
Конструкционные материалы. Свариваемость и сварка
.pdfно регулировать с помощью предварительного и сопутствующего подогрева и термической обработки конструкции после сварки, а также путем применения присадочного материала и правильно выбранной системы легирования.
Однако кроме охрупчивания околошовной зоны следует учесть и наличие разупрочнения в зоне термического влияния. Наличие зоны разупрочнения связано с исходным состоянием стали (после полной термической обработки – закалка (нормализация) и высокий отпуск). Разупрочнение наблюдается на участке, где металл нагревается в интервале от температуры Ас3 до температуры отпуска (см. рис. 3.2). При этом кратковременные прочностные свойства сварного соединения ухудшаются по сравнению с основным металлом на 5–10 %, а длительная прочность на 20 %. Мягкая прослойка в зоне термического влияния может являться причиной локальных разрушений жестких сварных соединений в процессе эксплуатации, особенно при изгибающих нагрузках.
Повышение погонной энергии при сварке вызывает большое разупрочнение свариваемой стали. Зону разупрочнения можно разделить на два участка:
1 – от температуры Ас3 до температуры Ас1 (зона неполной перекристаллизации);
2 – от температуры Ас1 до температуры отпуска (зона отпуска).
Взависимости от легированности стали в условиях сварки
вэтой зоне могут обнаруживаться самые разнообразные продукты распада аустенита – от мартенсита до зернистого перлита. Также может наблюдаться коагуляция карбидной фазы, увеличение количестваферрита, чтоприводит к разупрочнению этойзоны (рис. 3.5). Для устранения провала твердости в этой зоне необходима последующая термическая обработка.
Также следует учитывать изменение свойств в зоне сплавления с основным металлом. При температурах эксплуатации 450–600 °С возникают диффузионные процессы между основным металлом и металлом шва. В первую очередь это относится к углероду как наиболее диффузионно подвижному элементу. Миграция
51
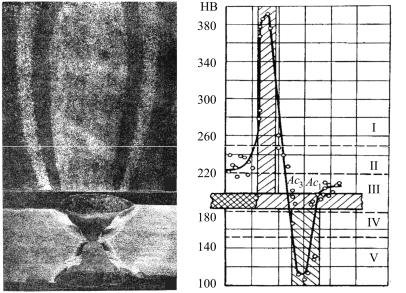
а |
б |
Рис. 3.5. Макроструктура сварного соединения из теплоустойчивой стали (а) и диаграмма распределения твердости по зонам сварного соединения (зона охрупчивания и зона разупрочнения – участок белой полосы на макрошлифе) (б): I – недопустимая область, HB > 250; II – допустимая область, HB 220–250; III – оптимальная область, HB 180–220; IV – допустимая область, HB 180–160;
V – недопустимая область, HB < 160
углерода из основного металла в шов и наоборот может наблюдаться даже при небольших различиях в легировании их карбидообразующими элементами. Образование в процессе эксплуатации обезуглероженной ферритной прослойки по одну сторону линии сплавления и карбидной гряды по другую приводят к снижению длительной прочности и пластичности сварного соединения и локальному разрушению. Поэтому сварочные материалы должны обеспечить химический состав металла шва, близкий к составу основного металла. В отдельных случаях при необходимости от-
52
каза подогрева и термической обработки можно использовать сварочные материалы на никелевой основе, так как диффузионная подвижность элементов в сплавах на никелевой основе при температурах 450–500 °С значительно меньше, чем в низколегированных сталях перлитного класса.
3.2.2.Предварительный и сопутствующий подогрев
Влитературе для одних и тех же сталей приводят различные температуры предварительного подогрева, тогда как в производственных условиях нагрев вызывает большие трудности. Особенно трудности усугубляются при сварке толстостенных крупногабаритных конструкций, поэтому температуру подогрева необходимо учитывать как можно точнее. Неоправданное завышение температуры подогрева затрудняет работу сварщиков и увеличивает трудоемкость работы. Недостаточный подогрев не может обеспечить хорошего качества сварных соединений и приводит к образованию трещин.
Рекомендуемые температуры предварительного и сопутствующего подогрева:
Маркастали |
Температураподогрева, °С |
12МХ, 12ХМ, 15ХМ |
200–250 |
20ХМ, 12ХМФ |
250–300 |
20ХМФ, 15Х1М1Ф |
350–400 |
15Х2М2ФБС |
400–500 |
Предварительный подогрев также способствует выделению водорода, ранее поглощенного аустенитом стали. Растворимость водорода в продуктах распада аустенита невелика, и при превращениях значительная часть водорода выделяется на отдельных участках в молекулярной форме. В местах скопления молекулярного водорода возникает высокое давление. При одновременном воздействии давления водорода и напряжений, связанных с превраще-
53
нием аустенита, в зоне термического влияния могут возникать надрывы и трещины. При подогреве атомарный водород обладает большей подвижностью, он успевает выделяться, и в результате уменьшается возможность образования трещин.
Подогрев при сварке может быть общим, местным и комбинированным. При выборе способа подогрева необходимо учитывать:
–характер и объем сварочных работ;
–толщину изделия;
–протяженность и расположение швов;
–степень механической обработки;
–размеры конструкции;
–возможность транспортировки после нагрева;
–имеющиеся на предприятии средства нагрева.
Поскольку теплоустойчивые стали чувствительны к резким изменениям температуры в интервале 0–500 °С, скорость предварительного подогрева должна быть низкой, а подогрев равномерным и симметричным. Оптимальная скорость подогрева 30–50 град/ч. Тепло с поверхности металла вглубь должно передаваться так, чтобы градиент температур был минимальный, поэтому нагревательные устройства должны позволять регулировать скорость нагрева.
3.2.3. Отдых сварной конструкции
Свойства металла шва и зоны термического вливания сварных соединений в значительной степени зависят от времени и условий выдержки их после сварки до термической обработки. Как правило, сразу после сварки сопротивляемость металла сварных соединений образованию холодных трещин относительно низка. Через некоторое время (5–10 сут) при вылеживании при комнатной температуре в сварных соединениях образуются холодные трещины.
Суть технологической операции отдыха заключается в том, что после сварки сварное соединение не охлаждается до комнатной температуры, а выдерживается при повышенных температурах в течение некоторого времени. Минимальная температура отдыха
54
должна быть выше температуры, при которой возможно образование холодных трещин. Максимальная температура отдыха не должна превышать нижней температуры интервала термического старения. Рекомендуемые температуры отдыха при свариваемой толщине более 30 мм:
–сталь 12Х1МФ – 130–200 °С,
–сталь 12Х2МФ – 130–200 °С.
Впроцессе отдыха в сварных соединениях не происходит фазовых превращений, имеют место лишь диффузионные и релаксационные процессы.
3.2.4.Термическая обработка сварной конструкции
Взависимости от применяемых материалов и условий эксплуатации термическая обработка сварных конструкций может преследовать различные цели и одновременно выполнять многие функции. Целями проведения термической обработки теплоустойчивых сталей являются:
– получение необходимых свойств шва и зоны термического влияния;
– снятие остаточных напряжений;
– стабилизация размеров конструкций при эксплуатации (особенно это важно для энергетического оборудования, крупных конструкций, которые находятся под воздействием различных температур и нагрузок).
Термическая обработка сварных конструкций должна рассматриваться с учетом характера изменения структуры и свойств не только в зоне повышения твердости, но и в зоне разупрочнения. При выборе режимов термической обработки сварных конструкций из теплоустойчивых сталей необходимо учитывать следующие ме-
таллургические и технологические особенности сварки:
1. В процессе многослойной сварки каждый последующий валик термически воздействует на предыдущий и околошвную зону. В результате металл шва и зоны термического влияния (за ис-
55
ключением верхнего слоя) подвергается высокотемпературному нагреву, который происходит при больших скоростях и сопровождается быстрым охлаждением. При этом заметного роста зерна не наблюдается, так как пребывание металла отдельных валиков и зоны термического влияния при высокой температуре кратковременно. Основные изменения связаны с прочностью и пластичностью сварного соединения в целом. В околошовной зоне наблюдается скачкообразное повышение и понижение твердости и прочности.
2.Температура термической обработки при улучшении свойств околошовной зоны должна обеспечить снижение внутренних напряжений первого рода до возможно минимального значения. Например,
вэнергомашиностроении максимальные значения остаточных напряженийв сварныхконструкцияхнедолжныпревышать50 МПа.
3.В процессе термической обработки должны быть сохранены исходные механические свойства свариваемой стали, т.е. двух-, трехкратная термическая обработка после сварки не должна приводить кразупрочнениюсталей, металлашваисварногосоединениявцелом.
4.Выбранный режим термической обработки должен обеспечить высокие пластические свойства околошовной зоны при длительной эксплуатации в условиях одновременного приложения температуры и нагрузки при одновременном обеспечении прочности
взоне разупрочнения.
Основными видами термической обработки теплоустойчивых сталей являются высокий отпуск и нормализация (рис. 3.6).
Высокий отпуск после сварки нельзя рассматривать как самостоятельную термическую обработку, наоборот, ее необходимо увязывать с исходным отпуском стали перед сваркой. В общем случае сварное соединение нагревается до температуры на 20–30 °С ниже температуры Ас1, выдерживается в течение 1–5 ч и затем медленно охлаждается. В результате отпуска должно произойти:
–уменьшение уровня остаточных сварочных напряжений на
70–90 %;
–распад закалочных структур околошовной зоны, получение более равновесных, более пластичных структур (т.е. улучшение структуры околошовной зоны);
56

Рис. 3.6. Виды термической обработки сварных соединений теплоустойчивых сталей: 1 – термический отдых сварной конструкции; 2 – высокий отпуск; 3 – нормализация
– получение оптимальных свойств (т.е. уменьшение твердости в околошовной зоне, повышение пластичности и ударной вязкости).
При выборе температуры отпуска следует оценивать комплексно все факторы, при этом необходимо ограничивать как верхний, так и нижний пределы температуры отпуска. Так, при повышении содержания хрома, молибдена, ванадия и других элементов повышается релаксационная стойкость стали, поэтому температура отпуска и время выдержки должны увеличиваться. При занижении температуры отпуска хромомолибденованадиевых сталей возможно дисперсионное твердение (выделение карбидов ванадия в околошовной зоне) и образование трещин при термической обработке. Отпуску подвергаются изделия толщиной более 10 мм из хромомолибденовых сталей и более 6 мм из хромомолибденованадиевых сталей (табл. 3.4).
При нормализации сварное соединение нагревают до температуры выше критической точки Ас3 на 20–30 °С, выдерживают в течение непродолжительного времени и охлаждают на спокойном воздухе. Нормализация позволяет получить однородную мелкозернистую структуру, улучшить механические свойства сварного со-
57
единения, снизить уровень остаточных напряжений. Нормализации чаще всего подвергаются сварные стыки толстостенных труб малого диаметра и после газовой сварки.
Таблица 3 . 4 Режимы отпуска сварных соединений, сваренных дуговой сваркой
Маркастали |
Толщинасвариваемых |
Минимальнаяпродолжи- |
Температура |
|
|
деталей, мм |
тельностьвыдержки, ч |
отпускаТ, °С |
|
12МХ, 12ХМ, |
10–20 |
1 |
|
|
20–40 |
2 |
715 ± 15 |
||
15ХМ. 20ХМЛ |
40–80 |
3 |
||
|
||||
|
более80 |
4 |
|
|
|
6–10 |
1 |
|
|
12Х1МФ, |
10–20 |
2 |
|
|
20–40 |
3 |
735 ± 15 |
||
0ХМФЛ |
||||
40–80 |
4 |
|
||
|
|
|||
|
более80 |
5 |
|
|
15Х1М1Ф, |
6–10 |
1 |
|
|
10–20 |
2 |
|
||
15Х1М1ФЛ, |
20–40 |
3 |
745 ± 15 |
|
12Х2МФСР |
40–80 |
4 |
|
|
|
более80 |
5 |
|
Возможно сочетание нормализации и последующего высокого отпуска (сталь 15Х1М1Ф) для обеспечения высокого уровня исходной твердости (не наблюдаются разупрочнения в зоне нагрева).
3.3. ТЕХНОЛОГИЯСВАРКИТЕПЛОУСТОЙЧИВЫХСТАЛЕЙ
Основными способами сварки, используемыми при изготовлении конструкций из теплоустойчивых сталей перлитного класса, являются электродуговая и электроконтактная. Электроконтактная сварка используется для выполнения стыковых соединений труб, поверхностей нагрева, котлов в заводских условиях. В подавляющем большинстве других случаев используется сварка покрытыми электродами, в среде защитных газов и под слоем флюса.
58

Общими рекомендациями по всем видам дуговой сварки являются: оптимальная подготовка свариваемых кромок, тепловые условиясваркиирежимытермическойобработкисварныхсоединений.
Подготовка кромок деталей под дуговую сварку производится с помощью механической обработки, на специализированном оборудовании и устройствах стационарного и переносного исполнения, токарных станках, рабочим инструментом которых являются резцы, фрезы, стальные диски и ролики, абразивные армированные круги. Шероховатость поверхности кромок труб, подготовленных для сварки, не должна превышать норм, приведенных на рис. 3.7.
Рис. 3.7. Конструктивные размеры кромки трубы, обработанной под подкладное кольцо
Фаски на трубах под ручную или автоматическую аргонодуговую сварку стыков без подкладных колец независимо от способа сварки необходимо снимать только механическим способом.
Допускается применение кислородной, плазменно-дуговой или воздушно-дуговой резки с последующей зачисткой кромок режущим или абразивным инструментом до удаления следов огневой резки (табл. 3.5). Подготовленные к сборке кромки должны быть без вырывов, заусенцев, резких переходов и острых углов. Кислородную резку труб из хромомолибденовых и хромомолибденованадиевых сталей со стенкой толщиной более 12 мм при температуре окружающего воздуха ниже 0 °С нужно производить с предварительным подогревом до 200 °С и медленным охлаждением под слоем асбеста.
59
Таблица 3 . 5
Рекомендуемая величина технологического припуска при разметке низколегированных теплоустойчивых сталей, мм
№ |
Способсварки |
Припуск |
|
п/п |
|||
|
|
||
1 |
Кислороднаярезка |
3–8 |
|
2 |
Кислороднаямашиннаярезка |
2–4 |
|
3 |
Плазменно-дуговаярезка |
6–8 |
|
4 |
Механическаярезка |
4–6 |
|
5 |
Механическаяобработкаторцовпослетермическойрезки |
2–3 |
При термической резке должен быть предусмотрен припуск на последующую механическую обработку, величина которого определяется нормативно-технической документацией. После кислородной или плазменной резки кромки реза необходимо зачистить механическим способом на глубину не менее 2–3 мм.
Непосредственно перед сборкой изготовленные под сварку кромки и прилегающие к ним участки поверхностей деталей должны быть зачищены до металлического блеска и обезжирены. Ширина зачищенных участков, считая от кромки разделки, должна быть не менее 20 мм с наружной и не менее 10 мм с обратной стороны детали. В табл. 3.6 приведены примеры конструктивных элементов подготовки кромок под сварку при изготовлении трубопроводов.
Дуговая сварка производится при температуре окружающего воздуха не ниже 0 °С с предварительным и сопутствующим подогревом.
При выборе сварочных материалов (покрытых электродов, сварочной проволоки и флюсов) стремятся приблизить химический состав металла шва к химическому составу основного металла. В противном случае в условиях длительной работы сварных соединений при высоких температурах возможно развитие диффузионных процессов, особенно миграции углерода.
60