
книги / Неформованные огнеупоры. Т. 1 Общие вопросы технологии
.pdfРис. 5.5. Интегральные кривые зернового распре |
100 |
|
|
|
|
|
|
|
|
деления систем с большей (1) и меньшей (2) поли- |
90 |
|
|
|
|
|
|
|
|
дисперсностыо и табличные данные их показателей |
|
|
|
|
|
|
|
|
|
|
|
|
|
|
|
|
|
|
|
(см. в тексте) |
70 |
|
|
|
|
|
|
|
|
|
|
|
|
|
|
|
|
|
|
|
60 |
|
|
|
|
|
|
|
|
|
ан 50 |
|
|
|
|
|
|
|
|
|
40 |
|
|
|
|
|
|
|
|
|
30 |
|
|
|
|
|
|
|
|
|
**20 |
|
|
|
|
|
|
|
|
|
10 |
|
|
|
|
|
|
|
|
|
0 |
10 20 |
30 |
40 |
50 |
60 |
70 |
80 |
90100 |
|
|
|
|
|
|
|
|
|
</, мкм |
Часто дисперсность порошков характеризуют их удельной поверхностью 5 , под которой понимают отношение суммарной наружной поверхности частиц к их массе, выражаемое в сантиметрах или метрах квадратных на грамм. Между тем, учитывая различные значения плотности керамических порошков, целесообразнее величину $ исчислять в сантиметрах квадратных на сантиметр кубический, т.е. на единицу объема.
Для характеристики полидисперсности твердой фазы суспензий или порошков в последние годы стал общеупотребительным предложенный нами еще в работе [5.19] показатель полидисперсности
Сущность определения последнего видна из рис. 5.5, где приведены и охарактери зованы интегральные кривые, характеризующиеся существенно отличающейся полидисперсностыо.
Часто оценивают также медианный диаметр частиц </м, соответствующий среднему (50 %-ному) содержанию частиц на интегральной кривой. В зарубежных проспектах по порошкам огнеупорных материалов обычно приводятся данные по их медианному диаметру (обычно И50), а также диаметр частиц, соответствующий 90 %-ному содер жанию (/990). Применительно к анализу зернового состава твердой фазы ВКВС наи более приемлемым является седиментационный анализ. При этом предварительно ситовым методом определяется содержание в них более крупных (ситовых) фракций (40-100 мкм).
Зерновой же состав огнеупорных заполнителей определяют ситовым анализом. Та кой анализ осуществляют сухим просеиванием в соответствии с межгосударствен ным стандартом ГОСТ 18318-94. Навеску порошка (100±1 г при насыпной плотности порошка >1,5 г/см3 или 50±0,5 г в других случаях) просеивают через набор стандарт ных тканых сеток (сит) с квадратными отверстиями различной величины (табл. 5.1) [5.20].
Сетки № 004-016 ткут из мягкой отожженной бронзовой проволоки марки БрОФ 6,5-0,4 с содержанием фосфора 0,3-0,4 %, а № 0071-1 — из полутомпака марки Л80. Сита должны быть круглыми с диаметром обечайки 200 мм и глубиной от 25 до 50 мм.
|
|
|
|
Т а б л и ц а 5.1 |
|
|
П р о в о л о ч н ы е с е т к и с к в а д р а т н ы м и о т в е р с т и я м и (Г О С Т 6 6 1 3 - 8 6 ) |
||||
Номер |
Номинальный размер |
Номинальный |
Количество отверстий |
Живое сечение сетки |
|
стороны отверстия в |
диаметр проволоки, |
на линейном дюйме |
(доля площади |
||
сетки |
|||||
свету, мкм |
мкм |
(число меш) |
отверстий), % |
||
|
|||||
004 |
40 |
30 |
363 |
32,7 |
|
0045 |
45 |
36 |
314 |
30,9 |
|
005 |
50 |
36 |
295 |
33,8 |
|
0056 |
56 |
40 |
265 |
34,0 |
|
0063 |
63 |
40 |
247 |
37,4 |
|
0071 |
71 |
50 |
210 |
34,4 |
|
008 |
80 |
50 |
195 |
37,9 |
|
009 |
90 |
60 |
170 |
36,0 |
|
01 |
100 |
60 |
154 |
39,1 |
|
0112 |
112 |
80 |
132 |
34,0 |
|
0125 |
125 |
80 |
124 |
37,2 |
|
014 |
140 |
90 |
110 |
37,0 |
|
016 |
160 |
100 |
98 |
37,9 |
|
018 |
180 |
120 |
85 |
36,0 |
|
02 |
200 |
120 |
79 |
39,1 |
|
0224 |
224 |
120 |
74 |
42,4 |
|
025 |
250 |
120 |
69 |
45,6 |
|
028 |
280 |
140 |
60 |
44,4 |
|
0315 |
315 |
160 |
53 |
44,0 |
|
0355 |
355 |
160 |
49 |
47,0 |
|
04 |
400 |
160 |
45 |
51,0 |
|
045 |
450 |
200 |
39 |
47,9 |
|
05 |
500 |
250 |
34 |
44,4 |
|
056 |
560 |
250 |
31 |
47,8 |
|
063 |
630 |
300 |
27 |
45,9 |
|
07 |
700 |
300 |
25 |
49,0 |
|
08 |
800 |
300 |
23 |
53,0 |
|
09 |
900 |
400 |
20 |
47,9 |
|
1 |
1000 |
400 |
18 |
51,0 |
Для ситового анализа порошков используют специальное устройство (рис. 5.6), рабо тающее по принципу вращательного движения со скоростью вращения 300±15 мин"1 при одновременном встряхивании с равномерной частотой 180±10 в минуту.
Допускается применять другие механизмы, а также режимы работы, обеспечиваю щие идентичные результаты (например, российский ситовый анализатор “Гран”, не мецкие установки фирмы ФРИЧ “Анализетте-3” и “Анализетте-18” и др.). Просеива ние продолжают до окончания рассева, или в течение времени, указанного в норма тивной документации на конкретный порошок. Время окончания рассева достигается в момент, когда количество порошка, проходящее в течение одной минуты через сито, задерживающее наибольшую его массу, изменяется менее чем на 0,1 % массы пробы для испытания. Допускается просеивание порошка вручную (его приемы должны быть указаны в нормативной документации на конкретный порошок).
Рис. 5.6. У стройство для рассева порош ков
на ф ракции (си то в ы й ан ал и затор м арки 028М : 1 — электродвигатель; 2 — кулиса;
3 — набор сит; 4 — корпус с вмонтирован ным редуктором )
В США применяют свою шкалу се ток. За основу принято сито с разме ром отверстий в свету 0,074 мм. Есть основной ряд сит с модулем л/2 = = 1,414 и дополнительный ряд с мо дулем ур2 = 1,189 (модулем называ ют постоянное отношение размеров отверстий двух сит, смежных в набо ре, т.е. следующих одно за другим). Размер отверстий любого сита кратен
0,074 мм. Например^размер отверстий следующего за основным более крупного сита составляет 0,074- л/2 = 0,104 мм, затем 0,104- л/2 = 0,147 мм и т.д. Для вычисления размера отверстий сит дополнительного ряда пользуются модулем у2
В этой системе номер сита указывают в мешах (число меш означает количество отверстий на одном линейном дюйме, равном 25,4 мм). Диаметр проволоки каждого сита равен размеру отверстия а, который определяют по формуле а = с1= 25,4/2/л, где т — число меш. Например, для сита 200 меш размер отверстия составляет
а = 25,4/(2-200) = 0,0635 мм = 63,5 мкм.
Для любой шкалы сеток зависимость между размером отверстия а, мм, диаметром проволоки <1, мм, числом меш т и живым сечением сетки $ , % — относительной площадью отверстий, выражается так:
т = 25,4/(а + О); Зс= 0,155 (25,4 - те!)2; 5с= [а/(а + </)2]100.
Долю порошка, оставшуюся на сите при просеве, называют плюсовой фракцией, а прошедшую через сито — минусовой фракцией. Кроме того, часто термином “субси товая фракция” обозначают долю порошка, прошедшего через сетку с наименьшим размером отверстий в данном наборе сит.
Фракцию, количество которой составляет <0,1 %, обозначают как “следы”.
5.3. Технологические свойства и характеристики порошков. Способы их изучения
К основным технологическим свойствам порошков относится их текучесть (сыпу честь), насыпная плотность рнас, г/см3 или соответствующий показатель коэффициен та упаковки Куп[5.15; 5.20]. Эти показатели определяют как для насыпного состояния, так и в состоянии утряски (виброуплотнения).
Рис. 5.7. Схема (а) образования угла естественного откоса а и приборы (б, в) для его определения: 1
— корпус; 2 — шибер; 3 — прозрачная стенка с угломером
Характеристика сыпучести (текучести) для огнеупорных порошков и формовочных систем является весьма важной. Она в значительной степени определяет возможность быстрого и равномерного заполнения форм различной конфигурации. Сыпучесть за висит прежде всего от трения и сцепления зерен на контактах частиц. О ней можно косвенно судить по углу естественного откоса (рис. 5.7). Значения последнего чаще всего находятся в интервале 30-40°.
Показатель величины насыпной плотности рн представляет собой массу единицы объема порошка при свободной насыпке, т.е^ рн является объемной характеристикой. В соответствии с межгосударственным стандартом ГОСТ 19440-94, принятым в по рошковой металлургии [5.20] для определения ри, используют либо воронку (рис. 5.8, а), если порошок способен самопроизвольно истекать через отверстие, либо систему воронок с пластинками (волюмометр Скотта, рис. 5.8, б), представляющую собой пря моугольный сосуд с внутренними наклонными стеклянными полочками, по которым под действием силы тяжести ссыпается порошок.
Перед анализом проба порошка объемом >100 см3 должна быть высушена при 110=Ь5 °С до постоянной массы в сушильном шкафу с последующим охлаждением в эксикаторе до температуры окружающей среды.
Величину, обратную насыпной плотности, называют насыпным объемом Г|мс, см3/г, который представляет собой объем, занимаемый единицей массы порошка при его свободной насыпке:
Насыпной объем порошка всегда в несколько раз больше удельного объема компак тного материала Ук( Г = 1/ук, где ук — табличная плотность материала порошка или пикнометрическая плотность его частиц).
Для виброформуемых огнеупоров исключительно важной характеристикой являет ся величина “плотности утряски”, т.е. насыпной плотности после виброуплотнения гу. В соответствии с ГОСТ 25279-82, навеску порошка 50-100 г после просушки поме щают в стеклянный мерный цилиндр объемом 100 или 25 см3, на который накладыва ют осевую вибрацию с частотой 100-300 ударов в минуту при амплитуде встряхива ния 3,0±0,2 мм [5.20]. После прекращения изменения объема порошка в процессе встря хивания его фиксируют прямо в мерном цилиндре и известную массу порошка делят на эту величину объема:
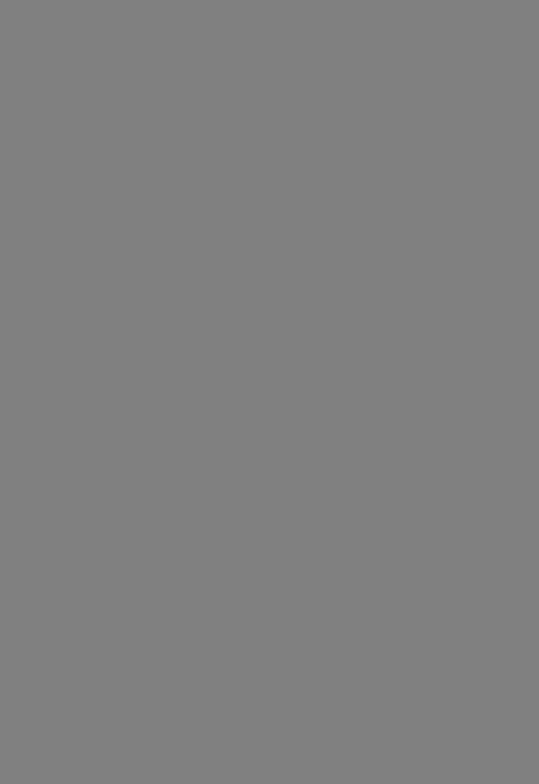
5.4. Влияние некоторых технологических параметров на упаковочные свойства огнеупорных порошков
Одной из существенных характеристик порошков в технологии неформованных огнеупоров является их упаковочная способность, выражаемая коэффициентами упа ковки в свободно насыпанном состоянии К п“, и после утряски Купу или соответствую щими значениями насыпной плотности рн и ру. Известно, что эти показатели подвер жены значительным колебаниям в зависимости от влажности порошков (масс); это может оказывать влияние на некоторые технологические процессы и качество конеч ного материала. Так, при объемном дозировании компонентов огнеупорной шихты, осуществляемом пластинчатыми, ленточными, вибрационными, барабанными пита телями, вследствие изменяющейся насыпной плотности порошков (из-за непостоян ной их влажности) заданный состав может не соблюдаться, что неблагоприятно ска зывается на свойствах огнеупора.
Известно существенное влияние влажности на плотность укладки компонентов в технологии керамики [5.15], бетонов [5.21, с. 205] и огнеупоров.
В работе [5.22] на примере порошков огнеупорных материалов [электрокорунд, электроплавленая М&О, 2Ю2,2г8Ю4,8Ю2 (песок и кварцевое стекло), синтетический мул лит, высокоглиноземистый шамот, каолин, 8Ю] изучено влияние влажности, дисперс ности, зернового распределения, типа смачивающей жидкости на показатели /Г ",Куу
(Р н . Ру>*
По аналогии с грунтами [5.23, с. 100], в увлажненных огнеупорных порошках мож но различать три основные фазы: твердую (скелет), жидкую (смачивающая жидкость, связка) и газообразную (поровый воздух). Для оценки фазового состава порошков и влияния на него влажности (0^), кроме указанных, целесообразны показатели влаж ностного изменения насыпной плотности в свободно насыпанном состоянии К* или после утряски К у.
|
|
п |
Кн |
п |
К у |
|
|
лгн - |
Рн2 - |
У"2 • |
- Иу2 - |
У"2 |
(5.1) |
|
|
|
|
" ' Р У |
|
|
где рн1, ру|, |
— соответствующие значения р и |
порошка в абсолютно су |
||||
хом состоянии; р^, ру2, |
— соответственно “истинные” насыпные плотности |
в насыпанном состоянии и после утряски (или соответствующие значения /Сп), отне сенные к абсолютно сухому веществу влажного порошка (кажущаяся плотность ске лета влажного порошка).
“Истинные” насыпные плотности определяются по формулам
Рн? |
н3 |
Руз |
(5.2) |
|
1+Ж ./100’ Ку2 |
1 + Жд/ЮО* |
|||
"2 |
|
где Риз,ру3— соответствующие “кажущиеся” значения рн порошкаво влажном состоянии. Влияние утряски (виброутряски) на р или оценивали коэффициентом утряски Ку:
К |
РУ_= Ц 1 |
|
у |
(5.3) |
|
|
Рн |
К}*' |
Для определения влажностного изменения рн, ру исследованных систем исходные пробы порошков (около 1 л) в абсолютно сухом состоянии увлажняли с постепенным увеличением влажности вплоть до достижения пастообразного состояния, характери зуемого показателем влажности У?п(влажность пасты).
После каждой стадии порционного увлажнения водой или другой жидкостью до соответствующей заданной влажности порошки смешивали и определяли р , р , К н,
К \ К " , К \ К . " у
Влияние абсолютной влажности на изменение К ^ порошков А12Оэ, М §0,2Ю 2 раз личной дисперсности показано на рис. 5.9.
В зависимости от среднего диаметра ( ^ ) частиц наблюдается существенная разни ца в /Гу1)" как в исходном состоянии (IVа= 0), так и в увлажненном. Во всех случаях с ростом IVа(до определенных пределов) наблюдается уменьшение (влажностное разрыхление); при дальнейшем увлажнении происходит уплотнение материала (уве
личение# ").
уп 7
Как правило, более тонкодисперсным порошкам соответствуют и большие степени их максимального влажностного разрыхления К™ Так, в случае А120 3 для монофрак ций 1,6-2,5; 0,1-0,2; 0,04-0,05 мм (с исходным К ^1= 0,42) # шсоставляет 1,16; 1,44; 1,61; для монофракций М §0 1,6-2,5; 0,315-0,4; 0,16-0,2 мм (с исходным = = 0,45*0,50) # тсоставляет 1,08; 1,33; 1,8 соответственно. Существенное разрыхле-
Р и с. 5 .9 . З а в и си м о сть К ^" о т \Уа для порош ков элекгр о ко р унд а(а), элекгроплавлено й М § 0 (б), 2 г О ,
(в) различной д и сп е р сн о сти : |
а) I — 5 - 7 м м ; 2 — 1 ,6 -2 ,5 |
м м ; 3 — 0 ,4 -0 ,6 3 м м ; 4 — |
0 ,1 - 0 |
,2 |
м м ; 5 — |
|||||||||||
0 ,0 4 -0 ,0 5 м м ; б — |
см е сь 5 |
0 % |
ф р акц и и 1 ,6 -2 ,5 мм и 50 % |
0 ,0 4 -0 ,0 5 м м ; б) 1 — |
1 ,6 -2 ,5 м м ; 2 |
— 0 , 3 1 5 - |
||||||||||
0,4 |
мм; 3 — |
0 ,1 6 |
-0 ,2 м м ; |
4 — |
< 0 ,0 8 м м ; |
5 — |
по ли ди сперсны й |
состав (46 % |
1 ,6 -3 |
,5 м м ; |
2 4 % |
0 ,2 — |
||||
0,4 |
мм; 30 % |
< 0 ,0 |
8 м м ); в) 1 — |
2 ,5 -5 ,0 м м |
; 2 — |
1 ,5 -2 ,5 мм; 3 — |
0 ,0 4 -0 ,0 5 м м ; 4 — |
0 ,0 0 5 - |
0 |
,0 1 |
мм) |
ние отмечается у тонкодисперсных порошков 2Ю,, для которых Кнтдостигает 2,25 (кривые Зу 4 рис. 5.9, в).
Аналогичное влияние дисперсности на К и Ккустановлено на монофракциях квар цевого песка. Так, для монофракций 0,1-0,2; 0,2-0,315; 0,315-0,4 мм /Гпи при IVа= 0 составляет 0,54-0,56, а Кнтпри влажности, соответствующей максимальному разрых лению (5-10%), 1,80; 1,62; 1,50 соответственно.
Характерно поведение двухфракционных смесей порошков, показанное на рис. 5.9, а (кривая 6) и рис. 5.9, б (кривая 5). Для них отмечаются большие значения исходных Ку *и пониженные величины IVаперехода в состояние суспензии, что характеризуется соответствующим увеличением К ”
Показатели Кншдвухфракционных, а также полидисперсных порошков близки к ад дитивным по отношению к исходным монофракциям или определяются тонкой фрак цией. Так, в случае корунда для монофракций 1,6-2,5 и 0,04-0,05 мм Кнтсоставляет 1,25 и 1,61, а для смеси этих фракций (50:50) Китповышается до 1,68.
В случае пористых порошков в области низких значений РК для достаточно круп ных монофракций разрыхления упаковки не наблюдается, что показано на рис. 5.10 для высокоглиноземистого шамота пористостью около 15 %.
После насыщения пор жидкостью поведение таких порошков аналогично беспористым, при этом влияние дисперсности столь же существенно.
Рассмотренная закономерность увеличения эффекта влажностного разрыхления порошков по мере повышения их дисперсности не соблюдается в том случае, когда исходные порошки вследствие высокой дисперсности или анизодиаметричности име ют рыхлую упаковку. В качестве примера приведена подобная зависимость для по рошков кварцевого стекла (рис. 5.11).
Если монофракция 0,2-0,315 мм характеризуется Купни Куу0,50 и 0,60, то полидисперсный порошок со средним размером частиц */ср = 9 мкм соответственно 0,26 и 0,37, а К* и К* достигают значений 2,12 и 1,45; 1,22 и 1,33 соответственно. Тонкодисперс ные порошки при влажностях максимального разрыхления обладают меньшим коэф фициентом утряски К (1,32 против 1,9 для монофракции).
Как следует из уравнений (5.1) и рис. 5.11, показатели Кпни Кххуэквивалентны соответ ствующим показателям Куп. Кривые зависимости Куппорошков от Ж для насыпанного
Рис. 5.10. Зависимость |
от IVадля высокоглиноземистого |
пористого шамота фракции 1,6-3,0 мм (У); 0,63-1,6 мм (2); <0,63 мм (5)
Рис. 5.11. Зависимость и (а), К* и (б) от \Уддля монодисперсного порошка фракции 0,2- 0,315 мм (состав 1) и полидисперсного со средним размером частиц = 9 мкм (состав 2) порошка кварцевого стекла
состояния и после утряски, как правило, идентичны; с тем отличием, что вибрация по зволяет достигать пастообразного состояния системы при меньших значениях \Уа.
Специфично поведение каолиновых порошков, для которых характерно низкое зна чение Куп в исходном состоянии (#уп" = 0,13; # пу = 0,20) и его повышение по мере увлажнения. В отличие от рассмотренных случаев, для каолиновых порошков по мере роста IVанаблюдается влажностное уплотнение системы (К„< 1) с постепенным пере ходом в пастообразное состояние.
С целью изучения влияния на упаковочную способность вида дисперсионной сре ды (увлажняющей жидкости) к порошкам добавляли, кроме воды, гидролизованный этилсиликат-40 [5.24], этиловый спирт, раствор с.с.б.; опробованы также добавки кремнийорганической жидкости ГКЖ.
Существенное влияние жидкости на упаковочную способность полидисперсных порошков М§0 показано на рис. 5.12.
В области низкой влажности при использовании спирта (кривые У, Г) наблюдается некоторый рост при этом переход в пастообразное состояние достигается при мень ших значениях IVа, чем при затворении водой (кривые 3, У). Еще более эффективным в этом отношении является этилсиликат (кривые 2 ,2').
Лучшая упаковочная способность с применением этилсиликата отмечается и у по рошков синтетического муллита, циркона и карбида кремния (рис. 5.13).
Анализ экспериментальных данных показывает, что в большинстве случаев в опре деленной области влажности отмечается существенное “разрыхление” порошка (умень шение плотности упаковки), максимальная абсолютная величина которого зависит от ряда факторов: дисперсности, зернового распределения и плотности порошка, вида смачивающей жидкости и др. При этом в зависимости от влажности в системе поро шок-жидкость условно можно выделить три характерных состояния: сыпучее при Ж = = 0, максимального влажностного разрыхления (УСупт) при IV и перехода в пасто образное состояние при IVп(рис. 5.14).
Плотность упаковки порошка в сыпучем состоянии снижается с повышением дис персности частиц за счет увеличения их поверхности на единицу веса (рост числа
Рис. 5.12. Зависимость |
(— ) и К ^ (------ |
) |
Рис. 5.13. Зависимость К^' от \Уадля полидиспер |
||
порошков окиси магния полидисперсного со |
сного порошка (33 %фракции 0-0,63 мм; 67 % 1,6— |
||||
става (46 % фракции 1,6-3,5 мм; 24 % 0,2-0,4 |
3,0 мм) синтетического муллита (7), монофракци- |
||||
мм; 30 % <0,08 мм) от IVдпри использовании |
онного (0,16-0,2 мм) ЗЮ (2) и полидисперсного |
||||
для увлажнения и связки спирта (7, 7), этил- |
(</ф » 10 мкм) 2г5Ю4 (5) при использовании для ув |
||||
силиката (2, 20, воды (5, З1) |
|
лажнения этилсиликата (------ |
) и воды (------ |
) |
контаетов и уменьшение удельного “сжимающего” давления в них). По мере увлаж нения порошков в них появляются дополнительные силы сцепления вследствие ка пиллярного давления стыковой воды [5.21, с. 243], окружающей точки контакта меж ду частицами. При этом наибольшая интенсивность повышения сцепления наблюда ется в области влажности 1-2 %, максимальное же сцепление достигается при \Укр (см. рис. 5.14). При дальнейшем увлажнении мениски в точках контакта исчезают, сцепление системы уменьшается и она уплотняется до значений Куп, как в исходном сухом порошке, или даже больших, что желательно при получении из порошков сус пензий и паст.
К
III
Рнс. 5.14. Общий характер зависимости коэффициента влажностного изменения плотности К (а) и К^ (б) от влажности керамических порошков со связкой на основе воды (7) и с добавкой ПАВ (2) и основные их состояния: 7— максимальная сыпучесть; II— максимальное разрыхление; 7/7— пере ход в пасту