
806
.pdf
Солома зерновых культур – очень энергоѐмкая биомасса, она является превосходной альтернативой традиционному топливу.
Количество энергии в 1 литре дизельного топлива, в 1 м3 природного газа и в 2,4 кг соломы –примерно одинаковое.
Один рулон соломы диаметром 1,8 м и весом 330 кг заменяет минимум 140 литров дизельного топлива или 140 м3 природного газа.
В Красноярском крае, например, в 2012 г. произведено около 1 млн 700 тыс. тонн соломы (табл. 1).
Таблица 1
Производство соломы по районам Красноярского края
Наименование района |
Произведено соломы, т |
|
Восточная зона |
Абанский |
13131 |
Дзержинский |
4861 |
Иланский |
5951 |
Ирбейский |
5491 |
Канский |
7948 |
Нижнеингашский |
3410 |
Партизанский |
3531 |
Рыбинский |
3957 |
Саянский |
2438 |
Тасеевский |
1183 |
Уярский |
2918 |
|
Западная зона |
Ачинский |
2402 |
Боготольский |
8660 |
Большеулуйский |
281 |
Назаровский |
1011 |
Новоселовский |
23350 |
Тюхтетский |
8719 |
Ужурский |
14283 |
Шарыповский |
16392 |
|
Центральная зона |
Балахтинский |
2927,3 |
Березовский |
1311,8 |
Большемуртинский |
5666 |
|
|
|
Продолжение таблицы 1 |
Емельяновский |
2914 |
Манский |
283 |
Сухобузимский |
7531 |
|
Южная зона |
Ермаковский |
366 |
Идринский |
751 |
Каратузский |
6870 |
Краснотуранский |
1733 |
Курагинский |
1792 |
Минусинский |
4551 |
Шушенский |
3086 |
|
Северная зона |
Казачинский |
317 |
Пировский |
18 |
Одну часть соломы следует использовать в энергоэффективных газогенераторных установках и котлах, например фирма HERLT (Германия) и Viessmann
10
(Германия) [5], работающих в составе зерноочистительно-сушильных комплексовали местных котельных.
Другую часть соломы можно эффективно использовать, например, при беспривязном содержании животных на глубокой несменяемой подстилке[6].
На территории Красноярского края имеется около 20 крупных животноводческих хозяйств и птицефабрик, которые могут быть источниками биомассы (сырья) для биогазовых станций[7].
Таблица 2
Поголовье сельскохозяйственных животных (2012 г.)[7]
№ |
Наименование района, хозяйства |
|
|
Поголовье, голов |
|
|
|||
п/п |
|
|
КРС |
в т.ч. |
свиньи |
|
лошади |
овцы |
птица |
|
|
|
|
коровы |
|
|
|
|
|
|
|
Емельяновский район |
|
|
|
|
|
||
1 |
ООО Емельяновское |
|
2554 |
1100 |
|
|
17 |
|
|
2 |
ЗАО Частоостровское |
|
1128 |
450 |
|
|
21 |
|
|
3 |
СХП ООО «Мустанг» |
|
52 |
20 |
|
|
309 |
1430 |
|
4 |
ОАО П/З Шуваевский |
|
|
|
28437 |
|
|
|
|
5 |
ООО «Птицефабрика «Заря» |
|
|
|
|
|
|
|
848500 |
|
|
Березовский район |
|
|
|
|
|
||
1 |
ООО с/з Енисей |
|
1280 |
573 |
|
|
|
|
|
2 |
АПК Сибирcкая Губерния |
|
|
|
|
|
|
|
2589000 |
3 |
ОАО п/ф Бархатовская |
|
|
|
|
|
|
|
1129000 |
|
|
Назаровский район |
|
|
|
|
|
||
1 |
СЗАО «Ададымское» |
|
4280 |
1480 |
15084 |
|
51 |
|
|
2 |
ЗАО «Владимировское» |
|
2384 |
985 |
|
|
39 |
|
765900 |
3 |
ЗАО «Гляденское» |
|
4213 |
1481 |
4206 |
|
228 |
|
|
4 |
СЗАО «Краснополянское» |
|
4626 |
1792 |
|
|
97 |
|
|
5 |
ЗАО «Крутоярское» |
|
3569 |
1000 |
|
|
44 |
|
|
6 |
ЗАО «Назаровское» |
|
17932 |
4338 |
77535 |
|
1446 |
|
|
7 |
ЗАО «Подсосенское» |
|
3989 |
1548 |
|
|
41 |
|
|
8 |
ЗАО "Сахаптинское" |
|
2745 |
1110 |
|
|
137 |
|
|
|
|
Ужурский район |
|
|
|
|
|
||
1 |
ЗАО «Солгонское» |
|
6833 |
2415 |
3706 |
|
169 |
|
|
2 |
СПК Оракский |
|
2542 |
900 |
|
|
31 |
104 |
|
3 |
СПК «Андроновский» |
|
6889 |
2149 |
9605 |
|
304 |
|
|
4 |
ЗАО «Искра» |
|
7732 |
2182 |
|
|
205 |
1575 |
|
Для указанных предприятий возможно строительство биогазовых станций электрической мощностью от 1 МВт и более.
Другим значимым биоресурсом Красноярского края являются отходы лесной и лесоперерабатывающей отраслей.
Как следует из результатов научных исследований по техникоэкономической оценке возможности использования возобновляемых источников энергии на территории Красноярского края в разрезе муниципальных образований края [7], в результате лесохозяйственной деятельности в Красноярском крае образуются древесные отходы в объеме 4 419,53 тыс. м3 (табл. 3).
11

Таблица 3
Объем древесных отходов лесопромышленных и деревообрабатывающих предприятийКрасноярского края [7]
Отходы от видов деятельности |
2012г. |
Лесозаготовительная, тыс.м3 |
2 035,00 |
Деревообрабатывающая, тыс.м3. |
2 384,53 |
Всего, тыс.м3 |
4 419,53 |
Отходы от лесозаготовительной деятельности обычно сжигаются на месте заготовки.Основное количество отходов от всего объема отходов от лесозаготовительной деятельности в крае приходится на районы:
-Кежемский - 28 %;
-Богучанский - 31 %;
-Енисейский - 13 %;
-другие районы - 28 %.
Объемы отходов деревообрабатывающей деятельности предприятий Красноярского краяпредставлены в таблице 4.
Таблица 4
Объемы отходов деревообрабатывающих предприятий [7]
Отходы от деревообрабатывающей деятельности |
2012 |
Переработанные отходы, тыс.м3 |
1 541,25 |
Не переработанные отходы, тыс.м3 |
843,29 |
Основные предприятия, производящие переработку отходов в другие виды продукции, находятся в:
-г. Лесосибирске (ОАО «Лесосибирский ЛДК № 1», ЗАО «Новоенисейский ЛХК»);
-г. Красноярске (ЗАО «Красноярский ДОК», ООО «Енисейский ЦБК»);п. Ярки(ЗАО «Краслесинвест»);
-г. Кодинске (ООО «Приангарский ЛПК»);
-п. Верхнепашино (ООО «Сиблес Проект»);
-Березовском районе (ООО «ДОК «Енисей»); Енисейском районе (ОАО «Ангара Пейпа»).
Общий объем непереработанных отходов от деревообрабатывающей деятельности в крае приходится на: г. Лесосибирск - 38 %;г. Канск - 11 %;г. Кодинск - 35%; п. Богучаны - 16 %.
Выводы
1.Технико-экономическая оценка возможности использования возобновляемых источников энергии на территории Красноярского края в разрезе муниципальных образований края, проведенная учеными Сибирского федерального университета при участии ученых Красноярского аграрного университета [7], позволяет эффективно использовать ВИЭ, в том числе биоэнергетические ресурсы.
2.Например, с учетом количества объема отходов и годовой выработки тепловой энергии, можно сделать вывод, что применение в качестве топлива отходов древесины позволит обеспечить г. Лесосибирск на 14 % , г. Кодинск на 79
%и п. Богучаны на 70% от годовой тепловой выработки[7].
12
Литература
1.Делягин, В.Н. Оптимизация параметров систем энергообеспечения сельскохозяйственных потребителей (тепловые процессы)/В.Н. Делягин. -Новосибирск: РАСХН Сиб. отд-ние. СибИМЭ, 2005. -300 с.
2.Цугленок, Н.В. Рациональное сочетание традиционных и возобновляемых источников энергии в системе энергоснабжения сельскохозяйственных потребителей / Н.В. Цугленок, С.К. Шерьязов, А.В. Бастрон; Краснояр. гос. аграр. ун-т. – Красноярск, 2012. – 306 с.
3.Горбунов, Б.И. Биоэнергетический вектор перспективного развития сельскохозяйственных производств / Б.И. Горбунов, И.В. Филимонов, Е.В. Михалѐв и др. // Актуальные проблемы энергетики АПК: материалы VIмеждународной научно-практической конференции. – Саратов: ООО «ЦеСАин», 2015. – С. 38 – 41.
4.Саплин Л.А. Энергоснабжение сельскохозяйственных потребителей с использованием возобновляемых источников: Учеб.пособие / Л.А. Саплин, С.К. Шерьязов и др.; под общей ред. Л.А. Саплина. – Челябинск: ЧГАУ, 2000.
5.Промышленные котлы в Тульской области [Электронный ресурс] // КОТЛЫ HERLT СЕРИИ HSV НА СОЛОМЕURL:http://bizorg.su/tulskaya-obl-rg/promyshlennye-kotly-r(дата обращения 30.09.2015 г.).
6.Перов, Н.В. Анализ вариантов содержания КРС на глубокой соломенной подстилке / Н.В. Перов // Современный фермер. 2012. - №2.- С. 26 – 27.
7.Инвестиции в возобновляемую энергетику [Электронный ресурс] // Пояснительная записка к исследовательской работе «Технико-экономическая оценка возможности использования возобновляемых источников энергии на территории Красноярского края в разрезе муниципальных образований края» (Том 5 - Биоэнергетика) URL:http://gkh24.ru/pages/view/61 (дата обращения 30.09.2015 г.).
УДК 631.3.004.67-034
И.В. Комаровский, В.А. Мальцев,
ФГБОУ ВО Пермская ГСХА, г. Пермь, Россия
ВТУЛКИ НАСОСОВ ГИДРОПРИВОДОВ СЕЛЬСКОХОЗЯЙСТВЕННОЙ ТЕХНИКИ ИЗ ПОРОШКОВОГО АНТИФРИКЦИОННОГО МАТЕРИАЛА
НА ОСНОВЕ АЛЮМИНИЯ
Аннотация. Работа посвящена разработке порошковых материалов на основе алюминия, а также упрочнению путем калибрования и микродугового оксидирования.
Ключевые слова: порошковая металлургия, втулка насосов НШ-46У, испытания.
В настоящее время особое внимание уделяется созданию антифрикционных порошковых алюминиевых сплавов. Эти сплавы являются перспективными заместителями и конкурентами оловянистых бронз: они дешевые, характеризуются более высокой теплопроводностью, имеют большой срок службы и величину произведения РV. Однако промышленное производство порошковых алюминиевых сплавов в нашей стране не развито, а за рубежом оно имеют ограниченное применение.
Настоящая работа посвящена разработке порошковых материалов на основе алюминия для изготовления деталей тяжело нагруженных узлов трения, в частности втулок шестеренных насосов НШ-46У, НШ-32У гидросистем сельхозмашин.
13
Для выявления влияния состава материалов на структуру и физико-механические свойства исследование выполнено с применением метода математического планирования.
Изучение влияния давления калибрования на физико-механические свойства и оценка работоспособности aнтифрикционных порошковых материалов проведены на сплавах оптимального состава.
Исследование осуществляли на порошковых материалах системы Al-Cu- Sn-S. Медь – самый распространенный легирующий элемент, используемый для получения порошковых легированных материалов. Медь – благоприятно влияет как на технологию изготовления (улучшает прессуемость, уменьшает усадку, стабилизирует размеры изделий при спекании), так и на механические свойства и износостойкость порошковых материалов.
Олово не растворяется в алюминии и не смачивает его, зато хорошо взаимодействует с медью, образуя легкоплавкую эвтектику CuSn, которая легко заполняет поры и тем самым способствует увеличению прочности и износостойкости порошкового алюминиевого сплава. Частично олово остается в свободном виде и повышает антифрикционные свойства материала.
Сера, введенная в состав порошковых материалов, способствует образованию сульфидов, которые играют роль твердой смазки, и приводит к возникновению на трущихся поверхностях разделительной пленки, позволяющей исключить контакт ювенильных металлических поверхностей и последующее схватывание в условиях сухого и граничного трения.
Концентрация меди в порошковых алюминиевых сплавах изменяли в пределах 1-5% массы, серы – 1-2% массы, олова – 1-3% массы. В трехмерном пространстве факторов точки, соответствующие исследованным составам, располагали в вершинах прямоугольного параллелепипеда. Все композиции были получены механическим сухим перемешиванием порошков, прессованием при давлении 300 МПа и спеканием в вакууме 1х10-2 Па при температурах 550оС (композиции системы Al-Cu- Sn) и 600оС (композиции системы Al-Cu, Al-Cu-S) в течение 2-х часов. Калибрование спеченных материалов проводили при давлениях 200-800 МПа.
Металлографическое исследование спеченных композиций показало, что структура сплавов системы Al-Cu представляет собой твердый раствор меди в алюминии с избыточными выделениями интерметаллидов CuAl2 по границам и в теле зерна, а также одиночными включениями не растворившейся меди. В структуре сплавов системы Al-Cu-Sn наблюдается эвтектика Al-Sn, которая образуется на начальных стадиях спекания, конгломерируясь с медью, перераспределяется по межчастичным границам, заполняет поры и затвердевает при охлаждении до комнатной температуры. Для структуры сплавов системы Al-Cu-S характерным является наличие включений свободной серы и сульфидов, равномерно распределенных в металлической основе.
При испытании физико-механических свойств спеченных материалов на основе алюминия установлено, что увеличение содержания меди в сплавах от 1% до 5% массы приводит к снижению усадки, повышению их прочности и твердости материалов. Ударная вязкость алюминиевых сплавов при внедрении меди от 1% до 3,5% массы уменьшается, а при дальнейшем увеличении ее концентрация возрастает. С повышением содержания серы до 2% массы и олово до 3% массы усадка ма-
14
териалов несколько возрастает, прочностные свойства снижаются, твердость практически не изменяется. Оптимальным сочетанием механических свойств характеризуются алюминиевые сплавы, содержащие 3% массы Сu и 1% массы S и 5% массы Cu и 3% массы Sn. Предел прочности при растяжении спеченных алюминиевых сплавов, легированных серой и оловом, оставляет 63 МПа, предел прочности при изгибе – 17 МПа и 8 МПа, сжатие – 360 МПа и 340 МПа, ударная вязкость – 20 кДж/м2 и 50 кДж/м2, соответственно, твердость – 41 НВ.
После калибрования прочности характеристики порошковых алюминиевых сплавов повышаются в 1,3-1,5 раза, ударная вязкость при этом снижается. Оптимальное давление калибрования, обеспечивающее максимальный комплекс механических свойств, составляет 400 МПа. Коэффициент трения порошковых алюминиевых сплавов после калибрования при испытании в паре с цементированной и закаленной сталью 18ХГТ при скорости скольжения – 0,9 м/сек, в дизельном масле М10В2 снижается по сравнению со спеченным состоянием с 0,03- 0,1 до 0,02-0,05. Допустимое давление повышается с 4-4,5 МПа до 9-10 МПа. Износостойкость откалиброванного порошкового сплава, легированного серой (J =1,21 мкм/км) в 3,5 раза выше, чем у антифрикционного компактного алюминиевого сплава АО-7-3 (J = 4.3 мкм/км), в то время как величина износа порошкового материала, содержащего олово, (J= 3,5мкм/км) находится примерно на одном уровне с аналогичной характеристикой указанного компактного сплава.
На основании исследований для изготовления втулок насосов НШ-4У, НШ-32У гидросистем сельхозмашин опробован сплав ПДЗК1, характеризующийся требуемым сочетанием механических и триботехнических свойств. Испытания шестеренных насосов с втулками из порошкового сплава на основе алюминия проводили на стенде КИ 4815М с целью оценки работоспособности в условиях, близких к эксплуатационным. В качестве рабочей жидкости применяли масло М10В2. Температура рабочей жидкости 50оС 5о. Испытываемые насосы подвергали нагружению давления ступенями от 0 до 13 МПа, через каждые 2 МПа с выдержкой на каждой ступени 5 минут. Втулки насосов работали в паре с ведущей и ведомой шестернями из стали 18ХГТ, подвергнутой цементации на глубину 0,9-1,5 мм и закалке до твердости 5=62 НРС. Максимальное давление в зоне контакта составляло 15 МПа. При этом замеряли объемный КПД, После испытаний насосы разбирали и проводили техническую экспертизу деталей. Состояние деталей после испытаний дало основание сделать вывод о пригодности разработанного материала для изготовления втулок гидронасосов. Продолжаются испытания насосов в полевых условиях, которые показывают положительные результаты.
Применение метода порошковой металлургии для изготовления деталей гидронасосов тракторов и других сельскохозяйственных машин позволит снизить себестоимость, сократить технологический цикл изготовления деталей за счет исключения основных операций механической обработки, повысить коэффициент использования материала с 0,45-0,6 до 0,8-0,9 и повысить ресурс работы насосов. Кроме того, с целью увеличения механических и антифрикционных было опробовано микродуговое оксидирование втулок и продолжаются испытания таких втулок.
15
Литература
1.Комаровский, И.В. Опыт применения антифрикционных материалов при ремонте насосов гидросистем /И.В. Комаровский, Н.Н. Масленников, А.П. Тихонова //Организация и технология ремонта сельскохозяйственной техники. Межвузовский сборник научных трудов.- Пермь: ПСХИ, 1984.- С.23-27
2.Комаровский, И.В. Прессформа для изготовления втулок насосов НШ-46, НШ-32 /И.В. Комаровский, В.В. Разина // Организация и технология ремонта сельскохозяйственной техники. Межвузовский сборник научных трудов.- Пермь: ПСХИ , 1984.-С.28-29
3.Порошковый антифрикционный материал на основе алюминия: а.с. 1280906: 4 С 22 С 21/12, F 16 С 33/12 /Пермский политехнический институт, Анциферов В.Н., Тимохова А.П., Масленников Н.Е., Комаровский И.В., Федосеева С.Н. (СССР).- № 387528/22-02; заявл. 26.03.85; опубл. 01.09.86
УДК 621.6.052:620.089.111
Ю.Е. Куимов – канд. техн. наук, В.А. Мальцев,
ФГБОУ ВО Пермская ГСХА, г. Пермь, Россия
ОПРЕДЕЛЕНИЕ ИЗНОСА СОПРЯЖЕНИЯ КОРПУС-ПЛАСТИНА РОТАЦИОННОГО НАСОСА
ДЛЯ СОЗДАНИЯ РАЗРЯЖЕНИЯ ДОИЛЬНОЙ УСТАНОВКИ
Аннотация. Теоретически обоснованы параметры лопастного насоса, влияющие на износ сопряжения корпус-пластина.
Ключевые слова: насос, износ, изнашивание, ротор, расчет.
В доильных установках, применяемых на молочно-товарных фермах, широко используются ротационные насосы. К их работе предъявляются высокие требования по производительности, т.к. его снижение приводит к нарушению процесса доения коров и их заболеваниям.
Снижение производительности происходит по причине увеличения радиального и торцевого зазора из-за износа сопряжения корпус-пластина. Корпус насоса изготовлен из чугуна, имеющего кристаллическое строение, пластины – текстолитовые. Такие разнородные материалы пары трения накладывают свои особенности на процесс изнашивания.
Для определения суммарного износа сопряжения сделаем следующие допущения:
-всасывающие и выпускные окна насоса, расположенные в корпусе, не оказывают существенного влияния на удельное давление пластины на корпус;
-окружная скорость пластины по поверхности корпуса постоянна
V=2 n R=const,
где n – частота вращения ротора;
R – средний радиус вращения пластин в корпусе, из-за наличия эксцентриситета ротора относительно корпуса;
16

- износ деталей пары трения подчиняется линейной зависимости. Поскольку поверхность контакта общая для двух тел [1], то суммарный из-
нос определяют из выражения
или = (1)
где J1 и J2 - износ корпуса и пластины, измеренный в направлении нормальной к поверхности трения, соответственно;
- угол между нормалью к поверхности трения и направлением движения.
= 90 ;
- скорость изнашивания сопряжения;
и- скорость изнашивания корпуса и пластины, отнесенная к дан-
ной точке поверхности трения, соответственно.
Скорость изнашивания корпуса и пластины можно определить из выражения [2]
= 1 |
, (2) |
= 2 |
, |
где n – показатель степени. Для линейной зависимости износа n = 1; 1 и 2
– характеристики физико-механических свойств материалов пары трения (твердость, износостойкость, шероховатость и др.).
– удельное давление на поверхности контакта. v – окружная скорость пластины.
Удельное давление определяется из выражения
= ц , (3)
где ц центробежная сила,– площадь контакта.
Центробежная сила определяется по формуле
ц = |
|
, (4) |
|
где – масса пластины.
Площадь контакта определяется из выражения
= |
, (5) |
где – площадь контакта,
–ширина пластины,
–длина пластины.
После преобразования получим
=
Удельное давление на поверхности контакта пары трения зависит от частоты вращения ротора.
17

Скорость изнашивания корпуса |
и пластины |
определяется через вре- |
||
мя работы насоса |
|
|
|
|
1 = |
|
, |
|
|
|
|
|||
2 = |
|
, (6) |
|
|
|
|
где t – время работы насоса.
Подставив в формулу (1) полученные выражения и сделав соответствующие преобразования, получим выражение для определения суммарного износа пары трения
= ( 1 ) , (7)
где – число пластин ротора насоса.
Износ сопряжения корпус-пластина ротора зависит от частоты вращения, физико-механических свойств материала пары трения, числа пластин и времени работы. Данный вывод должен быть подтвержден экспериментально.
Литература
1.Костецкий, Б.И. Трение, смазка и износ в машинах /Б.И. Костецкий.- Киев: Техника,
1970.- 396с.
2.Трение, износ и смазка (Трибология и триботехника) /А.В. Чичинадзе, Э.М. Берлинер, Д.Э. Браун и др.; под общ. ред. А.В. Чичинадзе.- М.: Машиностроение, 2003.- 576с.; ил.
УДК 631.362.
Е.А. Лялин, М.А. Трутнев – канд. техн. наук,
ФГБОУ ВО Пермская ГСХА, г. Пермь, Россия
К ОБОСНОВАНИЮ ДЛИНЫ ЗАГРУЗОЧНОГО ОКНА СПИРАЛЬНО-ВИНТОВОГО ДОЗАТОРА
Аннотация. Рассмотрена зависимость длины загрузочного окна бункера спирально-винтового дозатора (СВД) от его конструктивных параметров. Теоретически определена зависимость длины загрузочного окна от частоты вращения и шага спирали, удобная для практического применения.
Ключевые слова: спирально-винтовой дозатор, загрузочное окно, частота вращения, шаг спирали.
Для нормальной работы спирально-винтового дозатора (СВД) необходимо, чтобы пропускная способность загрузочного окна бункера дозатора несколько превышала максимальную транспортирующую способность винтовой спирали или была равной ей. Подача материала из бункера осуществляется через отверстие загрузочного окна. Конец спирали на участке, равном длине этого окна, захватывает материал и передает его в кожух. Исходя из конструктив-
18
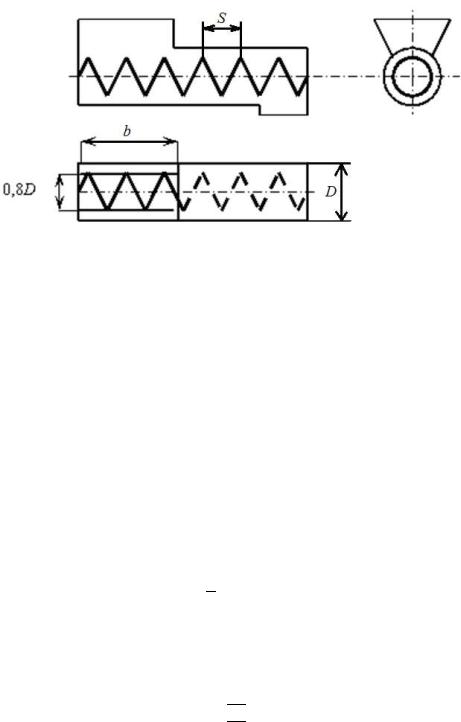
ных соображений ширину окна h принимают обычно равной 0,6...0,8диаметра кожуха D, а длину b=(1,5-2,5)S, гдеS – шагвинта (рис. 1).Исследования показали, что отклонение длины загрузочного окна отоптимальнойвеличинывызываетвозрастаниеудельнойпотребноймощности и существенно влияет на подачу Qд дозатора[2]. Причем здесь не учтено влияние частоты вращения спирали на длину загрузочного окна.
Рисунок 1. Схема спирально-винтового дозатора
Теоретически определим оптимальную величину b в зависимости от частоты вращения спирали n, диаметра кожуха D и шага пружины S.
Как мы уже отметили ранее, нормальная работа СВД возможна при соблюдении следующего условия[2]:
д, (1)
где Q0 – подача истечения или пропускная способность отверстия загрузочного окна, равная[4]
, (2)
где – общий коэффициент расхода сыпучего материала; ρ–плотность сыпучего материала, кг/м3;
v – cкорость истечения сыпучего материала; F0–площадьвходногоотверстия,м2.
Общий коэффициент расхода сыпучего материала может быть найден из выражения
√, (3)
гдеλиλ1-коэффициенты расхода, зависящие от удельного веса и плотности укладки, размера сыпучего материала и радиуса выходного отверстия[4].
Скорость истечения сыпучего материала из загрузочного окна Р.Л. Зенков рекомендует определять по формуле[4]:
√ г , (4)
где г –гидравлический радиус входного прямоугольного отверстия; f-коэффициент внутреннего трения.
19