
Выбор абразивных инструментов и режимов резания для высокоэффективно
..pdf
Из представленных зависимостей следует, что режимы обработки оказывают существенное влияние на стойкость алмазного инструмента. Применение более форсированных режимов обработки дает возможность выбирать их оптимальные значения, обеспечивающие наибольшую производительность при минимальной себестоимости обработки. Рекомендации по выбору рациональных подач и глубины шлифования приведены в табл. 17.
Таблица 1 7
Выбор подач и глубины шлифования в зависимости от размера алмазного зерна и вида шлифования
Вид шли- |
Зернистость |
Глубина шли- |
Продольная |
Поперечная |
Окружная |
||
фования |
алмазного |
фования, мм |
подача, м/мин |
подача |
скорость |
||
|
порошка, мкм |
|
|
|
детали, |
||
|
|
|
|
|
м/мин |
||
|
250/200–160/125 |
0,01–0,02 |
|
|
– |
||
Плоское |
125/100–80/63 |
0,007–0,01 |
10–20 |
1/5–1/3 |
– |
||
|
80/63–50/40 |
0,005–0,007 |
|
|
– |
||
Круглое |
250/200–160/125 |
0,015–0,03 |
|
– |
|
|
|
125/100–80/63 |
0,009–0,010 |
0,5–2,0 |
– |
20–40 |
|||
наружное |
|||||||
80/63–50/40 |
0,005–0,008 |
|
– |
|
|
||
|
|
|
|
||||
Круглое |
250/200–100/80 |
0,007–0,02 |
0,3–3,0 |
– |
20–40 |
||
внутреннее |
80/63–50/40 |
0,001–0,007 |
– |
||||
|
|
|
|||||
Заточка |
250/200–160/125 |
0,01–0,03 |
0,5–3,0 |
– |
– |
|
|
125/100–80/63 |
0,008–0,02 |
– |
– |
|
|||
инструмента |
|
||||||
|
80/63–50/40 |
0,005–0,009 |
|
– |
– |
|
Эффективность процессов алмазной обработки изделий из твердого сплава определяется в основном двумя факторами: производительностью процесса обработки и затратами на алмазный инструмент. При этом повышение производительности процесса обработки (т.е. повышение режимов) приводит к снижению трудовых затрат, но одновременно повышается расход алмазного инструмента.
Оценка себестоимости обработки может быть произведена исходя из расчета затрат на съем 1 см3 твердого сплава. В качестве критерия работоспособности алмазного круга удобно пользоваться коэффициентом шлифования (Кш).
141
Затраты на алмазный инструмент рассчитываются по формуле Ск = (1 : Кш) · (Цк : М) · 4,4· (N : 100 %),
где Кш – коэффициент шлифования; (1 : Кш) – износ слоя алмазного круга (см3) на 1 см3 твердого сплава; Цк – цена круга; M, N – годовая потребность и количество инструмента.
5.3. Выбор абразивных материалов для притирки, доводки и полировки
Все вышеописанные виды абразивного инструмента не могут обеспечить доводку и полирование поверхностей до совершенной (зеркальной). Для получения таких поверхностей используют тонкодисперсные абразивные материалы (менее 40 мкм) в свободном виде, в суспензионном или в виде паст. В качестве полировального инструмента используются притиры, тканевые, войлочные или сизалевые круги, а также струйные аппараты.
Наиболее широко применяются полировальные пасты, состоящие из абразивного и связующего материала. Вследствие этого характеристиками паст следует считать: абразивный материал, зернистость, рецептуру неабразивных материалов, концентрацию (процентное количество абразивногоматериалавпасте), консистенцию(степеньгустотыпасты).
Абразивные материалы в пастах – это твердые абразивы (все виды шлифматериалов, описанные выше) и мягкие материалы: окись железа, окись хрома, маршаллит (порошок кремнезема SiO), меловая пудра, тальк. В качестве связки в пастах используются жиры и масла, главным образом олеин, стеарин, парафин, вазелин и т.д. По консистенции пасты делят на 3 группы: жидкие, мазеобразные и твердые (брикетированные). Ввиду простоты изготовления паст предприятия сами осваивают их выпуск. Однако подбор абразивного материала, его грансостав, определение оптимального количества не всегда производятся профессионально. Необходимо применять стандартные пасты с требуемыми эксплуатационными параметрами.
5.3.1. Выбор паст и суспензий из СТМ
Алмазные пасты изготавливаются по ТУ 2-037-506–85, алмазные суспензии – по ТУ 2-037-628–88. Применяются при ручной и механической доводках, притирке и полировании поверхностей точных
142
деталей из металлов, сплавов и хрупких неметаллических материалов. Это сложные многокомпонентные структурированные системы, состоящие из синтетических алмазов, наполнителей и основы из органических масел, поверхностно-активных веществ (органические кислоты, спирты, эфиры), структурообразователей (воски, парафины, церезины, проксанол-268), смазочные материалы, присадки.
Алмазные пасты оказывают на обрабатываемую поверхность химическое и механическое воздействие. Они образуют тонкодисперсные эмульсии, способствующие равномерному распределению алмаза в рабочей зоне. В состав пасты входят поверхностноактивные вещества, которые облегчают промывку деталей, выводят из зоны отработки легковоспламеняющиеся жидкости, образовавшиеся в процессе обработки шлаки и стружку. Это повышает производительность за счет повышения абразивной способности, улучшает качество обрабатываемой поверхности.
Большое значение при подборе компонентов основ паст и суспензий имеют не только их поверхностная и химическая активность, но и структурно-механические свойства. Одним из параметров, характеризующих структуру паст, является их коллоидная стабильность, т.е. способность основы пасты сопротивляться расслаиванию.
В случаях, когда процесс обработки сопровождается выделением большого количества тепла, пасты и суспензии должны обладать определенной термостойкостью.
На основе поверхностно-активных веществ, структурообразователей, термостойких соединений с различными, адгезионными, антистатическими и другими свойствами и были разработаны разные типы паст, обеспечивающие высокую работоспособность, стабильность свойств.
Алмазные пасты и суспензии изготавливаются из синтетических алмазных порошков разных зернистостей. В зависимости от зернистости они применяются для различных видов обработки. Рекомендации по выбору зернистости алмазных паст для различных видов доводочных работ приведены в табл. 18.
Чем мельче алмазный порошок, а следовательно, чем больше количество зерен, содержащихся в 1 карате, и больше его удельная поверхность, тем меньше должно быть процентное содержание алмаз-
143
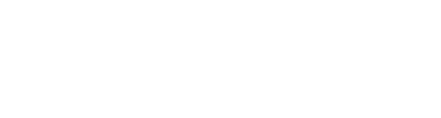
ного порошка в пасте. Порошок в пасте должен быть равномерно распределен по всему объему. От правильного выбора концентрации пасты зависит величина удельного расхода алмаза и эффективности ее применения. Понижение содержания порошка в пастах приводит
кснижению производительности обработки. Высокое содержание порошка в пастах, превышающее оптимальное значение, приводит
кнарушению структуры пасты, накоплению шлама и экранированию рабочих поверхностей абразивного порошка, что также значительно снижает удельную работоспособность пасты.
|
|
|
|
Таблица 1 8 |
|
|
Область применения алмазных паст |
||
|
|
|
|
|
Зернистость |
|
Шероховатость |
Область применения |
|
алмазного |
|
поверхности Rа, мкм |
|
|
порошка, |
|
до обработки |
после |
|
мкм |
|
|
обработки |
|
125/100– |
– |
– |
Шлифование, грубая черновая доводка |
|
50/40 |
|
|
|
различных материалов |
60/40–40/28 |
0,4–0,2 |
0,195–0,155 |
Грубая черновая доводка сталей, сплавов, |
|
|
|
|
|
неметаллических материалов |
28/20–14/10 |
0,16–0,1 |
0,12–0,075 |
Предварительная доводка сталей, спла- |
|
|
|
|
|
вов, неметаллических материалов |
10/7–5/3 |
0,08–0,05 |
0,06–0,038 |
Точная доводка сталей, сплавов, неме- |
|
|
|
|
|
таллических материалов |
3/2–1/0 |
0,04–0,025 |
0,03–0,02 |
Полирование сталей, сплавов, неметал- |
|
|
|
|
|
лических материалов |
1/0,5–0,1/0 |
– |
– |
Тонкое полирование сталей, сплавов, |
|
|
|
|
|
неметаллических материалов |
Были подобраны оптимальные варианты по содержанию алмазного порошка в пастах. Алмазные пасты выпускаются нормальной (Н), повышенной (П) и высокой концентрации (В) в зависимости от массовой доли порошка в пасте для каждой зернистости.
В зависимости от зернистости, пасты условно подразделяются на пять групп, которые окрашиваются в различные цвета. В эти же цвета должна окрашиваться этикетка, наклеенная на емкость с пастой. В табл. 19 приводятся данные о содержании алмазных порошков различных зернистостей в пастах и маркировке.
144

Таблица 1 9
Обозначение паст на этикетках
Зернистость алмазного |
Концентрация алмазного |
Цвет пасты и этикетки |
||||
порошка, мкм |
|
порошка, мас.% |
|
|
||
|
Н |
|
П |
|
В |
|
125/100 100/80 80/63 |
40 |
|
60 |
|
– |
Сиреневый |
63/50 50/40 |
20 |
|
40 |
|
– |
Сиреневый |
60/40 40/28 |
8 |
|
20 |
|
40 |
Красный |
28/20 20/14 14/10 |
6 |
|
15 |
|
30 |
Голубой |
10/7 7/5 5/3 |
4 |
|
10 |
|
20 |
Зеленый |
3/2 2/1 1/0 |
2 |
|
5 |
|
10 |
Желтый |
1/0,5–0,1/0 |
2 |
|
5 |
|
10 |
Не окрашивается |
По согласованию с потребителем возможно изготовление паст с другими массовыми долями алмазов в пасте, без красителя, с применением нестандартных зернистостей алмазных порошков. В табл. 20 приведены данные по концентрации алмазного порошка в суспензиях.
|
|
|
Таблица 2 0 |
Содержание алмазного порошка в пастах |
|||
|
|
|
|
Зернистость алмазного |
Концентрация алмазного порошка, мас. % |
||
порошка, мкм |
Н |
П |
В |
10/7–5/3 |
4 |
10 |
20 |
3/2–1/0 |
2 |
5 |
10 |
0,7/0,3; 0,5/0,1 |
2 |
5 |
10 |
0,3/0; 0,1/0 |
2 |
5 |
10 |
Одним из основных показателей качества изготовленной пасты является ее абразивная способность. При контроле абразивная способность паст определяется количеством сошлифованного слоя образца из твердого сплава марки ВК6 или ВК8 навеской пасты за установленное машинное время (как разница массы блока с образцами из твердого сплава до и после испытаний).
Абразивная способность паст в зависимости от зернистости и концентрации алмазного порошка в пасте представлена в табл. 21.
Субмикропорошки применяются в виде паст и суспензий для обработки твердых сплавов, полупроводников и других изделий из труднообрабатываемых материалов, к которым предъявляются особенно высокие требования по точности и качеству поверхности.
145

|
|
|
|
Таблица 2 1 |
|
Абразивная способность алмазных паст |
|||||
|
|
|
|
|
|
Зернистость алмазного |
|
Абразивная способность пасты, мг (не менее) |
|||
порошка, мкм |
|
Н |
П |
|
В |
60/40 |
|
67 |
127 |
|
175 |
40/28 |
|
62 |
123 |
|
163 |
28/20 |
|
57 |
112 |
|
157 |
20/14 |
|
52 |
102 |
|
153 |
14/10 |
|
47 |
97 |
|
148 |
10/7 |
|
42 |
93 |
|
143 |
7/5 |
|
37 |
82 |
|
137 |
5/3 |
|
32 |
65 |
|
108 |
Рекомендуемая скорость съема материала при полировании пастами из алмазных субмикропорошков приведена в табл. 22. В зависимости от консистенции пасты подразделяются на мазеобразные (М) и твердые (Т).
Консистенция алмазных паст определяется пенетрацией (числом проницаемости) на пенетрометре. Консистенция паст при температуре 20±50 °С по показаниям пенетрометра должна соответствовать: мазеобразной (М) – от 100 до 400 делениям пенетрометра, твердой (Т) –
от 20 до 80.
|
|
|
Таблица 2 2 |
|
Рекомендуемая скорость съема материала при полировании |
||||
|
|
|
|
|
Зернистость алмазного |
Массовая доля |
Скорость съема материала, мкм/мин, |
||
порошка, мкм |
алмазов в пасте, % |
не менее |
||
|
|
АСМ5 – М |
|
АСМ5 – Т |
1/0,5 |
2 |
0,8 |
|
0,65 |
|
5 |
0,9 |
|
0,70 |
|
10 |
1,0 |
|
0,75 |
0,7/0,3 |
2 |
0,6 |
|
0,45 |
|
5 |
0,7 |
|
0,50 |
|
10 |
0,8 |
|
0,60 |
0,5/0,1 |
2 |
0,4 |
|
0,35 |
0,5/0 |
5 |
0,45 |
|
0,40 |
|
10 |
0,5 |
|
0,45 |
0,3/0 |
2 |
– |
|
|
0,1/0 |
5 |
|
|
– |
|
10 |
|
|
|
146
Мазеобразные пасты поставляются потребителям в шприцах по 5, 10 или 20 г, в тубах по 40 и 80 г или банках по 500 и 1000 г. Твердые пасты – в специальных футлярах с подвижным дном, позволяющим выдавливать пасту.
В зависимости от состава основы пасты подразделяются на следующие виды:
1.Смываемые органическими (О) растворителями (керосином, бензином, спиртом и т.п.), которые разбавляются индустриальными маслами, керосином или смесью.
2.Смываемые водой (В), которые разбавляются и смываются
водой.
3.Универсальные, смываемые как водой, так и органическими растворителями (ВО), разбавляются и смываются дистиллированной водой, спиртом, индустриальными маслами, бензином, керосином.
Пасты, смываемые органическими растворителями, рекомендуются для обработки металлов и сплавов.
Пасты и суспензии, смываемые водой, рекомендуются для обработки неметаллических материалов, а также металлов в тех случаях, когда недопустимо применение огнеопасных жидкостей для промывки обработанных изделий.
Пасты и суспензии, смываемые водой и органическими растворителями, рекомендуются для обработки металлов, сплавов и неметаллических материалов.
Рекомендации по выбору типа паст для различных видов доводочных работ представлены в табл. 23.
|
|
|
Таблица 2 3 |
|
Характеристика и область применения алмазных паст |
||
|
|
|
|
Тип |
Смываемость |
Консистенция |
Область применения |
пасты |
|
|
|
|
|
|
Обработка черных и цветных металлов, |
Г |
В |
М |
сталей, сплавов, неметаллических и |
|
|
|
полупроводниковых материалов |
Л |
ВО |
М |
Обработкалегированныхсталей, чугуна, |
|
|
|
керамики, металлокерамики, твердых |
|
|
|
сплавов, феррита, сапфира, драгоценных, |
|
|
|
полудрагоценных, поделочныхкамней |
147

|
|
|
|
Окончание табл. 2 3 |
|
Тип |
Смываемость |
Консистенция |
Область применения |
||
пасты |
|
|
|
|
|
|
|
|
|
Обработка стекла, полупроводниковых |
|
X |
В или ВО |
|
М или Т |
материалов, твердосплавного инстру- |
|
|
мента, армированных пластмасс, нержа- |
||||
|
|
|
|
||
|
|
|
|
веющих сталей |
|
|
|
|
|
Обработка стекла, полупроводниковых |
|
Э |
В |
М |
материалов, твердосплавного инстру- |
||
мента, армированных пластмасс, хруп- |
|||||
|
|
|
|
||
|
|
|
|
ких неметаллических материалов |
Пример условного обозначения пасты из микропорошка синтетических алмазов марки АСН зернистостью 28/20, с повышенной массовой долей алмазов (П) в пасте, смываемой водой и органическими растворителями (ВО), мазеобразной консистенции (М) типа Л: АСН 28/20 ПВОМЛ.
Хранить алмазную пасту следует при температуре не выше 30 °С. При более высокой температуре вязкость ее уменьшается, происходит расслоениепасты иалмазный порошок осаждается.
5.3.2.Выбор материалов для доводочных притиров
иполировальников
Большое значение для эффективного использования паст имеет выбор материала притира или полировальника. В качестве материала для притира применяют чугун, сталь, латунь, медь, древесину, кожу, войлок, фетр и др. Выбор притира зависит от материала обрабатываемой детали, его твердости и требуемого качества обработанной поверхности.
Чугун имеет высокую производительность, необходимую геометрию поверхности, но дает более грубую обработку, чем притиры из более легкого материала. Чугун используется при обработке наиболее твердых материалов пастами крупных зернистостей. Для изготовления притиров следует применять мелкозернистый чугун с минимальной пористостью.
Сталь используется вместо чугуна в тех случаях, когда при малом поперечном сечении притира прочность чугуна оказывается недостаточной. Сталь применяется только длясъема больших припусков.
148
Латунь, медь лучше использовать при доводке изделий алмазной пастой средних зернистостей. Для увеличения жесткости притиров применяются стальные сердечники. Медные притиры при сильном нагреве склонны к засаливанию, вэтом случае их надо увлажнять.
Древесина различных пород от твердых (граб, бук, дуб) до самых мягких (береза, липа) хорошо удерживает алмазные зерна, снижает расход пасты. Притиры делают из поперечных срезов древесины.
Стекло рекомендуется использовать при полировании полудрагоценных камней, корунда, граната и т.п.
Фибра применяется для притиров, которые должны хорошо сохранять свою форму при использовании паст средних и мелких зернистостей. Фибра обеспечивает очень низкую шероховатость поверхности.
Кожу, войлок, фетр следует применять только при использовании паст мелких зернистостей для окончательной обработки поверхностей и полирования до зеркального блеска. Эти материалы могут быть использованы в виде вращающихся дисков, оправок или вставок при возратно-поступательном движении.
Для осуществления процесса доводки необходимо, чтобы притир шаржировался, т.е. чтобы абразивные зерна вдавливались в его поверхность.
В одном карате алмазного порошка содержится от десятков тысяч до сотен миллиардов зерен, поэтому на притир необходимо наносить оптимальное количество пасты, снижая тем самым ее расход и себестоимость обработки.
Для пасты каждой зернистости следует применять отдельный притир. При переходе от пасты крупной зернистости к мелкой обрабатываемую деталь требуется тщательно промывать.
При выборепритиранеобходимо соблюдать следующиеусловия:
1)притир должен быть мягче обрабатываемого материала;
2)твердые притиры следует применять при больших припусках
ипастах крупных зернистостей;
3)мягкие притиры рекомендуются для получения минимальной шероховатости обработанной поверхности.
149
При плоской доводке вращающимися притирами необходимо на рабочей поверхности притира нарезать кольцевые канавки, которые позволяют лучше выводить отработанный шлам, увеличить удельное давление при постоянном усилии прижима. При ручной доводке на притире лучше делать поперечные канавки.
5.3.3. Выбор и применение паст из карбида титана
Абразивные пасты карбида титана (КТ) выпускаются по ТУ 2-037-273–88 в диапазоне зернистостей: шлифпорошков 630/500– 50/40; микропорошков 60/40-Н/О.
Это сложные многокомпонентные структурированные системы, состоящие из классифицированных по зернистостям порошков КТ и основы из органических масел, поверхностно-активных веществ, структурообразователей, смазочных материалов.
Абразивные пасты КТ оказывают на обрабатываемую поверхность химическое и механическое воздействие. Они образуют тонкодисперсные эмульсии, способствующие равномерному распределению абразива в рабочей зоне. В состав пасты входят поверхностноактивные вещества, которые облегчают промывку деталей, выводят из зоны обработки легковоспламеняющиеся жидкости, образующиеся в процессе обработки шлаки и стружку. Это обеспечивает высокую работоспособность паст, стабильность их свойств.
Пасты применяются при шлифовании, доводке, полировании деталей авиационной техники, прецизионных подшипников, запорнотормозной аппаратуры и узлов пневмоприводов (кранов, вентилей, гидроциклонов), инструментальной оснастки, а также для обдирки крупногабаритных деталей и узлов.
В зависимости от массовой доли порошка карбида титана концентрация выпускаемых паст может быть нормальной (Н) и повышенной (П). В табл. 24 приведены данные по содержанию порошков КТ в зависимости от зернистости.
По консистенции абразивные пасты КТ выпускается мазеобразные (М). Мазеобразные пасты поставляются расфасованными в тубы по 40 и 80 г, в банках по 500 и 1000 г.
150