
книги / Технология термического производства. Способы наноструктурирования материалов
.pdfЭти же графики могут быть использованы для определения времени нагрева и удельной мощности при других частотах.
Иногда поверхностной термообработке подвергают изделия малого диаметра. Такие режимы для D2 = 0,54÷2,0 см приведены в табл. 5.10.
Таблица 5.10
Зависимость времени нагрева и удельной мощности от диаметра цилиндра и глубины закаленного слоя при f ≥ 440 кГц
D2, см |
|
|
|
хк, см |
|
|
|
|
0,1 |
|
0,2 |
|
0,5 |
||
|
tк, с |
P0, кВт/см2 |
tк, с |
|
P0, кВт/см2 |
tк, с |
P0, кВт/см2 |
0,5 |
0,77 |
0,85 |
– |
|
– |
– |
– |
1 |
1,47 |
0,8 |
3,14 |
|
0,416 |
0,425 |
0,33 |
1,5 |
1,6 |
0,8 |
4,53 |
|
0,408 |
6,9 |
0,28 |
2 |
1,9 |
0,8 |
5,9 |
|
0,39 |
8,5 |
0,28 |
Примечание: хк – глубина закаленного слоя; D2 – диаметр цилиндра; tк – время нагрева; Р0 – удельная мощность.
Для получения времени нагрева при частоте 70 кГц соответствующее его значение, полученное на основании графика рис. 5.17, следует разделить на 1,2. Удельная мощность наоборот увеличивается также в 1,2 раза.
Время нагрева и удельная мощность при частоте 8000 Гц с большой точностью могут быть получены из графиков, приведенных на рис. 5.17, 5.18.
Во всех случаях удельная мощность вычислена без учета отвода теплоты в осевом направлении, что с достаточно большой точностью справедливо при одновременном нагреве всей поверхности детали. При нагреве участка поверхности или при непрерывно-последовательном нагреве необходимо полученную на основании графиков удельную мощность увеличить в 1,2 раза.
181
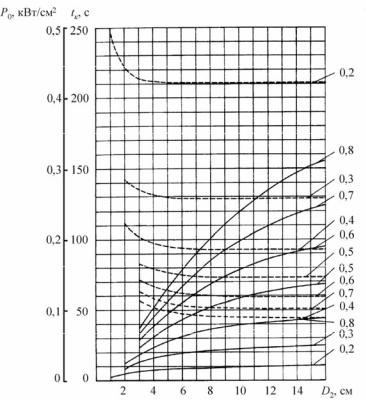
Аналогичные графики построены для плоских поверхностей.
Рис. 5.17. Зависимость времени нагрева tк (сплошные линии) и удельной мощности Р0, сообщаемой детали (штриховые линии), от диаметра D2 нагреваемого цилиндра при частоте выше 250 кГц.
Цифры на кривых указывают глубину закаленного слоя в см
182
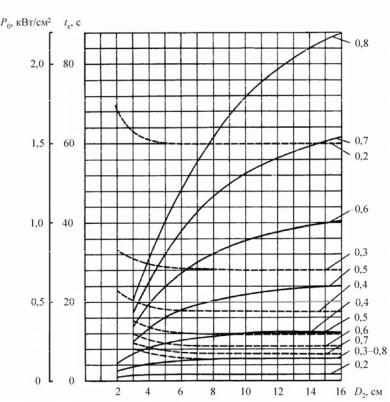
Рис. 5.18. Зависимость времени нагрева tк (сплошные линии) и удельной мощности Р0, сообщаемой детали (штриховые линии), от диаметра D2 нагреваемого цилиндра при частоте тока 10000 Гц.
Цифры на кривых указывают глубину закаленного слоя в см
183
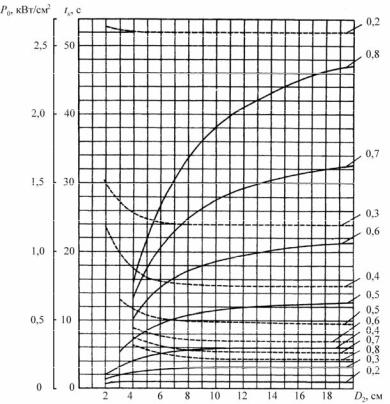
Рис. 5.19. Зависимость времени нагрева tк (сплошные линии) и удельной мощности Р0, сообщаемой детали (штриховые линии), от диаметра D2 нагреваемого цилиндра при частоте тока 2500 Гц.
Цифры на кривых указывают глубину закаленного слоя в см
На рис. 5.20–5.22 приведены зависимости времени нагрева и удельной мощности от толщины плоской детали для различных глубин закаленного слоя при высокой частоте и частотах 8000–10 000 и 2500 Гц, вычисленные для конструкционной стали при температуре нагрева поверхности 900 °С. Эти же зависимости с несколько меньшей точностью могут быть использованы и для случая нагрева внутренних
184
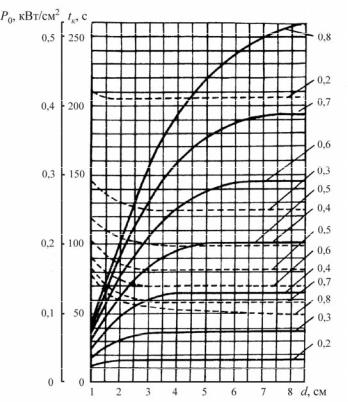
поверхностей. Если плоская деталь нагревается с двух сторон, то в качестве d при пользовании графиками следует брать половину ее толщины. Как указывалось выше, при отклонении температуры поверхности от 900 °С на ±50 °С время нагрева изменяется примерно в 1,7 раза, а удельная мощность – в 1,5 раза.
Рис. 5.20. Зависимость времени нагрева tк (сплошные линии) и удельной мощности P0 (штриховые линии) от толщины плоской детали d при частоте выше 250 кГц. Цифры на кривых указывают глубину закаленного слоя в см
Например, при закалке плоского тела толщиной 4 см, глубиной 0,6 см при частоте 2500 Гц на основании кривых
185
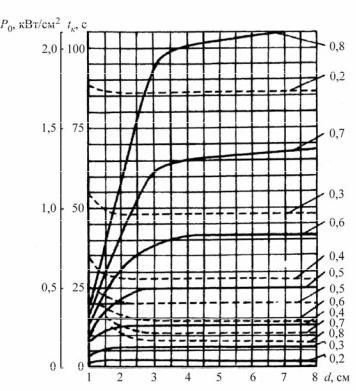
рис. 5.22 находим время нагрева tк = 31 с и удельную мощность Р0 = 0,36 кВт/см2.
Рис. 5.21. Зависимость времени нагрева tк (сплошные линии) и удельной мощности Р0 (штриховые линии) от толщины плоской детали d при частотах 8000–10 000 Гц. Цифры на кривых указывают глубину закаленного слоя в см
Удельную мощность и время нагрева для частоты 4000 Гц можно получить на основании графика на рис. 5.22. Как было сказано раньше, время умножается на 1,25 и мощность – на 0,83.
Электрический расчет индуктора включает определение необходимой мощности индуктора, напряжение на индукто-
186
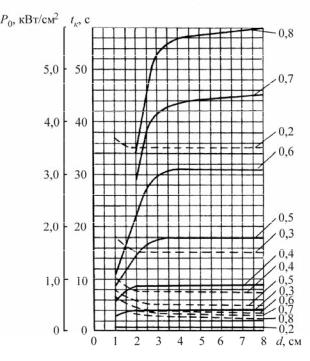
ре и ток индуктора, сопротивление индуктора, расчет потребной мощности преобразователя частоты.
Теоретические расчеты и эксперименты показали, что для различных индукторов при определенных частоте и удельной мощности напряжение на единицу длины индуктирующего провода и ток, рассчитанный на единицу ширины паза, при зазорах 4–6 мм колеблются в сравнительно небольших пределах.
Рис. 5.22. Зависимость времени нагрева tк (сплошные линии) и удельной мощности (штриховые линии) от толщины плоской детали d при частоте 2500 Гц. Цифры на кривых указывают глубину закаленного слоя в см
В среднем можно считать, что при удельной мощности 1 кВт/см2 будем иметь:
187
при частоте 10000 Гц
U0 = 1,45 В/см; I0 = 2400 А/см;
при частоте 8000 Гц
U0 = 1,3 В/см; I0 = 2500 А/см;
при частоте 4000 Гц
U0 = 0,93 В/см; I0 = 3000 А/см;
при частоте 2500 Гц
U0 = 0,75 В/см; I0 = 3400 А/см,
где U0 – напряжение на 1 см длины индуктирующего провода при удельной мощности 1 кВт/см2; I0 – ток на 1 см ширины паза в магнитопроводе при удельной мощности 1 кВт/см2.
Электрический расчет включает также определение всех геометрических параметров индуктора.
Методики расчетов приводятся в специальной литературе, примеры расчетов даны в источниках [24, 29, 30, 32].
Контрольные вопросы
1.Физические основы индукционного нагрева.
2.Применение индукционного нагрева при термической обработке.
3.Преимущества индукционного нагрева.
4.Энергетические и термические параметры индукционного нагрева.
5.Особенности нагрева и охлаждения при поверхностной закалке ТВЧ.
6.Источники ТВЧ (типы преобразователей).
7.Методы поверхностной закалки ТВЧ.
8.Конструкции и типы индукторов.
9.Детали и стали для поверхностной закалки.
188
10.Технология поверхностного упрочнения при индукционном нагреве.
11.Сравнение процессов отпуска и самоотпуска.
12.Изменение структуры среднеуглеродистых сталей при поверхностной индукционной закалке.
13.Выбор частоты при индукционном нагреве.
14.Методики определения времени (tк) и удельной мощности (Р0) индукционного нагрева.
15.Определить (tк) и (Р0) для валика диаметром 120 мм, закаливаемого на глубину 5 мм
– при f = 2500 Гц;
– при f = 8000 Гц.
189
6. ТЕРМОЦИКЛИЧЕСКАЯ ОБРАБОТКА МЕТАЛЛОВ
Термическая обработка является эффективным и простым методом повышения работоспособности компактных металлических материалов. Основные технологические параметры классических способов термической обработки и их влияние на формирование структуры стали рассмотрены в данной работе ранее.
Традиционным способам термической обработки свойственно некоторое принципиально важное ограничение: неспособность повышать одновременно прочность и пластичность или, сохраняя значения одних свойств, например пластических, увеличивать показатели прочности, и наоборот. А именно такое комплексное повышение характеристик прочности и пластичности наиболее эффективно для обеспечения надежной работы конструкционных материалов, снижения массы и габарита машин и т.д.
Сформулированная задача сейчас решается в основном путем совмещения термической обработки с упрочнением от пластической деформации. На этой основе разработаны такие новые методы упрочнения металлов и сплавов, как механикотермическая обработка (МТО) и термомеханическая обработка (ТМО). Различие этих обработок состоит в том, что в первом случае вначале дают механическое упрочнение пластическим деформированием и затем производят термическую обработку, а во втором механическое упрочнение осуществляется в процессе термической обработки. Применение МТО и ТМО к металлическим материалам дает положительные результаты, повышая уровень прочности обрабатываемого материала. Однако МТО и ТМО не нашли еще широкого применения в производстве в силу их технологической сложности.
Известно [18, 33, 34, 36], что на конечные свойства термообработанных материалов влияет в первую очередь вели-
190