
книги / Технологические процессы и технические средства для глубинно-насосной эксплуатации нефтяных скважин
..pdf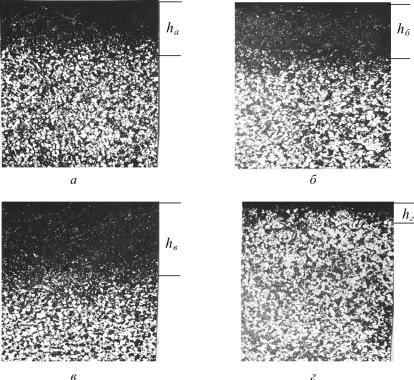
ности штанги могло быть связано с исходно неоднородной глубиной обезуглероженного слоя, а также с неравномерностью заполнения контейнера карбюризатором.
Заключительной операцией для штанг с цементованными концевыми участками была закалка с нагревом ТВЧ по технологии Очёрского машзавода. Величина предела прочности, выборочно определенная у двух цементованных и закаленных ТВЧ штанг, составила
Рис. 1.24. Микроструктура участков насосной штанги (см. рис. 1.22) из стали 20Н2М после цементации в твердом карбюризаторе при 900 ° С в течение 28 мин на производственных площадях Очёрского машзавода (г. Очёр): hа – глубина цементованного слоя вблизи высаженной части штанги; hб – глубина цементованного слоя на удалении от высаженной части штанги; hв – глубина цементованного слоя со стороны заглушки;
hг – глубина цементованного слоя вне контейнера
61
640 МПа и 714 МПа, что ниже требований ГОСТ 13877–80 [32] для штанг, прошедших закалку с нагревом ТВЧ.
Результаты усталостных испытаний образцов насосной штанги, изготовленной по данному способу, приведены в табл. 1.9.
Таблица 1 . 9
Величина предела выносливости образцов штанги их стали 20Н2М
Режим термической |
Характеристика |
Характеристикасредней |
|
упрочненныхучастков |
части(нормализация |
||
обработкиучастков |
|||
(цементацияспоследующей |
споследующейзакалкой |
||
штанги |
закалкойснагревомТВЧ) |
снагревомТВЧ) |
|
|
|||
1 |
2 |
3 |
|
Величинапредела |
|
|
|
выносливости участков |
590±23 МПа |
500±10 МПа |
|
штанги |
|
|
Примечание. Испытания проведены методом «лестницы» по схеме консольный изгиб в одной плоскости (ГОСТ 25.502–78).
Таким образом, преимущество данной технологии изготовления насосных штанг заключается в том, что появилась возможность получить насосные штанги, концевые участки которых, а именно – галтели и прилегающие к ним части тела штанги, имеют предел выносливости, превосходящий предел выносливости средней по длине части тела штанги в 1,2 раза – для штанг, прошедших дополнительное упрочнение нагревом ТВЧ, и в 2,4 раза для штанг, прошедших только нормализацию в средней ее части, что позволяет увеличить межремонтный период штанги в 2,5–10 раз.
Данные показатели достигнуты благодаря присутствию в поверхностном слое концевых участков штанги благоприятных напряжений сжатия.
Поскольку усталостное разрушение штанг будет происходить за пределами термоупрочненных концов насосной штанги, обеспечивается возможность ее восстановления после разрушения, так как разрушенную в средней по длине части штангу возможно подвергнуть механической обработке, а низкое содержание углерода в данной части штанги обеспечивает, например, свариваемость этих час-
62
тей. При этом и после ремонта сохраняется достаточный для эксплуатации межремонтный период.
Насосные штанги, прошедшие цементацию в твердом карбюризаторе по отработанной технологии, были переданы в количестве 1130 штук для промысловых испытаний в НГДУ «Осинефть» ПО «Пермнефть».
1.7. Холодная правка и контроль насосных штанг продольным нагружением. Технические средства, обеспечивающие правку и контроль
Преимущество данного способа, предназначенного для использования на предприятиях нефтегазодобывающей промышленности, ведущих ремонт и контроль нефтепромыслового оборудования [8, 34, 7, 35, 5], заключается в повышении качества правки за счет исключения приложения к штанге, бывшей в эксплуатации, растягивающих усилий, превышающих ее предел прочности, а также в увеличении производительности процесса за счет деформации штанги механическим путем, уменьшении и/или смещении остаточных макронапряжений за счет растяжения и обеспечения прямолинейности тела штанги.
Технический результат достигается за счет того, что в способе правки насосных штанг растяжением, включающем предварительное устранение местной кривизны ее тела при скорости 1,5 м/мин, упругую и пластическую деформацию штанг и контроль остаточной пластической деформации, использованы данные предварительно установленные на контрольных образцах. На образцах, выполненых из бывших в эксплуатации насосных штанг, определяют зависимость величины предела выносливости от величины пластического удлинения в процессе правки продольным растяжением. Причем контроль величины остаточной пластической деформации осуществляют в соответствии с величиной требуемого пластического удлинения, определенного по наибольшему значению предела выносливости для данной штанги из полученной ранее зависимости, и при
63
достижении требуемого пластического удлинения насосной штанги прекращают ее нагружение и завершают процесс правки.
Поскольку контрольные образцы готовят предварительно из бывших в эксплуатации насосных штанг, представилась возможность проводить испытания на образцах с различными техническими характеристиками (типоразмер, материалы, режим термоупрочнения и т.д.) и с учетом особенностей той среды, в которой штанги насосные эксплуатировались.
Исходя из того, что на контрольных образцах известной структуры, изготовленных из бывших в эксплуатации насосных штанг, получена зависимость величины предела выносливости от величины пластического удлинения, появилась возможность в процессе правки, растяжения и пластического удлинения каждой штанги производить до величины, при которой обеспечивается и сохраняется ее прямолинейность и исключается снижение предела выносливости, исходя из технических характеристик материала, геометрических размеров штанги, режима ее термообработки и условий эксплуатации.
Поскольку контрольные образцы и штанги насосные, подлежащие правке, подвергаются нагружению в идентичных условиях, появилась возможность максимально приблизить результаты испытаний на контрольных образцах к условиям эксплуатации насосной штанги в скважине. Как следствие, требуемая для обеспечения гарантированной прямолинейности насосной штанги величина пластического удлинения на стадии ее пластического деформирования определяется с высокой точностью и при сохранении предела выносливости материала штанги.
Для осуществления способа правки насосных штанг выполняют следующие операции в нижеуказанной последовательности:
–готовят контрольные образцы насосных штанг одной марки стали, одной плавки и прошедших одинаковую термическую обработку;
–каждый образец устанавливают в захваты растягивающего устройства [8], производят пластическое удлинение и на заранее выбранном базовом образце фиксируют остаточную деформацию в диапазоне от минимально регистрируемой до максимальной, сопровождающейся образованием «шейки»;
64
–из образцов, прошедших пластическое удлинение, формируют партии с одинаковой для каждой партии величиной пластического удлинения;
–образцы каждой партии подвергают усталостным испытаниям по схеме «консольный изгиб в одной плоскости» методом «лестницы» при действии нагрузки, полученной из величины приведенного напряжения в теле штанги, исходя из условий нагружения ее
вскважине;
–по полученным данным строят зависимости в координатах «предел выносливости», «относительное пластическое удлинение», по которым определяют недопустимый диапазон значений относительного удлинения, соответствующий пониженным значениям предела выносливости;
–в процессе правки укладывают штангу насосную в захваты растягивающего устройства и нагружают ее до устранения местной кривизны при непрерывном контроле величины усилия и перемещения головки штанги;
–замеряют длину насосной штанги после устранения ее местной кривизны;
–по полученным ранее зависимостям для контрольных образцов и по величине длины штанги, полученной после устранения местной кривизны с учетом ее технических характеристик (марка стали, режим термоупрочнения и т.п.), определяют величину требуемого пластического удлинения насосной штанги;
–продолжают нагружение насосной штанги при непрерывном контроле деформирующего усилия и удлинения штанги на стадии упругого и пластического деформирования;
–при достижении удлинения штанги величины, равной требуемому пластическому удлинению, прекращают нагружение насосной штанги;
–разгружают штангу насосную.
Способ правки насосных штанг растяжением был реализован в производственных условиях, где было использовано следующее оборудование: универсальная испытательная машина ГМС для рас-
65
тяжения штанг с усилием до 18 тс с регулируемой скоростью деформации до 1,5 м/мин, ходом подвижной части до 780 мм; датчик контроля величины удлинения насосной штанги, включающий задатчик величины удлинения насосной штанги и исполнительный механизм, прекращающий процесс нагружения насосной штанги; датчик контроля величины нагружения штанги, динамограф ГДМ-3; машину для усталостных испытаний по схеме «консольный изгиб».
Из насосных штанг с известными техническими характеристиками (типоразмер, марка стали, режим термоупрочнения, заводизготовитель, год и квартал изготовления и т.п.) изготовили контрольные образцы базовой длины (например, по 350 м/м). Затем каждый образец устанавливали в захват растягивающего устройства и производили их пластическое удлинение на заданную величину (от минимально возможного 0,06 % до образования «шейки» в теле). Из образцов, прошедших пластическое удлинение, сформировали партии образцов насосных штанг с одинаковой для каждой партии величиной пластического удлинения (каждая партия включала до 15 образцов). После этого каждый образец из каждой партии насосных штанг устанавливали в захват машины для усталостных испытаний по схеме «консольный изгиб в одной плоскости» при частоте нагружения 20 Гц методом «лестницы» на воздухе и определяли предел усталости для каждой партии образцов насосных штанг при одновременном действии на образец нагрузки, полученной из величины приведенного напряжения в теле штанги, исходя из условий нагружения ее в скважине.
В табл. 1.10 приведены результаты усталостных испытаний натурных образцов из насосных штанг.
По результатам усталостных испытаний построили зависимость величины предела выносливости от величины пластического удлинения, представленную на рис. 1.25.
Эксплуатация пластически деформированных штанг с неустойчивой дислокационной структурой может привести к их преждевременному усталостному разрушению [36].
66

Таблица 1 . 1 0
Результаты усталостных испытаний натурных образцов из насосных штанг, пластически деформированных действием продольной нагрузки
Порядковый |
Относительное |
Предел |
Примечание |
|
номер образца |
удлинение, % |
выносливости, МПа |
||
|
||||
0,0 |
0,0 |
255–270 |
|
|
18, 2 |
0,06–0,0876 |
220–238 |
Натурные образцы выпол- |
|
5, 8, 9, 15 |
0,2377–0,299 |
230–247 |
нены из штанг производ- |
|
1, 7, 10, 11, 13, |
0,3–0,377 |
240–252 |
ства Очёрского машзавода |
|
14, 17, 19, 21 |
(г. Очёр), сталь 20Н2М, |
|||
|
|
|||
3, 16, 4, 2, 12 |
0,4668–0,477 |
259–272 |
режим термообработки |
|
0,505–0,6944 |
нормализация |
|||
|
|
|||
22, 23, 24, 25 |
1,2–1,33 |
160–142 |
|
Рис. 1.25. Зависимость величины выносливости натурных образцов из насосных штанг от величины пластического удлинения
Штангу насосную, бывшую в эксплуатации, подлежащую правке, укладывают в захваты машины для растяжения штанги и нагружают ее до величины, при которой происходит устранение местной кривизны изделия [35]. При данном нагружении замеряют длину штанги. Длина штанги составила, например, 8020 м (начало отсчета величины удлинения штанги).
Из полученной ранее зависимости предела выносливости от величины пластического удлинения насосной штанги с учетом ее технических характеристик, например марки стали 20Н2М, режима
67
термоупрочнения – нормализации, длины, определили величину требуемого пластического удлинения данной штанги, равную 38 мм, при этом условие достижения допустимой величины предела выносливости соблюдается, так как за пределами этой величины находится недопустимый диапазон значений относительного удлинения. Продолжают нагружение насосной штанги, непрерывно контролируя по записи самопишущего прибора величину упругого и пластического удлинения насосной штанги. При достижении величины пластического удлинения, соответствующего, например, заданной величине 38 мм, начинают разгружение насосной штанги. Штангу насосную достают из захватов растягивающей машины для последующей консервации, например с использованием многокомпонентного состава [37].
Наряду с процессом правки насосной штанги продольным нагружением осуществляли визуальный и/или инструментальный контроль за видом нагрузочной диаграммы, при этом штанги, имеющие пилообразный вид диаграммы, включая начало микропластической деформации, браковали [9]. В ходе проведенных исследований по виду нагрузочной диаграммы, по результатам магнитоиндукционного контроля [5] и металлографических работ, было установлено, что большинство штанг, поступающих на правку, имели нормальную однородную ферритно-сорбитную структуру, характерную для нормализованных сталей. Однако у ряда штанг с неоднородным распределением легирующих элементов, имеющим ликвационную природу, после замедленного охлаждения при нормализации возникали условия для формирования неблагоприятной полосчатой ферритносорбитной структуры.
По результатам усталостных испытаний, металлографических исследований насосных штанг, разрушившихся в процессе эксплуатации, было установлено, что порядка 20 % штанг из стали 20Н2М (режим термоупрочнения – нормализация) из общего количества разрушений имели полосчатую ферритно-сорбитную структуру.
Проведенные усталостные испытания показали, что у штанг
стакой структурой величина предела выносливости может снизиться
с22 до 40 %, что также подтверждено исследования, изложенными
68
[27]. Полосчатая ферритно-сорбитная структура представляет собой чередующиеся полосы малопрочных, пластинчатых ферритных зерен и полосы сорбита, имеющие большую величину предела текучести. При правке штанг с такой структурой первоначально пластическая деформация начинается в ферритных полосах, причем из-за обособленности сорбитных полос в ферритных участках может наблюдаться микрососредоточенная пластическая деформация, которая сопровождается уменьшением деформирующего усилия и продолжается до тех пор, пока в процесс деформации не включаются смыкающиеся сорбитные участки, после чего дальнейшая деформация происходит уже при увеличении деформирующего усилия. Первоначально такой цикл неоднородной деформации будет иметь место в тех сечениях штанги, где выше доля ферритных зерен, а по мере увеличения деформирующего усилия процесс неоднородной деформации будет происходить и в других сечениях штанги. В результате кривая «усилие – деформация» будет иметь характерный пилообразный вид, который косвенно свидетельствует о неоднородной полосчатой структуре деформируемой штанги [9].
У штанг с однородной ферритно-сорбитной структурой пластическая деформация ферритных зерен начинается практически одновременно в силу однородности структуры, а величина микрососредоточенной пластической деформации невелика из-за малой величины участков свободного феррита. Поэтому кривая «усилие – деформация» сохраняет плавный ход, включая начало микропластической деформации.
Для установления величин остаточных макронапряжений [22] в поверхности деформируемых штанг был взят прокат диаметром 19 мм Челябинского металлургического завода. Химический состав проката из стали 20Н2М представлен в табл. 1.11.
Далее из прутков, маркировка которых указана в табл. 1.11, были изготовлены две модельные структуры в режиме:
–низкотемпературного отжига при температуре 600 ° С в течение 1 ч с охлаждением на воздухе;
–нормализация при температуре 900 ° С в течение 1 ч.
69
Таблица 1 . 1 1 Химический состав проката из стали 20Н2М (плавка М50511)
Условное |
Маркастали, |
|
|
|
ГОСТ4543–71 |
|
|
|
||
0,17– |
0,10– |
0,40– |
|
|
|
|
0,20– |
|||
обозначение |
предприятие- |
0,25 |
0,30 |
0,70 |
<0,025 |
<0,025 |
1,5–1,6 |
– |
0,30 |
|
прутка |
изготовитель |
|
|
|
|
|
|
|
|
|
|
Содержаниехимических элементов, мас. % |
|
||||||||
проката |
|
|
||||||||
|
С |
Si |
Mn |
P |
S |
Ni |
Cr |
Mo |
||
|
|
|||||||||
1 |
2 |
3 |
4 |
5 |
6 |
7 |
8 |
9 |
10 |
|
11 |
20Н2М |
0,24 |
0,30 |
0,58 |
0,013 |
0,004 |
1,79 |
0,10 |
0,20 |
|
|
(плавкаМ50511), |
|
|
|
|
|
|
|
|
|
12 |
0,23 |
0,32 |
0,58 |
0,013 |
0,004 |
1,75 |
0,15 |
0,20 |
||
Челябинский |
||||||||||
13 |
0,24 |
0,32 |
0,58 |
0,013 |
0,006 |
1,86 |
0,14 |
0,20 |
||
металлургический |
||||||||||
14 |
завод |
0,21 |
0,31 |
0,55 |
0,013 |
0,004 |
1,79 |
0,14 |
0,20 |
Далее полученные образцы деформировали путем одноосного растяжения. Характеристики образцов после деформационного воздействия и остаточные макронапряжения, выявленные рентгенографическим путем, представлены в табл. 1.12.
Таблица 1 . 1 2
Характеристика образцов после деформационного воздействия и остаточные напряжения, выявленные рентгенографическим путем
Маркастали, |
Условное |
Базовая |
Усилие |
Длинапосле |
ε, |
Остаточное |
длина |
макронапря- |
|||||
режим |
обозначение |
образца, |
Р, тс |
растяжения, |
% |
жение, |
термообработки |
образца |
мм |
|
мм |
|
кгс/мм2 |
20Н2М, |
НХД6 |
200 |
– |
образец |
0 |
–25,9 |
предприятие- |
недеформирован |
|||||
изготовитель |
НХД3 |
200 |
10,2 |
200,6 |
0,3 |
13,1 |
Очёрскиймаш- |
НХД1 |
200 |
9,8 |
204,0 |
2,0 |
0 |
завод(г. Очёр), |
НХД2 |
200 |
11,5 |
206,3 |
3,15 |
13,0 |
нормализация |
НХД4 |
200 |
13 |
209,6 |
4,8 |
–3,3 |
(полныйотжиг) |
НХД5 |
200 |
14,7 |
241,3 |
20,7 |
–6,5 |
20Н2М, |
ОХД6 |
200 |
– |
образец |
0 |
–25,9 |
предприятие- |
недеформирован |
|||||
изготовитель |
ОХД2 |
200 |
15,3 |
200,5 |
0,25 |
–6,5 |
Очёрскиймаш- |
ОХД1 |
200 |
16 |
202,5 |
1,25 |
0 |
завод(г. Очёр), |
ОХД3 |
200 |
17 |
205,4 |
2,7 |
–3,3 |
низкотемператур- |
ОХД4 |
200 |
17,8 |
206,6 |
3,3 |
13,0 |
ныйотжиг |
ОХД5 |
200 |
18,3 |
216,1 |
8,1 |
–19,7 |
70