
525
.pdf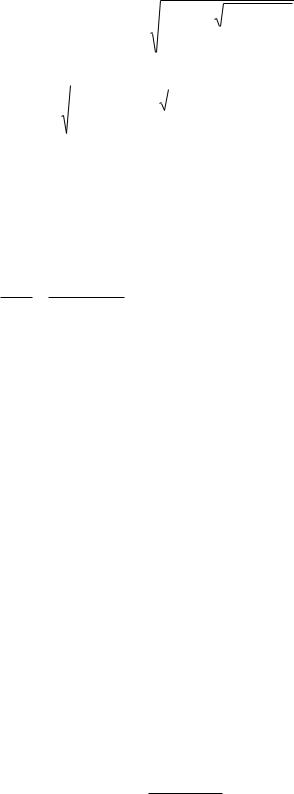
1.10.17. Проверка контактной прочности зубьев конического колеса
|
|
|
|
|
335 |
|
|
|
T2 Kн (U К |
2 |
1) |
3 |
н ; |
|||||
|
|
|
Ϭн= |
|
|
|
|
|
|
|
|
|
|
|||||
|
|
|
Re 0.5 b |
|
|
в U К |
2 |
|
|
|
||||||||
|
|
|
|
|
|
|
|
|
|
|
|
|
|
|
|
|||
|
|
|
|
|
|
|
|
|
|
|
|
|
|
|
|
|
|
|
Ϭн = |
|
335 |
|
|
15,3 104 |
1,1 |
|
|
(3,142 1)3 |
|
=376,3 Н/мм2. |
|||||||
|
0,5 |
|
|
|
40 |
3,142 |
|
|
||||||||||
130 |
40 |
|
|
|
|
|
|
|
|
|
Действующее контактное напряжение Ϭн2 =376,3 Н/мм2 меньше допускаемого [Ϭн]2 = 409,4 Н/мм2. Условие прочности выдержано.
1.10.18. Определение сил в зацеплении Окружное усилие
Ft1=- Ft2= 2 Т1 = 2 5.07 104 1516 Н. dm1 66.89
Радиальное усилие шестерни, по модулю равное осевому усилию на коническом колесе
Fr1 = Fа2 =Ft1 ·tgα·cosδ1 = 1516·tg20°·cos17.7° =526 Н.
Основное усилие шестерни, по модулю равное радиальному усилию на коническом колесе
F а1=Fr2 = Ft1 ·tgα·cosδ2 =1516·tg20°·cos72.3° =168 Н.
1.10.19. Определение эквивалентного числа зубьев шестерни и колеса
|
Z1 |
21 |
|
66 |
66 |
|
|||
Zυ1 = |
|
|
|
22 , |
Zυ2= |
|
|
|
220 . |
cos 1 |
cos17.7 |
cos 2 |
cos 72.3 |
1.10.20. Уточнение коэффициента нагрузки при расчете на изгиб
KF=KFβ· KFυ ;
по табл. П.16 приложения KFβ=1,24; по табл. П.17 приложения KFυ = 1,05; KF=1,24· 1,05=1,3.
1.10.21. Проверка прочности зубьев на изгиб
Ft K Y
ϬF = F F F
b mtm
где YF – коэффициент формы зуба, по табл. П20
YF1 = 4,08; YF2 =3,6.
,
приложения
21
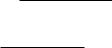
Шестерня - ϬF1 = 1516 1,3 4,08 63,2 Н/мм2, 40 3,185
Колесо - ϬF2 = 1516 1,3 3,6 55,8 Н/мм2. 40 3,185
Действующее напряжение изгиба в зубьях шестерни и колеса меньше допускаемого. Условие прочности выполняется.
1.10.22. Определение геометрических размеров конической передачи производят по параметрам, приведенным в табл. П21 приложения.
2.ЧЕРВЯЧНЫЕ ПЕРЕДАЧИ
2.1.Критерии работоспособности и расчета передачи
Методические советы. Студент изучает классификацию червячных передач по форме червяка и профилю зубьев, силы в зацеплении, расчет на прочность по контактным напряжениям и напряжениям изгиба. Обратить внимание на необходимость теплового расчета червячных редукторов.
Для передачи значительных нагрузок при большом передаточном числе применяются червячные передачи, представляющие собой разновидность винтовой передачи.
Червячные передачи так же, как и зубчатые, рассчитывают по контактным напряжениям и напряжениям изгиба. В отличие от зубчатых, в червячных передачах чаще наблюдается износ и заедание, а не выкрашивание от усталости поверхности зубьев. Повышенный износ и заедание червячной передачи связан с большой стойкостью скольжения в зацеплении.
Для предупреждения заедания ограничивают величину контактных напряжений и применяют антифрикционные материалы: червяк – сталь, червячное колесо
– бронза или чугун. Устранение заедания в червячной передаче не устраняет износа зубьев.
Интенсивность износа также зависит от величины контактных напряжений. Поэтому расчет по контактным напряжениям для червячных передач является основным. Расчет по напряжениям изгиба проводится при этом как проверочный. Только при мелкомодульных колесах с большим числом зубьев червячного колеса напряжение изгиба может оказать решающее значение.
2.2. Последовательность проектного расчета червячной передачи
При расчете червячной передачи рекомендуется придерживаться следующего порядка:
1.Выписывают исходные данные для расчета.
2.Задают число заходов червяка и определяют число зубьев червячного коле-
са.
22

3.Выбирают материалы для червячной пары и выписывают значения допускаемых напряжений.
4.Определяют расчетное значение допускаемых напряжений.
5.Определяют межосевое расстояние червячной передачи на условия контактной прочности зубьев червячного колеса.
6.Определяют модуль зацепления, согласуя модуль и относительную толщину червяка с ГОСТ 2144 - 76.
7.Определяют скорость скольжения в зацеплении и назначают степень точности передачи.
8.Уточняют КПД червячной передачи и значение вращающего момента на валу червячного колеса.
9.Уточняют коэффициент нагрузки.
10.Проверяют контактную прочность зубьев червячного колеса.
11.Проверяют прочность зубьев червячного колеса по напряжениям изгиба.
12.Определяют геометрические размеры червячной передачи.
13.Определяют силы, действующей в зацеплении червячной передачи.
2.3.Пример проектного расчета червячной передачи
2.3.1. Исходные данные Мощность на валу червяка Р1 = 5 кВт.
Вращающий момент на валу червяка Т1 = 5·104 Нмм. Частота вращения вала червяка n1 = 970 мин-1. Передаточное число червячной передачи U = 24,25.
Вращающий момент на валу червячного колеса Т2 = 10,4·105 Нмм. Частота вращения вала червячного колеса n2 = 40 мин-1.
Срок службы передачи t=15000 ч.
2.3.2.Согласование передаточного числа червячной передачи Принимаем по ГОСТ 2144-76 U=25.
2.3.3.Процент отклонения передаточного числа червячной передачи от задан-
ного
∆U = 25 24,25 100 3% ,что является допустимым.
25
2.3.4. Назначение числа заходов червяка и определение числа зубьев червячного колеса
Принимаем Z1 = 2, тогда Z2=Z1·U=25·2=50.
Условие Z2≥Z2min =28 выдержано.
2.3.5. Уточнение частоты вращения вала колеса n2 = Un1 97025 38.8 мин-1.
23

2.3.6. Выбор материала червячной пары Для изготовления червячной передачи применяется архимедов червяк. По
табл.П1 приложения материал – Сталь 45 с твердостью витков не более HRC 45. Для венца червячного колеса – бронзу Бр.ОФ10-1 (отливка в кокиль). Табличные значения допускаемых напряжений: [Ϭн]' = 186 Н/мм2, [Ϭо]' F = 57 Н/мм2 (табл.П25 приложения).
2.3.7. Определение расчетного значения допускаемого контактного напряжения
[Ϭн] = [Gн]' ·КHL,
где КHL – коэффициент долговечности, определяющий по формуле
КHL = 8 107 ,
N
NΣ – суммарное число циклов зуба колеса за весь срок службы передачи
NΣ = 60·n2·t;
n2 – частота вращения вала червячного колеса; t – срок службы передачи;
NΣ = 60·n2·t= 60·38,8·15000=3,49·107;
минимальное значение коэффициента долговечности при расчете на контактную прочность КHLmin =0,67, максимальное - КHLmax =1,15.
107 |
0,855 ; |
||
КHL= 8 |
|
|
|
|
107 |
||
3,49 |
|
[Ϭн] = 186 ·0,855 = 159 Н/мм2.
2.3.8. Определение расчетного значения допускаемого напряжения изгиба
[Ϭо] F =[Ϭо]' F · КFL,
где КFL – коэффициент долговечности при расчете на изгиб, определяемый выражением
КFL = 9 106 .
N
Для передач машинного привода при числе циклов нагружения каждого зуба червячного колеса, меньшим чем 106 , следует принимать NΣ =106; если окажется, что число циклов больше 25·107, надлежит принимать NΣ =25·107.
Следовательно, коэффициент долговечности изменяется в пределах 1,0≥
КFL≥0,543
КFL= |
106 |
0,673 ; |
3,49 107 |
[Ϭо] F = 57·0,673=38,36 Н/мм2.
2.3.9. Определение межосевого расстояния передачи из условия контактной прочности зубьев червячного колеса
24

|
Z |
2 |
|
|
|
|
170 |
2 |
|
|
|
|
|
|
3 |
|
|
|
T2 Кн |
мм, |
|
|
|
|
|
|||||||
αω = |
|
|
1 |
|
Z2 |
|
|
|||
|
q |
|
|
|
Gн / q |
|
|
где q – коэффициент относительной толщины червяка; Z2 – число зубьев червячного колеса;
Т2 – нормальный вращающий момент на валу червячного колеса; Кн – коэффициент нагрузки.
В предварительных расчетах рекомендуется принимать: q=8…12; Кн=1,2. Принимаем первоначально q=10, тогда
|
|
50 |
|
|
|
|
|
170 |
2 |
5 |
|
|
||
αω = |
|
|
|
1 |
3 |
|
|
|
10,4 10 |
|
1,2 |
=227,34 мм. |
||
|
|
|
159 /10 |
|
||||||||||
|
|
10 |
|
|
|
|
50 |
|
|
|
|
|||
2.3.10. Определение модуля зацепления |
|
|||||||||||||
m = |
2 |
|
|
|
2 227.34 |
7.58 мм. |
|
|
|
|||||
|
|
|
|
|
|
|
|
|
|
|||||
Z2 q |
|
50 10 |
|
|
|
По ГОСТ 2144-75 (табл. П23 приложения) принимаем: m=8мм, q=10. 2.3.11. Уточнение межосевого расстояния
αω = |
m(q Z2 ) |
|
8(10 50) |
240 мм. |
|
2 |
|||
2 |
|
|
2.3.12.Определение угла подъема винтовой линии червяка По табл. П24 приложения γ=11°18' 36".
2.3.13.Определение окружной скорости червяка
υ1 |
= |
m q n1 |
|
3.14 8 10 970 |
4.06 м/с. |
|
60 1000 |
60 1000 |
|||||
|
|
|
|
2.3.14. Определение скорости скольжения в зацеплении
υS = |
1 |
|
4.06 |
|
4.14 |
м/с. |
|
cos |
|
|
|||||
|
|
|
|
||||
|
|
cos11 18 36 |
|
|
При такой скорости скольжения по табл. П31 приложения рекомендуется 8-я степень точности.
2.3.15. Уточнение КПД червячной передачи с учетом потерь в опорах
tg
η=(0,95…0,96) tg ( ) ,
где ρ' – угол трения, связанный пропорциональной зависимостью с коэффициентом трения f'
По табл. П29 приложения ρ' =1°43' ;
|
|
|
|
|
|
η=0,96 |
tg11 18 36 |
0,83 . |
|||
|
|
|
|||
|
|
||||
|
tg (11 18 36 |
1 43 ) |
|
2.3.16. Уточнение вращающего момента на валу червячного колеса
Т2 =Т1·U·η, Н·мм, где Т1· - вращающий момент на валу червяка,
Т2 =5·104 25·0,83=10,4·105 Н·мм.
25

2.3.17. Уточнение коэффициента нагрузки Кн=КF=Кβ·Кυ,
где Кн – коэффициент нагрузки при расчете на контактную прочность; КF – коэффициент нагрузки при расчете на изгиб;
Кβ – коэффициент, учитывающий неравномерность распределения нагрузки по длине контактных линий;
Кυ – коэффициент, учитывающий динамичность нагрузки.
Коэффициент Кβ зависит от характера изменения нагрузки и от деформации червяка. Определяется по выражению:
|
Z |
3 |
|
|
Кβ = 1+ |
|
2 |
|
1 x , |
|
||||
|
Q |
|
||
|
|
|
|
где Q – коэффициент деформации червяка, определяемый по табл. П32 приложения;
х – коэффициент, учитывающий характер изменения нагрузки и определяется по выражению
Ti ti ni
х = T max ti ni =1;
Ti, ti, ni– вращающий момент, продолжительность и частота вращения при режиме I;
Тmax – максимальный, длительно действующий вращающий момент. При постоянной нагрузке х =1, следовательно: Кβ =1. По табл. П30 приложения Кυ = 1,4.
Кн= Кυ=1·1,4=1,4.
2.3.18. Проверка контактной прочности зубьев червячного колеса
|
|
|
|
|
|
|
|
|
|
Z |
2 |
|
3 |
|
|
|
|
|
|
|
|
|
|
|
|
|
|
|
|
1 |
|
T K |
|
|
|
||
|
|
|
|
|
|
|
|
|
|
|
|
H |
|
|||||
|
|
|
|
|
170 |
|
|
g |
|
|
2 |
|
|
|||||
|
|
H |
|
|
|
|
|
|
|
|
|
H , |
||||||
|
|
Z |
2 |
/ g |
|
|
|
|
3 |
|
|
|
||||||
|
|
|
|
|
|
|
|
|
|
|
|
|
|
|
|
|
||
|
|
|
|
|
|
|
|
|
|
|||||||||
H |
|
170 |
|
|
|
50 /10 1 3 |
10.4 105 |
1.4 |
162.2 Н/мм2 |
|||||||||
50 /10 |
|
|
|
|
|
|
2403 |
|
|
|
|
|
||||||
|
|
|
|
|
|
|
|
|
|
|
|
|
|
|
Действительное контактное напряжение ϬH =162,2 Н/мм2 больше допустимого [ϬH]=159 Н/мм2 . Условие прочности не выполняется. Имеет место перегрузка по контактным напряжениям. Перегрузка в процентах:
162,2 159 100 1,97%
162,2
Результат проверочного расчета считается удовлетворительным, так как перегрузка по контактным напряжениям не превышает 5%, а недогрузка 15%.
2.3.19. Определение геометрических размеров передачи Червяк: d1 m g 8 10 80 мм
26
d 1 m g 2 m 8 10 2 8 96 мм
d f1 m g 2.4m 8 10 2.4 8 60.8 мм
b1 11 0.06 Z2 m 11 0.06 50 8 112 мм Колесо червячное:
d2 m Z2 8 50 400 мм
d 2 mZ2 2m 8 50 2 8 416 мм
d f 2 mZ2 2.4m 8 50 2.4 8 380.8 мм b2 0.75 d 1 0.75 96 72 мм
d |
d |
|
|
6m |
416 |
6 8 |
|
428 мм |
||||||
|
|
|
|
|
|
|||||||||
m2 |
|
|
2 |
|
|
Z1 2 |
|
|
|
2 2 |
||||
|
|
|
|
|
|
|
|
|
||||||
sin 1 |
|
|
|
b2 |
|
|
|
72 |
|
|
0.782 ; |
|||
d 1 0.5m |
|
0.5 8 |
||||||||||||
|
|
|
96 |
|
|
1 51 24 2 1 102 48
2.3.20. Проверка зубьев червячного колеса на выносливость по напряжениям изгиба
|
|
|
1.2 T2 |
K F YF |
|
|
, |
||
F |
|
|
F |
||||||
|
|
Z |
|
b m2 |
|
|
|||
|
|
|
2 |
|
|
|
|||
|
|
|
|
|
2 |
|
|
|
где YF – коэффициент формы зуба, определяемый по эквивалентному числу зубьев червячного колеса
Z 2 |
|
Z2 |
|
50 |
|
53; |
|
|
cos |
|
|
|
|
||||
|
|
|
cos11 18 36 |
|
|
|||
по табл. П20 приложения YF=2,18 |
|
|
||||||
|
|
|
|
F |
1.2 10.4 105 |
1.4 2.18 |
16.54 Н/мм2 |
|
|
|
|
|
|
50 72 |
82 |
||
|
|
|
|
|
|
|
Действующее в зубе напряжение изгиба ϬF = 16,54 Н/мм2 меньше допустимого [Ϭ0]F=38.36 Н/мм2 . Условие прочности выполняется.
2.3.21. Определение сил в зацеплении червячной передачи Окружное усилие червяка, по модулю равное осевому усилию на червячном
колесе:
|
|
|
2 T |
|
2 5 104 |
|
F |
F |
|
1 |
|
|
1255 Н. |
|
|
|||||
t1 |
1 |
|
d1 |
|
80 |
|
|
|
|
|
|
Окружное усилие червячного колеса, по модулю равное осевому усилию червяка:
|
|
|
2 T |
2 10.4 105 |
|||
F |
F |
|
|
2 |
|
|
5205 Н. |
|
|
|
|||||
t 2 |
2 |
|
d2 |
400 |
|
||
|
|
|
|
||||
Радиальное усилие в зацеплении |
|||||||
Fr1 Fr 2 |
Ft 2 |
tg 5205 tg 20 1895 Н. |
|||||
|
|
|
|
|
|
27 |
3. ПЛОСКОРЕМЕННАЯ ПЕРЕДАЧА
3.1. Материалы, конструкция и расчет
Методические советы. Обратить внимание, что ременная передача работает на использовании сил трения. Изучить кинематические, геометрические и силовые зависимости в ременной передаче. Тяговая способность ременной передачи и формула Эйлера. Напряжения в ремне. Скольжение и к.п.д. Расчет плоскоременных и клиноременных передач.
Приводной ремень должен обладать определенной тяговой способностью и достаточной долговечностью. Тяговая способность ремня обеспечивается надежным сцеплением его со шкивом, что обусловлено высоким коэффициентом трения между ними. Долговечность ремня зависит от возникающих в нем напряжений изгиба и частоты циклов нагружений – числа пробегов ремня в единицу времени.
По материалам конструкции различают несколько типов ремней. К стандартным плоским ремням относятся: прорезиненные по ОСТ 38.05.98-76, кожаные по ГОСТ 6982-75 и шерстяные по ОСТ НКТП 3157, резинотканевые по ГОСТ
23831-79.
Прорезиненные ремни самые распространенные. Их изготавливают трех типов: А, Б, и В (табл.П.33 приложения). Из них наибольшее распространение получили ремни типа А, как наиболее гибкие.
При работе в сырых помещениях, а также в среде, насыщенной парами кислот или щелочей применяют ремни с резиновыми обкладками.
Допускаемая скорость ремней типа А = 30 м/с, типа Б = 20 м/с, типа В = 15
м/с.
Ремни в соответствии с предъявленными к ним требованиями рассчитывают на тяговую способность и долговечность. Эти расчеты вполне обеспечивают требуемую прочность рассчитываемых ремней.
Основным расчетом ремней считается расчет по тяговой способности. Расчет ремней на долговечность производится обычно как проверочный.
3.2.Пример проектирования плоскоременной передачи
3.2.1.Исходные данные
Мощность на ведущем валу Р1=5,9 кВт. Частота вращения ведущего вала n1=1440 мин-1. Передаточное число передачи U=2,5.
Прочие данные: передача от электродвигателя к ленточному транспортеру; работа в одну смену с постоянной нагрузкой; расположение передачи горизонтальное; регулирование напряжения ремня периодическое.
3.2.2.Выбор типа ремня
28

Предполагая, что скорость ремня не более 15 м/с, принимаем предварительно ремень типа В.
3.2.3. Определение диаметра меньшего шкива
D1 1200 |
|
P |
|
3 |
1 |
мм, |
|
|
|||
|
|
|
|
|
|
n1 |
|
где Р1 – передаваемая мощность, кВт;
n1 – частота вращения ведущего шкива, мин-1;
D1 1200 3 14405.9 192 мм.
По ГОСТ 17383-73 (табл. П34 приложения) принимается ближайший по стандартному ряду диаметр D1=200 мм.
3.2.4. Определение диаметра ведомого шкива с учетом упругого скольжения ремня Применяем значение коэффициента упругого скольжения ε=0,01.
D2 D1 U (1 ) 200 2.5(1 0.01) 495 мм.
По ГОСТ 17,383-73 принимаем D2=500 мм.
3.2.5. Уточнение передаточного числа с учетом упругого скольжения и отклонение его в процентах от заданного
U |
D2 |
|
500 |
2.25 , |
D (1 ) |
200(1 0.01) |
|||
|
1 |
|
|
|
U 2.25 2.5100 1% , что является допустимым.
2.25
3.2.6. Определение частоты вращения ведомого шкива с учетом упругого скольжения
n |
D1 n1(1 ) |
|
200 1400(1 0.01) |
570.2 мин-1. |
||||
|
|
|
|
|||||
2 |
|
D2 |
500 |
|
|
|||
|
|
|
|
|||||
3.2.7. Определение скорости ремня |
|
|||||||
|
D1 n1 |
|
3.14 200 1440 |
11.94 м/с. |
||||
60 1000 |
|
|||||||
|
|
|
60 1000 |
|
Предварительно принятый ремень типа А отвечает условию максимальной скорости.
3.2.8. Определение межосевого расстояния Так как по условию проектирование межосевое расстояние не задано, вос-
пользуемся рекомендуемой зависимостью: aw=2(Д1+Д2)=2 (200+500)=1400мм, aw=1400мм.
3.2.9. Определение длины ремня без учета провисания и с учетом стандарт-
ного ряда L=2aw- π(Д1+Д2)/2+(Д2-Д1)2/4aw=2·1400-3,14(200+500)/2+(500- 200)2/4·1400=3915мм.
С учетом стандартных значений (ГОСТ 23831 -79) принимается длина рем-
ня L=4250мм [1, с.120].
29

3.2.10. Проверка ремня на долговечность по числу пробегов ремня в секунду
,
L
где υ – скорость ремня, м/с;
L – теоретически длина ремня, м;
[ν] – допускаемое число пробегов ремня в секунду, рекомендуется для плоских приводных ремней [ν] =3…5 1/с;
3,915511,94 3,04 1/с.
Критерий долговечности удовлетворительный. 3.2.11. Определение угла обхвата на малом шкиве
180 60 |
D2 D1 |
|
180 60 |
500 200 |
167 . |
||||||
|
|
|
|
||||||||
1 |
|
|
|
|
|
|
|
1400 |
|
||
|
|
|
|
|
|
|
|||||
|
|
|
|
|
|
|
|
|
|
||
Условие 1 |
1 min |
150 соблюдается. |
|||||||||
3.2.12. Определение окружного усилия |
|||||||||||
F |
P 103 |
|
5.9 103 |
494 Н. |
|||||||
1 |
|
|
|
|
|
||||||
|
|
|
|
|
|
||||||
t |
|
|
11.94 |
|
|
|
|
|
|||
|
|
|
|
|
|
|
|||||
3.2.13. Определение расчетного допускаемого полезного напряжения в |
|||||||||||
ремне |
|
|
|
|
|
|
|
|
|
|
|
|
|
|
|
|
|
|
|
|
F F 0 K0 K K KP , |
||
где |
[ϬF]0 |
– допускаемое полезное напряжение в ремне. Значение этого |
напряжения для ременных передач приведены в табл. П36 приложения, для прорезиненных ремней F 0 2.25 Н/мм2;
К0 – коэффициент, учитывающий способ натяжения ремня и наклон линии центров передачи к горизонту; при периодическом натяжении ремня и угле наклона к горизонту не более 60° К0=1; при наклоне линии центров свыше 60° до
80° К0=0,8;
Кα – коэффициент, учитывающий влияние угла обхвата ремня малого шкива, определяется по выражению
K 1 0.003(180 1) ,
K 1 0.003(180 167 ) 0.96 ;
Кυ – коэффициент, учитывающий влияние скорости ремня, определяется по формуле
K 1.04 0.0004 2 ,
K 1.04 0.0004 11.942 0.98 ;
КР – коэффициент режима нагрузки, учитывающий влияние периодических колебаний нагрузки на долговечность ремня, изменяется в пределах 1…0,6. С учетом характера рабочей нагрузки по условию задания принимаем КР=1.
F 2.25 1 0.96 0.98 1 2.12 Н/мм2.
30