
книги / Технология термического производства. Способы наноструктурирования материалов
.pdf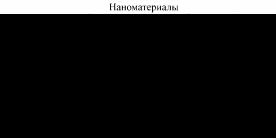
впрактику в самых различных областях деятельности человека (например, наноэлектроника, наномедицина, наноэнергетика и др.).
По данным Исследовательской службы конгресса США
(Congressional Research Service), мировая промышленность использует нанотехнологии в процессе производства как минимум 80 групп потребительских товаров и свыше 600 видов сырьевых материалов, комплектующих изделий и промышленного оборудования. Функционируют свыше 16 тыс. нанотехнологических компаний (конец 2006 г.), число которых
впоследнее время удваивается каждые полтора года. Объем мировых инвестиций в наноиндустрию с 1996 по 2006 г. вырос в 50 раз и составил к концу 2006 г. более 110 млрд долларов. К сожалению, на Россию приходится только менее 0,5 % всех мировых «наноинвестиций». К 2015 г. согласно прогнозам министерства торговли Великобритании спрос на результаты деятельности в области нанотехнологий в этой стране составит не менее 1 трлн долларов в год, а численность специалистов, занятых в ней, возрастет до 2 млн человек (рис. 7.1). В связи с этим следует ожидать появления спроса на выпускников вузов с дополнительным образованием в области нанотехнологий.
Рис. 7.1. Основные секторы рынка продукции нанотехнологий к 2015 г. (млрд долларов США в год, прогноз Министерства торговли Великобритании)
211
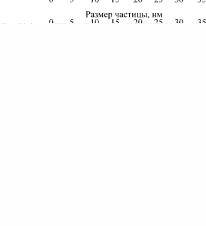
Для общего машиностроения наиболее интересно получение компактных материалов субмикрокристаллического (СМК) и нанокристаллического (НК) строения. В зависимости от величины структурных элементов наноструктур значительно изменяются все свойства наноматериалов. Для нанокристаллических металлических материалов свойства определяются размерами отдельных зерен, свойствами граничного слоя, а также коллективным взаимодействием основных составляющих структуры с поверхностными слоями частиц. В нанокристаллических материалах доля граничного слоя быстро возрастает при измельчении зерен от 100 до 4−5 нм (рис. 7.2). Считая, что зерна имеют сферическую форму, и полагая толщину слоя 1 нм (это соответствует 2–3 атомным слоям для большинства металлов), получаем следующие соотношения между диаметром зерна и объемной долей поверхностного слоя [33]:
Диаметр зерна (частицы), нм...... 100 50 25 20 10 6 4
Объемная доля поверхностного слоя, % .......................................... 6 12 24 30 60 100 150
Рис. 7.2. Доля поверхностных и объемных атомов в наноматериалах [39]
212
Таким образом, в нанокристаллических материалах, начиная с диаметра зерен 6 нм, объем граничного слоя становится больше объема кристаллов.
По мере того как размеры зерен или частиц становятся все меньше и меньше, все большая доля атомов оказывается на границах или свободных поверхностях и поведение УДМ часто определяется именно процессами на границе частиц или зерен.
Например, нанокерамика может заметно пластически деформироваться за счет скольжения по границам, что находится в сильном противоречии с хрупким поведением обычной керамики.
Уменьшение размера зерна металла с 10 мкм до 10 нм повышает прочность примерно в 30 раз. Величина зерна существенно влияет также на твердость и другие свойства материалов. Например, твердость нанокристаллических материалов при t < 0,4−0,5tпл в 2–7 раз выше, чем у соответствующих обычных кристаллических аналогов, твердость которых подчиняется известной зависимости Холла-Петча
HV = HV0 +kd −1/ 2 ,
где НV0 − твердость по Виккерсу монокристалла; k − коэффициент пропорциональности; d − размер зерна.
Аналогично можно записать закон Холла-Петча и для предела текучести материала:
σm = σ0 + kd –1/2,
где σ0 − напряжение текучести монокристалла, d – размер зерна, наночастицы или упорядоченного фрагмента наноструктуры.
Нанокристаллические материалы отличаются повышенной прочностью, что справедливо как для однофазных (медь, палладий), так и для многофазных, полученных кристаллизацией аморфных сплавов. Предел текучести таких материалов
213
в 2–3 раза, а временное сопротивление в 1,5–8 раз выше, чем у соответствующих мелкозернистых (d не более 5–10 мкм) аналогов.
Нанокристаллические материалы имеют высокие демпфирующие свойства, так как из-за различия модулей упругости самих зерен и граничных слоев упругие колебания распространяются неоднородно и существенно рассеиваются. Например, у меди с размером зерен 200 нм уровень фона внутреннего трения, являющегося мерой демпфирующей способности, в 2–3 раза выше, чем у серого чугуна, который считается хорошим демпфером.
Теплофизические свойства нанокристаллических и обычных материалов отличаются из-за влияния масштабного фактора (размера зерна), а также содержания и состояния граничных слоев. В порошковых сплавах и в деформированных металлических сплавах после рекристаллизационного отжига состояние граничного слоя максимально неравновесное. При 20–25 °С с заметной скоростью и полнотой развиваются процессы рекристаллизации, а следовательно, изменяются свойства. В порошковых керамических материалах свойства более устойчивы, так как для их изменения требуется отжиг при 300–500 °С.
Теплоемкость нанокристаллических сплавов при низких температурах в 1,2–2 раза выше, чем у соответствующих обычных кристаллических аналогов, а при 20–25 °С несколько выше ее из-за высокой теплоемкости граничного слоя. Нанокристаллические сплавы сильнее расширяются при нагреве из-за более интенсивного (в 2,5–2 раз) расширения граничного слоя по сравнению с зернами. У нанокристаллической меди при размере зерен 8 нм коэффициент теплового расширения вдвое превысил его значение у поликрасталлической меди.
Удельное электросопротивление нанокристаллических материалов выше, чем у соответствующих аналогов, так как
214
электроны проводимости сильнее рассеиваются на границах зерен. Так, у нанокристаллических меди, никеля и железа с размерами зерен 100–200 нм удельное электросопротивление при 20 °С возрастает соответственно на 15, 35 и 55 %. Уменьшение диаметра зерна меди до 7 нм повышает удельное электросопротивление в несколько раз.
Способы получения и применение нанокристаллических металлических материалов
В компактном виде нанокристаллические материалы получают тремя способами:
1)переработкой частиц размером <100 нм методами порошковой технологии в компактный материал;
2)кристаллизацией аморфных металлических сплавов в контролируемых условиях;
3)рекристаллизационным отжигом интенсивно деформированных металлических сплавов.
Ближе всего к традиционным способам получения и обработки обычных металлических материалов третий путь получения НКМ.
Интенсивную деформацию (ИПД) можно осуществить, например, используя сложные схемы деформации, препятствующие разрушению: кручение под квазигидростатическим давлением (наковальня Бриджмена – рис. 7.3, а) либо метод равноканального углового прессования (рис. 7.3, б).
Интенсивная деформация (при соответствующих условиях) металлов Cu, Co, Fe, Ni, Pd позволяет получить в них однородную зеренную субмикрокристаллическую и нанокристаллическую структуру со средним размером зерен
0,1…0,2 мкм [40, 42, 43]. При исследовании структуры на электронном микроскопе на электронограммах четко фиксируются рефлексы от отдельных зерен. Границы зерен при этом оказываются неравновесными, что связано с повышенной
215
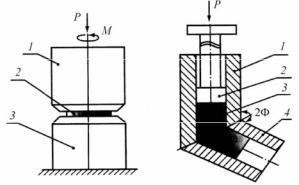
аб
Рис. 7.3. Схемы интенсивного деформирования: а – наковальня Бриджмена (1, 3 – наковальни, 2 – образец); б – равноканальное угловое прессование (1, 4 – пересекающиеся каналы, 2 – пуансон, 3 – образец)
плотностью зернограничных дислокаций, образовавшихся в процессе пластической деформации.
Получение однородной СМК и НК структуры путем сверхпластической деформации (СПД) обеспечивает материалу непосредственно или в сочетании с термической обработкой высокий уровень конструкционной прочности и стабильность свойств во времени, особенно в сплавах сложного состава. Весьма показателен в этом отношении сплав систе-
мы Mg – Li МА21 (рис. 7.4) [42].
Особенно существенно можно повысить свойства материалов, если использовать обработку в сверхпластических условиях в сочетании с фазовыми превращениями (деформа- ционно-термическая обработка в условиях сверхпластического течения).
В многофазных сплавах можно получить более мелкие нанокристаллические зерна. При этом необычно то, что такие сплавы способны изменить и свой фазовый состав [43]. Например, инструментальная сталь У12, имеющая после норма-
216
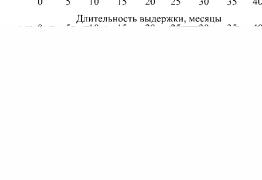
лизации структуру перлитного типа, в наноструктурном состоянии (d = 20 нм), полученном ИПД путем кручения в наковальнях Бриджмена, становится безцементитным твердым раствором. Не исключено, что исчезновение цементита связано с растворением углерода в зернограничной фазе.
Рис. 7.4. Влияние длительности выдержки при комнатной температуре на стабильность механических свойств сплава МА21: y – обычная горячая деформация, закалка, старение; – СП-деформация, закалка, старение
При использовании рекристаллизационного отжига нанокристаллических материалов следует учитывать особенности их поведения при нагреве. Например, для нанокристаллических меди и никеля возврат наблюдается при температуре немногим выше 100 °С, а начало роста зерен при 150– 200 °С, а для умеренно деформированного (40–70 %) никеля начало рекристаллизации – при температуре 700–800 °С.
В настоящее время технологии СПД и СПР (сверхпластическая раскатка) применяются в промышленности при изготовлении деталей из титановых сплавов, жаропрочных никелевых сплавов [43].
В получении компактных нанокристаллических материалов весьма распространены традиционные методы по-
217
рошковой технологии [40, 44], то есть различные виды прессования и спекания, модифицированные применительно к нанопорошкам. Модификация сводится к выбору оптимальных параметров компактирования и спекания нанопорошков. Такими параметрами являются: давление прессования и способы его приложения, температурный режим спекания, среда и скорость проведения процесса.
Применяемые способы компактирования нанопорошков различны, это, например, ультразвуковое прессование, холодное статическое прессование с односторонним или двусторонним приложением давления и др. Значительные трудности при компактировании нанопорошков связаны с их большой удельной поверхностью: от 20−40 м2/г при диаметре частиц 100 нм и до 110−120 м2/г при диаметре 10 нм; они легко захватывают примеси, особенно кислород, а также водород.
Порошки трудно собирать и транспортировать к месту переработки. Для предупреждения их окисления предлагается, в частности, окружать каждую частицу защитной пленкой, которая должна разрушаться и удаляться без остатка при нагреве порошков или прессовок при спекании. Нанокристаллические порошки плохо прессуются. В компактном материале остаточная пористость достигает 10 % (об.), у металлических нанокристаллических материалов ее удается сократить до 3 % (об.), в керамических материалах (у которых порошки прессуются еще хуже) остаточная пористость составляет 15 % (об.). Из-за пористости свойства порошковых нанокристаллических материалов непостоянны. Сложность получения постоянства свойств связана также с интенсивной рекристаллизацией при спекании. Сокращая продолжительность спекания, можно уменьшить рекристаллизацию и рост зерен. В то же время получение и переработка нанокристаллических порошков является наиболее универсальным методом, пригодным для создания нанокристаллической структуры в разнообразных материалах.
218
Работа [40] дает наглядное описание методов синтеза нанокристаллических порошков. При синтезе нанопорошков была открыта новая аллотропная модификация углерода, названная фуллереном. Название дано по фамилии американского архитектора Б. Фуллера, который запатентовал аналогичную структурную основу для строительства сферических конструкций (павильон США на выставке Экспо-67 в Монреале). За открытие фуллеренов Р. Карл, Х. Крото
иР. Смалли в 1996 г. Получили Нобелевскую премию в области химии.
Особенностью фуллеренов является упорядоченное размещение атомов углерода на сферической поверхности. Фуллерены, молекулы которых содержат 60; 70 и 82 атома угле-
рода, устойчивы; их обозначают С60, С70, С82. Молекулы фуллеренов представляют собой углеродную оболочку диаметром ~ 1 нм со сравнительно большой внутренней полостью (~ 0,7 нм).
Фуллерены получают электродуговым распылением графита в атмосфере гелия при давлении газа ~ 104 Па. В результате горения дуги образуется сажа, которая конденсируется на холодной поверхности. Собранная сажа обрабатывается в кипящем толуоле или бензоле. После выпаривания раствора образуется черный конденсат, который примерно на
10–15 % состоит из фуллеренов С60 и С70. Вместо электрической дуги используют также электронно-лучевое испарение
илазерный нагрев.
Наиболее высокую симметрию и, следовательно, наибольшую стабильность имеет молекула С60 (рис. 7.5). Атомы углерода в молекуле С60 образуют замкнутую полую сферическую поверхность, состоящую из 5- и 6-членных колец, причем каждый атом имеет координационное число, равное 3, и находится в вершинах двух шестиугольников и одного пятиугольника. Высокой стабильностью обладает так же фуллерен С70. Фуллерены можно рассматривать как сфериче-
219

скую форму графита, так как механизмы межатомного связывания в фуллерене и объемном графите в большой степени подобны.
С70
Рис. 7.5. Структура наиболее важных фуллеренов С60 и С70. Молекула С60 построена как футбольный мяч и имеет диаметр около 0,7 нм. Все фуллерены содержат гексагональные шестичленные
ипентагональные пятичленные кольца из атомов углерода
Вначале 2001 г. обнаружили новую фуллереноподобную форму С48Н12, в которой по сравнению с обычным фуллереном С60 пятая часть атомов углерода замещена атомами азота (рис. 7.6).
Рис. 7.6. Структура фуллерена C48N12 (сплошная линия показывает положение оси симметрии)
220