
Технология машиностроения 2006 Махаринский
.pdf
161
Рис. 3.93. Накатывание резьбы плоскими плашками
При применении цилиндрических вращающихся роликов резьбу можно накатывать тремя видами подач: тангенциальной, радиальной, осевой.
Накатывание можно выполнять одним (рис. 3.93, в), двумя (рис. 3.93, б) и тремя роликами. На рис. 3.93, б оба ролика 1 и 3 вращаются непрерывно; при вращении ролик 1 получает радиальную подачу (от механического привода или гидропривода); при достижении требуемой глубины резьбы наступает выдерж- ка с неизменным межцентровым расстоянием, затем ролики отходят друг от друга. В процессе накатывания цилиндрическую заготовку 2 поддерживает нож 4, установленный между роликами. Профиль нарезки на периферии роликов является зеркальным отображением резьбы изделия.
Непрерывное накатывание резьбы роликами может производиться с тан- генциальной подачей (рис. 3.93, в) двумя роликами 1 и 3 разных диаметров (D1>D2) с одинаковой частотой вращения, причем расстояние между центрами роликов остается постоянным. При этом способе нет надобности в ноже, под- держивающем заготовку 2.
На рис. 3.93, г показана схема накатывания резьбы с тангенциальной пода- чей двумя затылованными роликами 1 н 3. У каждого такого ролика имеется: загрузочно-разгрузочная часть 4 (срез), образованная путем срезания резьбы по радиусу ниже внутреннего диаметра резьбы, затылованная заборная часть, ка- либрующая часть, затылованная освобождающая часть. Ролики 1 и 3 устанав- ливают на станке с постоянным расстоянием между их центрами, рассчитан- ным на получение резьбы заданного диаметра. Вращение роликов синхронно. Заготовка 2 подается автоматически в момент, когда срезы 4 роликов будут на-
162
ходиться друг против друга. Накатывание резьбы происходит за один оборот роликов.
Такие ролики иногда бывают многоцикличными: на одном ролике делают несколько загрузочно-разгрузочных участков (срезов) 4 и соответствующее ко- личество остальных указанных выше участков (второй ролик в этом случае бе- рут цилиндрический, обычного профиля). В рабочее положение заготовку уста- навливают специальным сепаратором последовательно, по мере подхода срезов 4 ко второму (обычному) ролику. За один оборот ролика может быть накатано от 1 до 7 заготовок. Шероховатость поверхности резьбы при накатывании заты- лованными роликами несколько повышается.
Накатыванием можно получить резьбу диаметром от 0,3 до 150 мм на де- талях из сталей твердостью НВ 120...340, а также из цветных металлов и спла- вов с точностью по 5-му квалитету и с шероховатостью поверхности Rа=0,2...0,1 мкм. Скорость накатывания резьбы на деталях из сталей с пределом прочности 400,..800 МПа составляет 40... 80 м/мин.
3.4. Методы предварительной и чистовой обработки плоских поверхностей
Плоские поверхности как правило обрабатывают строганием, долблением, фрезерованием, шлифованием и протягиванием.
Строгание и долбление наиболее применимы в серийном, особенно в мел- косерийном и единичном производствах, так как для работы на строгальных и долбежных станках не требуется сложных приспособлений и инструментов. Однако эти виды обработки малопроизводительны. Низкая производительность объясняется тем, что обработку ведут одним или небольшим числом резцов с потерями времени на обратные холостые ходы.
Обработку строганием производят резцами, сходными по форме с токарны- ми, на строгальном станке. Однако в отличие от токарной обработки строгание выполняют прерывисто со снятием стружки при поступательно-прямолинейном движении заготовки или резца.
Скорости резания при этих видах обработки небольшие, так как возвратно-
поступательное движение с большими скоростями вызывает большие силы инерции при движении узлов станка. Так, например, при строгании заготовок из чугуна для черновой обработки рекомендуется скорость резания 15...20 м/мин, для чистовой – 4... 12 м/мин с глубиной резания соответственно 0,5...0,8
и0,08 мм. Шероховатость поверхности при тонком строгании Rа=0,8 мкм.
Взависимости от служебного назначения и обрабатываемого материала строгальные резцы подразделяются по следующим признакам: 1) материалу режущей части; 2) форме; 3) типу. Режущая часть строгальных резцов изготав- ливается из быстрорежущей стали или твердых сплавов.
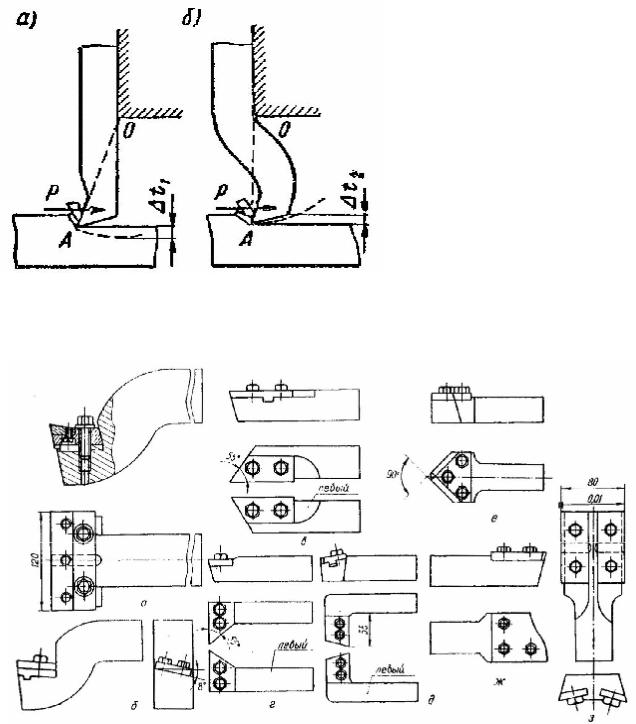
163 |
|
|
По форме стержня разли- |
|
чают прямые (рис. 3.94-а) и |
|
изогнутые (рис. 3.94-б). В пер- |
|
вом случае в результате упру- |
|
гой деформации стержня рез- |
|
ца под действием силы реза- |
|
ния Р его вершина А смещает- |
|
ся так, что глубина резания |
|
увеличивается с увеличением |
|
силы резания. Это приводит к |
|
потере устойчивости процесса |
|
резания (к автоколебаниям). |
Рис. 3.94. Схема строгания прямым (а) и на- |
При работе изогнутого резца |
указанная упругая деформа- |
|
клонным (б) резцами |
ция вызовет не увеличение, а |
уменьшение глубины резания, что приводит к устойчивому резанию.
Рис. 3.95. Строгальные чистовые резцы с механическим креплением режущих пластин из быстрорежущей стали:
а, б– для обработки плоскостей; в– для обрезки; г– для обработки направляющих типа «ласточкин хвост»; д– подрезной; в– для обработки V-образных направляющих: ж– про- фильный; з– для обработки пазов
Однако прямые строгальные резцы имеют некоторые преимущества по сравне- нию с изогнутыми:
1) прямой резец можно установить с меньшим вылетом, чем изогнутый, что повышает его жесткость;
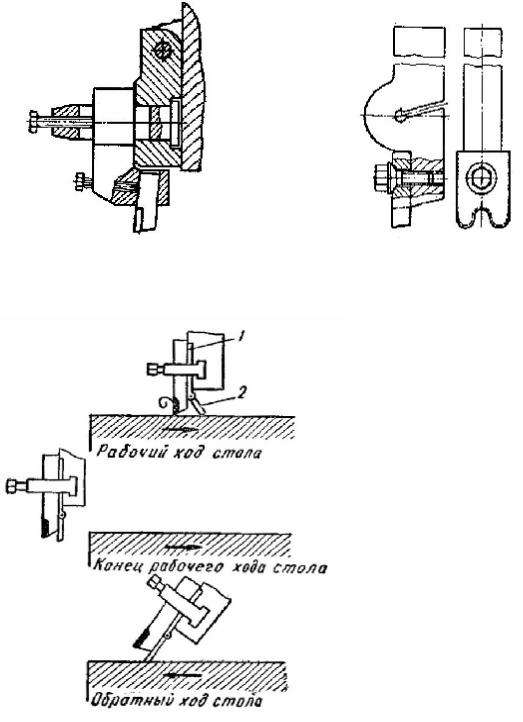
164
2) прямые резцы можно изготавливать двухсторонними, сокращая расход металла на державки;
3) прямые резцы проще в изготовлении.
На рис. 3.95 показаны различные типы строгальных резцов.
Рис. 3.96. Державка для |
Рис. 3.97. Пружинящая |
|
державка для фасонных |
||
проходных резцов |
||
резцов |
||
|
Для крепления резцов достаточное распространение нашли различные державки. Державка для крепления про-
ходных и подрезных резцов показана на рис. 3.96, а для фасонных резцов – на рис. 3.97.
При строгании горизон-
тальных поверхностей и пазов резец при обратном ходе набе- гает задней гранью на обраба- тываемую поверхность и, по- ворачивая откидную доску, несколько приподнимается.
Благодаря этому режущая кромка резца при обратном ходе не прижимается со зна- чительной силой к обработан- ной поверхности и изнашива- ется. На рисунке 3.98 показано
простейшее приспособление для подъема резца при обрат- ном ходе. Пластина 1 устанавливается в резцедержателе под резцом. Конец
165
створки 2 расположен ниже вершины резца и она при рабочем ходе свободно откидывается назад. В конце рабочего хода створка принимает вертикальное положение, а при обратном ходе упирается в деталь и поднимает резец, не да- вая ему соприкасаться с обработанной поверхностью.
Обрабатываемые строганием заготовки закрепляются:
1)на столе станка с помощью универсальных крепежных элементов;
2)в машинных тисках;
3)на угольниках и призмах;
4)на магнитных плитах;
5)на поворотных столах.
Универсальные строгальные станки подразделяют на продольно- и попе- речно-строгальные.
Продольно-строгальные станки подразделяют на одностоечные, двухстоеч- ные и портальные. Имеются специализированные строгальные станки — кромко- строгальные, копировально-строгальные и др.
Длина столов продольно-строгальных станков зависит от их назначения и достигает 12... 15 м. Стол может двигаться с помощью реечных передач или гид- равлических устройств. В последнем случае можно достигнуть более высокой скорости хода стола и более плавного реверсирования.
У поперечно- и продольно-строгальных станков резцедержатель вместе с резцом может поворачиваться в вертикальной плоскости при обратном ходе. Для установки резца по высоте суппорт с резцедержателем можно перемещать в вер- тикальном направлении. Для обработки наклонных поверхностей суппорт мо- жет быть повернут на требуемый угол.
На строгальных станках чаще всего обрабатывают плоскости. На круп- ных продольно-строгальных станках, снабженных несколькими суппортами, можно одновременно строгать несколько плоскостей на разных сторонах заго- товки.
На долбежных станках резец при долблении совершает только возвратно- поступательное движение в вертикальном направлении, а движение подачи осуществляется заготовкой.
Схемы обработки, реализуемые на строгальных и долбежных станках, пока- заны на рис. 3.99.
Долбежные станки чаще всего применяют для долбления шпоночных пазов, канавок, профильных отверстий. Наиболее характерные схемы строгания и долбления приведены на рис. 3.99.
При строгании и долблении резцы устанавливают на размер обычно по разметке или по шаблонам и реже с помощью «пробных стружек». Обрабаты- ваемые заготовки устанавливают непосредственно на столе станка, выверяют с помощью клиньев и подкладок и закрепляют прихватами и другими нормали- зованными зажимами.
Вспомогательное время при работе на строгальных и долбежных станках относительно велико, что еще больше снижает производительность. В некото-
рых случаях при одновременной обработке нескольких заготовок применяют простейшие установочно-зажимные приспособления. Наиболее выгодно на
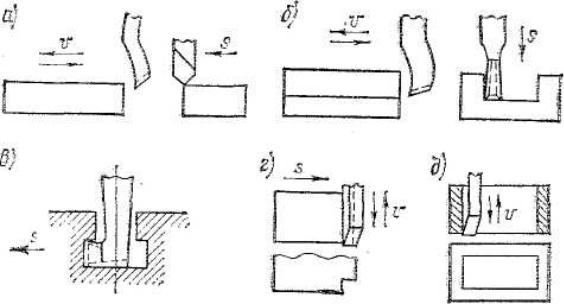
166
продольно-строгальных станках обрабатывать длинные и узкие плоскости, на- пример, кромки стальных листов и плит, направляющие станин металлообраба- тывающих станков и т. п.
Рис. 3.99. Схемы строгания и долбления: а — строгание плоскости; б – стро- гание паза; в — строгание Т-образного паза; г — долбление углового профиля; д — долбление прямоугольного отверстия (v — главное движение резания; s – движение подачи)
Точность работы на продольно-строгальных станках обусловливается главным образом квалификацией и опытом рабочего, а также качеством и со- стоянием станка. На ряде станкостроительных заводов при чистовом строгании станин станков достигнута такая точность, что отпадает необходимость в шаб- рении, так как отклонения от прямолинейности не превышают 0,02 мм на 1 м длины и 0,05 мм на всю длину станины. В обычных условиях погрешность об- работки на строгальных станках не выходит за пределы 0,1...0,2 мм на 1 м дли- ны.
При чистовой обработке вследствие тихоходности строгальных станков следует применять широкие резцы с шириной режущей кромки 15...40 мм и большие подачи (10...25 мм/дв. ход) в зависимости от требуемых точности и шероховатости обрабатываемой поверхности.
Долблением обрабатывают поверхности внутренних контуров, когда не- возможно или затруднительно выполнять эту операцию на другом станке.
Процессы строгания и долбления аналогичны, однако в первом случае (при работе на продольно-строгальных станках) движение резания придается заго- товке, а движение подачи – резцу; во втором – движение резания придается резцу, а движение подачи – заготовке, причем движение подачи осуществляет- ся в плоскости, перпендикулярной направлению движения резца.
Обработка плоских поверхностей фрезерованием. В массовом производст-
ве фрезерование совершенно вытеснило применявшееся ранее строгание и час- тично долбление. При обработке фрезерованием можно обеспечить значитель-
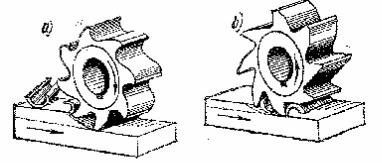
167
но большую производительность —• благодаря применению многолезвийного
инструмента можно обрабатывать в единицу времени значительно большую поверхность.
Производительность фрезерования выше еще и потому, что можно одно- временно обрабатывать несколько заготовок несколькими одновременно рабо- тающими инструментами. Кроме того, сокращается продолжительность рабо- чих и холостых ходов заготовки и инструмента.
На фрезерных станках плоские поверхности можно обрабатывать цилинд- рическими фрезами при движении стола станка с закрепленной заготовкой на- встречу направлению движения зубьев, т, е. методом встречного фрезерования (рис. 3.100, а) или в том же направлении методом попутного фрезерования (рис. 3.100, б). В обоих случаях стружка, снимаемая каждым зубом фрезы, имеет форму запятой, но в первом случае толщина стружки постепенно увеличивается в про- цессе резания, а во втором – уменьшается.
Преимущество встречного фрезерования заключается в плавном увеличении нагрузки на зуб и во врезании зубьев в металл под коркой. Недостатком этого ме- тода является стремление фрезы оторвать заготовку от поверхности стола.
Точность фрезерования зависит от типа станка, инструмента, режимов ре- зания и других факторов. При фрезеровании может быть достигнута точность по
|
8... 11-му квалитетам, а при |
|
|
скоростном и тонком фрезе- |
|
|
ровании — до 7-го квалитета. |
|
|
Шероховатость |
поверхности |
|
при чистовом фрезерова- |
|
|
нии Ra=6,3...1,6 мкм. |
|
|
Методы |
формообразо- |
|
вания на фрезерных станках. |
|
Рис. 3.100. Схемы встречного и попутного |
На фрезерных станках обра- |
|
фрезерования |
батывают: 1) плоскости (го- |
|
|
ризонтальные, |
вертикальные |
и наклонные); 2) уступы; 3) пазы прямоугольные (открытые, полуоткрытые и закрытые); 4) Т-образные пазы (открытые и полуоткрытые); 5) направляющие типа «ласточкин хвост» (охватывающие и охватываемые); 6) многогранники. Также на фрезерных станках обрабатывают угловые канавки (на периферии и торце цилиндра или конуса); прямоугольные выступы кулачковых муфт; зубья зубчатых колес и реек; окна; фасонные поверхности. Главным движением реза- ния на фрезерном станке является вращение инструмента (фрезы). Движение подачи (продольной, поперечной и вертикальной) осуществляет заготовка. При помощи круглого поворотного стола заготовке можно сообщать круговую по- дачу.
Обработку открытых относительно широких плоскостей без уступов с не- большими уступами обычно осуществляют торцовыми фрезами, диаметр D ко- торых выбирают в зависимости от ширины фрезерования В. D= (1,25…1,5)В.
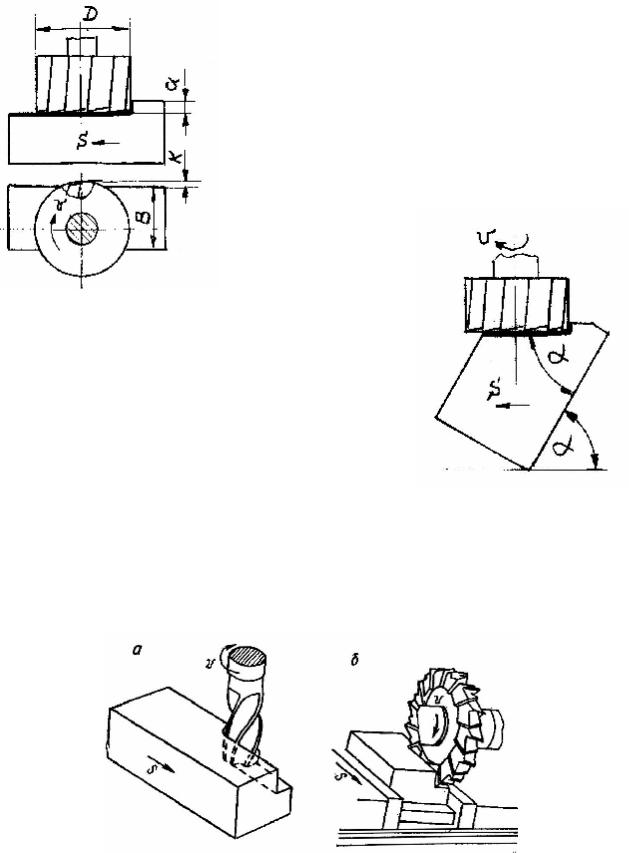
168
При фрезеровании плоскости без уступа в заготовке из конструкционной стали необходимо сдвинуть ось фрезы так, как это показано на рис. 3.101. Сдвиг К= (0,03…0,05)D. При этом ре-
зание каждый зуб фрезы начинает при меньшей толщине среза. При обработке жаропрочной ста-
ли сдвиг нужно сделать в противоположную сторону. Такая настройка станка обеспечивает повышение стойкости фрезы.
Схема, показанная на рис. 3.102, реализуется на вертикально- фрезерном станке.
Такую плоскость можно обработать и на горизонтально- фрезерном станке,
но тогда она должна располагаться вер- тикально. Плос-
кость, наклонную к другим под углом α, можно фрезеровать, если расположить заготовку так, что- бы эта плоскость была параллельна подаче.
Схемы фрезерования уступов показаны на рис. 3.103. Уступ можно обрабатывать либо конце- вой (рис. 3.103.б, на вертикально-фрезерном стан- ке), либо дисковой фрезой (рис. 3.103.б, на гори- зонтально-фрезерном станке). Ширина дисковой и
диаметр концевой должны быть больше ширины уступа. Набором дисковых фрез (рис. 3.104) можно одновременно фрезеровать 2 уступа.
Рис. 3.103. Схемы фрезерования уступов
концевой и дисковой фрезами

169
Обработка прямоугольных и шпоночных пазов производится дис- ковыми, концевыми и шпоночными фрезами, а пазов для сегментных шпонок – специальными фрезами. От-
крытые прямоугольные пазы чаще всего фрезеруют трехсторонними дисковыми фрезами, а полуоткрытые и закрытые – концевыми.
Т-образные пазы обрабатывают за несколько операций. Сначала фрезе-
руется прямоугольный паз шириной а и глубиной h концевой или дисковой трехсторонней фрезой, затем специальной фрезой для Т-образных пазов, разме-
ры которой соответствуют размерам паза, фрезеруют внутреннюю часть паза с размерами b и с. Фаски в размер е обрабатывают концевыми или дисковыми угловыми фрезами. Один из вариантов последовательности обработки Т- об- разного паза показан на рис. 3.105.
Рис. 3.105. Последовательность фрезерования Т- образного паза
Обработка направляющих типа «ласточкин хвост» также осуществляется за несколько операций. Последовательность обработки охватывающих направ- ляющих на вертикально-фрезерном станке показана на рис. 3.106. Прямоуголь- ный паз можно обрабатывать дисковой трехсторонней фрезой, а углы не только концевой, но и дисковой одноугловой фрезой (рис. 3.107). Вариант последова- тельности обработки охватываемых направляющих типа «ласточкин хвост» по- казан на рис. 3.108.
Рис. 3.106. Фрезерование паза типа «ласточкин хвост»
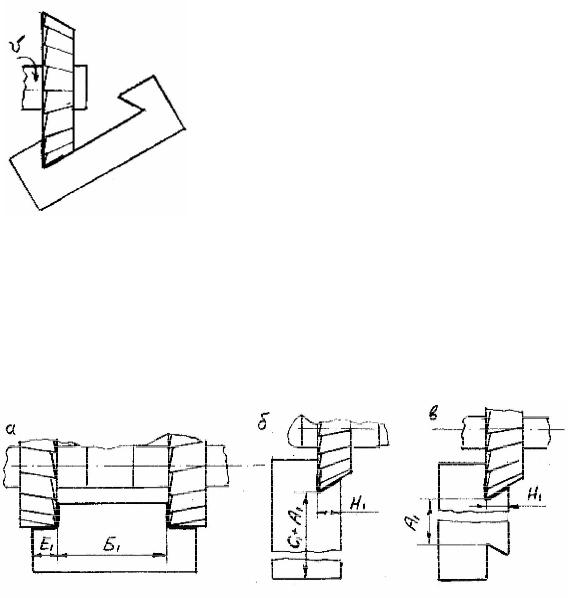
170
Фасонная поверхность на фрезерном станке может быть обработана: 1) фасонной фрезой или набором фрез (рис. 3.109); 2) комбинированием двух подач (по разметке, или с помощью систе- мы с ЧПУ); 3) с помощью копиров.
Копиры представляют собой основную деталь копировального устройства, очертания которой определяют траекторию движения режущего ин- струмента и соответствуют профилю обрабаты- ваемой поверхности.
Системы управления процессом копирова- ния подразделяют на системы прямого и непря- мого действия. При прямом действии контакт ко- пировального ролика (пальца) и копира обес- печивается силой тяжести груза, силой гидрав-
лического давления или силой сжатия пружины. В системах непрямого дейст- вия копировальный ролик находится в соприкосновении с копиром под действи- ем незначительной силы, измеряемой долями ньютона. Копировальный ролик
является промежуточным подвижным
Рис. 3.108. Вариант последовательности обработки охватываемых направ- ляющих типа «ласточкин хвост»
элементом, незначительные перемещения которого, составляющие сотые или де- сятые доли миллиметра, в виде команд передаются в специальные усилительные устройства, выходные элементы которых воздействуют на исполнительные меха- низмы и перемещают режущий инструмент и (или) обрабатываемую заготовку.
На рис. 3.110, а приведена схема копировальной обработки по системе пря- мого действия с механическим управлением. Стол 9 перемещается ходовым вин- том 8 от редуктора 7. На столе 9 установлены копир 1 и заготовка 10. При движении стола палец 2 с бабкой 3 под действием копира 1 сжимает пружи- ну 4 и перемещается в вертикальном направлении по стойке 5. Фреза 6, имею- щая форму и размеры пальца 2, обрабатывает заготовку, придавая ей форму ко- пира.