
Аэрокосмическая техника высокие технологии и инновации – 2016
..pdfщей уровень кинетической энергии Эо, введем следующие допущения:
–твердостьчастицыбольшетвердостиматериалаповерхности;
–шероховатость частицы отсутствует;
–глубина внедрения частицы много меньше радиуса кривизны поверхности в точке контакта, но больше высоты ее микронеровностей;
–внедрение частицы происходит по нормали к поверхности. Модель изменения пористости по глубине пластической де-
формации hпл поверхностного слоя детали можно представить
вследующем виде:
–в исходном состоянии структура материала представлена
ввиде частиц, близких к сферической форме, соединенных между собой «мостиками» межчастичного контакта, образованными
врезультате спекания материала. Относительная плотность такого материала будет характеризоваться отношением объема твердой части системы спекшихся частиц Vт.ф к общему объему сис-
темы V : |
ν |
Vт.ф |
, а его пористость выразится как 1 ; |
|
|||
o |
|
Vo |
|
|
|
|
– при взаимодействии частиц обрабатывающей среды с поверхностью образуются следы в виде лунок (отпечатков), которые, покрывая всю поверхность, создают напряженно-деформи- рованное состояние по толщине. При полном укрытии поверхности отпечатками можно предположить, что сжатие всех слоев по толщине в среднем будет соответствовать деформации осевого сжатия под одним отпечатком.
Наши исследования показывают, что глубина пластической деформации при вибрационной обработке захватывает всего несколько слоев частиц приповерхностного слоя. Без большого ущерба для точности глубину зоны пластической деформации можно принять hпл kпл аП , где kпл – коэффициент, находя-
щийся в интервале от 1 до 3; аП – средний размер частиц исход-
ного порошка спеченного материала.
Исходя из полного покрытия отпечатками диаметром d всей поверхности, а также убывания степени деформации частиц порошка и заполнения пор по мере удаления от поверхности в глубину материала, при постоянстве объема твердой части системы
131

Vт.ф получена зависимость изменения пористости поверхностно-
го слоя в условиях линейного убывания концентрации твердой части системы, выдавленной из объема восстановленной лунки.
|
|
|
2h |
1 1 |
x |
|
, |
(1) |
0 |
|
|
|
|||||
|
|
h |
|
h |
|
|
||
|
|
|
|
|
|
|
||
|
|
|
пл |
пл |
|
|
где х – расстояние деформированного слоя с измененной пористостью от поверхности; h – глубина восстановленного отпечатка,
h |
d 2 |
; D1 – двойнойрадиускривизнывосстановленнойлунки[3]: |
||||||||
4D |
||||||||||
|
|
|
|
|
|
|
|
|
||
|
1 |
|
|
|
|
|
|
|
|
|
|
|
1 |
|
1 |
|
7,5 1 2 |
S , |
(2) |
||
|
|
|
D1 |
D |
d E |
|||||
|
|
|
|
|
|
|
где μ, Е, σs – коэффициент Пуассона, модуль упругости и предел текучести спеченного материала.
Принимая по [4] s sk 1 m , где σsk – предел текуче-
сти компактного материала; m – эмпирический коэффициент [4], получили зависимость величины диаметра пластического отпечатка:
|
|
3 |
Kу |
2 |
|
|
|
|
3Эo D 1 |
8 |
|
|
|
||
d 4 |
|
|
|
|
, |
(3) |
|
sk 1 m |
|
|
|||||
|
|
|
|
|
где K у – коэффициент восстановления при ударе.
Таким образом, зависимости (1)–(3) позволяют рассчитать необходимый уровень кинетической энергии частиц обрабатывающей среды, формирующий требуемую пористость поверхностного слоя деталей из порошковых материалов, и аналитически обосновать силовые (амплитудно-частотные) режимы вибрационной обработки.
Это расширяет возможности применения в авиационной промышленности как самих деталей порошковой металлургии, так и технологий вибрационной обработки.
132
Список литературы
1.Металлические порошки и порошковые материалы: справочник / Б.Н. Бабич, Е.В. Вершинина, В.Г. Люлько [и др.]; отв. ред. проф. Ю.В. Левинский. – М.: ЭКОМЕТ, 2005. – 520 с.
2.Бабичев А.П., Бабичев И.А. Основы вибрационной технологии. – Ростов н/Д: Изд-во ДГТУ, 1998. – 624 с.
3.Complex change in superficial layer properties of specimen obtained by metallurgical powder under vibration process method / H. Khaled, J.P. Ankudimov, T. Saeah, M.N. Benallal, A.P. Babichev // Defect and Diffusion Forum. – 2010. – Vol. 297–301.
4.Конструкционные порошковые материалы / И.Д. Радомысельский, Г.Г. Сердюк, Н.И. Щербань [и др.]. – Киев: Техника, 1985. – 152 с.
УДК 665.7.038.5
ПРИМЕНЕНИЕ АНТИКОРРОЗИОННЫХ ПРИСАДОК ПРИ СЖИГАНИИ ПОПУТНОГО НЕФТЯНОГО ГАЗА
О.О. Матюнин, Н.Ю. Бачева, Р.В. Бульбович, Н.Л. Бачев
Пермский национальный исследовательский политехнический университет, Пермь, Россия
matoleg@gmail.com
Для увеличения ресурса работы зарубежных газотурбинных установок (ГТУ) для утилизации попутных нефтяных газов (ПНГ) на малодебитных месторождения предлагается осуществлять впрыск антикоррозионных присадок в топливную магистраль ПНГ. Проведен информационно-аналитический обзор имеющихся присадок и выбраны наиболее подходящие из них. Осуществлены термохимические и термодинамические расчеты топливной пары влажный воздух + влажный ПНГ с антикоррозионными присадками и без них. Анализ полученных результатов показал, что включение присадок до 1 % от массового расхода ПНГ может снизить скорость коррозионного уноса до 98 % и уменьшить концентрацию коррозионно-активных веществ в составе продуктов сгорания на 10–15 %.
133
Ключевые слова: попутный нефтяной газ, утилизация, ресурс работы, антикоррозионные присадки, условная химическая формула, температура горения, состав продуктов сгорания.
На сегодняшний день отсутствуют отечественные газотурбинные установки (ГТУ) для утилизации попутных нефтяных газов (ПНГ) на малодебитных месторождениях. Нефтяные компании вынуждены закупать зарубежные установки типа C-65 или C-200 Capstone, камеры сгорания которых предназначены для сжигания топливных газов типа метана или пропана. При утилизации неподготовленных и разнородных по составу ПНГ в продуктах сгорания могут содержаться вредные и коррозионноактивные вещества типа NOx, CO, SOx, H2SO4, H2O и т.д. Для увеличения ресурса работы эксплуатируемых газотурбинных установок на малодебитных месторождениях предлагается вводить антикоррозионные присадки в магистраль подачи ПНГ.
Ингибиторы коррозии могут функционировать по одному из следующих механизмов [1]: как поверхностно-активные соединения с образованием на металле защитной пленки; как оказывающие нейтрализирующее действие на кислые агрессивные продукты, содержащиеся в топливе или образующиеся во время его горения; химически взаимодействующие с металлом с образованием защитной пленки на его поверхности.
Термодинамические и термохимические расчеты проведены с учетом влажности компонентов в реальных условиях эксплуатации. Влагосодержание [2]
d |
mп |
|
Pп |
|
Mп |
, |
|
m |
Р Р |
|
|||||
|
|
|
M |
сух |
|
||
|
сух |
|
п |
|
|
|
где mп, mсух – массы пара и сухого компонента в смеси соответственно; Mп, Mсух – молярные массы пара и сухого компонента соответственно; Рп, Рсух – парциальное давление пара и общее давление смеси.
Парциальное давление пара
Pп Ps
100
где φ – относительная влажность, %; Рs – давление насыщенных паров при температуре подачи.
134

Массовые доли сухого компонента и пара в составе влажной смеси
mсух 1 1d ,mп 1 dd .
Массовая доля i-го элемента (i = C, H, S, O, N, Ar, He) в смеси
mi mсух miсух mп miп,
где miсух , miп – массовые доли i-го элемента в сухом компонен-
те и паре соответственно.
Количество атомов i-го элемента в условной химической формуле
Zi gi Mсм .
Аi
Молярная масса смеси определялась по известному компонентному составу σVj
Mсм Vj M j .
j
С использованием указанного алгоритма определены услов-
ные химические формулы воздуха C0,0003H0,0202O0,4254N1,5459Ar0,0092
(относительная влажность φ = 60 %) и попутного нефтяного газа
C1,4072H4,0372O0,0272N0,7253He0,0001S0,0066 (относительная влажность
φ = 45 %).
Стехиометрическое соотношение между компонентами вычислялось по формуле
8 mCг 8 mHг mSг mOг
Km0 3 o 8 o o o
mO 3 mC 8 mH mS
и составило 10,6 при температуре подачи ПНГ Tвх = 165 °С (отсутствие в составе ПНГ конденсированной фазы).
Получены и проанализированы результаты термохимических и термодинамических расчетов горения с введением в со-
135
став ПНГ в количестве 1 % от его массового расхода следующих присадок: анилин, диэтиламин, триметиламин, хинолин, морфолин, циклогексиламин.
Работа выполнена в рамках гранта РФФИ № 16-48-590072 «Разработка энергоустановки для утилизации нефтяных газов на малодебитных месторождениях с выработкой электрической энергии».
Список литературы
1.Кулиев А.М. Химия и технология присадок к маслам и топливам. – Л.: Химия, 1985. – 312 с.
2.Поршаков Б.П., Бикчентай Р.Н., Романов Б.А. Термодинамика и теплопередача (в технологических процессах нефтяной
игазовой промышленности): учеб. для вузов – М.: Недра, 1987. – 349 с.
УДК 621.91.1
РАЗРАБОТКА СБОРНЫХ КОНСТРУКЦИЙ ПРОТЯЖНОГО ИНСТРУМЕТА ДЛЯ СКОРОСТНОГО ПРОТЯГИВАНИЯ ХВОСТОВИКОВ ЛОПАТОК КОМПРЕССОРА
ИЗ ТРУДНООБРАБАТЫВАЕМОГО МАТЕРИАЛА Г.Д. Петухов1, В.Ф. Макаров2
1АО «ОДК-ПМ»,
2Пермский национальный исследовательский политехнический университет, Пермь, Россия
el190980@yandex.ru, makarovv@pstu.ru
Проанализированы виды режущего инструмента при различной обработке. Охарактеризованы существующие протяжные инструменты, методы крепления сменных твердосплавных пластин. Произведено сравнение методов крепления пластин, отмечены их достоинства и недостатки. Выбран оптимальный метод крепления. Смоделирован узел крепления пластины. Рассчитано влияние режимов резания на усадку стружки различных сплавов. Рассмотрен метод уравновешивания сил реза-
136
ния при обработки детали одновременно по нескольким поверхностям путем изменения угла наклона режущей кромки. Разработан алгоритм технологии изготовления сборной конструкции протяжки.
Ключевые слова: протягивание, нагрузка, лопатка, действующая сила, режущая пластина, титан, жаропрочный сплав.
Всовременном машиностроении процесс протягивания является высокопроизводительным методом обработки металла резанием и получения высокого качества обрабатываемой поверхности. По трудоемкости протягивание превосходит такие виды обработки, как фрезерование и шлифование. Получаемая шероховатость Ra ≤ 1,25, допуск размера ∆ = 0,02 мм, отклонение прямолинейности по углу не более 5׳. Однако главной проблемой протягивания является применение протяжек из быстрорежущей стали и ограниченных скоростей резания V ≈ 1,5–2,0 м/мин.
Использование сборного режущего инструмента при механической обработке в промышленном производстве с каждым днем становится все актуальнее. Оно нашло широкое применение в таких видах промышленности, как автомобилестроение, судостроение, авиастроение, двигателестроение, приборостроение и т.д. Особенно гибко применяют сборный режущий инструмент в токарных, фрезерных, сверлильных, расточных работах. В нашей стране этим вопросом занимались такие ученые, как В.К. Перевозников, С.А. Васин, И.И. Семенченко, В.Ф. Бобров, В.И. Баранчиков, В.С. Самойлов, В.А. Фальковский, С.С. Четвериков, Д.М. Корытный, П.Г. Петруха, А.И. Марков, П.Д. Беспахотный и др. Очень далеко продвинулись в своих исследованиях такие зарубежный фирмы, как Sandvik Coromant, Mitsubishi, Walter, Iscar идр.
Анализ литературных данных показывает, что этому вопросу уделяется недостаточное внимание. Применяемые методы и разработанные методики весьма трудоемки. Некоторые исследователи рекомендуют при протягивании низкие скорости резания (до 3 м/мин) с использованием как быстрорежущих, так и твердосплавных протяжек.
Вто же время Н.И. Жигалко, Н.И. Ковзель, Н.Ф. Пронкин, В.И. Белашков, А.Е. Вишняков, В.Ф. Скиженок, П.Г. Кацев и др. рекомендуют для труднообрабатываемых материалов повышенные скорости (до 30–50 м/мин) протягивания как быстрорежу-
137
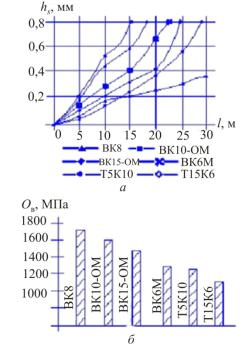
щими, так и твердосплавными протяжками. Анализ литературы по вопросу показал, что большинство работ выполняется в лабораторных условиях с использованием образцов обрабатываемых материалов, станков-стендов и носит рекомендательный характер, не учитывающий конкретные производственные и технические условия, размеры и конфигурацию обрабатываемых деталей, мощность и жесткость применяемого оборудования и т.д.
При выборе для режущих пластин оптимальной марки твердого сплава к напайным протяжкам проведены испытания твердых сплавов марок ВК6М, ВК8, ВК10-ОМ, Т5К10 и Т15К6 на величину износа, изгибную прочность, выкрашивание режущих кромок и интенсивность адгезионного взаимодействия с обрабатываемыми материалами [1].
Рис. 1. Результаты предварительных исследований износостойкости (а) и предела прочности (б) различных марок твердых сплавов
138
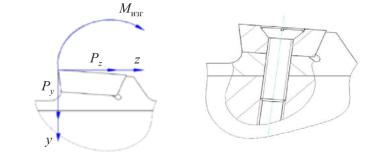
Моделирование нагрузок, действующих на режущие кромки протяжки. Геометрические параметры режущего инструмента оказывают существенное влияние на усилие резания, качество поверхности и износ инструмента. Так, с увеличением угла γ инструмент легче врезается в материал, снижаются силы резания, улучшается качество поверхности, но повышается износ инструмента. Наличие угла а снижает трение инструмента о поверхность резания, уменьшая его износ, но чрезмерное его увеличение ослабляет режущую кромку, способствуя ее разрушению при ударных нагрузках.
На рис. 2 рассмотрена схема распределения нагрузки на кромку режущей пластины. В данном случае сила действует в оси y, z и изгибающий момент Мизг..
Рассматривались схемы крепления винтом сверху, методом косой тяги, клиновое крепление, напайное крепление, крепление силами упругой деформации и др. Измерение величины давления производилось при помощи протарированной динамометрической скобы с индикаторной головкой. Измерение величины прогиба вершины резца осуществлялось при помощи индикаторной головки. По результатам испытаний наилучшие результаты показали образцы, методом крепления пластин которых были напайная конструкция и винт. Окончательно выбранная схема пластин к корпусу протяжки изображена на рис. 3.
Рис. 2. Распределение нагрузки |
Рис. 3. Схема крепления |
на кромку режущей пластины |
выбранных пластин для титана |
при протягивании |
и сталей с учетом действующих сил |
На рис. 3 представлен узел крепления твердосплавных многогранных пластин, оптимальный для действующих нагрузок на ре-
139
жущие кромки в процессе протягивания. В данном примере нагрузки компенсируются жесткими поверхностями корпуса протяжки, нагрузки на регулируемые или подвижные опоры отсутствуют. Крепление производится винтом сверху с утопающей головкой, что не препятствует движению протяжки, сходу стружки [2].
Выводы:
1.Применение протяжек из быстрорежущей стали ограничивает процесс протягивания максимальной скоростью резания
V = 1,5–2,0 м/мин.
2.Решением проблем современного протягивания является применение сборных протяжек со сменными твердосплавными пластинами.
3.В результате эксперимента найден оптимальный метод крепления твердосплавных пластин на протяжке.
4.Данное решение позволяет спроектировать и изготовить протяжки с обработкой замка одновременно с пяти сторон, что обеспечит экономию в сумме 2 млн руб. в год [3].
Список литературы
1.Макаров В.Ф. Выбор и назначение оптимальных условий протягивания заготовок из труднообрабатываемых материалов: учеб.-метод. пособие // Технология механообработки. – 2008. – 395 с.
2.Справочник технолога машиностроителя: в 2 т. Т. 2 / под ред. А.Г. Косиловой, Р.К. Мещерякова. – 4-е изд., перераб. и доп. – М.: Машиностроение, 1986. – 496 с.
3.Макаров В.Ф. Оптимизация протягивания труднообрабатываемых материалов: монография. – Старый Оскол: ТНТ, 2014. – 440 с.
140