
книги / Основы экспериментальной механики разрушения
..pdfТаким образом, рост усталостной трещины происходит ди скретно мелкими скачками, что подтверждается экспериментом. На поверхности усталостного разрушения наблюдается харак терный рисунок, образованный концентрически расходящимися от точки зарождения трещины полосами и бороздками. Ширина каждой полосы равняется расстоянию, на которое продвинулась трещина за цикл нагружения, а бороздки представляют после довательные положения фронта трещины в момент остановок. Иногда по разным причинам полосы и бороздки на поверхности разрушения могут не наблюдаться. Это, однако, не означает, что механизм роста усталостной трещины в данном случае сущест венно отличается от изложенного.
В лабораторных условиях усталостные испытания, как пра вило, проводят при синусоидальном изменении внешней нагруз ки во времени
o(t) = о И1+оа sin <ùt,
где От — среднее напряжение цикла, о« — амплитуда, и — час тота, t — время.
Иногда применяются и другие формы цикла — прямоуголь ная, треугольная (показаны на рис. 4.2 штриховой линией) и т. д. В целом, однако, форма цикла не оказывает заметного влияния на результаты испытаний.
В качестве характеристик цикла нагружения (частота фик
сирована) |
используются не только ат и ов, но и другие величи |
|
ны: Стах, |
Grain — максимальное и минимальное напряжения, |
|
r = Omin/Omas — Коэффициент ЭСИММвТрИИ, До= Ощах— Omln |
рЭЗ- |
мах напряжения цикла. Для полного описания закона нагруже ния, очевидно, достаточно любых двух из этих величин, кроме
пары — Ов, Ао.
На рис. 4.2 построены возможные частные виды нагружения. Рис. 4.2, а соответствует симметричному циклу, для которого ат— 0, г = —1; рис. 4.2, б относится, к асимметричному циклу, для которого атфО, —1< г < 1. Среднее напряжение ат здесь может быть как положительным, так и отрицательным при по стоянной нагрузке г=1. Иногда удобно нагружение по асиммет ричному циклу представлять в виде суперпозиции симметрично го циклического нагружения с амплитудой оа и статического нагружения а— ат . Асимметричный цикл нагружения, соответ ствующий ат)п=0 (показан на рис. 4.2, в), называется пульси рующим.
Расширяя понятия линейной механики разрушения на усло вия усталостного нагружения, введем / С т а х , Кты, Кт соответст венно максимальное, минимальное, среднее значения коэффици ента интенсивности напряжений в цикле. Связь между / С т а х » Ктш, Km и напряжениями стах» Omin» от устанавливается фор мулой (2.44).
Поскольку рост усталостной трещины, как правило, носит хрупкий характер, то напряженное состояние в окрестности ее вершины при растяжении однозначно определяется величиной
К. При сжатии трещина перестает быть концентратором напря жений и понятие К утрачивает смысл.
Ограничиваясь случаем отсутствия сжатия, естественно предположить, что при равных коэффициентах интенсивности напряжений две трещины различной длины получают одинако вое приращение за один цикл нагружения, т. е. растут с одина ковой циклической скоростью dl/dn. Приняв за характеристики цикла /Стах и г, на основе сделанного предположения можно записать
dljdn= ф(/Стах» г). |
(4.1) |
В применении к нагружению по пульсирующему циклу |
( / С т а х = |
= Д/<", г= 0) из (4.1) получаем |
|
д а п = Ф(Д/С). |
(4.2) |
Дальнейшая конкретизация полученного соотношения требует обращения к эксперименту.
На рис. 4.3 в двойных логарифмических координатах по строена типичная экспериментальная зависимость скорости ро ста усталостной трещины от размаха коэффициента интенсивно сти напряжений. Можно видеть, что в достаточно большом диа пазоне изменения скоростей зависимость является линейной.
Это дает основание использовать степенную |
аппроксимацию |
для функции ф(ДК), и формула (4.2) принимает вид |
|
dl/dn= C (kK )m, |
(4.3) |
где С п т — константы материала, определяемые эксперимен тально. Обычно т колеблется между 2 и 7. Наиболее часто встречающееся его значение 4.
Формула (4.3), называемая формулой Пэриса, явилась пред метом многочисленных исследований, проведенных на различ ных материалах и в различных условиях. В частности, установ лено, что формула может использоваться не только в примене нии к пульсирующему циклу нагружения, но часто и в произ
вольном случае г > 0. При этом зави симость скорости dlldn от коэффици ента асимметрии цикла удается учесть введением данной зависимости в па раметры С и т , т. е- положив С—С (г) и m =m (r). В ряде случаев, когда ли нейные участки экспериментальных кривых dlldn—Д/С, относящихся к различным г, параллельны, функцией г оказывается только С. В настоящее время формула (4.3) является основ-
Рис. 4.3. Экспериментальная зависимость ско рости роста усталостной трещины от размаха коэффициента интенсивности напряжений
ной исходной базой для практических расчетов и эксперимен тальных исследований. Однако, будучи эмпирической, она тре бует соблюдения определенных предосторожностей, связанных с •ограниченностью области применимости, возможным различием в значениях С и т для диапазонов миогоцнкловон и малоцикловой усталости и т. д. Считается, что использование формулы Пэриса приводит к удовлетворительным результатам при ско ростях dl/dn>-2,5-10~5 мм/цикл, если максимальное напряжение цикла не превосходит предела текучести 0тах<0т и не учитыва ется относительно короткий участок ускоренного роста трещины перед разрушением.
Шурокому распространению формулы Пэриса в немалой степени способствует ее простота. При повышении требований к точности расчетов или в условиях неприменимости формулы Пэриса используются и другие зависимости, большое разнооб разие которых приводится в специальной литературе. Получила, например, распространение предложенная Формэном формула, в явной форме учитывающая влияние коэффициента асиммет рии цикла
dl_ _ |
С&кт |
_ |
С\Кт |
. |
dn |
(1 — г ) / с 1с— Д /( |
|
( 1 - г ) ( / С 1с- / С т зх) |
( ' ) |
При построении этой формулы принималось во внимание, что dl/dn -*■оо при /Стах -*■ К\с- На самом деле критическое значение коэффициента интенсивности напряжений при усталостном раз рушении может быть заметно меньше вязкости разрушения Kic из-за накопления микроповреждений в материале до подхода трещины. Чтобы учесть данные эффекты, иногда вводят вяз кость разрушения поврежденного материала K fc< K ic.
В качестве обобщения формулы Пэриса может рассматри ваться выражение, примеры успешнего практического примене ния которого также имеются:
f a = C\KmJ(г)1” . |
(4.5) |
Если функцию f(r) определить равенством f(r) = l—г, то (4.5) приводится к виду (4.3). Для одного из алюминиевых сплавов в условиях циклического изгиба для f(r) была получена следую щая аппроксимация:
f( r ) = l - r ( l+ r ) /2 .
До сих пор предполагалось, что режим нагружения является знакопостоянным растяжением. При г<0, т. е. при наличии на части цикла сжимающих напряжений, как показали исследова ния, можно пренебречь отрицательной частью цикла. Поскольку в этом случае единственной характеристикой цикла нагруже ния становится /Стах, то из (4.1) получаем
dl/dn— (ç(Km&x), г<[0. |
(4*6) |
Обращаясь к рис. 4.3, можно видеть, что при малых Д/С рост трещины замедляется и при достижении некоторого порогового
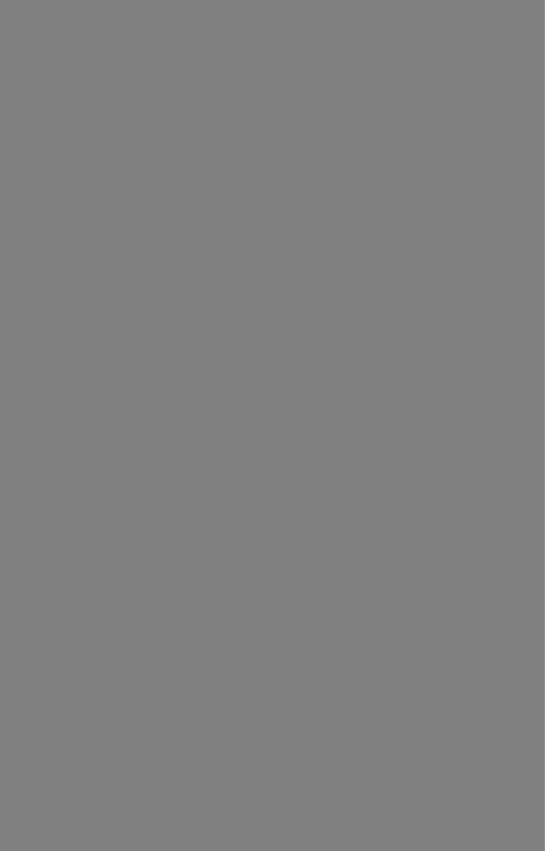
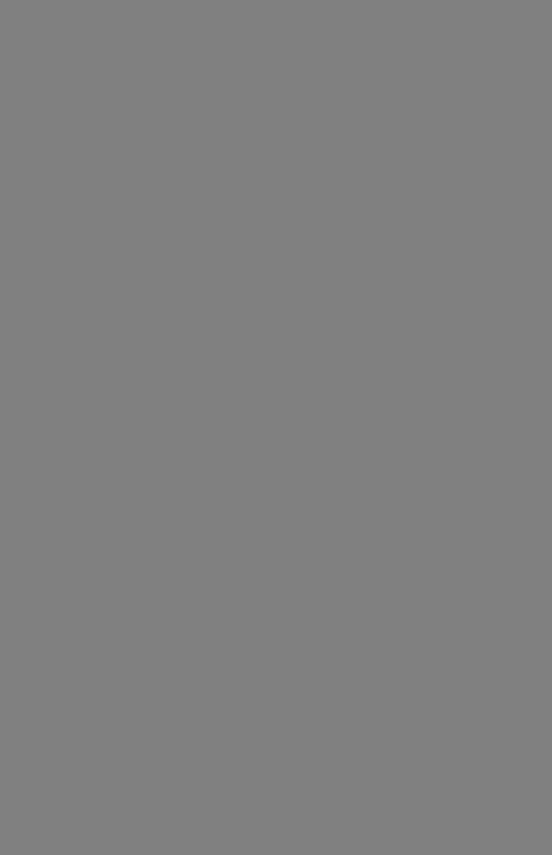
|
|
|
|
п Ю3 |
Рис. 4.4. Кривые роста усталост |
Рис. 4.5. |
Явления задержки |
роста |
|
ной трещины при различных на |
усталостной трещины |
после |
разовых |
|
грузках До и начальных длинах /0 |
перегрузок |
(данные |
относятся к |
|
|
алюминиевому сплаву) |
Кривые роста усталостной трещины при различных нагруз ках До и различных начальных длинах 1о схематически показа ны на рис. 4.4.
В заключение настоящего раздела остановимся вкратце на явлении задержки (замедления) роста усталостной трещины после приложения к телу разовой перегрузки. Данное явление наблюдается в эксперименте и иногда используется на практи ке с целью повышения долговечности конструкции. Его иллю страцией являются данные по алюминиевому сплаву, приведен ные на рис. 4.5. Здесь построены кривые роста трещины при ис пытании с постоянной амплитудой без перегрузок (кривая 1) и при испытании с этой же амплитудой при наличии разовых пе регрузок. Причем в одном случае перегрузка производилась с переменой знака (кривая 2), т. е. растяжение сопровождалось сжатием, а в другом — полуцикл сжатия отсутствовал (кривая ■3). Можно видеть, что перегрузка растягивающими напряжени
ями приводит к замедлению |
роста |
трещины |
на протяжении |
большого числа циклов (до |
нескольких сотен). |
Затем кривая |
|
роста трещины становится |
подобной |
кривой, |
относящейся к |
контрольному образцу. Приложение вслед за растяжением пе
регрузки отрицательного |
знака |
приводит |
к резкому |
уменьше |
|||||
нию продолжительности замедленного роста трещины. |
|
уста |
|||||||
|
|
Явление |
задержки роста |
||||||
|
лостной |
трещины |
получает |
ес |
|||||
|
тественную интерпретацию в тер |
||||||||
|
|
минах механики разрушения. |
|
||||||
|
|
При |
перегрузке |
положитель |
|||||
Rp |
|
ного знака |
в вершине |
трещины |
|||||
|
возникает |
большая |
пластическая |
||||||
«4------------- |
|
зона (на |
рис. 4.6 обозначена |
че |
|||||
Рис. 4.6. Пластические |
зоны |
рез Rp), в которой последующая |
|||||||
разгрузка |
|
вызывает |
появление |
||||||
в вершине трещины при пере |
остаточных |
сжимающих |
напря |
||||||
грузке и при стационарной ам |
|||||||||
плитуде нагружения |
|
жений. Эти |
напряжения в свою |
•очередь являются причиной замедленного роста трещины при стационарной амплитуде нагружения. Число циклов задерж ки определяется продолжительностью прохождения трещиной с пластической зоной стационарного размера гр образовавшейся области остаточных напряжений Rp.
Перегрузки отрицательного знака н_е влияют на рост уста лостной трещины. Однако, будучи приложенными вслед за рас тягивающей перегрузкой, они уменьшают величину остаточных •сжимающих напряжений, а также размер пластической зоны Rp, приводя к подавлению эффекта задержки.
Существующие подходы к количественному описанию рас смотренного явления относятся к эмпирическим. Обычно они базируются на введении поправочных коэффициентов, являю щихся функцией Rp, гр и текущей длины трещины.
ТРЕЩИНЫ в к о н с т ру к ц и о н н ы х
МАТЕРИАЛАХ
Современные конструкционные материалы при всем их разно образии условно можно разбить на три большие группы — это металлы, полимеры и композиты. Существенные различия BS структурном строении материалов, относящихся к различным группам, предопределяют различия в микромеханизмах их раз рушения (и деформирования), что в свою очередь проявляется на макроуровне в специфических для каждой группы особен ностях разрушения.
Настоящий параграф посвящен краткому изложению важ нейших экспериментальных фактов и модельных представлений о распространении трещин в металлических и полимерных ма териалах.
Применительно к металлам сведения подобного рода подроб но рассматривались ранее (см. разделы 2.6, 3.1, § 4.). Поэтому ниже обсуждаются лишь те аспекты, которые еще не получил» должного освещения. Как правило, они имеют непосредствен ное отношение к методикам экспериментального определения характеристик трещиностойкости и проведения лабораторных испытаний.
5.1.
ЛАБОРАТОРНЫЕ ИСПЫТАНИЯ МЕТАЛЛИЧЕСКИХ ОБРАЗЦОВ.
ОПРЕДЕЛЕНИЕ ХАРАКТЕРИСТИК ТРЕЩИНОСТОЙКОСТИ
В табл. 5.1 * приведены вязкости разрушения Ки нескольких марок сталей, алюминиевого и титанового сплавов. Приведены также пределы текучести от и значения параметра (/Cic/от)2, ха рактеризующего размер пластической зоны в вершине трещины.
Измерения Kic проводились на образцах с начальной трещи ной, что является обязательным при оценке прочностных свойств материалов в терминах механики разрушения.
В верхней части таблицы расположены высокопрочные ма териалы, склонные к хрупкому разрушению. Размер пластичес кой зоны, образующейся в таких материалах перед вершиной трещины, мал. При приближенных оценках можно считать, 4TOi материал обладает низкой трещиностойкостыо, если для н е т
* Данные для таблицы заимствованы |
из |
книги; У а й э т т О., |
Д ь ю - |
Х ь ю з Д. Металлы, керамики, полимеры. |
— |
М.: Атомиздат, 1979. — |
580 с. |
Т а б л и ц а 5.1
ВЯЗКОСТИ РАЗРУШЕНИЯ НЕКОТОРЫХ КОНСТРУКЦИОННЫХ МЕТАЛЛИЧЕСКИХ МАТЕРИАЛОВ ПРИ 20°С
|
Материал |
К 1с, М Па M '/J | |
вт. МПа |
(А'|с/°т)’. « « |
1 Мартенситностареющая сталь |
76 |
1800 |
1.8 |
|
"2 Высокопрочная легированная сталь: |
|
|
|
|
|
обычная термообработка |
98 |
1460 |
4.5 |
|
повышенный предел текучести |
51 |
1710 |
0.9 |
.3 Алюминиевый сплав |
30 |
540 |
3.1 |
|
4 |
Титановый сплав: |
|
|
|
|
обычная термообработка |
73 |
1060 |
4,8 |
|
повышенный предел текучести |
38 |
1100 |
1,2 |
•5 Среднеуглероднстая сталь |
54 |
260 |
43 |
|
<о |
Сталь для сосудов высокого давле |
|
|
|
|
ния |
209 |
470 |
1 200 |
.•выполняется условие (Ки/от 2<25 мм. Расчет прочности конст рукций из таких материалов часто требует привлечения методов механики разрушения при использовании Kic в качестве ос новной характеристики материала.
Стали низкой и средней прочности, расположенные на двух последних строках таблицы, обладают высокой трещиностойжостью в условиях, при которых проводились измерения (ком натные температуры, квазистатическое нагружение). Размер пластической зоны перед вершиной трещины в таких материа лах достигает десятков и даже сотен мм в предельно равновес ном состоянии. Прямое измерение Ки в условиях плоской де формации требует здесь использования образцов чрезвычайно ■большой толщины (см. раздел 3.1) и часто практически нереали зуемо. Кроме того, применяя Ки для расчета прочности конст рукций из таких материалов при обычных для приложений уме ренных толщинах, получают чрезмерно консервативные оценки,
что экономически неоправдано. |
В данной ситуации в качестве |
||||||
прочностной характеристики следу |
|
||||||
ет использовать |
трещиностойкость |
г »/ |
|||||
материала данной толщины Кс, не |
о>.« |
||||||
посредственно |
измеряемую в |
экс |
100 |
||||
перименте на образце, толщина ко |
|||||||
|
|||||||
торого совпадает с толщиной кон |
50 |
||||||
струкции. |
|
|
представлена типич |
||||
На |
рис. 5.1 |
|
|||||
ная зависимость измеряемых в экс |
|
||||||
перименте |
значений Кс и доли хруп |
|
|||||
кого излома F* от толщины образ- |
Рис. 5.1. Типичная зависи |
||||||
ма t. На |
графике, демонстрирую- |
мость трещиностойкости Кс |
|||||
щем в |
целом |
|
резко выраженную |
от ТОлщины металлического |
|||
зависимость |
трещниостоикостн Кс |
образца |
от толщины, можно отчетливо выделить три области — А, В, С. В области А при малых толщинах образца эта зависимость возрастающая, а поверхность разрушения является целиком шероховатой (волокнистой), что соответствует вязкому разру шению. Проявления хрупкого излома здесь отсутствуют — /гх= 0. В промежуточной области В трещиностойкость уменьша ется с увеличением толщины, а доля хрупкого излома (крис таллической поверхности разрушения) возрастает. В области С при больших толщинах образцов трещиностойкость постоянна и равна Kic, доля хрупкого излома близка к 100%.
Рис. 5.2. Геометрия поверхностей излома металлических образцов в областях А, В, С и соответствующие диаграммы нагрузка—смещение
На рис. 5.2 схематически показана геометрия поверхности излома образцов в каждой из выделенных областей. На рисун ке построены также диаграммы нагрузка—раскрытие трещины в месте установки датчика, фиксируемые в процессе испытания. Такие диаграммы принято называть диаграммами нагрузка— смещение, Р—V.
Вобласти А при малых толщинах образцов напряженное состояние в окрестности фронта трещины близко к плоскому. Трещина в этих условиях распространяется по механизму про дольного сдвига (тип III) под действием максимальных каса тельных напряжений, что приводит к полностью «косому» изло му под углом, близким к 45° по отношению к поверхности образ ца. С увеличением толщины сопротивление «соскальзыванию» верхней половины относительно нижней возрастает. Это в свою очередь вызывает увеличение трещиностойкости, которая при толщине t* достигает максимального значения. Затем начина ется уменьшение Кс из-за становящегося заметным влияния третьей составляющей напряжения с*.
Вобласти В излом имеет смешанный характер. В централь
ной части образца излом прямой, с блестящей (кристалличес кой) поверхностью, а по прилегающим к свободной поверхности краям — косой, аналогичный наблюдаемому в области А. Краевые зоны косого излома, получившие образное название
ПО