
книги / Технология термического производства. Способы наноструктурирования материалов
.pdfТаблица 2.10 Влияние циркуляции закалочной среды на уровень твердости и образование закалочных трещин
|
|
Ско- |
|
Сталь 45 |
|
|
Сталь 40Х |
|
|
Сталь У12 |
|
|
|
рость |
|
|
|
|
|
|
|
|
|
|
Охлаждаю- |
Твер- |
Число образцов |
Твер- |
Число образцов |
Твер- |
Число образцов |
||||
|
цирку- |
||||||||||
|
щая среда |
ляции, |
дость |
квадратных |
круглых |
дость |
квадратных |
круглых |
дость |
квадратных |
круглых |
|
|
м/с |
HRC |
10 мм |
12 мм |
HRC |
10 мм |
12 мм |
HRC |
10 мм |
12 мм |
61 |
|
0,0 |
55–60 |
2 |
0 |
52–56 |
3 |
1 |
48–65 |
0 |
0 |
Вода |
0,5 |
57–60 |
2 |
0 |
52–57 |
2 |
0 |
60–64 |
0 |
0 |
|
|
|
1,0 |
59–62 |
2 |
0 |
58–60 |
1 |
0 |
63–66 |
0 |
0 |
|
50% водный |
0,0 |
59–61 |
0 |
0 |
58–59 |
0 |
0 |
66–67 |
0 |
0 |
|
раствор |
0,5 |
60–62 |
0 |
0 |
58–59 |
0 |
0 |
66–67 |
0 |
0 |
|
NaOH |
1,0 |
60–62 |
0 |
0 |
58–59 |
0 |
0 |
67–68 |
2 |
1 |
|
|
|
|
|
|
|
|
|
|
|
|
61
погружать изделия в закалочный бак, обеспечивать достаточные зазоры между отдельными изделиями, а также между изделиями и приспособлениями, в которых они нагревались.
Как показал А.Г. Онисимов (данные приведены по источнику [13]), растворы солей и щелочей дают возможность получать на изделиях не только более высокую и однородную твердость, но и значительно меньшее по сравнению с чистой водой количество закалочных трещин (табл. 2.10).
Охлаждение в маслах
Несмотря на целый ряд недостатков: повышенную огнеопасность, недостаточную стабильность, более высокую стоимость, более низкую охлаждающую способность – масла применяются весьма широко.
Основным достоинством масел как закалочных жидкостей является небольшая скорость охлаждения в мартенситном интервале температур, что уменьшает опасность возникновения закалочных дефектов и приводит к постоянству закаливающей способности в широком интервале температур среды (20–150 °С). Охлаждающая способность закалочных масел зависит от их вязкости. Повышение температуры закалочного масла уменьшает вязкость и тем самым увеличивает охлаждающую способность. Для индустриальных масел, 12, 20 и 20В, широко применяемых для закалки деталей, наилучшая охлаждающая способность обеспечивается в интервале температур 40–80 °С, Основные свойства закалочных масел приведены в табл. 2.11.
В процессе длительной работы масла становятся непригодными для закалки. Изменение свойств закалочных масел обусловливается процессами окисления при контакте масла с нагретой металлической поверхностью изделий. Оксиды металлов, имеющиеся на поверхности изделии, вода, присутствующая в масле, ускоряют процессы окисления. Более интенсивно окисление масла протекает при повышенных
62
63
|
|
|
|
|
|
|
Таблица 2.11 |
||
|
|
Свойства закалочных масел |
|
|
|
|
|
||
|
|
|
|
|
|
|
|
|
|
|
Плотность |
|
Температура, °С |
Вязкость, π, |
|
Закаливаю- |
|||
|
|
при температуре, °С |
|
щая способ- |
|
||||
|
|
|
|
|
|
||||
Закалочные масла |
при температуре |
|
|
|
|
|
ность при |
|
|
|
|
|
|
|
|||||
|
18 °С |
|
вспышки |
воспламенения |
–20 |
40 |
|
температуре |
|
|
|
|
|
|
|
|
|
20 °С |
|
Индустриальное 12 |
0,876 |
|
165 |
– |
2,2–2,0 |
– |
|
0,35 |
|
Индустриальное 20 |
0,881 |
|
170 |
– |
2,8–3,2 |
– |
|
– |
|
Трансформаторное |
0,869 |
|
155 |
182 |
0,218 |
75 |
|
0,17 |
|
Машинное |
0,909 |
|
207 |
240 |
1,29 |
250 |
|
0,22 |
|
Хлопковое |
0,925 |
|
321 |
360 |
0,795 |
175 |
|
0,36 |
|
Оливковое |
0,917 |
|
310 |
360 |
0,80 |
200 |
|
0,37 |
|
Парафиновое |
0,879 |
|
163 |
188 |
– |
– |
|
0,29 |
|
Рапсовое |
0,874 |
|
193 |
229 |
– |
250 |
|
0,22 |
|
Пальмовое |
– |
|
224 |
252 |
0,449 |
220 |
|
0,15 |
|
Индустриальное 30 |
0,864 |
|
180 |
220 |
4,50 |
– |
|
– |
|
Индустриальное 45 |
0,900 |
|
190 |
240 |
5,5–7,0 |
– |
|
– |
|
Индустриальное 50 |
0,900 |
|
200 |
– |
6,0–7,5 |
– |
|
0,22 |
|
Цилиндровое |
– |
|
215 |
– |
– |
– |
|
– |
|
63
температурах. Для восстановления закалочных свойств окисленного масла осуществляют его регенерацию, или освежение, путем добавления свежего масла. К недостаткам закалочных масел следует также отнести необходимость дополнительной операции отмывки и обезжиривания поверхности закаленных изделий, а также пожароопасность.
Для сохранения светлой поверхности изделий к минеральным маслам добавляют органические вещества или различные фракции синтетических жирных кислот (типа CnH2nO2). Лучшие результаты получены при добавлении к минеральному маслу типа 12 около 20 % высокомолекулярной кислоты. Эту смесь успешно применяют для закалки изделий, нагреваемых в атмосфере эндогаза. Охлаждающая способность масла с такой присадкой выше, чем у масла без присадок. Высокую охлаждающую способность обеспечивает и смесь трансформаторного и авиационного МС-20 масел в пропорции 3:1. Светлая поверхность изделий сохраняется при применении смеси, содержащей 50 % авиационного МС-20 и 50 % вазелинового масла, а также при закалке изделий в 100%-ном авиационном масле МС-20.
Иногда в качестве ингибиторов (веществ, повышающих стойкость масел к окислению, а также улучшающих вязкость и другие свойства) применяют аминофенол в количестве 0,01–0,1 % от массы масла, ЦИАТИМ-330, ЦИАТИМ-331, ЦИАТИМ-334 и др.
В последние годы применяют и специальные закалочные масла с хорошими антиокислительными свойствами и сопротивлением загущению, характеристика которых приведена ниже:
Характеристика |
МЗМ-16 |
МЗМ-26 |
МЗМ-120 |
Температура вспышки, °С |
140 |
170 |
230 |
Вязкость при 50 °С, П |
2–4 |
3–4,5 |
13–19,5 |
Зольность, %, не более |
0,4 |
0,6 |
18 |
Рабочая температура, °С |
30–40 |
80–120 |
160–200 |
64
Широкое применение масел в практике закалки связано с особенностями охлаждения в маслах, которые обеспечивают резкое снижение образования трещин и закалочной деформации.
Кипение масел начинается при более высоких температурах, чем кипение воды (разница составляет 150–300 °С). Режим пленочного кипения в маслах распространяется на более узкую область температур, чем в воде (например,
вмасле индустриальном 20 – с 750 до 500 °С), режим пузырчатого кипения и максимум скоростей охлаждения относятся к более высоким температурам. Следовательно, главное различие в расположении стадий охлаждения в воде и масле
втом, что конвективный теплообмен в маслах захватывает более высокие температуры и распространяется на более широкий интервал температур (например, в масле индустриальном 20 – с температуры 380 °С до комнатной температуры). В воде этой области температур соответствует режим пузырчатого кипения и быстрое охлаждение. Скорость охлаждения
вводе в интервале мартенситного превращения в несколько раз превышает скорость охлаждения в масле [13].
При охлаждении в масле перепад температур между поверхностью и центром изделия значительно меньше, чем при охлаждении в воде и, следовательно, меньше закалочные напряжения и вероятность образования трещин. Кроме того, охлаждающая способность масел мало изменяется с изменением температуры масла.
Оптимальной температурой является интервал 40–80 °С. Допускать большего нагрева масла в целях противопожарной безопасности не следует.
Для охлаждения масла в закалочные баки встраивают змеевики, по которым проходит проточная холодная вода или холодный воздух. Более эффективно охлаждение в специальных маслоохладительных установках. Маслоохладители могут быть с водяным (рис. 2.25) и воздушным охлаждением.
65
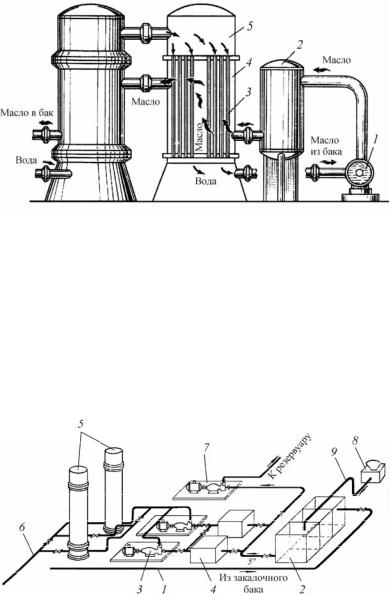
Рис. 2.25. Маслоохладитель с водяным охлаждением
Как видно из рис. 2.25, масло из закалочного бака подается насосом 1 в маслосборник 2, а оттуда в колонку 4, где и охлаждается. Охлаждающая вода из резервуара 5, расположенного в верхней части колонки, по трубкам 3 идет вниз, а масло противотоком идет снаружи трубок. Охлажденное масло подается в закалочный бак. Чаще всего в термических цехах используется централизованное охлаждение масла из всех закалочных баков. Схема такой системы дана на рис. 2.26.
Рис. 2.26. Централизованная установка для охлаждения закалочного масла
66
Масло из закалочных баков, расположенных в цехе, поступает по трубопроводу 1 в бак 2 с тремя секциями. В одной из секций бака масло отстаивается, другая включена в систему циркуляции и охлаждения, третья находится в процессе чистки. Из бака масло под всасывающим действием насоса 3 проходит через фильтр 4 и нагнетается через трубчатые маслоохладители 5 в напорную магистраль 6, из которой поступает в закалочные баки (в схеме дублируются насосные установки и фильтры как резервные на случай чистки или аварии). В схему включена насосная установка 7 для откачки отработанного масла из бака 2, а также сливная воронка 8 с трубопроводом 9, соединяющим ее с баком. Воронка служит для наполнения бака маслом из емкостей, находящихся вне помещения цеха.
Общая емкость всех 3 отсеков системы должно быть на 30–40 % больше объема всего масла, находящегося в системе и баках. Маслоохладители в зависимости от их мощности имеют производительность от 10 до 100 м3/ч.
Конструкции и типоразмеры применяемых закалочных баков должны соответствовать нагревательному оборудованию.
Способы погружения изделий в закалочные баки
Способ погружения детали (инструмента) в закалочную жидкость должен обеспечивать равномерное охлаждение различных частей изделия, сквозной отток образующихся при кипении жидкости паров, гарантировать отсутствие коробления горячих изделий под действием собственного веса или в результате неравномерного охлаждения.
Практикой обработки выработан ряд правил погружения закаливаемых изделий в жидкие среды (рис. 2.27).
67
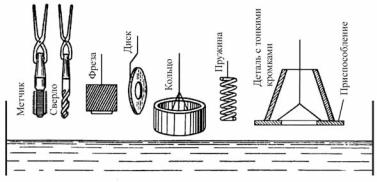
Рис. 2.27. Рекомендуемые способы погружения изделий
взакалочные баки
1.Изделия, имеющие неодинаковую толщину, должны погружаться сначала толстой, а затем тонкой частью. В некоторых случаях, при наличии тонких кромок на цилиндрических или конических изделиях, рекомендуется применение приспособлений, увеличивающих тепловую инерцию этих кромок.
2.Изделия с замкнутой полостью должны погружаться так, чтобы открытая сторона полости, в целях обеспечения выхода пара, была обращена вверх. Погружение изделий вы-
ходом полости вниз вызывает |
скопление пара в полости |
|
и образование паровых мешков. |
|
|
3. Длинные изделия |
типа |
ходовых винтов, разверток |
и сверл во избежание |
коробления должны погружаться |
встрого вертикальном положении.
4.Тонкие плоские детали, имеющие форму дисков, следует погружать на ребро.
5.Тонкостенные кольца должны погружаться так, чтобы их образующая занимала вертикальное положение.
6.Закалку листовых деталей необходимо производить на ребро. При закалке тонких листовых деталей пакетами погружение их может производиться и плашмя, но с обяза-
68
тельной установкой между отдельными деталями металлических прокладок. Высота прокладок должна быть тем большей, чем толще детали и чем больше их площадь. Количество прокладок должно обеспечивать отсутствие коробления изделий.
7.Охлаждение изделий, закаливаемых в приспособлениях или на цепях конвейера, должно производиться так, чтобы при этом обеспечивалось равномерное охлаждение всей их поверхности. Поэтому нельзя допускать скопления изделий, плотно прилегающих друг к другу.
8.Охлаждение тонких изделий, обладающих недостаточной конструктивной жесткостью в нагретом состоянии (дисков, шестерен, валиков, рессор и пр.), рекомендуется производить в закалочных прессах или в специальных закалочных устройствах, а в некоторых случаях – в металлических плитах.
Таким образом, правильный выбор как способа охлаждения, так и охлаждающей среды при закалке – гарантия качества закалки. Масло по охлаждающей способности резко отличается от воды, и этот разрыв до сих пор остается незаполненным, т.е. нет эффективных и качественных по своему действию промежуточных между водой и маслом закалочных сред. Таким образом, вопрос о создании универсальных сред, обеспечивающих во всех температурных интервалах требуемые условия охлаждения, остается актуальным. В источниках [1, 2, 12, 13] рассмотрено применение водных растворов полимеров и органических соединений в качестве закалочных сред, но все они мало технологичны, дороги, дефицитны, нестабильны во времени и значительно изменяют свою охлаждающую способность при изменении температуры.
69
Контрольные вопросы
1.Что понимают под качеством нагрева при термообработке стали?
2.Какие контролируемые атмосферы нельзя использовать в низкотемпературных печах? Почему?
3.Применение атмосфер типа КГО при термообработке стали.
4.Наиболее сильные компоненты-окислители при нагреве стали. Приведите реакции взаимодействия их со сталью.
5.Факторы, способствующие обезуглероживанию стали при ее нагреве.
6.Какие атмосферы рекомендуют применять при светлой закалке среднеуглеродистых сталей?
7.Типы контролируемых атмосфер. Условия их полу-
чения.
8.На чем основан контроль состава контролируемых атмосфер?
9.Способы защиты поверхности нагреваемых изделий от окисления и обезуглероживания.
10.Применение атмосфер типа ПС, ПСО при термообработки стали.
11.Изменение микроструктуры поверхности изделия из сталей разного состава при нагреве их в окислительной атмосфере.
12.Что такое идеальная кривая охлаждения? Чем обусловлен ее вид?
13.Основные требования к охлаждающей среде при за-
калке.
14.Условия охлаждения и закалочные среды при изотермической и ступенчатой закалке.
15.Основные охлаждающие среды при закалке, их достоинства и недостатки.
70