
Учебное пособие 800322
.pdfТаблица 5.2 Классификация коррозионной стойкости металлов по потере массы
Пятибалльная шкала |
|
Десятибалльная шкала |
|||
Группа стойкости |
Потеря массы |
Балл |
|
Скорость |
|
|
Группа стойкости |
коррозии, |
|||
|
г/(м2 ч) |
|
|||
|
|
|
|
мм/год |
|
Весьма стойкий |
<0,1 |
1 |
Совершенно стойкий |
<0,001 |
|
Стойкий |
0,1...1 |
2 |
Весьма стойкий |
0,001...0,005 |
|
Сравнительно стойкий |
1...3 |
3 |
Стойкий |
0,001...0,01 |
|
Малостойкий |
3...10 |
4 |
Сравнительно стойкий |
0,01...0,05 |
|
Нестойкий |
>10 |
5 |
0,01...0,1 |
||
|
|||||
|
|
6 |
Понижено стойкий |
0,1...0,5 |
|
|
|
7 |
0,1...1 |
||
|
|
8 |
Малостойкий |
1...5 |
|
|
|
9 |
1...10 |
||
|
|
10 |
Нестойкий |
>10 |
Изменение объема образцов. Объемный показатель коррозии можно определить по формуле
kv=Vг /S tи ,
где Vг – объем выделившихся или поглощенных газов; S – площадь поверхности образца; tи – продолжительность испытаний.
Скорость коррозионного разрушения. Скорость коррозионного разру-
шения К, г/(м2 год), вычисляется по формуле
K=( mо- m1)/Sτ ,
Пересчет потери массы металла на проницаемость П (потери при взвешивании образца до и после испытаний), мм/год, выполняется в соответствие с уравнением
П=К*8,76/ ρ ,
где ρ – плотность испытуемого металла, г/см3.
Изменение механических свойств образцов. Изменения механических свойств контролируют с помощью характеристик временного сопротивления и относительного удлинения. Показатель коррозионной стойкости по изменению временного сопротивления Kσв, % рассчитывается по формуле
Kσв =(σво-σв1)./ σво 100% ,
50
где σво и σв1-временные сопротивления образцов до и после коррозионных испытаний.
Оценка коррозионной стойкости по изменению относительного удлинения Кδ выполняется аналогичным образом:
Кδ=(δо-δ1)/ δо 100% ,
где δо и δ1-относительное удлинение образца соответственно до и после испытания.
Если в процессе коррозии уменьшается сечение образца, образуются трещины, расслоения или протекает межкристаллическая коррозия, то стойкость металла Кω характеризуют по относительному изменению электросопротивления
Кω= (Rо- R1)/ Rо ,
где Rо, R1 - электросопротивление образцов до и после испытания.
5.5. Методы защиты металлических конструкций от коррозии
Классификация методов защиты металлоконструкций от коррозии.
Разумеется можно придать металлу повышенную коррозионную стойкость при изготовлении, например, легированием, но такой металл получается очень дорогим, ибо легирующие присадки дефицитны и дороги. Поэтому в строительстве используется обычная сталь, которую приходится защищать от коррозии уже в изделиях.
Различают методы защиты от коррозии конструкций, работающих в атмосферных условиях, и конструкций, находящихся в почвенной среде, т.е. в заглубленных сооружениях, а так же прочие методы для некоторых ранее перечисленных условий эксплуатации. Каждый такой метод объединяет большую группу способов. Выбор способа и его реализация зависят от всестороннего учёта ряда факторов, характеризующих как металл и конструкцию из него, так и агрессивную среду, условия протекания коррозионного процесса. Часто бывает так, что единственно возможен только один вполне определённый способ.
Классификация методов защиты металлических конструкций от коррозии приведена в табл. 5.3.
5.5.1. Методы изоляции конструкций от агрессивных сред
Изоляция металла от среды. Защита конструкций от атмосферной коррозии осуществляется изоляцией металла от действия агрессивной среды.
51

Таблица 5.3
Этот метод весьма распространён не только в атмосферных условиях, но и в заглубленных сооружениях. Изоляция металла от среды может производиться следующими способами:
Нанесением лакокрасочных покрытий. В практике проведения антикор-
розионных работ наиболее распространены лакокрасочные покрытия на органической основе благодаря низкой стоимости материалов (в настоящее время более 80 % металлоконструкций защищаются именно такими покрытиями).
Лакокрасочное покрытие состоит из ряда последовательно нанесённых слоев грунтовки, шпаклёвки, краски и лака (рис. 5.5).
Рис. 5.5. Структура лакокрасочного покрытия: 1-металл, 2-шпаклёвка, 3 – грунтовка, 4 – краска, 5 – лак
52
Лаки, краски, а также различные смазки, хотя частично и проницаемы для воздуха и жидкостей, но широко применяются также потому, что их просто наносить и они придают конструкциям красивый внешний вид.
Для нанесения любого защитного покрытия металл зачищается до блеска и не позже чем в течение четырёх часов на него наносятся грунтовка, потом шпаклёвка, далее краска, эмаль и сверху лак с перерывами для высыхания каждого слоя.
Основными требованиями к покрытию являются: хорошая адгезия, непроницаемость к агрессивным средам, долговечность, технологичность проведения повторной окраски, экономичность с учётом срока эксплуатации.
Законченное покрытие должно быть сплошным, ровным, без наплывов и подтёков. Прочность сцепления его с поверхностью проверяется следующим образом: лезвием делают взаимно перпендикулярные надрезы до основания, причём плёнка не должна при этом отслаиваться и крошиться. Толщина её проверяется электромагнитными щупами и толщиномерами.
Работы по нанесению покрытий должны вестись со строгим соблюдением правил техники безопасности.
Покрытие металлами. Широко распространённым способом защиты металлов от коррозии является покрытие их слоем других металлов. Покрывающие металлы сами коррозируют с малой скоростью, так как покрываются плотной оксидной плёнкой. Покрывающий слой наносят различными методами: горячее покрытие (кратковременное погружение в ванну с расплавленным металлом), гальваническое покрытие (электроосаждение из водных растворов электролитов), металлизация (напыление), диффузионное покрытие (обработка порошками при повышенной температуре в специальном барабане).
Впроизводстве широко используется химическое нанесение металлических покрытий на изделия. Процесс химического металлирования является каталитическим или автокаталитическим, а катализатором является поверхность изделия. Используемый раствор содержит соединение наносимого металла и восстановитель. Поскольку катализатором является поверхность изделия, выделение металла происходит именно на ней, а не в объёме раствора.
Внастоящее время разработаны методы химического покрытия металлических изделий никелем, кобальтом, железом, палладием, платиной, медью, золотом, серебром, родием, рутением и некоторыми сплавами на основе этих металлов. В качестве восстановителей используют гипофосфит и боргидрид натрия, формальдегид, гидразин.
Вповседневной жизни человек чаще всего встречается с покрытиями железа цинком и оловом. Листовое железо, покрытое цинком, называют оцинкованным железом, а покрытое оловом называют белой жестью.
Металлические покрытия защищают конструкции от коррозии при сохранении сплошности. При нарушении покрывающего слоя коррозия изделия протекает даже более интенсивно, чем без покрытия. Это объясняется работой гальванического элемента железо металл. Трещины и царапины за-
53
полняются влагой, в результате чего образуются растворы, ионные процессы в которых облегчают протекание коррозионного процесса.
Металлические покрытия дорогие из-за большой дефицитности исходных материалов и способа защиты (напыление, гальванический способ и т.д.). Однако при анализе вариантов защиты следует учитывать, что в промышленной (среднеагрессивной) атмосфере слой цинка толщиной 50...200 мк обеспечивает сохранность защитного покрытия до 50 лет. Такой срок службы металлизационного покрытия практически без возобновления позволяет снизить эксплуатационные затраты по сравнению с лакокрасочным покрытием. В особо агрессивных средах хорошие результаты даёт алюминиевое покрытие в комбинации с лакокрасочным.
Применение ингибиторов. Применение ингибиторов один из самых эффективных способов борьбы с коррозией металлов в различных агрессивных средах. Ингибиторы это вещества, способные в малых количествах замедлять протекание химических процессов или останавливать их. Ингибиторы, добавленные в окрасочный состав или использованные для пропитки обёрточной бумаги, в восемь-десять раз продлевают срок службы металла, а потому их считают химической бронёй металлов. Добавление ингибиторов в агрессивную среду, например, кислоту позволяет хранить её в металлических ёмкостях. Обёртывание ингибированной бумагой удобно тем, что на распаковку изделий и приведение их в рабочее состояние затрачивается минимум сил и средств. Наиболее часто применяются следующие ингибиторы: нитрит натрия, добавляемый, например, к холодильным соляным растворам, фосфаты и силикаты натрия, бихромат натрия, различные органические амины, сульфоокись бензила, крахмал, танин и т. п. Поскольку ингибиторы со временем расходуются, они периодически должны добавляться в агрессивную среду.
Эффективность действия ингибиторов зависит в основном от условий среды, поэтому универсальных ингибиторов нет. Для их выбора требуется проведение исследований и испытаний.
Использование цементных покрытий. Для защиты стальных водяных труб от коррозии используют цементные покрытия. Поскольку коэффициенты теплового расширения портландцемента и стали близки, то он довольно широко применяется для этих целей. Недостатком портландцементных покрытий является высокая чувствительность к механическим ударам.
Способы подготовки поверхности и нанесения защитных покрытий.
Большое, порой определяющее, влияние на эффективность противокоррозионной защиты оказывает качество подготовки поверхности. Выбор конкретного способа подготовки поверхности зависит от места проведения работ (на заводе или в условиях строительно-монтажной площадки), сложности конфигурации изделия или конструкции, возможности остановки производства (при повторных окрасках) и др.
54
Основными способами подготовки поверхности под защитные поверхности являются:
-механическая очистка дробеструйная, пескоструйная, дробемётная, гидропескоструйная, а также металлическими щётками с пневматическим или электрическим приводом;
-химическая очистка с помощью травильных паст (выделяют следующие способы: фосфатирование, пассивация, анодирование);
-термическая очистка пламенем ацетилено-кислородной горелки или паяльной лампы. Значительные объёмы работ по очистке пока ещё выполняются вручную стальными щётками. В случаях незначительной коррозии и малой запылённости можно использовать приём закрепления и преобразования ржавчины на поверхности.
Производство работ по нанесению лакокрасочных покрытий предполагает использование следующих механизированных способов: пневматическое распыление; безвоздушное распыление с подогревом или без подогрева краски; нанесение покрытия в электростатическом поле высокого напряжения; нанесение покрытия окунанием и струйным обливом с выдержкой в парах растворителя; с помощью напорных окрасочных валиков. Применяется часто и ручная окраска кистями. Способ нанесения защитных покрытий выбирается с учётом производственных факторов таких, как условия выполнения работ, их объём, тип обрабатываемых поверхностей и их конфигурация, вид и свойство применяемого материала и др. Наиболее эффективен способ безвоздушного распыления, отличающийся небольшим туманообразованием, малыми потерями краски и использованием материалов повышенной вязкости. Весьма эффективна окраска в электрическом поле, позволяющая экономично использовать лакокрасочные материалы (применение такого способа требует наличия стационарной установки на заводе).
Способ защиты без удаления продуктов коррозии. В последние годы получил распространение способ защиты металлов без проведения мероприятий по удалению продуктов коррозии. Этот способ основан на растворении продуктов коррозии. Предложено несколько составов грунтовкипреобразователя ржавчины для защиты стальных конструкций от коррозии.
Так, например, давно известная мастика Назаровой, которая состоит из 160 весовых частей (в. ч.) ортофосфорной (фосфорной) кислоты, 20 в. ч. жёлтой кровяной соли, 56 в. ч. эпоксидной смолы и 24 в. ч. толуола. При этом ржавчина, вступая в реакцию с кислотой и кровяной солью, превращается в нерастворимые фосфаты и берлинскую лазурь, которая связывается эпоксидной смолой. Толуол является разжижителем и в дальнейшем испаряется.
Защита от почвенной коррозии. Методы защиты конструкций от почвенной коррозии подразделяются на ряд методов, связанных с использованием специальных материалов для защиты от воздействия внутренних факторов, а также на три группы методов, обеспечивающих защиту от воздействия внешних факторов. Использование специальных коррозионно-стойких мате-
55
риалов (например, полимербетонов) для конструкций подземных сооружений ещё не получило достаточного развития. Для защиты металлических конструкций от почвенной коррозии чаще всего применяются покрытия на основе битумов и электрохимическая защита.
Защитные битумные покрытия. Защитные битумные покрытия бывают трёх типов: нормальные, усиленные и весьма усиленные. Защита подземных конструкций покрытиями на основе битумов, как показал опыт эксплуатации, недостаточна. Действительно, первое время такие покрытия обладают воздухо- и водонепроницаемостью и надёжно изолируют конструкции от внешне агрессивной среды. Однако в дальнейшем под влиянием грунтовой воды, кислорода воздуха, температурных деформаций конструкции и иных факторов как на сооружение в целом, так и на защитное покрытие нарушается его герметичность, открывается доступ электролита к конструкции и начинается электрохимическая коррозия. Из этого следует вывод, что защита от почвенной коррозии должна предусматриваться с более полным учётом воздействия всех факторов почвенной среды и работы самого защитного покрытия. Там же, где это не учитывалось в процессе строительства, должны быть приняты меры в ходе эксплуатации с целью повышения надёжности сооружений и увеличения сроков их службы.
5.5.2. Электрохимическая защита
Развитие коррозии предотвращается электрохимической защитой, которая строится на основе теории многоэлектродных систем. Сущность такой защиты состоит в том, что защищаемая конструкция подвергается или катодной поляризации от специально установленных анодов из более активного металла, или поляризации наложенной, постоянным током от внешнего источника. Для прекращения почвенной коррозии надо, чтобы разность между катодным и анодным участками конструкции равнялась нулю, или чтобы электросопротивление протеканию тока коррозионного элемента (за счёт изоляции) было очень большим. Чтобы сделать разность потенциалов равной нулю, необходимо довести катодную поляризацию сооружения до общего потенциала, равного начальному потенциалу анодного участка.
В подобных условиях на всей поверхности защищаемой конструкции протекают лишь катодные процессы, и она перестаёт коррозировать. Потенциал, при котором прекращается коррозия, называют защитным потенциалом, а плотность тока, обеспечивающую сдвиг потенциала до защитного,- защитной плотностью тока. Всё это достигается одним из двух способов: протекторной или катодной (активной) защитой. Сравнение затрат на устройство и эксплуатацию протекторной и катодной защит в расчёте на десять лет показывает, что они примерно одинаковы.
Электрохимическая защита металлоконструкций от почвенной коррозии производится с учётом характеристики грунтов, срока службы сооруже-
56

ния и других факторов, в том числе наличия в зоне защищаемого сооружения блуждающих токов.
Протекторная защита. Протекторная защита (рис. 5.6) подземных конструкций от коррозии осуществляется электродами протекторами, обладающими большими отрицательными потенциалами и выполняющими в паре с защищаемым сооружением роль анода.
Рис. 5.6. Принципиальная схема (а) и примеры (б и в) протекторной защиты заглубленных сооружений:
1-конструкция (анод); 2-протектор (дополнительный анод); К1-катодная зона; A1-анодная зона конструкции; 3-проводник; 4-металлоизоляция; 5-анод; 6-наполнитель
Протекторы изготавливаются обычно из магниевого сплава и создают разность потенциалов до 1 В; они могут быть из цинка и реже из алюминия. Протекторы выполняются цилиндрическими или пластинчатыми. С сооружением они соединяются изолированным проводом через стальной сердечник, вставленный в протектор.
Методика расчёта протекторной защиты стальных трубопроводов и гидроизоляции объёмных сооружений различна, но во всех случаях основным её содержанием является определение защитного потенциала, защитной плотности тока, напряжения источника тока и мощности установки катодной защиты. Мощность последней возрастает при росте рН грунта, но снижается при уменьшении удельного сопротивления грунта и повышении сопротивления защитного покрытия конструкции.
Число протекторов п, необходимое для защиты данной конструкции, зависит от размеров защищаемой поверхности S , минимальной защитной плотности тока j (jCT=0,016 А/м), коэффициента к, характеризующего защищённость конструкции, величины тока протектора в данной среде in и определяется по формуле
n = k*j*S/iu .
57

Число протекторов может быть определено и по заранее составленным графикам в зависимости от удельного сопротивления грунта р и от рН грунта (рис. 5.7). С увеличением р, а также и рН грунта количество потребных протекторов увеличивается. Протекторную защиту целесообразно осуществлять при удельном сопротивлении грунтов не более 60 Ом·м и в грунтах с кислой реакцией. Продолжительность работы протектора в годах вычисляется по формуле
T = 0,114-(M-g-D/in) ,
где М - масса протектора, кг; g - электрохимический эквивалент материала протектора, А·ч/кг; in - защитный ток (A) в цепи «протектор - сооружение»; D - КПД протектора.
Полученное по расчёту или по графикам (рис. 5.7) число стандартных протекторов набирается из типовых элементов. Для лучшего контакта протектора с грунтом и устойчивой работы они размещаются в наполнителе, в качестве которого используются гипс, сернокислый натрий или магний. Срок службы протекторов составляет 10...15 лет.
Катодная защита. Катодная защита (рис. 5.8) осуществляется посредством постоянного тока, подаваемого через погруженный в грунт электрод (анодное заземление). При этом отрицательный электрод источника постоянного тока присоединяется к защищаемому сооружению-катоду, а положительный к аноду. Сооружение поляризуется отрицательно.
Рис. 5.7. Зависимость числа протекторов от удельного сопротивления грунта (а) и от кислотной характеристики (б)
58
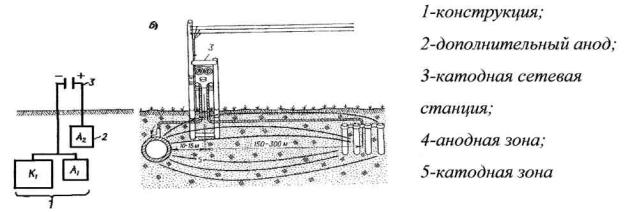
а)
Рис. 5.8. Принципиальная схема (а) и пример (б) катодной защиты подземной конструкции
Потенциал его становится отрицательнее потенциала коррозионных анодных пар, и ток коррозии прекращается. При такой защите разрушается от коррозии дополнительный электрод, с которого ток стекает в грунт. В качестве электрода (анода) используются рельсы, трубы и т.п.
В сущности, при электрохимической защите подземных конструкций от почвенной коррозии она не прекращается, а лишь переносится на дополнительный элемент анод, который разрушается и с течением времени может быть заменён новым. Защищаемое сооружение при этом является катодом и не разрушается.
Электрохимическая защита металлических конструкций (сооружений) от почвенной коррозии решается с учётом характеристики как самого сооружения, так и среды, в которой оно находится. При этом учитываются назначение и срок службы сооружения, расположение его на местности, геологопочвенные и климатические условия, наличие на конструкции пассивных средств защиты от коррозии, а также наличие в зоне расположения сооружения блуждающих токов.
Необходимость катодной защиты от коррозии определяется показателем В, вычисляемым по формуле
В = Т-(δо-δi/vk) ,
где vk - средняя скорость коррозии, мм/год; Т установленный срок службы конструкции (сооружения), годы; δо и δ1 - толщины металлоконструкции в начале и в конце срока эксплуатации сооружения, мм. При этом δ1 определяется, исходя из прочности конструкции (гидроизоляции подземного сооружения) и принимается не менее 2 мм. Если В < 0, то электрохимическая защита не требуется, а при В>0 она обязательна.
59