
книги / Технология производства полимерных композитных материалов и конструкций на их основе
..pdfДля увеличения относительного удлинения полимерной матрицы применяют для эпоксидных смол полуфункциональные пластификаторы, например, тиокол.
2. ТЕХНОДОШЯ ПРОИЗВОДСТВА КОНСТРУКЦИЙ ИЗ КОМПОЗИТНЫХ МАТЕРИАЛОВ
Для производства конструкций из композитных материалов не обходимо реализовать тот или иной технологический процесс, струк тура которого определяется технологическими, организационными, экономическими задачами. При проектировании процесса эти задачи решаются в соответствии с требованиями чертежа и ТУ на изготов ление конструкция. В частности, надо обеспечить:
1. Прочность и качество основных поверхностей конструкции
иточность их расположения относительно друг друга.
2.Получение композитов в готовых конструкциях с заданными физико-механическими характеристиками и специальными свойствами.
3.Неизменность формы (геометрии), размеров и положения по верхностей с течением времени.
4.Неизменность композитного материала по физико-механичес ким характеристикам в заданный период времени.
5.Производство конструкций с наименьшими затратами и наи большей технико-экономической эффективностью.
Таким образом, можно сказать, что существует две группы задач:
I. Связанные с формованием и получением композитного ма териала.
П.Связанные с формованием и получением системы основных
ивспомогательных поверхностей, соответствующей геометрии и точ ности с заданными характеристиками качества.
Решение этих задач можно осуществлять на основе двух прин ципов:
I. Принцип технологической "автономности”, т.е. сначала из готавливают композитный материал, затем конструкцию, обеспечивая соответствующие физико-механические характеристики и качество.
Например, детали изготавливают методом штамповки из листов ком позитного материала или резанием из прессованных материалов (текстолитов, деревопластиков).
2. Принцип технологического "совмещения" - совмещение про цессов получения композитного материала и конструкции, так как они протекают одновременно. Это создает определенные трудности, но позволяет сократить технологические циклы и резко снизить се бестоимость.
2.1. Формование конструкций
Формование конструкции - это процесс придания нужной формы полуфабрикату. В зависимости от технологии изготовления конст рукций процесс формования может быть совмещен с пропиткой и поч ти всегда предшествует отверждению связующего. Из большого чис ла технологий изготовления конструкций из композитных материалов наибольшее распространение получили контактное формование, напы ление, вакуумирование, протяжка и намотка.
2.1.I. Контактное формование
Первая стадия получения конструкции - нанесение на ее по верхность антиадгезионного покрытия (рис.14). Выбор его зависит от типа формуемой поверхности, заданной степени глянцевитости го тового продукта и наличия или отсутствия вторичных отделочных операций (например, окрашивания).
Рис.14. Схема формования конст рукций контактным формованием:
/ - армирующий материал; 2 - уплотняющий валок; 3 - матрица
Программа подготовки формы начинается с нанесения нескольких слоев (3 или 4) пастообразного парафина. Каждый слой выдерживает ся до затвердевания парафина. Для облегчения съема конструкций на поверхность формы дополнительно напыляют поливиниловый спирт. Пе риодически через каждые 10-20 конструкций форму чистят.
Для получения наружного смоляного слоя (гелькоата) обычно используют полиэфирную смолу, содержащую минеральные наполнители и пигменты. Эта композиция наносится сначала на поверхность фор мы, а затем в процессе формования переходит на формуемую конст рукцию, образуя наружный слой. Тем самым образуется декоративная глянцевая поверхность с хорошими защитными свойствами, которая почти или совсем не требует последующей отделки.
Следующей операцией процесса формования является подготовка материала.
Все типы армирующих материалов - маты из рубленой стеклопряжи, ткани и ткани ровинг - поступают в виде больших рулонов раз личной ширины. Лист нужной длины вырубается из рулона, а затем обрезается по шаблону с помощью ножа, ножниц или электрической машины для резки тканей. Армирующий материал укладывают в форму и пропитывают связующим. Для полного удаления воздуха и равно мерности пропитки связующее наносят сначала на участки армирую щего материала в верхней части формы. Для его уплотнения по фор ме и удалению пузырьков воздуха используют щетки, резиновые и зубчатые валики. Слои мата и тканого ровинга следует чередовать для обеспечения хорошей межслойной прочности сцепления, предот вращения появления воздушных включений и получения максимальной прочности.
При использовании стекломатов содержание армирующего мате риала должно быть 25-35 %, матов и тканого ровинга 35-45 %, а только ткани - около 50 %.
2.1.2. Формование напылением
Измельченный армирующий материал и связующее одновременно вводятся в форму (рис.15).Ровинг проходит через рубильное уст ройство и вдувается в поток смолы, который направляется в форму распылительной системой. Связующее покрывает армирующий материал,
и объединенный поток равномерно распыляется оператором в |
форме |
по заданной схеме. |
|
После введения в форму смеси связующего и армирующего |
мате |
риала образовавшийся слой прикатывают вручную для удаления |
воз |
духа, уплотнения армирующего материала и получения гладкой |
по |
верхности. |
|
Рис. 15. Безвоздушная система напыления с двумя емкостями: 1 - ро винг; 2 - рубильное устройство; з - связующее; 4 - валик; £ - уп
лотненный слой; 6 - форма
В обоих методах невозможно создать предварительное натяже ние армирующего материала, не обеспечивается равномерное распре деление связующего в композитном материале. Поэтому конструкции имеют низкие прочностные характеристики и высокую пористость. Эти методы формования применяют при изготовлении крупногабаритных кон струкций, не испытывающих больших силовых нагрузок.
2.1.3. Формование прессованием
Прессование применяется для деталей упрощенной формы я срав
нительно небольших габаритов, осуществляется в пресс-формах |
на |
||||
гидравлических прессах. Толщина деталей определяется величиной |
|||||
фиксированного |
зазора между пуансоном и матрицей, количество |
сло |
|||
|
|
|
ев армирующего материала назначается |
||
|
|
|
заранее. Формование деталей произво |
||
|
|
|
дится при расположении пуансона как |
||
|
|
|
снизу, так и сверху (рис.16). При по |
||
|
|
|
лучении мелких деталей |
связующее с |
|
|
|
|
армирующим материалом можно наносить |
||
|
|
|
в виде одного "пятна”. Для формования |
||
|
|
|
больших деталей необходимо распреде- |
||
Рис. 16. Схема |
формования |
лить композицию по довольно большой |
|||
прессованием: / |
- деталь; |
поверхности. Для каждой детали в этом |
|||
2 - ограничитель |
зазора; |
||||
3 - матрица; ^ - пуансон |
случае режимы формования находят |
ме |
|||
тодом проб и ошибок, пока |
не будет найден вариант, |
обеспечивающий |
|||
правильную пропитку |
заготовки. Необходимо тщательно контролировать |
конечную скорость прессования: смола должна течь не настолько быстро, чтобы вызвать разупорядочивание армирующего материала, но все-таки достаточно быстро, чтобы не произошло преждевремен ное ее отверждение при контакте с горячей поверхностью формы.
Максимальное давление формования может достигать 3,45 МПа, в то время как обычно достаточно 1,38 МПа. Цикл формования мел ких деталей может составлять всего 3 мин, а очень больших - 20 мин. Температура формования обычно лежит в диапазоне 104 - - 149 °С. После снятия большинство деталей следует помещать в
приспособления для их охлаждения, чтобы предотвратить коробление. При формовании деталей применяются полиэфирные связующие.
Они имеют сравнительно низкую вязкость (0,8... 1,2 Па*с). Это обу словлено тем, что они должны легко протекать через армирующий ма териал за время формования.
Прессованные под давлением детали характеризуются высокими прочностными показателями; производительность такого способа фор мования достаточно высока. Вместе с тем стоимость изготовления матриц и пуансонов заметно возрастает для деталей сложной формы, что и сдерживает широкое применение такой технологии.
2.1.4.Формование с эластичной диафрагмой
Кэтому методу относятся вакуумное формование (рис.17), фор
мование под давлением (рис.18) и автоклавное формование |
(рис.19). |
Формование производится с применением специальных форм, |
на которые |
после антиадгезионной обработки выкладывается предварительно рас кроенная ткань, пропитанная связующим. В отдельных случаях уклады вается сухая ткань с последующей пропиткой связующим.
На собранный пакет заготовок вслед за разделительной антиадгезионной пленкой (целлофан) укладывается эластичная оболочка, ча ще Всего резиновый чехол или мешок. Герметизация фланцев формы осуществляется прижимными кольцами и винтовыми (гидравлическими, пневматическими) зажимами. Далее производится отверждение связую щего при заданном термическом режиме и избыточном давлении.
Давление может создаваться вакуумированием, в пресс-камерах, в автоклавах. При отверждении конструкции необходимо избегать образования пузырей в композите, а также тщательно контролировать
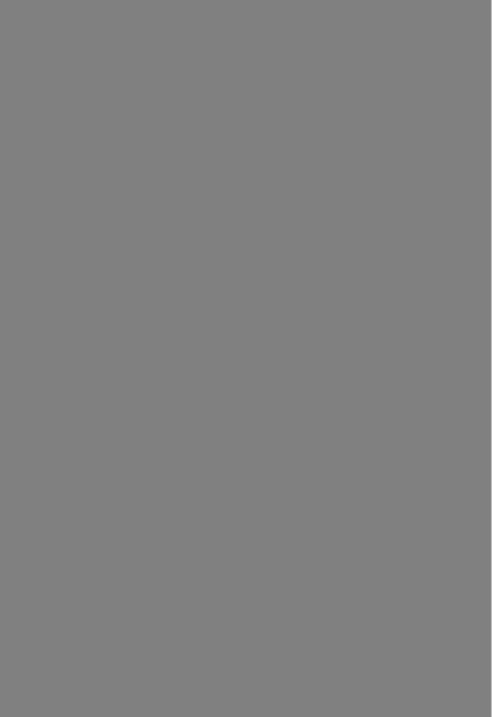
зуют воздушные сушилки, а также сушилки с инфракрасными нагре вателями.
Стоимость оснастки при вакуумном и автоклавном формовании ниже, чем при формовании на матрице. Формы и плиты при этих мето дах не деформируются и не разрушаются под действием нагрузок.
Более высокая стоимость оборудования при автоклавном формо вании может компенсироваться его более широкими возможностями для формования конструкций сложной.формы. В автоклавах темпера тура обычно составляет 177 °С и давление 1380 кПа; в новых авто клавах температура свыше 260 °С и давление более 3450 кПа. Всё же размер большинства специальных автоклавов ограничен, что за трудняет их использование для некоторых конструкций.
2.1.5. Формование протяжкой
Формование плоскостных конструкций методом протяжки (рис.20) заключается в укладке рубленого пропитанного стеклохолста ^ (или одновременное нанесение наполнителя и связующего) между двумя изолирующими лентами 5 . Получаемая трехслойная лента или лист поджимается и одновременно протягивается с помощью системы
вращающихся подогретых валков 6 через термокамеру, где происхо дит отверждение связующего.
В производстве конструкций более сложной конфигурации (швел леры, утолки и т.п.) нити с бобин сматываются, проходят через на
тяжное устройство и ванночку со связующим, отжимное устройство и формующую фильеру, в которой полуфабрикату придается нужная фор ма. Неотвержденная заготовка протягивается через термокамеру, где происходит частичное отверждение и, если необходимо, через окон чательную фильеру для доведения полуфабриката до требуемой формы
иразмеров и вводится во вторую термокамеру.
2.1.6.Непрерывные производственные процессы.
Пултрузия
Быстро расширяющееся применение деталей из композитных мате риалов в различных отраслях промышленности привлекает особое вни мание к непрерывным производственным технологиям. Непрерывный процесс их получения от сырья до готовой конструкции обеспечивает оптимальную эффективность производства в тех случаях, когда это оправдано объемом выпуска конструкций. При работе с композитными материалами, свойства которых зависят практически только от ори ентации армирующих материалов, непрерывный процесс дает дополни тельное преимущество, обеспечивая надежный контроль их ориента ции и натяжения. Сочетание этих методов переработки с другими приводит к такой экономии материала, которую не удается достичь при других технологиях производства.
При производстве профильных конструкций из одноосно-ориенти рованных волокнистых пластиков непрерывным способом применяют пултрузию, которая является точной аналогией экструзии алюминия или термопластов.
Вначале пултрузию рассматривали как метод получения простых сплошных профилей, армированных однонаправленным волокном. По мере усовершенствования процесса пултрузия превратилась в метод производства практически неограниченного ассортимента сплошных и полых профильных конструкций.
Первоначально скорость пултрузии составляла 0,6...О,9 м/мин, сейчас она увеличилась до 4,6...6,1 м/мин. Этот резкий рост про изводительности труда обусловлен эффектом от модификации смол и усовершенствования технологии их отверждения. Применение высоко частотного нагрева наряду с традиционными способами нагрева не только увеличивает рабочие скорости, но и позволяет выпускать как
простыв крупные профильные конструкции, так и такие, масса кото рых в пределах профиля резко изменяется.
В настоящий момент ведутся работы по усовершенствованию процесса, связанного с обеспечением точной ориентации армирующе
го материала, что позволит оптимизировать |
свойства |
конструкций |
в соответствии с их конкретным назначением. |
|
|
Для иллюстрации гибкости непрерывной |
технологии |
рассмотрим |
особенности получения грубы следующего строения: внутренний слой из полиэфирной смолк (для придания поверхности необходимой глад кости), затем слой мата из непрерывного волокна (для создания ненаправленных свойств), три продольных слоя ровинга (для обес печения прочности на изгиб), окружной слой ровинга (для прочно сти на разрыв под действием внутреннего давления), слой ровинга, наложенного под углом +45° и -45° (для сопротивления скручиваю щим нагрузкам), еще один слой мата из непрерывного волокна (для увеличения ударной прочности) и, наконец, наружный слой из хими чески стойкого стекловолокна (для обеспечения высокой коррози онной стойкости). Для получения конструкций высокой прочности применяют углеродные, арамидные и волокна из J -стекла.
2.1.7. Намотка
Намотка - сравнительно простой процесс, в котором армирую щий материал в виде непрерывного ровинга (жгута) или нити (пря жи) наматывается на вращающуюся оправку. Специальные механизмы контролируют угол намотки и расположение армирующего материала.
Существует несколько технологических методов формования конструкций. В зависимости от способа нанесения связующего и обеспечения необходимого коэффициента армирования в структуре композитного материала различают "сухой" и "мокрый" методы.
"Сухой" метод формования заключается в том, что армирующий материал перед формованием предварительно пропитывают связующим на отдельной технологической операции, которая выполняется на специальном оборудовании, в результате чего получается материал под названием препрег. Выделение пропитки в самостоятельную опе рацию позволяет значительно расширить диапазон применяемых свя зующих за счет возможности использования летучих растворителей
(толуола, ацетона, спирта и т.д.). Путем введения в связующее этих растворителей уменьшается их технологическая вязкость, что дает возможность улучшить качество я равномерность пропитки ар мирующего материала во всем объеме, сохраняя высокую жизнеспо собность связующего. Однако, чтобы последующее испарение летучих растворителей не отражалось на качестве композитного материала и плотности его структуры и чтобы предотвратить наличие газовых включений, пузырей и расслоений в конструкции, необходимо пре дусмотреть перед формованием, после пропитки, операцию сушки про питанного армирующего материала. Обычно операции пропитки и суш ки совмещают в едином технологическом цикле.
При намотке конструкций из препрега обеспечивается равно мерный коэффициент армирования в структуре формуемой стенки кон струкции, но стоит задача в обеспечении надежного прилипания слоев друг к другу (аутогезия). Это достигается технологически ми режимами: натяжением, прикаткой, температурой формования. Вы сокая температура формования способствует размягчению связующего, что обеспечивает качественную аутогезию и адгезию.
При "сухой” намотке получают более пористые и менее проч ные конструкции, чем при ”мокрой”. Поэтому для ответственных конструкций необходимо проводить дополнительное уплотнение, что однако делается и при производстве конструкций с "мокрой” намот
кой.
"Мокрый” метод характерен тем, что операции пропитки и формования совмещены. Последнее обстоятельство не допускает применения летучих растворителей для повышения текучести связу
ющих с целью |
улучшения условий пропитки, |
так как |
выделяющиеся |
|
из структуры |
отформованной стенки летучие |
резко |
ухудшают |
ка |
чество композитного материала, его монолитность, |
прочность |
и т.д, |
Использование связующих, разведенных летучими растворителями при формовании "мокрым" методом, допускается только при производстве неответственных конструкций.
Необходимая консистенция связующего обеспечивается выбором соответствующей марки смолы, применением разбавителей и приме нением подогрева.
Достоинством "мокрого" метода является его высокая произво дительность, полученная за счет ликвидации самостоятельных опе