
книги / Химия и технология баллиститных порохов, твердых ракетных и специальных топлив. Т. 2 Технология
.pdf1
Рис. 108. Вальцы завода «Большевик»:
1 — рабочий валок; 2 — холостой валок; 3 — редуктор; 4 — электродвигатель Габаритные размеры: длина — 10550 мм; ширина — 2890 мм; высота — 2100 мм
В новом процессе, как будет показано ниже, шнековые пресса выполняют практически все технологические операции фазы переработки, обеспечивая малую длительность техноло гического цикла и высокую безопасность процесса.
Отделение пороховой массы от воды после завершения ее «созревания» в непрерывном режиме представляло значитель ные трудности и потребовало длительных разработок различ ного рода конструкций и аппаратов, начиная от, так называе мой, сцежи — вращающегося перфорированного полотна — до шнекового пресса, совмещающегося в себя функции фильтрования и отжима.
Процесс удаления воды из любого материала может быть осуществлен двумя путями: механическим отделением (фильт рованием, центрифугированием, отжимом) и сушкой. При не большом содержании влаги, адгезионно связанной с материа лом, удаление возможно единственным способом — сушкой. С энергетической точки зрения наиболее оптимальным спосо бом является механическое отделение, причем, до адгезионно связанного предела. По мере снижения в материале содержа ния свободной влаги (не связанной адгезионно) возрастают сложности по ее удалению, а энергетические затраты увеличи ваются. На протяжении довольно длительного пути развития непрерывной технологии переработки операция отделения по роховой массы от воды была экспериментально исследована, и промышленное ее оформление усовершенствовалось в тече ние длительного времени. Ниже в разделе водоотжима даны физическая и математическая модели процесса и характери стика оборудования этой фазы.
Операция подсушки порохового полуфабриката после валь цевания была введена после исключения из технологического потока вторых вальцев, функция которых заключалась в до сушке массы до окончательной влажности. Высокий уровень диссипативной энергии при течении высоковязкой массы с низкой влажностью на вальцах приводил к частым загорани ям, что определило необходимость корректировки технологи ческого процесса с заменой вальцев на сушильный аппарат.
В конструктивном и технологическом плане применялись различные аппараты, но, в основном, барабанного и шнеково го типов. В зависимости от способа подачи теплоносителя (воздуха) барабанные сушилки были трех типов: с прямото ком, противотоком и поперечной продувкой. Сушилки этого типа отличались высокой пожароопасностью вследствие не-
222
достаточно эффективной противопожарной защиты (сложность подачи пожаротушащей жидкости внутрь сушилки). В этом отношении более безопасными являются шнек-транспортер- ные сушилки, в которых пороховой полуфабрикат рассредото чен, а сам аппарат защищен быстродействующей пожаротуша щей системой.
Однако оба типа аппаратов обладают существенным недос татком: технологический процесс сушки осуществляется мед ленно вследствие разнонаправленности двух действующих гра диентов — влагосодержания и температурного. Время сушки составляет от 40 до 90 минут, а загрузка аппарата полуфабри катом при его максимальной производительности составляет 500...750 кг, что при авариях может приводить к тяжелым по следствиям. Поэтому на протяжении длительного времени шел поиск путей сокращения времени сушки с одновременным резким снижением энергозатрат. Очевидно, это возможно только при увеличении скорости сушки за счет изменения на правления температурного градиента, т. е. совмещения его с направлением градиента влагосодержания. Возможные пути решения этой задачи — использование диссипативной энер гии, СВЧ-генераторов и переменного режима «нагрев — охла ждение» — были опробованы в реальных конструкциях. Су шилки с СВЧ-нагревом и типа КСВР были в эксперименталь ном порядке опробованы в опытном производстве, однако, по определенным причинам, о которых речь пойдет в разделе сушки, не нашли практического применения, и серийное про изводство осуществлялось по технологическим схемам с су шилками барабанного типа и шнек-транспортными.
Фаза формования — самая опасная по аварийным послед ствиям, — начиная со времени создания непрерывной техно логии (на базе шнековых прессов), подвергалась многочислен ным модернизациям, диктуемым необходимостью повышения безопасности работ и качества продукции.
Первые формующие пресса типа Ш-3 и Ш-4 (рис. 109, ПО), открывшие, по сути дела, эру непрерывной технологии переработки пороховой массы, имели конусные винт и втулку, обеспечивающие за счет уменьшения диаметров по ходу прес сования массы снижение объема канала, что приводит к сжа тию массы и сдвиговым деформациям вследствие обратного потока под действием противодавления и внешнего трения массы о поверхность винта. Сечение канала винта уменьшает ся от загрузочной к головной части пресса вследствие умень-
223
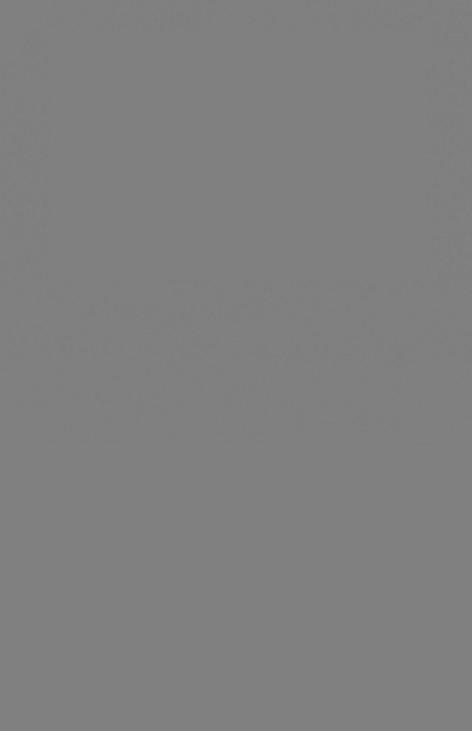

ской, а далее и непрерывной технологических схем. Исходя из целевого назначения, процесс заключается в удалении воды, придании массе заданной формы и спрессовыванию ее до плотности, близкой к теоретической (сумме аддитивных плот ностей компонентов). Казалось бы, процесс прост — удалили воду, высушили массу до окончательной влажности и спрессо вали ее в заданной форме при высоком давлении.
Однако первые же эксперименты по поиску оптимальной непрерывной технологии показали невозможность такого ре шения по следующим причинам:
— вследствие незавершенности процесса пластификации на фазе изготовления пороховой массы не обеспечивается од нородность спрессовываемой массы, наблюдаются белые вкра пления непропластифицированного полимера;
— двух параметров теплосилового поля (температура и давление) оказалось недостаточным для перестройки надмо лекулярной структуры полимерной системы. Необходимы сдвиговые деформации с разрывом межмакромолекулярных связей и рекомбинацией их в новом упорядоченном положе нии.
Таким образом, при поиске условий формования из полу ченной пороховой массы зарядов с требуемыми плотностью, прочностью и однородностью была выявлена необходимость, кроме удаления воды, организации такого режима течения по роховой массы, при котором четыре параметра «теплосилово го» поля — температура, давление, скорость сдвига и необра тимая деформация сдвига (как интеграл скоростей сдвига) — обеспечили бы завершение процесса пластификации, пере стройку структуры пластифицированной пороховой компози ции и необходимую прочность аутогезионного шва.
В процессе экспериментальных исследований и производ ственных испытаний нового оборудования была выработана определенная последовательность технологических операций: фильтрование — водоотжим — пластификация (вальцевание с одновременной сушкой) — досушка (на вальцах или специ альных сушилках) — гранулирование (таблетирование) — прессование на шнековых прессах с пресс-оснасткой в виде диффузорно-конфузорного раструбного пресс-инструмента.
Ниже рассматриваются результаты теоретических и экспе риментальных работ по каждой из фаз производства перера ботки, выполненных в 60 — 80-х гг. и завершившихся разра боткой нового технологического процесса переработки.
226
4.3.1 Отделение пороховой массы от воды. Водоотжимные шнековые пресса
4.3.1.1 Фильтрование суспензий пороховых масс
Ранее закономерности фильтрования суспензий баллиститных масс не исследовались, а параметры водоотасима на шне ковых прессах ШС-1, ШД и затем ПО-125 выбирались на ос нове эмпирических данных [122, 123].
Современные топлива, содержащие катализирующие систе мы в мелкодисперсном (почти коллоидном) состоянии, изме нили условия фильтрования:
—возросла связь дисперсной фазы с водой (иногда до коллоидного состояния);
—резко увеличилось сопротивление осадка вследствие за полнения пор частицами коллоидноизмельченного катализато ра (сажи, ФМС и т. д,).
Это потребовало проведения широких исследований про цесса фильтрования суспензий пороховых масс с определени ем оптимальных параметров как самого процесса, так и фильтровального аппарата.
Исследования базировались на основных закономерностях, рассмотренных в ряде работ [124, 125]. Учитывая особенности штатных и новых топлив, предполагалось, что в большинстве случаев имеет место фильтрование со сводообразованием осад ка на щелях фильтровальной перегородки. Однако для топлив, содержащих значительное количество тонкоизмельченных компонентов, недостаточно связанных с основой, более вероя тен механизм с закупориванием пор. Очевидно, с учетом это го механизма рамки исследования должны быть расширены.
В соответствии с законом Дарси скорость фильтрования
в дифференциальной форме может быть выражена: |
|
||
dV _ |
АР |
(4.35) |
|
Sdt |
p(i?0c 4'Дф.п.) |
||
|
где V — объем фильтрата, м3; S — поверхность фильтрования, м2; / — время фильтрования, с; АР — разность давлений, Па; ц — вязкость фильтрата, Па-с; Roc — сопротивление слоя осад
ка, |
м-1; |
ЛфП — сопротивление |
фильтровальной перегородки, |
||
м-1. |
|
|
|
|
(удельное сопротивление г0 |
Для |
несжимаемого |
осадка |
|||
по |
высоте |
не изменяется). Принимая постоянным отноше |
|||
ние |
между |
твердой и |
жидкой |
фазами (отношение объемов), |
227
1ж_ Vr*. _ |
Shpç |
М — модуль, hoc — высота осадка), сопротив- |
|||
V |
V |
’ |
|
|
|
ление осадка Д,с можно представить выражением: |
|
||||
|
|
|
|
V |
(4.36) |
|
|
^ос = го^ос ~ га М —■ |
|||
Тогда выражение (4.35) |
запишется в виде: |
|
|||
|
|
dV |
|
АР |
(4.37) |
|
|
Sdt |
|
|
|
|
|
М - +Р |
|
||
|
|
И го |
S ‘ |
|
Очевидно, удельное сопротивление г0 является функцией нескольких параметров: давления, температуры, химического состава, времени (для случая закупоривания пор), тогда в об щем виде дифференциальное выражение примет форму:
dV _______ АР________
(4.38)
Sdt
r0(P,T,t,x,)M^;+Rçn
Для частного случая, когда r0 = const, интегрирование урав нения (4.38) приводит к выражению:
K »+2_ V V - 2APS2t |
(4.39) |
|
г0М |
цг0М |
|
Для случая с малым сопротивлением фильтровальной пере городки:
V2 |
2APS2t |
(4.40) |
|
V-r0M |
’ |
У= |
12ДPt s |
(4.41) |
|
\xr0M |
|
Таким образом, закономерности фильтрования в основном определяются удельным сопротивлением осадка, а его иссле дование — путь к созданию математической модели процесса.
При разработке методики определения удельного сопротив ления осадка учитывалось, что существующие методы, бази рующиеся на предварительном сжатии осадка поршнем, для баллиститных топлив не могут дать объективных данных по следующим причинам:
2 2 8
—топливная баллиститная масса относится к классу сжи маемых осадков [126, 127], деформирование механическим пу тем существенно отличается от сжатия в фильтровальной зоне отжимного пресса;
—в фильтровальной зоне, которая и исследуется в данном случае, имеет место деформация только под действием гидро статического давления.
Для проведения исследований была разработана специаль ная установка, показанная на рис. 111.
Установка включает в себя стеклянный цилиндр 1 с фильт ровальной решеткой 2 в донной части, термостат 3 и центро бежный насос 4. Навеска пороховой массы в виде однородной
Рис. I I I . Схема установки определения удельного сопротивления осадка
влажных смесей:
1 — стеклянный цилиндр; 2 — фильтровальная решётка; 3 — термостат; 4 — центробежный насос; 5, 6 — вентили; 7 — мерная емкость
229
суспензии загружается в цилиндр 1. Температура осадка под держивается температурой воды, нагреваемой в термостате, а величина давления фильтрования задается насосом с помо щью вентилей 5 и 6. Мерным сосудом 7 замеряется объем по лученного фильтрата, а высота осадка определяется по мер ным делениям стеклянного цилиндра.
Расчет удельного сопротивления производится по уравне нию Дарси:
2APSt
(4.42)
Г° ~ №
Установка позволяет проводить исследования г0 в диапазо не температур 293...333 К и давлений 0,005...0,15 МПа. С ис пользованием данной установки в условиях опытного произ водства было определено удельное сопротивление топливных масс более 20 составов (относительная погрешность — 3...5%).
На рис. 112, 113 показаны зависимости удельного сопро тивления некоторых топлив от давления и температуры. Там же представлена графическая интерпретация допустимости ап-
Рис. 112. Зависимость удельного сопротивления осадка от давления:
1 - НДТ-ОМК; 2 - РНДСИ-5КМ; 3 - РСИ-60; 4 - МФ-40; 5 - обр. 1367МД
230