
ПиПИИЭ кр. испр
.pdfследовательно, уменьшения продолжительности процесса диффузии, окисленияиотжига.Поэтомупоявилисьиполучаютразвитиеметодыбыстрой термической обработки (Rapid Thermal Processing) [3], в том числе методы лазерной стимулированной диффузии и ускоренной диффузии в тлеющем разряде. Быстрые термические процессы, или импульсная термическая обработка, базируются главным образом на использование интенсивного когерентного (лазерного) или некогерентного (светового) излучения. В качестве источников последнего используют галогенные лампы накаливания, ксеноновые дуговые лампы, графитовые нагреватели.
В зависимости от условий импульсного нагрева и, в первую очередь, от экспозиционной мощности излучения, процесс можно проводить как в твердой фазе (фотонный отжиг), так и с плавлением - рекристаллизацией (лазерный отжиг и диффузия). Для современной технологии наибольший интерес представляет твердофазный режим благодаря соответственно другим технологическимоперациям.Вэтомслучаеиспользуютпримесныепокрытия, жидкие и газообразные источники.
Если пластину, находящуюся в атмосфере легирующего элемента,
например, PCl3, BCl3, B(CH3)3, B(C2H5)3, B2H6, подвергать воздействию импульсов лазерного излучения, приповерхностные области расплавляются, при этом удаляется получать очень мелкие бездефектные слои с высокой концентрацией примеси. Благодаря сильному различию коэффициентов диффузии примеси в жидкой и твердой фазе, толщина легированного слоя определяется толщиной расплавленного слоя, а концентрация примеси зависит от ее растворимости в жидкой фазе.
11
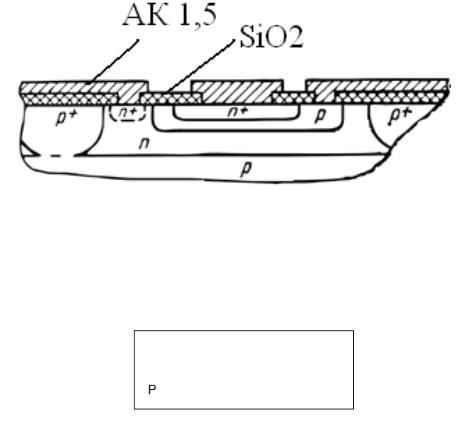
2.Маршрутный процесс формирования эпитаксиальнопланарной структуры.
1.Формирование партии пластин (рабочих и контрольных) 76 КДБ-0,3
2.Химобработка. Предназначена для удаления с поверхности механических и органических загрязнений. Используется перекисно-
аммиачный раствор (H2O2+NH4OH+HF) при Т=75°С, t=12 мин, затем каскаднаяпромывкадо ρH2O>5МОм∙смспоследующейсушкойнацентрифуге V=1000 об/мин, t=12 мин. на линии "Лада-1".
3.Контроль качества химобработки осуществляется на 3-х пластинах из партии по диаметру, проходящему перпендикулярно базовому срезу под микроскопом ММУ-3 в темновом поле при ув.≥250*. Допускается не более 5 дефектов.
4.Наращивание эпитаксиального слоя осуществляется в установке эпитаксиального наращивания "Лада-1" силановым методом
SiH4+H4 → Si + 3H2↑
предварительно для очистки поверхности Si используется газовое
травление в НСl.
Si+2HCl → Si + H2+ Cl2
В процессе эпитаксиального наращивания слой легируется путем введения ПГС легирующей примеси: смесь фосфина с водородом (PH3+ H2).
T=1100°C, t=I5 мин, hэ.с.=1,8 - 2,2 мкм , R=0,4-0,5 Oм/□.
12

5. Измерение толщины эпитаксиального слоя осуществляется на установке "Шар-Шлиф" с последующим травлением в хромовом травителе в течение 10 с.
Хромовый травитель: HNО3+HF+ H2O+Cr(NО3)2.
6. Определение плотности дефектов упаковки в эпитаксиальном слое осуществляется обработкой в хромовом травителе.
Плотность дефектов упаковки σx≤1×102см-2. Плотность дислокаций σy≤5×102см-2.
7. Определение коэффициента заполнения эпитаксиальных
структур линиями скольжения проводится путем травления в смеси HF+H2О. При этом выявляются дефектные области, возникающие по краям пластины в процессе эпитаксии. Коэффициент заполнения структур линиями скольжения К ≤ 0,5.
8. Контроль пластин после эпитаксии осуществляется по следующей схеме: 1. 100% визуально, не должно быть:
а) пятен, цветопобежалости, трещин; б) сколов на расстоянии 3 мм от края;
в) завалов, загибов на расстоянии более 3 мм от края; 2. Количество светящихся точек по диаметру, перпендикулярному базовому
срезу, не должно быть более 30 штук.
13
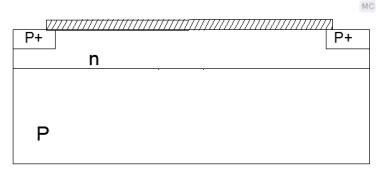
9.Фотолитография под скрытый р+ слой (см. п. 5). Контроль качества ф/л. в светлом поле микроскопа МИИ-4 при ув.250* не более 18% дефектных модулей по двум взаимно перпендикулярным диаметрам.
10.Ионное легирование бором осуществляется на ионно-лучевой установке "Везувий-3", в качестве источника примеси используется флобор.
D20 мкKл/см2, Е=100 КэВ.
11.Плазмохимическое снятие фоторезиста. Осуществляется на полуавтомате плазмохимической обработки пластин "Плазма-600". (Плазма600А) в течение 15-25 мин в плазме O2, Р(O2))=0,5 кгс/см2.
12.Доснятие фоторезиста на установке "Лада-1" в смеси H2SO4+H2O2 (3:1) при Т=60°С, t=2 мин в каждой из двух ванн.
13.Химическая обработка(см. п. 10).
14.Контролькачествахимическойобработки(см.п.10).Допускаетсяне более 10 дефектов по диаметру, проходящему перпендикулярно базовому срезу. Контролируют три пластины или из 6-ти рабочих, одну в темном поле, микроскопа МИИ-4 при ув.250*.
15.Высокотемпературная обработка для скрытого р+- слоя. Загрузка не менее 100 пластин.
N |
Изменение |
|
Расход |
|
|
п/п |
температуры |
Время, мин. |
газа, |
Оборудование |
|
|
°С |
|
литр/час |
|
|
|
|
|
|
||
|
|
|
|
|
|
1 |
700-900 |
10-20 |
О2(100) |
диффузионная |
|
2 |
900-1150 |
20-35 |
N2(250) |
печь СДОМ |
|
СДО-125/3 |
|||||
|
|
|
|
||
3 |
1150 |
60 |
N2(250) |
|
|
4 |
1150-700 |
30-55 |
N2(250) |
|
|
|
|
|
|
|
16. Определение толщины легированного р+ - слоя. Предназначено для контролятолщиныдиффузионныхиэпитаксиальныхслоев.Длявыявленияр+-
14
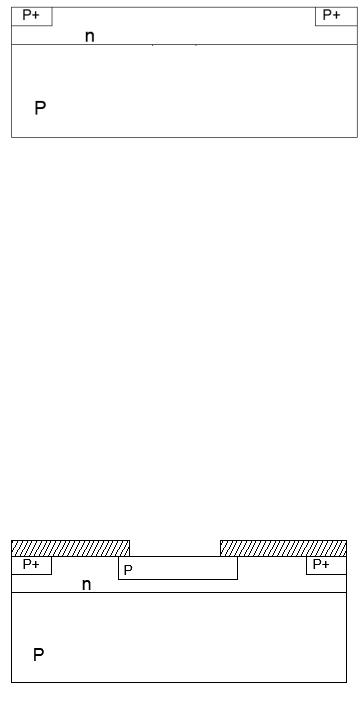
слоя используется хромовый травитель после изготовления сферического шлифа на установке "Шар-Шлиф".
h=1,5 - 2,2 мкм.
17.Снятие SiО2 (см. п. 16) на установке химобработки в HF+H2O+NH4F.
18.Химобработка пластин (см. п. 2).
19.Контроль качества химической обработки (см. п. 10).
20.Снятие SiО2. Осуществляется в травителе HF+H2O+ HN4F в течение трех мин на установке хим. обработки пластин.
21.Химическая обработка (см. п. 2)).
22.Контроль качества химической обработки (см. п. 10).
23.Провести химическую очистку пластин в ПАР; 24.Вырастить термический окисел при температуре 1000оС толщиной 1
мкм;
25.Провести фотолитографию «База» (оставляются открытыми места куда будет легирована примесь бора для создания области «Базы»;
26.Провести селективное травление окисла до кремния по маске фоторезиста;
27.Удалить фоторезист; 28.Провести ионное легирование бора в область БАЗЫ с последующей
разгонкой.
29.Провести высокотемпературный отжиг для активации примеси;
30.Удалить окисел;
31.Провести контроль параметров слоя БАЗА H и ϼsпо спутникам которые находились с пластинами в одном технологическом процессе
32.Провести химическую обработку в ПАР;
33.Провестивыращиваниеокислакремнияввысокотемпературнойпечи при температуре 1000оС толщиной 1 мкм;
15

34.Провести фотолитография «Эмиттер». Оставляются вскрытыми области в которых планируется диффузия примеси Фосфора (P)для создания Эмиттера.
35.Провести селективное травление окисла до кремния по маске фоторезиста;
36.Провести удаление фоторезиста; 37.Провести диффузия Фосфора в отрытые окна с последующей
разгонкой. (или ИЛ фосфора с последующей активацией примеси при температуре 800оС);
38.Провести контроль H и ϼsсозданного слоя, по спутникам; 39.Провести контроль ВАХ β(измеряется пробивное напряжение Uкб и
βна рабочих структурах); 40.Если параметры не достигнуты проводится дополнительный отжиг
(догонка) для достижения требуемых параметров:
41.Пластины которые не соответствуют карте ВАХ бракуются.
42.Фотолитография для создания рельефа требуемой конфигурации. Обработка пластин в парах ГМДС (гексаметилдисилозан). Затем нанесение фоторезиста h=1,1 мкм на установке "Лада-Электроника".
Сушка Т1=80оС, Т2=90оС, Тз=105°С, t=10 мин.
Экспонирование на установке совмещения и экспонирования ЭМ-576. Проявление в 0,9%-ном растворе КОН в течение 40 с.
Задубливание ф/р от Т=85°С до 105°С в течение 8 мин.
43.Травление диоксида кремния в течение 10 мин в установке с химической обработки пластин "Лада-1" в травителе: H2O+HF+HN4F.
44.Снятие фоторезиста в смеси H2SO+H2O2 в соотношении 3:1 в двух
ваннах по 2 мин при Т=60°С для одного объема. В одном объеме обрабатывают 300пластин. Затемкаскаднаяпромывка вдеионизованной H2O до ρ >3 МOм*см.
Сушка в центрифуге при V=I000 об/мин, t=5 мин. Линия "Лада-1".
16
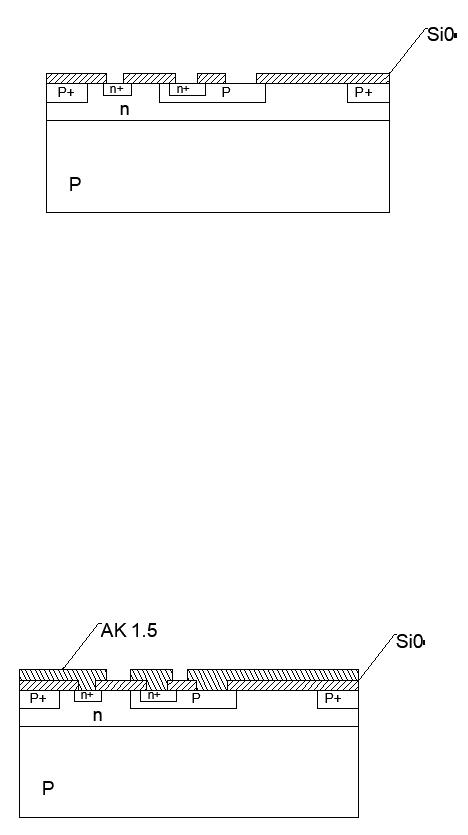
45.Контроль пластин после фотолитографии осуществляется под микроскопом МИИ-4 в светлом поле микроскопа при ув.250*. Не допускается более 18 дефектов. Из них не должно быть пятен, подтеков, остатков проявителя.
Кроме того, контролируется качество травления SiO2 во вскрытых окнах. Не должно быть проколов и растравов SiO2. Линейные размеры измеряются на соответствие КД и заносятся в память ЭВМ.
46.Напление металла 2. На установке магнетронного распыления
"Оратория-5" t=350 c, h=1,2 мкм. Сплав Al-Si-Cu (1,5%, 9%).
47.Контроль блока металлизации под микроскопом МИИ-4. Допускается не более 2 дефектных модулей (контролируют одну пластину из
10)100%- визуально.Недолжнобытьпятен,разводов,вспучиванияМе,пятна Ме, капель Me, отслаивания Me. Адгезия оценивается методом царапания с последующим контролем под микроскопом ММУ-3 (ув.12О*). Толщина на МИИ-4.
48.Химобработка пластин - обработка в изопропиловом спирте t=720 c, T- комнатная.119. Фотолитография-8.
49.Травление металла осуществляется на установке химической
обработки пластин "Лада-1" в травителе: Н2О+СН3COOН+НNO3+Н3РO4. Время травления контролируется по полному вытравливанию металла.
17
50.Плазмохимическое травление. Предназначено для вытравливанияSi
вметаллизации в плазме ВЧ-разряда. Среда-элегаз. Установка УВП-2.
51.Доснятие фоторезиста на линии "Лада-1" в диметилформалиде t=I0 мин, затем УЗ-ванне t=5 мин. Промывка в деионизованной воде до ρ> 3 МОм*см, сушка в центрифуге.
52.Контроль пластин после фотолитографии под микроскопом ММУ-3. 100%-ный визуальный контроль на 2-ом, не должно быть >18%дефектных модулей.
53.Высокотемпературная обработка осуществляется (вжигание) в диффузионной печи СДО-125/3, Т=510°С, t=15 мин в N2 (250 л/г).
54.Проверка ВАХ-1 проводится для контроля технологического процесса путем выборочной проверки ВАХ на пластине. Используется измеритель характеристик п/п приборов Л2-56. Данные поступают в ЭВМ.
При I=10 мкА, Uкбпроб >14 В.
55.Химобработка в среде диметилформалида t=7 мин, Т-комнатная.
56. Контроль блока металлизации под микроскопом ММУ-3, Допускается не более 12 дефектных модулей. Контролируют 1 пластину из 10 рабочих.
18
Список использованных источников
[1].Гаврилов Р.А., Скворцов А.М. Технология производства полупроводниковых приборов. - Л.: Энергия, 1968. - 240 с.
[2].Гук Е.Г., Ельцов А.В., Шуман В.Б., Юрре Т.А. Фоторезисты-диффузанты в полупроводниковой технологии. - Л.: Наука, 1984. -118 с.
[3].Готра З.Ю., Осадчук В.В., Кучмий Г.Л. Диффузионное легирование в современной технологии кремниевых ИС // Зарубежная электронная техника. - 1990.-№ 5(348). - с. 5 - 63.
19