номер скважины |
коррозии, мм |
в скважинной |
мм/год |
ние |
|
|
|
среде, сут |
|
|
|
Баклановское, |
0,12 |
197 |
0,22 |
сталь 40Х |
|
скважина № 652 |
|||||
|
|
|
|
||
Павловское, |
|
|
не установлены, |
|
|
0,07 |
нет данных |
так как нет данных |
сталь 45 |
||
скважина № 742 |
|||||
|
|
о сроке эксплуатации |
|
||
|
|
|
|
Характеристика пластовых жидкостей в которых эксплуатировались полые штанги, представлены в табл. 1.28.
Исходя из данных, представленных в табл. 1.28, и согласно классификации РД 39-0147103-362–86 (« Руководство по применению антикоррозионных мероприятий при составлении проектов на обустройство нефтяных месторождений», ВНИИСПТНефть, 1986 г.) продукцию скважины № 652 Баклановского месторождения можно отнести к высококоррозионноактивной за счет высокой степени обводненности (90 %) и присутствия в больших количествах растворенного углекислого газа, агрессивный в коррозионном плане газ –
122
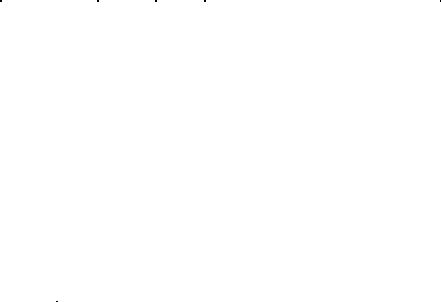
сероводород – в добываемой жидкости данной скважины отсутствует, а продукцию скважины №742 Павловского месторождения можно отнести кслабокоррозионноактивным.
|
|
|
|
|
Таблица 1 . 2 8 |
||
Характристика пластовых жидкостей, контактировавших |
|||||||
с полыми штангами в процессе эксплуатации |
|
||||||
|
|
|
|
|
|
|
|
|
Дебет |
% воды |
Физико-химичекские характеристики |
||||
Месторождение, |
|
пластовой воды |
|
||||
жидкости, |
в жидко- |
|
содержание |
|
углекис- |
||
номер скважины |
м3/cут |
сти |
рН |
солей, из них |
сероводо- |
лый газ, |
|
|
|
|
|
хлоридов, мг/л |
род, мг/л |
мг/л |
|
Баклановское, |
17,6 |
90,0 |
5,9 |
205/127 |
отс |
43,5 |
|
скважина № 652 |
|||||||
|
|
|
|
|
|
||
Павловское, |
17,6 |
48,00 |
6,3 |
73/43 |
отс |
23,9 |
|
скважина № 742 |
|||||||
|
|
|
|
|
|
Данные промысловых испытаний подтверждены результатами лабораторных исследований сталей и сплавов, которые представлены в табл. 1.29.
|
|
|
|
Таблица 1 . 2 9 |
|
Скорость общей коррозии различных сталей в модели |
|||
|
|
|
пластовой воды на ГОСТ 9.502 |
|
|
|
|
|
|
Марка |
|
Скорость коррозии, мм |
Группа коррозионной стойкости по ГОСТ 13819 |
|
стали |
|
Т = 20 ° С |
Т = 75 ° С |
|
|
|
|||
Ст. 45 |
|
0,32 |
1,49 |
Пониженно-стойкие к агрессивному воздействию |
Ст. 40Х |
|
0,22 |
1,17 |
Пониженно-стойкие к агрессивному воздейсвию |
Из исследований, представленных в табл. 1.29, следует, что сталь 45 и сталь 40Х относятся к группе пониженно-стойких к действию пластовых вод, содержащих сероводород и углекислый газ.
Для обеспечения временной противокоррозионной защиты штанг насосных при межоперационном хранении на открытом воздухе в условиях интенсивного атмосферного воздействия (дождь, снег, солнце, ветер, тепловое воздействие от +40 ° С до –36 ° С) использовано консервационное покрытие следующего состава [57]:
123
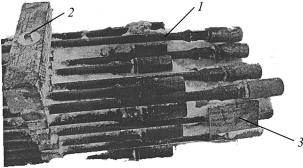
–лигносульфанат технический;
–индустриальное масло;
–асфальтосмолопарафиновые отложения (АСПО);
–амины первичные.
Использование в качестве основы данного состава АСПО позволяет получить на поверхности металла плотную беспористую пленку, снижающую воздействие агрессивных компонентов атмосферы до безопасного уровня;
–растворитель – индустриальное масло – обеспечивает эластичность покрытия тела штанги;
–покрытие, полученное из предлагаемого состава, является растворимым в нефти, исключая засорение погружных насосов и другого оборудования, работающего в скважине.
Внешний вид штанг в количестве 44 шт. в процессе хранения при наличии консервационного покрытия с 3 октября 2008 г. по 25 декабря 2008 г. на частично закрытой площадке (навес) и с 25 декабря 2008 г. по 21 января 2009 г. на открытой площадке ООО «Торговый дом ЛУКОЙЛ» (г. Чернушка) представлен на рис. 1.45.
Рис. 1.45. Внешний вид штанг насосных ШН22 (класс Д, номер сертификата ЦЗЛ 1155) при наличии консервационного покрытия тела, ниппеля, головки штанги (патент РФ № 2255102): 1 – штанга насосная ШН22 (концевой участок с муфтами); 2 – фрагмент упаковки; 3 – пластина с краткой характеристикой пакета штанг (ООО «ПермНИПИнефть», консервационный состав
по патенту РФ № 2255102)
124
Оценка надежности консервационного покрытия осуществлена
сиспользованием положений ГОСТ 9.011–78, ГОСТ 9.407–84 и стандарта API (спецификация 11В).
Исходя из результатов выполненных исследований и опытнопромышленной эксплуатации полых штанг конструкции ООО ПКТБ «Техпроект» и ЗАО «Элкамнефтемаш», установлено следующее:
–использование гладких НКТ по ГОСТ 633–80 с условным диаметром 42 мм в качестве полых штанг насосных в составе колонны штанг длинной 1224 м нецелесообразно;
–минимальная наработка на отказ гладкой НКТ по ГОСТ 633–80
сусловным диаметром 42 мм в качестве полой штанги составила 20736 качаний колонны штанг;
–исходя из экономической целесообразности технических решений для подъема вязкой или высоковязкой жидкости с учетом осложнений, необходимо предусмотреть нагрев глубинно-насосного оборудования и добываемой жидкости или подачу ингибитора в рабочую полость НКТ и/или полой штанги, предупреждающего АСПО на поверхности глубинно-насосного оборудования;
–минимальное сечение рабочего канала полой штанги не менее 260 мм2, при шероховатости поверхности рабочего канала штанги после прокатки и изготовления концевых участков штанги;
–для обеспечения ремонтопригодности полой штанги (для случая ее разрушения в резьбовом соединении) минимальная длина полой штанги должна быть 9,0 м и более;
– для достижения требований по надежности (ГОСТ Р 511161–2002) полой штанги насосной следует обеспечить жесткость и коррозионную стойкость полой штанги до уровня цельнометаллической за счет:
♦объемного улучшения механических свойств и использования штанг из стали 15 Н3МА, хромоникельмолибденовых низкоуглеродистых мартенситных сталей, например 07ХЗГНМ;
♦уменьшения толщины стенки полой штанги;
– в интервале спуска насосного оборудования измерение зенитного угла производить через 5 м.
125
ГЛАВА 2. НЕРАЗРУШАЮЩИЕ МЕТОДЫ КОНТРОЛЯ НАСОСНЫХ ШТАНГ НА ПРЕДМЕТ ВЫЯВЛЕНИЯ ДЕФЕКТОВ, НАРУШАЮЩИХ ИХ СПЛОШНОСТЬ И ОДНОРОДНОСТЬ СТРУКТУРЫ МАТЕРИАЛА ТЕЛА
Для достижения и обеспечения качественных эксплуатационных показателей нефтепромыслового оборудования, используемого
вагрессивных средах при действии статических и динамических нагрузок в условиях высоких температур и давлений, необходимым условием является проведение неразрушающего входного, выходного и текущего контроля как в процессе изготовления оборудования, так и в процессе его промышленного использования.
Теоретическое обоснование необходимости разработки и промышленного использования средств неразрушающего контроля деталей, узлов, изделий осуществили ученые В.К. Аркадьев, Н.С. Акулов, В.Г. Герасимов, Т.Я. Горадзовский, А.Л. Дорофеев, В.В. Клюев, А.Б. Сапожников, Р.И. Янус, Е.И. Окрушко, М.А. Ураксеев.
Особая роль в развитии теории электромагнитных процессов
впроводящих ферромагнитных материалах при решении задач по магнитной, вихретоковой дефектоскопии, магнитоструктурным исследованием принадлежат коллективу сотрудников Института физики металлов АН СССР С.В. Воносовскому, В.В. Власову, Н.Н. Зацепину, М.Н. Михееву, Н.М. Родигину, П.А. Халилеву, А.С. Шлеенкову.
2.1.Магнитолюминесцентный метод неразрушающего контроля концевых участков насосных штанг
Для раннего обнаружения усталостных микротрещин и видимого контроля состояния штанги на наличие микротрещин был исследован и апробирован один из эффективных методов неразрушающего контроля – магнитолюминесцентный метод. С этой целью
126
был выполнен комплекс работ по усталостным испытаниям штанг в коррозионной среде, приближенно моделирующей реальные условия их эксплуатации.
Магнитолюминесцентный метод, являющийся разновидностью магнитопорошкового метода, преимущественно предназначен для контроля деталей с темными поверхностями и для выявления дефектов, выходящих на поверхность и лежащих на небольшой глубине под поверхностью. Сущность метода заключается в том, что при намагничивании ферромагнитных материалов в местах дефектов происходит рассеивание и выход на поверхность магнитных силовых линий с образованием на границах дефекта полюсов. При проливании магнитной суспензии или нанесении магнитного порошка на поверхность штанги к полюсам в пределах дефекта (сплошности, структурной неоднородности) притягиваются частицы магнитного порошка, указывая его местонахождение, протяженность и вид. При данном методе в качестве индикаторного пенетранта были использованы магнитолюминесцирующие порошки. Применение таких порошков, как установлено в процессе исследований, имеет преимущество в связи с тем, что магнитные частицы, сложившиеся над дефектом, при ультрафиолетовом освещении как бы заставляют дефекты светиться и тем самым установить местоположение дефекта, его протяженность, границы и геометрию.
Рассмотрены два способа осуществления магнитолюминесцентного метода: сухой и мокрый. При мокром методе была использована суспензия магнитолюминесцирующего порошка, при этом мелкие частицы порошка в суспензии не ведут себя как индивидуальные. Мелкие частицы представляют собой готовые магнитики, которые при достаточно высокой концентрации в жидкости сцепляются в цепочки, создавая тем самым как бы новые искусственно удлиненные частицы с большим магнитным моментом. Мокрый метод обеспечивает быстрое и сплошное покрытие магнитными частицами поверхности изделия, например концевой участок насосной штанги, и при этом магнитные частицы имеют весьма высокую подвижность. Сухой и мокрый способы контроля были осу-
127

ществлены с применением магнитолюминесцентных сухих порош-
ков ЛЮМАГПОР-5 (ТУ 6-09-5296–86) и LY-2500 фирмы Helling
и суспензий на их основе.
На начальном этапе было проведено опробование порошка LY-2500 фирмы Helling с целью определения возможности его применения для магнитолюминесцентного контроля концевых участков штанг и на соответствие требованиям ТУ 6-09-5296–86 по пунктам 3, 5, 6 порошка ЛЮМАГПОР-5. Порошок LY-2500 визуально мелкодисперсный, зеленого цвета, без запаха, светлей порошка ЛЮМАГПОР-5. Порошок LY-2500 был проверен на соответствие ТУ 6-09-5296–86 по пунктам 3, 5, 6. Анализ порошка по пунктам 5, 6 соответствовал требованиям ТУ, но при выполнении пункта 3 «Определение выявляющей способности» порошка LY-2500 протяженность выявленных микротрещин на образцах на 2–3 мм больше, чем при применении порошка ЛЮМАГПОР-5, и при этом на образцах наблюдался небольшой желтовато-зеленый фон. Результаты использования сухого способа с применением вышеуказанных порошков при люминесцентном методе контроля поверхности штанги представлены в табл. 2.1.
Таблица 2 . 1
Чувствительность сухого способа (порошок ЛЮМАГПОР-5, LY-2500)
магнитолюминесцентного контроля поверхности штанги
№ |
Тип |
Способ контроля |
Результат контроля |
|
п/п |
порошка |
|||
|
|
|||
1 |
ЛЮМАГПОР-5 |
На остаточной намагниченности |
Дефекты не выявляются |
|
(соленоид) |
||||
2 |
–“– |
В приложенном поле постоянного |
Дефекты не выявляются |
|
|
|
магнита |
|
|
3 |
–“– |
В приложенном поле электромаг- |
Дефекты не выявляются |
|
|
|
нита |
|
|
4 |
LY-2500 |
На остаточной намагниченнсти |
Дефекты не выявляются |
|
|
|
(соленоид) |
|
|
5 |
–“– |
В приложенном поле постоянного |
Дефекты не выявляются |
|
|
|
магнита |
|
|
6 |
–“– |
В приложенном поле электромаг- |
Дефекты выявляются |
|
|
|
нита |
|
128

Из табл. 2.1 следует, что при сухом способе магнитолюминесцентного метода контроля поверхности штанги дефекты, нарушающие сплошность ее поверхности, были выявлены только при использовании порошка LY-250 в приложенном поле электромагнита с подружиненными шинами, работающего от сети переменного тока.
При опробованиимокрого способа магнитолюминесцентногометода контроля былиподготовлены два варианта суспензий: с порошком LY-2500 – два состава в разных соотношениях и с порошком ЛЮМАГПОР-5 – один состав. Концентрация всех суспензий составляла 2 г/л. В первом варианте были приготовлены две суспензии по стандартной методике с ЛЮМАГПОР-5 и LY-2500 с соотношением трансформаторного масла к РЖ-8 40 % и 60 %. Во втором варианте была приготовлена одна суспензия по стандартной методике с LY-2500
ссоотношением трансформаторного масла и РФ 40 % и 60 %. Опробование проводилось на рабочих образцах, выполненных из штанг
сшириной раскрытия трещин <1 мкм.
Впроцессе отработки сравнивалась протяженность выявленных микротрещин и наличие фона на образцах. Интенсивность фона оценивалась по 10-балльной шкале через 3 мин после полива суспензий. Результаты, полученныевпроцессеисследований, представленывтабл. 2.2.
Таблица 2 . 2
Чувствительность мокрого способа магнитолюминесцентного метода контроля поверхности штанг
|
|
|
|
Наименование суспензиииее характеристика |
|
|
|||||||||||||
Обозначение |
ЮМАГПОР-5 |
(25/75 %) |
LY-2500 (25/75 %) |
|
LY-2500 (40/60 %) |
||||||||||||||
|
Порядковый номермикротрещины, ее протяженность, мм; |
|
|||||||||||||||||
образца |
|
|
|||||||||||||||||
|
|
|
|
|
|
|
наличие фона, |
балл |
|
|
|
|
|
|
|||||
РСОМК |
|
|
|
|
|
|
|
|
|
|
|
|
|
||||||
1 |
2 |
3 |
|
4 |
фон, |
|
1 |
2 |
3 |
4 |
|
фон, |
|
1 |
2 |
3 |
4 |
фон, |
|
|
|
|
|
|
|||||||||||||||
|
|
балл |
|
|
балл |
|
балл |
||||||||||||
43–90 |
19 |
– |
– |
– |
|
1 |
20 |
– |
– |
– |
|
3 |
19 |
– |
– |
– |
1 |
||
52–90 |
17 |
– |
– |
– |
|
1 |
18 |
– |
– |
– |
|
3 |
18 |
– |
– |
- |
1 |
||
01–96 |
21 |
19 |
19 |
|
21 |
1 |
21 |
19 |
19 |
21 |
|
3 |
21 |
19 |
19 |
21 |
1 |
||
02–96 |
18 |
14 |
24 |
|
24 |
1 |
18 |
15 |
24 |
24 |
|
3 |
18 |
15 |
24 |
24 |
1 |
||
ИТОГО |
75 |
33 |
43 |
|
45 |
– |
77 |
34 |
43 |
45 |
|
– |
76 |
34 |
43 |
45 |
– |
||
Сумма |
|
196 |
|
|
4 |
|
|
199 |
|
|
12 |
|
|
198 |
|
4 |
129
Из табл. 2.2 видно, что протяженность выявленных трещин при использовании порошка LY-2500 в составе трансформаторного масла кРЖ-8 в соотношении 25/75 % на 3 мм больше, чем при использовании порошка ЛЮМАГПОР-5 в таком же соотношении масел, но при этом фон на образцах при наличии суспензии LY-2500 (25/75 %) в 3 раза превышает фон по сравнению с суспензией ЛЮМАГПОР-5 (25/75 %). Применение LY-2500 при соотношении масел 40/60 % (РЖ-8) позволяет выявлять трещины на образцах на 1 мм меньше, чем при соотношении 25/75 % (РЖ-8), и на 2 мм больше, чем при использовании ЛЮМАГПОР-5; наблюдаемый фон на образцах составляет 1 балл и соответствует фону сприменением ЛЮМАГПОР-5.
Из исследованных различных способов магнитолюминесцентного метода контроля следует, что лучшие результаты по выявляемости дефектов получены, во-первых, при использовании данного контроля в приложенном поле электромагнита, во-вторых, при использовании мокрого метода, а именно – с применением суспензии на основе люминесцентного порошка LY-2500. Применение порошка LY-2500 фирмы Helling позволяет выявлять трещины на рабочих стандартных образцах с шириной их раскрытия 1 мкм, что соответствует требованиям ГОСТ 21105–87.
Таким образом, из методов магнитолюминесцентного контроля наиболее оптимальным для контроля поверхности штанги является магнитолюминесцентный контроль в приложенном поле электромагнита с использованием суспензии на основе магнитолюминесцентного порошка LY-2500 с соотношением трансформаторного масла к РЖ-8 40/60 %.
Отработка мокрого способа магнитолюминесцентного метода контроля в производственных условиях была осуществлена в период проведения усталостных испытаний фрагмента насосной штанги. К штанге прижимались подпружиненные шипы электромагнита, включался электромагнит и при включенном электромагните на штангу наносилась магнитолюминесцентная суспензия путем полива. После стекания суспензии электромагнит отключался. После 6 081 500 циклов нагружения фрагмента штанги магнитолюминесцентным методом
130