
книги / Сварка и свариваемые материалы. Свариваемость материалов
.pdfрости охлаждения металла в околошовной зоне в интервале температур карбидообразования. Кроме того, высокий подогрев, как и сварка с высокой погонной энергией, обеспечивает дли тельный перегрев околошовного металла, результатом чего яв ляется рост зерна, сегрегация примесей на границах зерен и, как следствие, снижение пластичности и вязкости сварных со единений.
Лучшие свойства сварных соединений достигаются в случае предварительного подогрева в интервале Т„. „ — Тм.к, а также когда после сварки производится подстуживание до Гм. к, но не ниже 100 °С. Рекомендации по тепловому режиму сварки приведены в табл. 13.4.
13.2.3. Улучшение^ свариваемости сталей
Многие из отмеченных выше недостатков в свариваемости мар тенситных сталей не присущи малоуглеродистым хромистым сталям, дополнительно легированным никелем. Мартенсит, об разующийся при закалке хромоникелевых сталей, отличается вследствие низкого содержания углерода высокой пластично стью и вязкостью, не склонен к образованию холодных тре щин при сварке.
Высокие пластические свойства малоуглеродистого мартен сита повышают надежность получения качественных сварных соединений. Однако чувствительность металла швов к водород ной хрупкости вызывает необходимость при их сварке предва рительного и сопутствующего подогрева до 100—200 °С. Улуч шению свариваемости этих сталей способствует также остаточ ный аустенит. Количество остаточного аустенита закалки зависит в основном от химического состава стали и может быть при мерно оценено с помощью структурной диаграммы низкоуглеро дистых нержавеющих сталей, предложенной Я. М. Потаком и Е. А. Сагалевич для литого и наплавленного при сварке ме талла (рис. 13.3). Количество остаточного аустенита отпуска определяется режимом термической обработки.
13.3. Технология сварки и свойства сварных соединений
13.3.1. Способы сварки и сварочные материалы
Среди дуговых методов сварки для деталей из высоколегиро ванных мартенситных сталей применяют в основном способ ручной дуговой сварки штучными электродами, обеспечиваю
щими |
получение сварных |
швов, однородных |
по |
химическому |
||
составу |
с основным |
металлом (табл. |
13.5). Это электроды ма |
|||
рок КТИ-9, ЦЛ-32 |
с наплавленным |
металлом, |
содержащие |
|||
IQ—,)2 % Сг, ~0,8% |
Ni и |
~ 1 % Мо. В связи |
с применением |
ТАБЛИЦА 13.5
МЕХАНИЧЕСКИЕ СВОЙСТВА СВАРНЫХ СОЕДИНЕНИЙ ВЫСОКОЛЕГИРОВАННЫХ МАРТЕНСИТНЫХ СТАЛЕЙ (НЕ МЕНЕЕ)
|
|
|
Металл шва |
|
Сварное |
|||
|
|
се |
|
|
|
|
соединение |
|
Сталь, марка |
Способ сварки. |
се |
|
|
се |
|
|
|
Сварочные материалы |
с |
|
|
. s |
со |
|||
|
|
« |
С |
я |
£ |
Я Е |
||
|
|
|
2 |
oct |
§ я 5 |
|||
|
|
о |
я |
мэ |
|
я |
О и со |
|
|
|
4 |
|
ь со О. |
||||
|
|
Ь |
ь |
«О |
ь |
|
>»Я U |
15X11МФ, |
РДС: |
15Х12ВНМФ, |
электроды |
18Х11МНФБ |
Э-12Х11НМФ |
|
(КТИ-9); |
13X11Н2В2МФ |
Э-12Х11НВМФ |
15X11МФ, |
(КТИ-10); |
Э-11X15Н25М6АГ2 |
|
15Х12ВНМФ, |
(ЭА-395/9); |
18Х11МНФБ, |
Э-10Х25Н13Г2 |
15Х11Н2В2МФ |
|
|
(ЗиО); |
12X11В2МФ |
электроды |
|
Э-14Х11НВМФ |
12X11В2МФ |
(ЦЛ-32) |
АДС: |
|
|
проволока |
|
Св-15Х12НМБФ |
|
флюс АН -17; |
|
ОФ-6; |
12Х11В2МФ |
проволока |
|
Св-15Х12ГНМВФ |
|
флюс АН-17, ОФ-6; |
10Х12НД |
РДС: |
|
электроды |
|
Э-06Х13Н (ЦЛ-41) |
|
ЭШС* |
|
проволока |
|
Св-12X13 флюс |
|
АН-8 |
06X12НЗД |
РДС: |
|
электроды ЦЛ-51 |
|
АДС: |
|
проволока |
|
Св-01 Х12Н2-ВМ |
|
(ЭП-762-ВИ) |
|
флюс ФЦ-19 |
|
АрДС: |
|
проволока |
|
Св-01 Х12Н2-ВИ |
|
(ЭП-792-ВИ) |
|
ЭШС: |
|
проволока |
|
Св-01 Х12Н2-ВИ |
|
(ЭП-792) флюс |
|
АН-45 |
00сл 00 |
I 735 |
15 |
56 |
0,5 |
690 |
0,5 |
588 |
735 |
15 |
55 |
0,5 |
735 |
0,5 |
363 |
588 |
13 |
15 |
0,4 |
588 |
0,4 |
294 |
539 |
13 |
15 |
0,5 |
539 |
0,5 |
569 |
735 |
12 |
|
0,4 |
588 |
0,4 |
710 |
784 |
15 |
40 |
0,5 |
588 |
0,4 |
588 |
784 |
15 |
50 |
0,7 |
588 |
0,4 |
490 |
637 |
16 |
|
0,5 |
637 |
0,3 |
440 |
580. |
12 |
|
0,5 |
580 |
0,5 |
490 |
637 |
12 |
35 |
0,5 |
637 |
0,5 |
470 |
600 |
12 |
35 |
0,5 |
600 |
0,5 |
490 |
637 |
12 |
35 |
0,5 |
637 |
0,5 |
440 |
590 |
12 |
35 |
0,5 |
590 |
0,5 |
—
—
—
40
40
40
40
40
40
П р и м е ч а н и е . РДС — ручная дуговая сварка; АрДС — аргонодуговая сварка; ЭШС — электрошлаковая.
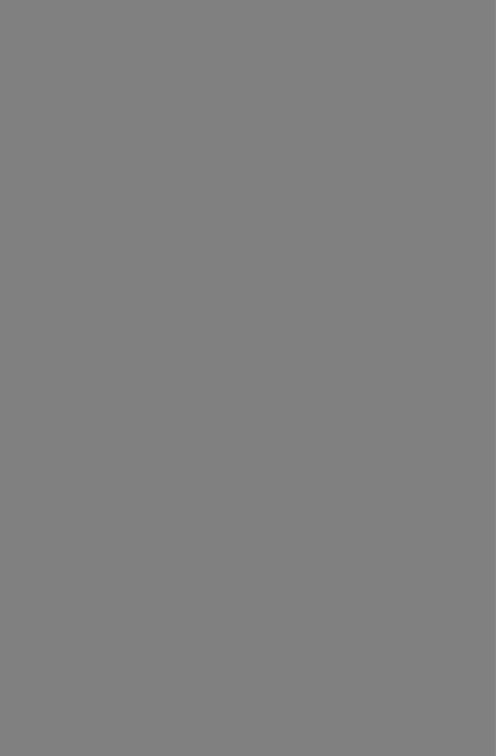
Г л а в а 14. МАРТЕНСИТНО-ФЕРРИТНЫЕ СТАЛИ (Зубченко А. С.)
14.1. Состав и свойства сталей
14.1.1. Структура сталей
С точки зрения коррозионной стойкости оптимальное содержание Сг в стали составляет 12-—14 %. Такой уровень легирования Сг обеспечивает легкую пассивацию поверхности во многих агрессивных средах, связанных с произ водством нефтехимических продуктов, а также в воде высоких параметров с борным регулированием. При повышении содержания хрома более 12% коррозионная стойкость практически не увеличивается. Вместе с тем в этом случае имеет место проявление склонности стали к охрупчиванию и сни жению прочности в связи с формированием в структуре значительного ко
личества |
ферритной составляющей. 13— 14 %-ные хромистые стали с час |
|||
тичным |
у-+а (М)-превращением относят |
к мартенситно-ферритным. По |
||
структуре мартенситно-ферритные стали |
соответствуют сплавам |
Fe — Сг, |
||
при охлаждении которых полиморфные превращения |
соответствуют |
реакции |
||
б->у+6->-а (Л /)+б. Количество 6-феррита |
в сталях |
повышается с |
увеличе |
нием содержания Сг и снижением концентрации С. С введением С границы существования области у твеРДых растворов сдвигаются в сторону более высокого содержания Сг.'У 13 %-ных хромистых сталей с <0,25% С тер мокинетическая диаграмма распада аустенита состоит из двух областей превращения. При температурах выше 600 °С в случае достаточно низкой скорости охлаждения возможно образование ферритной составляющей структуры. Ниже 400 °С при более быстром охлаждении наблюдается бездиффузионное превращение аустенита в мартенсит. Количество образовав шегося мартенсита в каждом из указанных температурных интервалов за висит, главным образом, от скорости охлаждения и содержания углерода в стали.
14.1.2. Назначение и марки сталей
Несмотря на отрицательное влияние 6-феррита на пластичность и ударную вязкость, мартенситно-ферритные стали марок 08X13, 12X13, 20X13,08X14МФ и др. находят довольно широкое применение при изготовлении химических
аппаратов |
и |
энергетического оборудования (табл. 14.1 и 14.2). Наиболее |
||||||
широкое |
применение |
в машиностроении имеют |
стали |
марок |
08X13 и |
|||
08X14МФ с пониженным содержанием углерода. |
листа и |
труб, |
так и |
кор- |
||||
Сталь 08X13 |
используют как в виде |
однородного |
||||||
|
|
|
|
|
|
Т А Б Л И Ц А |
14.1 |
|
ХИМИЧЕСКИЙ СОСТАВ МАРТЕНСИТНО-ФЕРРИТНЫХ СТАЛЕЙ |
|
|||||||
Сталь, марка |
|
ГОСТ, ТУ |
Содержание элементов, % по массе |
|||||
|
С |
Si |
|
Мп |
|
|||
|
|
|
|
|
|
|||
08X13 |
|
ГОСТ 5632—72 |
< 0 ,0 8 |
< 0 ,8 0 |
|
< 0 ,0 8 |
||
|
|
ГОСТ |
10835—75 |
0,09 -0 ,1 5 |
|
|
< 0 ,8 0 |
|
12X13 |
|
ГОСТ |
5632—72 |
< 0 ,8 0 |
|
|||
20X13 |
|
ГОСТ 5632—72 |
0,16—0,25 |
< 0 ,8 0 |
|
< 0 ,8 0 |
|
|
08Х14МФ* |
|
ТУ-14-159-155—82 |
0,03—0,12 |
0,20—0,45 |
0,8— 1,2 |
|||
14Х17Н2** |
|
ГОСТ 5632—72 |
0,11—0,17 |
< 0 ,8 |
|
< 0 ,8 |
|
Сталь, марка |
ГОСТ, ТУ |
Содержание элементов, % по массе |
|||
s |
1 |
Р |
Сг |
||
|
|
1 |
|
|
|
08X13 |
ГОСТ 5632—72 |
< 0,025 |
|
< 0,030 |
12,0— 14,0 |
12X13 |
ГОСТ 10835—75 |
|
|
|
|
ГОСТ 5632—72 |
< 0,025 |
|
< 0,030 |
12,0— 14,0 |
|
20X13 |
ГОСТ 5632—72 |
< 0,025 |
|
< 0,030 |
12,0— 14,0 |
08X14МФ* |
ТУ-14-159-155—82 |
< 0,022 |
|
< 0,035 |
12,0— 14,8 |
14Х17Н2** |
ГОСТ 5632—72 |
< 0,025 |
|
< 0,030 |
16,0— 18,0 |
* 0,2 -0,4 Мо; 0,15—0,30 V. 1,5-2,5 |
N1. |
|
|
|
|
|
МАРТЕНСИТО-ФЕРРИТНЫЕ СТАЛИ |
ТАБЛИЦА 14.2 |
|
Сталь, марка |
ГОСТ, ТУ |
Примеры использования |
|||
08X13 |
|
ГОСТ 5632—72 |
Корпуса, днища, труб |
|||
|
|
|
|
ные |
решетки, |
внутрен |
|
|
|
|
ние |
устройства |
химиче |
|
|
|
|
ских аппаратов, корпуса |
||
|
|
|
|
цилиндров паровых и га |
||
|
|
|
|
зовых турбин, рабочие и |
||
|
|
|
|
направляющие |
лопат |
|
08X13 (плакирующий |
ГОСТ 10835—75 |
ки, диафрагмы |
|
|||
Корпуса, днища, патруб |
||||||
слой |
биметалла) |
|
ки химических аппаратов, |
|||
(Ст. |
3, 20К, |
16ГС, |
|
подведомственных |
||
12ХМ, |
12МХ + |
|
Госгортехнадзору |
|||
+ 08X13) |
|
|
|
|
|
г, °с,
эксплуа
тации
4 0 -5 5 0
40—560
08Х14МФ |
ТУ 14-3-815—79 |
Теплообменники для теп |
350 |
|
|
ТУ 14-3-1065—82 |
ловых |
и атомных элек |
|
|
ТУ 14-159-155—82 |
тростанций, облицовка |
|
|
12X13 |
ТУ 14-1-3452—82 |
хранилищ |
|
|
ГОСТ 5632—72 |
Детали паровых, газовых |
500 |
||
|
|
и гидравлических турбин |
|
|
20X13 |
ГОСТ 5632—72 |
Детали |
насосов |
500 |
14Х17Н2 |
ГОСТ 5632—72 |
Детали |
внутренних уст |
400 |
|
|
ройств |
оборудования |
|
|
|
АЭС |
|
|
розионностойкого слоя биметалла. Сваренные детали из стали 08X13 при меняют в основном для изготовления внутренних устройств химических ап паратов и энергетического оборудования, не подлежащих контролю надзор ных органов за безопасной эксплуатацией. Биметалл с плакирующим слоем из стали 08X13 используют для изготовления нефтехимического оборудо вания, работающего под давлением при температурах от —40 до 560°С.
Сталь 08Х14МФ применяется на предприятиях энергетического маши ностроения, в основном в виде труб для изготовления теплообменного обо
рудования, работающего при температурах до 350 °С. Стали 12X13 и 20X13 с повышенным содержанием углерода. используют для изготовления деталей различных турбин и насосов с температурой эксплуатации до 500 °С.
МЕХАНИЧЕСКИЕ СВОЙСТВА
Сталь, марка |
ГОСТ, ТУ |
МАРТЕНСИТО-ФЕРРИТНЫХ
(0 |
|
|
С |
МПа, |
* |
еч |
||
Z |
|
|
Ь° |
ов |
О*о |
|
|
не менее |
Т А Б Л И Ц А U . 3
СТАЛЕЙ
•1
Я
ж
08X13 |
ГОСТ 5949—75 |
410 |
590 |
20 |
60 |
1,0 |
12X13 |
ГОСТ 5949-75 |
410 |
590 |
20 |
60 |
0,9 |
20X13 |
ГОСТ 5949—75 |
440 |
650 |
16 |
55 |
0,8 |
08X14МФ |
ТУ 14-1-3452—82 |
300 |
450 |
22 |
— |
— |
14X17Н2 |
ГОСТ 5949—75 |
635 |
835 |
10 |
30 |
0,5 |
Сталь марки 14Х17Н2 со значительно большим содержанием Сг, но име ющая мартенситно-ферритную структуру благодаря дополнительному леги рованию Ni, отличается высокой коррозионной стойкостью, не склонна к МКК. Применяется для внутренних устройств оборудования АЭС.
14.1.3. Механические свойства сталей
Механические свойства мартенситно-ферритных сталей регламентируют в за висимости от толщины и вида проката. В табл. 14.3 приведены основные требования к механическим свойствам. В связи с возможностью формирова ния структуры с большим количеством ферритной составляющей, способ ствующей охрупчиванию, нормативными документами, как правило, не пре дусматриваются требования по величине ударной вязкости. Лишь, для отдельных видов проката сталей марок 08X13 и 12X13 регламентирована ве личина ударной вязкости.
14.2. Свариваемость сталей
14.2.1.Фазовые, и структурные превращения при сварке
Устали марки 08X13 с содержанием углерода менее 0,08 % термокинетическая диаграмма распада аустенита имеет две области превращения: в интервале 600—930 °С; соответствую
щем образованию ферритно-карбидной структуры, и 120— 420 °С — мартенситной (рис. 14.1). Количество превращенного аустенита в каждом из указанных температурных интервалов зависит главным образом от скорости охлаждения. Например, при охлаждении со средней скоростью 0,025 °С/с превращение
аустенита происходит преимущественно в |
верхней области |
с образованием феррита и карбидов. Лишь |
10 % аустенита |
в этом случае превращается в мартенсит в процессе охлажде
ния от 420 °С. Повышение скорости |
охлаждения стали до |
10 °С/с способствует переохлаждению |
аустенита до темпера |
туры начала мартенситного превращения (420 °С) и полному его бездиффузионному превращению. Изменения в структуре,
обусловленные увеличением скорости охлаждения, сказыва ются и на механических свойствах сварных соединений. С воз растанием доли мартенсита наблюдается снижение ударной вязкости.
Увеличение содержания углерода приводит .к сдвигу в об ласть более низких температур границы превращения у->~(а+
+ К) |
и у -Ч а+ М ). У сталей с содержанием углерода 0,10— |
|
0,25 % |
в результате этого полное мартенситное превращение |
|
|
имеет место после охлаждения со |
|
|
СКОРОСТЬЮ |
1 °С/с. |
14.2.2.Сопротивляемость XT
ихрупкому разрушению
|
|
|
|
С |
точки |
зрения |
свариваемости |
||||||
|
|
|
|
мартенситно-ферритные стали яв |
|||||||||
|
|
|
|
ляются «неудобным» |
материалом. |
||||||||
|
|
|
|
В |
связи |
с |
высокой |
склонностью |
|||||
|
|
|
|
к подкалке в сварных соединениях |
|||||||||
|
|
|
|
этих |
сталей |
возможно |
образова |
||||||
|
|
|
|
ние |
холодных трещин. Склонность |
||||||||
|
|
|
|
к образованию трещин при сварке |
|||||||||
|
|
|
|
зависит |
от |
характера |
распада |
||||||
10° ю1 юг |
то3 ю* |
|
аустенита |
в процессе |
охлаждения. |
||||||||
|
В |
случае |
формирования |
мар |
|||||||||
|
В рем я, с |
|
тенситной |
структуры |
ударная |
вяз |
|||||||
Рис. 14.1. |
Термокинетическая |
ди |
кость |
|
сварных |
|
соединений |
||||||
13%-ных |
хромистых |
сталей- |
сни |
||||||||||
аграмма |
распада |
аустенита |
при |
||||||||||
непрерывном охлаждении 13 %-ной |
жается |
до |
0,05—0,10 |
МДж/м2. |
|||||||||
хромистой |
стали с |
различным |
со |
||||||||||
держанием |
углерода |
|
Последующий |
отпуск |
при |
650— |
|||||||
|
|
|
|
700°С |
приводит к |
распаду струк |
туры закалки, выделению карбидов, в результате чего тетрагональность мартенсита уменьшается. После отпуска ударная вяз кость возрастает до —1 МДж/м2. С учетом такой возможности восстановления ударной вязкости большинство марок хроми стых сталей имеет повышенное содержание углерода для пред
отвращения |
образования значительного количества феррита |
в структуре. |
Таким путем удается избежать охрупчивания |
стали. Однако при этом наблюдают ухудшение свариваемости вследствие склонности сварных соединений к холодным трещи нам из-за высокой хрупкости околошовного металла со структу
рой пластинчатого мартенсита.
Формирование значительного количества 6-феррита в струк туре околошовного металла резко уменьшает склонность свар ных соединений к образованию холодных трещин. Образование большого количества 6-феррита характерно для 13 %-ных хро мистых сталей с содержанием С<0,1 %• Количество 6-феррита
в структуре околошовного металла зависит от уровня темпера туры нагрева. В участках, нагреваемых до температур, близких к Гсолидуса) количество б-феррита в структуре может стать по давляющим. Такая структура характерна для участка зоны термического влияния, примыкающего к линии сплавления со швом и подвергающегося при сварке влиянию наиболее высо ких температур. Ширина этого участка мало зависит от тем пературы подогрева, но возрастает с погонной энергией сварки. Поэтому для сталей 08X13 и 08Х14МФ с увеличением ширины участка с большим количеством б-феррита отрицательное вли яние его на вязкость сварных соединений возрастает.
14.2.3, Выбор теплового, режима сварки
В соответствии с табл. 14.4 сварка мартенситно-ферритных сталей производится в основном с предварительным и сопут ствующим подогревом.
Даже для узлов и деталей из стали марки 08X13 с наибо лее низким содержанием углерода при сварке рекомендуется подогрев до 150—250 °С с последующей термической обработ кой. Подогрев не производится только при сварке плакирую щего слоя биметалла.
Дополнительное легирование стали 08Х14МФ карбидообра зующими элементами снижает «эффективное» содержание С и
устойчивость |
аустенита в процессе охлаждения, способствуя |
его распаду |
уже при 300 °С. Тетрагональность мартенсита |
уменьшается, что благоприятно сказывается на свариваемости. Сталь 08Х14МФ, легированная дополнительно Мо и V, свари вается в результате этого без подогрева.
|
|
|
Т А Б Л И Ц А 14.4 |
ОСОБЕННОСТИ ТЕПЛОВОГО РЕЖИМА СВАРКИ МАРТЕНСИТО |
|||
|
ФЕРРИТНЫХ СТАЛЕЙ |
|
|
Сталь, марка |
Температура |
Время пролежива- |
Термическая обработка |
подогрева, |
ния до термической |
||
|
°С |
обработки, ч |
|
08X13 |
150—250 |
Не ограничено |
Отпуск при 680—700 °С |
08X13 |
Без подо |
— |
Не производится |
(плакирующий |
грева |
|
|
слой биметалла) |
Без подо |
|
То же |
08Х14МФ |
|
||
12X13 |
грева |
2 |
Отпуск при 700—720 °С |
>300 |
|||
20X13 |
>300 |
2 |
Отпуск при 700—720 °С |
14Х17Н2 |
150—250 |
Не ограничено |
Отпуск при 620—640 °С |
МЕХАНИЧЕСКИЕ СВОЙСТВА СВАРНЫХ СОЕДИНЕНИЙ МАРТЕНСИТО-ФЕРРИТНЫХ СТАЛЕЙ (НЕ МЕНЕЕ)
Металл шва
Сталь, |
Способ сварки, |
С |
марка |
сварочные материалы |
|
|
|
£ |
*2;
Сварное
соединение |
|
& |
|
£ |
. |
2 | |
г р а д |
*2 |
08X13
08Х14МФ
08Х14МФ
08X14МФ
12X13
РДС: |
300 |
|
|
|
|
|
|
|
электроды |
540 |
15 |
15 |
0,5 |
540 |
0,5 |
40 |
|
Э-10Х25Н13Г2 |
|
|
|
|
|
|
|
|
(ОЗЛ-6, ЦЛ-25), |
|
|
|
|
|
|
|
|
Э-10Х25Н13Г2Б |
|
|
|
|
|
|
|
|
(ЦЛ-9), |
|
|
|
|
|
|
|
|
Э-08Х20Н15ФБ |
|
|
|
|
|
|
|
|
(АНВ-9), |
|
|
|
|
|
|
|
|
Э-10Х20Н15Б |
|
|
|
|
|
|
|
|
(АНВ-10), |
|
|
|
|
|
|
|
|
Э-12Х13 |
490 |
637 |
12 |
35 |
0,5 |
590 |
0,5 |
|
(УОНИ-13/НЖ, |
|
|
|
|
|
|
|
|
АНВ-1), ЦЛ-51 |
|
|
|
|
|
|
|
|
АДС: |
|
|
|
|
|
|
|
|
проволока |
300 |
540 |
15 |
15 |
0,5 |
540 |
0,5 |
40 |
Св-07Х25Н12Г2Т, |
|
|
|
|
|
|
|
|
Св-06Х25Н12ТЮ, |
|
|
|
|
|
|
|
|
Св-08Х25Н12БТЮ, |
|
|
|
|
|
|
|
|
флюс АН-26с, |
|
|
|
|
|
|
|
|
АНФ-14, ОФ-6, |
|
|
|
|
|
|
|
|
АН-18 |
|
|
|
|
|
|
|
|
АрДС: |
|
|
|
|
|
|
|
|
проволока |
300 |
540 |
15 |
15 |
0,5 |
540 |
0,5 |
|
Св-06Х25Н12Т, |
|
|
|
|
|
|
|
|
Св-08Х25Н13БТЮ, |
|
|
|
|
|
|
|
|
Св-07Х25Н12Г2Т, |
|
|
|
|
|
|
|
|
аргон по |
|
|
|
|
|
|
|
|
ГОСТ 8050-85 |
|
|
|
|
|
|
|
|
РДС: |
|
|
|
|
|
|
|
|
электроды |
300 |
540 |
15 |
15 |
0,5 |
450 |
0,5 |
|
Э-10Х25Н13Г2, |
|
|
|
|
|
|
|
|
(ЦЛ-25) |
|
|
|
|
|
|
|
|
АДС: |
|
|
|
|
|
|
|
|
проволока |
|
|
|
|
|
|
|
|
Св-07Х25Н13 |
|
|
|
|
|
|
|
|
флюс АН-26 |
|
|
|
|
|
|
|
|
АрДС; |
|
|
|
|
|
|
|
|
проволока |
|
|
|
|
|
|
|
|
Св-04Х20Н5М6Б, |
314 |
490 |
18 |
15 |
0,9 |
490 |
0,5 |
|
Св-07Х25Н13 |
300 |
540 |
15 |
0,5 |
540 |
0,5 |
|
|
электроды |
490 |
|
12 |
|
|
|
|
|
Э-12X13 (ЛМЗ-1), |
637 |
35 |
0,5 |
590 |
0,5 |
|
||
Э-06Х13Н (ЦЛ-41) |
|
|
||||||
ЦЛ-51 |
|
|
|
|
|
|
|
|
Сталь, |
Способ сварки, |
СО |
марка |
сварочные материалы |
Е |
|
|
2 |
|
|
еч |
|
|
о |
|
|
О |
Металл шва
МПа |
* |
* |
|
b, |
|||
ю |
|
||
<J |
«О |
|
|
|
|
Сварное
соединение
ев |
х соев |
S Е |
sT*
град.
12X13 |
Э-11X 15Н25 М6АГ2 |
363 |
588 |
13 |
15 |
0,4 |
590 |
0,5 |
|
12X13 |
(ЭА-395/9) |
|
|
|
|
|
|
|
|
Э-10Х25Н13Г2, |
300 |
540 |
15 |
15 |
0,5 |
540 |
0,5 |
||
20X13 |
(ЗиО-8, ЦЛ-25) |
|
|
|
|
|
|
|
|
Э-10Х25Н13Г2, |
300 |
540 |
15 |
15 |
0,5 |
540 |
0,5 |
||
|
(ЗиО-8, ЦЛ-25). |
|
|
|
|
|
|
|
|
20X13 |
ЦЛ-51 |
|
490 |
637 |
12 |
35 |
0,5 |
637 |
0,5 |
АДС: |
|
|
|
|
|
|
|
|
|
|
Св-07 Х25Н13 |
300 |
540 |
15 |
15 |
0,5 |
540 |
0,5 |
|
14Х17Н2 |
флюс АН-26 |
|
|
|
|
|
|
|
|
АДС: |
|
|
|
|
|
|
|
|
|
|
электроды |
588 |
755 |
17 |
60 |
0,6 |
755 |
0,5 |
|
|
Св-10Х18Н2, |
|
|
|
|
|
|
|
|
|
(АН В-2) |
|
|
|
|
|
|
|
|
|
АДС: |
|
|
|
|
|
|
|
|
|
Проволока |
588 |
755 |
20 |
45 |
0,7 |
755 |
0,5 |
|
|
Св-08Х18Н2ГТ, |
|
|
|
|
|
|
|
|
|
Св-08Х14ГНТ |
|
|
|
|
|
|
|
|
|
флюс АН-26с, |
|
|
|
|
|
|
|
|
14Х17Н2 |
ОФ-6; АНФ-6 |
|
|
|
|
|
|
|
|
АрДС: |
|
|
|
|
|
|
|
|
|
|
проволока |
588 |
755 |
20 |
40 |
0,8 |
755 |
0,5 |
|
|
Св-08Х18Н2ГТ, |
|
|
|
|
|
|
|
|
|
Св-08Х14ГНТ, |
|
|
|
|
|
|
|
|
|
аргон |
по |
|
|
|
|
|
|
|
|
ГОСТ |
10157—73 |
|
|
|
|
|
|
|
14.3. Технология сварки и свойства соединений
14.3.1. Способы сварки и сварочные материалы
Для стали 08X13 применяют различные способы сварки: руч ная штучными электродами и в защитных газах, автоматиче ская под флюсом. Разнообразны также применяемые свароч ные материалы. Их марки регламентированы в ОСТ 26-01-77, РТМ 108.940.08—85 и отраслевых инструкциях (табл. 14.5). Среди них наибольшее распространение имеют сварочные электроды и проволоки, обеспечивающие получение аустенит ного наплавленного металла (электроды типа Э-10Х25Н13Г2, проволока Св-07Х25Н12Г2Т).
Присадочные материалы для ручной дуговой сварки (элек троды типа Э-10Х18Н2), аргонодуговой и автоматической сварки под флюсом (проволока Св-08Х18Н2ГТ и Св-08Х14ГНТ)