
книги из ГПНТБ / Применение методов статистического моделирования в автоматизированном химическом производстве
..pdf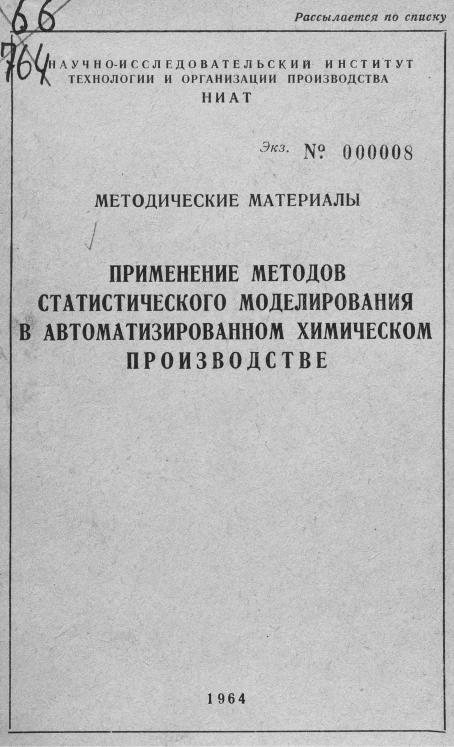
Рассылается по списку
Н А У Ч Н О - И С С Л Е Д О В А Т Е Л Ь С К И Й И Н С Т И Т У Т ТЕХНОЛОГИИ И ОРГАНИЗАЦИИ ПРОИЗВОДСТВА
Н И А Т
эхз. N ? 0 0 0 0 0 8
МЕТОДИЧЕСКИЕ МАТЕРИАЛЫ
ПРИМЕНЕНИЕ МЕТОДОВ СТАТИСТИЧЕСКОГО МОДЕЛИРОВАНИЯ
В АВТОМАТИЗИРОВАННОМ ХИМИЧЕСКОМ
П Р О И З В О Д С Т В Е
1964
УДК 621—501.75:66—52
Р а з р а б о т а л д: ЧЕРЕИСКАЯ Н. Н„ ЧЕСНИНА Т. А. (МИЭИ), ГОЛЕНКО Д. И., КАРЕВСКАЯ Г. И. (НИАТ).
К а ч. л а б о р а т о р и и Н И А Т НАИДОВ-ЖЕЛЕЗОВ Ч. Г.
Зав. кафедрой экономики и организации хим. промышленности МИЭИ проф. ФЕДОРОВИЧ М. М.
Отв. редакторы:
НОВАЦКИЙ В. Ф. (НИАТ), ГИРОВСКИЙ В. Ф. (МИЭИ)
ПУБЛИЧНАЯ |
|
ГиС' п; ° ,!S,u;ECHA5 |
|
•1ДS'UI -1 |
' л мэ |
& 5 Q
&
Я
Редактор Федосеева Ж . В. |
Техн. редактор Бродянская С. 10. |
|||
Сдано |
в набор 9/1V 1964 г. Т-09071 |
Подп. в |
печать 22/VIII 1964 г. |
|
Объем |
33/4 печ. л. Бумага 60x90/16 |
Издание |
подписное |
Зак. 396 |
В В Е Д Е Н И Е
Исключительно важная роль в деле создания материаль но-технической базы коммунизма принадлежит химической промышленности. На декабрьском Пленуме ЦК КПСС 1963 г. были выдвинуты важнейшие задачи развития химической промышленности, с решением которых окажется возможным осуществить коренные качественные преобразования в веду щих областях материального производства. Ускоренное раз витие химической промышленности будет осуществляться за счет расширения, реконструкции и интенсификации действу ющих производств и строительства новых предприятий. К 1970 г. войдет в строй около 200 новых и будет реконструи ровано свыше 500 действующих предприятий. Это должны быть предприятия нового типа: комплексно автоматизирован ные и с высоким уровнем организации производства.
В этих условиях особенное значение приобретает разра ботка системы внутризаводского планирования, которая должна отвечать требованиям автоматического управления производством с использованием математических методов, а также универсальных и управляющих машин. В настоящее время разработана и внедряется система технико-экономиче ского планирования химических предприятий с использова нием матричного метода и электронно-вычислительных машин. Для оперативного планирования требуется разработать более сложную экономико-математическую модель, которая позво ляла бы устанавливать для отдельных участков производства такие технико-экономические показатели, которые были бы увязаны с технологическим режимом процессов и позволяли бы установить критерий оптимальности работы предприятия. Для разработки оптимальных технико-экономических пока зателей оперативного плана необходимо знать зависимость этих показателей от технологического режима.
В химических процессах такие технико-экономические по казатели, как расходные нормы сырья, устанавливаются на основании стехиометрических соотношений, однако скорость реакции, ее обратимость, степень конверсии, появление по бочных реакций и т. д. ограничивают возможность установ-
3
ления четких расходных норм. Кроме того, зачастую увели чение производительности аппарата с некоторого момента начинает сопровождаться повышением расходного коэффи циента сырья. Поэтому для разработки показателей опера тивного плана и установления их на оптимальном уровне не обходимо иметь такие алгоритмы расчета, которые увязыва ли бы эти показатели с условиями технологического режима (с параметрами процесса). Такие алгоритмы могут быть по лучены на основании математического описания технологиче ских процессов. В химических процессах математические опи сания могут быть получены на основании изучения законов кинетики с учетом материальных и энергетических потоков. В настоящее время такие математические описания составля ются для некоторых процессов в Институте катализа Сибир ского отделения АН СССР и в ряде других институтов. Одна ко это сложный путь, требующий большой и длительной экспериментальной работы. Для того чтобы ускорить внедре ние автоматизированных систем управления, в последнее время широко применяется описание процессов с использо ванием методов математической статистики.
В выступлении на декабрьском Пленуме ЦК КПСС Пре зидент АН СССР М. В. Келдыш, отмечая основные направле ния в развитии химической науки, подчеркнул, что «необхо димо резко усилить изучение физико-химических закономер ностей химических процессов и на их основе проводить расче ты оптимальных технологических режимов с применением вы числительных машин и методов физического и математико статистического моделирования. Применение этих методов позволит сэкономить много времени и средств за счет сокра щения многостадийности опытно-промышленных работ».
Экспериментально-статистические методы основаны на математической обработке данных, собранных непосредствен но на действующем объекте. В зависимости от сбора и обра ботки информации экспериментально-статистические методы подразделяются на пассивное наблюдение и активный экспе римент.
Сбор информационного материала посредством пассивного наблюдения состоит в регистрации контролируемых техноло гических условий в режиме нормальной работы объекта без внесения в него каких-либо преднамеренных изменений (воз мущений). Сбор исходных данных путем активного экспери мента основан на введении в процесс искусственных измене ний по заранее спланированной программе. Преимущество второго способа в том, что он позволяет экспериментально проверить область оптимума. Однако в условиях действую щего промышленного предприятия этот способ менее досту пен, поскольку он требует изменения режимных условий и управляемости объекта. В настоящей работе приводится ком
4
плекс статистических методов, основанных исключительно на пассивном эксперименте.
Внастоящее время на основании Постановления Совета Министров СССР создаются четыре опытно-показательных предприятия химической промышленности по комплексной автоматизации: Воронежский завод синтетического каучука,. Новомосковский и Лисичанский химические комбинаты и Барнаульский завод химического волокна. Опыт этих заводов по внедрению комплексной автоматизации предполагается перенести в дальнейшем на другие предприятия химической промышленности. На этих предприятиях в первую очередь будут разработаны экономико-математические модели, внут ризаводского планирования.
Внастоящее время для некоторых процессов разрабаты ваются математические описания на основе изучения кинети ки процесса, однако для большинства процессов они отсутст вуют. Для целого ряда процессов в силу их сложности воз можность получения в скором времени такого математическо го описания маловероятна. В этом отношении большую помощь в изучении процессов и в разработке модельных алго ритмов должны оказать экспериментально-статистические ме тоды, которые в дальнейшем будут совершенствоваться и уточняться.
Предлагаемую методику составления оперативного плана химического процесса с использованием пассивного наблю дения можно применять для изучения любого химического процесса и при составлении предварительного алгоритма как одного из элементов экономико-математической модели хи мического предприятия. Следует отметить, что эта методика может применяться не только для химических, но и для ши рокого класса непрерывных процессов.
Настоящая работа построена на статистическом материа ле одного из крупнейших химических заводов СССР.
Она выполнена в творческом содружестве кафедры эко номики и организации химической промышленности Москов ского инженерно-экономического института имени С. Орджо никидзе и отдела математического моделирования Научноисследовательского института технологии и организации про изводства (НИАТ).
1. ПОСТАНОВКА ЗАДАЧИ ИССЛЕДОВАНИЯ
Оперативно-календарное планирование химических про изводств в настоящее время состоит в распределении показа телей техпромфинплана на короткие отрезки времени (сутки, смены, часы), в детализации их по рабочим местам и в дове дении до непосредственных исполнителей (смен, бригад, аппаратчиков) в виде наряд-заказов. Контроль за выполне нием этих показателей в настоящее время, как правило, носит пассивный характер: он не предупреждает, а только конста тирует их нарушение. Поэтому основная задача диспетчера (сменного инженера) состоит в том, чтобы обеспечить восста новление нарушенных технико-экономических показателей (по возможности путем регулирования факторов процесса).
В условиях комплексной автоматизации плановые показа тели задаются не людям, а электронной вычислительной ма шине, в которую они вводятся в виде управляющего алгорит ма. Машина ведет процесс на оптимум в соответствии с за данным алгоритмом. Отклонения от последнего возможны лишь по аварийным причинам [1]. В этих условиях основной задачей оперативно-календарного планирования является установление оптимальных технико-экономических показате лей процесса (частные критерии), которые подчиняются обще му критерию оптимальности предприятия таким образом, что бы обеспечить заданный выпуск продукции при минимальных затратах на производство.
Основными планируемыми технико-экономическими пока зателями процесса являются производительность оборудова ния в единицу времени, затраты сырья, материалов и различ ных видов энергии на единицу продукции, технологическая себестоимость единицы продукции. Под последней понимается сумма затрат предприятия на сырье, материалы и все виды расходов на единицу продукции, то есть цеховая себестои мость без затрат на заработную плату, амортизацию и цехо вых расходов.
В химических процессах выбор технологической себестои мости в качестве показателя объясняется тем, что в полной себестоимости химической продукции удельный вес материаль
ных и энергетических затрат очень велик, а затраты на зара ботную плату, амортизацию и цеховые расходы не зависят от технологических факторов процесса.
В химических процессах изменение технологических фак торов оказывает влияние на технико-экономические показа тели через такие технические коэффициенты, как степень пре вращения (конверсия), степень извлечения, выход целевого продукта на разложенную или пропущенную шихту, так как
производительность |
_ |
подача |
(выход целевого продукта). |
|
|
установки |
— |
шихты |
х \ на пропущенную шихту J ’ |
||
расходный |
коэффи- |
_ |
~Г~ |
1 |
'' |
циент сырья |
|
целевого продукта на разло |
|||
4 |
v |
|
(выход |
|
|
|
|
|
|
женную шихту) |
|
Технические коэффициенты могут быть приняты за функ цию отклика ряда переменных
"'ll = Т ( Х 1> ■ * * , • • • > х к ) -
Зная функцию отклика, можно найти оптимальные усло вия течения процесса при ограничениях, накладываемых на функцию [2].
Для установления зависимости функции отклика от фак торов процесса используются различные математические ме тоды.
В настоящей работе рассматривается методика расчета технико-экономических показателей оперативного плана в ус ловиях комплексно автоматизированного производства на ос новании информации о процессе, собранной посредством пас сивного наблюдения.
2. РАЗРАБОТКА МАТЕМАТИЧЕСКОЙ МОДЕЛИ ПРОЦЕССА НА ОСНОВЕ ПАССИВНОЕО НАБЛЮДЕНИЯ
Как указывалось выше, пассивноенаблюдение состоит в регистрации контролируемых технологических условий в ре жиме нормальной работы объекта без внесения в него какихлибо преднамеренных изменений (возмущений) [3].
Разработка математической модели процесса состоит из следующих этапов:
1)выбор факторов процесса;
2)выбор функции отклика;
3)стабилизация всех основных факторов;
4)составление матрицы исходных данных;
5)группировка исходных данных;
8
6)отбор наиболее существенных факторов;
7)составление математической модели процесса;
8)проверка адекватности полученного уравнения.
Методика разработки математической модели подробно рассматривается на примере каталитического процесса дегид рирования.
1)Выбор факторов процесса
Впроизводственных условиях на химический процесс влияет множество факторов, которые подразделяются на за меряемые и незамеряемые. Замеряемые факторы фиксируют ся датчиками в специальных диаграммах.
Предварительно проводится логический выбор факторов, то есть выделяются факторы, которые больше влияют на ход процесса и не зависят от других факторов. При этом можно руководствоваться опытом работников завода.
Например, в процессе дегидрирования замеряются следу ющие переменные: подача шихты на реактор, температура верха, низа и средины реактора, соотношение пар — шихта, анализ контактного газа, давление перед и после реактора, расход топливного газа, температура пара вверху реактора, после испарителя, после конвекционной части реактора, после пароперегревательной печи, температура шихты в испарителе и после перегревателя, температура контактного газа после реактора, после испарителя, после перегревателя, подача пара в испаритель и в пароперегревательную печь.
Логический выбор позволяет установить, что такой фактор, как расход топливного газа, определяется подачей пара в па роперегревательную печь и его температурой. Температура пара предопределяет температуру в реакторе, от которой за висит степень разложения шихты в целевой продукт. Следо вательно, если будут учтены температура в реакторе и пода ча пара в пароперегревательную печь, отпадает необходи мость в учете остальных указанных факторов, так как их влияние будет косвенно учтено.
После тщательного логического анализа были отобраны следующие факторы: соотношение пар — шихта, температура верха, средины и низа реактора, давление перед реактором и после него, перепад давления, подача шихты в реактор, пода ча пара в пароперегревательную печь и в испаритель, остаток в печном масле. Изменение последнего фактора дает возмож ность учесть изменение активности катализатора во времени, так как по мере дезактивации катализатора в продуктах раз ложения увеличивается содержание твердого остатка.
9
2)Выбор функции отклика
Вхимических процессах в качестве функции отклика мо гут быть приняты технические коэффициенты, которые опре деляют степень интенсивности ведения технологического про
цесса: в каталитических процессах — выход целевого продук та на пропущенную и разложенную шихту, в диффузионных процессах — коэффициент извлечения, в процессах полимери зации (синтеза) — глубину конверсии.
3) Стабилизация всех основных факторов
Стабилизация факторов достигается в случае, если сбор информации осуществляется в условиях установившегося ре жима, то есть режима, не изменяющегося во времени.
В этом случае производная факторов по времени равна нулю. Практически это означает, что после внесения возмуще ний необходимо фиксировать замеры по основным факторам только после того, как на диаграммах появятся плавные пря мые.
После сбора информации о процессе из диаграмм необхо димо исключить те замеры, которые являются случайными. Последнее может быть вызвано неисправностью контрольно измерительных приборов.
Просматривая такие записи, можно еще до проведения де тального статистического анализа ориентировочно оценить скорость изменения фактора во времени, диапазон этих изме нений, или степень разброса фактора. Последнюю характери стику оценивают величиной дисперсии.
На практике проверка стабильности информации прово дится графически. По оси абсцисс откладывают время измене ния фактора, по оси ординат — значение фактора (см. фигу-
РУ)-
Строки, содержащие точки выброса, исключаются из ин формации.
10