
Конструкционные материалы. Свариваемость и сварка
.pdfМеханические свойства высокохромистых мартенситных сталей и их сварных соединений определяются фактическим химическим составом и режимом термической обработки, с помощью которой можно регулировать как свойства самой мартенситной матрицы, так и конечный фазовый состав и структуру сталей.
Таблица 6 . 3 Механические свойства высокохромистых мартенситных сталей
Сталь, марка |
σ0,2, МПа |
σв, МПа |
δ5, % |
|
ψ, % |
KCU, МДж/м2 |
|
|
не менее |
|
|
||
|
|
|
|
|
||
15Х11МФ |
490 |
690 |
15 |
|
55 |
0,6 |
15Х12ВНМФ |
590 |
740 |
15 |
|
45 |
0,6 |
18Х11МНФБ |
590–735 |
740 |
15 |
|
50 |
0,6 |
1ЗХ11Н2В2МФ |
735 |
880 |
15 |
|
55 |
0,9 |
12Х11В2МФ |
392 |
588 |
18 |
|
– |
– |
10Х12НД |
500 |
650 |
14 |
|
30 |
0,3 |
06Х12НЗД |
500–700 |
700 |
14 |
|
30 |
0,5 |
Существенное влияние на механические свойства оказывают также количество, величина и геометрическая форма δ-феррита, в общем случае способствующего снижению пластичности и ударной вязкости без существенного влияния на пределы прочности
итекучести (табл. 6.3).
6.2.СВАРИВАЕМОСТЬ ВЫСОКОЛЕГИРОВАННЫХ
МАРТЕНСИТНЫХ СТАЛЕЙ
Мартенситные стали имеют повышенную склонность к хрупкому разрушению в состоянии закалки, что усложняет технологию их сварки.
При содержании углерода более 0,10 % мартенситные стали склонны к образованию холодных трещин при сварке из-за высокой степени тетрагональности кристаллической решетки мартенсита. При снижении содержания углерода вязкость мартенсита по-
121
вышается, однако образующийся при этом структурно свободный δ-феррит повышает хрупкость. В связи с этим в сварных соединениях мартенситных сталей трещины могут наблюдаться в процессе непрерывного охлаждения при температурах ниже начала мартенситного превращения Tм.н, а также в процессе выдержки при нормальной температуре (замедленное разрушение).
Для высокохромистых сталей температура начала мартенситного превращения не превышает 360 °С, а окончания – 240 °С. С увеличением содержания углерода точки начала Tм.н и конца Тм.к мартенситного превращения еще более понижаются, что приводит к возрастанию твердости мартенсита и его хрупкости. Учитывая это, а также необходимость обеспечения высокой пластичности и ударной вязкости сварных соединений для безопасной эксплуатации ответственных энергетических установок, содержание углерода в хромистых мартенситных сталях ограничивают до 0,20 %.
Для предотвращения образования холодных трещин при сварке 11–12%-ных хромистых сталей применяют предварительный и сопутствующий подогрев до 200–450 °С. Температура подогрева тем выше, чем выше склонность стали к закалке. В то же время температура подогрева не должна быть чрезмерно высокой, так как это может привести к отпускной хрупкости вследствие снижения скорости охлаждения металла в околошовной зоне в интервале температур карбидообразования. Кроме того, высокий подогрев, как и сварка с высокой погонной энергией, обеспечивает длительный перегрев околошовного металла, результатом чего является рост зерна, сегрегация примесей на границах зерен и, как следствие, снижение пластичности и вязкости сварных соединений. Лучшие свойства сварных соединений достигаются в случае предварительного подогрева в интервале температур Тм.н–Тм.к, а также когда после сварки производится подстуживание до Тм.к, но не ни-
же 100 °С.
Однако в отдельных случаях можно отказаться от подогрева. Так, низкоуглеродистые мартенситные стали толщиной до 8–10 мм удается сваривать без подогрева. Сварку без подогрева проводят
122
при использовании аустенитных присадочных материалов. Не требуется также подогрев при электрошлаковой сварке.
Многие из отмеченных выше недостатков в свариваемости мартенситных сталей не присущи малоуглеродистым хромистым сталям, дополнительно легированным никелем. Мартенсит, образующийся при закалке хромоникелевых сталей, отличается вследствие низкого содержания углерода высокой пластичностью и вязкостью, не склонен к образованию холодных трещин при сварке. Высокие пластические свойства малоуглеродистого мартенсита повышают надежность получения качественных сварных соединений. Однако чувствительность металла швов к водородной хрупкости вызывает необходимость при их сварке предварительного и сопутствующего подогрева до 100–200 °С. Улучшению свариваемости этих сталей способствует также остаточный аустенит. Количество остаточного аустенита закалки зависит в основном от химического состава стали. Количество остаточного аустенита отпуска определяется режимом термической обработки.
Еще одним неблагоприятным фактором является наличие участка отпуска в зоне термического влияния основного металла. На этом участке наблюдается разупрочнение, приводящее к снижению прочности и пластичности сварного соединения при длительной работе в условиях высоких температур. Разупрочнение не устраняется после отпуска, и для его устранения требуется применение нормализации с отпуском или закалки с отпуском. Степень разупрочнения металла в околошовной зоне зависит от температуры предварительного подогрева.
6.3. ТЕХНОЛОГИЯ СВАРКИ И СВОЙСТВА СВАРНЫХ СОЕДИНЕНИЙ
Сварка мартенситных высокохромистых сталей должна выполняться только при положительной температуре окружающего воздуха.
123
Ручная дуговая сварка
При ручной дуговой сварке высокохромистых мартенситных сталей не рекомендуется применять электроды, содержащие в покрытии в качестве газообразующих элементов органические соединения. Это связано с тем, что растворяющийся при сварке в расплавленном металле водород значительно усиливает склонность к образованию холодных трещин в хрупком металле швов и околошовной зоны. Обычно применяют электроды с покрытием фтори- сто-кальциевого типа, при которых газовая защита сварочной зоны образуется за счет распада карбонатов покрытия, в основном мрамора. Образующиеся при этом высококальциевые шлаки благоприятны для удаления из сварочной ванны вредных примесей – серы и фосфора. Окислительное влияние газовой фазы (СО2 и продуктов распада) компенсируется использованием электродов, содержащих раскислители в металлическом стержне или (чаще) в покрытии.
Для уменьшения возможного поглощения водорода электроды перед сваркой следует прокаливать при температуре 450–500 °С течение 2 часов (режим часто приводится в паспорте на электроды). Сварку выполняют постоянным током обратной полярности.
При выборе электродов для сварки высокохромистых мартенситных сталей требуется обеспечивать следующие основные свойства наплавленного металла и металла шва:
–стойкость к атмосферной коррозии и слабоагрессивным жидким средам;
–жаростойкость до температуры 650 °С;
–жаропрочность до температуры 550 °С.
Для ручной дуговой сварки применяют электроды, обеспечивающие получение сварных швов, близких по химическому составу и свойствам основному металлу (табл. 6.4). Это электроды марок КТИ-9, КТИ-10 с наплавленным металлом, содержащие 10–12 % Cr, 0,8 % Ni и 1 % Мо.
Электроды марки ЦЛ-32 применяют для сварки конструкций, работающих при температурах до 600 °С, они содержат также 1 % W и характеризуются пониженным содержанием углерода
124

Таблица 6 . 4 Механические свойства сварных соединений высоколегированных мартенситных сталей (не менее)
Сталь, марка
15X11МФ,
15Х12ВНМФ,
18Х11МНФБ
13Х11Н2В2МФ
15X11МФ,
15Х12ВНМФ,
18X11МНФБ,
15Х11Н2В2МФ
12X11В2МФ
10Х12НД
125
Способсварки. |
|
Металлшва |
|
|
|
Сварноесоединение |
|||||
Сварочныематериалы |
σ0,2, МПа |
σв, МПа |
δ5, % |
ψ, % |
KCU, |
2 |
σв, МПа |
KCU, |
2 |
Угол |
|
|
|
|
|
|
|
МДж/м |
|
МДж/м |
загиба |
||
РДС |
|
|
|
|
|
|
|
|
|
|
– |
Электроды: Э-12Х11НМФ(КТИ-9) |
|
|
|
|
|
|
|
|
|
|
|
588 |
735 |
15 |
|
56 |
0,5 |
|
690 |
0,5 |
|
|
|
|
|
|
|
|
|||||||
|
|
|
|
|
|
|
|
|
|
|
|
Э-12Х11НВМФ(КТИ-10) |
588 |
735 |
15 |
|
55 |
0,5 |
|
735 |
0,5 |
|
– |
Э-11X15Н25М6АГ2 |
363 |
588 |
13 |
|
15 |
0,4 |
|
588 |
0,4 |
|
– |
(ЭА-395/9) |
|
|
|
||||||||
|
|
|
|
|
|
|
|
|
|
|
|
|
|
|
|
|
|
|
|
|
|
|
|
Э-10Х25Н13Г2 (ЗиО) |
294 |
539 |
13 |
|
15 |
0,5 |
|
539 |
0,5 |
|
– |
Э-14Х11НВМФ(ЦЛ-32) |
569 |
735 |
12 |
|
|
0,4 |
|
588 |
0,4 |
|
– |
АДС |
|
|
|
|
|
|
|
|
|
|
|
Проволока: Св-15Х12НМБФ |
|
|
|
|
|
|
|
|
|
|
– |
Флюс: АН-17; ОФ-6 |
710 |
784 |
15 |
|
40 |
0,5 |
|
588 |
0,4 |
|
|
|
|
|
|
|
|
|
|
|
|
|
|
Проволока: Св-15Х12ГНМВФ |
588 |
784 |
15 |
|
50 |
0,7 |
|
588 |
0,4 |
|
– |
Флюс: АН-17, ОФ-6 |
|
|
|
||||||||
|
|
|
|
|
|
|
|
|
|
|
|
РДС |
|
|
|
|
|
|
|
|
|
|
|
Электроды: Э-06Х13Н(ЦЛ-41) |
490 |
637 |
16 |
|
– |
0,5 |
|
637 |
0,3 |
|
40 |
ЭШС |
|
|
|
|
|
|
|
|
|
|
|
Проволока: Св-12X13 |
|
|
|
|
|
|
|
|
|
|
|
Флюс: АН-8 |
440 |
580 |
12 |
|
– |
0,5 |
|
580 |
0,5 |
|
40 |
|
|
|
|
|
|
|
|
|
|
|
|
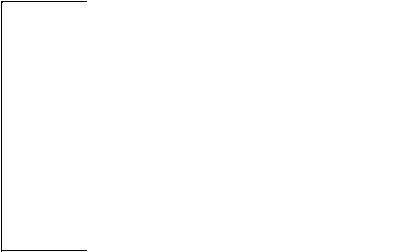
126
Окончание табл. 6 . 4
Сталь, марка |
Способсварки. |
|
Металлшва |
|
|
|
Сварноесоединение |
|||||
Сварочныематериалы |
σ0,2, МПа |
σв, МПа |
δ5, % |
ψ, % |
KCU, |
2 |
σв, МПа |
KCU, |
2 |
Угол |
||
|
|
|
|
|
|
|
МДж/м |
|
МДж/м |
загиба |
||
|
РДС |
|
|
|
|
|
|
|
|
|
|
|
|
ЭлектродыЦЛ-51 |
490 |
637 |
12 |
|
35 |
0,5 |
|
637 |
0,5 |
|
40 |
|
АДС |
|
|
|
|
|
|
|
|
|
|
|
|
Проволока: Св-01Х12Н2-ВМ |
|
|
|
|
|
|
|
|
|
|
|
|
(ЭП-762-ВИ) |
|
|
|
|
|
|
|
|
|
|
|
06X12НЗД |
Флюс: ФЦ-19 |
470 |
600 |
12 |
|
35 |
0,5 |
|
600 |
0,5 |
|
40 |
|
|
|
|
|
|
|
|
|
|
|
|
|
АрДС |
|
|
|
|
|
|
|
|
|
|
|
|
|
Проволока: Св-01Х12Н2-ВИ |
|
|
|
|
|
|
|
|
|
|
|
|
(ЭП-792-ВИ) |
490 |
637 |
12 |
|
35 |
0,5 |
|
637 |
0,5 |
|
40 |
|
ЭШС |
|
|
|
|
|
|
|
|
|
|
|
|
Проволока: Св-01Х12Н2-ВИ |
|
|
|
|
|
|
|
|
|
|
|
|
(ЭП-792) |
|
|
|
|
|
|
|
|
|
|
|
|
Флюс: АН-45 |
440 |
590 |
12 |
|
35 |
0,5 |
|
590 |
0,5 |
|
40 |
* РДС – ручная дуговая сварка; АДС – автоматическая дуговая сварка; ЭШС – электрошлаковая сварка; АрДС – аргонодуговая сварка.
(0,02–0,08 %). Это приводит к существенному повышению вязкости металла швов по сравнению с металлом шва, полученным «однородными» электродами.
Для сварки сталей с пониженным содержанием углерода и дополнительно легированных никелем рекомендуются электроды типа Э-06Х13Н (марка ЦЛ-41). Наряду с этим более высокая стойкость металла шва и зоны термического влияния против образования холодных трещин в сварных соединениях коррозионностойких закаливающихся сталей (06Х12НЗД и др.) достигается при использовании электродов марки ЦЛ-51, обеспечивающих наплавленный металл с большим, чем у электродов ЦЛ-41 содержанием никеля (до 2,5 %) и более низким содержанием углерода.
Наряду с «однородными» электродами имеет место также применение аустенитных электродов марок ЗиО-8 и ЭА-395/9 (в основном для обварки лопаток при изготовлении диафрагм). Сварные швы в данном случае обладают повышенной работоспособностью. Последующая термообработка, как правило, ухудшает свойства металла шва и вызывает резкие перепады остаточных напряжений вблизи границы сплавления, поэтому термообработку таких сварных соединений обычно не проводят.
При использовании аустенитного наплавленного металла обязательно необходимо учитывать и долю основного металла, попадающего в металл шва и тем самым влияющего на его состав, структуру и свойства.
При использовании «однородных» электродов сварное соединение отличается структурной однородностью и высокой прочностью после соответствующей термообработки. При применении аустенитных электродов соединение отличается структурной неоднородностью, усугубляемой диффузионными процессами, происходящими при эксплуатации изделий в области повышенных температур. При этом равнопрочность сварных соединений, как правило, не достигается.
127
Сварка в среде защитных газов
Используют дуговую сварку плавящимся электродом в углекислом газе и в инертных газах неплавящимся вольфрамовым электродом.
При сварке высокохромистых сталей в среде инертных газов в основном используют аргон и аргоно-гелиевые смеси. Присадочный материал подбирают близким по химическому составу к основному металлу. При данном виде сварки создаются благоприятные металлургические условия для снижения выгорания Cr и других легирующих элементов, поэтому в шов удается вводить почти без потерь такие активные элементы, как титан и алюминий, улучшающие свойства металла шва.
Сварку в среде инертных газов применяют в основном для изготовления конструкций малых толщин и для выполнения корневого валика в многослойных швах металла большой толщины. Это связано с пониженной производительностью данного способа сварки.
Для автоматической сварки используется проволока Св-15Х12НМВФБ и Св-15Х12ГНМБФ и флюсы АН-17 и ОФ-6.
Сварка плавящимся электродом в углекислом газе хотя и обеспечивает обычно достаточное оттеснение воздуха от сварочной зоны, однако оказывает значительное окислительное воздействие на металл. Для борьбы с недопустимым окислением металла шва в электродную проволоку необходимо вводить раскислители в количествах, достаточных для предохранения от выгорания основных элементов, определяющих свойства металла шва.
Сварка под флюсом
Широко применяемые окислительные высококремнистые, высокомарганцовистые флюсы не пригодны для сварки высокохромистых мартенситных сталей, это связано с процессами окисления не только активных легирующих элементов, но и основного легирующего элемента – хрома. В ряде случаев повышение концентрации кремния, а также марганца в высокохромистом металле вредно для его свойств, уменьшает его пластичность и вязкость.
128
Фторидные бескислородные флюсы не обеспечивают достаточно хорошего формирования швов, поэтому для сварки высокохромистых сталей рекомендуется применять:
–безокислительные, высокоосновные флюсы, почти не изменяющие в процессе плавления состава электродной проволоки;
–слабоокислительные флюсы в комбинации с проволоками Св-15Х12НМВФБ и Св-15Х12ГНМБФ (за счет введения в низкокремнистый флюс некоторого количества окислов железа).
При изготовлении лопаточного аппарата турбин большое распространение получил способ электронно-лучевой сварки.
Термическая обработка сварных соединений
Независимо от толщины изделий сварные соединения высокохромистых мартенситных сталей, как правило, подвергают термической обработке для снятия остаточных напряжений, распада закалочных структур и формирования необходимого комплекса механических свойств. Вылеживание перед термической обработкой допускается только для сварных соединений стали марки 12Х11В2МФ. Во всех остальных случаях сварные соединения подвергают немедленному (без охлаждения ниже температуры подогрева) высокотемпературному отпуску. В некоторых случаях перед отпуском производится подстуживание до 100 °С для завершения
γ→α(M)-превращения. Температура отпуска выбирается не выше значений критической точки Ас1. Рекомендации по тепловому режиму сварки приведены в табл. 6.5.
Свойства сварных соединений
В табл. 6.4 приведены механические свойства сварных соединений высоколегированных мартенситных сталей после термической обработки, описанной в табл. 6.5. Прочность сварных соединений определяется свойствами применяемых для сварки присадочных материалов. В случае однородных с основным металлом швов свойства сварных соединений близки к основному металлу. Использование сварочных электродов КТИ-9, КТИ-10 и ЦЛ-32 обеспечиваетсварным соединениям сталей 15X11МФ, 15Х12ВНМФ, 18Х11МНФБ и
129
13Х11Н2В2МФ длительную прочность за 106 ч при максимальной температуреэксплуатациинеменее120 МПа
Таблица 6 . 5 Особенности теплового режима сварки мартенситных сталей
|
Температура |
Времявылежива- |
|
Маркастали |
подогрева, |
ниядотермиче- |
Термическаяобработка |
|
°C |
скойобработки, ч |
|
15Х11МФ |
|
|
Отпускпри700–720 °C |
15Х12ВНМФ |
|
|
(безохлаждениянижетемпера- |
18Х11МНФБ |
300 |
Недопускается |
турыподогрева). |
|
Приδ более30 ммпередтер- |
||
13Х11Н2В2МФ |
|
|
мообработкойрекомендуется |
|
|
|
«подстуживание» до100 °C |
|
|
|
Отпускпри715–745 °C (пред- |
12Х11В2МФ |
250–300 |
72 |
варительный) и735–765 °C |
|
|
|
(окончательный) |
10Х12НД |
≥100 |
Недопускается |
Отпускпри650 °C (спредвари- |
тельнымподстуживанием) |
|||
|
|
|
Отпускпри610–630 °C (пред- |
06Х12Н3Д |
≥200 |
Недопускается |
варительный) и625–650 °C |
|
|
|
(окончательный) |
130