
книги / Основы проектирования сборочно-сварочных приспособлений
..pdf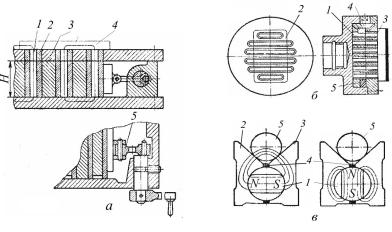
Рис. 8.11. Схемы зажимных устройств с постоянными магнитами
В магнитных патронах (рис. 8.11, б) магнитный блок 1 выполняют поворотного типа. Удерживание заготовки 2 происходит при положении блока, когда его полюса совпадают с полюсами крышки 3. При повороте блока вокруг оси патрона его полюса выходят за конфигурацию полюсов крышки, магнитный силовой поток замыкается через корпус и крышку, и заготовку можно снять с патрона. Поворот блока осуществляется через конические зубчатые колеса 4 и 5 при помощи ключа. Магнитные патроны часто снабжают наставками в виде дисков, на лицевой стороне которых выполняют центрирующие выточки для установки заготовок типа колец или шайб с базовой внутренней или наружной цилиндрической поверхностью.
На рис. 8.11, в показана магнитная призма для закрепления цилиндрических заготовок. При горизонтальном положении поворотного магнита 1 (проекция слева) магнитный силовой поток проходит через обе щеки 2, 3 призмы и заготовку 5. При вертикальном положении магнита (проекция справа) поток замыкается в корпусе призмы, и заготовка раскрепляется.
121
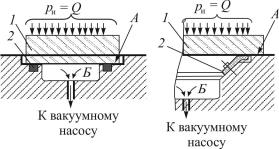
Преимущество плит с постоянными магнитами: полная автономность вследствие отсутствия питания током; исключена возможность сдвига детали при аварийном выключении тока, большая безопасность в работе. Плиты с постоянными магнитами обеспечивают удерживающую силу до 15 кг/смг, как и электромагнитные устройства.
Недостатки: небольшие в сравнении с пневмоили гидравлическими устройствами усилия зажима; базовые поверхности заготовок должны быть ровными и чисто обработанными, поскольку с увеличением шероховатости поверхности удерживающая сила снижается; закрепление деталей только из магнитных материалов; возможность намагничивания деталей.
8.3. Вакуумные зажимные устройства
Работают по принципу непосредственной передачи атмосферного давления на обрабатываемую заготовку. Схемы вакуумных зажимов показаны на рис. 8.12.
аб
Рис. 8.12. Схемы вакуумных зажимов
Заготовка 1 устанавливается в центрирующую выточку (рис. 8.12, а) или на плоскость (рис. 8.12, 6) корпуса приспособления А, из полости Б которого удаляют воздух. Заготовка к корпусу приспособления прижимается атмосферным давлени-
122
ем. Герметичность системы обеспечивают уплотнением из круглого или прямоугольного резинового шнура 2. Уплотнительный шнур выполняют из вакуумной резины (при отсутствии масел). Размеры шнура и канавки определяют работоспособность приспособления. При контакте заготовки с опорной поверхностью плиты шнур должен заполнять канавку и деформироваться по высоте на 5–10 %.
Сила зажима в вакуумном приспособлении определяется по формуле
Q =[F(ра – р0) – Руп]k, |
(8.15) |
где F – площадь, ограниченная внутренним контуром резиновой прокладки, см2; ра – атмосферное давление; р0 – остаточное давление в камере после разрежения, (ра – р0) = ри – избыточное давление и обычно составляет 0,88…0,931 кгс/см2; Руп – упругая сила сжатой прокладки; k = 0,8 …0,90 – коэффициент герметичности вакуумной ситемы. Поскольку более глубокий вакуум незначительно увеличивает силу прижима поэтому создание его нецелесообразно.
В прил. 2 представлена Лабораторная работа № 2, в которой отражено практическое применение теоретического материала, изложенного в гл. 6–8.
Контрольные вопросы к главе 8
1.Какие зажимные устройства относятся к простым?
2.Какие зажимные устройства называются комбинированными? Назовите их.
3.Перечислите основные требования, предъявляемые к зажимным устройствам.
4.Простые зажимные устройства и механизмы.
5.Какая характеристика является важной для удержания заготовки электромагнитным устройством?
6.Какой основной недостаток электромагнитных зажимных (удерживающих) устройств?
123
7.Какие зажимные устройства называются центрирующими?
8.Какие силовые приводы применяются в зажимных устройствах и механизмах?
9.Что такое пневматические приводы?
10.Назовите рычажные прижимы, их достоинства, недос-
татки.
11.К какому типу приводовотноситсямембранныйпривод?
12.Что такое эксцентриковый привод зажимных устройств?
13.Чем определяется сила зажима в вакуумном приспособле-
нии?
124
ГЛАВА 9. КОРПУСА ПРИСПОСОБЛЕНИЙ И ВСПОМОГАТЕЛЬНЫЕ ЭЛЕМЕНТЫ
Корпус является базовой деталью приспособления. На корпусе монтируют зажимные и силовые устройства, установочные элементы, детали для направления инструмента и вспомогательные детали.
Форма и размеры корпуса приспособления зависят от формы и габаритных размеров обрабатываемых в приспособлении заготовок и расположения установочных зажимных и направляющих деталей приспособления.
К корпусу приспособления предъявляют следующие основные требования:
–поскольку силы зажима и силы, возникающие при сборке
исварке изделия закрепленного в приспособлении, передаются корпусу приспособления, он должен иметь достаточную жесткость и прочность при минимально возможном весе;
–должен быть удобный доступ к корпусу для быстрой и правильной установки опорных, зажимающих элементов приспособления
–обеспечивать быструю, удобную установку и снятие обрабатываемых деталей;
–удобную конструкцию для очистки приспособления от флюса, шлака, брызг и т.п.;
–возможность быстрой и удобной установки и съема заго-
товок;
–конфигурация и размеры основной базы корпуса должны быть такими, чтобы обеспечить возможно большую устойчивость приспособления при установке его на фундаменте, столе сварщика, планшайбе позиционера, манипулятора, столе станкаавтомата и тому подобном оборудовании;
–корпус должен быть прост в изготовлении, обеспечивать безопасность работы.
125
При соблюдении всех технических требований трудоемкость изготовления корпуса и его себестоимость должны быть минимальными.
Корпуса приспособлений изготавливают:
–литыми из серого чугуна;
–сварными из листовой стали;
–коваными из стали;
–из отдельных стандартизованных или нормализованных деталей, скрепленных винтами.
Корпуса приспособлений из чугуна СЧ 12 и СЧ 18, СЧ 32 применяют для изделий мелких и средних размеров; их изготавливают из литых стандартных заготовок (например, некоторые типы заготовок корпусов плиты; коробки; швеллеры; трехгранник; четырехгранник; угольники; угольники с ребрами; ребра; планки. Рабочие поверхности корпусов обработаны с шероховатостью поверхностей Ra = 2,5…1,25 мкм; отклонение от параллельности и перпендикулярности рабочих поверхностей корпусов 0,03…0,02 мм на длине 100 мм.
Применение таких стандартных заготовок значительно уменьшает трудоемкость и стоимость изготовления корпусов и всего приспособления. Корпуса из чугуна имеют преимущества перед корпусами из стали: они дешевле, им легче придать более сложную форму, легче изготовить. Недостаток чугунных корпусов заключается в возможности их коробления, поэтому после предварительной механической обработки их подвергают термообработке (естественное или искусственное старение).
Сварные стальные корпуса применяют в основном в приспособлениях для крупных изделий. Сварные корпуса изготавливают из стали марок Ст3, 5, 6. Сварные стальные корпуса по сравнению с литыми чугунными имеют меньший вес, проще в изготовлении и стоят дешевле.
К недостаткам сварных корпусов относится деформация при сварке, поэтому в деталях корпуса возникают остаточные напряжения, которые влияют на точность. Для снятия остаточ-
126

ных напряжений сварные корпуса проходят отжиг. Для большей жесткости к сварным корпусам приваривают уголки, служащие ребрами жесткости.
Использование стандартных и нормализованных заготовок для корпусов приспособлений значительно снижает трудоемкость и стоимость изготовления приспособлений и сокращает сроки подготовки производства к выпуску новых изделий.
Корпусы приспособлений для сборки простейших конструкций выполняют в виде единой базовой детали различной конфигурации. Корпусы сложных приспособлений представляют собой сборную конструкцию. Ее элементы (рис. 9.1) могут быть выполнены литьем, сваркой или из сортового проката, путем использования различных материалов. Выбор варианта определяется условиями эксплуатации приспособления, сроками, себестоимостью и технологией его изготовления.
Рис. 9.1. Типы стандартных элементов корпусов
Детали приспособлений должны быть жесткими при изгибе и кручении. Корпусные детали приспособлений не должны деформироваться при зажиме и вызывать деформаций стола, на
127
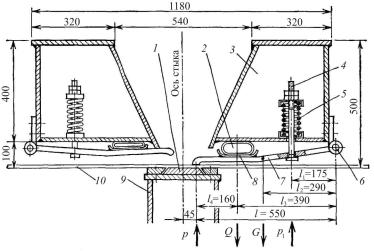
которых они закреплены. Поэтому при конструировании приспособлений опорные и несущие конструкции корпусов приспособлений рассчитываются на прочность и жесткость либо по заданным зажимным усилиям, либо по возможным деформациям, возникающим в процессе сварки.
В качестве примера приведем расчет верхней и нижней опорных балок сборочно-сварочного стенда клавишного типа
(рис. 9.2).
а |
б |
Рис. 9.2. Клавишное зажимное устройство с возвратными пружинами: а – в исходном; б – в рабочем состоянии; 1 – медная подкладка; 2 – прижимной шланг; 3 – верхняя несущая балка; 4 – натяжной болт; 5 – возвратная пружина; 6 – шарнир клавиша; 7 – прижимной клавиш; 8 – подложка для шланга; 9 – нижняя опорная балка; 10 –
свариваемые листы
Приспособление предназначено для сборки и сварки стыковых соединений листов 10 длиной до 6,5 м. Расчетная длина опорных балок равна 7 м. Материал опорных балок ВСт.Зсп. Верхняя балка 3 является опорой зажимного клавишного уст-
128
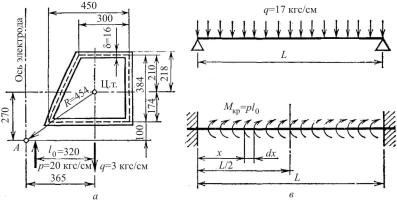
ройства 7 и одновременно несущей конструкцией для рельсового пути сварочного автомата. Поэтому ее необходимо рассчитывать как на прочность, так и на жесткость, чтобы упругая деформация балки не превышала величины, обусловленной требуемой точностью положения электрода относительно линии шва.
9.1. Расчет верхней балки на прочность
Составляем расчетные схемы (рис. 9.3). Балка работает на изгиб и кручение. Поскольку в приспособлении используются клавишные прижимы, примем их погонное усилие р = 20 кгc/см. На балку действует распределенная нагрузка q = р – g = 20 – 3 = = 17 кгc/см, где g = 3 кгс/см – собственный вес балки и закрепленных на ней устройств, приходящийся на единицу длины балки. Таким образом, изгиб балки происходит под действием нагрузки q = 17 кгc/см.
б
|
|
в |
|
а |
|||
|
|
||
|
|
|
Рис. 9.3. Расчетныесхемыверхнейопорнойбалкизажимного устройства: а – поперечное сечение балки и схема расположения действующих сил; б – схема нагружения балки на изгиб; в – схема нагружения балки на скручивание
129
Наибольший изгибающий момент (рис. 9.3, б) будет посредине балки:
Ми = (q·L2)/8 = 17·7002/8 = 1041250 кг/см.
Момент инерции сечения балки относительно горизонтальной оси, проходящей через центр тяжести сечения, I = 58 520 см4. Момент сопротивления W = 2680 см3.
Максимальное напряжение изгиба:
σи = Ми/W = 1041250/2680 = 388 кг/см2.
Балка изготовлена из стали ВСт.Зсп, для которой допускаемое напряжение на изгиб [σ]и = 2400 кг/см2, что существенно выше расчетного, следовательно, балка обладает гарантированной прочностью на изгиб. Однако она одновременно работает и на кручение.
Наибольший крутящий момент (от внецентренной нагрузки на клавиши) действует не посредине длины балки (как при изгибе), а по ее концам и, следовательно, не совмещается с действием наибольшего изгибающего момента. В среднем сечении балки крутящий момент равен нулю. Поэтому влияние скручивания балки на ее прочность невелико и им можно пренебречь, чего, однако, нельзя сказать об этом влиянии на жесткость балки.
9.2. Расчет верхней балки на жесткость
Наибольший прогиб балки под действием равномерно распределенной нагрузки q будет посредине ее пролета
(см. рис. 9.3, б):
f = |
5q L4 |
5 17 7004 |
|
|
|
= |
|
= 0,43 см = 4,3 мм. |
|
384E I |
384 2,1 106 58520 |
Кроме того, балка приобретает деформацию скручивания, причем наибольший угол закручивания будет посредине балки и, следовательно, его деформативное действие будет совме-
130