
книги / Технология переработки нефти и газа. Первичная переработка нефти и газа
.pdf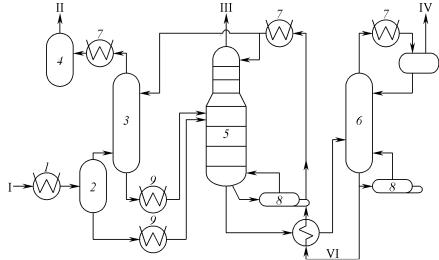
параторе 2 сконденсированных углеводородов через детандер 3 по- ступает в колонну 4. В нее же из теплообменников 8 поступает смесь сконденсированных углеводородов после сепаратора 2. С низа колон- ны отбирают смесь всех сконденсированных углеводородов (от С2 и выше), а деэтанизированный газ с верха колонны 4, пройдя тепло- обменники 8, сжимается в турбодетандере 3 и идет к потребителю. ШФЛУ направляется на ректификацию, где отделяется С2 (содержа- ние которого составляет 87–90 мол. %) и остальные углеводороды.
4.4.3. Маслоабсорбционное извлечение
Сущность процесса состоит в поглощении тяжелых углеводоро- дов абсорбентом (маслом) с последующей их десорбцией путем от- парки из абсорбента.
В качестве абсорбента обычно используют керосиновую или ди- зельную фракции (средняя молекулярная масса 140–200). Рассмотрим технологическую схему процесса абсорбции (рис. 4.7).
Рис. 4.7. Принципиальная схема процесса масляной абсорбции:
1 – охладитель газа; 2, 4 – сепаратор; 3 – абсорбер; 5 – отпарная колонна; 6 – десорбер; 7 – холодильники; 8 – ребойлеры; 9 – теплообменники.
I – исходный газ; II – отбензиненный газ; III – газ деэтанизации; IV – ШФЛУ; V – насыщенный абсорбент; VI – регенерированный абсорбент
151
Согласно схеме исходный газ охлаждается в охладителе 1, раз- деляется в сепараторе 2 и поступает в абсорбер 3, где извлекается ос- новная масса тяжелых углеводородов. Насыщенный абсорбент через теплообменник 9 поступает в абсорбционно-отпарную колонну 5. В нее же поступает конденсат из сепаратора 2. На верх колонны 5 по- дается регенерированный абсорбент, а снизу через ребойлер 8 пода- ется тепло. В колонне 5 из насыщенного абсорбента с абсорбера 4 от- париваются легкие углеводороды, а свежим абсорбентом поглощают- ся углеводороды С3 и выше. Полностью насыщенный абсорбент с низа колонны 5 нагревается в теплообменнике 9 и идет в десорбер 6, где от него отгоняется ШФЛУ. Регенерированный абсорбент посту- пает в аппараты 4 и 5.
Технологические параметры процесса:
абсорбер: t = 10–30 °C, |
Р = 4–7 МПа; |
десорбер: tниза = 220–230 °С, |
Р = 0,7–1,5 МПа. |
Схема позволяет извлечь 50–70 % углеводородов С3 и до 98 % углеводородов С4 и выше.
4.4.4.Стабилизация газового бензина
иполучение индивидуальных углеводородов
Полученный в ходе отбензинивания УГ газовый бензин, или ШФЛУ, содержит в своем составе достаточно много углеводоро- дов С2–С4, а следовательно, имеет высокое давление насыщенных па- ров и не может быть использован в качестве компонента товарного бензина. В связи с этим данный бензин подвергают стабилизации – удалению легких углеводородов. Различают 2 типа стабилизацион- ных установок, различающихся ассортиментом получаемых продук- тов помимо стабильного бензина:
а) с получением сжиженного газа; б) с получением индивидуальных углеводородов.
Установка стабилизации с получением сжиженного газа
Рассмотрим схему процесса (рис. 4.8).
Согласно схеме нестабильный бензин через теплообменник 1 поступает в колонну 2. Колонна работает при t = 40–45 °С и Р = 1,0–
152
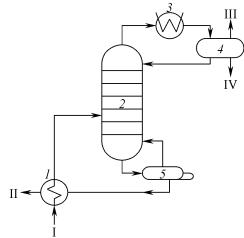
1,5 МПа. С верха колонны уходит газ С1–С4, который после охлажде- ния в конденсаторе-холодильнике 3 попадает в емкость орошения 4, с верха которой уходит газ С1–С2, с низа – пропан-бутановая смесь (сжиженный газ).
Рис. 4.8. Принципиальная схема установки стабилизации газового бензина с получением сжиженного газа:
1 – теплообменник; 2 – колонна ректификации; 3 – конденсатор-холодильник; 4 – емкость орошения; 5 – ребойлер.
I – нестабильный бензин; II – стабильный бензин;
III– газ; IV – пропан-бутановая смесь
Сниза колонны 2 отбирают стабильный газовый бензин, кото- рый, пройдя теплообменник 1, уходит с установки. Тепло вводится
внизу колонны за счет нагрева части стабильного бензина в ребойле- ре 5 и возврата его в колонну.
Установка стабилизации с получением индивидуальных углеводородов
Рассмотрим схему процесса (рис. 4.9).
Согласно схеме нестабильный газовый бензин после нагрева в теплообменнике 5 поступает в этановую колонну 1, с верху которой выходят углеводороды С1–С2. Остаток идет в пропановую колонну 2,
153
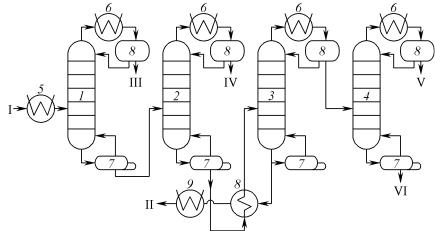
сверху которой отводится С3, а остаток идет в бутановую колонну 3,
сверху которой получают С4, а с низу – стабильный бензин. Бутаны дополнительно разделяют в колонне 4 на изобутан (сверху) и н-бутан (снизу).
Рис. 4.9. Принципиальная схема установки стабилизации с получением индивидуальных углеводородов:
1, 2, 3, 4 – этановая, пропановая, бутановая, изобутановая колонны; 5 – теплообменник; 6 – холодильники-конденсаторы; 7 – ребойлеры; 8 – емкость орошения; 9 – холодильник.
I – нестабильный бензин; II – стабильный бензин; III – углеводороды С1–С2;
IV – углеводороды С3; V – изобутан; VI – н-бутан
Давления в колоннах: в этановой (1) Р = 4 МПа; в пропано- вой (2) Р = 1,0–1,5 МПа; в бутановой (3) и изобутановой (4) – Р = 0,4– 0,6 МПа.
4.5. Стабилизация и переработка газовых конденсатов
Для ряда газовых месторождений характерно высокое содержа- ние высокомолекулярных углеводородов, которые при снижении дав- ления выделяются в виде жидкой фазы. Такие месторождения отно- сятся к разряду газоконденсатных, и при их эксплуатации в качестве основного продукта получают не только газ, но и газовый конденсат, представляющий собой фракцию с температурой кипения от 30–50
154
до 180–360 °С (бензиновую, дизельную). Содержание конденсата в газе может достигать 500 г/м3. Стабилизированный конденсат – это жидкость светло-желтого цвета с плотностью 700–800 кг/м3.
В зависимости от содержания конденсата в газе газоконденсат- ные месторождения разрабатываются как обычные газовые или как газоконденсатные. В первом случае по мере добычи газа пластовое давление падает и за счет конденсации тяжелые углеводороды теря- ются уже в пласте. Если же месторождение разрабатывается как газо- конденсатное, с поддержанием внутрипластового давления за счет за- качки в пласт сухого газа, то удается достаточно полно наряду с газом извлечь и конденсат.
Газовыми конденсатами являются как смесь тяжелых углеводо- родов (ШФЛУ), выделяемая из газа перед его отправкой в магист- ральные газопроводы, так и жидкая смесь тяжелых углеводородов, выносимая газом из скважин в виде капель и отделяемая от него ме- ханически на первых ступенях сепарации.
Первый из конденсатов получил название газового бензина. Он содержит смесь углеводородов от этана до гексана (с примесью гептана и октана) и обычно перерабатывается на установках газо- фракционирования с получением индивидуальных углеводородов, которые используются в качестве сырья для нефтехимии.
Сырой газовый конденсат, выносимый в виде капельной жидко- сти из скважины (10–500 г/нм3), по своему составу более тяжелый
исодержит углеводороды от С2 до С20 и выше. Технология перера- ботки этого конденсата включает следующие процессы: стабилиза- цию, обезвоживание и обессоливание, очистку от серы, перегонку
ивыделение фракций моторных топлив и их облагораживание. Групповой химический и фракционный состав газовых конденса-
тов разных месторождений различается, и для того чтобы установить определенный подход к их оценке, введена стандартная классифика- ция (ОСТ 51.56–79). Классификационными признаками при этом слу- жат: содержание общей серы, массовая доля ароматических и нор- мальных алкановых углеводородов и фракционный состав (табл. 4.7).
155
Наряду с углеводородами метанового ряда газовые конденсаты могут содержать в своем составе много нафтеновых и ароматических углеводородов. В связи с этим газовые конденсаты являются прекрас- ным сырьем для нефтехимических производств и позволяют строить нефтехимические комплексы без нефтеперерабатывающей части.
|
|
|
Таблица |
4.7 |
|
Классификация газовых конденсатов |
|
|
|||
|
|
|
|
|
|
Классификационный |
Обозначе- |
Наименование |
|
Нормы |
|
признак |
ние |
|
|
|
|
Содержание серы |
I |
Малосернистые |
До 0,05 мас. % |
||
|
|
|
|
||
|
II |
Сернистые |
От 0,05 до 0,8 мас. % |
||
|
III |
Высокосернистые |
Свыше 0,8 мас. % |
||
Содержание аромати- |
А1 |
Высокоароматизиро- |
Свыше 20 мас. % |
||
ческих углеводородов |
|
ванные |
|
|
|
|
А2 |
Среднеароматизиро- |
От 15 до 20 мас. % |
||
|
|
ванные |
|
|
|
|
А3 |
Малоароматизиро- |
До 15 мас. % |
|
|
|
|
ванные |
|
|
|
|
|
|
|
||
Содержание |
Н1 |
Высокопарафинистые |
Свыше 25 мас. % |
||
н-алканов во фракции |
|
|
|
||
Н2 |
Парафинистые |
От 18 до 25 мас. % |
|||
200–3200С |
|
|
|
||
Н3 |
Малопарафинистые |
От 12 до 18 мас. % |
|||
|
Н4 |
Беспарафинистые |
До 12 мас. % |
|
|
Фракционный состав |
Ф1 |
Облегченного состава |
80 мас. % выкипает |
||
|
|
|
при |
температуре |
|
|
|
|
до 250 °С |
|
|
|
Ф2 |
Промежуточного соста- |
Полностью |
выки- |
|
|
|
ва |
пает |
при темпера- |
|
|
|
|
туре 250–320 °С |
||
|
|
|
|
||
|
Ф3 |
Тяжелые |
Выкипают при тем- |
||
|
|
|
пературе |
свыше |
|
|
|
|
320 °С |
|
|
|
|
|
|
|
|
Газовые конденсаты стабилизируют одним из двух методов – ступенчатой дегазацией или ректификацией в стабилизационных ко- лоннах. Стабилизация конденсатов ступенчатой дегазацией характер- на для промыслов, где стабильный конденсат хранится в атмосфер-
156

ных резервуарах и подается затем на переработку на НПЗ. Однако схема ступенчатой дегазации не позволяет обеспечить высокую чет- кость разделения. Для исключения потерь ценных компонентов более широкое применение получили методы «закрытой» стабилизации в ректификационных колоннах.
Современные установки стабилизации газовых конденсатов рек- тификацией включают две колонны: абсорбционно-отпарную и ста- билизационную (рис. 4.10).
Согласно схеме газовый конденсат I из сепаратора установки НТС через дроссель 6 поступает в предварительный сепаратор 1, от- куда обе фазы (газовая и жидкая) после рекуператорного нагрева го- рячим потоком стабильного конденсата поступают в абсорбционно- отпарную колонну 2. Давление в этой колонне 2,0–2,5 МПа, темпера- тура на верху колонны 15–20 °С, в низу – 170–180 °С. С верху колонны
Рис. 4.10. Схема стабилизации газового конденсата ректификацией: 1 – предварительныйсепаратор; 2 – абсорбционно-отпарная колонна; 3 – стабилизационная колонна; 4 – печи; 5 – теплообменник;
6 – дроссели; 7 – холодильник.
I – нестабильный конденсат; II – газ стабилизации; III – ШФЛУ;
IV – стабильный конденсат
157
отбирается сухой газ (метан-этан). Деэтанизированный конденсат с низа колонны 2 через дроссель 6 вводится в стабилизационную ко- лонну 3, где путем ректификации от него отделяют ШФЛУ (пропан- пентановую фракцию), а с низа – стабильный газоконденсат. Давле- ние в этой колонне обычно 1,0–1,5 МПа, температура верха – 50– 75 °С, температура низа – 180–190 °С.
4.6. Извлечение гелия из природного газа
Гелий – редкий, с уникальными свойствами газ, обладающий при нормальных условиях плотностью 0,1609 кг/м3. Основное его количество получают из природных газов. Его запасы составляют примерно 56–60 млрд м3. Ежегодная его добыча в мире составляет около 1,2 млрд м3. Наиболее богаты этим газом США, Россия, Ал- жир, Канада, Польша, Голландия. В России это Оренбурское, Астра- ханское месторождения, Башкирия, Иркутская область, Якутия, Красноярский край.
Производство гелия в мире превышает его потребление пример- но на 80–85 %. Избыток гелия закачивают в сжиженном виде в хра- нилища.
Основные потребители гелия – предприятия военно- космических ведомств (до 50 %), его применяют в криогенной техни- ке, при проведении сварочных работ, в водолазном деле, в хромато- графии, как наполнитель дирижаблей.
Концентрация гелия в природных газах невелика и колеблется от 0,001 до 3,0 об. %. Промышленно рентабельной считается концен- трация гелия в газе 0,03–0,04 об. %. Чистый гелий из УГ обычно полу- чают в три стадии: 1) выделение гелиевого концентрата (80–90 % ге- лия); 2) его дальнейшее концентрирование (до 99,98 %); 3) сжижение для удобства транспортирования и хранения.
Получение гелиевого концентрата возможно четырьмя способа- ми: криогенным, абсорбционным, путем гидратообразования, диффу- зией через пористые мембраны. Из этих методов только криогенный получил промышленное применение.
158
Криогенный способ основан на охлаждении газа до температуры конденсации азота, при которой конденсируется и метан, а гелий ос- тается в газовой фазе.
Абсорбционный метод основан на использовании активных по- глотителей метана (ССl3F, ССl2F2 и др.). Их поглотительная способ- ность по метану в 10–20 раз выше, чем по гелию, а при понижении температуры это различие дополнительно возрастает.
Способ гидратообразования основан на том, что гелий не обра- зует с водой гидратов при низких температурах и высоких давлениях. Если в таких условиях создать контакт воды и газа в соотноше- нии 20–100 : 1, то почти все компоненты газа дадут гидраты, а из кон- тактора выйдет гелиевый концентрат. Недостаток метода – использо- вание больших количеств воды и необходимость осушки гелиевого концентрата.
Мембранный способ основан на высокой проникающей способ- ности гелия по сравнению с другими газами и его способностью се- лективно проникать через очень мелкие поры различных материалов, выполненных в виде тонких пленок – мембран.
Глубокую очистку гелиевого концентрата ведут с использовани- ем глубокого охлаждения. Из гелиевого концентрата удаляют приме- си водорода, азота, метана. Обогащение включает 4 стадии:
–очистку концентрата от примесей водорода каталитическим гидрированием;
–глубокую очистку от влаги, образующейся при гидрировании, адсорбцией на Al2O3;
–сжатие до 15–20 МПа и охлаждение до –207 °С с последую- щим дросселированием концентрата и его сепарацией в 1 или 2 ступени (после данной стадии газовая фаза содержит 99,5 % гелия);
–адсорбционная доочистка концентрированного гелия актив- ным углем, охлаждаемым жидким азотом, с получением гелия с чистотой 99,98 %.
159
Для перевода газообразного гелия в жидкое состояние газ охла- ждают жидким азотом, направляют в турбодетандер, далее – в паро- жидкостный турбодетандер (или дросселируют). После этих процес- сов часть гелия переходит в жидкую фазу, которую затем доочищают адсорбцией и разливают в сосуды Дьюара, в которых гелий транспор- тируется потребителю.
Для хранения жидкого гелия используют криогенные хранили- ща. В мире существует 10 таких хранилищ вместимостью по 120 м3.
4.7. Транспортирование и хранение углеводородных газов
Транспортировка газа осуществляется, главным образом по трубопроводам (газопроводам) от мест его добычи и промысловой подготовки к потребителям.
Сжиженные газы транспортируются в специальных цистернах по железным дорогам или автомобилями. Существуют также специ- альные танкеры для перевозки сжиженных газов морским путем.
Для нашей страны (с учетом больших расстояний) в основном применяется трубопроводный и железнодорожный транспорт.
При транспортировке газа по трубопроводам обязательно дол- жен выполняться ряд условий:
–давление в трубопроводах не должно быть ниже давления на- сыщенных паров (для предотвращения образования газовых пробок);
–газ должен быть осушен (чтобы избежать образования гидра- тов);
–необходимо использовать буферные смеси при перемене про- качиваемых по трубопроводу продуктов (для исключения за-
грязнения новых продуктов).
Магистральные газопроводы имеют большую протяженность (3–5 тыс. км) и составляют важную энергетическую сеть любой стра- ны. Строятся они из труб диаметром до 1,4 м, рассчитанных на давле- ние до 10 МПа, и имеют пропускную способность до 30 млрд м3/год.
160