
книги / Системы, технологии и организация услуг в автомобильном сервисе. Ч. 1
.pdfагрегата, узла, системы, детали. Получение такой информации возможно путем непосредственного измерения параметров технического состояния данного автомобиля и сравнения их текущих значений с нормативами.
Автомобиль представляет собой сложную техническую систему. Как известно, качественной мерой, позволяющей оценить состояние системы или ее элементов, а также проявление свойств системы, является параметр (показатель). С точки зрения оценки состояния системы и проявления ее свойств различают параметры структурные и выходные.
На основании анализа и классификации по методу назначения или определения нормативные значения параметров можно разделить на три группы.
К первой группе параметров относятся нормативные значения, задаваемые на уровне государственных стандартов или других руководящих документов общегосударственного значения. Нормативы этой группы назначаются для параметров систем, обеспечивающих безопасность автомобиля и определяющих его влияние на окружающую среду. К ним относятся параметры, определяющие состояние тормозных систем, рулевого управления, шин и колес, системы освещения и сигнализации и другие, а также параметры токсичности отработавших газов, шума, вибрации и т.д. Эксплуатация автомобилей в любых условиях с отклонениями от этих параметров недопустима.
В настоящее время в Российской Федерации работают ГОСТ Р 51709–2001 «Автотранспортные средства. Требования безопасности к техническому состоянию и методы проверки» (с изм. № 1), ГОСТ Р 52033–2003 «Выбросы загрязняющих веществ с отработавшими газами. Нормы и методы контроля при оценке технического состояния», ГОСТ Р 52160–2003 «Автотранспортные средства, оснащенные двигателями с воспламенением от сжатия. Дымность отработавших газов. Нормы и методы контроля при оценке техни-
151
ческого состояния», ГОСТ Р 17.2.02.06-99 «Охрана природы. Атмосфера. Нормы и методы измерения содержания окиси углерода и углеводородов в отработавших газах газобаллонных автомобилей». Примером документа общегосударственного значения могут быть «Правила дорожного движения Российской Федерации».
Ко второй группе параметров относятся нормативы параметров, изменение которых не зависит от условий эксплуатации автомобилей, а определяется только конструктивными и технологическими факторами, такими как применяемые материалы, технология изготовления, форма и размеры и т.п. Эти нормативы обычно оговариваются в технических условиях завода-изготовителя или в инструкции по эксплуатации изделия и являются одинаково достоверными для различных условий эксплуатации. Это, например, нормативные значения тепловых зазоров в газораспределительном механизме двигателя, зазор между электродами свечи зажигания и т.д.
К третьей группе относятся нормативы для параметров, на изменение которых в зависимости от наработки существенное влияние оказывают условия эксплуатации. В этом случае нормативные значения одного и того же параметра для автомобилей, работающих на различных видах перевозок, могут существенно (в 1,5–2 раза) отличаться.
В процессе диагностирования можно обнаружить такие неисправности, как нарушения в работе двигателя и приборов системы зажигания, отклонение углов установки колес, а также произвести некоторые виды регулирования (например, регулирование системы управления двигателем или – тормозных усилий на каждом колесе, балансировку колес и т.д.).
Диагностические параметры (ДП) выходных рабочих процессов характеризуют функциональные свойства автомобиля, агрегата, системы.
Примеры: мощность двигателя, скорость автомобиля, расход топлива, тормозной путь.
152
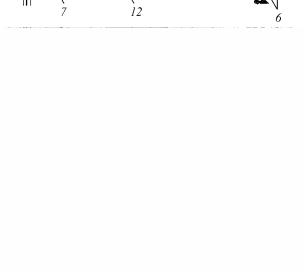
Диагностические параметры сопутствующих про-
цессов сопровождают работу двигателя, агрегата, системы. Примеры: температура агрегата, материала; уровень
шума или вибрации; содержание продуктов износа в масле; содержание вредных веществ в отработавших газах.
Типовой диагностический комплекс
Полная компьютерная диагностика автомобиля выполняется на стационарных проездных комплексах многовариантной конфигурации, имеющих возможность дальнейшего расширения функций (рис. 1.28).
Рис. 1.28. Схема типового стационарного проездного диагностического комплекса: 1 – тестер (детектор) увода автомобиля от направления прямолинейного движения; 2 – амортизаторный стенд; 3 – тормозной стенд; 4 – люфтдетекторный стенд; 5 – газоанализатор; 6 – дымомер; 7 – анализатор света фар; 8 – тестер тормозной жидкости; 9 – тестер охлаждающей жидкости и электролита; 10 – диагностический центр; 11 – дисплей вывода результатов проверок систем автомобиля в графическом виде; 12 – смотровая канава для
визуального осмотра узлов и деталей подвески
153
Комплекс построен по модульному принципу, что позволяет укомплектовывать его оборудованием исходя из индивидуальных возможностей предприятия. В технологическую линию легко интегрируются дополнительно любые необходимые стенды и приборы.
Каждая группа стендов и приборов, входящих в состав комплекса, оснащена специальными программируемыми устройствами для взаимодействия системы управления с оборудованием. Данные контроля параметров технического состояния агрегатов и систем автомобиля со всех стендов обрабатываются компьютером и могут быть выведены на дисплей в графическом либо в цифровом виде. При необходимости результаты проверок можно распечатать на встроенном принтере. Вся информация сохраняется в памяти компьютера, что позволяет создать базу данных, и является веским аргументом в случае с разногласий с клиентом.
Технологический процесс диагностирования на комплексе строится таким образом, чтобы за один проход автомобиля можно было проверить максимум параметров: увод автомобиля от направления прямолинейного движения, состояние амортизаторов и тормозов, износ шарниров подвески, качество тормозной жидкости, плотность охлаждающей жидкости и электролита, токсичность выхлопных газов, правильность регулирования света фар (и произвести их регулирование).
Таким образом, итоговый отчет представляет собой максимум информации об автомобиле и исправности его систем. При этом программа предусматривает разбивку всех измеренных параметров на группы, а также занесение в перечень данных, не измеряемых на диагностическом комплексе.
Поскольку полная диагностика автомобиля включает в себя еще и визуальный осмотр узлов и деталей подвески, протокол состояния автомобиля можно пополнить описанием состояния шин, колесных дисков, световых приборов
154
и многого другого, вплоть до лакокрасочного покрытия кузова.
Диагностические комплексы являются наиболее совершенным решением вопроса комплексной механизации диагностических работ, технологических, организационных и других вопросов любого предприятия. Представляя собой оборудование высокого технического уровня, они аккумулируют в себе лучшие достижения в области приборостроения, электроники и других областей науки и техники. Сложные комплексы называются диагностическими системами.
Многие виды проверки технического состояния автомобиля, его агрегатов, узлов и механизмов не могут быть автоматизированы и требуют непосредственного участия специалистов, поскольку выполняются путем визуального осмотра, прослушивания, на ощупь или с применением простейших контрольных приборов (например, контроль поверхностей на отсутствие коррозии, вмятин и повреждений окраски, контроль состояния гидропривода тормозной системы и т.п.). Поэтому любая автоматизированная система должна включать в себя и ручные устройства для выполнения оператором осмотра и некоторых других операций.
1.5.7. Диагностирование технического состояния автомобиля
Для контроля расхода топлива наибольшее распространение получили расходомеры следующих типов: объемные, весовые, тахометрические (рис. 1.29) и массовые (ротаметрические). Первый и второй типы представляют собой расходомеры дискретного действия (для определения расхода топлива необходимо израсходовать порцию топлива на интервале пробега или времени). Третий и четвертый типы расходомеров – приборы непрерывного действия, показывающие в каждый момент времени мгновенный расход топлива и определяющие суммарный расход. К основным пре-
155
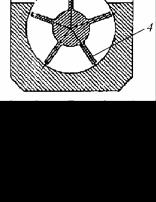
имущеествам расходомеров такого типа относятся возможность их установки непосредственно на автомобиле и использования как при стендовых испытаниях для оценки показателей топливной экономичности на различных режимах, в том числе и на холостом ходу, так и при работе автомобиля на линии для диагностирования его технического состояния, аттестации навыков водителя, и обучения его экономичным навыкам вождения и определения маршрутных норм линейного расхода топлива.
Исправность рулевого управления в целом проверяют люфтомером, который закрепляется на ободе рулевого колеса. При фиксированном усилии определяют величину люфта, который характеризует суммарные зазоры в механизме и приводе. Проверяется также наличие износа в сочлененных соединениях.
Передние колеса автомобиля устанавливают на две площадки (рис. 1.30), которые под действием гидропривода попеременно, с частотой примерно 1 Гц, перемещаются в разные стороны, создавая на колесах имитацию движения по неровностям дороги.
Сочлененные узлы: шаровые опоры, шкворневые соединения, шарниры рулевых тяг, узел посадки сошки руля и др. – визуально проверяются на недопустимые перемещения, стуки, скрипы. Выявляются места подтекания масел.
156
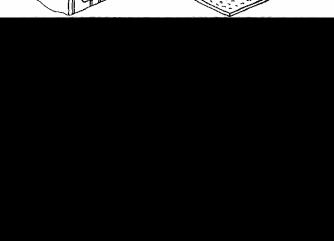
Рис. 1.30. Стенд для контроля состояния сочленения узлов подвески: 1 – площадка; 2 – лампа
При обслуживании рулевых систем, снабженных гидроусилителем, дополнительно с помощью специальной аппаратуры проверяют производительность и давление гидравлического насоса.
Для определения токсичности отработавших газов автомобилей с бензиновыми двигателями применяются газо-
анализаторы, которые могут измерять содержание СО, СО2, NОх, О2 и СхНу, а также контролировать состав топливновоздушной смеси, частоту вращения коленчатого вала двигателя внутреннего сгорания (ДВС) и тепловой режим.
Действие большинства газоанализаторов основано на поглощении газовыми компонентами инфракрасных лучей с различной длиной волны. Принципиальная схема такого газоанализатора приведена на рис. 1.31.
Определение содержания СО в отработавших газах происходит следующим образом: исследуемый газ, пройдя через фильтры 2–4 и насос 5, поступает в рабочую камеру, вклю-
157
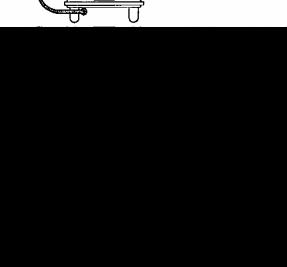
чающую измерительную кювету 6 и мембранный конденсатор 12, и удаляется в атмосферу. Сравнительные камеры, состоящие из сравнительной кюветы 10 и инфракрасного лучеприемника 11, заполнены азотом и герметично закрыты. В каждой схеме измерения излучение от двух накаленных спиралей, сфокусированное параболическими зеркалами 7, через обтюраторы 9 направляется соответственно в сравнительную и рабочую камеры. В сравнительных камерах поглощения инфракрасного излучения не происходит, в рабочих камерах продуваемые отработавшие газы поглощают из
Рис. 1.31. Принципиальная схема газоанализатора: 1 – зонд; 2–4 – фильтры; 5 – насос; 6 – измерительная кювета СО; 7 – инфракрасный излучатель; 8 – синхронный двигатель; 9 – обтюратор; 10 – сравнительная кювета СО; 11 – инфракрасный лучеприемник СО; 12 – мембранный конденсатор; 13, 16 – усилители; 14 – сравнительная кювета СхНу; 15 – инфракрасный лучеприемник СхНу; 17,
19 – индикаторы; 18 – измерительная кювета СхНу
158
спектра лучи соответствующей длины волны. Сравнение интенсивности двух потоков излучения позволяет определить содержание СО. Аналогично происходит определение содержания в отработавших газах СхНу и СО2.
Инфракрасные анализаторы чувствительны к изменению параметров среды, поэтому газ фильтруют, удаляют из него конденсат и подают насосом с постоянной скоростью. Метрологические характеристики данных газоанализаторов обеспечены при температуре окружающей среды 5–40 °С и относительной влажности воздуха до 80 %.
Проверка дизелей производится по уровню дымности отработавших газов. Оценивается дымомерами, которые работают по принципу поглощения светового потока, проходящего через отработавшие газы.
Контрольные вопросы
1.Назначение, содержание и место в технологическом процессе видов работ по техническому обслуживанию и текущему ремонту автомобилей.
2.Каким образом классифицируются моечные установки для автомобилей.
3.В чем заключается специфика работ, связанных с требованиями производственной и экологической безопасности? Применяемое оборудование, принцип работы.
4.Диагностика как метод получения индивидуальной информации о техническом состоянии автомобиля и его компонентов.
5.Укажите методы проведения диагностирования технического состояния автомобиля и его компонентов.
6.Какие средства диагностирования технического состояния автомобиля и его компонентов?
7.Назовите диагностические параметры, нормативы, ГОСТы, применяемые при контроле технического состояния автомобилей.
159
8.Дайте характеристику технологии диагностирования отдельных узлов, механизмов и систем автомобилей.
9.Диагностирование технического состояния автомобиля по топливным и мощностным характеристикам.
10.Диагностирование технического состояния автомобиля по характеристикам, обеспечивающим безопасность движения, по выбросам в окружающую среду отработавших газов.
11.Представьте схематически классификацию подъем- но-осмотрового и подъемно-транспортного оборудования.
12.По каким признакам и каким образом классифицируются подъемники?
13.Дайте классификацию осмотровых канав.
14.В чем заключается рациональная организация ТО
иремонта автомобилей?
15.Представьте схематически организацию ТО и ремонта автомобилей с применением диагностирования.
1.6.Общая характеристика технологических
идиагностических работ по текущему ремонту автомобилей
1.6.1. Текущий ремонт как способ восстановления работоспособности автомобиля и его компонентов
Одной из важнейших проблем инженерно-технической службы АТП является уменьшение объема работ ТР автомобилей и сокращение материальных и трудовых затрат на его выполнение.
Под текущим ремонтом понимается устранение отказов и неисправностей, возникающих в процессе их эксплуатации до капитального ремонта или списания, восстановление или замена неисправных деталей, узлов и агрегатов, а также необходимые при этом контрольно-диагностические, монтажнодемонтажные, регулировочные и цеховые ремонтные работы.
160