
книги / Эксплуатация, техническое обслуживание и ремонт горных машин калийных рудников
..pdfбольшинстве случаев сотрудники сервисных служб и подрядных организаций не привлекаются к выполнению ремонтов. Указанный способ ремонта позволяет добычным предприятиям существенно снизить временные и материальные затраты на проведение технического обслуживания и текущего ремонта комбайнов (до семи раз, по сравнению с привлечением подрядных сервисных организаций), но обусловливает возникновение затруднений при проведении ремонтов сложных гидравлических систем, систем электроники, автоматики и прочих узлов и систем, требующих проведение ремонта высококвалифицированнымперсоналом.
Внедрение автоматизированных систем контроля параметров работы и диагностирования комбайновых комплексов значительно упростит работу инженерно-технических и ремонтных служб предприятия, позволит осуществлять ремонтно-восстановительные мероприятия по фактическому техническому состоянию комбайна, отказаться от затратной системы планово-предупредительных ремонтов. Накопление статистических данных об отказах и соответствующих им предельных значениях диагностических параметров обусловливает возможность прогнозирования времени выхода оборудования из строя с высокой степенью вероятности. Прогноз величины остаточного ресурса будет тем точнее, чем более стандартизированы условия эксплуатации и ремонта. Эффективный мониторинг технического состояния добычного оборудования, анализ данных о его надежности с использованием высокоточных прогнозных моделей обеспечивает равномерную и обоснованную загрузку ремонтногоперсонала, снижениеэксплуатационныхзатрат.
5.2.Эксплуатация и ремонт бункеров-перегружателей
5.2.1.Назначение, конструкция и принцип действия бункера-перегружателя самоходного БПС-25
Самоходный бункер-перегружатель БПС-25, грузоподъемностью 30 тонн, предназначен для аккумулирования горной массы, добываемой проходческо-очистными комбайнами, и после-
111
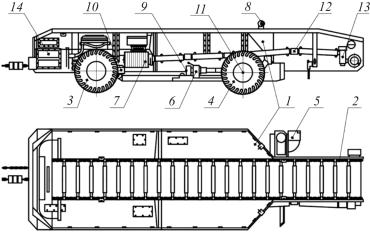
дующей перегрузки ее в самоходный вагон на рудниках и шахтах, опасных по газу (метану) и пыли. Возможность самостоятельного перемещения бункера предусмотрена для возможности его отгонки от комбайна при маневровых операциях.
Самоходный бункер-перегружатель БПС-25 (рис. 5.3) представляет собой бункер-кузов 1 со встроенным в его днище двухцепным скребковым конвейером 2.
Рис. 5.3. Схема самоходного бункера-перегружателя БПС-25: 1 – борт-кузов; 2 – скребковый конвейер; 3, 4 – пневмоколеса; 5 – станция управления; 6 – привод хода; 7 – привод конвейера; 8 – фары; 9 – тормоз; 10 – рулевая тяга; 11 – конический редуктор, встроенный в приводные колеса; 12 – карданная передача конвейера; 13 – планетарный редуктор конвейера;
14 – силовая станция
Кузов установлен на четырех пневмоколесах: два передних 3 – поворотных, не ведущих; два задних 4 – приводных, не поворотных. Станция управления 5 при этом находится в задней части машины и позволяет контролировать работу привода хода 6 и конвейера 7 бункера-перегружателя, фар 8 и тормозов 9.
Рулевое управление – ручное с гидроусилителем, на базе «гидроруля» через рулевую тягу 10. Привод ведущих колес –
112
гидравлический. Гидромотор передает вращающий момент колесам через редуктор, кардан, коническую передачу 11 и планетарный редуктор, встроенный в колесо. В конструкции БПС-25 предусмотрены нормально-замкнутые тормоза 9, а также устройства, отключающие редукторы для уменьшения сопротивления движения БПС-25 в режиме сцепки с комбайном.
Привод конвейера 7 – электродвигатель, установленный в средней части БПС, передающий вращение приводным звездочкам через цилиндрические редукторы, карданную передачу 12 и приводной вал с конической и планетарной передачей 13.
Силовая станция бункера-перегружателя 14 находится в передней части машины и запитывается со станции управления комбайна по двум кабелям 40 м, что позволяет отъезжать от комбайна на 30…35 м.
5.2.2.Особенности эксплуатации
иконтроля технического состояния самоходного бункера-перегружателя БПС-25
Бункер-перегружатель БПС-25 при работе в механизированном комбайновом комплексе должен иметь сцепку с комбайном. Самостоятельное перемещение БПС-25 производится при маневровых операциях со скоростью и преодолеваемым уклоном, представленными в технических характеристики БПС-25 в табл. 5.3. Страховочную сцепку с комбайном при отгоне отсоединяют только после включения привода хода бункера-перегружателя и его опробования. Тормоза должны удерживать БПС-25 от самопроизвольного движенияпримаксимальномпреодолеваемомуклонедо12°.
Узлы и детали бункера-перегружателя должны быть надежно закреплены, не допускается подтекание масла. Запрещается эксплуатация при отсутствии света, табличек на оболочках и нарушениях параметров взрывозащиты силовых агрегатов.
Кузова бункеров-перегружателей подвержены значительным нагрузкам, являются базовыми элементами и их ремонт в рамках применяемых мероприятий ТОиР не предусмотрен. Кузова под-
113
вержены интенсивному абразивному изнашиванию, в силу отсутствия негабаритных кусков калийной руды в результате комбайновой выемки аварийно, как правило, не выходят из строя. Процесс изнашивания днища и бортов кузова приводит к потере толщины металла, нарушению сплошности, однородности материала и, как следствие, появлению в них трещин и сквозных отверстий. В то же время по степени деградации состояния базовой детали можно судить о состоянии машины в целом, т.е. диагностика технического состояния базового элемента позволяет судить о величине остаточного ресурса горной машины.
|
|
Таблица 5.3 |
|
Технические характеристики БПС-25 |
|
||
|
|
|
|
Параметр |
Значение |
Единица |
|
измерения |
|||
|
|
||
Грузоподъемность |
30 |
т |
|
Скорость передвижения порожнего БПС |
0,9 |
км/ч |
|
Наибольший уклон, преодолеваемый |
12 |
град |
|
порожним БПС |
|||
|
|
||
Рабочее напряжение |
660 или 1140 |
В |
|
Габаритные размеры |
10,33 ×2,9×1,95 |
м |
|
(длина ×ширина × высота) |
|||
|
|
||
Высота разгрузки |
690…2150 |
мм |
|
Масса |
17,3 |
т |
|
Тип конвейера |
Скребковый |
– |
|
двухцепной |
|||
|
|
Для оценки состояния материала кузова бункера-перегружа- теля БПС-25 и определения скрытых дефектов целесообразно контролировать толщину материала кузова, а также проводить диагностирование методом возбуждения колебаний в отдельных участках кузова единичным ударом с последующим анализом отклика. Измерение толщины материала обеспечивает контроль за изнашиванием поверхностей кузова, оценка временных параметров движения волны возбужденных колебаний внутри объекта позволяет анализировать параметры среды, выявлять и локализовать зону возникновения дефекта.
114

Таким образом, обеспечивается комплексность оценки технического состояния базовой детали при сравнительно небольшой трудоемкости этих диагностических операций. На рис. 5.4 представлены точки контроля толщины листа кузова, а также места установки датчиков регистрации возбужденных колебаний.
Рис. 5.4. Схема установки датчиков на бортах и днище кузова бункера-перегружателя самоходного БПС-25
Указанный принцип реализуется комплектом приборов: ультразвуковым толщиномером «Булат-1М», компания ООО «Константа» (рис. 5.5, б), и многоканальным синхронным анализатором колебаний «Камертон» (рис. 5.5, а) с экспертным программным обеспечением анализа сигналов и определения дефектов, компания ООО «НПП «РОС».
В состав анализирующего комплекса «Камертон» входят пьезоакселерометрические датчики, предназначенные для измерения возбужденных колебаний, синхронный аналого-цифровой преобразователь для нормирования и первичного преобразования сигналов, анализатор на базе персонального компьютера, возбудитель колебаний.
Методика проведения контроля технического состояния с использованием многоканального анализатора «Камертон» преду-
115
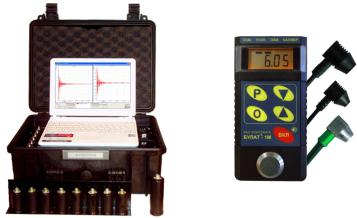
сматривает установку датчиков непосредственно на бортах и днище порожнего кузова бункера-перегружателя БПС-25 (см. рис. 5.4). Местаустановкидатчиковпредварительноочищаютсяветошью.
Единичные ударные возбуждения колебаний, регистрируемые датчиками анализатора «Камертон», осуществляются штатным инструментом прибора (молоточком), что позволяет исключить влияние на обследуемый объект переменной нагрузки, создаваемой весом импульсного источника колебаний. Методикой диагностирования предусмотрено проведение четырех циклов измерений подряд в каждой контрольной точке кузова (см. рис. 5.4) с сохранением в энергонезависимой памяти анализатора «Камертон» данных измерений сигналов возбуждения и отклика для дальнейшей их обработки. Сигнал возбуждения представляет собой плавно затухающие гармонические колебания, в которых отсутствуют резкие локальные выбросы, изломы, зашкаливания(рис. 5.6).
а |
б |
Рис. 5.5. Средства проведения диагностирования: а – многоканальный анализатор «Камертон»; б – ультразвуковой толщиномер «Булат-1М»
В однородной по плотности среде временные, скоростные и частотные параметры сигнала отклика идентичны параметрам сиг-
116

нала возбуждения. При наличии дефектов – трещин раковин, несплошностей, а также при аномалиях, обусловленных возникновением пороков, вызываемых процессом усталости металла, условия прохождения колебаний, вызванных идентичной импульсной нагрузкой, на различных участках объекта отличаются друг от друга. Анализ энергетических составляющих каждого зарегистрированного сигнала позволяет провести не только качественную, но и количественную оценку технического состояния объекта.
а |
б |
Рис. 5.6. Сигнал возбуждения (а), генерируемый бойком молоточка, и отклик (б), регистрируемый датчиком пьезоакселерометром диагностического комплекса «Камертон»
Обработка зарегистрированных прибором сигналов проводится при использовании экспертного программного обеспечения анализа сигналов и определения дефектов, реализующей анализ спектрального состава колебаний бортов и днища кузова бунке- ра-перегружателя БПС-25, осуществляющей расчет обобщенных параметров качества металлоконструкций.
Для каждого сигнала рассчитывается скорость затухания колебаний, ударная (несущая) частота, наличие отклонений ударной частоты от нормального для данного материала диапазона
117
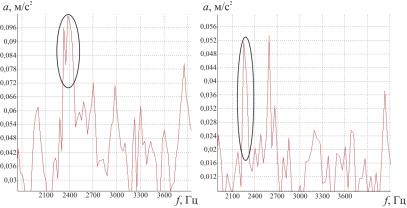
значений, проводится распознавание образа спектральной картины сигнала отклика.
Спектральный образ дефектов (рис. 5.7) в отдельных элементах металлоконструкций одинаков, что обусловливает возможность их выявленияиидентификациисвысокойдостоверностью.
а |
б |
Рис. 5.7. Примеры спектров сигнала-отклика, полученного при обследовании методом анализа возбужденных колебаний: а – наличие трещины в металле; б – дефект отсутствует
Далее обработка сигналов всех регистраций осуществлялась с использованием методов математической статистики. Экспертное программное обеспечение «Камертон» при определении критериев качества элемента использует следующие параметры:
–средняя несущая резонансная частота по всем имеющимся сигналам для элемента или соединения;
–средняя скорость затухания колебаний в элементе или соединении;
–взаимное отклонение частот в соединении и элементе;
–вероятность утонения стенок или снижения плотности, ослабления структуры металла элемента;
–вероятность наличия трещин, раковин, несплошностей в элементе или соединении.
118
Для интегральной оценки технического состояния элементов металлоконструкций определяется обобщенным условным коэффициентом качества k, вычисляемым на основе корреляции вышеперечисленных параметров. На основании анализа собранного статистического материала, результатов осмотров и оценочных расчетов предложена шкала качества, характеризующая степень риска или вероятность возникновения отказа. В диапазоне значений условного коэффициента качества k (0; 0,35] металл характеризуется недопустимым состоянием; при k (0,35; 0,65] состояние металла обозначают как тревожное; допустимым является состояние конструкцииприk (0,65; 0,8]; хорошеесостояние– k (0,8; 1].
Значения обобщенного условного коэффициента качества металла, полученные при диагностировании бортов и днища кузова бункера-перегружателя БПС-25 (эксплуатировался на руднике БКПРУ-4 ПАО «Уралкалий») комплексом «Камертон», приведены в табл. 5.4. Результаты замеров толщин металлоконструкций кузова того же бункера-перегружателя, выполненных с использованием толщиномера «Булат-1М», представлены в табл. 5.5. Исходная толщина листового металла бортов и днища кузова бункера БПС-25 составляет 10+1 мм.
Анализ результатов обследования показал, что наибольший износ днища кузова БПС-25 зафиксирован в зоне загрузки бункера рудой. Поток руды, поступающий со скребкового конвейера выемочного комбайна в кузов бункера, обусловливает интенсивный абразивный износ и формирование множественных усталостных микротрещин. Визуально в зоне загрузки на бортах и днище кузова зафиксировано образование «рельефа морского дна», что свидетельствует об ослаблении структуры металла. Наиболее существенная величина изнашивания бортов с образованием сквозных дефектов зафиксирован в сечении 3 кузова (см. рис. 5.4, точка 4.2 и табл. 5.5), что обусловлено наличием зоны с резким изменением формы поверхности (сужение кузова), подверженной интенсивному воздействию движущейся абразивной рудной массы.
119

Таблица 5.4
Значения обобщенного коэффициента качества k, определённые по результатам диагностирования кузова БПС-25 с использованием анализатора «Камертон»
Зона |
Место |
Коэф- |
|
|
установки |
фициент |
Состояние |
Примечание |
|
контроля |
датчика |
качества k |
|
Ослабление структуры |
|
a |
0,32 |
«Недопус- |
|
|
тимо» |
материала, трещины |
||
|
|
|
||
Борта |
b |
0,56 |
«Тревожно» |
Микротрещины |
|
|
|
Ослабление структуры |
|
кузова |
a' |
0,39 |
«Тревожно» |
|
|
|
|
|
материала, микротрещины |
|
b' |
0,47 |
«Тревожно» |
Ослабление структуры |
|
|
|
|
материала, микротрещины |
|
|
|
|
Множественные микро- |
|
A–B |
0,27 |
«Недопус- |
трещины; значительное |
|
тимо» |
ослабление структуры ма- |
||
|
|
|
||
|
|
|
|
териала |
Днище |
Централь- |
0,52 |
«Тревожно» |
Микротрещины; ослабле- |
кузова |
ная зона |
ние структуры материала |
||
(A–D; B–C) |
|
|
||
|
|
|
|
Незначительные микро- |
|
C–D |
0,68 |
«Допустимо» |
трещины; незначительное |
|
|
|
|
ослабление структуры ма- |
|
|
|
|
териала |
|
|
|
|
Таблица 5.5 |
Результаты толщинометрии бортов кузова бункера БПС-25 с использованием комплекса «Булат-1М»
Борта кузова |
|
Левый борт |
|
Правый борт |
|
|
Точка замера |
1.1 |
2.1 |
3.1 |
4.1 |
5.1 |
6.1 |
Толщина, мм |
7,0 |
6,5 |
6,3 |
6,4 |
6,8 |
7,4 |
Точка замера |
1.2 |
2.2 |
3.2 |
4.2 |
5.2 |
6.2 |
Толщина, мм |
9,0 |
8,5 |
7,0 |
5,5 |
7,1 |
7,9 |
|
|
|
Днище кузова |
|
|
|
Точка замера |
I.1 |
II.1 |
III.1 |
I.2 |
II.2 |
III.2 |
Толщина, мм |
6,3 |
6,4 |
6,4 |
7,0 |
7,0 |
7,6 |
Точка замера |
I.3 |
II.3 |
III.3 |
I.4 |
I.4 |
I.4 |
Толщина, мм |
7,8 |
8,1 |
8,4 |
9,6 |
9,6 |
9,5 |
120