
Оперативно-производственное планирование
..pdf−выпуск продукции в натуральном или денежном выражении
врасчёте на 1 тыс. руб. стоимости активной части основных фондов или на 1 тыс. руб. стоимости производственного оборудования;
−выпуск продукции в натуральном или денежном выражении
врасчёте на 1 м2 полезной производственной площади (площади, занятой производственным оборудованием или отведённой под сборку изделий) и др.
2. Показатели степени вовлечения оборудования в производ-
ство. Для оценки экстенсивного использования оборудования применяют показатели, характеризующие степень вовлечения оборудования в производство:
1. Удельный вес установленного оборудования во всём наличном парке оборудования
Уу/н = |
nу |
, |
(2.35) |
|
nн |
||||
|
|
|
где Уу/н – удельный вес установленного оборудования во всём наличном парке оборудования; nу – количество установленного оборудования, шт.; nн – количество наличного оборудования, шт.
2. Удельный вес фактически работающего оборудования по отношению к наличному оборудованию
Ур/н = |
nр |
, |
(2.36) |
|
nн |
||||
|
|
|
где Ур/н – удельный вес фактически работающего оборудования по отношению к наличному оборудованию; nр – количество фактически работающего оборудования, шт.; nн – количество наличного оборудования, шт.
3. Удельный вес фактически работающего оборудования во всём установленном оборудовании
Ур/у = |
nр |
, |
(2.37) |
|
nу |
||||
|
|
|
61

где Ур/у – удельный вес фактически работающего оборудования во всём установленном оборудовании; nр – количество фактически работающего оборудования, шт.; nу – количество установленного оборудования, шт.
Пример. На токарном участке цеха имеется в наличии 10 станков, из них установлено и готово к работе 8 станков, фактически эксплуатируется 7 станков.
Удельный вес установленного оборудования во всём наличном парке оборудования
Уу/н = |
nу |
= |
|
8 |
= 0,8000, |
или80,00 %. |
|
nн |
10 |
||||||
|
|
|
|
Удельный вес фактически работающего оборудования по отношению к наличному оборудованию
Ур/н = |
nр |
= |
|
7 |
= 0,7000, |
или70,00 %. |
|
nн |
10 |
||||||
|
|
|
|
Удельный вес фактически работающего оборудования во всём установленном оборудовании
Ур/ у = nр = 7 = 0,8750, или87,50 %. nу 8
Показатели вовлечения наличного оборудования в процесс производства широко используются при анализе фондоотдачи основных производственных фондов, когда необходимо выявить излишнее и малоиспользуемое оборудование, количество неустановленного оборудования, определить пути лучшего использования парка машин (ускорение монтажа неустановленного оборудования, реализация ненужного оборудования, сокращение сроков ремонта оборудования).
3. Показатели оценки использования машин и оборудования.
Оценка и анализ использования машин и оборудования осуществля-
ются с помощью коэффициента экстенсивной нагрузки оборудова-
62
ния (или коэффициента экстенсивного использования оборудования)
(Кэкс), т.е. использования его во времени, который определяется отношением фактического времени работы оборудования (Fф) к плановому действительному (полезному) фонду времени, или к номинальному (режимному) фонду времени, или к календарному фонду времени по следующим формулам:
Кэкс1 |
= |
|
|
Fф |
; |
(2.38) |
||
|
|
Fк |
||||||
|
|
|
|
|
|
|
|
|
Кэкс2 |
= |
|
Fф |
|
|
; |
(2.39) |
|
Fн |
|
|
||||||
|
|
|
|
|
|
|
|
|
Кэкс3 |
= |
Fф |
. |
(2.40) |
||||
|
||||||||
|
|
|
|
Fд |
|
|
|
|
В первом случае коэффициент экстенсивной нагрузки характеризует использование календарного фонда времени оборудования, во втором – режимного (номинального) фонда времени, в третьем – планового полезного (действительного) фонда времени работы оборудования.
Пример. Фактический фонд времени работы оборудования равен 3700 ч в год, плановый действительный фонд времени оборудования равен 3800 ч в год.
Кэкс = 3700 / 3800 = 0,9737, или 97,37 %.
Коэффициент интенсивной нагрузки оборудования (или коэффициент интенсивного использования оборудования) (Кинт), т.е. его использования по мощности, определяется отношением фактической производительности оборудования в единицу времени (Пф) к максимально возможной или плановой производительности оборудования в единицу времени (Ппл):
63
К |
инт |
= |
Пф |
. |
(2.41) |
|
|||||
|
|
Ппл |
|
Показатель интенсивной нагрузки оборудования характеризует уровень организации труда на рабочем месте, который позволяет использовать оборудование на полную мощность в течение длительного времени, а также уровень надёжности оборудования. Чем выше надёжность оборудования, тем ближе коэффициент интенсивной нагрузки к единице.
Пример. Фактическая производительность оборудования по итогам отчётного года составила 50 дет./ч, максимально возможная – 65 дет./ч.
Кинт = 50/65 = 0,7692, или 76,92 %.
Обобщающим показателем, характеризующим использование машин и оборудования по времени и по мощности, является коэф-
фициент интегральной нагрузки (Кинтегр), определяемый как произ-
ведение коэффициентов интенсивной и экстенсивной нагрузок по формуле
Кинтегр = Кэкс Кинт . |
(2.42) |
Пример. Коэффициент экстенсивного использования оборудования составил 0,97, коэффициент интенсивного использования оборудования равен 0,77.
Кинтегр = 0,97 · 0,77= 0,7469,или 74,69 %.
Основные пути улучшения использования производственных мощностей состоят в использовании экстенсивных и интенсивных резервов, а также в повышении общеобразовательного и технического уровня рабочих.
64
Экстенсивные резервы измеряются единицами неиспользуемого оборудования и находят своё выражение:
−в увеличении единиц установленного и фактически работающего оборудования;
−совершенствовании организации планово-предупредитель- ного и капитального ремонта оборудования;
−повышении сменности работы цехов и участков;
−повышении уровня механизации сборочно-монтажных ра-
бот;
−совершенствовании организации работы вспомогательных и обслуживающих служб и цехов предприятия;
−развитии рационального кооперирования заводов, цехов и участков.
Экстенсивные резервы должны использоваться в первую очередь, так как их вовлечение в производство не требует больших капитальных вложений, ведёт к росту фондоотдачи и рентабельности производства. Резервы экстенсивного использования имеют естественный предел: больше 365 дн. в году и 24 ч в сутки оборудование работать не может.
Интенсивные резервы заключаются в увеличении объёма выпуска продукции единицей оборудования в единицу времени его работы. Интенсивные резервы заключаются:
−в совершенствовании конструкции выпускаемых изделий;
−углублении специализации заводов, цехов и участков с целью увеличения серийности производства и внедрения современных технологий;
−расширении унификации и стандартизации изделий;
−обновлении и модернизации оборудования;
−повышении технической оснащённости производства;
−применении скоростных методов обработки (повышение скорости резания, увеличениескорости подачи, глубины резания);
65

−внедрении многошпиндельной обработки, многолезвийного инструмента, многорезцовых держалок;
−комплексной механизации и автоматизации производства;
−внедрении научной организации труда на рабочих местах. Повышение эффективности использования производственной
мощности предприятия является комплексной проблемой, не только охватывающей вопросы капитальных вложений и использования оборудования, но и тесно связанной с вопросами организации, планирования, технической подготовки и управления производством.
2.6. Распределение производственной программы
по плановым периодам
Производственная программа предприятия составляется, как правило, на один год с последующим её распределением по кварталам и месяцам. Оптимальность распределения производственной программы по более коротким периодам имеет очень большое значение для повышения эффективности производства и улучшения качества выпускаемой продукции.
Распределение годовых заданий по кварталам (месяцам) необходимо осуществлять с учётом следующих факторов1:
−установленных договорами сроков поставки продукции потребителям;
−увеличения выпуска продукции за счёт прироста и улучшения использования производственных мощностей, а также за счёт мероприятий, предусмотренных планом инноваций;
−сроков вводавдействие новыхмощностей иоборудования;
−обеспечения равномерной загрузки всех производственных подразделений;
−повышения серийности (массовости) производства;
−числа рабочих дней в каждом квартале;
1 Ильин А.И. Планирование на предприятии : учеб. пособие. – Минск: Новое знание, 2005. – С. 616.
66
−сезонности и сменности работы;
−сезонности сбыта продукции;
−возможного выбытия основных фондов, а также остановки отдельныхагрегатов, участков ицехов для ремонта оборудования;
−снятия с производства устаревших видов изделий и продукции, не соответствующих по своим технико-экономическим показателям современному уровню развития науки и техники, а также не пользующихся спросом потребителей, и замены их новыми видами.
В массовом и крупносерийном производстве, когда потребле-
ние продукции не носит сезонного характера, распределение производственной программы по плановым периодам производится про-
порционально количеству рабочих дней.
В остальных случаях распределение заданий производится
сучётом сроков поставки продукции потребителям. Сроки постав-
ки продукции определяются на основании заключённых договоров
спредприятиями и организациями-потребителями. Для этого в договорах должны быть определены конкретные условия поставок: полный ассортимент, количество и сроки поставки по каждой его позиции; специальные требования к качеству продукции; объёмы партий и периодичность их поставок; способы упаковки и транспортировки продукции.
2.7. Выбор метода изготовления производственной программы
Планирование способа изготовления производственной программы определяет, как будет организован производственный процесс в пространстве и во времени.
Различают поточный, партионный и единичный способы изготовления изделий.
Поточный метод изготовления изделий является наиболее прогрессивным, позволяет реализовать большинство принципов рациональной организации производственного процесса. Поточное
67
производство основано на ритмичной повторяемости согласованных во времени технологических операций, выполняемых параллельно на специализированных рабочих местах, расположенных по ходу следования технологического процесса изготовления изделий.
Основными преимуществами данного метода являются:
1)повышение производительности труда в результате механизации и автоматизации операций, внедрения эффективных технологий и специальных быстродействующих средств технологического оснащения, оптимальной планировки рабочих мест, приобретения рабочими навыков выполнения повторяющихся операций;
2)сокращение длительности производственного цикла, что становится возможным в результате специализации рабочих мест, их бесперебойного обслуживания в соответствии с ритмом, устранения перерывов в движении деталей по рабочим местам, сокращения расстояния и времени их транспортировки, запараллеливания процессов и совмещения операций;
3)уменьшение заделов незавершённого производства и ускорение оборачиваемости оборотных средств в результате сокращения длительности производственного цикла;
4)снижение себестоимости продукции в результате комплекса мер по рационализации производства и сокращения затрат всех видов ресурсов.
Основной недостаток поточного метода заключается в том, что однообразие работы, выполняемой рабочими в быстром темпе, ослабляет внимание и способствует быстрой утомляемости, подавляет творческую активность рабочего (не случайно именно в подразделениях с поточным производством наблюдается повышенная текучесть кадров).
В мировой практике отмечается несколько успешных способов устранения недостатков поточного производства.
На предприятиях шведской компании Volvo однообразные участки работ полностью автоматизированы (рис. 2.2).
68
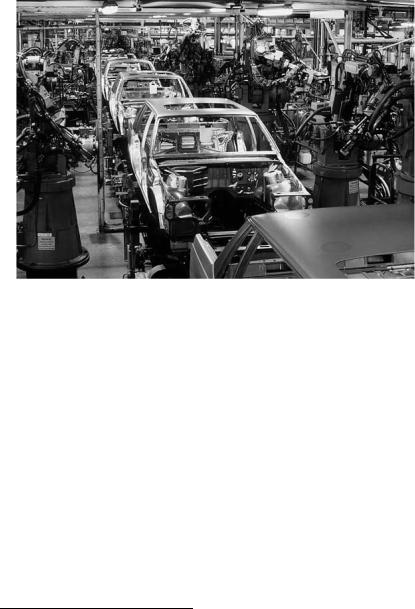
Рис. 2.2. Роботизированная линия сборки
На других участках вместо конвейера с принудительным ритмом применяется полустендовая групповая сборка. Для этого разрабатываются комплексные укрупнённые операции, выполнение которых поручается группе рабочих, т.е. создаются условия для внедрения коллективных форм организации труда. Члены группы самостоятельно решают, как распределить между собой работу, чтобы в установленное время выполнить задание, и полностью отвечают за качество выполненных работ. Главным отличием этого способа является то, что темп работы задает коллектив, обеспечивая при этом среднюю запланированную производительность за смену1.
В Германии и других развитых странах на предприятиях электротехнической и автомобильной промышленности на непрерывнопоточных линиях, где сборочные операции выполняются вручную, создаются гибкие взаимосвязи рабочих, занятых на ручных операциях перед автоматизированными участками и после них. Это по-
1 Рязанова В.А., Люшина Э.Ю. Организация и планирование производства: учеб. пособие / под ред. М.Ф. Балакина. – М.: Академия, 2010. – С. 89.
69

зволяет освободить рабочих как от жесткой связи друг с другом, так
иот такта потока и создать некоторые условия для роста квалификации, повышения содержательности и привлекательности труда. Каждая бригада на свое усмотрение осуществляет перекомпоновку операций, организует труд своих работников, исходя из характера операций, возрастного и полового состава, уровня квалификации. В бригаде создаются резервные рабочие места, которые используются для обучения новичков и выполнения операций за отстающих рабочих, благодаря чему создаются возможности исполнения заданного объёма работ сокращённым штатом1.
Японский опыт заключается в укрупнении операций и обеспечении на этой основе профессиональной ротации кадров, а также в предоставлении возможности каждому рабочему остановить конвейер в любой момент. Рабочий на конвейере осваивает до 10 операций, которые он в состоянии выполнять в высоком темпе, заданном скоростью конвейера. Переход с операции на операцию происходит несколько раз в день по разработанному графику. Каждое рабочее место оснащено кнопкой для остановки конвейера теми рабочими, которые не успевают качественно выполнить операцию или ощущают явные признаки переутомления. Норма простоя конвейера составляет 20 мин в смену. Для снятия психологического напряжения и повышения заинтересованности в труде конвейер размещен таким образом, чтобы рабочие могли видеть конечный продукт, сходящий с линии2.
Объектом планирования в поточном производстве является поточная линия. Поточная линия – это совокупность рабочих мест, расположенных в последовательности технологического процесса
ипредназначенных для выполнения синхронизированных операций. Синхронизация операций состоит в том, что технологический процесс и организация труда проектируются с таким расчётом, чтобы время обработки или сборки одного изделия на каждом рабочем
1Рязанова В.А., Люшина Э.Ю. Указ. соч. С. 89–90.
2Там же. С. 90.
70