
книги / Структурно-механические свойства эластомерных композитных материалов
..pdf
mulation of vacuoles around delaminated filler particles during tensile strain of the sample:
d V/V0dε = f(ε).
Oberth conducted careful study of 3D cross-linked polyurethane filled with glass beads of different fractional composition under tension using the photoelastic method and dilatometry [7]. He showed that before reaching of fracture stress of elastic binder, the main load on a composite will be taken by hard (high modulus) filler particle. The mechanism of this total fracture depending on the physicochemical properties of the components may include a step of violation of adhesion at the filler – elastomer interface. Applying a high hydrostatic pressure suppresses in the sample the delamination process of the filler particles from the polymer binder under tension and therefore retains its volume. A similar result was obtained in the Sakovich’s study of structural and mechanical behavior of the 3D cross-linked of polyisoprene and butyl rubber fi lled with ammonium perchlorate plasticized with a transformer oil [8].
Information search revealed that there are no published data on the use of numerical methods for predicting the dependence of stress –tensile strain of filled elastomers in view of the internal fracture. Up to now no equation for calculating the energy of the mechanical fracture of the filled elastomers based on their basic composition parameters was derived. The purpose of the study was development (using a computer program [9]) of a technique for the numerical simulation of the mechanical fracture of the 3D cross-linked elastomer filled with hard particles,
ch r1/3RT 1 29exp 0,225 10 3 (T Tg )2 1a 1
|
|
/ |
|
n |
|
1 |
|
|
2 |
(1) |
||
|
|
m |
1 |
|
|
exp( 0,5ti2 )dti |
|
( 2 ), |
||||
1 |
1,25 |
|
|
|
i |
|||||||
1 / m |
2 |
|||||||||||
|
|
i 1 |
|
|
|
|
|
|||||
|
|
|
|
|
|
|
1 |
|
|
as well as derivation of an equation for calculating the energy of mechanical fracture of fi lled elastomers under uniaxial tension in view of the main parameters of the composition. Results of the studies carried out in both cases were obtained based on solving the problem of a multiple increase in the service life of roads in Russia through the development and use of a material for an expansion joint and waterproofi ng and frost asphalt coverage preserving elastic properties over a wide temperature range.
101
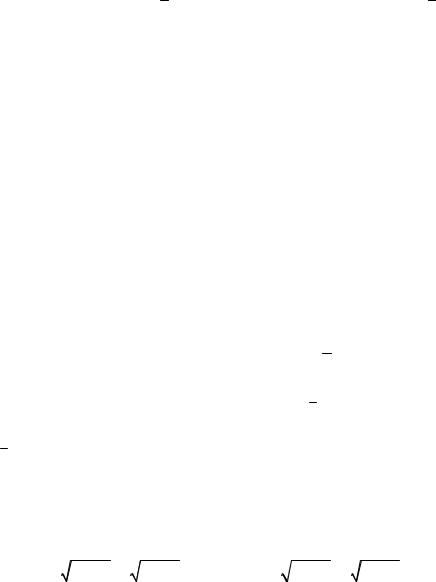
NUMERICAL SIMULATION OF MECHANICAL FRACTURE
A numerical experiment on mechanical fracture in view of the possible delamination of the polymer binder from fi ller particles in stretching of the sample is based on a description of its structural and mechanical behavior [1]. In this case, the dependence of relative (related to the initial cross section of the sample) stress σ on the elongation α associated with the strain ε by expression of α = 1 + ε/100% includes the following main structural parameters and
deformation conditions: vch / Ms , where ρ is density of the polymer, – Ms ,
an average internodal molecular weight of the polymer backbone of the binder; φr = 1 – φsw, volume fraction of the polymer in the binder; φsw, volume fraction of plasticizer in the matrix of the composite; R, universal gas constant; T∞, equilibrium temperature, at which the concentration of the “physical” (intermolecular) bonds νch tends to zero; Tg, glass transition temperature of the structural polymer binder; T, temperature of a sample test (numerical experiment); a 1, speed coeffi cient of stretching, a 1 1 for the standard rela-
tive strain rate , s 1 adopted in science and industry; φ, volume fraction of
filler; φm, limiting volume fraction of filler depended on the fractional composition and shape of particles, as well as the physicochemical interactions at the interface of filler–elastomer.
The general equation considering delaminated components has the form where the kinetics of accumulation of internal fracture of composite in the form delaminated polymer binder from the filler particles is described by a Gaussian function; n, a number of the volume fractions φi of delaminated
fractions (species) of the particulate filler; ti ( 0,5i ) / si function param-
eter; α0.5i, elongation of the sample corresponding to half of the volume of delaminated particles of ith fraction (species) of the filler, si i, rms dispersion for
the ith fraction (species) of the filler.Parameter α0.5i determines onset of delaminating, si characterizes the rate of the violations in integrity of the compo-
site. Ultimate mechanical characteristics of the σb, αb in the absence of interphase delaminations in the elastomeric composite can be estimated accounting for the velocity and magnitude of the average interlayer of the polymer binder between the solid particles of the filler:
|
f |
|
o |
(1 3 / ) 3 |
/ |
m |
; |
f o (1 3 |
/ |
m |
) 3 |
/ |
m |
, |
|
|
|
m |
|
|
b |
b |
|
|
|
|
102
where the indices “f” and “0” means fi lled and free state of elastomer, respectively. In terms of ultimate strains we obtain Parameter εb 0 is determined from
the graphical dependence εb. bo f ( eff ), previously derived by generaliza-
tion of the numerous experimental data [1]. The effective concentration of cross-links is the sum of the concentrations of the chemical bonds (defi ning the initial three-dimensional cross-linking of linear polymers) and physical bonds (intermolecular depending on the structure of the polymer and the test temperature):
eff ch r1/3 (1 ph ) ch r1/3 1 29exp 0,225 10 3 (T Tg )2 .
For example, when νeff = 1 × 10–5 mol/ cm–3 and T = 293 K breaking strain of 3D cross-linked elastomeric binder ( bo ) is about 1000%. Said graph-
ical relationship is also included in the computer program as the gauge [9]. In the case of violation of the sample integrity until it breaks the values at
“peak” for the cone-shaped diagrams of tension (σmax, εmax) or at the conventional “peak” ofthe diagram, which guarantees the usability of composite par-
tially destroyed, are taken as limiting mechanical characteristics despite the possible continued stretching of the sample. For quantifying estimate changes in energy (work) of mechanical degradation
b |
|
Ab ( )d , |
(2) |
0 |
|
determining the service life of the filled elastomer depending on the degree of interfacial delamination the envelopes of points of discontinuity of samples in the absence of delamination (σb, εb) or points specifi ed above as “peak” (σmax, εmax) were used, which were proposed by Smith as dependencies log σb,max – log εb,max [10, 11].
ENGINEERING EXAMPLE OF NUMERICAL SIMULATION
In accordance with “windows” for the input data of a computer program [9] for the numerical experiment on mechanical degradation the following physico-chemical properties and structural performance of the modelbased compositions were used based on 3D cross-linked elastomer. Poly(diene epoxy ester uretane) of the PDI-3B grade with terminal epoxy groups and polybutadiene of the SKD-KTP grade carboxyl-terminated are used as the initial low molecular weight rubbers of linear structure. Their 3D cross-linking
103
was carried out using threefunctional epoxy resin (EET-1 grade). Polymeric binder contained plasticizer dibutyl phthalate (φsw = 1 – φr = 0.3). The effective concentration of cross-linking in the binder was assumed equal to 1 × 10–5 mol /cm3. Particulate filler, silica (quartz), in the form of an optimal mixture of three fractions of different average particle size: 600 : 30 : 1 = 0.68 : 0.24 : 0.08 (μm : volume feaction), a total amount of which was assumed equal to unit. Values of φmi for each of the fractions were 0.640, 0.614, 0.535, respectively, which were used in the calculation of φm using the combinatorial multiplicative method as the most accurate [12]. The optimum ratio of the fractions was calculated by the highest packing density of the mixture in the initial bulky form [13] taking into account the physicochemical effect of the polymer binder [14]. Silica filler volume fraction was equal to 0.65, the limiting degree of fi lling volume was 0.93. Structural glass transition temperature of the binder components, as well as the value of the universal gas constant, were taken from the data and taken into account in calculating the value of Tg of the polymer binder composite. A value of the equilibrium temperature was calculated by the formula T∞ = Tg + 200° [15]. Standard relative strain rate ( = 1.2 × 10–3 s–1) corresponded a value assumed in rezin branche of industry. The following temperatures were preset in the numerical simulation experiments (K): 223, 273, 293, 323. Calculated strain diagrams were plotted using 3% step of strain. For constructing the tension diagrams the effect of possible delamination of the particulate fi ller of the polymer binder was determined by the method of numerical simulation under conditions of insuffi cient adhesion at the coarse fraction–elastomer boundary. Table 1 shows the values of the parameters of the Gaussian function for the coarse fraction (600 μm). The tension diagrams at 100% adhesion to the binder for all factions of the composites at all temperatures tested were also taken into account. In the process of numerical simulation the following degrees of delamination of the fi ller particles of the polymer binder (as a percentage of the volume fraction of the coarse fraction in a mixture of filler) were preset: 20, 40, 60, 80, 100. Since the volume fraction of the coarse fraction of silica in the composite was 0.68 × 0.65 = 0.442, we can assume that thereby 0.0884, 0.1768, 0.2652, 0.3536, 0.4420 of volume fraction of the filler, respectively, were fractured.
Figure 1a–1d shows the calculated tension diagrams of the 3D crosslinked plasticized elastomer filledwith silica. It is evident that a bundle of curves with delaminated coarse fraction of 20–100% of its original amount shows up regardless of the temperature of a numerical experiment. This demonstrates that even the emergence of internal fracture of the composite at the filler–elastomer
104

interface leads to a sharp fall in the service life of the material. Stipulated above conditional values of acceptable limiting mechanical characteristics (σmax, εmax), including the initial case (σb, εb at the zero delamination of the coarse fraction of particles) are connected by straight lines. It is also noteworthy that the tendency to “cone-shaped” tension diagrams is observed in samples with a low degree of violation of the composite integrity. It is apparently due to a prevailing load resistance of a remained fi lled subsystem, which includes a more amount of particles of mean and fi ne fractions of signifi cantly greater specifi c surface area of attaching (adhesion) to the polymer binder.
Table 1. Parameters of delamination of the coarse fractui (600 μm) of silicium dioxide from the binder
Temperature of an experience |
Value of elongation |
RMS dispersion, |
s |
at simulation, K |
half-period α0.5 |
|
|
223 |
1,140 |
0,250 |
|
273 |
1,285 |
0,500 |
|
293 |
1,375 |
0,625 |
|
323 |
1,505 |
0,833 |
|
Figure 2 contains envelopes of fracture points in the tension diagrams of samples without delamination (σb, εb) and samples with varying degrees of delamination of the coarse fraction from the polymer binder (σmax, εmax). Conditional allowable values of stresses and strains in the samples until their complete degradation with a break into two parts are denoted by the subscript “max”. The data show that in the case of moving along perpendicular straights from the source (0% delamination of the coarse fraction of particles) to subsequent (20–100% delaminated particles of coarse fraction) the fracture energy of samples characterized by an area under the relevant sections of the tension diagrams is repeatedly reduced. For example, in full delamination of the coarse fraction of the mechanical fracture energy is reduced about 10 times. The results of the numerical experiment were used to reduce the amount of experiments in developing of material for a movement joint and a waterproofi ng frostresistant coating of asphalt with a view to improving the service life of roads [16]. Note also that scientifi c and technical directions in solving the problem of providing reliable adhesion of components to each other exist including the formation of chemical bonds at the fi ller binder boundary. In particular, with respect to the silica and elastomer binder silicon compound with a functionally active groups relative to functional groups in the original low molecular weight rubbers were high effective coupling agents [17].
105
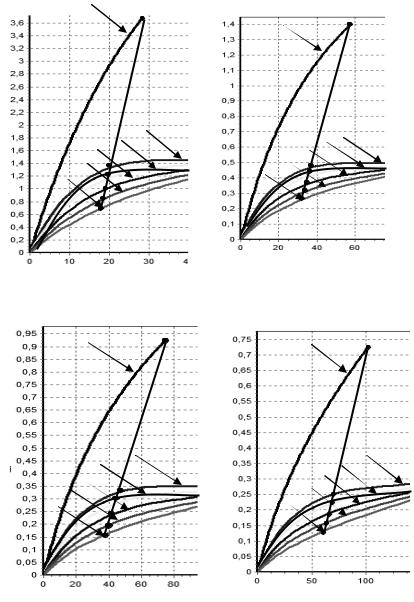
1
|
|
|
|
1 |
|
σ |
|
|
|
|
|
|
|
σ |
|
|
|
3 |
2 |
|
|
|
2 |
|
|
|
4 |
3 |
|
5 4 |
|
|
5 |
||
|
6 |
|
|||
6 |
|
|
|
|
|
|
|
|
|
|
|
ε, % |
ε,% |
|
|
|
|
a |
b |
σ |
1 |
1 |
|
σ |
|
|
|
|
|
2 |
|
2 |
4 |
3 |
|
4 |
3 |
5 |
|
|
5 |
|
|
|
6 |
|
|
6 |
|
|
|
c ε, % |
ε, % |
d |
Fig. 1. Calculated tension diagrams of 3D cross-linked filled elastomer with various degrees of delamination of the silica coarse fraction. (σ) Stress (MPa), (ε) strain (%). Degree of delamination (%): (1) 0, (2) 20, (3) 40, (4) 60, (5) 80, (6) 100; the same for Fig. 2. Temperature of experiment (K): (a) 223, (b) 273 (c) 293, (d) 323
106
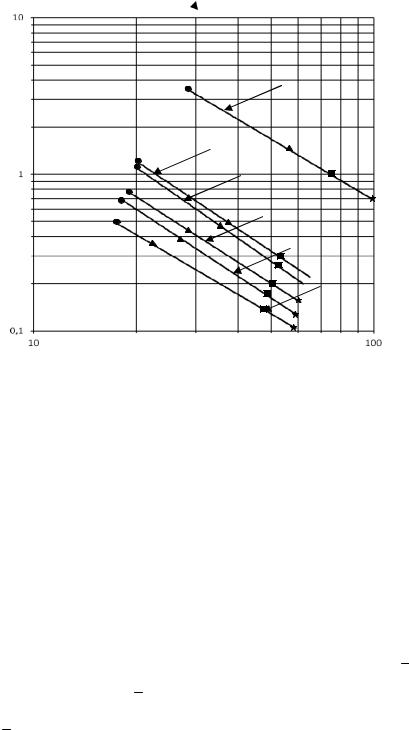
σb, max |
1 |
|
2
3
4
5
6
εb, max
Fig. 2. Calculated envelopes of fracture points and conditionally allowable stresses
and strains σb,max (MPa) = f[εb,max (%)] in logarithmic coordinates for on 3D crosslinked filled elastomer at different degrees of delamination of the coarse fraction
of silica. Temperature of experiment (K): (I) 323, (II) 293, (III) 273, IV 223
DERIVATION OF THE EQUATION FOR CALCULATING THE MECHANICAL FRACTURE ENERGY OF ELASTOMER
Let us explore an option of maintaining the continuity of the polymer composite material until the sample breaks that is of the greatest practical interest for improving its service life in such operational conditions as, e.g., roads (Poisson’s ratio → 0.5). Let us calculate an integral (2) substituting in it
the values of equation (1) therewith bearing in mind that in νch = /Mc the value of structural parameter Mc – is assessed using a molecular graph [1]:
[ Mc ] = [–(f32)2–R3–f32–R2–f21–(R1–f12–R2)n – f23–R3–(f32)2–]∞,
107

where R1 and R2 are molecular chain of two rubbers with two terminal functional groups f1 and f2; R3 is a cross-linker molecule with three functional groups f3; combination of subscripts at f correspond to the reaction products of i th and j th antipode terminal functional groups of bifunctional polymers of R1 and R2 types and also of a trifunctional cross-linking agent of R3 type.
Given that usually R3 << R1 and R2 it can be assumed that the value of Mc
is proportional to the increment of a mole fraction of linear polymerization –(–R1–f12–R2–)n in accordance with the above-mentioned molecular graph.
The value of φm can be calculated [12, 18] or determined by a viscometric method [14, 19]. Elongation α is related to strain ε by known relation α = 1 + ε/100%. In the case of maintaining the continuity of the material a true stress σver is the product σα, but in practice it is more convenient to use conditional stress for comparison with the results of investigation of composites, in which continuity is violated prior to a time the sample break [1]. On the basis of relations (1) and (2 ) the following ratio can be written
|
b |
|
bb |
|
|
|
|
|
|
|
|
|
|
|
|
|
|
|
|
|
|
|
|
|
W |
|
( )d |
|
|
|
1/3 |
RT |
|
|
|
|
0,225 10 |
3 |
(T T ) |
2 |
a |
1 |
1 |
|
|||||
|
|
|
1 29exp |
|
|
|
|
|
|
|||||||||||||||
|
|
|
ch r |
|
|
|
|
|
g |
|
|
|
|
|
||||||||||
|
1 |
|
1 |
|
|
|
|
|
|
|
|
|
|
|
|
|
|
|
|
|
|
|
|
(3) |
|
|
|
|
|
|
|
|
|
|
/ m |
2 |
|
|
|
|
|
|
|
|
|
|
|||
|
|
|
|
|
|
|
|
|
|
|
|
|
|
|
|
|
|
|
|
|||||
|
|
|
|
1 |
1,25 |
|
|
|
( 2 )d , |
|
|
|
|
|
|
|
|
|
||||||
|
|
|
|
|
|
|
|
|
|
|
|
|
|
|
|
|||||||||
|
|
|
|
|
|
|
|
1 |
/ m |
|
|
|
|
|
|
|
|
|
|
|
|
where W is the mechanical fracture energy at the uniaxial tension with dimension of MPa × elongation, mm, = 1 × 103 J.
The extension degree is the equivalent of resistance time of the polymer composite to growing tensile stress.
Assuming that W, σ are variables and denoting a combination of the remaining of alphabetic characters and digits by constants C1 and C2 from the Eq. (3), we obtain
|
|
/ m |
|
|
|
2 |
|
|
||||
C |
1/3RT |
1 1,25 |
|
|
; |
|
||||||
|
|
|
|
|
|
|
||||||
1 |
ch r |
|
|
|
1 / m |
|
|
|
|
|
|
|
|
|
|
|
|
|
|
|
|
|
|
||
|
|
0,225 10 |
3 |
(T Tg ) |
2 |
|
1 |
, |
||||
C2 29exp |
|
|
a |
|||||||||
that allows to write Eq. (3) in a compact form: |
|
|
|
|
|
|
|
|||||
|
b |
|
|
|
|
|
|
|
|
|
|
|
W C1(1 C2 1)( 2 )d . |
|
(4) |
||||||||||
|
1 |
|
|
|
|
|
|
|
|
|
|
|
108

Equation (4) is solved by the table of main integrals [18]:
b |
b |
b |
b |
W C1 d C1C2d C1 2d C1C2 3d ; |
|||
1 |
1 |
1 |
1 |
As a result of integration and algebraic transformations it can be written
W C1 |
|
3 |
3 |
b |
2 |
|
C1C2 |
|
2 3 |
3 2 |
1 |
|
(5) |
||
|
b |
|
|
|
|
b |
|
b |
|
|
|
||||
|
2 b |
|
|
2 |
|
|
|
||||||||
|
|
|
|
|
|
|
|
2 b |
|
|
|
|
|
from which in view of the notation in Eq. (4) the required dependence of mechanical fracture energy of the filled elastomer on its main structural parameters is derived:
|
|
|
|
|
|
|
|
|
|
|
|
m |
|
|
2 |
|
|
3 |
3 b |
|
2 |
|
|
||||
|
|
|
1 |
|
|
|
|
|
|
|
|
|
|
|
|
|
|
||||||||||
W |
|
|
|
3 RT |
1 |
1,25 |
|
|
|
|
|
|
|
b |
|
29exp |
|||||||||||
ch |
r |
|
|
|
|
|
|
|
|
|
|
||||||||||||||||
|
|
|
|
|
|
|
|
|
|
|
|
|
2 b |
|
|
|
|
||||||||||
|
|
|
|
|
|
|
|
|
1 |
|
|
|
|
|
|
|
|
|
|
|
|||||||
|
|
|
|
|
|
|
|
|
|
|
|
|
|
|
|
|
|
|
|
|
|
|
|
(6) |
|||
|
|
|
|
|
|
|
|
|
|
|
|
|
m |
|
|
|
|
|
|
|
|
|
|
||||
|
|
|
|
|
|
|
3 |
|
|
|
|
|
2 |
|
1 |
|
|
3 |
|
|
2 |
1 |
|
||||
|
|
|
0,225 |
10 |
T |
Tg |
|
|
2 b |
3 b |
|
||||||||||||||||
|
|
|
|
|
a |
|
|
2 |
2 |
|
|
|
|
||||||||||||||
|
|
|
|
|
|
|
|
|
|
|
|
|
|
|
|
|
|
|
b |
|
|
|
|
||||
|
|
|
|
|
|
|
|
|
|
|
|
|
|
|
|
|
|
|
|
|
|
|
|
|
Fracture energy W is equal to zero when αb = 1 that indicates its normability.
The limiting values for elongation αb as well as for strain εb can be estimated accounting for the velocity and magnitude of strain of average interlay-
er of the polymer binder between the solid particles of the filler [1]: |
|
|||||||
a |
f |
a |
(1 3 / |
m |
) 3 / |
m |
; |
|
|
0 |
|
|
|
|
|||
bf |
b0 (1 3 / m ) 3 / m ; |
(7) |
bf b0 (1 3 / m ),
where the indices “f” and “0” are related to fi lled and free states of the 3D cross-linked polymeric binder.
109
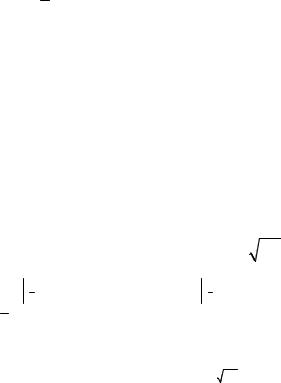
ULTIMATE ELONGATION AND FRACTURE ENERGY
For engineering use Eq. (6) in developing of new composites based on the 3D cross-linked elastomers, in particular the movement joint material and waterproofi ng frost-resistant coating of asphalt roads [16], it is necessary to know the value of the maximum tensile elongation or strain of the polymer binder.
As follows from the dependence (1) b0 or b0 values are determined by
the volume fraction of polymer in plasticized binder φr, effective concentration of crosslinks νeff, consisting of constant chemical cross-links νch and variable physical (intermolecular) bonds νph. Therewith latter determine the temperature dependence of mechanical properties.
Parameters of molecular structure, including the average internodal molecular weight Mc , of 3D crosslinked systems based on low molecular weight
polymers with terminal functional groups were theoretically evaluated in [19]. However, the authors did not account for intermolecular interaction, which similar to the mechanical properties, as it was noted above, depend on many factors [15, 20, 21]. Therefore, experimental data obtained previously in [1] were summarized below for use in engineering practice of determining the tensile strain of the free polymeric binder depending on the value νeff.
It turned out that the nonlinear experimental dependence bo (%) = = f ( eff ) for various polymeric binders built on a logarithmic scale [1] is linearized in the coordinates
log 0 |
log 0 |
|
|
|
C |
eff |
, |
(8) |
b |
b |
Mc |
|
|
|
where log b0 Mc 3,1 corresponds b0 Mc c 1250 % coeffi cient C = 40,
eff d / Mc 1 in accordance with Eq. (7).
After algebraic transformations we obtain an empirical relationship
bo 103,1 40 |
eff . |
(9) |
Figure 3 shows the generalized dependence of the tensile strain of various polymer binders (in logarithmic scale) on the square root of the effective concentration of cross-links (a linear scale). The 3D cross-linked elastomers of viscous liquid low molecular weight rubbers with terminal functional groups
110