
книги / Экспертиза качества и разрушений
..pdf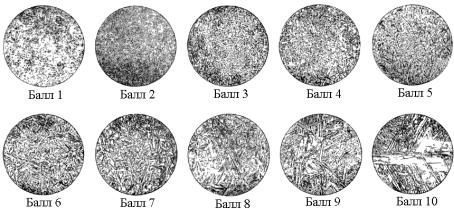
– силикаты, присутствующие в стали в виде стекол, образованных чистым SiO2 или SiO2 с примесями в нем оксидов железа, марганца, хрома, алюминия, вольфрама, а также кристаллических силикатов.
Силикаты составляют самую большую группу неметаллических включений. В жидкой стали неметаллические включения находятся
втвердом или жидком состоянии в зависимости от их температуры плавления.
Современный уровень производства стали позволяет в значительной мере удалить из металла различные включения. Однако общее содержание их в различных сталях колеблется в широких пределах и значительно влияет на свойства металла.
Современные способы производства стали и сплавов не дают возможности получить металл, не содержащий неметаллических включений. Большее или меньшее количество включений существует в любой стали
всоответствии с ее составом и условиями производства. Обычно количество неметаллических включений в стали не превышает 0,1 %. Однако
всвязи с их малыми размерами число включений в металле очень велико.
Определение и оценка микроструктуры сталей. Для быстрой оцен-
ки микроструктуры сталей используют стандартные шкалы микроструктур с указанием реактивов для травления. Наиболее часто встречаются следующие виды эталонных структур в соответствии с ГОСТ 8233–56 «Эталоны микроструктуры»: ферритно-перлитная, зернистый и пластинчатый перлит, мартенсит, остаточный аустенит, карбидная неоднородность, карбидная сетка, структурная полосчатость. К примеру, на рис. 3.37 приведены эталоны мартенситной структуры.
Рис. 3.37. Эталоны мартенситной структуры
101
Выявление и определение величина зерна производится в соответствии сГОСТ 5639–82. Различают действительное и наследственное зерно.
Часто определяют именно величину наследственного зерна, т.е. величину зерна аустенита после нагрева при определенных условиях, указанных в соответствующих стандартах. Наследственное зерно характеризует чувствительность стали к росту зерна при нагреве для термообработки. Для выявления границ зерен аустенита используют несколько методов.
Метод травления. Обычно применяют для сталей, закаливаемых на мартенсит или бейнит. Образец нагревают выше на 20–30 °С температуры нагрева под закалку, выдерживают 2–3 часа и охлаждают в масле или в воде, подвергают отпуску при 25–250 °С, а образцы высоколегированных сталей при 500–550 °С в течение 15–30 мин. Травление проводят пикриновой кислотой.
Метод цементации. Применяется для цементуемых сталей. Цементация проводится при температуре 900–950 °С в течение нескольких часов вкарбюризаторе с последующим медленным охлаждении до 600 °С. В результате на поверхностиобразуется карбидная сетка по границам зерен.
Метод окисления. Полированные шлифы нагревают в окислительной атмосфере, затем охлаждают в воде. Пленка окислов при ускоренном охлаждении откалывается от полированной поверхности в результате разных коэффициентов линейного расширения с металлом, а по границам сохраняется сетка оксидов.
Метод сетки феррита или цементита. Небольшие образцы нагре-
вают в аустенитной области, выдерживают и охлаждают: доэвтектоидные – на воздухе, а заэвтектоидные – с печью. Метод подходит для выявления зерна в углеродистых и низколегированных сталях.
Полученное зеренное строение подвергается дальнейшему анализу – производится определение балла (номера) зерна и его размеров. Существует несколько методов.
Метод сравнения с эталонными шкалами (рис. 3.38). Структуру, на-
блюдаемую при увеличении 100 в окуляре микроскопа, сравнивают с эталонной шкалой по ГОСТ 5639–82 и определяют размер зерна. Шкалы составлены таким образом, что при увеличении в 100 раз номер зерна G соответствует формуле m = 8 · 2G, где m – число зерен на 1 мм2 площади шлифа. Эталоны приведены в виде круга диаметром 79,8 мм, что соответствует площади на шлифе 0,5 мм2. Если размер зерна в образце выходит за пределы номеров 1–10, то пользуются другими увеличениями.
102

Рис. 3.38. Фрагмент эталонной шкалы для определения величины зерна (ГОСТ 5639–82)
Метод подсчета числа зерен. Выбирают характерное поле, которое ограничивают окружностью диаметром 79,8 мм (рис. 3.39). Общее число зерен на площади поверхности 0,5 мм2. Подсчитывают по формуле m100 = n1 + 0,5n2 для круга, где n1 – число зерен внутри выбранной фигуры, а n2 – число зерен, пересеченных ее границами. Число зерен, приходящихся на 1 мм2 площади поверхности шлифа, m = 2n100, при этом n100 должно быть не менее 50. Подсчет зерен проводят не менее чем в трех характерных полях зрения и определяют среднеарифметическое значение. Среднюю площадь сечения зерна (а) и средний диаметр (d) определяют по формулам: a = 1/m; d = 1/√m.
Рис. 3.39. Схема подсчета числа зерен по площади
103
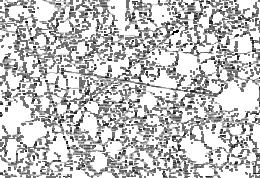
Метод подсчета пересечений границ зерен (рис. 3.40). На микро-
фотографии проводят несколько отрезков произвольной длины, каждый из которых пересекает не менее 10 зерен. Средний условный диаметр зерна определяют по формуле d = L/N.
Рис. 3.40. Схема подсчета числа зерен по пересечению границ
Для количественной оценки зеренной структуры и степени разнозернистости применяют статистические методы и строят кривые распределения или гистограммы. Для построения гистограмм определяют число зерен в различных размерных группах, для которых длина хорд, полученных при пересечении зерен прямыми линиями, находится в пределах определенного числа делений шкалы микрометра. Рекомендуется величины линейных размеров в группах представить в виде геометрической прогрессии с коэффициентом 1,45. В этом случае размерные группы соответствуют номерам эталонной шкалы. Общее количество измерений зависит от однородности величины зерна, требуемой точности и достоверности результатов. На основе построенной по этим данным кривой распределения подсчитывают по соответствующим формулам средний условный диаметр зерна, среднюю площадь и другие статистические параметры распределения.
3.5.2.2. Электронная микроскопия
Возможности световых микроскопов ограничены волновой природой света. При оптимальных условиях световые микроскопы позволяют наблюдать объекты, вследствие явления дифракции не менее 1/3 длины световой волны. Дальнейшее проникновение в мир малых величин стало возможным лишь при использовании в микроскопии электронных лучей, обладающих более короткими длинами волн, чем длины волн световых лучей.
104

Приборы, в которых получают увеличенное изображение с помощью электронных пучков, называются электронными микроскопами
(рис. 3.41).
Рис. 3.41. Общий вид просвечивающего электронного микроскопа
Libra-200FE фирмы Carl Zeiss
Электронная микроскопия высокого разрешения развивалась сравнительно медленно. Поколение приборов 50-х гг. имело разрешающую способность ~2 нм, 70-х – до 0,3 нм. Разработка микроскопов с ускоряющим напряжением 300–400 кВ открыла возможность для дальнейшего увеличения их разрешающей способности. К 80-м гг. разрешающая способность была уже 0,2 нм, к 90-м – 0,15 нм и менее. В электронных просвечивающих микроскопах (ПЭМах) диаметр электронного луча составляет 0,1 нм.
Электронно-лучевая пушка (рис. 3.42) с термоэмиссионным или электрополевым катодом испускает поток электронов, который формируется вупорядоченный пучок с помощью магнитных линз, играющих роль конденсоров в оптической системе. Фокусировка осуществляется изменением тока в магнитных катушках. Пучок проходит через образец, собирается магнитной объективной линзой, а затем с помощью проекционных линз подается на люминесцентный экран. Все устройство размещается в колонне, откачиваемой до высокого вакуума, в миллиард раз меньше атмосферного. Образец в виде тонкой фольги изготовляется путем шлифовования и последующего электролитического полирования. В качестве образца могут быть использованы угольные реплики. ПЭМ может работать в двух
105
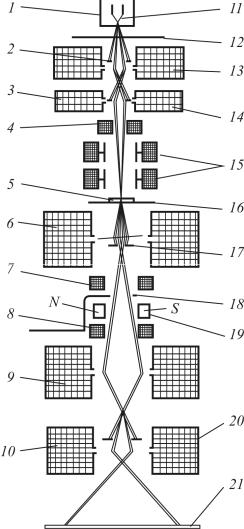
режимах: получение изображения образца и дифракционной картины. Изображение формируется вследствие того, что разные атомы рассеивают и поглощают электроны с различнойэффективностью.
Рис. 3.42. Оптическая схема электронного микроскопа: 1 – фокусирующий электрод; 2 – диафрагма первого конденсора; 3 – диафрагма второго конденсора; 4 – стигматор второго конденсора; 5 – объект; 6 – объективная линза; 7 – стигматор объективной линзы; 8 – стигматор промежуточной линзы; 9 – промежуточная линза; 10 – диафрагма поля зрения; 11 – катод; 12 – анод; 13 – первый конденсор; 14 – второй конденсор; 15 – призмы для юстировки осветителя; 16 – столик объектов; 17 – апертурная диафрагма; 18 – селекторная диафрагма; 19 – механизм
юстировки объектива; 20 – проекционная линза; 21 – экран
106
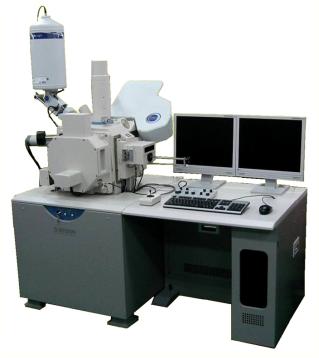
Электронную микрофотографию получают в условиях, когда апертурная диафрагма вырезает из общего потока только центральный пучок. Они могут дать сведения о форме и размерах отдельных зерен, фаз и других структурных единиц.
Растровая (сканирующая) электронная микроскопия основана на рас-
сеянии электронов на потенциальном рельефе поверхности и приповерхностных слоев твердого тела. Он позволяет получить изображение дефектов, расположенных как на поверхности исследуемого образца, так и на глубине в доли микрона под ней. Вид растрового электронного микроскопа и схема устройства представлены на рис. 3.43, 3.44 соответственно.
Рис. 3.43. Сканирующий электронный микроскоп Hitachi S-3700N
Изображение в растровом микроскопе строится путем перемещения (сканирования) сфокусированного электронного луча по поверхности образца. Синхронно на мониторе по экрану движется луч, формирующий изображение. Яркость изображения модулируется сигналом приемника. Ввиду своей многофункциональности и универсальности растровые микроскопы получили большее распространение, чем просвечивающий электронный микроскоп.
107

Наряду с прошедшими электронами можно регистрировать множество других эффектов из облучаемой зоны: эмиссию света, тормозное
ихарактеристическое рентгеновское излучение, отраженные вторичные
иОЖЕ-электроны, разность потенциалов на противоположных сторонах образца.
Рис. 3.44. Схема устройства растрового электронного микроскопа: 1 – электронная пушка; 2 – конденсор; 3 – отклоняющая система; 4 – конечная линза с корректором астигматизма; 5 – объектный столик; 6 – образец; 7 – вакуумная система; 8 – генератор разверток; 9 – блок управления увеличением; 10 –селектор сигналов (для выбора регистрируемого вторичного излучения); 11 – видеоусилитель; 12, 13 – ЭЛТ и ее отклоняющая система; BИ1–BИ3 – потоки вторичных излучений; C1–C3 – электрические сигналы; Д1–Д3 – детекторы; ЭЛ1, ЭЛ2 – электронные
лучи; X, Y – направления сканирования (строчная и кадровая развертки)
Зондом в РЭМ является электронный луч диаметром обычно 1 мкм, в лучших образцах – до 1 нм, а разрешение – около 7–10 и 1 нм соответственно.
Предельное увеличение в 150 000–200 000 крат при чрезвычайно большой глубине резкости. При взаимодействии электронов с веществом в условиях работы РЭМ основными являются неупругие столкновения падающих электронов с электронами образца и упругие столкновения с ядрами атомов. Наиболее универсальное значение имеют реги-
108
страция вторичных электронов и регистрация отраженных электронов. Те и другие электроны улавливаются коллектором, установленным около образца, преобразуются в электрический сигнал, который усиливается и направляется к электронно-лучевой трубке, где он модулирует яркость электронного луча.
Изображение во вторичных электронах дает высокое разрешение – на порядок более высокое, чем оптический микроскоп.
В каждом из этих сигналов содержится независимая информация об облучаемой зоне. Растровая микроскопия позволяет исследовать микрорельеф, локальный химический состав, распределение отдельных элементов по образцу, дает возможность получать снимки с большой глубиной резкости.
Наиболее простые микроскопы с успехом могут заменить оптические, поскольку разрешение у них на порядок больше и одновременно проводятся фазовый и поэлементный анализы. Применение электронной просвечивающей микроскопии сдерживает сложная и трудоемкая подготовка образца, в результате чего их свойства могут измениться; возможны радиационные повреждения, необходимость высокого вакуума, высокая стоимость прибора (до 1 млн долл.). В растровых микроскопах часть этих ограничений снимается.
Сканирующие зондовые микроскопы (СЗМ) появились как приборы для изучения наноструктур и как инструмент, используемый в нанотехнологиях (рис. 3.45). За короткое время число разновидностей сканирующих микроскопов приблизилось к 20.
Общими конструктивными узлами и компонентами всех сканирующих зондовых микроскопов являются следующие элементы:
–зонд, обычно выполненный в виде иглы с радиусом закругления от единиц до десятков нанометров;
–пьезосканер, позволяющий перемещать зонд с точностью ~0,01– 0,001 нм;
–цепь обратной связи между полезным сигналом с зонда и устройством (пьезоактуатором), определяющим его положение;
–столик, позволяющий менять область исследования на образце;
–электронный блок, который управляет всеми циклами;
–программное обеспечение, с помощью которого обрабатывается сигнал и строится изображение на мониторе компьютера;
–виброзащитный стол.
109
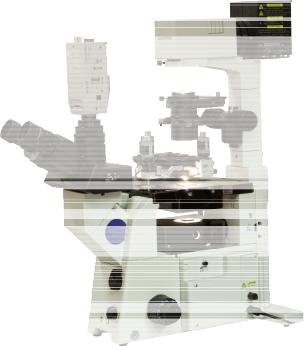
Рис. 3.45. Сканирующий зондовый микроскоп Certus Optic I
Принципиальная схема сканирующего зондового микроскопа представлена на рис. 3.46.
Возможности сканирующих зондовых микроскопов многообразны. СЗМ позволяет:
–измерять твердость и модуль Юнга;
–выявлять сопротивление чистоупругому локальному деформированию;
–выявлять критическую нагрузку перехода из чисто упругой в упругопластическую область;
–измерять энергию, поглощаемую в контактном взаимодействии;
–определять упругопластические характеристики материала;
–определять KIС;
–моделировать процесс усталости;
–оценивать пористость материала;
–исследовать превращения;
–судить о структуре многофазных и градиентных материалов;
–оценивать анизотропию;
–определять толщину и степень адгезии слоев.
110