
Выбор абразивных инструментов и режимов резания для высокоэффективно
..pdfда собирается металлическая стружка) и окончательная – доводка (она производится притирами с гладкой поверхностью). В качестве притирочных порошков используются: корундовый, карборундовый, наждачный порошки, окись железа, алюминия, хрома, толченое стекло. Зернистость абразивных порошков – от М40 до М7. В качестве смазки применяются олеиновая кислота, машинное масло, керосин, скипидар, техническое сало.
Разновидностью притирки является доводка, обеспечивающая получение не только правильных заданных геометрических форм и заданной чистоты, но и заданных размеров детали с точностью до 0,001 мм. Эту операцию применяют при изготовлении калибров, шаблонов, лекал. Иногда доводят резцы, шаберы и другие инструменты для получения поверхности. Доводка – окончательная притирка, обеспечивающая высокую износо- и коррозионностойкость при изготовлении измерительных, поверочных инструментов и очень точных деталей. При доводке вместо абразивных порошков используются пасты, в частности паста ГОИ. Нанесение притирочных порошков на притиры (или на поверхности деталей, если притирка осуществляется одной деталью о другую) называется шаржированием и осуществляется двумя способами: во-первых, абразивный порошок можно вдавить в притир стальным закаленным валиком, после чего лишний порошок удалить, а поверхность притира смазать; во-вторых, притир можно смазать и уже поверх смазки насыпать абразивный порошок и вдавить его валиком. Притирочная паста наносится на поверхность притира тонким слоем без вдавливания. Перед шаржированием поверхность притира предварительно промывают керосином и начисто протирают. Притирка плоских поверхностей происходит следующим образом: деталь обрабатываемой стороной накладывают на подготовленную плоскость притира (или другой притираемой детали) и производят 20–30 сложных кругообразных движений с сильным нажимом. Траектория движений должна быть действительно сложной (даже можно сказать – хаотичной), чтобы они не накладывались друг на друга. Скорость движений должна быть приблизительно 20 м/мин (рис. 38).
51

Рис. 38. Притирка плоских поверхностей: а – предварительная; б – окончательная
Затем отработанную притирочную массу убирают с поверхности притира и детали и наносят новый слой (зернистость используемого порошка на этот раз должна быть меньше). Таким образом чередуют притирочные движения с заменой притирочного слоя до получения соответствующего вида изделия (при последних подходах абразивный порошок заменяют пастой: сначала грубой, затем средней и в последнюю очередь тонкой). Окончательную притирку (доводку) осуществляют без нанесения пасты, а лишь со смазыванием притира смесью керосина и машинного масла. В качестве абразивных порошков применяют: корунд, наждак, карборунд, алунд, графит. Абразивные порошки делят по величине зерен на шлифовальное зерно, шлифовальные порошки, микропорошки и тонкие микропорошки. Среди мягких абразивов наиболее применимы пасты ГОИ: грубые (светлозеленого цвета), для удаления десятых долей миллиметра, средние (зеленого цвета), снимающие сотые доли миллиметра, и тонкие (черного цвета с зеленоватым оттенком), обеспечивающие зеркальный блеск. Для обработки материалов типа твердых сплавов, стекла, рубина, керамики применяют алмазосодержащие пасты с размерами зерна 1–40 мкм. Если заготовка очень тонкая в сечении и ее неудобно двигать по притиру, то ее закрепляют на деревянном бруске и перемещают по плите вместе с ним. Притирка узких граней деталей
52
или мелких заготовок производится пакетом. Несколько заготовок с помощью струбцин соединяют в пакет и притирают как широкую поверхность. Для этой цели можно использовать стальные или чугунные направляющие бруски или призмы.
Притирка криволинейных поверхностей имеет свои особенности. Чаще всего криволинейные поверхности двух деталей взаимосоприкасаемы, при этом одна из поверхностей выпуклая, а другая вогнутая (например, пробка и гнездо под нее, вместе составляющие самоварный краник), поэтому притирку этих поверхностей производят одна об другую. Пробку смазывают и присыпают абразивным порошком, вставляют в гнездо и вращают попеременно в разные стороны приблизительно на 1/4 оборота 5–6 раз, после чего делают полный оборот пробки вокруг ее оси. Чередование притирки с заменой притирающих материалов аналогично притиранию широких плоских поверхностей. Проверку точности притирки можно осуществить с помощью грифельного карандаша: наносят линию на одну из притертых поверхностей и проводят ею по другой притертой поверхности. При удовлетворительном качестве притирки карандашная линия равномерно стирается или смазывается по всей длине.
В завершение операции притирки (доводки) детали при необходимости обрабатывают полировальниками – эластичными кругами из фетра или войлока. В качестве механического привода полировальника может выступать двигатель от бормашины или электрическая дрель. Полировку производят очень тонкими абразивными порошками со связкой из вазелина, говяжьего жира. Смазывающая среда не только повышает скорость притирки и доводки, но и улучшает качество их. В зависимости от материала, из которого сделан притир, применяют различные смазки: для чугунных притиров – бензин или керосин, для стальных – машинное масло. При притирке медных сплавов применяют смесь машинного масла с животным жиром. Выбранную смазку смешивают сабразивнымипорошкамиитщательнорастирают.
Для тонкой отделки и притирки плоских и цилиндрических поверхностей применяют притирочные станки. Применяются вертикальные притирочные станки (для обработки наружных поверхностей) и горизонтальные (для наружных и внутренних поверхностей).
53
Вертикальный притирочный станок имеет один или два металлических диска-притира, между которыми в эксцентрично расположенном сепараторе (деталедержателе) помещаются притираемые детали. Притиры вращаются с различной частотой в одну или в противоположные стороны, сепаратор совершает колебательное движение в горизонтальной плоскости. В результате сложного движения обрабатываемых поверхностей деталей относительно притиров обеспечивается равномерная их обработка, высокая точность формы (погрешность до 1–3 мкм). Обработка на притирочных станках позволяет получать поверхности до Rа<0,1 мкм.
Вопросы для самопроверки
1.В чем заключается физическая сущность процессов абразивной обработки?
2.Каковы особенности процесса стружкообразования при абразивной обработке?
3.Какую роль играют процессы теплообразования при шлифовании на формирование качества обработанной поверхности?
4.Каковы причины возникновения силы сопротивления резанию при шлифовании?
5.Какие виды износа шлифовальных кругов вы знаете?
6.Какие основные виды абразивной обработки вы знаете?
7.Перечислите особенности и назовите область применения круглого наружного шлифования, внутреннего шлифования, плоского шлифования.
8.Перечислите особенности и назовите область применения бесцентрового, глубинного, высокоскоростного шлифования.
9.Перечислите особенности и назовите область применения профильного и ленточного шлифования.
10.Перечислите особенности и назовите область применения полирования, хонингования, суперфиниширования.
11.Какие существуют методы разрезки заготовок абразивным инструментом?
12.Перечислите особенности и назовите область применения притирки и доводки.
54
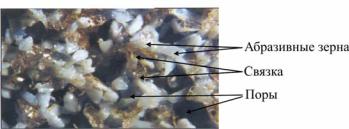
ГЛАВА 2. ХАРАКТЕРИСТИКА АБРАЗИВНЫХ ИНСТРУМЕНТОВ
2.1. Основные определения и виды абразивного инструмента
Абразивный инструмент – это инструмент или набор инструментов, определяющим признаком которого является наличие абразивного материала, производящего механическую обработку изделия. Абразивный инструмент состоит из зерен абразивных материалов, скрепленных каким-либо связующим веществом, и пор (рис. 39). Он изготавливается в основном из искусственных и, в небольшом количестве, из природных абразивных материалов преимущественно путем формообразования или нанесения на какую-либо основу смеси, состоящей из шлифовального зерна и связующего материала, с последующей термической и механической обработкой полученных заготовок. Абразивным инструментом можно снимать стружку толщиной в доли микрометра и сливнуюстружкутолщиной в500–700 мкм.
Рис. 39. Общий вид поверхности и составных элементов абразивного инструмента
Несмотря на универсальные возможности, абразивный инструмент применяется только там, где он не может быть заменен другими инструментами или имеет явное преимущество перед ними. Разработана широкая номенклатура разновидностей инструмента из различных абразивных материалов. Процесс создания новых абразивных материалов продолжается и сегодня, создаются новые виды абразивного инструмента.
55
Абразивный инструмент условно можно разделить на 3 вида.
1. Абразивный инструмент фиксированной геометрической формы: круги всех типов, кольца, сегменты, шлифовальные головки, бруски и т.д. В состав абразивного инструмента этого типа входит абразивный материал определенной зернистости или зернистостей, связующее, наполнители и, при необходимости, упрочняющие элементы. Основные технические параметры: состав, твердость, структура, геометрические размеры. Под размерами абразивного инструмента понимаются размеры в миллиметрах, полностью определяющие его геометрию. Для обычного шлифовального круга это диаметр наружный, высота, диаметр посадочного отверстия, которые приводятся именно в таком порядке без указания размерности через знак «×». Например: 600×80×305, т.е. наружный диаметр – 600 мм, высота (толщина круга) 80 мм, диаметр посадочного отверстия 305 мм. Более сложно обозначаются чашки, круги с выточками, сегменты и т.д. При заказе достаточно указать основные размеры, предусмотренные стандартами, отдельно согласовываются с изготовителем прочие размеры. Размеры кругов регламентируются нормативно-технической документацией, в первую очередь ГОСТами, в которых они, как правило, соответствуют общепринятому в технике размерному ряду. Однако на практике в зависимости от конструктивной особенности обрабатываемой детали абразивная промышленность в состоянии изготовить абразивный инструмент любой формы и размеров, это является чисто технологической задачей и не носит принципиального характера. Инструментальщик, исходя из своего станочного оборудования и обрабатываемой детали, выбирает тип и размер инструмента на базе ГОСТов, если же искомое не находится, то он вправе обратиться со специальным заказом к производителю. Вообще же размеры абразивного инструмента бывают очень различные. При полировке используется микропорошок, размер которого 1 мкм, а отрезной сегментный круг для резки горных пород может достигать 4 м в диаметре. Отрезные круги выпускаются от 40 до 2000 мм в диаметре, шлифовальные круги общего назначения – от 3 до 1060 мм и т.д. Толщины их от долей миллиметра до 1,5 м (для обработки больших поверхностей). Менее широка гамма посадочных отверстий кругов: от 1 до 305 мм. Диаметр посадочного отверстия подбирается, как правило,
56

только по параметрам станочного оборудования. В ГОСТах предусмотрено более 2500 типоразмеров инструмента разной геометрической формы, а при наличии различных связок и шлифматериалов номенклатура доходит до 8000 видов, не неся особой информационной нагрузки. Исходя из вышесказанного, можно не акцентировать внимание на размерах кругов.
2. Гибкий шлифовальный инструмент: шлифовальная шкур-
ка, шлифовальные ленты, лепестковые круги, сетчатые и фибровые диски, щетки из абразивонаполненных волокон.
Шлифовальная шкурка изготавливается на тканевой, бумажной или синтетических основах (в том числе сетчатой, нетканой) с использованием шлифовального зерна, шлифовальных порошков и микропорошков. В зависимости от клеящего вещества, связывающего абразивный материал и основу, шкурка может быть водостойкой (органическая водостойкая смола) или неводостойкой (мездровый клей или неводостойкая органическая смола).
Схема изготовления абразивной шкурки с использованием электростатического поля изображена на рис. 40.
Рис. 40. Схема изготовления абразивной шкурки с использованием электростатического поля
Шлифовальные ленты. В зависимости от назначения из шлифшкурки вырезаются ленты необходимой длины и ширины. Если концы ленты не склеены между собой, то это бобина, если склеены, то
57
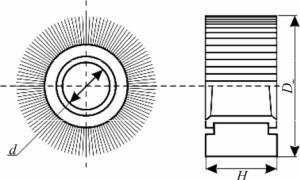
это бесконечная шлифовальная лента. Листы, диски из шлифоваль-
ной шкурки на различных основах, в том числе на самоклеящихся, изготавливаются методом вырубки необходимой формы и размера из соответствующей шлифшкурки.
Лепестковые круги – это круги, состоящие из радиально расположенных и жестко закрепленных одной из торцевых сторон лепестков. В зависимости от конструкции крепления производятся радиальные, торцевые и на оправках. Лепестковые круги изготавливаются из шлифовальной шкурки, методом вырубки или вырезания на «лепестки» и их скреплением на основе или в корпусе. Промышленность выпускает следующие основные виды лепестковых кругов.
Круги лепестковые КШЛ с отверстием (насадные) (рис. 41) нашли наиболее широкое применение в промышленности. Они изготавливаются диаметром от 100 до 400 мм и в основном устанавливаются на стационарном оборудовании.
Рис. 41. Общий вид лепесткового круга КШЛ с отверстием
В специальных автоматах для обработки ножево-вилочных изделий используются наборылепестковых кругов в видевалов для шлифования
иполирования заготовок по плоскости. Шлифование и полирование наружных и внутренних поверхностей посуды из нержавеющих сталей
иалюминия выполняются на специальных машинах для получения матовых или блестящих поверхностей. Круглошлифовальные станки позволяют использовать КШЛ для «продольного» наружного шлифования
58
цилиндрических и конических поверхностей заготовок, длина которых превосходит высоту круга (валов, штоков, гильз и т.п.) и «врезного» наружного шлифования для цилиндрических, конических, ступенчатых и профильных поверхностей (шеек коленчатых валов, фланцев, осей, цапф, шаровых пальцев и т.д.). На универсальном бесцентровошлифовальном станке наиболее эффективно производить полирование цилиндрических, конических и профильных поверхностей в условиях массового икрупносерийного производства.
Сетчатые диски и листы изготавливаются из шлифшкурки на сетчатой основе (лавсан, стеклосетка и т.д.) методом вырубки. Используются взамен шлифшкурки (полирование) и фибровых дисков (зачистка поверхностей). При увеличенном количестве связующего получают жесткие сетчатые диски, которые используются для разрезки заготовок малого диаметра и дорогостоящих материалов. Фибровые диски – абразивные диски, выполненные нанесением шлифовального материала на фибровую основу или методом вырубки дисков из подготовленной фибровой основы. Фибра – твердый, гибкий и пластичный материал из целлюлозы, пропитанный хлористым цинком. Фибровые диски используются для зачистных и шлифовальных операций. Щетки из абразивонаполненных волокон – аналог металлических щеток различной формы, в которых проволока заменена на нити из синтетического материала с включенными в них, при их экструдировании, абразивными зернами либо с нанесенным на поверхность нитей абразивом. Абразивные диски,
листы, губки на волокнистой основе типа Скотч-Брайт изготавливаются методомвырубкииз абразивонаполненного нетканогополотна.
3. Свободный абразив и пасты. Абразивными пастами назы-
ваются смеси абразивных материалов с неабразивными различной густоты, от довольно твердых брикетов до совершенно жидких. И пасты, и свободный абразив используются для операций доводки, полирования и притирки.
2.2. Абразивные материалы и их свойства
Абразивные материалы – это преимущественно материалы природного или искусственного происхождения, содержащие минералы высокой твердости и прочности, зерна и порошки которых способны
59
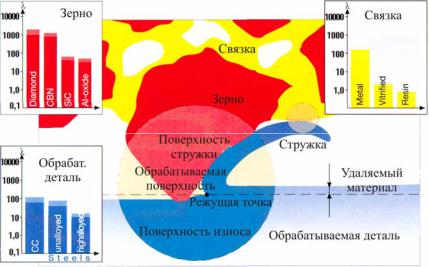
обрабатывать поверхности других тел путем царапания, скобления или истирания, т.е. способные осуществлять абразивную обработку. Их применяют для изготовления шлифовальных и заточных кругов, головок, брусков, хонов, доводочных порошков и паст.
Сравнительная характеристика эффективности работы шлифовальных кругов из различных абразивных материалов с различными связками по данным зарубежных источников наглядно представлена на рис. 42.
Рис. 42. Схема процесса шлифования заготовки и графики эффективности работы различных абразивных материалов и связок
В изготовлении абразивного инструмента столетиями использовались такие виды природных абразивов, как алмаз, гранат, кремень, корунд или наждак. Корунд (англ. corundum < тамильск. kuruntam < санскр. curuvinda – рубин) являлся самым распространенным абразивным материалом, который широко использовался в обработке металлов. Шлифовальные (наждачные) круги из корунда получали с помощью обтесывания (материал хорошо скалывается) и обтачивания еще более твердым абразивом, таким как алмаз, кремень. Природный ко-
60