
книги / Сварка и свариваемые материалы. Свариваемость материалов
.pdf

ной вязкости, |
что наблюдается |
на |
образцах, |
нагретых до |
||
1300 °С. |
Термической обработкой |
можно измельчить |
зерно |
|||
аустенита |
[5] |
и восстановить ударную |
вязкость |
стали |
только |
в случае отсутствия высокотемпературной химической микроне однородности.
Следовательно, на ударную вязкость участка у линии сплав ления влияют величина первичных и вторичных зерен и состоя-
|
|
v 0,15 O f / |
Z |
4 6 |
Зона |
т ерм ического |
|||
|
Врем я |
охлаж дения |
|
|
|
в л и я н и я , мм |
|
||
Рис. 11.5. Термокинетическая диаграмма превра |
Рис. 11.7. |
Изменение микротвердо |
|||||||
щения аустенита |
в стали |
42Х2ГСНМА. |
Нагрев |
сти в зоне термического влияния |
|||||
950 °С, выдержка |
20 мин. Кривые охлаждения |
на |
сварных |
|
соединений |
стали |
|||
несены, начиная с 800°С |
|
|
42Х2ГСНМА, |
6=4,5 мм: |
|||||
|
|
|
|
|
1 — односторонняя |
аргоно-дуговая |
|||
|
|
|
|
|
сварка; |
// — электронно-лучевая |
|||
|
|
|
|
|
сварка с большой погонной энер |
||||
|
|
|
|
|
гией; |
111 — электронно-лучевая |
|||
|
|
|
|
|
сварка |
на |
оптимальном |
режиме |
Рис. 11.6. Зависимость критических точек Асх |
Рис. |
11.8. |
Зависимость |
предела |
(I) и Ас3 (2) стали 42Х2ГСНМА от скорости |
прочности |
термически упрочненной |
||
нагрева |
стали |
42Х2ГСНМА от |
максималь |
|
|
ной температуры нагрева по сва |
|||
|
рочным |
термическим |
циклам |
ние их границ. Это справедливо применительно к сварным со единениям, не подвергающимся термической обработке после сварки. В этом случае хрупкий участок у линии сплавления уширяется за счет зерен, нагревающихся до температуры ниже 1300 °С. Действительно, электрошлаковые сварные соединения стали 30Х2Н2М, выполненные проволокой Св-08ХЗГ2СМ, при надрезе Менаже по участку у линии сплавления имеют удар ную вязкость 27 Дж/см2 при температуре +20 °С. Последую щая закалка с высоким отпуском сужает этот участок до ши рины подплавления, измельчая вторичные зерна. В результате улучшения этого весьма узкого участка соседними нет сниже ния ударной вязкости (100 Дж/см2). В данном случае участок уже ширины надреза Менаже.
Серьезные трудности при сварке термически упрочненных среднеуглеродистых мартенситно-бейнитных сталей возникают также из-за разупрочнения основного металла в участке зоны термического влияния, нагреваемого до температуры высокого отпуска. Особенности разупрочнения основного металла в этом участке целесообразно рассмотреть на стали 42Х2ГСНМА, так как она наиболее интенсивно разупрочняется при сварке из-за высоких прочностных характеристик.
Построенная термокинетическая диаграмма показывает, что сталь имеет низкую критическую скорость закалки (0,625 °С/с). Она закаливается на мартенсит при скоростях ^ охлаждения, возможных при сварке (рис. 11.5).
Установлено влияние скорости нагрева и структуры металла на критические точки, а следовательно, и температурный ин тервал участка разупрочнения. Показано (рис. 11.6), что изме-- нение скорости нагрева в пределах 160—700 °С/с не оказывает существенного влияния на положение критических точек. Для стали 42Х2ГСНМА в состоянии закалки и низкого отпуска из менение скорости нагрева в пределах 30—2000 °С/с смещает температурный интервал а->у-превращения на 35—40 °С при точности измерения температуры ±10 °С. Можно полагать, что смещение температурного интервала участка разупрочнения в область повышенных температур будет таким же незначи тельным.
Изучение влияния термических циклов сварки на структуру и твердость зоны термического влияния показывает, что раз упрочнение имеет место в участке, нагреваемом до температур 500—770 °С. При этом его минимальная твердость остается практически постоянной и не зависит от погонной энергии сварки (рис. 11.7).
Определение предела прочности образцов, нагретых по сва рочным термическим циклам этого участка, показало, что па дение прочности также имеет место при нагреве до температур 500—770 °С (рис. 11.8). Прочность образцов не зависит от
скорости нагрева (0,05—700 °С/с) и скорости охлаждения (0,05—500 °С/с). Значительное разупрочнение может иметь место только при длительных изотермических выдержках по рядка нескольких часов.
С повышением погонной энергии сварки увеличивается ши рина участка разупрочнения и уменьшается предел прочности сварного соединения (рис. 11.9). Сравнение соединений стали 42Х2ГСНМА, выполненных двумя способами сварки, показало, что наименьшее разупрочнение в зоне термического влияния наблюдается при электронно лучевой сварке с низкой по гонной энергией (—6,8 %), в то время как при аргоноду говой сварке оно значительно больше (22,3%). Ширина уча стков разупрочнения в сопо ставляемых соединениях со ставляла соответственно 1,1 и
2,7 мм.
При одинаковой эффективнбй погонной энергии элект ронно-лучевая сварка по срав нению с аргонодуговой дает более узкий разупрочненный участок и более высокие зна чения прочности сварных сое динений из-за высокой кон центрации энергии в электрон ном луче.
Исследование участка раз упрочнения при аргонодуго вой и электронно-лучевой сварке металла толщиной 4,5—8 мм показывает, что
твердость в этом участке определяется только температурой нагрева, а прочность соединений зависит не от уровня твердо сти разупрочненного участка, а от его ширины. При этом сле дует учитывать, что участок разупрочнения имеет плавный переход к более прочным участкам зоны термического влияния.
Для каждой толщины металла и способа сварки существует определенная ширина разупрочненного участка, при которой обеспечивается максимально возможное контактное упрочнение и достигается равнопрочность сварного соединения основному металлу (рис. 11.10,а).
Исследования кинетики и механизма разупрочнения в зоне термического влияния позволили установить характер влияния
свойств участков, окружающих мягкую прослойку, на прочность сварных соединений. Экспериментально обоснован новый кри терий— относительная ширина мягкой прослойки bi/bo, опре деляющий предел прочности сварного соединения (рис. 11.10,6). Предложенная эмпирическая зависимость имеет вид [6]
= «? + М о “ • У + 0,3 а“ - У У
где <Твсв — предел прочности сварного соединения; ствм +- предел прочности мягкой прослойки; Ь0— ширина прослойки при равнопрочности сварного соединения основному металлу; bi — те кущая ширина прослойки.
Рис. 11.10. Зависимость предела прочности сварных соединений 42Х2ГСНМА от:
а —ширины разупрочненного участка; |
б — относительной |
ширины разупрочненного |
Участка; О — электронно-лучевая сварка, |
6=4,5 мм; X — аргоно-дуговая сварка, 6= |
|
“•4,5 мм; Д — электронно-лучевая сварка, |
6=8 мм |
Следовательно,, технологические процессы сварки, приводя щие к сужению участка зоны термического влияния сварных соединений среднеуглеродистых мартенситно-бейнитных сталей, повышают не только технологическую, но и конструктивную прочность соединений и позволяют достигнуть равнопрочность сварных соединений предварительно термоупрочненному основ ному металлу в условиях эксплуатации.
11.2.4. Выбор тепловых режимов сварки
Установлено, что участок ВХМН является наименее пластич ным участком с низкой ударной вязкостью. Уровнем его свойств определяется склонность сварных соединений к замедленному разрушению. Именно на подплавленных границах формируются Микронесплошности, которые развиваются в виде горячих или Холодных трещин.
На основании вышеизложенного методы, способствующие уменьшению склонности околошовной зоны сварных соединений
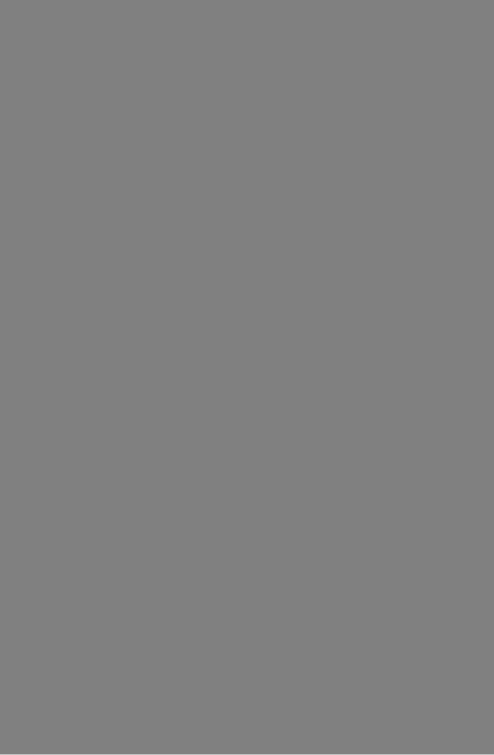
ЭЛЕКТРОДЫ ДЛЯ ДУГОВОЙ СВАРКИ к о н с т р у к ц и о н н ы х СТАЛЕЙ И МЕХАНИЧЕСКИЕ СВОЙСТВА МЕТАЛЛА ШВА
|
|
|
|
|
|
|
Электрод |
|
Механические |
|
|
|
|
|
|
|
|
|
свойства, |
||
|
|
Термическая |
|
|
не менее |
|||||
Марка стали |
|
|
|
cd |
|
|||||
|
обработка |
|
|
|
||||||
|
|
|
|
|
|
|
Тип |
гост |
с |
ь * |
|
|
|
|
|
|
|
£ |
|||
|
|
|
|
|
|
|
|
|
в |
* |
|
|
|
|
|
|
|
|
|
to |
|
25ХГСА |
Закалка |
и |
от- |
Э70 |
9467—75 |
700 |
60 |
|||
ЗОХГСА |
пуск |
после свар |
Э85 |
9467—75 |
800 |
50 |
||||
|
ки |
|
на |
|
ов^ |
|
|
|
|
|
25ХГСА |
< |
900 МПа |
|
|
|
|
|
|||
Закалка |
и |
от |
Э85 |
9467—75 |
800 |
50 |
||||
ЗОХГСА |
пуск |
после |
свар- |
|
|
|
|
|||
ки на |
ав > 900 |
|
|
|
|
|||||
25ХГСА |
МПа |
|
|
|
|
|
|
|
|
|
Сварка |
в |
упроч |
Э-10Х20Н9Г6С |
10052—75 |
600 |
90 |
||||
|
ненном |
|
состоя |
|
|
|
|
|||
ЗОХГСА |
нии |
без |
после |
Э-11X 15Н25М6АГ2 |
10052—75 |
600 |
90 |
|||
|
дующей |
термиче |
|
|
|
|
||||
12Х2НВФА |
ской |
обработки |
|
|
|
|
||||
Закалка |
|
и |
от |
Э85 |
9467—75 |
0,90а„ |
60 |
|||
23Х2НВФА |
пуск |
после свар |
Э100 |
|
основ |
50 |
||||
|
ки |
|
на |
|
ов> |
|
|
ного ме |
|
|
12Х2НВФА |
> |
1000 МПа |
Э85 |
|
талла |
|
||||
Сварка |
в |
упроч |
9467—75 |
900 |
60 |
|||||
23Х2НВФА |
ненном |
|
состоя |
Э-10Х20Н9Г6С, |
10052—75 |
600 |
90 |
|||
|
нии |
без |
после |
Э-11X 15Н25М6АГ2 |
|
|
|
|||
|
дующей |
термиче |
|
|
|
|
||||
|
ской |
обработки |
Э85, Э100, |
|
|
|
||||
ЗОХГСНА |
Закалка |
|
и |
от |
9467—75 |
900 |
50 |
|||
|
пуск |
после свар |
Э150 |
|
1400 |
40 |
||||
|
ки на ав = |
1600ч- |
|
|
|
|
||||
ЗОХГСНА |
-ч- 1800 МПа |
|
Э-10Х20Н9Г6С, |
|
|
|
||||
Сварка |
в |
упроч |
10052—75 |
600 |
90 |
|||||
|
ненном состоянии |
Э-11X 15Н25М6АГ2 |
|
|
|
|||||
|
без |
последующей |
Э-06Х19Н11Г2М2 |
|
|
|
||||
|
термической |
об |
|
|
|
|
||||
|
работки |
|
|
|
|
|
|
|
тоспособность конструкций в условиях динамических и ударных нагрузок. Аустенитные электроды применяются для соединений, не подвергающихся термической обработке после сварки.
11.3.2. Сварка в защитных газах
Высокое качество «сварных соединений толщиной 3—5 мм до стигается при аргонодуговой сварке неплавящимся электродом [2, 7]. При выборе присадочного материала (электродной
Марка
стали
25ХГСА
ЗОХГСА
12Х2НВФА
23Х2НВФА
23Х2НВФА
12Х2НВФА
23Х2НВФА
30Х2ГСНВМА
42Х2ГСНМА
ПРИСАДОЧНЫЕ МАТЕРИАЛЫ И МЕХАНИЧЕСКИЕ СВОЙСТВА СВАРНЫХ СОЕДИНЕНИЙ ПРИ ДУГОВОЙ СВАРКЕ НЕПЛАВЯЩИМСЯ
ЭЛЕКТРОДОМ В ЗАЩИТНЫХ ГАЗАХ
Термическая
обработка
Закалка и отпуск после сварки
Сварка в термиче ски обработанном состоянии без после дующей термической обработки
Закалка + отпуск после сварки
Закалка + отпуск после сварки:
на ав = 1700 ±
± 1 0 0 МПа
на а в = 2000 ±
± 1 0 0 МПа
В среде инертных газов
марка |
ГОСТ или |
ТУ |
|
Св-18ХМА, |
ГОСТ 2246—70 |
Св-18ХГС |
ГОСТ 2246—70 |
Св-18ХМА |
|
Св-18ХМА |
|
Св-08Х21Н10Г6, |
|
Св-08Х 20Н9Г7Т, |
|
Св-10Х16Н25АМ6 |
|
Св-18ХМА |
ГОСТ 2246—70 |
Св-20Х2ГСНВМ |
ЧМТУ ЦНИИЧМ |
|
582—61 |
Св-20ХСНВФАВД |
ЧМТУ ЦНИИЧМ |
|
1-91—67 |
В углекислом газе
ГОСТ 2246—70
СВ-18ХМА, Св-18ХГС,
Св-08ГСМТ Св-08ГСМТ
Св-08ГСМТ Св-08Х20Н9Г7Т
Св-08ГСМТ
—
а в МПа |
ксс/, |
|
Дж/см2 |
не менее |
|
0,9 ов ос |
50 |
новного ме |
|
талла |
|
0,9 авоснов ного метал ла 40
600 90
0,9 овоснов |
60 |
|
ного |
ме |
40 |
талла |
|
|
0,9 а в основ |
|
|
ного |
ме |
|
талла |
|
|
(0,9—0,95) |
— |
|
ав основно |
|
|
го металла |
|
проволоки) для дуговой сварки в среде защитных газов сле дует руководствоваться табл. 11.8. Первый слой выполняют без присадки с полным проваром кромок стыка и обратным формированием, второй — с поперечными низкочастотными ко лебаниями электрода и механической подачей присадочной проволоки. Возможен и третий слой с поперечными колеба ниями электрода без присадочной проволоки со стороны об ратного формирования на небольшом режиме для обеспечения плавного перехода от шва к основному металлу.
Для увеличения проплавляющей способности дуги при арго нодуговой сварке сталей применяют активирующие флюсы (АФ). Применение АФ повышает проплавляющую способность дуги в 1,5—2 раза, что обеспечивает увеличение производитель ности процесса, повышение качества, возможность исключения разделки кромок и многопроходной сварки при толщинах 8— 10 мм [7]. Для сварки сталей рекомендуется применять флюс, представляющий смесь компонентов (Si02, NaF, ТЮ2, Ti, Сг20з). Эффективно применять АФ при аргонодуговой сварке неплавящимся электродом среднеуглеродистых мартенситнобейнитных сталей, подвергнутых электрошлаковому и элек тронно-лучевому переплавам и требующих для обеспечения заданного провара увеличения сварочного тока по сравнению с металлом открытой выплавки. Сварку с АФ рекомендуется применять преимущественно механизированным способом для получения равномерной глубины проплавления. Неплавящийся электрод при сварке с АФ рекомендуется применять из наибо лее стойких марок активированного вольфрама ВТ 15 или СВИ-1. Весьма целесообразно и эффективно сочетать примене ние АФ с поперечными низкочастотными колебаниями элек трода при выполнении поверхностных слоев шва для обеспече ния плавного перехода от шва к основному металлу.
После сварки, не позднее чем через 30 мин, «сварные соеди нения с ферритными швами подвергаются высокому отпуску при 600—650 °С в течение 2 ч. Затем производится окончатель ная термическая обработка по режиму основного металла.
Ряд ответственных конструкций из термически упрочненных среднеуглеродистых мартенситно-бейнитных сталей сваривают проволокой Св-08Х20Н9Г7Т в углекислом газе как в автомати ческом, так и полуавтоматическом режиме. При прочности ме талла шва 600 МПа достигают конструктивную равноценность сварных соединений основному металлу при высокой их надеж ности.
U.3,3. Сварка под' флюсом
Автоматическая сварка под флюсом рекомендуется при ^толщине свариваемого металла свыше 4 мм для прямолинейных и кольцевых (диаметром 80 мм и выше) соединений.