
ОБЕСПЕЧЕНИЕ ЭКСПЛУАТАЦИОННОЙ НАДЕЖНОСТИ МЕТАЛЛОКОНСТРУКЦИЙ КОНВЕЙЕРОВ
2.1. ОСОБЕННОСТИ ЭКСПЛУАТАЦИИ МЕТАЛЛОКОНСТРУКЦИЙ В СУРОВЫХ КЛИМАТИЧЕСКИХ
УСЛОВИЯХ
Эксплуатация конвейеров в суровых климатических усло виях характерна для карьеров горных предприятий Северного Урала, Сибири и Востока. Подвижность горного оборудования в процессе разработки открытых месторождений в карьерах ведет к тому, что конвейеры комплексов непрерывного дейст вия постоянно работают на открытой местности, часто без лег ких навесов. Линейная часть конвейера в течение всего года подвергается воздействию солнца, ветра, пыли, осадков и осо бенно отрицательных температур в зимнее время. Темпера тура воздуха на угольных разрезах Северного Урала колеб лется от +40 до —47 °С. При низких температурах происхо дит намерзание транспортируемого материала и пробуксовка ленты, затрудняется работа обслуживающего персонала, увели чиваются затраты мощности. В зимние месяцы количество вне плановых простоев конвейеров на карьерах возрастает до
200%.
Всвязи с вводом в действие комплексов непрерывного дей ствия для разрезов большой производственной мощности (на пример, в условиях Канско-Ачинского топливного энергетиче ского комплекса) вопрос о повышении надежности работы кон вейеров при низких температурах стал особенно актуальным. Для проектируемой конвейерной линии производительностью
5000 м3/ч (при ширине ленты 1600 мм и скорости движения 4,5 м/с), устанавливаемой с навесом и ограждением от раз реза «Березовский» до Березовской ГРЭС № 1, расчетная тем пература воздуха в наиболее холодную пятидневку составляет —41 °С. Средняя температура воздуха в холодный период со ставляет —22 °С, продолжительность снежного покрова и ме телей— соответственно 5,5 мес и 300 ч [1]. Предложения по решению данной проблемы сводятся к двум вариантам. Боль шинство специалистов, ссылаясь на опыт эксплуатации лен точных конвейеров на Коркинском разрезе, в производствен ных объединениях «Вахрушевуголь» и «Александрияуголь», на карьерах в Канаде, считают возможным нормальную эксплуа тацию конвейеров при температурах до —45 °С, используя для этого морозостойкие ленты и смазки, местный прогрев привод ных блоков, микропривод для обеспечения постоянной замед-
ленной работы конвейера на холостом ходу, растворы для уменьшения намерзания груза на ленту, механизированные средства уборки просыпи. Металлоконструкции става конвей ера также должны отвечать определенным требованиям. На пример, частота поломок нагружаемых деталей экскаватора за метно возрастет с понижением температуры от —15 °С и при температуре —40 °С в 4—5 раз больше, чем при положитель ных температурах [7]. Предлагается применять вместо обыч ных углеродистых сталей, имеющих повышенную хрупкость, легированные стали с мелкозернистой структурой, содержащие марганец, никель, медь. В этом отношении интересен опыт эксплуатации конвейеров, транспортирующих нефтеносный пе сок в карьерах Канады при температурах до —55 °С. Здесь наряду с морозостойкими лентами и смазками, инфракрасным обогревом барабанов и микроприводом для прокручивания ленты при отсутствии груза в металлоконструкции конвейера используется специальная легированная сталь с мелкозернистой структурой. К вопросу применения в конвейерах специальных сталей следует подходить осторожно. Опыт эксплуатации кон вейерного комплекса Новокраматорского машиностроительного завода производительностью 5000 м3/ч на разрезе «Морозовский» объединения «Александрияуголь» при температуре
—15 °С признан в целом положительным. Вместе с тем от мечены еще значительные простои на устранение отказов (34 % от календарного времени), значительная доля которых прихо дится на конвейерное оборудование.
Исследования состояния металлоконструкций конвейеров при температурах до —44 °С на Коркинском угольном разрезе, проведенные ИГД Минчермета СССР, показали стойкость их к поломкам. Это объясняется отсутствием высоких кратковре менных нагрузок. Отсюда делается вывод, что при изготовлении конвейеров, предназначенных для работы при низких темпера турах, нет необходимости применять хладостойкие стали [8]. Отмечены также надежная работа морозостойких лент и смазки БНЗ-ЗМ, несущественное влияние низких температур на производительность конвейера и потребляемую мощность. Оснащение конвейеров оборудованием, стойким к воздействию окружающей среды в районах с умеренным климатом, соответ ствует климатическим исполнениям У1 и У2 (с использованием навесов и ограждений), а в северных районах — исполнениям ХЛ1 и ХЛ2 (ГОСТ 15150—69). По данным Сызранского тур бостроительного завода стоимость конвейерного оборудования с лентой шириной 1600—2000 мм в исполнении ХЛ2 в 1,3 раза, а эксплуатационные расходы в 1,2 раза выше, чем при обыч ном исполнении У4.
Другой вариант связан с установкой конвейеров, имеющих обычное исполнение (УЗ, У4, У5), в неотапливаемых или отап ливаемых галереях, предохраняющих оборудование от воздей ствия окружающей среды и низких температур. Для конвейе
ров с лентой шириной 400—1600 мм применяются неотапли ваемые галереи серии 3.016-1 (с ограждающими конструкци ями из волнистых асбестоцементных листов) и 3.016-2 (с само несущими асбестоцементными оболочками), а также отапли ваемые галереи серии ИС-01-15 для конвейеров с лентой шириной 400—2000 мм [9]. Стоимость галерей, особенно отап ливаемых, по данным Промтрансниипроекта значительно превы шает стоимость приобретения и монтажа конвейера (табл. 2.1).
Поэтому выбор типа укрытия для магистральных ленточ ных конвейеров повышенной протяженности и производитель ности для районов с суровым климатом имеет принципиаль ное значение. Например, для конвейеров с шириной ленты
2000 мм стоимость |
строительства укрытий в исполнении ХЛ2 |
с навесом на 38 % |
меньше, чем в исполнении У4 с отапливае |
мой галереей, а эксплуатационные расходы отличаются не значительно. Приведенные затраты по первому варианту на 16f% меньше, чем по второму. Однако следует иметь в виду,
что машинное время |
работы |
конвейеров |
в |
исполнении |
ХЛ2 |
в условиях сурового |
климата |
ниже, чем |
в |
исполнении |
У4 |
(5500 ч в год по сравнению с 7500 ч). Этот фактор может по влиять на решение вопроса о резервировании конвейерной линии. При установке резервной конвейерной линии более эко номичен вариант с использованием укрытия в виде отапливае мой галереи. По данным ИГД Минчермета СССР экономи чески целесообразна установка конвейеров в суровых клима тических условиях в неотапливаемых галереях или только с навесом на открытом воздухе, когда это допустимо по горно геологическим условиям.
Таким образом, при проектировании конвейерных линий при выборе типа укрытия должны учитываться технические и эко номические показатели, условия обслуживания конвейеров, дли тельность, надежность и уровень их эксплуатации, возможность получения оборудования соответствующего исполнения. Промтрансниипроектом на основе методики П. И. Коха и В. Л. Ореш
кина предложена балльная |
система выбора |
типа укрытия ста- |
|||||
|
|
|
|
|
|
ТАБЛИЦА 2.1 |
|
|
Стоимость |
Стоимость строительства укрытий, тыс. руб/км |
|||||
|
|
|
Неотапли |
Неотапли |
Отапли |
||
Ширина |
приобретения |
Навес |
|||||
и монтажа |
ваемая |
ваемая |
ваемая |
||||
ленты, мм |
с односто |
||||||
конвейера, |
галерея |
галерея |
галерея |
||||
|
ронним |
||||||
|
тыс. руб/км |
серии |
серии |
серии |
|||
|
ограждением |
||||||
|
|
3. 016-1 |
3. 016-2 |
ИС-01-15 |
|||
|
|
|
|
||||
800 |
120 |
64,6 |
|
364,6 |
198,4 |
604,4 |
|
1000 |
148 |
70,0 |
|
364,6 |
245,5 |
681,0 |
|
1200 |
225 |
75,8 |
|
460,5 |
245,5 |
681,0 |
|
1400 |
287 |
81,9 |
|
460,5 |
245,5 |
760,0 |
|
1600 |
478 |
90,0 |
|
460,5 |
245,5 |
760,0 |
|
2000 |
690 |
99,0 |
|
— |
— |
828,2 |
ционарных конвейеров, имеющих круглогодичный режим ра боты. При выборе типа укрытия учитываются температура воз духа, длина и проектная производительность конвейера, вид
транспортируемого материала, скорость ветра |
и |
число ниток |
в конвейерной линии (см. СНиП П-А.6—72). |
В |
зависимости |
от значений параметров назначается определенное число бал лов (табл. 2.2).
При сумме баллов, равной 50—55, 56—100 и более 100, выбирают соответственно в качестве укрытия навес (или навес с ограждением со стороны преобладающих ветров), закрытую неотапливаемую галерею и закрытую отапливаемую галерею. Предложенные рекомендации не распространяются на транс портные системы обогатительных фабрик.
Преимущество галерей побуждает |
к разработке новых кон |
струкций для снижения их стоимости, |
материалоемкости, массы, |
износа, компактности, трудоемкости |
монтажа. Тяжелые асбес |
тоцементные |
конструкции |
заменяются |
пластмассовыми, |
из |
|||||
|
|
|
|
|
|
|
|
ТАБЛИЦА12.2 |
|
Исходные |
|
Пределы изменения параметра (1-я строка) |
|
||||||
параметры |
|
|
и число баллов (2-я строка) |
|
|
||||
Средняя темпера |
—5 |
—10 |
—15 |
—20 |
—25 |
—30 |
—35 |
Ни |
|
тура |
воздуха |
10 |
20 |
30 |
40 |
50 |
60 |
70 |
же |
в наиболее холод |
|
|
|
|
|
|
|
- 3 5 |
|
ный период года, |
|
|
|
|
|
|
|
80 |
|
°С |
|
|
|
|
|
|
|
|
|
Длина |
конвейер |
До 2 |
До 4 |
До 6 |
До 8 |
До 10 |
Более |
|
|
ной линии, км |
1 |
2 |
3 |
4 |
5 |
10 |
|
|
|
|
|
7 |
|
|
Проектная |
про |
До 5 |
До 10 |
До 15 |
До 20 |
Более |
изводительность |
5 |
10 |
15 |
15 |
20 |
|
конвейерной |
ли |
25 |
||||
нии, млн. т/год |
|
|
|
|
|
___
— |
___ |
___ |
Крупность транс |
Мелкосыпучие |
Среднекус |
Крупнокусковые |
|||||
портируемого ма |
|
материалы |
|
ковые |
материалы 25 |
|
||
териала |
|
5 |
|
материалы 10 |
|
|
|
|
Средняя скорость |
До 5 |
До 10 |
Более |
___ |
_ |
_ |
_ |
__ |
ветра в январе, |
5 |
15 |
10 |
|
— |
— |
— |
|
м/с |
25 |
|
|
|||||
Число ниток кон |
1 |
2 |
— |
—- |
— |
— |
|
|
вейерной линии |
10 |
— |
|
|
гофрированной листовой стали толщиной до 2 мм. Большое внимание уделяется конфигурации галерей и технологии их монтажа при строительстве и ремонтных работах. Все большее внимание привлекают галереи с трубчатым сечением. В США конвейеры для подачи руды на фабриках (с лентой шириной 1375 мм) устанавливаются в трубчатых галереях диаметром 3000 мм, сваренных из стальных листов толщиной 8 мм. Га лереи составляются из отдельных модулей-секций длиной 18 м, изготовленных на заводе металлоконструкций. При монтаже модулей в галерею внутри них устанавливается конвейерное оборудование, после чего модули поднимаются на проектную отметку. Благодаря большой жесткости трубы, поддерживаю щие ее опоры в виде компактных трубчатых стоек с вильча тым верхним основанием для галереи устанавливаются с ша гам 50 м, при этом модули соединяются между собой бол тами. В трубе имеется пешеходный настил и прокладываются коммуникации. Облегчена уборка просыпи подачей под напо ром воды, попадающей затем в систему шламового хозяйства предприятия. Упрощается отопление галерей. Обогреватели монтируются в нижней части галереи, и теплый воздух сам пе ремещается к верху.
Основные преимущества трубчатых галерей: уменьшение стоимости и трудоемкости строительства за счет исключения устройства стен, кровли и совмещения операций монтажа гале реи и конвейера, малое сопротивление ветровым нагрузкам, улучшение компоновки и эксплуатации. Однако отмечается сравнительно большой расход стали. Чтобы уменьшить расход стали, галерею монтируют в виде оболочки из гофрированного стального листа толщиной 1,3—1,6 мм, привариваемой к пло скому стальному основанию и оснащаемой внутри поперечными балками и вертикальными стойками для монтажа конвейерного оборудования.
2.2. ОСОБЕННОСТИ ЭКСПЛУАТАЦИИ МЕТАЛЛОКОНСТРУКЦИИ ПРИ ДОСТАВКЕ
КРУПНОКУСКОВЫХ СКАЛЬНЫХ ПОРОД И РУД
Технические возможности мощных ленточных конвейеров за последние годы расширились благодаря внедрению маги стральных конвейеров тяжелого типа с лентой шириной 1600, 2000 мм, разработанных ВНИИПТмашем и Сызранским тур бостроительным заводом. Они предназначены для доставки кусковых скальных пород и руд крупностью до 500 мм из глу боких карьеров на перегрузочные пункты и обогатительные фабрики. В проектах конвейеров тяжелого типа с жестким ставом предусмотрены три типа роликоопор: жесткие, подвес ные и амортизирующие. Опыт эксплуатации конвейеров тяже лого типа за 15 лет подтвердил общую их работоспособность при производительности до 2000 т/ч, скорости движения ленты
3,15 м/с, крупности груза до 400 мм и массе отдельных кусков до 70 кг. Превышение этих параметров приводит к резкому увеличению износа металлоконструкций, ленты и роликов, в ре зультате чего снижается надежность работы конвейеров. При менение современной технологии буровзрывных работ, повыше ние предела крупности транспортируемой горной массы с 400 до 700 мм, скорости движения ленты до 5 м/с, производительно сти до 6000 т/ч позволит значительно снизить капитальные к эксплуатационные расходы по доставке скальных пород и руд. Реальность достижения таких параметров подтверждается дан ными эксплуатации конвейеров с податливой конструкцией ли нейной и загрузочной частей ставов.
К современным металлоконструкциям линейной части кон вейера, транспортирующего крупнокусковую горную массу, предъявляются следующие требования: высокая прочность; амортизирующая способность при больших динамических на грузках; устойчивость, малые металлоемкость и трудоемкость монтажа, унификация; удобство доставки и обслуживания. Ра боты по созданию металлоконструкций, конвейеров, отвечаю щих поставленным требованиям, ведутся в следующих на правлениях:
конвейеры с канатным ставом и жесткими подвесными ротикоопорами;
конвейеры с канатными ставами и шарнирными подвесными роликоопорами;
конвейеры с комбинированным ставом (жестким и канат ным) и жесткими роликоопорами;
конвейеры с опорами скольжения для ленты [10].
Переход к эксплуатации ленточных конвейеров с канат ными ставами и опорами скольжения требует тщательного рас чета и выбора конструктивных параметров канатов, опорных стоек, опор скольжения.
2.2.1. КОНВЕЙЕРЫ С КАНАТНЫМ СТАВОМ И ЖЕСТКИМИ ПОДВЕСНЫМИ РОЛИКООПОРАМИ
На угольных шахтах СССР успешно эксплуатируются лен точные конвейеры с канатным ставом и жесткими подвесными роликоопорами, имеющими жесткое соединение роликов между собой и изготавливаемыми Краснолучским и Александровским машиностроительными заводами. Основное достоинство кон вейеров — малые трудоемкости монтажа и металлоемкость, снижение ударных нагрузок на ленту и ролики. Они пред назначены для доставки угля крупностью до 500 мм и породы крупностью до 300 мм по горным выработкам, имеют горизон тальное (слабонаклонное), уклонное, бремсберговое телескопи ческое и грузолюдское исполнения. Производительность кон вейеров составляет 545—1200 т/ч по углю при ширине и скорости
движения ленты соответственно 1000—1200 мм и 1,6—2,5 м/с, мощности привода 100—500 кВт.
Большинство конвейеров выпускается как для установки на почву (напольные), так и для подвески к кровле (рис. 2.1, а—в). Подвесной став включает два несущих каната, закреп
ляемых на |
головной и концевой станциях |
и подвешиваемых |
||
к кровле выработки |
с помощью регулируемых по |
высоте цеп |
||
ных подвесок. Через |
определенные интервалы устанавливаются |
|||
растяжки |
для обеспечения устойчивости |
става. |
Напольный |
|
|
|
|
рис. |
|
|
|
|
|
|
Ленточный |
конвейер 1Л100К с канатным ставом |
и |
жесткими |
подвесными |
||||||
|
|
|
|
роликоопорами: |
|
|
|
|
||
а ~ иапол9ьное |
исполнение; |
б—в — подвесное |
исполнение: |
|
1 — несущий |
канат; |
2 — |
|||
стопка; о |
датчик |
схода |
ленты; 4 —тросовый |
выключатель; 5 — подвеска из |
цепи; |
|||||
г |
каната, |
~ неподвижный |
блок; |
2-стойка; |
д |
- стяжка для натяжения |
||||
несущего |
/ — зажим; 2 — тяга; |
3 — гайка; 4 —отрезок каната; |
5 — жимок |
став имеет стойки, на которые опираются несущие канаты с верхними роликоопорами и нижние однороликовые роликоопоры. Верхние роликоопоры состоят из трех роликов, соеди ненных скобами с жесткими нешарнирными втулками. Боковые ролики наклонены под углом 30° и с помощью литых втулок и клиньев прикрепляются к несущим канатам. Для натяжения канатов напольного става применяют натяжные стойки с не подвижными и подвижными блоками, перемещаемыми домкра тами при натяжении (рис. 2.1, г). На подвесных ставах обычно используют стяжки с зажимами, жимками, тягами, гайкой и отрезком каната (рис. 2.1, <?). Стяжкой натягивается несущий канат, после чего жимками закрепляется отрезок каната и снимается стяжка.
Надежность работы конвейеров во многом зависит от натяжения канатов, шага установки опорных стоек. Отклоне ние этих параметров от оптимальных приводит к неравномер ному нагружению канатов и подшипников роликоопор, сходу ленты, возникновению колебаний. По рекомендациям ДонУГИ и Донгипроуглемаша, требуемое натяжение канатов определя ется по условиям контакта ленты с роликоопорой:
|
|
|
|
|
(2.1) |
где 5 к — требуемое |
натяжение |
каната, |
Н; |
S — натяжение |
|
ленты, Н; т р — масса роликоопоры, кг; |
/ — расстояние между |
||||
роликоопорами, м; |
qK— масса |
1 |
м каната, кг; |
qn— масса 1 м |
|
ленты, кг. |
|
задается определенное натяже- |
|||
Заводами-изготовителями |
нце канатов, которое должно быть создано при монтаже и поддерживаться при эксплуатации. Заданное натяжение кана тов можно контролировать сравнением фактического макси мального прогиба каната между стойками с расчетным значе нием, определяемым по формуле
g (mp/f + 2<ук) l\ |
|
(2.2) |
|
где бп — фактический максимальный |
прогиб |
канатов между |
|
стойками, м; g — ускорение свободного падения, |
м/с2; /с — рас |
||
стояние между стойками, м. |
значению |
еп |
получают не |
При контроле SK по расчетному |
сколько завышенное натяжение канатов, что положительно сказывается на работе става и роликоопор. Считается опти мальным, если прогиб каната составляет сотую долю от рас стояния между стойками и меньше. Шаг между стойками реко мендуется выбирать равным удвоенному расстоянию между ро ликоопорами, расположенными симметрично относительно стоекПри изменении натяжения канатов нагрузка на роликоопоры распределяется равномерно. Диаметр каната выбирается как
функция от максимального рабочего натяжения с учетом ко эффициента динамичности, суммарного разрывного усилия всех проволок каната и запаса прочности, равного 3—3,5.
Обследования работы конвейеров с канатным ставом и жест кими подвесными роликоопорами на угольных шахтах Дон басса выявили ряд недостатков и определили направления их дальнейшего совершенствования [11]. Для одинаковых условий работы параметры ставов изменяются в широких пределах. Расстояния между стойками составляют 3—5 м, а число роликоопор между ними 2—4. Диаметр канатов практически одина ков для всех конвейеров (22—23 мм). Натяжения обоих кана тов неравномерны до 50 % и не достигают номинальных значений (в некоторых случаях только 20 % номинального натяжения в 40—50 кН). Стойки недостаточно устойчивы, в результате чего происходит их опрокидывание. Устройства для натяжения канатов имеют малый ход. Отсутствует прибор для постоян ного контроля натяжения канатов. Необходимо предусматри вать установку указателей натяжения канатов, например ди намометров. Регулировка натяжения канатов осуществляется при полностью загруженном конвейере.
2.2.2. КОНВЕЙЕРЫ С КАНАТНЫМ СТАВОМ И ШАРНИРНЫМИ ПОДВЕСНЫМИ РОЛИКООПОРАМИ
Для доставки тяжелых крупнокусковых грузов (скальных пород и руд) предпочтительно применение конвейеров с канат ным ставом и шарнирными подвесными роликоопорами. Си стема канаты — подвесная шарнирная роликоопора имеет боль шую податливость, обусловленную возможностью изменения геометрии провисания роликоопор. Наибольшая податливость проявляется на участках расположения шарниров. В СССР раз работаны, выпускаются серийно и опытными партиями лен точные конвейеры с канатными ставами и подвесными шар нирными роликоопорами, имеющими производительность 600— 1500 т/ч при ширине и скорости движения ленты соответст венно 1000—1200 мм и 2,34—2,58 м/с, мощности привода 132— 150 кВт.
Конвейер КЛЗ-600 предназначен для транспортирования угля, калийных солей и других материалов крупностью до 400 мм. Линейная часть конвейера имеет два несущих каната, опирающихся на Н-образные стойки. К канатам подвешива ются трехроликовые роликоопоры с упругим (шарнирным) соединением роликов. Для плавного перехода ленты от привод ной станции к линейной части имеются стойки с телескопиче скими опорами.
Конвейер КЛШ-800 с канатным ставом и подвесными шар нирными роликоопорами, выпускаемый Артемовским машино строительным заводом, служит для транспортирования куско-
26
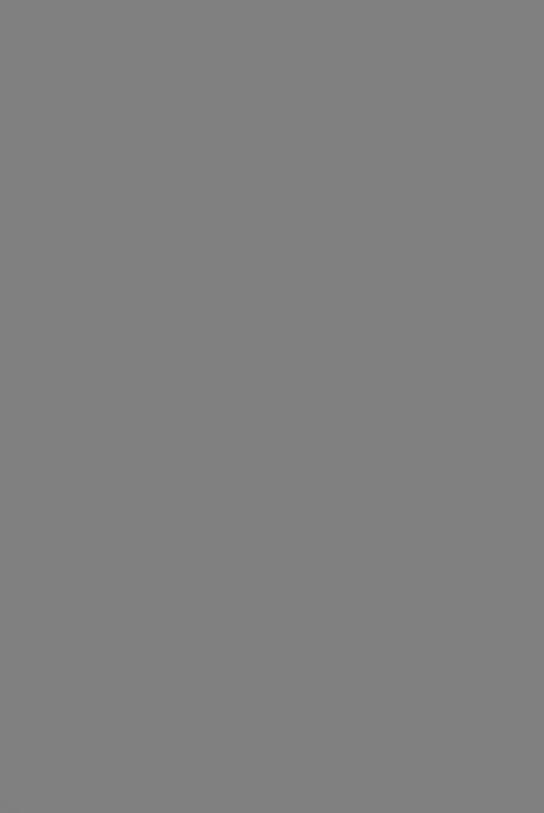
.происходят в резонансном режиме. Работа конвейера при та ком режиме недопустима из-за увеличения сопротивления дви жению и потери устойчивости ленты, повышенных нагрузок на стойки и канаты. Применяют одновременно четыре несущих каната (рис. 2.2, б). Все ролики роликоопоры расположены в шахматном порядке и опираются своими осями на канаты посредством крюкообразных зажимов. Средние канаты присое диняются к поперечинам, устанавливаемым на расстоянии
.30—40 м друг от друга, и натягиваются винтовыми стяжками. Аналогичный по компоновке канатов и роликов став разрабо тан и испытан Киевским политехническим институтом. Став •опытного конвейера состоит из трех линейных секций длиной по 50 м и загрузочной секции длиной 4 м. Каждая линейная секция содержит четыре параллельно натянутых каната, оги бающих концевые блоки. В промежутке между концевыми блоками крайние канаты поддерживаются стойками, установ ленными с шагом 3 м. При транспортировании тяжелых руд возможно дополнительное крепление канатов к консольным стойкам, приваренным к продольным швеллерам в промежут ках между стойками. По высоте канаты расположены так, что при навеске на них роликов образуется желобчатая роликоопора с углом наклона боковых роликов 25° Натяжение ка натов производится винтовыми натяжными устройствами. Шаг установки роликов 1 м. Конвейер был применен на Гниваньском карьере при транспортировании крупнокускового гранита. Он работает бесшумно, удобен для осмотра и обслуживания, не было случаев выброса материала с конвейера. Металлоем кость конвейера на 25—30 % меньше обычного, а срок службы ленты увеличился в 2 раза. К недостатку конвейера можно от нести большую трудоемкость работ, связанную с повторной регулировкой натяжения канатов через 1—2 мес эксплуатации. В этом случае требуются демонтаж ленты и роликоопор, про филактика элементов натяжных устройств. После повторной регулировки натяжения канатов канатные ставы работают до
капитального ремонта. |
возникновение |
колебательного режима |
|
Наиболее |
вероятно |
||
на канатном |
ставе в |
момент подхода |
крупных кусков груза |
к роликоопорам, когда имеют место значительные ударные на грузки. Чтобы исключить это явление, к опорным стойкам шарнирно крепятся коромысла с помощью крюка и звена цепи. На концах коромысел между щеками установлены блоки для поддержания несущих канатов става (рис. 2.2, в). Если пере мещается однородный грузопоток, став и вся система коромы сел находятся в равновесии. При подходе более нагруженных участков ленты к первой паре роликоопор последние просе дают, поворачивая коромысло относительно крюка в свою сто рону. Куски груза проходят по этим роликоопорам, не ударяя по ним. В момент подхода кусков груза ко второй паре роли коопор коромысло поворачивается в их сторону, роликоопоры
28
проседают и сглаживают ударные нагрузки. Повороты коро мысла происходят до тех пор, пока нагрузка на роликоопоры справа и слева от оси поворота коромысла не сравняются. Та ким образом, происходит непрерывное автоматическое вырав нивание нагрузок на все роликоопоры. Благодаря коромыслам, канатный став имеет по длине более равномерную поперечную жесткость. Уменьшаются предварительное натяжение канатов и резонансные явления.
Конвейеры с канатными ставами и шарнирными роликоопорами эксплуатируются на многих горных предприятиях
страны, |
например |
на карьерах |
по добыче |
калийной соли |
||
в |
г. Солигорске |
(КЛЗ-600), на |
Зангезурском медно-молиб |
|||
деновом |
комбинате (конвейеры |
|
конструкции |
УкрНИИпроекта |
||
с |
пятироликовыми |
подвесными |
шарнирными |
роликоопорами). |
В результате их применения достигнуто снижение металлоем кости конструкций в несколько раз, увеличение срока службы ленты до 50%, уменьшение просыпей и увеличение надеж ности работы конвейеров.
УкрНИИпроектом предложены зависимости для выбора ос новных параметров канатных ставов с подвесными роликоопо рами [12]. Для конвейера с двухканатным ставом нагрузка на
1 м каната в вертикальной плоскости (рис. 2.2, г) |
|
|||
, к. в = , к + ^ - |
+ ^ |
+ ^ |
, |
(2.3) |
где <7г — масса груза, приходящаяся на |
1 м ленты. |
|
||
Прогиб каната в вертикальной плоскости принимается рав |
||||
ным 1,5—2 % расстояния между стойками /с: |
|
|||
еп. в = (0,015 4-0,02)/с. |
|
(2.4) |
||
Для обеспечения расчетного |
прогиба |
натяжения в |
канате |
|
S K = <7к.в^с/(88п. в). |
|
(2.5) |
||
Разрывное усилие каната |
|
|
|
|
S K . р ^ |
/IK S K , |
|
|
(2.6) |
где Як— запас прочности каната (принимается равным |
4—5). |
|||
Для горизонтальной плоскости |
|
|
|
|
= |
+ |
|
|
(2-7) |
где ар — угол наклона бокового |
ролика |
трехроликовой |
роли |
|
коопоры. |
|
|
|
|
Прогиб каната в горизонтальной плоскости |
|
|||
бп. г= Як. TIJ&SK* |
|
(2.8) |
29
При установке распорок, препятствующих сближению кана тов в горизонтальной плоскости,
еп. г = ?к. г (/c/2)2/8SK. |
(2.9) |
Вертикальная составляющая усилия на стойку линейной секции от каната в направлении реакции подвесной роликоопоры
Рк.ъ= [(2?к + Ял |
Яг) U+ 4 тр + /71р. с] 0,5, |
(2.10) |
где т р. с — масса распорки. |
|
|
Горизонтальная составляющая усилия |
|
|
Рк. г = |
Рк. eCtg Otp. |
(2.11) |
Результирующее усилие на стойку |
|
р«=л/ р1. в+ р1.г. |
(2.12) |
|
Условие прочности трубчатой стойки в сечении |
А —А (см. |
|
рис. 2.2,в): |
|
|
ос = |
Рк.гМс, < [<Тс]) |
(2.13) |
Гс |
2/ с |
|
где ас — усилие на единицу площади сечения стойки; Fc— пло щадь сечения стойки; hK— расстояние от каната до более опас ного сечения стойки; dc— диаметр стойки; / с — момент инер ции стойки.
На крайние стойки секции, кроме того, действуют усилия от натяжения в канатах, отклоняемых для закрепления с основа
нием: |
|
|
|
|
Рк. о = 2SKsinap. |
(2.14) |
|
С учетом (2.14) |
условие прочности стойки в сечении |
А—А |
|
<ТС= |
Рк. в+_Рк.о + |
Рк. М < [Стс1< |
(2.15) |
|
Fс |
2 /с |
|
2.2.3. КОНВЕЙЕРЫ С КОМБИНИРОВАННЫМ СТАВОМ
При транспортировании кусковых скальных пород и руд крупностью свыше 500 мм трудно обеспечить одновременно вы сокие податливость и устойчивость канатного става с подвес ными роликоопорами. Этот недостаток устранен в комбиниро ванных ставах, в которых для опоры роликов используют ка наты и жесткие элементы из проката. Комбинированные ставы выполняют из отдельных самостоятельных секций, которые можно использовать как на линейной, так и на загрузочной частях конвейера.
Комбинированный став разработан и испытан ВНИИПТмашем на конвейерном стенде с лентой шириной и скоростью движения соответственно 1600 мм и 1—2,5 м/с и с грузом массой 500 кг (рис. 2.3,а). Он включает в себя зам кнутую раму с продольными балками и уравнительными бло-
1 I |
|
|
|
|
|
|
|
5 1 |
|
г |
|
з |
k 5 |
|
|
t / ~ Ah |
i |
a |
|
_ |
— |
— -vf— f — 1VI---------V-WB-----r----- |
|||||||
|
|
: PTl |
f r y |
HHI |
|
|
|
|||||||
|
- ! ~ £l /_- iе8 . 9 11 |
|
_ J |
|
|
|
||||||||
|
|
. |
|
m |
|
щ |
||||||||
3 |
|
|
C |
U |
|
|
|
|
— DSJ--------------ffl |
|
|
|
||
#гг\. |
|
|
|
|
|
|
|
=-7ES— |
|
|
; |
|||
|
|
|
|
|
|
|
|
|
|
8 |
7 |
|
6 |
|
в |
|
|
2 |
1 |
|
|
|
|
|
|
|
|
|
|
|
|
|
|
j f N |
J |
|
|
|
|
|
|
|
|
|
|
|
|
|
5 ^ |
|
|
|
|
|
|
|
|
|
|
|
|
9 W |
6 ^ |
7 |
8 |
|
|
|
|
|
|
|
|
|
|
|
|
|
1 |
f |
|
_i_ |
|
|
|
|
|
|
|
|
|
|
|
1 |
|
|
I |
|
|
|
|
|
|
|
Ленточные конвейеры с комбинированным ставом:
/ — рама; |
|
а — секция става |
с |
уравнительными |
блоками: |
|
|
|
|
|||||
2 — ролики; 3 — канаты; 4 |
— уравнительный блок; |
5 — натяжное устройство; |
||||||||||||
б — став |
с |
повышенной |
податливостью: / — рама; |
2 — канаты; |
3 — ролики; |
4 — упру |
||||||||
гая связь; |
5— жимок; |
6 — стойка; |
7 — натяжное |
устройство; |
8 —скоба; |
в — став |
||||||||
с единой системой компоновки и натяжения канатов: |
/ — шпалы; |
2 |
— рельсы; 3 — |
|||||||||||
стойки; 4 — поперечины; |
5 — шарнирная |
подвеска; |
б — ролики; |
7 — канаты; 3 — муфта; |
||||||||||
2 — коромысло с блоками |
и винтом; |
10 — гайка; |
г — став |
с |
рамками |
для |
роликов: |
|||||||
/ — ролики; |
2 — рамки; |
3 — канаты; |
д — крепление |
рамки |
ролика |
к |
канату |
посредст |
||||||
|
|
вом упругой |
пластины: |
/ — ролик; |
2 — пластина; |
3 — канат |
|
ками с двумя ветвями канатов, концы которых натянуты винтовым устройством [13]. Стандартные ролики, расположенные в шахматном порядке, крепятся через оси с пазами с помощью шарниров, скоб и фиксаторов к балкам и канатам. Измере ниями установлено снижение динамических нагрузок в 2,0— 3,9 раза на средние ролики податливой секции по сравнению с жесткими роликоопорами, а в сравнении с подвесными шар нирными роликами на жестком ставе — в 1,5—2,8 раза. Подат ливая секция предложена для использования на конвейерах, транспортирующих скальные породы и руды плотностью до 3,5 т/м3, крупностью отдельных кусков 600—900 мм и массой до 500 кг при содержании фракции груза крупностью свыше 300 мм до 60%, скорости движения резинотросовой ленты ши риной 1600 мм до 4 м/с, производительности до 7200 т/ч.
Институтом геотехнической механики АН УССР разработай комбинированный став с повышенной податливостью (рис. 2.3,6). Он включает в себя раму, канаты, средние и боко вые ролики, прикрепленные к продольным канатам при помощи упругой связи и жимков, стойки. Натяжные устройства состоят из опорного швеллера, натяжной скобы и гаек. Оси роликов вы полнены с отверстием для пропуска упругой связи, которая фиксируется от продольных смещений и поворота. Упругая связь бокового ролика прикреплена скобой и гайками к стой кам. Натяжение упругой связи боковых и средних роликов регулируется скобами и гайками. Для увеличения надежности крепления упругой связи с продольными канатами и стойками она выполнена замкнутой для двух боковых роликов, располо женных в одной вертикальной плоскости, а также для двух соседних средних роликов. Под действием ударных нагрузок деформируется сначала упругая связь, а затем продольные ка наты. Из-за податливости роликов в вертикальном и боковом направлениях секцию можно применять на наклонных кон вейерах.
Смещение роликов в плане на канатном ставе с шахматной схемой расположения роликов отрицательно влияет на харак тер деформации ленты и устойчивость системы. В конструкции податливого става производственного объединения «Ждановтяжмаш» ролики в секции монтируют в одной плоскости из-за монтажа двух пар параллельно смонтированных канатов. При этом соседние ролики крепятся к различным канатам, улучшая равновесие системы.
В процессе эксплуатации конвейеров с канатными ставами нарушается равномерность натяжения канатов и изменяется геометрия, расположения роликов на смежных секциях; повы шается сопротивление движению ленты и вращению роликов, снижается надежность работы конвейера. Всесоюзным научноисследовательским институтом нерудных строительных материа лов и гидромеханизации (ВНИИНЕРУД) разработан став с еди ной системой компоновки и натяжения канатов для забойных передвижных конвейеров карьеров (рис. 2.3,в). Каждая секция става имеет шпалы с рельсами и стойки с поперечинами, на ко торых монтируются шарнирные подвески, ролики и канаты. Ка наты в пределах секций соединяются между собой муфтами. Соединение и натяжение канатов смежных секций осуществля ются балансирными стяжными устройствами, состоящими из двух коромысел с блоками на концах, к осям которых крепятся винты с гайкой. При монтаже става секции устанавливаются рядом и ориентируются в одну линию по продольной оси. Ка наты укладываются в желобы блоков. Гайкой винты коромысел собираются в винтовую стяжку. Натяжение любой из стяжек равномерно передается через коромысла на все канаты; уста навливается задание на единое натяжение канатов по всей длине става. Уменьшение или увеличение натяжения достигается вра-
32
щением гайки любой из винтовых стяжек става. Все ролики имеют одинаковый угол наклона. При вытяжке одной из ветвей каната любой секции через коромысла натяжение выравнива ется во всех секциях става. При передвижке конвейера винты гайкой разъединяются, секции устанавливаются и собираются на новом месте. При передвижке конвейера турнодозерами на тяжение канатов только ослабляется и секции в собранном виде перемещаются на новое место.
Одно из направлений конструирования комбинированных секций канатного става связано с установкой серийных роликов в жесткие прямоугольные рамки с пазами (рис. 2.3,г). Облег чаются монтаж и замена роликов, однако увеличиваются метал лоемкость конвейера и динамическая масса роликоопор. Умень шение ударных нагрузок от крупных кусков груза происходит за счет как бокового смещения боковых рамок с роликами, так и опускания средних рамок с роликами.
Уменьшить влияние жесткости рамок на работу секции можно подвеской их к канатам через дугообразные пластины (рессоры). Один конец пластины (рис. 2.3,5) крепится жестко к канату, а другой установлен на канате с возможностью сме щения при действии ударной нагрузки. При соударении крупных кусков груза с роликами последовательно деформируются пла стины и канаты. Подбором жесткости пластины достигают уменьшения колебаний системы.
2.2.4. КОНВЕЙЕРЫ С ОПОРАМИ СКОЛЬЖЕНИЯ ДЛЯ ЛЕНТЫ
Одно из перспективных направлений в области создания но вых конструкций ставов для доставки крупнокусковых руд на добычных участках шахт и рудников — применение опор сколь жения. Для опор скольжения характерны отсутствие вращаю щихся частей, а значит, подшипниковых узлов, систем смазки подшипников, простота конструкции и компактность, уменьше ние образования пыли и просыпи; они надежны в работе. Очень важно, что ставы с опорами скольжения обеспечивают спокой ное (без воздействия ударных нагрузок на ленту) перемещение груза практически неограниченной крупности. Кроме того, сни жаются нагрузки на металлоконструкцию конвейера в целом, улучшаются условия обслуживания конвейера и техника без опасности. К факторам, ограничивающим использование опор скольжения, относятся: повышенная энергоемкость, уменьшение скорости движения и повышенный износ ленты из-за нагрева и трения при скольжении по опорам. Таким образом, достоинства ставов с опорами скольжения наиболее очевидны при неболь шой длине и производительности конвейеров, предназначенных для внутрицеховых перевозок. Коэффициент трения между лен той и опорами скольжения составляет обычно 0,15—0,80, кото рый в 10—30 раз выше, чем в конвейерах с роликоопорами.
2 Заказ № 1462 |
33 |
Срок службы ленты и опор скольжения находится в пределах
6—8 мес.
Повышение эффективности работы ставов с опорами сколь жения и расширение области их использования связаны с вы бором износостойких материалов для опор скольжения и при менением смазок, созданием оптимальных конструкций опорных поверхностей и лент; выбором оптимальных параметров кон вейера (ширины, скорости движения и загрузки ленты, длины става), применением вспомогательных средств, снижающих со противление движению ленты, температурный и фрикционный износ трущихся поверхностей. Работы в этом направлении про водились ИГТМ АН УССР и ВОСТНИГРИ.
На установке, оборудованной машиной трения МИ-2, иссле дованы фрикционные характеристики наиболее износостойких конструкционных материалов для опор скольжения (табл. 2.3).
Наиболее выгодными из исследованных материалов для опор скольжения оказались ситаллы и шлакоситаллы, обладающие невысоким коэффициентом трения и значительной износостой костью абразивному изнашиванию. Например, шлакоситалл ли стовой толщиной 10—12 мм по ТУ УССР 21-138—66 имеет зна чительно меньшую стоимость, чем сталь Ст. 3. При давлении 5-10-3 МПа и скорости скольжения 1 м/с коэффициент трения ленты по шлакоситаллу, имеющему чистую поверхность, соста вил 0,49, а при наличии угольной пыли — 0,22. Пыль активно осаждается на опоры скольжения из шлакоситалла, обладаю щего диэлектрическими свойствами, при трении которого возни кают электростатические заряды. Последние имеют незначитель ную величину и способствуют образованию слоя пыли на опорах, выполняющей роль смазки. Целесообразно опоры скольжения выполнять в виде секций, состоящих из расположенных в шах-
|
|
|
|
ТАБЛИЦА 2.3 |
|
|
|
Плотность, |
Микро |
Относи |
Коэффици |
|
Материал опор |
тельная |
|||
|
т/м3 |
твердость, |
износо |
ент трения |
|
|
|
|
МПа |
стойкость |
о ленту |
Сталь Ст.З |
7,8 |
1 500 |
1,00 |
0,67 |
|
Сталь 65Г |
7,8 |
2 500 |
1,23 |
0,56 |
|
Сталь |
Г13Л |
8,0 |
2 500 |
1,25 |
0,58 |
Сталь Х18Н10Т |
7,8 |
2 000 |
2,37 |
0,58 |
|
Капрон |
1,1 |
100 |
0,29 |
0,54 |
|
Полиэтилен НД |
0,9 |
50 |
0,37 |
0,51 |
|
Фторопласт-4 |
2,3 |
40 |
0,05 |
0,42 |
|
ВолокиИТ |
1.4 |
250 |
0,06 |
0,56 |
|
Дуб |
|
0,7 |
— |
0,06 |
0,57 |
Древесно-слоистый пластик |
1,3 |
300 |
0,08 |
0,63 |
|
Стекло |
|
2,4 |
4.500 |
0,52 |
0,64 |
Ситалл технический |
2,5 |
10 000 |
2,49 |
0,52 |
|
Шлакоситалл черный |
2,6 |
8 500 |
2,33 |
0,49 |
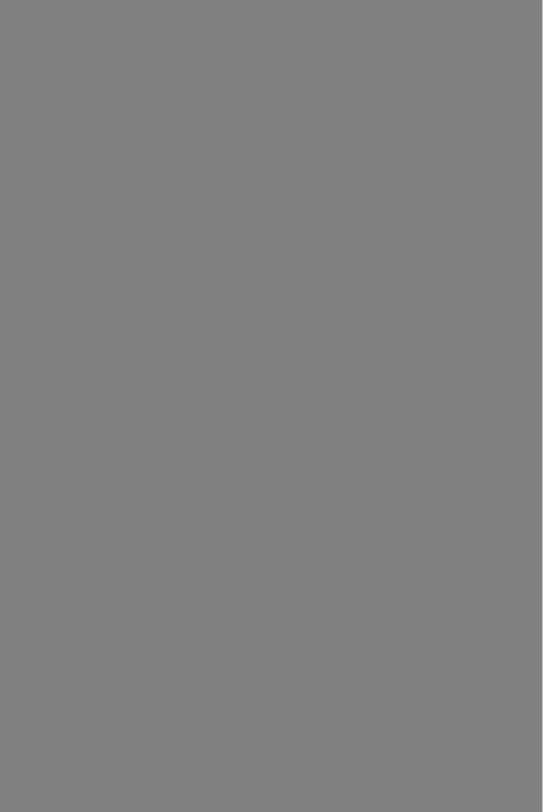
блоки толщиной 50 мм, набранные из кусков снятой с эксплуа тации ленты. Конвейер рекомендован к применению для вторич ной доставки руды из очистного забоя в рудниках с подэтажной системой обрушения [14].
Загрузка ставов железной рудой крупностью до 1500 мм при плотности 3,7 т/м3 и крепости 4—8 по шкале М. М. Протодьяконова осуществлялась с четырех пунктов скреперными установ ками 30ЛС-2С. Масса отдельных кусков груза, падающего с высоты 0,5—0,7 м, достигала одной тонны. Наблюдения за ра ботой конвейеров подтвердили их работоспособность. Коэффи циент сопротивления движению ленты составил 0,6 при потреб ляемой мощности не более 35 кВт. Разрушений на поверхности ленты, температура которой превышала на 2—4 °С темпера туру окужающей среды, не наблюдалось. Большему износу под вергались кромки ленты. Один из конвейеров доставил 70 тыс. т руды при средней производительности 500 т/ч.
Институтом ВОСТНИГРИ разработан конвейер с опорами скольжения повышенной производительности, достигнутой бла годаря применению смазки. Конвейер имеет производитель ность 1000 т/ч при ширине и скорости движения ленты соответ ственно 1200 мм и 1,0—1,5 м/с, мощности привода 70 кВт. Опоры скольжения изготовлены из кусков конвейерной ленты, укладываемых на гибкие дугообразные подвески с амортизато рами, прикрепляемые к бортам става. Имеются дефлекторные ролики, установленные на дугообразных пластинах для умень шения износа кромок ленты. Холостая ветвь ленты располага ется на роликоопорах. Наилучшие результаты получены при использовании резинотросовой ленты типа 2РТЛО-1500, об кладка которой содержит графит, улучшающий скольжение. В качестве смазки применена антифрикционная водная суспен зия серебристого графита, подаваемая по всей длине опор сколь жения с помощью системы шлангов и форсунок. Коэффициент трения ленты по опоре составил 0,4—0,55. Конвейером достав лено 60 тыс. т руды. Нагрева ленты и опор скольжения не на блюдалось. Роль смазки могут выполнять вода и виброэле менты, которыми оснащаются секционные опоры скольжения. Вибрация способствует отрыву ленты от опор, в результате чего уменьшается сопротивление ее перемещению. Чтобы уменьшить сопротивление движению ленты, можно использовать комбини рованные опоры, когда в ставе одновременно устанавливают ролики (обычно по бокам) и опоры скольжения в центральной части секций.
2.3.ЭКСПЛУАТАЦИЯ МЕТАЛЛОКОНСТРУКЦИИ
ВУЗЛАХ ЗАГРУЗКИ ПРИ ДОСТАВКЕ КУСКОВЫХ
МАТЕРИАЛОВ
Загрузочная часть ленточного конвейера, транспортирующего кусковые абразивные грузы, является наиболее ответственным участком. Здесь лента активно подвергается ударно-абразив
ному износу. Улучшение условий эксплуатации загрузочной ча сти конвейера связано с применением следующих типов амор тизирующих систем: с жесткой секцией и упругими (амортизи рующими) роликоопорами; канатной секцией и упругими роликоопорами; опорами скольжения; подвижным гибким контуром.
Загрузочная часть с жесткой секцией и упругими ролико опорами. На конвейерах с жесткими ставами широко распрост ранено применение в загрузочной части конвейера отдельной секции из усиленных балок, на которых жестко крепится система упругих роликоопор. Каждая роликоопора является амортизи рующей. В более податливых системах роликоопоры крепятся подвижно за счет гирляндной компоновки из пяти гуммирован ных ребристой резиной роликов (рис. 2.5,а). Крайние ролики присоединяются к шарнирам пластинчатых цепей. Сами цепи подвешиваются к пружинным амортизаторам. Снижение удар ных нагрузок происходит за счет упругой деформации ленты, футеровки роликов и пружинных амортизаторов. Ролики могут крепиться также в вырезах отрезка амортизирующей ленты, концы которой подвешиваются к трубчатым продольным бал кам. При загрузке мелкосыпучего груза работают только ро лики, а при подаче кускового груза одновременно касаются грузоиесущей ленты ролики и амортизирующий отрезок ленты. Если место загрузки конвейера изменяется, загрузочная секция выполняется передвижной в виде портала, перемещаемого по рельсам, или тележки, установленной на продольных балках става. Кроме упругих роликоопор на портале или тележке име ются направляющие борта с уплотнениями.
Загрузочная часть с канатной секцией и упругими ролико опорами. По сравнению с жесткими канатные секции обеспечи вают в 1,5—2 раза большую податливость и, соответственно, больший амортизирующий эффект. Канатные секции выполня ются либо отдельными, либо в составе канатного става в хво стовой или средней части конвейера. Канаты рассчитываются на суммарные статические и динамические нагрузки:
(2.16)
где 53 — суммарное натяжение каната в месте загрузки, Н; 5 К.с — статическое натяжение каната в месте загрузки, Н (опре деляется исходя из максимального прогиба каната по формулам (2.1) и (2.2); SK.д —динамическая составляющая натяжения ка натов, Н (достигает 50% статической составляющей).
Динамическую составляющую натяжения канатов для рас смотренных вариантов компоновки канатов можно рассчитать по методике, предложенной А. О. Спиваковским и В. Г. Дмит риевым [15]:
Э Е к^2к
(2.17)
V2
Секции |
загрузочной |
части |
конвейера |
с |
подвесными |
роликоопорамн: |
|
||||
а — жесткая |
секция: |
/ — стойка; |
2 — пластинчатая |
цепь; |
3 — подвеска; |
4 — ролико- |
|||||
опора; б — канатная секция |
с направляющими |
сегментами: |
/ — зажим; 2 — канат; |
5 — |
|||||||
сегмент; 4 — каретка; |
в — многоканатная секция: |
/ — упругая |
подвеска; |
2 — канат; |
|||||||
3 — оттяжка; |
4 — рама; г — канатная |
секция с |
вертикальной запасовкой |
каната; |
/ — |
||||||
|
|
|
ролик; |
2 — канат; |
3 — i/илка |
|
|
|
|
V(s |
(2.18) |
|
3E KF2KIJ2CK |
|
{EKF2K + IJ2 CK) I J 2 |
|
(2.19) |
где EK— модуль упругости материала |
канатов; F2к — площадь |
сечения двух канатов; Э — кинетическая энергия системы канат ный став — подвесные роликоопоры; Ск — жесткость соседних участков канатного става.
Канатные секции загрузочной части конвейера отличаются схемой запасовки и компоновкой канатов. Для выравнивания натяжения канатов канатная секция оборудуется дугообраз ными направляющими сегментами (рис. 2.5,6). Одна пара сег ментов монтируется на каретках, перемещаемых винтовым на тяжным устройством. Натяжным устройством можно регулиро вать натяжение каната и положение в плане подвесных роликоопор. Концы канатов закрепляются зажимами на стойках.
Для широких лент при транспортировании недробленной гор ной массы крупностью 600—1000 мм может быть применен по датливый став с многоканатной системой подвески пяти рядов роликов (рис. 2.5,б). Особенностью конструкции является также то, что к продольным балкам крепятся не боковые ролики, а бо ковые канаты с помощью упругих подвесок. При падении кус ков груза ударные нагрузки через ленту передаются на ролики, канаты и упругие подвески. Подвески сначала сжимаются, а за тем восстанавливают свое положение. Подъем ленты вверх за держивается упругими оттяжками, соединяющими поперечины рамы секции с поперечинами става. Благодаря этому снижается ударное взаимодействие ленты с кусками груза.
При запасовке канатов в вертикальной плоскости ветви ка ната служат для поэтапного гашения кинетической энергии па дающих кусков груза. Прогибаясь, верхний канат через при крепленный к нему вильчатый элемент передает часть энергии
.нижнему канату (рис. 2.5,г). Податливость ленты при этом уменьшается. Секция обладает повышенной первоначальной по датливостью, благодаря чему снижается износ ленты.
Загрузочная часть с опорами скольжения. Достоинством применения опор скольжения в загрузочной части конвейера яв ляется простота конструкции, более равномерное распределение динамических нагрузок. Секции с опорами скольжения имеют незначительную по сравнению со ставом конвейера длину, по этому нагрев ленты при скольжении значительно меньше.
Опоры скольжения эффективно предохраняют ленту от про дольных порывов при сквозном пробое острыми посторонними предметами или их заклинивании, которые часто встречаются в грузопотоке металлургических предприятий. Для этих условий
опоры скольжения монтируются совместно с загрузочным лотком.
Промтрансниипроектом разработана и внедрена на Магнито горском металлургическом комбинате загрузочная секция, рабо тающая в комплексе со специальным загрузочным лотком и предназначенная для защиты ленты шириной 1200 мм от удар ного разрушения и продольных разрывов [16]. Загрузочная сек ция (рис. 2.6, а) включает жесткие опоры скольжения, состоя щие из двух футерованных сталью Ст. 3 и шлакоситадлом бо ковин и основания. Параметры опор скольжения выбираются так, чтобы лента над опорами скольжения принимала желобча тую форму и не касалась при отсутствии крупных кусков груза и длинномерных острых предметов основания. Для регулирова ния положения боковин служат шарниры, которые после уста новки боковин в заданное положение жестко фиксируются. По обе стороны от опор скольжения монтируются подвесные трех роликовые роликоопоры с амортизаторами. Такая компоновка секции позволяет снижать ударные нагрузки на ленту за счет как ее упругости, так и подвесных роликоопор. Загрузочный ло ток имеет в передней части поворотную подпружиненную стенку с контргрузом. На боковой стенке лотка установлен электромаг нитный датчик КВП-16, сблокированный с приводом конвейера. Поворотная стенка служит для контроля возможного заклини вания посторонних предметов и выпуска их из лотка до момента останова конвейера. При загрузке материала лента под дей ствием ударных нагрузок прогибается и перемещается по опо рам скольжения и подвесным роликоопорам. Если попадают весьма крупные заостренные куски, лента, прогибаясь, достигает основания опор скольжения и сквозного пробоя не происходит. При поступлении в лоток длинномерного предмета лента увле кает его и прижимает к передней стенке лотка. Стенка повора чивается, и электромагнитный датчик срабатывает, отключая привод конвейера. Датчик срабатывает также и при заштыбовке лотка. Желобчатое положение ленты исключает попадание ча стиц груза в зону контакта ее с опорами скольжения. Нагрев боковин не превышал 6 °С. Максимальная нагрузка на аморти заторы подвесных роликоопор составила 19,8 кН. Надежность срабатывания датчика заклинивания длинномерного предмета зависит от параметров компоновки ленты на опорах скольже ния относительно лотка. Необходимо знать минимальную и максимальную длину предмета, при которой он не заклинится и произойдет срабатывание датчика при повороте стенки прямо линейного лотка (рис. 2.6, б) :
Ln. min ^ : |
V |
“Ь Ьл-f- ЬЛНл cos (Xj, |
(2.20) |
s i n a i |
|
|
|
U max = — Г ---- ( # л + |
1Я Sin О ,)2 + Ь2„ + Ь(НЛ+ /д Sltl Ctx) COS СС1( |
||
sin ct>i |
|
|
|
(2.21)
|
разрушения |
и продольного порыва: |
|
|
||||
а — конструкция секции: / — лоток; |
2 — поворотная |
стенка |
с контргрузом; 3 — датчик; |
|||||
4 —длинномерный |
предмет; 5 — подвесная ролнкоопора; |
6 —лента; 7 |
— опоры |
сколь |
||||
жения; 8 — рама; |
9 — амортизатор; |
10 — боковины |
опор |
скольжения; |
// — основание |
|||
опор скольжения; |
12 — шарниры; б — расчетная |
схема |
выпуска длинномерных |
пред |
||||
|
метов; |
В — ширина |
ленты |
|
|
|
|
где <xi — уГол наклона прямолинейного лотка; Нп — расстояние между средней частью ленты и поворотной стенкой лотка; Ьл — ширина лотка; /д— длина поворотной стенки лотка.
В загрузочной части конвейера срабатывание датчика про исходило при поступлении предметов длиной свыше 1,7—2,1 м и следующих значениях параметров: # л= 380 мм, 6Л = 700 мм, а, = 50°.
Чтобы улучшить работу жесткой опоры скольжения при вы соких ударных нагрузках, уменьшают массу воспринимающих удары частей опоры путем разделения ее на отдельные аморти зирующие элементы (рис. 2.7,а). Последние монтируют на Т-об разных поперечинах, установленных на плите, посредством фи гурного паза и, кроме того, оснащают износостойким покрытием со снятыми фасками. В опорах скольжения загрузочной часта конструкции Всесоюзного научно-исследовательского проектно конструкторского технологического института механизации труда в черной металлургии и ремонтно-механических работ (ВНИИмехчермета) плотное прилегание ленты к средним опо рам скольжения (рис. 2.7, б) исключает сквозной пробой ленты острым длинным предметом или его заклинивание, чем преду преждается продольный разрыв ленты. В момент падения круп-
а —в виде |
отдельных |
опор |
с амортизаторами: |
/ — плита; |
2 — опора; |
|
3 — поперечина; |
||||||
4 — покрытие; |
б — с |
раздельными |
консольными и средней |
опорами |
скольжения: |
1 — |
|||||||
консольные |
опоры; |
2 |
— средняя |
опора; |
3 — выступ; |
4 — амортизатор; |
5 — площадка |
||||||
с пазом; 6 — стойка; |
в — в |
виде |
короба с сыпучим |
материалом и |
диафрагмы: |
/ — |
|||||||
наклонные |
опоры; |
2 —диафрагма; 3 — короб; |
4 — сыпучий |
материал; |
5 — рыхлитель; |
||||||||
г — опоры |
скольжения |
рессорного |
типа: |
I —лента; 2 —опоры |
с |
покрытием |
|
ных кусков средняя опора скольжения благодаря амортизатору и выступу перемещается направленно вниз. Одновременно опус каются боковые опоры скольжения и лента принимает желобча тое положение без перегибов. Наклон средних опор скольжения способствует выталкиванию посторонних предметов. Рассмот ренная конструкция внедрена на многих металлургических и коксохимических заводах Кривбасса.
В качестве опор скольжения могут быть использованы ко роба (рис. 2.7, в), заполненные сыпучим материалом. Боковые части ленты движутся по наклонным опорам скольжения, а средняя — по сыпучему материалу. Чтобы исключить образо вание пыли и уменьшить износ ленты, короб сверху оборудуют гибкой антифрикционной диафрагмой, а внутри массы сыпучего материала устанавливают взрыхляющий механизм. При поступ лении кусков груза диафрагма и сыпучий материал деформиру ются. Взрыхляющий механизм способствует восстановлению де формационных свойств сыпучего материала, который, подвер гаясь ударам, уплотняется.
За рубежом (США, Великобритания, ФРГ, Франция) для снижения ударных нагрузок на загрузочную часть конвейера широко применяют опоры скольжения в виде упруго смонтиро ванных листов. Последние подвешиваются шарнирно к боковым стойкам. Опоры скольжения из упругих листов рессорного типа (рис. 2.7, г) консольно присоединяют к кронштейнам продоль ных балок. Такие опоры просты по конструкции и хорошо рабо тают при погрузке среднекускового материала. Чтобы повысить грузонесущую способность консольных опор скольжения, под лентой монтируют прямую роликоопору с двумя дисками, имею щими выступы, на которые опираются консольные опоры сколь жения. Взаимодействуя с выступами, опоры скольжения вибри руют, благодаря чему уменьшается сопротивление движению ленты.
Еще большей степенью упругости обладают эластичные опоры скольжения. Они выполняются из полос полиуретановой ленты с низким коэффициентом трения или отрезков ленты, рас тягиваемых под грузонесущей лентой и армируемых сверху ан тифрикционными полосами (рис. 2.8,а). Чтобы обеспечить авто матическое регулирование деформации отрезка ленты в зависи мости от величины ударных нагрузок, концы ленты закрепляют на барабанах, один из которых установлен поворотно и кинема тически связан с канатным барабаном с пружинно-гидравличе скими демпферами (рис. 2.8,6). При падении крупных кусков груза лента прогибается, немного сматываясь с поворотного ба рабана. Перемещению ленты и возникновению колебаний пре пятствуют демпферы. Испытания конвейера с лентой, армиро ванной материалом типа «Нафтлен», показали, что такая опора позволяет снизить ударные нагрузки в 1,8—2,3 раза по срав нению с подвесными шарнирными роликоопорами. Для повы шения стойкости к многократным ударным нагрузкам эластич-
РИС. 2.8.
Эластичные опоры скольжения в виде:
а — отрезка ленты с антифрикционными |
полосами: / — полосы; |
2 — отрезок |
ленты; б — |
|||||
сматывающейся ленты; / — борт; 2 —сматывающаяся |
лента с |
барабанами; 8 |
— канат |
|||||
ный |
барабан; |
4 — демпфер; |
в — магнитного полотна; |
/ — лента; 2 — упругое |
магнит |
|||
ное |
полотно; |
3 — продольный |
элемент; |
4 — жесткое |
магнитное |
полотно; |
5 — магниты |
ную опору в виде утолщенного резинового листа с антифрик ционным покрытием устанавливают на подпружиненной желоб чатой траверсе.
Все большее внимание уделяется практическому использова нию в упругих опорах скольжения магнитных сил. Лента в за грузочной части конвейера опирается на упругое полотно с ан тифрикционным покрытием, в которое снизу полосами вмонти рованы постоянные магниты. Магнитное полотно (рис. 2.8, в) располагается на промежуточных продольных элементах, со здающих заданный зазор между лентой и другой жесткой маг нитной опорой с чередующимися полюсами. Одноименные полюсы магнитных опор располагаются напротив друг друга. Жесткое магнитное полотно подвешивается к продольному на клонному основанию загрузочной части. Эффект снижения дина мических нагрузок достигается за счет взаимного магнитного от талкивания опор, силы которого возрастают нелинейно при их сближении. Магнитные опоры скольжения успешно внедрены на конвейерах поверхностного комплекса шахты «Ягуновская» про изводственного объединения «Северокузбассуголь». Они обеспе чивают снижение динамических нагрузок по сравнению с лен той, расположенной между амортизирующими роликоопорами,
44
в 2,31 раза, а по сравнению с гуммированными роликами — 3,9 р^за. Срок службы опор скольжения составил 14—16 мес.
Загрузочная часть с подвижным гибким контуром. При по вышенных скоростях движения ленты эффективность работы неподвижных амортизирующих секций снижается. Возрастают динамические и фрикционные нагрузки на элементы конструк ции, снижается устойчивость перемещения материала, возни кают просыпи. В этом случае может быть рациональным приме нение подвижных движущихся синхронно с грузонесущей лен той амортизирующих систем. Хорошие результаты получены при использовании подвижных ленточных контуров. Такой контур огибает хвостовой и дополнительный барабаны (рис. 2.9,а). Опоры дополнительного барабана подпружиниваются для со здания определенной податливости амортизирующей ленте. Дви
жение амортизирующей ленте передается хвостовым |
бараба |
|
ном и грузонесущей лентой. |
общем |
|
Недостаток |
компоновки амортизирующей ленты на |
|
с конвейером |
барабане — сложность ее замены после |
износа. |
Для устранения этого недостатка амортизирующая лента, имею щая ширину, меньшую, чем грузонесущая лента, монтируется на отдельных бесприводных барабанах и роликоопорах. Такая кон струкция успешно испытана ИГД Минчермета СССР для за грузки крупнокусковой железной руды на приемный конвейер, установленный под молотковой дробилкой. В загрузочной сек ции конструкции ВНИИПТмаша амортизирующая лента уже, чем грузонесущая, и опирается только на барабаны и один про межуточный ролик. Бортовые участки грузонесущей ленты под держиваются боковыми роликами, которые одним концом шар нирно крепятся к раме, а другим к канатам, образующим ка натную секцию (рис. 2.9,6). Ширина амортизирующей ленты для грузонесущих лент шириной 1600, 2000, 2500 и 3000 м выбира ется равной соответственно 500, 650, 800 и 1000 мм, а расстоя ние между барабанами, имеющими диаметр 400—500 мм, со ставляет 4—6 м. Снижение динамических нагрузок происходит за счет работы упругой системы: амортизирующая лента — под весные ролики — канаты. Секция рекомендована к применению на магистральных тяжелых конвейерах производительностью 6000 т/ч по руде (крупностью до 600 мм), имеющих ширину и скорость движения резинотросовой ленты соответственно 1600 мм и 3,15—4,0 м/с и оборудованных на линейной части ка натными секциями, узлами и роликами тяжелых конвейеров Сызранского турбостроительного завода.
В отличие от рассмотренной конструкции в загрузочной сек ции конвейера нижние концы смежных боковых роликов соеди няются между собой через пластины и пружины. Упрощается монтаж секции, однако возможно возникновение колебаний. Дополнительная лента может выполнять также функции ускори тельной при загрузке материала. Для этого она оснащается вы ступающими бортовыми участками, между которыми распола-
Конструкции загрузочной части конвейера с гибкими подвижными аморти зирующими контурами:
а — ленточными, |
связанными с |
барабанами |
конвейера: |
/ — грузонесущая |
лента; |
2 — |
|||||||
амортизирующая |
лента; |
3 — подпружиненный барабан; |
б — ленточным с |
дополнитель |
|||||||||
ными |
барабанами |
и |
канатной |
секцией: 1 — грузонесущая лента; 2 — амортизирующая |
|||||||||
лента; |
3 — подвесные |
ролики; |
4 — канатная |
секция; |
в — ленточными загрузочными: |
1 — |
|||||||
лоток; |
2 — грузонесущая |
лента; |
3 —дополнительная лента; |
4 — амортизирующие |
ро |
||||||||
лики; |
г — с ходовыми |
опорами: |
1 — лента; |
2 — ходовая |
опора |
с эластичными элемен |
|||||||
|
тами; |
3 — выступ; |
|
4 — направляющая; |
б — пневмоамортизатор |
|
|
гается более узкая грузонесущая лента (рис. 2.9, в ). Под грузо потоком бортовые участки дополнительной ленты занимают плоское положение и лежат на амортизирующих роликах. В на правлении движения грузонесущей ленты бортовые участки до полнительной ленты с помощью наклонных боковых роликов занимают положение под углом, а через определенное расстоя ние снова переходят в горизонтальное положение. Крупнокусковый груз не падает свободно на грузонесущую ленту, а сте кает поперек ленты по наклонным плоскостям лотка на борто вые участки дополнительной ленты, над которой установлены
ограждающие борта. При дальнейшем движении обеих лент груз в результате наклона бортовых участков дополнительной ленты стекает на грузонесущую ленту без значительного соуда рения с ней и проскальзывания. Таким образом, грузонесущая лента не подвергается интенсивному износу крупнокусковым грузом. Дополнительная лента, имеющая незначительную длину, после износа заменяется новой.
При загрузке крупнокускового материала крупностью до 1000 мм целесообразно применение подвижных контуров с ходо выми опорами (рис. 2.9,г), соединенными цепями. Ходовые опоры монтируются на траверсах с эластичными элементами, фрикционно взаимодействующими с грузонесущей лентой. Ро лики опор перемещаются по направляющим со встроенными в них пневматическими амортизаторами с выдвижными высту пами. Пневматические камеры сообщаются с источником сжа того воздуха. Под действием ударных нагрузок пневмоамортиза торы деформируются, при этом ходовые опоры совершают вертикальные перемещения, снижая нагрузки на ленту. Если крупнокусковый груз не поступает, подача сжатого воздуха пре кращается и выступы опускаются, после чего ходовые ролики движутся по направляющим.
2.4. ПЕРЕДВИЖКА КОНВЕЙЕРОВ НА ОТКРЫТЫХ РАЗРАБОТКАХ
При эксплуатации мощных конвейерных комплексов в карье рах одной из наиболее трудоемких операций является переме щение забойных и отвальных конвейеров вслед за подвиганием уступов. Перемещение осуществляется после разборки конвейера на части их последовательным переносом и монтажом или без разборки непрерывной передвижкой на определенный шаг. По следний способ более производителен и позволяет полностью механизировать и автоматизировать процесс передвижки. При непрерывной передвижке секции конвейеров жестко соединяют в единый блок с помощью шпал и боковых рельс, которые вос принимают основные усилия. Передвижник подхватывает рель созахватной головкой, фиксируемой в заданном положении кра ном и тяговосцепным устройством, боковой рельс, приподнимает его вместе со шпалами и ставом конвейера, затем приближает к себе на шаг передвижки и совершает челноковые движения вдоль става. Шпалы смещаются на весу и частично волочением по почве. Производительность передвижника соответствует про изведению длины става на шаг передвижки (в единицу вре мени), т. е. имеет размерность площади (м2) передвижки на единицу времени.
В СССР средства непрерывной передвижки выполняют на базе тракторов С-80, Т-100, Т-140, Т-180, ДЭТ-250, оснащенных крановым навесным оборудованием и рельсозахватной голов кой. Мощные передвижники (турнодозеры) типа Т-10С и
МПТК-1 на базе тракторов Т-180 и ДЭТ-250С изготавливаются донецким машиностроительным заводом им. Ленинскогф ком сомола Украины и Ново-Краматорским машиностроительным заводом. Они предназначены для передвижки забойных и от вальных конвейеров производительностью до 5000 м2/ч при шаге передвижки до 2 м и скорости передвижки до 10 км/ч. Передвижники успешно применяются на карьерах КМА (Лебе динском, Стойленском), Никопольского марганцевого бассейна (Шевченковском, Грушевском), на разрезах производственного объединения «Александрияуголь» и др.
Производительность передвижки конвейеров во многом зави сит от схемы расстановки оборудования и последовательности проводимых операций. Применение одновременно двух пере движников, движущихся навстречу друг другу к центру става с последующим выравниванием средней части конвейера одним передвижчиком, позволяет сократить время передвижки. Сокра щению времени передвижки способствует также увеличение длины одного конвейера в линии, при этом уменьшаются про тяженность и частота обхода «мертвых» зон, создаваемых при водными станциями. Чтобы уменьшить нагрузки на узлы пере движника и элементы захвата на конвейере, навесное оборудо вание выполняют с двумя обоймами рельсозахватных головок, разнесенных по длине става и смещенных поперечно. Общий шаг передвижки слагается из двух полушагов, создаваемых сначала первой, а потом второй по ходу движения рельсозахват ными головками. Для этого на ходовой тележке передвижника шарнирно закрепляется балка, несущая на концах рельсоза хватные головки, взаимодействующие с рельсом конвейерного става. На концах балки и на раме ходовой тележки установ лены блоки, огибаемые канатом, концы которого закреплены на балке стопорным механизмом каната, сблокированным с при водом тележки. Для обеспечения устойчивой работы передвиж ника (рис. 2.10, а) на раме ходовой тележки смонтирован контр груз. В процессе передвижки конвейерного става рельсозахват ные головки захватывают головку рельса и передвигают его и связанный с ним конвейерный став на новую линию. Балка по ворачивается на некоторых угол, определяемый шагом пере движки. Барабан может свободно вращаться. Канат переходит с одной стороны барабана на другую. Усилия от передвижки, приложенные к передней и задней рельсозахватным головкам, выравниваются, что сопровождается перемещением каната че рез блоки. Балка в зависимости от соотношения этих усилий по ворачивается в одну или другую сторону. Канат воспринимает часть усилий передвижки, разгружая частично балку от изги бающего момента в горизонтальной плоскости. При необходимо сти барабан затормаживают, перемещение каната прекращается и балка стопорится в заданном положении.
Рельсы передвижного конвейера служат также для переме щения по нему перегрузочных тележек. Если передвижной кон-
|
|
|
|
|
|
|
|
РИС. 2.10. |
|
|
|
|
|
|
|
а — |
|
Средства передвижки |
ленточных |
конвейеров |
на |
карьерах: |
|
||||||||
|
|
с двумя |
обоймами |
рельсозахватных |
головок- |
/ |
|
о |
* |
||||||
с |
- передвижчик |
|
|||||||||||||
каната«нахами; |
3J -— поворотная |
обалка; 4 —-шшпалапала; 5 ~- рельсозахвлт^чя* ! ^ ™ * * ,Г~ |
WIWIV"бЛОКН |
||||||||||||
б — передвижчик |
с |
балкой |
в виде |
шаонноного |
папялва„___ головка, |
б став; |
|||||||||
О - передвижчик с балкой в виде |
шарнирного |
параллелограмма- |
/ — -гоактов- С? В; |
||||||||||||
балка; |
3 — гидро; |
|
|
4 -рам а; |
5 -шарнир; |
«-направляющая; 7 - |
^нусоЯиднь^ |
||||||||
|
|
- |
дродомкрат; |
||||||||||||
|
|
|
|
|
|
: |
— |
: |
— |
и |
г |
|
____ ые |
|
|
ролики на ставе конвейера; |
8 - шпала; |
в - конвейер |
с катками для |
поперечного и |
|||||||||||
продольного |
перемещения: |
/-опорны е |
катки; 2 - дополнительные |
роликовые |
катки- |
||||||||||
3 |
домкрат; |
4 |
рычаг; г |
|
система |
ориентирования |
движением передвижника |
с по |
|||||||
мощью |
газового |
лазера: |
/ — лазер; |
2 — экран; |
3 — ориентир; |
4 — шаг |
передвижки* |
||||||||
5, |
6 — соответственно |
приводная и концевая станции; |
7 — передвижчик; |
/ —/ V — после |
|||||||||||
|
|
|
|
|
довательность передвижки конвейера |
|
|
|
|
вейер не имеет рельсов, в качестве захватываемого элемента ис пользуют опорные стойки с роликами конусовидной формы, монтируемые на шпалах конвейера. При этом навесной меха низм передвижника выполняют в виде шарнирного параллело грамма с направляющей. Поворот параллелограмма в горизон тальной плоскости вокруг шарнира рамы навесного механизма осуществляется гидродомкратом, шток и цилиндр которого свя-
49
заны шарнирно с рамой и звеном параллелограмма (рис. 2.10, б). Звенья параллелограмма посредством С-образных планок же стко соединены с направляющей, которая состоит из шарнирно соединенных средней и концевых частей трубчатой формы. Кон цевые части направляющей ориентированы в пространстве па раллельно друг другу для параллельного перемещения кон вейера. Средняя часть направляющей выполнена дугообразной в вертикальной плоскости с плавными переходами к концевым частям. Своей выпуклостью дуга обращена вверх. Направляю щая касается поверхности конусовидного ролика со стороны конвейера. Вращая параллелограмм гидродомкратом, выстав ляют средние и концевые части направляющей в одну линию. Передвижчик с конца конвейера заводит концевую часть на правляющей навесного механизма под конусовидный ролик и, передвигаясь вдоль конвейера, отрывает шпалы от грунта. До стигнув второго конца конвейера и установив направляющую на возможный шаг передвижки, передвижчик движется обратно параллельно конвейеру. Секции конвейера перемещаются в бо ковом направлении.
Передвижка забойных конвейеров незначительной длины осуществляется установкой секций ставов на тележки и приме нением вспомогательных тяговых средств. Такие конвейеры мо гут перемещаться в поперечном и продольном направлениях. Кроме опорных катков имеются дополнительные катки (рис. 2.10, в) с конусными частями, выполняющие функцию лыж для продольной передвижки става. Дополнительные катки под вешиваются шарнирно к боковинам рамы конвейера с помощью поворотных кронштейнов и домкратов. При поперечной пере движке става дополнительные катки находятся на одном уровне с опорными катками. Для продольного перемещения конвейера дополнительные катки опускают с помощью домкратов, после чего став приподнимается и перемещается на дополнительных катках.
После передвижки конвейера производят рихтовку става в горизонтальной плоскости. Рихтовка става — трудоемкая опе рация. Чтобы добиться прямолинейности передвижки става, т. е. прямолинейности хода передвижчика, используют прицепные плужки, оставляющие след на почве, колышки на трассе, под весные лампы — ориентиры. НИИКМА разработана система ориентирования движением передвижчика с помощью газового лазера непрерывного действия. Газовый лазер позволяет иметь вдоль конвейера практически нерасходящийся луч, который слу жит базой для определения положения передвижчика относи тельно конвейера. Система ориентирования (рис. 2.10,г), в со став которой входят газовый лазер с устройством изменения его положения, ориентир на концевой станции, устройство для из мерения перемещения концевой станции (или забойного бун кера), экран на передвижчике, радиостанции на приводной стан ции и передвижчике, испытана на забойных конвейерах вскрыщ-
50
ного роторного комплекса К.МА. Расположение лазера на при водной станции, экрана на передвижчике и ориентира на кон цевой станции образует линию для ориентировки передвижника. Поворот лазера в горизонтальной и вертикальной плоскостях при корректировке положения луча осуществляется микропри водами. С помощью объектива оператор с приводной станции наводит луч на ориентир в конце конвейера с отклонением по горизонтали, не превышающим 10 см. Положение луча по вер тикали корректируется по радио. Экран на передвижчике по зволяет проводить работы в дневное время и выполнен из полотна с нанесенной на него координатной сеткой. Полотно по мещается в трубу длиной 1200 мм и диаметром 800 мм. Следую щий шаг передвижки начинается с перемещения приводной и концевой станций на заданный шаг. Приводная станция пере двигается на собственной гусеничной ходовой части. Концевая станция перемещается волоком с помощью каната и тягача (С-100, ДЭТ-250). Затем оператор с приводной станции направ ляет луч на ориентир концевой станции, в качестве которого обычно применяют электрическую лампочку, окрашенную в жел тый цвет, и опускают его до середины экрана. Передвижчик разворачивается в направлении передвижки и выходит середи ной (по горизонтали) экрана на луч, после чего движется к приводной станции, удерживая луч в пределах вертикальной полосы шириной 5—6 см, проходящей через центр экрана. При подходе передвижника к приводной станции весь конвейер ока зывается выставленным соосно со станциями. Далее у привод ной станции передвижчик останавливается, а приводная и кон цевая станции передвигаются на следующий шаг. Цикл при обратном ходе повторяется. Достигнутая производительность передвижки составила 4840 м2/ч и может быть увеличена до 10 тыс. м2/ч при составе бригады восемь человек в смену и производительности труда 2500 м2/чел-смену. Это показатели более чем в 20 раз превышают среднестатистические значения по Михайловскому карьеру КМА до внедрения лазерной си стемы [17].
ОБЕСПЕЧЕНИЕ ЭКСПЛУАТАЦИОННОЙ НАДЕЖНОСТИ И КОНТРОЛЬ состояния
ОСНОВНЫХ УЗЛОВ
3.1. УПЛОТНЕНИЕ, СМАЗКА И КОНТРОЛЬ
состояния подшипниковых УЗЛОВ РОЛИКООПОР
По данным УкрНИИпроекта, полученным на предприятиях угольной и других отраслях горнодобывающей промышленно сти, стоимость технического обслуживания и ремонта роликов составляет 28 % всех эксплуатационных расходов на ленточные конвейеры. Фактический срок службы роликов на шахтах и угольных разрезах составляет соответственно 1,5 и 2 года с уче том проведения ремонтов, пополнения или замены смазки. Ос новная причина преждевременного отказа роликов — заклинива ние подшипников из-за нарушения работы уплотнений, которые изнашиваются в результате попадания в подшипник атмосфер ных осадков, пыли, агрессивной воды, абразивных частиц транс портируемого груза. В среднем 66 % отказов роликов прихо дится на засорение подшипников пылью и попадание в них влаги. Для роликов с шариковыми подшипниками характерно увеличение кольцевых зазоров, а для роликов с коническими подшипниками — увеличение люфтов.
Существенное влияние на снижение долговечности роликов оказывают большие колебания температуры окружающей среды (от +40 до —55 °С). В летнее время температура роликов от действия солнечных лучей может повышаться до 70 °С. Это приводит к возрастанию испаряемости смазки, к ее разжиже нию и вытеканию из подшипников. При низких температурах увеличивается вязкость смазки и повышается сопротивление вращению роликов. Очевидна целесообразность применения ро ликов с долгодействующей смазкой. При этом уплотнения под шипникового узла роликов должны надежно защищать подшип ники от попадания в них инородных тел, обеспечить сохран ность смазки, быть компактными, простыми и технологичными в изготовлении, с минимальным сопротивлением вращению, из носостойкими.
Из применяемых в настоящее время уплотнений (лабиринт ных, канавочных, дисковых, скользящих и комбинированных) наиболее надежны комбинированные. Ролики с комбинирован ными уплотнениями, отвечающими основным требованиям, со зданы и внедрены в производство УкрНИИпроектом. Уплотне ния имеют многоступенчатую систему защиты подшипников от засорения и вытекания смазки, включающую лабиринт, кольце-
52
вые канавки в отверстии крышки, камеру большой емкости, за полненную смазкой, в которую помещена плавающая втулка. Между плавающей втулкой, на которую действует сила тяже сти, и уплотнительным кольцом или крышкой создается сколь зящий контакт. Несмотря на изменение давления между поло стью ролика и окружающей средой, возникающее в периоды на гревания и охлаждения ролика, контакт между плавающей втулкой и уплотнительным кольцом или крышкой остается по стоянным. Благодаря этому сохраняется смазка в зазорах и кольцевых канавках уплотнения при наклонном расположении ролика. Давление, действующее на втулку в верхнем подшипни ковом узле, направлено против веса втулки и может нарушить уплотнительный контакт. В нижнем подшипниковом узле на правление этих сил совпадает, благодаря чему возрастает на дежность уплотнения. Поэтому расчет параметров уплотнения производится из условия обеспечения герметичности верхнего подшипникового узла.
Подшипниковые узлы горизонтально расположенных роликов работают в лучших условиях, и смазка в них не вытекает. Эф фект уплотнения обеспечивается благодаря тому, что буртик втулки постоянно внедрен в смазку. В промышленных условиях исследовалось также влияние низких температур на сопротив ление вращению роликов при различных типах смазки. На дол говечность подшипника наибольшее влияние оказывают попа дание воды и качество смазки.
На основе полученных данных были разработаны техниче ские требования на смазки БНЗ-З и БНЗ-ЗМ (морозостойкая) для роликов. Установлено, что в процессе длительной работы (свыше 5 лет) основные показатели смазок БНЗ-З и БНЗ-ЗМ (предел прочности, вязкость, температура каплепадения) изме няются незначительно. Смазка БНЗ-З рекомендуется при темпе ратурах окружающей среды от —16 до +90 °С, а смазка БНЗ-ЗМ соответственно от —45 до +90 °С. В угольной и дру гих отраслях промышленности успешно эксплуатируется свыше 150 тысяч роликов рассмотренной конструкции.
При конструировании роликов, работающих в условиях по вышенного загрязнения окружающей среды, широко применя ются лабиринтные уплотнения. Для надежной работы лабиринт ных уплотнений весьма важна рациональная компоновка сто порных элементов. Лабиринтные уплотнения фиксируются сто порными элементами (рис. 3.1,а), размещаемыми в кольцевых канавках на валу, и стопорными элементами, размещенными в кольцевых канавках корпуса подшипника. Стопорный элемент, расположенный в кольцевой канавке на валу, представляет со бой пружинную шайбу, а другой — стопор треугольной формы. Канавка на валу имеет конический профиль с вершиной конуса, обращенной в сторону ролика, причем угол между образующей канавки и осью вала составляет не менее 7°. При взаимодей ствии пружинной шайбы с конической поверхностью канавки
J
*
/
|
|
|
РИС. |
3.1. |
|
|
|
||
Конструкции |
уплотнений роликов |
с |
шариковыми |
подшипниками: |
|||||
а — со стопорными |
нажимными |
элементами: |
/ — обечайка; 2 — вал; |
3 — подшипник; |
|||||
4 — уплотнение; 5, 6 — стопорные |
элементы; |
б — из |
трех колец; |
/ — вал; 2 — обечайка; |
|||||
3 — стакан; |
4 — подшипник; 5—7 — соответственно |
наружное, |
внутреннее и среднее |
||||||
кольца; в — с антифрикционным |
кольцевым |
вкладышем: / — обечайка; |
2 — уплотнение; |
||||||
3 — корпус |
подшипника; 4 — пружинные |
кольца; |
5 — подшипник; 6 — антифрикцион |
||||||
|
|
|
ный |
вкладыш |
|
|
|
возникает горизонтальная составляющая сила Рi, прижимаю щая лабиринтное уплотнение к подшипнику. Профиль канавки в корпусе подшипника выполнен в виде прямоугольной трапе ции. При взаимодействии стопора с канавкой корпуса возникает горизонтальная составляющая сила Р 2 , также прижимающая уплотнение к подшипнику. Благодаря этому повышается гер метизация ролика.
Чем меньше выдавливается в процессе работы ролика смазки из уплотнения, тем меньше износ подшипников. Умень шение выдавливания смазки достигается уплотнением, состоя щим из наружного, внутреннего и среднего колец (рис. 3.1,6). Наружное и внутреннее кольца выполняются в виде усеченных конусов с удлиненными посадочными втулками. Втулка наруж ного кольца имеет ступенчатую форму, ступень которой явля ется посадочной частью для вала, а удлиненная часть служит для посадки втулки внутреннего кольца. Удлиненная часть
втулки наружного кольца имеет перфорацию. Наружное и внутреннее конические кольца изготавливаются из эластичного материала. Среднее кольцо состоит из двух колец — внешнего с отбортовкой конической формы по центральному отверстию и внутреннего кольца с аналогичной отбортовкой. Эти кольца со единяются соосно так, что отбортовки колец направлены в про тивоположные стороны. Кольца могут быть или приварены одно к другому, или приклеены.
Наличие перфораций и биконическая поверхность среднего кольца способствуют удержанию смазки и уменьшают ее выте кание при нагреве.
В роликах с неподвижной осью и подшипниками качения конструкции Гипрорудмаша нашли применение эластичные уп лотняющие шайбы с антифрикционным кольцевым вкладышем (рис. 3,1,в). Снаружи шайба фиксируется крышкой с пружин ным кольцом. Между шайбой и внутренним кольцом подшип ника устанавливается антифрикционный вкладыш, проскальзы вающий относительно внутреннего кольца подшипника. При вращении обечайки ролика вместе с ним вращаются корпус подшипника и уплотняющая шайба с антифрикционным вкла дышем, обеспечивающая герметизацию подшипника.
Конструкции уплотнений роликов, применяемых зарубеж ными фирмами, весьма разнообразны. Для роликов фирм ФРГ характерно использование нескольких зон уплотнения. Система уплотнения включает уплотнительную крышку, три зоны кон тактного уплотнения, лабиринт и контактное уплотнение. Чем тяжелее ролик, тем сложнее уплотнение. Ролики с повышенной герметичностью конструкции «Тема» (ФРГ) имеют в составе уплотнения магнитные элементы. Уплотнение состоит из анти коррозионного корпуса, в который заключены гибкие магнитные уплотнительные диски, облицованные материалом с незначи тельным коэффициентом трения. Уплотняющий прижим дисков зависит от силы магнитного притяжения. В роликах тяжелого типа, выпускаемых в Швеции, имеются защитная крышка с маслозадерживающими канавками и многозаходный штампо ванный из стального листа осевой лабиринт. Нередко все уплот нение лабиринтное. Многозаходный лабиринт иногда собира ется из отдельных элементов и может иметь заданное число за ходов. В Великобритании больше применяют блочные уплотне ния, представляющие собой собранный готовый узел, помещае мый перед подшипником. Такой блок, например, может состоять из четырех штампованных уплотнительных шайб, смонтирован ных в обойме. В роликах, выпускаемых фирмами США, име ются, как правило, две-четыре зоны лабиринтных или контакт ных уплотнений с внешней и уплотнение с внутренней стороны. Широко используются подшипники со встроенными уплотне ниями. Такие подшипники позволяют лучше использовать высо кокачественные смазки и обеспечивают уплотнение с внутрен ней стороны ролика.
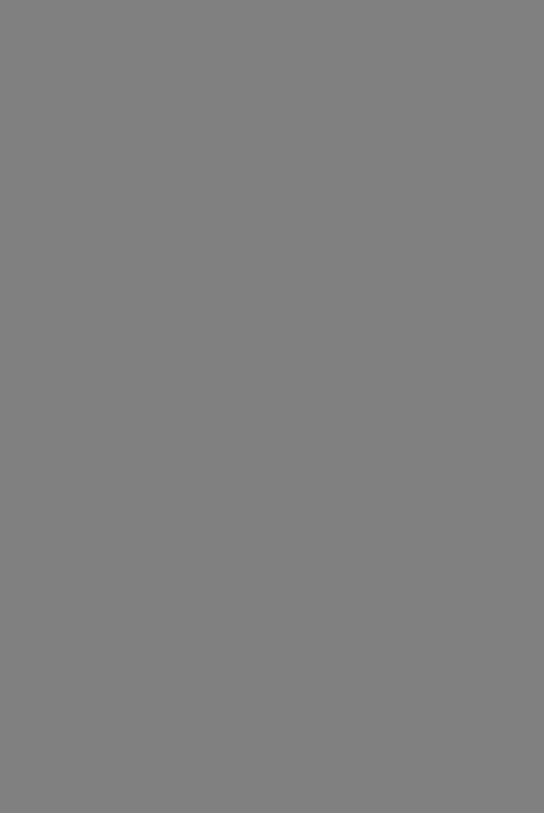
смазкой производят сквозной прокол пробки наконечником на гнетателя смазки, и смазка поступает непосредственно в по лость подшипника и заполняет ее. После заправки подшипника смазкой проколотое отверстие в пробке перекрывается за счет упругости. Рекомендуется проколы в пробке производить уже в процессе изготовления пробки.
Всесоюзным научно-исследовательским институтом электроугольных изделий (ВНИИЭИ) разработана антифрикционная паста АФЗ-1, которая может успешно применяться для длитель ной смазки роликов, работающих в условиях весьма высоких температур (до 350 °С). Пасту закладывают в пространство между кольцами и шариками.
В конструкциях роликов зарубежных фирм для смазки под шипниковых узлов характерно применение пресс-масленок. Пресс-масленками снабжаются каждый подшипниковый узел, подшипниковые полости ролика соединяются трубкой, охваты вающей ось ролика и образующий с ней канал для подвода смазки. Если необходимо произвести одновременно смазку всех роликов роликоопоры, подшипниковые узлы их последовательно соединяют гибкими трубками.
Охлаждение обечайки и подшипниковых узлов роликов про изводится преимущественно в транспортных системах горячих цехов (на металлургических заводах, вспомогательных про изводствах горнодобывающих предприятий). Узлы конвейеров в таких цехах имеют специальное исполнение (например, грузонесущая лента выполняется из металла, роликоопоры — из ке рамики и металла). При этом применяется принудительная система охлаждения роликов. В качестве охлаждающего компо нента используется охлажденные воздух или вода. В конструк ции охлаждаемых роликов предусматриваются расположенные по их оси цилиндрические неподвижные оболочки, между кото рыми и обечайкой ролика подается охлаждающий компонент. Отработанный охлаждающий компонент выходит из ролика че рез полость неподвижной оболочки. В радиаторной схеме теп лоотвода вокруг оси ролика монтируется трубчатая спираль. Через спираль подается охлаждающая жидкость, которая за тем отводится из ролика и поступает в общую систему охлаж дения.
Контроль за состоянием роликов осуществляется обычно ви зуально при профилактическом осмотре эксплуатируемого кон вейера. Неисправный ролик издает повышенный шум в виде по стукивания, резких периодических звуков повышенной частоты. Когда силы трения, в подшипниковых узлах достигают значи тельной величины, обечайки роликов перестают вращаться и очень быстро изнашиваются движущейся лентой. Если остано вившийся ролик вовремя не заменить, на его корпусе образу ются острые режущие кромки. От них на ленте возникают глу бокие порезы или длинные сквозные порывы. На мощных лен точных конвейерах большой протяженности контроль за состоя
нием роликов приобретает особое значение. Для этой цели сле дует использовать постоянно или периодически действующие средства контроля с применением регистрирующей аппаратуры. Так, например, на конвейерной линии протяженностью 100 км в Западной Сахаре, составленной из 11 конвейеров длиной’ 0,9—11,8 км каждый, для контроля и технического ухода за роликами используются самоходные вагонетки, оборудованные акустической аппаратурой. Датчики аппаратуры реагируют на резкое изменение шума участка става, контролируемого в дан ный момент. Быстрая замена роликов производится без оста нова конвейера.
3.2. РЕГУЛИРОВАНИЕ УСТАНОВКИ РОЛИКООПОР НА КОНВЕЙЕРАХ С ЖЕСТКИМИ И КАНАТНЫМИ
|
|
СТАВАМИ |
|
Цель регулирования |
установки роликоопор — обеспечение |
||
правильной |
геометрии |
расположения опор |
по оси движения |
ленты и на |
переходных участках, заданной |
желобчатой ленты |
в зависимости от расчетной производительности конвейера. Узлы крепления должны быть компактны, надежны, износостойки и просты в изготовлении, легко собираться и демонтироваться. Регулировка положения жестких роликоопор производится на жестких или гибких (канатных) опорных элементах и подвес
ных |
(гирляндных) на |
жестких или гибких опорных элементах |
|||
става |
конвейера. На |
переходных |
участках |
конвейера |
(загру |
зочном, разгрузочном, |
поворотном) |
роликоопоры монтируются |
|||
с возможностью изменения их положения |
по высоте |
и шагу |
установки. Для этого узел крепления выполняется в виде скобы (рис. 3.3, а) с пазом под ось ролика и резьбовыми отверстиями. В отверстия вставляются стопорные болты. Скоба навешивается на опорный уголок и раскрепляется стопорными болтами. В про цессе работы конвейера в местах установки оси роликов в пазы кронштейнов возникают зазоры, из-за которых появляются стуки и биение в узлах крепления. Чтобы уменьшить зазоры, для крепления осей используют фигурные упругие обоймы. При де монтаже роликов ось ролика быстро выводится из обоймы (рис. 3.3,6). В конструкциях ставов с трубчатыми опорными элементами в основании роликоопоры выполняются отверстия под крепежные скобы с винтовыми концами (рис. 3.3,в). При монтаже роликоопоры ее основание перемещается по трубча тым элементам и фиксируется скобами и гайками.
Уменьшения шума работающих роликов можно достичь, если оси роликов при монтаже оснастить эластичными втулками, ус танавливаемыми в отверстиях или пазах опорных элементов. После износа эластичные втулки могут быть легко заменены.
В некоторых конструкциях роликоопор предусматривается возможность регулирования угла наклона боковых роликов (чаще от 0 до 40 °С), которое улучшает работу конвейера в ус
ловиях изменения загрузки конвейера. Это особенно важно на мощных конвейерах с лентами повышенной толщины и жест кости. Лента как при загрузке, так и при холостом ходе должна касаться роликоопоры по всей ее ширине. Изменяя угол наклона боковых роликов, можно обеспечить плавный переход ленты от желобчатой формы в плоскую при набегании ленты на барабан. Для обеспечения регулирования угла наклона боковых роликов в значительном диапазоне могут быть применены дугообразные элементы с системой отверстий (рис. 3.3,г). При монтаже ро ликоопоры боковые ролики устанавливаются под заданным уг лом и фиксируются элементами крепления. Положение дугооб разных элементов может также регулироваться. На ставах с консольной компоновкой боковых роликов внутренние концы осей роликов оснащаются секторными кронштейнами (рис. 3.3,5). Кронштейны устанавливаются поворотно на оси и с по мощью паза штифта фиксируются под заданным углом.
Для этого боковые ролики монтируют на эксцентричных кронштейнах, а средний ролик — на поворотной рамке. При по вороте кронштейнов изменяется угол наклона боковых роликов, а при повороте рамки — высота расположения среднего ролика.
На конвейерах большой производительности с широкими лен тами предварительная регулировка положения роликов не всегда обеспечивает оптимальное положение ленты при загрузке и холостом ходе. В этих условиях эффективно применение роликоопор с автоматически изменяющейся в зависимости от за грузки желобчатостью. Роликоопора такого типа (рис. 3.3, е) разработана ВНИИПТмашем. Она включает боковые и средние ролики, которые закреплены в рамках. Рамки связаны между собой пакетом плоских рессор. Рессоры крепятся к рамкам крайних роликов неподвижно, а к рамке среднего ролика — подвижно с помощью пальцев, входящих в пазы рессор. Рамка среднего ролика снабжена вертикальными направляющими, в которых расположен подпружиненный винтовой механизм, укрепленный на раме конвейера. Боковые ролики имеют стойки, которые шарнирно крепятся одним концом к рамкам, а другим концом — к раме конвейера. Роликоопора работает следующим образом. Перед пуском конвейера в зависимости от загрузки ленты задается определенная желобчатость роликоопоре путем перемещения винтового механизма. Боковые ролики принимают наклонное положение, поворачиваясь на шарнирах стоек. При перемещении ленты с грузом по роликоопорам последние изме няют свою желобчатость благодаря рессорным пластинам. При увеличении загрузки ленты конвейера необходимо увеличить желобчатость роликоопор. Это достигается перемещением сред него ролика в вертикальной плоскости винтовым механизмом. Компоновка роликов на рамках с рессорами способствует умень шению нагрузок на подшипниковые узлы. В конструкциях роли коопор со смещенным средним роликом предусматривается воз можность раздвижки роликов по ширине с помощью кронштей-
иов и системы отверстий. Сдвижка роликов или увеличение желобчатости ленты осуществляется тогда, когда требуется бо лее высокая производительность. В стесненных условиях гор ных выработок иногда требуется уменьшать габариты става по ширине, что достигается также увеличением желобчатости ленты. Для этой цели средний ролик выполняется из дисков с подвижными подшипниковыми узлами, перемещаемыми по средством втулок на оси. Ось и втулки могут иметь резьбу с правой и левой навивками, которые обеспечивают сдвижку
или раздвижку дисков при изменении длины среднего |
ро |
лика. |
под |
Регулировка положения роликов лучше достигается в |
весных (гирляндных) роликоопорах. На линейных секциях става с умеренными динамическими нагрузками подвеска роликоопор упрощается. Распространены шарнирные крепления роликов роликоопоры между собой и к жестким продольным балкам става швеллерной, коробчатой или трубчатой конструкции. Роликоопоры с шарнирными креплениями при наклонном расположе нии става конвейера (транспортирование груза вниз) смеща ются вниз по ходу движения ленты, немного раскачиваются, при этом изменяется геометрия их расположения по высоте. Во ВНИИПТмаше разработана конструкция элементов подвески роликоопоры, устраняющая этот недостаток (рис. 3.4,а). Концы осей роликов выполнены с лысками, на которые надеты обоймы. Каждая обойма имеет паз, в который вводится ось ролика. В отверстия каждой обоймы вставляется скоба и фик сируется гайкой. При этом на внутренних концах осей соседних роликов скобы расположены в отверстиях обойм концами вверх, а на внешних концах осей — концами вниз. Скобы соединяются между собой шарнирно посредством звена круглозвенной цепи. Роликоопора навешивается с помощью скоб на балки, закреп ленные на стойках става. В соединительные звенья пропуска ется канат, который препятствует смещению роликов в верти кальной плоскости по ходу движения ленты. Роликоопора мо жет быть навешена на различные типы ставов.
В некоторых конструкциях подвесных роликоопор применяют обычные серийные ролики, устанавливаемые на рамках, шар нирно соединяемых между собой. Однако такие роликоопоры имеют повышенные металлоемкость и число сборных элементов. В роликоопоре, разработанной институтом «Союзпроммеханизация», эти показатели улучшены. Роликоопора состоит из шар нирно соединенных между собой рамок (рис. 3.4,6), на которых
рис. з.з.
Роликоопоры с изменяющейся геометрией расположения:
в — с |
установкой оси ролика на скобе: |
1 — скоба; |
2 |
— стопорные |
болты; |
б — с |
ус |
||||
тановкой оси в упругой |
обойме: |
1 — ось; |
2 — обойма; |
в — с |
возможностью |
перемеще |
|||||
ния по трубчатым опорам: |
/ — труба; г, 5 — с возможностью |
регулирования угла |
на |
||||||||
клона |
боковых роликов: |
1 — дугообразные |
элементы; |
2 — боковые |
ролики; |
е — с |
воз |
||||
можностью регулирования |
всех |
роликов |
роликоопоры: |
/ — ролики; |
2 — рессоры; |
3 — |
|||||
|
|
подпружиненный |
винтовой механизм |
|
|
|
|
а
1 2 |
J |
Ч |
|
|
Подвеска |
гирляндных роликоопор |
к |
жесткому |
ставу: |
|
|||
а — с |
соединительными |
обоймами: / — обойма; |
2 — паз; |
5 — отверстия; |
4 — скоба; |
5 — |
||||
ось ролика; |
5 —звено |
цепи; |
7 — канат; б — с |
опорными |
рамками: |
/ — стержни рамок; |
||||
2 — кронштейны; 3 — ролики; |
4 — поперечные |
балки; |
5 — резьбовое |
соединение; |
6 — |
|||||
упор; |
а — с |
крюкообразными |
соединительными |
элементами; г — с |
регулированием |
же- |
лобчатости; / — гирлянда
посредством кронштейна смонтированы ролики. Каждая рамка состоит из поперечных балок, соединенных между собой про дольными стержнями с винтовой нарезкой. По торцам каждой балки имеются соединительные планки с отверстиями под пальцы. Балки могут быть выполнены коробчатого профиля. Каждый кронштейн смещен от середины балки на величину, превышающую половину ширины кронштейна. Это необходимо для совместного размещения кронштейнов соседних рамок в ра бочем положении роликоопоры. На торцах балок имеются отвер стия для стержней. Боковые ролики соединяются со ставом на весными элементами в виде винтовых стержней, гаек и упоров, позволяющих регулировать положение роликоопоры по высоте. Кронштейны, балки, стержни и планки имеют унифицированное исполнение.
Наиболее распространена простая по конструкции подвеска шарнирных роликоопор к жестким продольным балкам кон вейера посредством крюкообразных элементов или звеньев цепи. Такие роликоопоры применяют для перемещения вскрышных по род на открытых разработках фирмы «Веб-Монтан» (ГДР). Гирляндные роликоопоры устанавливаются на мощных ленточ ных конвейерах производительностью 14000 м3/ч при ширине резинотросовой ленты 2750 мм и скоростью движения 6 м/с. Роликоопоры (рис. 3.4, в) для рабочей ветви состоят из пяти ро ликов диаметром 159 мм и длиной 530 мм, шарнирно соединен ных между собой звеньями круглозвенной цепи. На холостой ветви устанавливаются по три ролика диаметром 159 мм, футе рованных резиновыми кольцами диаметром 194 мм для самоочистки роликов. Такие роликоопоры могут устанавливаться на линейной и загрузочной частях конвейера. Для уменьшения ди намических нагрузок на подвески гирляндной роликоопоры по следние оснащаются упругими элементами в виде пружин, рес сор, резиновых амортизаторов, торсионов. Желобчатость ленты в подвесных роликоопорах с упругой подвеской изменяется в за висимости от степени загрузки конвейера.
Желобчатость и грузонесущие возможности гирляндных ро ликоопор регулируется соответствующей компоновкой роликов. Например, гирляндную роликоопору можно монтировать из двух самостоятельных гирлянд, которые устанавливаются со смещением относительно друг друга по ходу движения ленты и могут иметь несимметричную компоновку при использовании ее на криволинейных участках трассы, промежуточной разгрузке и переворачивании ленты (рис. 3.4,г).
При монтаже гирляндных роликоопор на канатный став эле менты крепления должны минимально воздействовать на ка наты и обеспечивать быстрый монтаж и демонтаж роликоопоры.
Наиболее |
распространено крепление гирляндной роликоопоры |
к канатам |
посредством скоб (рис. 3.5,а). Крепление оснащено |
Г-образной планкой, которая шарнирно крепится к скобе и оси ролика. Планка выполняет роль рычага.
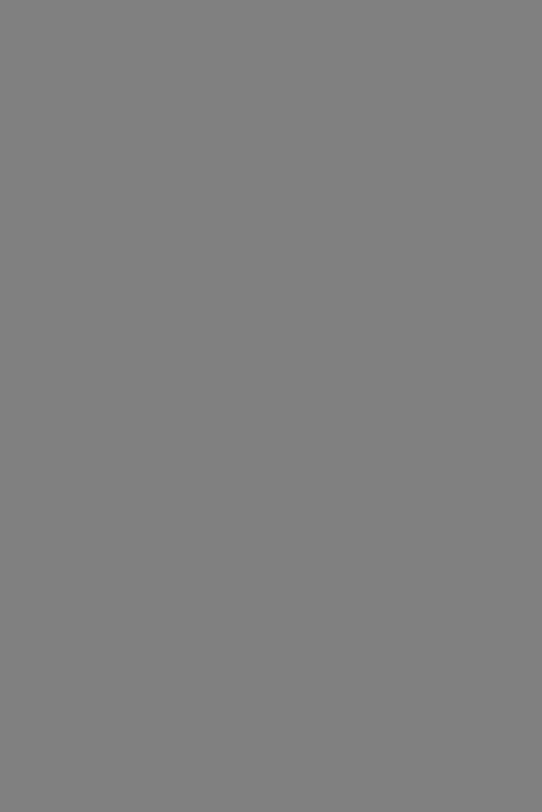
ется при использовании цилиндрических захватов (рис. 3.5,в). Цилиндрический захват охватывает ось бокового ролика и имеет паз для каната, расположенный под углом. Захват и ось ролика выполняются с отверстиями, в которые вставляются фиксаторы (штифты). При навеске роликоопоры захват надевается на ось ролика и фиксируется штифтом. В прорезь помещают канат, а затем вставляют клин, который забивается между стенкой ци линдра и канатом. Выпадание клиньев самопроизвольно не про исходит, благодаря чему обеспечивается надежность соединения.
Весьма простое соединение достигается применением скоб и звеньев круглозвенной цепи. Скобы гайками крепят на осях ро ликов и соединяют между собой звеньями цепи. Таким образом, получается подвижное и быстроразъемное соединение роликов. Обычно стремятся к уменьшению числа крепежных элементов.
Соединительные кронштейны |
выполняют в |
виде скобы |
(рис. 3.5, г) с клинообразным |
пазом и выступом |
треугольного |
сечения. Скоба устанавливается под углом наклона боковых ро ликов. В клинообразном пазу скобы заклинивается канат. Ось бокового ролика крепится в каплеобразном отверстии в нижней части скобы. Выступы треугольного сечения исключают продоль ное скольжение канатов.
3.3. ЭКСПЛУАТАЦИЯ РОЛИКООПОР, ЛЕНТ
ИЗАГРУЗОЧНЫХ УСТРОЙСТВ ПРИ ДОСТАВКЕ
к р у п н о к у с к о в ы х ГРУЗОВ
При подземной и открытой разработке скальных пород и руд буровзрывным способом перед транспортировкой ленточными конвейерами их подвергают первичному дроблению. Поток скального груза после первичного дробления отличается нерав номерностью, имея в своем составе основую часть груза круп ностью менее 400 мм и отдельные куски груза крупностью 400— 600 мм. В процессе погрузки и доставки крупнокусковой горной массы загрузочное устройство, лента, роликоопоры и став под вергаются периодически следующими в интервале 0,7—4,3 с уда рами от кусков груза крупностью 300—500 мм и в интервале 30—80 с от кусков груза крупностью свыше 500 мм [18]. Ча стота прохождения отдельных кусков груза приведена в табл. 3.1.
Ударное взаимодействие наиболее крупных кусков груза с элементами конструкций приводит к их интенсивному разру шению и снижению надежности работы конвейерного оборудо вания. Удовлетворительная эксплуатация ленточных конвейеров для кусковых грузов, представленных в основном ленточными конвейерами тяжелого типа Сызранского турбостроительного за вода с жесткими ставами и роликоопорами, гарантирована лишь при доставке скальных грузов крупностью 300—400 мм. Сроки службы ленты и роликов из-за ударного взаимодействия с кус
ками груза |
существенно ниже нормативных. Например, сроки |
3 Заказ № Н62 |
65 |
|
|
Частота прохождения |
|
|||
|
|
отдельных кусков груза |
Ско |
|||
|
|
|
(мин”*1) при размере |
|
||
|
Транспор |
Шаг между |
кусков, мм |
|
рость |
|
|
|
|
|
движе |
||
Предприятие |
тируемый |
ролико- |
|
|
|
|
|
|
|
ния |
|||
|
груз |
опорами. мм |
|
|
|
|
|
|
|
|
ленты, |
||
|
|
300— 400— 500свыше |
м/с |
|||
|
|
400 |
500 |
600 |
600 |
|
Камыш-Бурун- |
Руда |
1200 |
6G |
40 |
1,5 |
0,6 |
1.5 |
|
ский железо |
|
|
|
|
|
|
|
|
рудный комби |
|
|
|
|
|
|
|
|
нат |
|
Известняк |
1500 |
40 |
24 |
0,9 |
0,3 |
|
Комсомольское |
2,0 |
|||||||
рудоуправление |
Руда |
1000—1500 |
72 |
18 |
|
|
|
|
Карьер |
Ново |
2,1 |
0,6 |
2.0 |
||||
криворожского |
Скальная |
1000—1500 |
80 |
14 |
0,8 |
0,3 |
|
|
горно-обогати |
2.0 |
|||||||
тельного |
ком |
порода |
|
|
|
|
|
|
бината |
|
|
|
|
|
|
|
|
службы лент и роликов на некоторых конвейерах комплексов КМА не превышает соответственно одного и двух лет.
Решение проблемы доставки ленточными конвейерами тради ционного типа крупнокусковых скальных пород и руд связано с применением (кроме рассмотренных в гл. 2 специальных ста вов) амортизирующих роликоопор, устанавливаемых на линей ной и загрузочной частях конвейера, лент с повышенной стой костью к ударным нагрузкам, загрузочных устройств с профиль ными направляющими, упругими, отделяющими негабариты и подсеивающими элементами.
3.3.1. АМОРТИЗИРУЮЩИЕ РОЛИКООПОРЫ
Очевидна тенденция к полной замене роликоопор жесткой конструкции на гирляндные, обладающие повышенной аморти зирующей способностью. Гирляндные роликоопоры собираются с помощью шарниров, чаще из обычных серийных роликов и нодвешиваются к жесткому или канатному ставам. На отвалообразователях комплексов КМА исследовались динамические нагрузки на эти роликоопоры, которые сравнивались с нагруз ками, действующими на жесткие трехроликовые роликоопоры [19]. На линейной части конвейера при транспортировании груза крупностью до 500 мм амплитуда колебаний нагрузки из-за эксцентриситета центрального ролика жесткой конструкции со ставляет 3500 Н, а максимальная ударная нагрузка — 5800 Н при коэффициенте динамичности до 2,3. Трехроликовые гир ляндные роликоопоры на жестком ставе подвергаются нагруз кам из-за эксцентриситета роликов до 2200 Н при максималь ных ударных нагрузках, не превышающих 3500 Н. Коэффициент
66
динамичности таких роликоопор достигает 1,75. Использование гирляндных роликоопор с канатным ставом позволяет умень шить амплитуду колебаний нагрузки на роликах до 2000 Н, а максимальную ударную нагрузку — до 3000 Н при коэффици енте динамичности до 1,5. При попадании в грузопоток кусков
груза крупностью до |
900 мм динамические нагрузки (1000 Н |
и более) в жестких |
роликоопорах зафиксированы в 88 % слу |
чаях прохождения отдельных кусков при максимальной на грузке в 12 500 Н. Коэффициент динамичности при ударах до стигает 5 при продолжительности удара 0,038—0,042 с. В этих условиях гирляндные роликоопоры на жестком ставе испыты вают нагрузки до 7000 Н от 63 % проходящих кусков при коэф фициенте динамичности 3,8 и продолжительности удара 0,08— 0,084 с. Максимальные динамические нагрузки на ролики трех-
ичетырехроликовых опор на канатном ставе составляют соот ветственно 5000 и 4000 Н при коэффициенте динамичности 1,88
и1,76 и продолжительности удара 0,11 с. На основе получен ных данных о действующих динамических нагрузках на ролико опоры различного типа подсчитаны сравнительные сроки службы подшипников роликов, которые для жесткой роликоопоры с же стким ставом, подвесной роликоопоры с жестким ставом, под весной трех- и четырехроликовой роликоопор с канатным ста вом составляют соответственно 2500, 8500, 11720 и 16 540 ч.
Движение крупных кусков по конвейеру с гирляндными роликоопорами происходит с меньшим подбрасыванием, благодаря чему создаются условия для повышения скорости транспорти рования до 3,15 м/с. На наклонных и горизонтальных конвей ерах с гирляндными роликоопорами боковой сход ленты при мерно в 2 раза менее вероятен, чем на конвейерах с ролико опорами жесткой конструкции.
Исследованиями ИГД Минчермета СССР на конвейерах КЛМ-500 Коркинского разреза, транспортирующих скальную породу крупностью 0—500 мм, установлено, что подвесные ро ликоопоры при скорости движения ленты 3,5 м/с испытывают те же динамические нагрузки, что и жесткие роликоопоры при ско рости движения ленты 2 м/с (табл. 3.2).
При оценке условий работы роликоопоры целесообразно пользоваться эквивалентными нагрузками. Действие эквивалент ных нагрузок равноценно по условиям износа суммарному дей ствию переменных нагрузок. Снижение эквивалентных динами ческих нагрузок в подвесных роликоопорах в 1,6—1,8 раза по сравнению с жесткими роликоопорами позволяет в 2—4 раза
увеличить срок службы ленты. На конвейерах, транспортирую щих рядовую горную массу с кусками крупностью до 1000 мм, а в отдельных случаях до 1600 мм, амортизирующие гирлянд ные роликоопоры обычного исполнения уже не обеспечивают необходимого снижения ударных нагрузок. Наибольшие удар ные нагрузки приходятся на роликоопоры, располагаемые в за грузочной части конвейера. Для решения этой проблемы разра-
з* |
67 |
|
|
|
|
Динамические нагрузки (Я). действующие |
|||
|
|
|
|
на различные типы роликоопор. при |
|||
Конструкция роликоопоры |
скорости движения ленты, м/с |
||||||
|
|
|
|
||||
|
|
|
|
2 |
2.5 |
3 |
3.5 |
Жесткая |
с жестким ставом |
жестким |
1000 |
1050 |
1250 |
1600 |
|
Подвесная трехроликовая |
с |
950 |
950 |
1050 |
1250 |
||
ставом |
пятироликовая |
с |
жестким |
750 |
790 |
830 |
1000 |
Подвесная |
|||||||
ставом |
|
с канатным |
630 |
660 |
790 |
1020 |
|
Подвесная трехроликовая |
|||||||
ставом |
|
|
|
|
|
|
|
батываются и внедряются специальные амортизирующие роликоопоры, оснащаемые упругими элементами. Из известных ти пов специальных амортизирующих роликоопор наибольшее рас пространение получили роликоопоры с пружинными, резиноме таллическими упругими элементами, роликоопоры качаю щегося типа, роликоопоры, в компоновке которых используется упругость ленты.
Роликоопоры с пружинными упругими элементами. В амор тизирующих роликоопорах часто применяют пружины, монти руемые в сочетании с опорными элементами, к которым кре пятся ролики роликоопоры. Гирляндные роликоопоры с пружи нами, имеющие сравнительно простую компоновку, монтируются на линейной части конвейера. На конвейерах, устанавливаемых в горных выработках шахт Великобритании, используются гир ляндные роликоопоры типа «Флексиролл» (рис. 3.6, а) с гибкой стальной осью и уплотнениями, короткими роликами из пожаро устойчивого поливинилхлорида, крайние из которых посредством шарнирных цапф и цилиндрических пружин крепятся к жестким боковым кронштейнам. Ось роликоопоры проходит через отвер стие во втулке шарнира и снабжена упорной шайбой; между шайбой и втулкой установлена пружина. При набегании на роликоопору участков ленты с кусками груза пружины и шар ниры позволяют роликоопоре прогибаться на величину, пропор циональную действующей динамической нагрузке, благодаря чему уменьшается удар на ленту и роликоопору. Жесткость пру жин подбирается в зависимости от крупности и плотности транс портируемого материала. Эффективны в работе конические пру жины с нелинейной характеристикой. Такие роликоопоры имеют большую податливость и меньший период колебаний.
Для придания упругости трехроликовой роликоопоре можно использовать только одну пружину (рис. 3.6,6). Пружины мон тируются на подвесках, шарнирно связанных с рамкой среднего ролика, на которой закрепляются оси боковых роликов. Другие
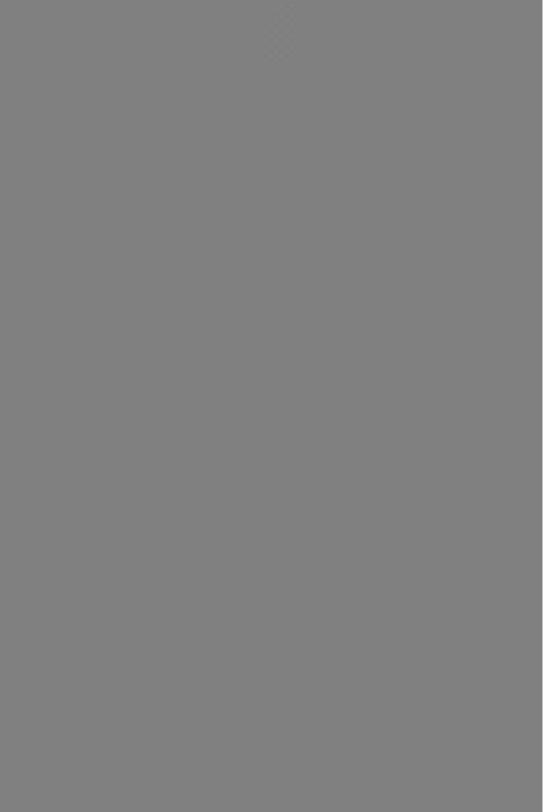
|
|
|
РИС. 3.7. |
|
|
|
|
Амортизирующие роликоопоры |
с резинометаллическими |
упругими |
элемен |
||||
|
|
|
тами: |
|
|
|
|
а — бандажом: |
1 — оболочки; 2 — упругие |
элементы; 3 — корпус; |
б —дисками: |
/ — ре |
|||
зиновые диски; |
в — с корпусом со |
сферическими гнездами |
под |
стаканами: / — диски; |
|||
2 — корпус; 3 — стакан; |
г — оболочками, |
имеющими полости: |
/ — полости; 2 — резино |
||||
вая |
шайба; |
д — амортизатором: |
/ — крепление; 2— упругие опоры |
|
роликоопоры обеспечивают плавный изгиб ленты, пропорцио нальный нагрузке, и обладают свойствами самоочистки.
Большим разнообразием конструктивного исполнения отли чаются амортизирующие роликоопоры с резинометаллическйми упругими элементами. Резинометаллические упругие элементы являются составной частью оболочки ролика и выполняют функ цию амортизирующих опор для корпуса ролика. УкрНИИпроектом разработаны ролики, цилиндрический корпус которых со держит амортизирующие бандажи в виде двух обечаек из пру жинящего материала с установленными между ними упругими элементами (рис. 3.7,а). При ударах упругие элементы банда жей подвергаются деформации сдвига-сжатия, чем и обеспечи ваются их значительная податливость и снижение контактных динамических нагрузок на ленту. Отсутствие трения между уп ругими элементами и лентой способствует уменьшению износа ролика.
Большое распространение получили дисковые амортизирую щие роликоопоры, изготавливаемые надеванием на обечайку роликов фасонных резиновых дисков. Дисковые роликоопоры могут собираться в гирлянду и подвешиваться на жесткий или канатный став или жестко крепиться относительно друг друга.. Дисковые амортизирующие ролики изготовляются донецким машиностроительным заводом им. Ленинского комсомола Ук раины (рис. 3.7,б).
В обычных роликах ударные нагрузки передаются через кор пус и стаканы на подшипники. При этом корпус работает как.
балка с неподвижно заделанными концами. Это приводит к ин тенсивному износу подшипников. Уменьшить ударные нагрузки на подшипники можно компоновкой частей корпуса как сво бодно опирающихся балок. Ролик такой конструкции включает в себя корпус, эластичные диски со стопорными кольцами, ста каны с подшипниками и ось (рис. 3.7,в). Концевые внутренние участки корпуса выполнены сферическими и взаимодействую щими шарнирно с внешней поверхностью стаканов также сфери ческой формы, выполняющих функцию упругих элементов. Эла стичные диски смягчают удары и передают их на корпус, край ние участки которого, изгибаясь, работают как балки, свободно лежащие на двух опорах. Величина прогиба такой балки при ударе больше, чем у балки с неподвижно заделанными концами. Сферические поверхности уменьшают напряжения в месте со единения корпуса со стаканами и местную жесткость корпуса. Корпус ролика изготавливается из пластмассы, например поли этилена.
Хорошей амортизирующей способностью обладают обечайки роликов в виде утолщенных оболочек с полостями внутри (рис. 3.7,г). Такие ролики содержат трубчатый корпус, на ко торый надеваются резинометаллические диски, прилегающие плотно друг к другу благодаря выступам и имеющие отверстия, которые после монтажа ролика образуют продолговатые поло сти, расположенные по окружности. Для загрузочной части кон вейера рекомендуются амортизирующие роликоопоры, собран ные из эластичных пневматических роликов с утолщенной фи гурой в сечении оболочкой, в которой воздух находится под давлением. При увеличении нагрузки на роликоопору пневмати ческие ролики упруго деформируются, снижая напряжения в элементах конструкций и ленте. Следует отметить, что пневма тические ролики обеспечивают хорошее сцепление с лентой, про порциональное нагрузке. УкрНИИпроектом разработан ряд кон струкций роликоопор с податливой оболочкой для работы в кон вейерных комплексах марганцевых карьеров «Шевченковский» и «Грушевский». В качестве роликов используют авиационные шины, насаженные на полую вращающуюся трубу. Ролико опоры с шинами оказались долговечнее ранее применявшихся подпружиненных роликоопор с обрезиненными роликами. Ха рактерным для роликов с податливой оболочкой является отсут ствие шума, который обычно имеет место при работе обрезиненных роликов. Пневматический ролик конструкции ИГТМ АН УССР включает бандаж из склеенных фигурных резиновых шайб с привулканизированной к ним износостойкой резиновой оболочкой. Кольцевые полости бандажа соединяются отвер стиями. В отверстия вентилем подается сжатый воздух, давление которого регулируется в соответствии с действующими удар ными нагрузками. Ударостойкостью обладают ролики с подат ливой оболочкой, имеющей в сечении арочный профиль. Обо лочка выполняется с упорами внутри, насаживается на трубу и
фиксируется относительно их с помощью стержней и дисков. При весьма больших нагрузках смятие оболочки ограничивается упорами.
По данным ВНИИПТМаша при погрузке крупнокускового груза пневматический ролик может быть набран из шин диамет ром 300 мм для сельскохозяйственных машин. Такие ролики монтируются в трехроликовой опоре на месте среднего ролика в комбинации с боковыми роликами, набранными из резиновых дисков. Шаг роликоопор выбирается равным 0,5 м при плотно
сти груза 2 т/м3 и его |
падении с |
высоты, не превышающей |
0,3 м, толщине оболочки |
12—15 мм. |
Возможно также использо |
вание серийных автомобильных шин камерной и бескамерной конструкции. Конструкция ролика, оборудованного шинами ат мосферного давления, позволяет насаживать шины непосредст венно на обечайку ролика без применения специальных посадоч ных устройств. УкрНИИпроектом получены экспериментальные данные амортизирующей способности пневматических и других типов амортизирующих роликоопор (табл. 3.3). Амортизирую щая способность роликов находится в следующем соотношении: пневматических 2,21—3,65; обрезиненных 1; гирляндных с шарнирным соединением 0,615; гирляндных из роликов на гибкой оси 0,545.
Повысить эффективность работы амортизирующих ролико опор можно применением дополнительных амортизаторов, на которые опирается или через которые подвешивается роликоопора. Для амортизирующих подвесных роликоопор характерна подвеска их к стойкам става через амортизаторы в виде отдель ных блоков резинометаллических элементов, аналогичных по принципу работы пружинным упругим элементам. Такие амор тизаторы собираются из плотно расположенных друг к другу резиновых дисков с элементами крепления или из фигурных эла-
|
|
|
|
|
ТАБЛ И Ц А 3.3 |
|
|
|
Сила удара. Н |
Вероятность безот |
|||
|
|
|
|
|
||
|
|
Высота падения, м |
казной работы |
|||
Амортизирующая |
роликоопора |
|
|
|
|
системы. |
|
|
1 |
2 |
3 |
ленты |
лента- |
|
|
ролико- |
||||
|
|
|
|
|
|
опора |
Пневматическая |
авиационная |
1 640 |
2 380 |
3 160 |
0,995 |
0,795 |
избыточного давления |
2 180 |
4 270 |
5 500 |
0,990 |
0,792 |
|
Пневматическая |
атмосферного |
|||||
давления |
|
4 360 |
9 450 |
12 000 |
0,980 |
0,784 |
Обрезиненная |
|
|||||
Гирляндная с шарнирным со |
12 900 |
18 150 |
20 000 |
0,967 |
0,757 |
|
единением роликов |
13 200 |
18 000 |
22 000 |
0,963 |
0,725. |
|
Гирляндная с роликами на гиб |
||||||
кой оси |
|
|
|
|
|
|
стичных элементов с металлическими фигурными дисками и со единительного стержня с эластичной втулкой.
Промтрансниипроектом и шахтой № 2 им. Артема (Кривой Рог) разработана и внедрена амортизирующая роликоопора, обеспечивающая постоянную упругость опор в течении времени удара и работу при центральной и боковой загрузке крупноку скового груза (рис. 3.7, д). Она включает желобчатую раму с роликами и опорными выступами, основание с упругими опо рами. Упругие опоры выполнены в виде дугообразных средней и соединенных с ней боковых пластин из резины. Каждая бо ковая пластина имеет длину, меньшую средней пластины, на которой закреплен опорный выступ роликоопоры. Пластины установлены с возможностью регулировки их формы и длины посредством винтового механизма. Боковые пластины армиро ваны с двух сторон металлическими пластинами. Основание роликоопоры закрепляется на раме конвейера болтами. Для со единения средних пластин с опорными выступами служат болты. После сборки и монтажа роликоопоры производится регули ровка вертикальной и поперечной жесткости упругих пластин посредством перемещения регулировочных гаек. Минимальная их жесткость в вертикальном направлении достигается при ми нимальной высоте боковых пластин, а максимальная — при наи большей высоте; наибольшая жесткость опор в поперечном на правлении— при средней высоте боковых упругих опор. В за грузочной части конвейера устанавливается от двух до четырех амортизирующих роликоопор в зависимости от ширины ленты и величины действующих нагрузок. Роликоопора работает сле дующим образом. При поступлении на ленту потока крупнокус кового груза динамические нагрузки передаются через ролики на желобчатую раму. Рама через выступы передает нагрузку на среднюю пластину упругой опоры. Средняя пластина деформи руется за счет упругого изменения своей формы и последующего упругого взаимодействия с боковыми пластинами. Этим обеспе чиваются высокие податливость и упругость пластин.
Роликоопоры качающегося типа испытаны в производствен ных условиях. В процессе транспортирования горной массы, со держащей отдельно расположенные крупные куски груза, экс тремальные нагрузки на ленту и роликоопору возникают в мо мент набегания отдельного куска на роликоопору. Чем больше в данный момент угол обхвата (угол встречи) лентой ролика, тем больше сила удара. Уменьшить угол встречи кусков груза с роликоопорой можно, если роликоопора изменяет свое верти кальное положение по высоте при набегании на нее кусков груза. Это достигается роликоопорами качающегося типа. Укр-
НИИпроектом разработана роликоопора |
качающегося типа |
|
с двумя |
парами боковых и средних роликов |
(рис. 3.8,а). Пары |
роликов |
монтируются поворотно на держателях, установленных |
шарнирно на кронштейнах рамы конвейера. Держатели соединя ются между собой пневмоили гидравлическими демпфирую-
а
РИС. |
3.8. |
и с использова |
Амортизирующие роликоопоры качающегося типа (а, б) |
||
нием упругости холостой ветви ленты (в—г): |
||
/ — держатель; 2 — рама; 3 — качающаяся |
опора; 4 —траверса; |
5 — дополнительный |
ролик; 6 — направляющая |
|
щими элементами. При увеличении нагрузки на роликоопору держатели поворачиваются, а штоки демпферов выдвигаются и опускаются. Увеличивается желобчатость роликоопоры. Демп фирующие элементы могут быть выполнены в виде двух пружин, работающих на сжатие, связанных между собой тягой с шарни рами. Оригинальная конструкция жесткой роликоопоры качаю щегося типа включает в себя качающуюся опору с двумя пле чами, на каждом из которых установлена роликоопора (рис. 3.8,6). При подходе куска груза к качающейся опоре первая по ходу движения ленты роликоопора перемещается вниз, а вторая — вверх. После того как кусок груза оказывается за шарнирной опорой, происходит поворот роликоопор в обрат ную сторону. Благодаря повторяющемуся смещению роликоопор в вертикальной плоскости, существенно снижается прямое удар ное взаимодействие кусков груза с роликоопорами. Испытания рассматриваемой конструкции проводились на магистральном ленточном конвейере Михайловского ГОКа производственного объединения «КМАруда» со следующими параметрами: произ водительность 8800 м3/ч, длина 760 м, лента резинотросовая,
74
шириной 2000 мм и скоростью движения 5,24 м/с. Измерения показали, что динамические нагрузки на средние ролики качаю щейся роликоопоры примерно в 1,4 раза меньше, чем на средние ролики стандартных жестких трехроликовых роликоопор (табл. 3.4).
Нагрузки на I ролик качающейся роликоопоры при равен стве плеч в 1,2 раза больше, чем на II ролик. Для выравнива ния и уменьшения нагрузок рекомендуется принимать длину плеча I среднего ролика в 1,2 раза больше II ролика. К недо статкам роликоопор качающегося типа можно отнести услож нение и увеличение металлоемкости конструкции, необходи мость регулировки, уменьшение устойчивости сыпучего матери ала на ленте. Наиболее предпочтительная область применения роликоопор этого типа — на забойных конвейерах, транспор тирующих недробленную горную массу.
Роликоопоры с использованием упругости ленты. При соот ветствующей компоновке амортизирующей роликоопоры упру гие свойства последней можно усилить, используя упругие свой ства ленты, свободной от груза. Концы подвесной роликоопоры могут быть установлены на поворотных подпружиненных рыча гах, связанных с осью дополнительного ролика, опирающегося на холостую ветвь ленты. При ударных колебаниях ролико опоры рычаги поворачиваются, перемещая дополнительную ро ликоопору, которая нажимает на холостую ветвь ленты, дефор мирует ее, благодаря чему амортизируются ударные нагрузки.
Чтобы уменьшить число шарнирных соединений, подвижную амортизирующую роликоопору монтируют на траверсах тре угольной формы, снабженных подпружиненными ползунами для перемещения в направляющих жестких стоек. В углах траверсы устанавливаются верхняя трехроликовая и две нижние одноро ликовые роликоопоры (рис. 3.8, в) . Нижние роликоопоры не сколько деформируют ленту относительно роликоопоры холо стой ветви ленты. При попадании кусков груза на роликоопору траверса опускается и передает часть кинетической энергии удара на холостую ветвь ленты путем взаимодействия с ней
|
|
|
|
|
|
ТАБЛИЦА 3.4 |
|
|
|
Нагрузки на роликоопоры, Н |
|
||
|
стандартная |
|
балансирная |
|
||
Масса |
|
|
1 |
ролик |
11 |
ролик |
куска |
|
|
|
|
|
|
груза, кг |
верти |
горизон |
горизон |
верти |
горизон |
|
|
кальная |
тальная |
верти |
|||
|
|
|
кальная |
тальная |
кальная |
тальная |
176 |
2600 |
400 |
1450 |
240 |
1250 |
150 |
111 |
1250 |
290 |
1150 |
160 |
1050 |
135 |
85 |
1000 |
200 |
900 |
130 |
850 |
100 |
64 |
750 |
175 |
600 |
90 |
500 |
70 |
нижних роликов траверсы. Для упрощения конструкции аморти зирующая роликоопора устанавливается на поворотной раме, концы которой служат для крепления дополнительного ролика, взаимодействующего с холостой ветвью ленты при ударных на грузках (рис. 3.8,г). В наиболее простой схеме амортизирую щие роликоопоры с эластичной футеровкой могут непосредст венно опираться на холостую ветвь ленты и передавать ей часть ударных нагрузок.
3.3.2. ЛЕНТЫ С ПОВЫШЕННОЙ СТОЙКОСТЬЮ К УДАРНЫМ НАГРУЗКАМ
Требования к конвейерным лентам, применяемым в горно рудной промышленности, за последние годы значительно воз росли. Это обусловлено спецификой работы значительной части конвейеров, транспортирующих тяжелые высокоабразивные грузы повышенной крупности (300—600 мм). Например, для предприятий черной и цветной металлургии распределение лен точных конвейеров по крупности перемещаемых грузов состав ляет: до 300 мм — 76%, 300—600 мм — 24%. Наиболее абра зивные материалы (известняки и руды) имеют плотность 2,6— 4,6 т/м3, крепость по шкале проф. М. М. Протодьяконова 6—20, а масса отдельных кусков крупностью 400—500 мм составляет 21—140 кг при радиусе закругления выступов 7,5—22 мм и угле между гранями 55—66°. При максимальной крупности транспор тируемого материала и приведенной высоте его падения в уз лах загрузки, составляющей 0,5—1,5 м, лента подвергается зна чительным ударным нагрузкам, в результате чего происходит ударное разрушение обкладок и каркаса ленты. Сроки службы лент в этих условиях во многих случаях не превышают не сколько месяцев.
Резинотканевые и специальные ленты. Для транспортирова ния крупнокусковых грузов разработаны высокопрочные резино тканевые ленты типов 1 и 2Р общего назначения и морозостой кие (табл. 3.5).
|
|
|
|
|
|
ТАБЛИЦА 3.& |
|
|
|
Проч |
Проч |
Удлине |
Соответственно прочность |
||
|
|
(МПа), удлинение {%) |
|||||
|
|
ность |
ность |
ние |
и истирание (см3/кВт-ч) |
||
Тип |
|
проклад |
защитной |
ленты |
|||
Ткань каркаса |
обкладок по классам |
||||||
ленты |
ки по ос |
или бре- |
при ра |
|
|
|
|
|
|
нове |
керной |
бочей |
|
|
|
|
|
и утку, |
проклад |
нагруз |
А |
Б |
в |
|
|
Н/мм |
ки, Н/мм |
ке, % |
|||
1 |
МК-400/120 |
i' |
200 |
2,5 |
250 |
200 |
150 |
400 |
|||||||
2Р |
ТА-300 ' |
120 |
200 |
— |
450 |
400 |
350 |
300 |
40 |
4,0 |
300 |
500 |
500 |
||
|
|
600 |
100 |
— |
|
|
|
Конвейерные ленты типа 1 состоят из каркаса на основе вы сокомодульной многоосновной ткани МК-400/120, защитной про кладки из равнопрочной ткани МК-200Р, расположенной под рабочей обкладкой, и обкладки из износостойких резин. Защит ная тканевая прокладка, имеющая меньший модуль упругости, снижает ударные нагрузки на ленту. Испытания ленты типа 1 на конвейерах Соколовско-Сарбайского и Криворожского ГОКов показали, что они обладают большей стойкостью (в 1,5—2 раза) к ударным нагрузкам. Это позволяет уменьшить число прокла док. Срок службы лент типа 1 на опытных конвейерах при до ставке крупнокусковой горной массы составил 18—26 мес, что на 20 % выше, чем при эксплуатации серийных лент на основе ТА (ТК)-ЗОО.
Меньшую каркасность, но значительную амортизирующую способность имеют ленты со шнурами (рис. 3.9,а), аналогич ными тросам. Шнуры включают одну центральную и краевые пряди, состоящие из большого числа нитей. Увеличение стой кости к ударным нагрузкам ленты достигается также включе нием в ленту нетканых прокладок, располагаемых между сет чатыми прокладками. Основная функция сетчатых прокладок заключается в защите каркаса от воздействия ударных нагрузок
и |
повышении |
монолитности |
ленты |
за счет улучшения |
связи |
|
с |
эластичными |
слоями. Сочетание |
эластичных |
слоев, |
сеток |
|
с |
большими удлинениями и |
корда |
(рис. 3.9,6) |
обеспечивает |
также ленте повышенную сопротивляемость усталостным на грузкам.
РИС. 3.9.
Резинотканевые ленты для крупнокусковых грузов:
о — со шнурами, образующими пряди; 6 |
—с сеткой |
и кордом; |
/ — обкладка; 2 — амор |
||
тизирующие |
слон; 3 — эластичные слои; |
4 — корд; |
в — с диспергированными в об |
||
кладке |
волокнами; / — обкладка; |
|
2 — амортизирующий |
слой; 3 — каркас |
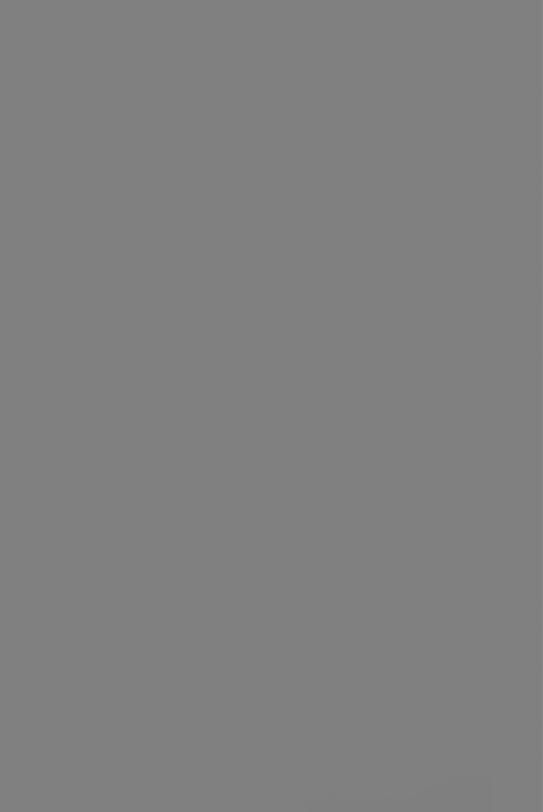
Лента
Прочность. кН см |
Диаметр троса, мм |
Прочность, троса, кН |
Шаг между тросами, мм |
Толщина верхней и нижней обкладок, мм |
Ширина ленты, мм
Диаметр приводного барабана, мм
РТЛ 500 |
5 |
2,7 |
6 |
9 |
3 -4,5 |
800 |
500 |
|
РТЛ |
1000 |
10 |
3,4 |
10 |
9 |
2—2,5 |
800—1000 |
630 |
4 |
||||||||
РТЛ |
1500 |
15 |
4,2 |
16 |
9 |
2—4 |
800—2000 |
800 |
5.5 |
||||||||
РТЛ |
1500У |
15 |
6,0 |
26,1 |
15 |
5.5 |
800—1400 |
800 |
5.5 |
||||||||
РТЛ 2500 |
25 |
7,5 |
42 |
14 |
5.5 |
1000—2000 |
1000 |
|
5.5 |
||||||||
РТЛ 3150 |
31,5 |
8,25 |
52 |
14 |
5.5 |
1000—2000 |
1250 |
|
5.5 |
||||||||
РТЛ 4000 |
40 |
10,9 |
72 |
15 |
5.5 |
1600—2000 |
1640 |
|
8 |
||||||||
|
|
50 |
10,6 |
|
17 |
А |
|
|
РТЛ 5000 |
98 |
10 |
1400—2400 |
— |
||||
|
|
|
|
|
|
А |
|
|
РТЛ 6000 |
60 |
12,9 |
128 |
18 |
Л |
1400—2400 |
|
|
10 |
|
|||||||
|
|
|
|
|
|
4 |
|
|
Ленты изготавливаются с усиленной тканевой прокладкой (1РТЛ) и без прокладки (2РТЛ), а также в теплостойком и огнестойком исполнениях.
На открытых работах в ФРГ используют преимущественно резинотросовые ленты, имеющие меньшую массу при достаточно большой разрывной прочности и не требующие больших диа метров приводных барабанов. Фирма «Континенталь» (ФРГ) выпускает резинотросовые ленты шириной 500—3200 мм, раз рывной прочностью 8—63 кН/см ширины ленты. Для резинотро совых лент, изготовляемых в ФРГ, характерно увеличение тол щины рабочей обкладки до 16 мм и нерабочей до 8 мм. Ленты, предназначенные для конвейеров большой протяженности, имеют разрывную прочность 26 кН/см ширины ленты и толщину обкладок на рабочей стороне 20 мм и на нерабочей — 10 мм. Фирмой проведены исследования по повышению сопротивляемо сти резинотросовых лент разрушению. Попытки увеличить со противление лент порезам введением в резину различных до бавок (полиамид, полиэфир, сталь, стекло) по различным при чинам не оправдались. Положительные результаты в этом направлении достигнуты при использовании дополнительных про кладок из полиамида, расположенных над рядом тросов для ар мирования средней части ленты. Особенность прокладки состоит в том, что она имеет сетчатую структуру, нити утка которой имеют значительную большую прочность на разрыв, чем нити
основы. Армирование с внешней стороны повышает ударную прочность резинотросовой ленты на 14%, с внутренней — 25%. с обеих сторон — 40 %. Армирование тросиками с обеих сторон повышает ударную прочность ленты лишь на 26 %. Чем тоньше диаметр тросиков арматуры и меньше шаг их расположения, тем лучше. Величина разрушающей нагрузки возрастает при мерно пропорционально толщине верхнего резинового слоя в ленте.
3.3.3. ЗАГРУЗОЧНЫЕ УСТРОЙСТВА
Эффективность применения мощных ленточных конвейеров для доставки крупнокусковых скальных грузов крупностью бо лее 300 мм во многом зависит от конструкций и схем компо новки загрузочных устройств. С точки зрения минимального разрушающего воздействия на ленту кусков груза в узлах пере грузки загрузочные устройства должны обеспечивать: уменьше ние высоты падения кусков груза для снижения ударных нагру зок на ленту; сообщение грузопотоку скорости, равной скорости ленты по величине и направлению, для уменьшения проскальзы вания груза по ленте и, соответственно, износа ленты трением; заданную производительность при минимальном налипании груза с вязкими включениями; возможность регулирования и контроля режима истечения грузопотока; разделение грузопо тока на фракции для создания подсыпки и соответственно сни жения ударных нагрузок на ленту; снижение ударных и фрик ционных нагрузок на конструкцию загрузочного устройства для повышения надежности работы и срока службы; отделение не габаритов. Кроме того, загрузочные устройства должны быть компактны, относительно несложны, с минимальным использо ванием приводных механизмов.
Перед загрузкой ленточных конвейеров крупнокусковым грузом характерно использование специальных дробильных установок, устанавливаемых вблизи забоев на перегрузочных пунктах или непосредственно при перегрузке с конвейера на кон вейер (исключая случаи дробления горной массы по технологи ческим условиям), средств для отделения и дробления негаба ритов, отбойно-направляющих элементов и промежуточных бункеров. Загрузочные устройства представлены приводными питателями и лотками с самотечным движением груза, оснащае мыми элементами контроля, регулирования истечения и под сыпки груза, уплотняющими бортами и фартуками, системой орошения или аспирации для удаления пыли.
Отделение и дробление негабаритов. При загрузке конвейера из бункера отделение негабаритов (кусков груза крупностью более 1000 мм) осуществляется с помощью последовательно устанавливаемых виброгрохота и грохота, выполненного в виде консольно закрепленных колосников (рис. 3.10,а). Концевая часть виброгрохота расположена над загрузочной частью колос-
80
10 |
11 |
12, |
РИС. зло.
Устройства для удаления негабаритов на колосниках (а), с контурами тра ков (б) и направления грузопотока (в):
1 — виброгрохот; 2 — грохот |
из колосников; 3 — упругая связь; |
4 — бункер; 5 — траки; |
|
6—13 — отражатели цепной, |
ленточный, щитовой, |
конвейерный, |
воронкообразный, ба |
рабанный, вибрационный |
соответственно |
|
никового грохота и соединена с ней упругой связью. Основная часть кускового груза просыпается под виброгрохотом, а нега бариты поступают на колосники. Перепад высот между грохо тами позволяет дополнительно разрыхлить горную массу. При накоплении негабаритов на колосниках производится их раз рушение кумулятивными зарядами ВВ. Дробленый продукт про сыпается через колосники, в результате чего бункер равномерно заполняется. Упругая связь между грохотами позволяет исклю чить попадание негабаритов в пространство между грохотами.
Отделение негабаритов может осуществляться приводными ме ханизмами роторного типа в виде вращающихся решетчатых лопастей, дисков, о которые ударяются крупные куски груза и удаляются в бункер или на отводящий конвейер для дробления. Известно также использование грейферных механизмов для захвата и удаления наиболее крупных кусков груза непосред ственно с ленты конвейера.
В перегружателях ПГС-100, обеспечивающих технологиче скую связь между экскаватором и забойным ленточным конвейе ром, отделитель негабаритов встраивается в нижнюю часть бун кера и представляет собой два наклонных приводных контура траков (рис. 3.10,6). Поверхности траков являются продолже нием стенок бункера. В сужающемся пространстве между тра ками горная масса крупностью выше 900 мм задерживается дви жущимися полотнами и удаляется на площадку в сторону от коса.
Удаление негабаритов часто применяется в транспортных комплексах шахт для выпуска и доставки руды. Сначала руда по ступает на забойный вибропитатель и далее на грохотную ре шетку и реверсивный питатель, который включается только в мо мент попадания на решетку негабарита. При остановке комплекса негабариты разбиваются с помощью ВВ с применением буриль ных штанг непосредственно в желобе питателя, при этом ре шетка перекрывается затвором. После пуска комплекса реверсо ром кондиционная горная масса возвращается на решетку с открытым затвором и поступает в транспортную линию. Дро бление негабаритов может осуществляться и бутобоями с высо кой энергией удара, имеющими пневматический, гидравлический или электрический привод.
Отбойно-направляющие элементы. Перед подачей крупноку сковой горной массы на загрузочное устройство или непосред ственно на ленту конвейера необходимо погасить кинетическую энергию отдельных кусков и изменить направление их переме щения. Это достигается отбойно-направляющими элементами (отражателями) различного типа (рис. 3.10,в). Рельсовый от ражатель состоит из набора рельсов, шарнирно навешенных од ним концом на траверсу, перекрывающую в плане перегрузоч ную воронку. При взаимодействии с грузопотоком рельсы вос принимают и гасят часть его кинетической энергии. Отдельные куски, ударясь о тяжелые рельсы, частично дробятся, за счет чего улучшается формирование грузопотока. Недостатками этого типа отражателя являются его залипание при перегрузке влаж ных грунтов и большой шум при работе.
Цепной отражатель представляет собой набор тяжелых кора бельных цепей длиной до 3 м, подвешенных одним концом на траверсе. Установка цепных отражателей по сравнению с рель совыми более проста, однако они в меньшей мере способствуют формированию грузопотока и дроблению крупных кусков.
Ленточные отражатели — фартуки применяются в основном
при перегрузке мелкокусковой горной массы. Они изготовля ются из кусков конвейерной ленты, свободно подвешенных на траверсе. Такая подвеска, а также эластичность фартука спо собствуют их самоочистке от налипшего грунта. На мощных ленточных конвейерах 2ЛУ160 ленточные отражатели представ ляют собой рессору, набранную из отрезков ленты и стальных канатов, число которых подбирается в зависимости от условий работы. Недостаток ленточных отражателей — отсутствие дроб ления крупных кусков и быстрое разрушение отрезков ленты.
Щитовые отражатели находят применение при перегрузке горной массы различной крупности. Они выполняются свар ными из листовой стали и имеют криволинейную рабочую по верхность в поперечном, а иногда и в продольном направлении, что способствует центрированию грузопотока. Для уменьшения залипания поворотной щит футеруется конвейерной лентой. Су щественно снижает износ щита при перегрузке абразивных по род наварка на его рабочую поверхность полосовой стали, удер живающей защитный слой груза. В исходное положение щит возвращается под действием собственной массы или пружин. Большая масса щита способствует дроблению груза, но затруд няет монтаж и эксплуатацию. При работе на липких грунтах щит удерживает значительные массы, обрушение которых мо жет вызвать разрушение приемного лотка, ленты и роликоопор. Кроме того, налипание грунта на щит зачастую приводит к ча стичной или полной заштыбовке загрузочного устройства. Для предотвращения налипания грунта щит-отражатель иногда обо рудуется вибратором. При этом рабочая поверхность щита фу теруется резиной или гидрофобным покрытием.
Значительно реже применяются отражатели, оснащаемые приводными узлами с элементами регулирования. К ним отно сятся отражатели в виде вертикально установленного ленточ ного конвейера, вращающейся воронки, приводных барабанов, вибрационных плит, оснащаемых очистителями.
Конструкции загрузочных устройств. Типы и конструкции за грузочных устройств для крупнокусковых скальных грузов под робно рассмотрены в работе [20]. Из приводных загрузочных устройств для этих целей по оценке ВНИИПТмаша наиболее эф фективны вибрационные питатели и питатели-грохоты в комп лексе с бункерами. Они обеспечивают непрерывную подачу гру зопотока с заданной производительностью с минимальной высо той падения (0,2—0,3 м), разделение груза с подсевом, имеют сравнительно простую конструкцию и малые габариты, надежны в работе. Однако скорость транспортирования, равная 0,2— 0,7 м/с, значительно ниже скорости движения лент, и это за трудняет согласование производительностей питателя и конвей ера. Благоприятная продольная подача груза вибропитателями возможна, например, для лент шириной 1600 мм при скорости движения ленты не более 1,6 м/с. Производительность вибро питателей, выпускаемых серийно, не превышает 1000—1100 т/ч.
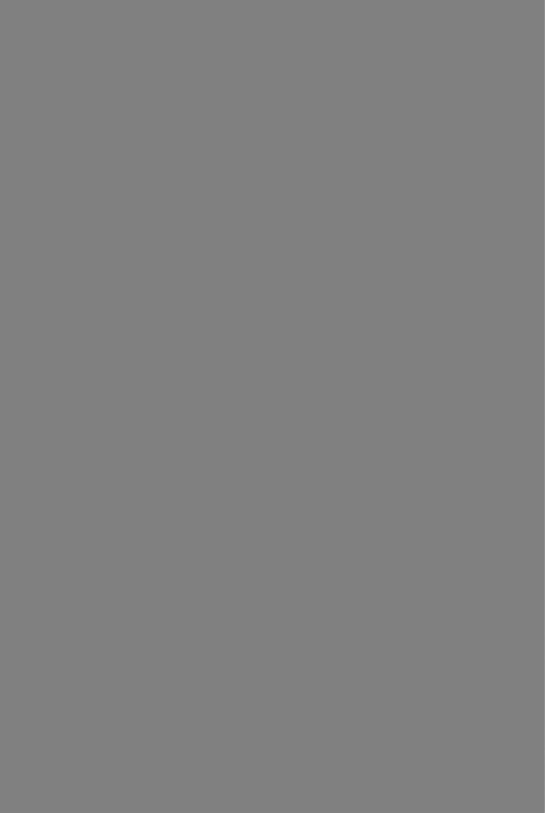
г
Рис. 3.11.
Схемы для расчета параметров загрузочных лотков с криволинейным окон чанием (а—в) и построения профиля лотка (г):
1 — лоток; 2 — приемный конвейер; 3 — подающий конвейер
при проектировании радиуса кривизны криволинейной части лотка:
R* = АНп~\~ Вил Cvо, |
(3.4) |
где А, В, С — коэффициенты, значение которых для |
основного |
диапазона параметров /л, аь аг приведены в табл. 3.7.
Если известен радиус кривизны криволинейной части лотка,
то по формуле (3.4) можно определить скорость |
грузопотока |
|
на выходе лотка: |
|
|
«л = д / |
R„ — AH^„ — Cvo_ ' |
(3.5) |
Для оптимизации параметров лотка рекомендуется соотно |
||
шение |
R„ < (0,7 Ч- 1) Яп, |
|
(3-н 4) Ar < |
(3.6) |
где НГ— толщина слоя грузопотока на выходе лотка.

£ « -i. |
я |
|
|
|
|
|
У гол н ак л о н а л о тк а а , , |
гр а д у с |
|
|
|
|
||||
5 5 Ь Ч |
У |
|
|
|
|
|
|
|
|
|
|
|
|
|
|
|
& е * |
* « |
|
30 |
|
36 |
|
42 |
|
48 |
|
54 |
|
|
|
|
|
я _ я |
2 °* |
|
|
|
|
|
|
60 |
|
66 |
||||||
g s s |
к« о |
|
|
|
|
|
|
|
|
|
|
|
|
|||
5 в а |
|
|
|
|
|
|
|
|
|
|
|
|
|
|
||
1 5 2 |
Р » в |
|
|
|
К оэф ф ициенты соответственно А, В, С |
|
|
|
||||||||
|
&S& |
|
|
|
|
|
|
|||||||||
|
|
|
|
0 ,2 7 |
|
0 ,2 2 |
|
0 ,1 8 |
|
0 ,1 6 |
|
0 ,1 4 |
|
0 ,1 2 |
|
0,11 |
|
|
5 |
|
0 ,4 9 |
|
0 ,9 5 |
|
1,16 |
|
1,24 |
|
1,27 |
|
1,27 |
|
1,27 |
|
|
— |
0 ,3 5 |
— 0,3 2 |
— 0 ,3 0 |
— 0 ,2 9 |
- 0 ,2 6 |
— 0 ,2 0 |
— 0 , 29' |
|||||||
|
|
|
||||||||||||||
|
|
|
|
0 ,1 9 |
|
0 ,1 6 |
|
0 ,1 3 |
|
0,1 2 |
|
0 ,1 0 |
|
0 ,0 9 |
|
0 ,0 8 |
0 ,5 |
|
9 |
|
0 ,3 8 |
|
0 ,7 5 |
|
0 ,9 2 |
|
0 ,9 9 |
|
1,02 |
|
1,02 |
|
1,01 |
|
— |
0 ,2 9 |
— 0 ,2 7 |
— 0 ,2 6 |
— 0,2 5 |
— 0,2 4 |
— 0 ,2 4 |
—0 , 25- |
||||||||
|
|
|||||||||||||||
|
|
|
|
0,1 4 |
|
0 ,1 2 |
|
0,11 |
|
0 ,0 9 |
|
0 ,0 8 |
|
0 ,0 7 |
|
0 ,0 7 |
|
|
13 |
|
0 ,3 0 |
|
0,59 |
|
0,73 |
|
0 ,8 0 |
|
0,82 |
|
0,8 3 |
|
0,82 |
|
|
— |
0 ,2 4 |
— |
0,23 |
— |
0,22 |
- |
0,21 |
- |
0,21 |
— |
0,21 |
— |
0,21 |
|
|
|
|
|
0 ,13 |
|
0 ,1 0 |
|
0 ,0 8 |
|
0 ,0 7 |
|
0 ,0 7 |
|
0 ,0 6 |
|
0 ,0 5 |
|
|
17 |
|
0,2 4 |
|
0 ,4 8 |
|
0 ,60 |
|
0,65 |
|
0 ,67 |
|
0 ,6 8 |
|
0,69 |
|
|
|
|
|
|
|
|
|
|
|||||||
|
|
|
— |
0,21 |
— |
0 ,20 |
— |
0,19 |
— |
0,19 |
— |
0,19 |
— |
0 ,19 |
— |
0 ,1 9 |
|
|
|
|
0,0 9 |
|
0 ,0 8 |
|
0,07 |
|
0 ,06 |
|
0,0 5 |
|
0 ,0 5 |
|
0 ,0 4 |
|
|
17 |
|
1,38 |
|
2,31 |
|
2,90 |
|
2,9 8 |
|
2,96 |
|
2,9 4 |
|
2 ,96 |
|
— |
— |
1,20 |
— 1,01 |
— |
0,75 |
— |
0,6 3 |
- |
0 ,58 |
— |
0,57 |
— |
0 ,5 8 |
||
|
|
|
|
0,92 |
|
0 ,6 8 |
|
0,44 |
|
0,33 |
|
0,27 |
|
0,23 |
|
0,21 |
|
|
13 |
|
0 ,8 6 |
|
1,58 |
|
2 ,1 6 |
|
2,31 |
|
2,3 4 |
|
2,3 4 |
|
2 ,3 5 |
|
— |
— |
0 ,8 3 |
— |
0 ,75 |
— |
0,61 |
— |
0,5 3 |
- |
0 ,5 0 |
— |
0,4 9 |
- |
0 ,5 0 |
|
|
|
|
|
0 ,5 8 |
|
0,4 6 |
|
0,3 3 |
|
0 ,26 |
|
0,21 |
|
0 ,18 |
|
0,1 6 |
|
— |
9 |
|
0 ,5 8 |
|
1,11 |
|
1,60 |
|
1,77 |
|
1,82 |
|
1,83 |
|
1,83 |
|
— |
0,64 |
— |
0,57 |
— |
0,4 9 |
— |
0 ,4 5 |
— |
0,42 |
— |
0,42 |
— |
0 ,4 2 |
||
|
|
|
||||||||||||||
|
|
|
|
0 ,39 |
|
0,33 |
|
0 ,25 |
|
0 ,2 0 |
|
0 ,17 |
|
0,14 |
|
0 ,1 3 |
|
— |
5 |
|
0 ,4 0 |
|
0,8 0 |
|
1,21 |
|
1,36 |
|
1,42 |
|
1,43 |
|
1,42 |
|
- |
0 ,4 8 |
— |
0,4 5 |
— |
0,40 |
— |
0,3 7 |
— |
0 ,3 6 |
- |
0 ,35 |
- |
0,3 6 |
||
|
|
|
||||||||||||||
|
|
|
|
0,2 7 |
|
0 ,23 |
|
0 ,18 |
|
0 ,1 5 |
|
0 ,13 |
|
0,11 |
|
0 ,1 0 |
|
|
0 |
|
0 ,2 7 |
|
0 ,5 5 |
|
0 ,8 6 |
|
0 ,9 9 |
|
1,04 |
|
1,05 |
|
1,05 |
0 ,6 |
|
- |
0 ,3 6 |
— |
0,3 4 |
- |
0,32 |
— |
0 ,30 |
— |
0 ,29 |
— |
0,29 |
— |
0 ,2 9 |
|
|
|
|||||||||||||||
|
|
|
|
0 ,1 8 |
|
0 ,1 6 |
|
0,13 |
|
0,11 |
|
0 ,09 |
|
0 ,0 8 |
|
0 ,0 7 |
|
|
5 |
|
0,1 9 |
|
0 ,3 9 |
|
0 ,63 |
|
0 ,74 |
|
0 ,7 8 |
|
0,7 9 |
|
0 ,7 9 |
|
|
- |
0 ,2 8 |
— |
0 ,2 7 |
- |
0 ,2 6 |
- |
0 ,2 5 |
— |
0 ,2 4 |
— |
0,24 |
— |
0,2 4 |
|
|
|
|
||||||||||||||
|
|
|
|
0 ,13 |
|
0 ,1 2 |
|
0 ,1 0 |
|
0 ,0 8 |
|
0 ,0 7 |
|
0 ,0 6 |
|
0 ,0 5 |
|
|
9 |
|
0 ,1 5 |
|
0,31 |
|
0 ,5 0 |
|
0,5 9 |
|
0,6 2 |
|
0 ,6 3 |
|
0 ,6 3 |
|
|
- |
0 ,24 |
- |
0 ,2 3 |
— |
0,2 2 |
- |
0,22 |
— |
0,21 |
— |
0,21 |
— |
0,21 |
|
|
|
|
||||||||||||||
|
|
|
|
0 ,1 0 |
|
0 ,0 9 |
|
0 ,0 8 |
|
0 ,07 |
|
0 ,0 6 |
|
0 ,0 5 |
|
0 ,0 4 |
|
|
13 |
|
0 ,1 2 |
|
0 ,2 5 |
|
0 ,4 0 |
|
0 ,4 7 |
|
0,51 |
|
0,51 |
|
0,51 |
|
|
- |
0,21 |
— |
0,2 0 |
- |
0 ,1 9 |
- |
0,1 9 |
— |
0 ,1 9 |
- |
0,1 9 |
— |
0 ,1 9 |
|
|
|
|
||||||||||||||
|
|
|
|
0 ,0 8 |
|
0 ,0 7 |
|
0 ,0 6 |
|
0 ,0 5 |
|
0 ,0 5 |
|
0 ,0 4 |
|
0 ,04 |
|
|
17 |
|
0 ,0 9 |
|
0 ,1 9 |
|
0,3 2 |
|
0 ,3 9 |
|
0,41 |
|
0,42 |
|
0,4 2 |
|
|
— |
0 ,1 8 |
— |
0 ,18 |
- |
0,1 7 |
— |
0 ,1 7 |
— |
0,1 7 |
— |
0 ,1 6 |
— |
0 ,1 7 |
|
|
|
|
|
0 ,0 6 |
|
0,0 6 |
|
0 ,0 5 |
|
0 ,04 |
|
0,04 |
|
0 ,03 |
|
0 ,0 3 |
Коэффициент трения груза по лотку (/л) |
Угол наклона конвейера а 2* градус |
|
— 17 |
|
— 13 |
|
—9 |
|
—5 |
0,7 |
0 |
|
5 |
|
9 |
|
13 |
|
17 |
|
|
Угол наклона лотка а Р градус |
|
|
||
30 |
36 |
42 |
48 |
54 |
60 |
66 |
|
Коэффициенты соответственно А * В. с |
|
||||
|
0,41 |
1,56 |
1,87 |
1,95 |
1,96 |
1,96 |
|
—0,91 |
—0,66 |
—0,55 |
—0,50 |
—0,48 |
—0,48 |
|
0,57 |
0,36 |
0,26 |
0,20 |
0,17 |
0,15 |
|
0,27 |
1,12 |
1,40 |
1,50 |
1,52 |
1,52 |
——0,65 —0,52 —0,46 —0,42 —0,41 —0,41
0,37 |
0,26 |
0,16 |
0,16 |
0,13 |
0,11 |
0,18 |
0,81 |
1,06 |
1,15 |
1,18 |
1,18 |
——0,49 —0,42 —0,38 -0,36 —0,35 —0,35
|
0,25 |
0,19 |
0,15 |
0,12 |
0,10 |
0,09 |
— |
0,13 |
0,61 |
0,81 |
0,89 |
0,91 |
0,91 |
|
—0,38 |
—0,34 |
—0,32 |
—0,31 |
—0,30 |
—0,30 |
|
0,18 |
0,14 |
0,11 |
0,09 |
0,08 |
0,07 |
___ |
0,09 |
0,43 |
0,59 |
0,65 |
0,67 |
0,67 |
|
—0,30 |
—0,28 |
—0,26 |
—0,25 |
—0,25 |
—0,25 |
|
0,12 |
0,10 |
0,08 |
0,07 |
0,06 |
0,05 |
— |
0,06 |
0,31 |
0,43 |
0,49 |
0,50 |
0,50 |
|
—0,24 |
—0,23 |
—0,22 |
—0,21 |
—0,21 |
—0,21 |
|
0,09 |
0,07 |
0,06 |
0,05 |
0,04 |
0,04 |
— |
0,05 |
0,25 |
0,34 |
0,39 |
0,40 |
0,40 |
|
—0,21 |
—0,20 |
—0,19 |
—0,19 |
—0,19 |
—0,19 |
|
0,07 |
0,06 |
0,05 |
0,04 |
0,03 |
0,03 |
— |
0,04 |
0,20 |
0,28 |
0,31 |
0,33 |
0,33 |
|
—0,18 |
—0,17 |
—0,17 |
—0,17 |
—0,77 |
—0,17 |
|
0,05 |
0,05 |
0,04 |
0,03 |
0,03 |
0,02 |
— |
0,03 |
0,16 |
0,23 |
0,26 |
0,27 |
0,27 |
|
—0,16 |
-0,16 —0,15 —0,15 —0,15 —0,15 |
||||
|
—0,04 |
0,04 |
0,03 |
0,03 |
0,02 |
0,02 |
Угол наклона прямолинейной части лотка |
для /л= 0,3-*-0,4; |
||
/л= 0,5ч-0,6; /л= 0,7ч-0,8 |
выбирается |
равным |
соответственно |
а, =304-39°; сц = 39+54°; сц = 544-69° |
|
|
|
С увеличением влажности грузопотока угол наклона лотка |
|||
выбирают большим. На |
рис. 3.11, г |
показано |
геометрическое |
построение профиля лотка. Сначала проводят линию АВ под уг лом а\ к горизонтали. Далее параллельно продольной оси при емного конвейера проводят линию MN на расстоянии, равном ра диусу кривизны криволинейной части лотка. От прямой АВ вос ставляется перпендикуляр до пересечения с линией MN в той точке, где расстояние ОВ будет равным радиусу. Точка пересе чения О линий MN и ОВ является центром радиуса кривизны криволинейной части лотка. Под углом ao= ai + a2 проводится линия ОС. Точки В и С соединяются дугой окружности радиу сом Rn.
Применение лотков с криволинейным окончанием позволяет существенно снизить износ лент. Однако невысокая скорость загрузки, интенсивный фракционный износ футеровок и значи тельные ударные нагрузки при погрузке крупнокускового груза на конструкцию ограничивают область применения лотков. При погрузке кусковой горной массы более эффективны загрузочные устройства (лотки) с подвижной компоновкой лотков, обеспе чивающей им вибрацию в автоколебательном режиме. Это до стигается упругим и шарнирным креплением соответственно верхней и нижней частей лотка и использованием кинетической энергии падающего грузопотока. Упругие опоры снижают удар ные нагрузки на конструкцию, уменьшают разброс, пылеобразование, дробление и просыпи материала, а вибрация способ ствует ускорению истечению грузопотока с устройства.
Были изучены особенности самотечного перемещения грузо потока в лотках с вибропробуждением [21]. Упрощенная модель устройства представляет собой наклонную балку, которая одним концом шарнирно связана с основанием, а другим опирается на упруго-вязкие элементы. Такой лоток рассматривается как уз кополосная линейная колебательная система с одной степенью свободы. Грузопоток скального груза, воздействие от которого может быть описано как стационарный случайный процесс F(t), поступает на лоток устройства и создает в нем устойчивый ре жим колебаний. Влияние грузопотока на параметры колебатель ного процесса лотка определяется передаточной функцией си стемы
Ф (jw) = |
(3.7) |
Шд + 2fijww0 — иг
где w — частота колебаний системы; Ьа— коэффициент приведе ния; Wo— собственная частота колебаний лотка; р— характери стика затухания колебательного процесса.
Совмещенное движение грузопотока по лотку осуществля ется под действием сил собственного веса и динамических воз действий, создаваемых вибрацией. В этом случае коэффициент трения груза по лотку заменяется коэффициентом сопротивле ния движению груза, зависящим от параметров вибрации лотка. Установлено, что грузопоток скального груза создает устойчи вый режим колебаний лотка с частотой, близкой к его собст венной, и амплитудой, обеспечивающими заданный коэффи циент сопротивления движению груза. Обобщающим парамет ром, влияющим на величину сопротивления движения груза по лотку, служит ускорение его колебаний. Экспериментально вы явлена для скальных пород зависимость (рис. 3.12, а) между коэффициентами сопротивления движению грузопотока при нали чии вибрации (fB) и без вибрации (f„) от ускорения колебании лотка W
При расчете скорости движения грузопотока использовались модели лотков с криволинейным и прямолинейным окончаниями
|
РИС. |
3.12. |
|
Зависимости |
опытная |
(7) |
|
и |
аппроксимирующая |
(2) |
|
коэффициента |
сопротивле |
||
ния движению |
грузопотока |
||
от |
ускорения |
колебаний |
лотка (а) и расчетные мо дели для определения ско рости грузопотока в криво линейном (б) и прямоли нейном (в) вибрирующих лотках
(рис. 3.12,б,в). Скорость движения грузопотока по прямолиней ному лотку
v* = v0-±-2g (х sin ccj—f„z cos аг), |
(3.8) |
где |
|
z = -----0,87 {[l,15ot1tt)2(Ly—x)— 10]arcctg[1,15а]ДУ2(Ly—x)— 10] +
яаiw 2
-4-0,5In {1 4- [1,1Ъ а ^ (Z.y—JC)— 10]2}—(1,1b a ^L y — 10) X X arcctg(l.lSajt^Ly— 10)—0,5 In [1 +(l,15a1oy2Ly— 10)2]);
где Lv — расстояние от шарнира до оси у, м; х — текущая коор дината, м.
Для расчета скорости движения грузопотока в лотке с кри волинейным окончанием используется аппроксимирующая ку сочно-линейная зависимость fB/fn от W, при этом кривая зави симости /в//л от W разбивается на три участка с точками пере
гиба, которым соответствуют значения ускорений Wi= 4 м/с2 и №2=13 м/с2. Для данных ускорений величина угла дуги криво линейного окончания лотка
г/' — |
9 СИ 1 .0 1 1 1 |
4 |
|
(3.9) |
|
2< X i w2R n |
|
||||
|
|
|
|
|
|
а" = |
2 arcsin |
13 |
|
(3.10) |
|
2 а 1 ^ 2 / ? л |
|
||||
|
|
|
|
|
|
Для значений угла |
а 0, изменяющегося в пределах |
(а0<а')> |
|||
(а '< а 0< а") и (а,< а 0> а //), получены |
формулы для |
расчета |
|||
скорости грузопотока |
в лотке с криволинейным окончанием. |
||||
Скорость грузопотока |
на |
вибрирующем |
лотке по сравнению |
с неподвижным лотком возрастает более чем в 2 раза.
Контроль и улучшение режима работы загрузочных уст ройств с криволинейным профилем. Проверка правильности вы бора и расчета параметров загрузочных устройств может осу ществляться датчиками, позволяющими измерять скорость дви жения грузолотка, амплитуду и частоту колебаний лотка. Датчик скорости грузопотока (рис. 3.13,а) состоит из измеритель ного ролика и механизма поджатая. Ролик имеет корпус, футе рованный слоем резины и установленный на подшипниках отно сительно неподвижной оси. Внутри корпуса расположены свя занная с ним диафрагма с отверстием, а также источник света и фотоэлемент, укрепленные на оси по обе стороны от перего родки. Датчик устанавливается в конце криволинейного окон чания лотка под днищем с помощью механизма поджатая. По ложение ролика относительно лотка регулируется винтом. Ра бота датчика заключается в следующем. Грузопоток, выйдя из лотка, скользит по поверхности корпуса ролика и, благодаря фрикционному взаимодействию с футеровкой, приводит во вра щение ролик. За один оборот ролика в электрической цепи с фо тоэлементом (рис. 3.13,6) возникает импульс за счет освещения лампочкой фотоэлемента (фотодиода) через отверстие в диа фрагме. Выход цепи фотоэлемента соединяется с измеритель ным прибором, например осциллографом. По тарировочному графику определяется скорость грузопотока.
Принцип действия датчика для измерения амплитуды боль шой величины и частоты колебаний лотков основан на измене нии сопротивления в электрической цепи при регистрации ко лебаний. Датчик включает в себя поворотный потенциометр, ук репленный на одном конце держателя. На оси потенциометра неподвижно укреплен шкив диаметром 20 мм с двумя витками гибкой нити. Перед шкивом располагается винтовая пружина небольшой жесткости (примерно 10 Н/см). Одним концом она связана с неподвижным штырем, а другим —с гибкой нитью. Другой конец гибкой нити соединяется с вибрирующим элемен том на лотке. Держатель датчика укрепляется на основании,

типы датчиков отличаются простотой конструкции, не требуют специальных усилителей и могут быть широко использованы при исследованиях и контроле работы загрузочных устройств.
Совершенствование загрузочных устройств с упругими опо рами осуществляется в направлении расширения области их применения благодаря использованию элементов регулирования скорости движения и направления истечения грузопотока, улуч шающих режим работы устройств. Установлено, что положи тельный эффект от вибрации лотка загрузочного устройства по вышается с увеличением ускорения колебаний. Однако энергия грузопотока, взаимодействующего с лотком, имеет низкочастот ную характеристику. Поэтому лотки на упругих опорах вибри руют с низкой частотой, что приводит к уменьшению скорости движения груза и увеличению износа днища лотка. Чтобы улуч шить рабочую характеристику лотков, последние оснащают до полнительными упругими опорами (рис. 3.15, а) и Н-образной наклонной рамой со съемными дебалансами. Нижняя часть до полнительной рамы соединяется с упругим шарниром лотка, а верхняя расположена между упругими опорами лотка и до полнительными упругими опорами. Грузопоток, поступающий с определенной высоты, взаимодействует с лотком, который на чинает вибрировать с низкой частотой. Часть энергии при взаи модействии лотка с грузопотоком передается через упругие опоры лотка Н-образной раме, которая также начинает вибри ровать. Так как дополнительные упругие опоры имеют меньшую упругость, Н-образная рама колеблется с более высокой часто той, чем лоток. Таким образом, лотку сообщается полигармонический колебательный режим. Регулируя массу Н-образной рамы изменением числа съемных дебалансов, обеспечивают за данный режим колебаний лотка в высокочастотном диапазоне. Это способствует увеличению скорости движения грузопотока и уменьшению износа лотка.
Необходимо создавать унифицированные конструкции загру зочных устройств, выполнение элементов которых мало зависело бы от геометрии загрузки, например от взаимного расположе ния загружающего и приемного конвейеров. Этому требованию отвечают загрузочные устройства с телескопической компонов кой коротких лотков (рис. 3.15,6). На неподвижной опорной раме посредством упругих опор устанавливаются балки, выпол ненные из отдельных секций, связанных одна с другой посред ством муфт. Опоры имеют корпус, в котором смонтирована опорная ось с насаженной на нее эластичной втулкой. К бал кам винтовыми стержнями прикреплен наклонный лоток, кото рый содержит телескопически расположенные желобчатые пла стины-лотки. Пластины соединены упругими шарнирами и имеют в боковых стенках овальные пазы. Стержни снабжены эластич ными элементами. Выдвижением винтовых стержней обеспечива ется необходимый расчетный профиль лотка различной длины и кривизны. При поступлении груза основные удары нагрузки при-
|
|
|
|
|
|
|
|
РИС. |
3.15. |
|
|
|
|
|
|
|
|
Загрузочные |
устройства |
с |
регулированием |
движения |
грузопотока: |
|
|||||||||
а — с дополнительными |
упругими |
опорами; |
/ — основные |
упругие опооы- 2 — дополни |
||||||||||||
тельные упругие |
опоры; |
3 |
лоток; |
4 |
упругий шарнир; |
б — с |
телескопическими |
пла |
||||||||
стинами-лотками: |
/ — упругая шарнирная |
опора; |
2 — балка; |
з — винтовые |
стержни* |
|||||||||||
4 |
— пластины-лотки; |
в —с |
пневматической |
системой: |
|
/ — вентиль- |
2 — трубопровод* |
|||||||||
3 |
— козырек; 4 — опоры; |
5 — привод |
|
регулирующего |
клапана; |
б — сопла- |
7 — датчик |
|||||||||
скорости ленты; |
8 — датчик |
скорости |
грузопотока; |
9 — полости в |
днище |
лотка; |
г — |
|||||||||
с магнитной системой; / — лоток; 2 — магниты; 3 — обмотка |
|
|
|
|
ходятся на приемную часть. Упругое подвешивание пластин из-за эластичных элементов и упругих шарниров снижает их износ.
При погрузке скальной горной массы со значительным со держанием липких фракций трудно обеспечить заданный режим движения грузопотока по лотку. Одним из направлений созда ния системы автоматического регулирования движения грузопо тока в широком диапазоне изменения свойств горной массы является применение в лотках воздушного поддува от пневмати ческой системы (рис. 3.15, в). Криволинейная часть лотка выпол няется со сквозными полостями и перегородками. В полостях
устанавливают пневмосопла, которые через шланги, распредели тельный трубопровод и вентиль соединены с пневмомаги стралью. Пневмосопла расположены под острым углом к днищу желоба и могут поворачиваться. В приемной части лотка также устанавливают пневмосопла с предохранительным козырьком. Пневмосопла криволинейной части лотка имеют регулировочный клапан, который приводится в действие исполнительным меха низмом в виде индукционной катушки с сердечником. Лоток оснащается датчиком скорости грузопотока. Загрузочное уст ройство работает следующим образом. В момент включения кон вейера в работу через сопла криволинейной части лотка пода ется сжатый воздух под небольшим давлением. Сжатый воздух поступает и на приемную часть лотка. Расход воздуха в зависи мости от свойств поступаемого груза регулируется вентилем. При поступлении скальной горной массы с липкими включе ниями на приемной части лотка возникает так называемый «рас порный клин», который способствует зависанию части мате риала. Сжатый воздух оттесняет и поворачивает грузопоток в направлении днища лотка. Часть воздуха оказывается между днищем лотка и слоем груза, благодаря чему возникает эффект «воздушной подушки». При поступлении грузопотока на криво линейную часть лотка возрастает торможение грузопотока. По дача воздуха через полости в лотке позволяет ускорить движе ние грузопотока до заданной скорости. Если скорость грузопо тока на выходе устройства не равна скорости движения ленты приемного конвейера в исполнительный механизм, от датчиков скорости грузопотока и ленты поступают сигналы, которые по зволяют регулировать подачу воздуха через клапан и сопла.
На конвейерах, транспортирующих руды с ферромагнит ными свойствами, в качестве ускорителя движения грузопотока в лотках можно использовать бегущее магнитное поле (рис. 3.15,г). В таком устройстве под днищем криволинейной части лотка устанавливается дугообразный сердечник с индуктирую щей обмоткой. Криволинейная часть лотка закрывается сверху дугообразной крышкой. На крышке расположены съемные по стоянные магниты с большой коэрцитивной силой. Криволиней ная часть лотка выполняется из неферромагнитного электроизо ляционного износостойкого материала, например шлакоситалла. Устройство работает следующим образом. Поток ферромагнит ного электропроводящего груза (например, железной руды) по ступает в лоток и перемещается вниз под действием сил соб ственного веса. При поступлении груза на криволинейную часть лотка действие сил тяжести вдоль плоскости скольжения умень шается. Сердечник с индуктирующей обмоткой создает бегущее магнитное поле, которое индуктирует ток в частицах груза. Вследствие взаимодействия магнитных полей индуктора (сер дечника с обмоткой) и тока, индуктируемого в частицах груза, последний получает дополнительный движущий импульс. По стоянные магниты уменьшают нормальное давление груза на
днище лотка, а индуктирующая обмотка создает движущий им пульс, благодаря чему грузопоток ускоряется. Изменяя мощ ность, подводимую к индуктирующей обмотке, можно регулиро вать скорость движения грузопотока на выходе устройства в со ответствии со скоростью движения ленты приемного конвейера.
Применение подсыпки и уплотнений. При погрузке скальных кусковых грузов в некоторых случаях недостаточно применение загрузочных устройств (лотков) с формирующими и ускоряю щими грузопоток элементами. Исследованиями УкрНИИпроекта установлено, что вероятность удара кусков груза своими за остренными местами по ленте составляет 76%. Многократное ударное воздействие груза на рабочую обкладку приводит к ее разрушению. В этих условиях использование подсыпки из более мелкой фракции груза относится к весьма эффективным сред ствам, снижающим износ ленты. Кроме известных конструкций вибрационных питателей, хорошую подсыпку обеспечивают про стые по компоновке бесприводные грохоты с подпружиненными колосниками консольного типа и приемно-отбойной плитой, раз работанные Институтом горного дела Минчермета СССР и ис
пытанные в конвейерной |
линии Тургоякского рудоуправления |
||
в комплексе с самоходным дробильным |
агрегатом |
СДА-1000. |
|
В усовершенствованных |
вариантах таких |
грохотов |
(для лент |
шириной 1200 и 1600 мм), отличающихся повышенной долговеч ностью, колосники выполняются со съемной футеровкой толщи
ной |
100 мм — в 3 раза |
большей |
по |
толщине колосников |
(рис. |
3.16,а). Футеровка |
отливается |
из |
легированной стали |
713Л, обладающей почти в 2 раза большей износостойкостью, чем сталь Ст.З и увеличивающей срок службы колосников до
20мес.
Вузле сопряжения загрузочного устройства и приемной ча сти конвейера, оборудованной уплотнительными фартуками, из нос ленты может быть наибольшим из-за интенсивного вороше ния и скольжения мелкой фракции груза между торцевыми ча стями уплотнений и лентой. В этом случае целесообразно мел кую фракцию груза отводить за переднюю по ходу движения ленты стенку бункера (лотка). В таком бункере (лотке) име ется вертикальная перегородка, которая делит его на две ка меры (рис. 3.16,6). Одна камера имеет колосниковую решетку, расположенную с наклоном вниз по ходу движения ленты. Гор ная масса сначала попадает на колосниковую решетку. Здесь мелкая фракция просеивается и далее через течку поступает на
ленту. Крупные куски груза скатываются по колосникам и попа дают уже на слой подсыпки из мелкой фракции груза.
Наилучшими амортизирующими свойствами обладает диф ференцированная система подсыпки в несколько слоев, при ко торой увеличение размеров частиц подсыпки происходит в на правлении снизу вверх. С увеличением числа слоев расширяется зона распределения ударной нагрузки, и эффективность под сыпки возрастает. Дифференцированная схема подсыпки обеспе-
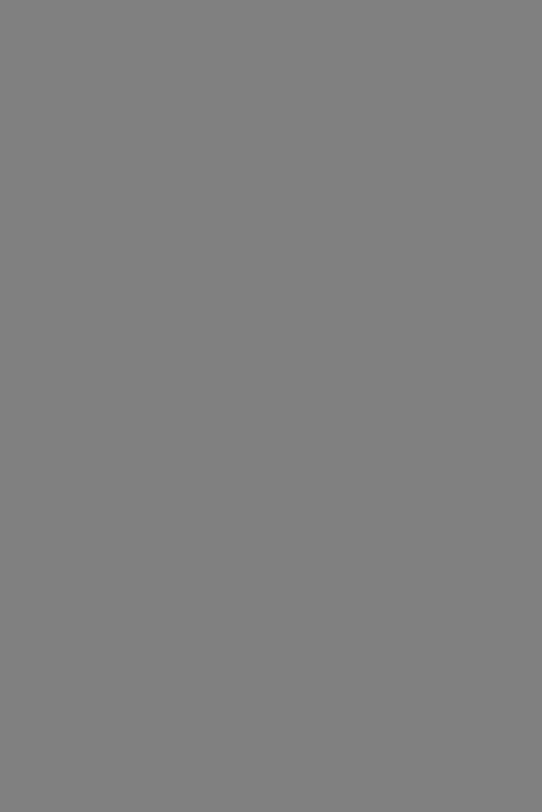
В комбинированных схемах доставки горной массы с при менением автомобильно-конвейерного транспорта загрузочный узел представляет собой комплекс дробильно-перегрузочных средств. В проекте реконструкции схемы доставки горной массы на угольном разрезе имени 50-летия Октября производ ственного объединения «Кемеровуголь» предусмотрено исполь зование двух параллельных комплексов оборудования произ водительностью до 2000 м3/ч (рис. 3.16, г). Горная масса, со стоящая из кусков размером до 1700 мм, автосамосвалами грузоподъемностью 75—180 т доставляется в приемный бун кер, из которого извлекается пластинчатым питателем и по дается на вибрационный колосниковый грохот. Надрешетный продукт поступает в щековую дробилку, а подрешетный про дукт и продукт дробления из бункера выгружаются валковым питателем, обеспечивающим подсыпку на ленточном конвейере. Для разрушения крупных кусков предусмотрено применение самой крупной в мире щековой дробилки ЩДП-21Х25 или ЩДП-15Х21 в комплекте с устройством роторного типа кон струкции УкрНИИпроекта для избирательного дробления не габаритов размером до 1700 мм.
3.4. ПРЕДУПРЕЖДЕНИЕ РАЗРУШЕНИЯ ПОСТОРОННИМИ ПРЕДМЕТАМИ И КОНТРОЛЬ
ЦЕЛОСТНОСТИ ЛЕНТЫ
3.4.1. ПРЕДУПРЕЖДЕНИЕ ВОЗНИКНОВЕНИЯ И РАЗВИТИЯ РАЗРУШЕНИИ ЛЕНТЫ
На многих ленточных конвейерах повышенной производи тельности, особенно эксплуатируемых на крупных ГОКах металлургических предприятий, имеет место аварийное разру шение дорогостоящих лент, связанное с попаданием в грузопо ток посторонних предметов. Например, длинномерный пред мет, поступающий на ленту вместе с грузом, пробивает ее и расклинивается между лотком и роликоопорой. В этом месте движущаяся лента разрезается на две продольные части до тех пор, пока длинномерный предмет не устранится или не разрушится. В другом случае длинномерный предмет может только расклиниться в загрузочном узле и затем протирает («пропиливает») ленту насквозь. Длинномерными предметами могут быть доски, бревна, ломы, пластины, элементы футеровок лотков, дробилок, грохотов, бункеров и др. Менее часто пробивают ленту и заклиниваются короткомерные предметы, однако они также могут быть причиной аварийного разруше ния ленты. Только на горно-обогатительном производстве Маг нитногорского металлургического комбината из-за продольных
порывов выходит из строя около 3000 м ленты в год при сроке службы лент на конвейерах от 10 до 24 мес. При величине
98
разрыва, равной 5,15 и 25 % ширины ленты, прочность ее умень шается соответственно на 30, 50 и 60 %.
В процессе эксплуатации ленты на ее внешней поверхности возникают видимые повреждения в виде разрывов на бортах ленты, отдельных лоскутов на верхней или нижней поверхности ленты, которые могут развиваться, если вовремя не принима ются предохранительные меры. Не менее опасны и скрытые от визуального наблюдения внутренние повреждения или де фекты в ленте.
Таким образом, к мероприятиям, предупреждающим раз рушение и контролирующим целостность лент, должно уде ляться повышенное внимание. К этим мероприятиям относятся: удаление посторонних предметов; предупреждение возникнове ния разрушений при наличии посторонних предметов; предуп реждение развития возникших разрушений при наличии по сторонних предметов: контроль внешней и внутренней целост ности лент.
На ленточных конвейерах в узлах перегрузки нашли при менение механические и электромагнитные (для ферромагнит ных грузов) отделители посторонних предметов. Механическиеотделители имеют рабочий орган в виде ротора с гребенкой. Длинномерные предметы (обычно из дерева) попадают на гребенку вращающегося ротора и под действием центробежных сил отбрасываются на отводящий лоток. Гребенка может быть сблокирована с датчиком. При ее повороте под действием длинномерного предмета срабатывает датчик и привод кон вейера отключается. При редком поступлении посторонних фер ромагнитных предметов в загрузочный узел целесообразна ус тановка приводного лотка-ловушки (рис. 3.17, а). На разгру зочном барабане устанавливается магнитный датчик. Если в зону действия датчика попадает посторонний предмет, он подает сигнал на привод лотка-ловушки. Последний устанав ливается в рабочее положение так, что в него попадает по сторонний предмет, который затем после поворота лотка пе ремещается на отводящий лоток. Наибольшее распростране ние получили магнитные и электромагнитные отделители. Они устанавливаются на линейной части конвейера или разгрузоч ной части. Датчиком на линейной части конвейера может слу жить вибрационный прибор, регистрирующий ударные на грузки от тяжелых посторонних предметов. Посторонний пред мет удаляется вручную или вспомогательными средствами.
Московским геологоразведочным институтом разработан от делитель ферромагнитных предметов, выполняемый в виде на клонного лотка с магнитами (рис. 3.17, б). Над лотком монти руются магниты, с помощью которых посторонние предметы скольжением перемещаются к отводящим элементам. Сила воз действия магнитов уменьшается в направлении лотка.
Электромагнитные отделители выпускают подвесного, шкивного и барабанного типов. Подвесные саморазгружаю-
4* |
99 |
|
|
|
РИС. |
3.17. |
|
|
|
|
Устройства для удаления |
посторонних предметов: |
|
||||
а — приводной лоток-ловушка: |
1— датчик; |
2 — лоток-ловушка; 3 — отводящий лоток; |
|||||
4 — привод; |
б —лоток с |
магнитами: / — лоток; |
2 — магниты; 3 — отводящие элементы; |
||||
4 — грохот; |
5 — предмет; |
в — электромагнитный |
шкив: / — шкив; |
2 — предмет; |
3 — |
||
течка; г — электромагнитный |
барабан: / — барабан; 2 — магниты; |
3 — предмет; |
4 — |
||||
|
|
|
течка; 5 — электромагнит |
|
|
щиеся отделители ПС-120 и ПС-160 для лент шириной до 1200
и1600 мм чаще устанавливаются над линейной частью кон вейера и позволяют удалять предметы массой до 25 кг. Шкивные отделители Ш65-63, Ш100-80 и Ш140-100 устанавливаются в загрузочных узлах и выполняют роль приводных или неприводИых барабанов. При вращении шкива (рис. 3.17, е ) не магнитный материал разгружается под действием сил инерции
исобственного веса, а ферромагнитные предметы уносятся под
шкив и разгружаются |
после него. |
Барабанный |
отделитель |
Ж Б140-100 (рис. 3.17, г) |
в рудничном |
исполнении |
предназна |
чен для извлечения посторонних предметов непосредственно с конвейера. Он имеет электромагнит для извлечения ферро магнитных предметов и постоянные магниты, служащие для передачи предметов в отводящий лоток. Известны также элек тромагнитные отделители конвейерного типа, подвешиваемые над разгрузочным барабаном конвейера и состоящие из лен точного контура с электромагнитным барабаном и магнитом, способствующим притяжению предметов к ленте.
Находят применение средства, предупреждающие возникно вение разрушающего воздействия на ленту посторонним пред метом, так как своевременно отключают привод конвейера. Функцию защитного устройства выполняет, например, установ ленный под бункером подвижный лоток с тележкой (рис.3.18,а). Тележка от перемещения ее движущимся грузо потоком удерживается контргрузом, подвешенным через блок на канате, и снабжена рычагом, взаимодействующим с конеч ным выключателем привода конвейера. Посторонний пред мет, расклиниваясь в узле загрузки, нажимает на стенки лотка и перемещает его вместе с тележкой. Конечный выключатель срабатывает, и привод конвейера отключается. Бункер с лот ком может монтироваться совместно с роликоопорами загру зочной части конвейера на подпружиненной подвижной раме, подвешенной к опорной металлоконструкции. Пружины при дают подвижной раме устойчивость и ограничивают ее пере мещение в направлении движения ленты. При этом опорная металлоконструкция имеет вал, соединенный посредством ры чага и каната с подвижной рамой. Вал снабжен противовесом и кулачком, воздействующим на датчик. При заклинивании ленты в узле загрузки посторонним предметом подвижная рама перемещается вместе с лентой. Канат поворачивает рычаг вала, и кулачок воздействует на конечный выключатель привода. Функцию устройств, предупреждающих возникновение разру шения лент при наличии посторонних предметов, выполняют также загрузочные части става конвейера, выполненные в виде неподвижных опор скольжения. Посторонний предмет может пробить ленту, но, ударившись о днище опор скольжения, от скакивает от него, благодаря чему исключается расклинивание ленты.
Предупреждение развития возникающих разрушений поз воляет избежать продольных разрывов ленты на большой длине. После замены поврежденного отрезка ленты новым лента опять пригодна к работе. Обычно посторонний предмет расклинивается между стенками лотка и роликоопорами кон вейера. Это обстоятельство позволяет использовать роликоопоры в схеме защиты ленты от разрыва. В конструкции ус тройства для защиты ленты, разработанного ГПКИ Союзпроммеханизация, несколько жестких роликоопор устанавливаются на тележке с противовесами. При сквозном разрыве ленты по сторонний предмет взаимодействует с роликоопорой и переме-
Z |
3 |
* |
5 |
щает тележку по ходу движения ленты. Конечный выключа тель срабатывает, и привод конвейера отключается. Тележка может оснащаться упорами, взаимодействующими через пру жины с неподвижными упорами, установленными на раме (рис. 3.18, б). Движение тележки ограничивается неподвиж ными упорами, в то время как другой упор взаимодействует с конечным выключателем привода. Устройства данного типа нашли применение на многих металлургических предприятиях.
Меньшую металлоемкость имеет устройство с поворотными роликоопорами (рис. 3.18, в). Роликоопоры крепятся на швел лерах, которые с одной стороны посредством пластин присое диняются к раме шарнирно, а с другой — пружинами. Посто ронний предмет воздействует на одну из роликоопор, повора чивает ее, и тросик, прикрепленный к боковому кронштейну роликоопоры, поворачивают стойку, воздействующую на ко нечный выключатель привода.
На Новокриворожском горно-обогатительном комбинате ис пытано устройство конвейерного типа для защиты ленты от разрыва (рис. 3.18, г). Оно представляет собой короткий вспо могательный конвейер, установленный под грузонесущей лен той в месте загрузки. Лента вспомогательного конвейера при водится в движение грузонесущей лентой. Один из барабанов вспомогательного конвейера оборудован тахогенераггорным дат чиком реле скорости. При сквозном пробое обеих конвейерных лент и расклинивании постороннего предмета между роликоопорой и лотком загрузочного устройства лента вспомогатель ного конвейера останавливается. Это фиксируется тахогенераторным датчиком, и конвейер отключается. Достоинствами устройства являются повышенная амортизирующая способность загрузочной секции конвейера, уменьшение вероятности попа дания кусков груза под направляющие борта. Вспомогатель ная лента может быть выполнена с отверстиями или решетчатой. При пробивании грузонесущей ленты посторонним предметом
он попадает в отверстие, останавливает |
вспомогательную |
ленту, в результате чего привод конвейера |
отключается. |
Простую компоновку имеют контактные устройства для за щиты ленты от разрыва. Они представляют собой контактные пластины, монтируемые между роликоопорами загрузочной ча сти конвейера. При пробивании ленты посторонним предметом конец его нажимает на контактные пластины и замыкает их.
Срабатывает |
электрическая |
цепь управления приводом кон- |
|||||||
|
|
|
|
РИС. 3.18. |
|
|
|
|
|
Устройства, предупреждающие |
возникновение и |
развитие |
разрушений |
||||||
|
|
|
|
в лейте: |
|
|
|
|
|
■а —с |
подвижным |
лотком: |
/ — лоток; |
2 — тележка; |
3 — контргруз; |
4 — выключатель; |
|||
-б —с |
тележкой, |
имеющей |
подпружиненные |
упоры: |
/ — посторонний |
предмет; 2 — те |
|||
лежка; 3 — выключатель; |
4 — упоры; |
о — с |
поворотными |
роликоопорами: |
/ — поворот |
||||
ная |
роликоопора; |
2 —стойка; 3 —тросик; |
4 — опорная |
пружина; |
5 — шарнир; г — |
свспомогательной лентой: / — грузонесущая лента; 2 — вспомогательная лента; 3 —
посторонний предмет
вейера. Известны также устройства, работающие на принципе изменения давления воздуха при пробивании ленты посторон ним предметом. Одновременно пробивается пневматическая ка мера, выполненная в виде ролика с упругой обечайкой или не подвижного кожуха с повышенным давлением внутри.
3.4.2. КОНТРОЛЬ ВНЕШНЕЙ И ВНУТРЕННЕЙ ЦЕЛОСТНОСТИ ЛЕНТЫ
Своевременное обнаружение повреждений в лентах поз воляет повысить срок их эксплуатации при минимальных зат ратах на ремонт. К применяемым для контроля внешней целостности ленты относятся устройства, работающие по прин ципу обнаружения просыпи, контактные, вибрационные, пнев матические, с использованием проникающего излучения.
Устройства, работающие по принципу обнаружения про сыпи, имеют простую конструкцию. Для обнаружения просыпи может быть использован зигзагообразный провод, закреплен ный на изоляторах под лентой. Провод располагается с неболь шим зазором над заземленным металлическим листом пере крытия и подключен к реле контроля ИКС-2Н. При возник новении в ленте трещины или продольного разреза образуется просыпь, уменьшающая сопротивление между проводом и лис том перекрытия. Происходит срабатывание реле, и конвейер останавливается.
Испытан другой вариант устройства с аналогичным прин ципом работы. Под лентой располагается лоток из двух метал лических пластин, в зазоре между которыми монтируется элек трод. При разрыве ленты просыпь попадает в зазор, после чего срабатывает промежуточное реле, отключающее конвейер. Для ускорения процесса обнаружения повреждений в ленте применяются два ряда металлических щеток, расположенных под лентой. Щетки закреплены на изоляторах и находятся в контакте с лентой. Усилие прижатия щеток к ленте регулиру ется посредством перемещения направляющих втулок. Щетки электрически соединены с реле ИКС-2Н. При разрезе ленты рудная просыпь (рис. 3.19, а) попадает в разрез сверху, а снизу в него заходят проволочки щеток. Происходит резкое изменение электрического сопротивления контролируемого участка, сра батывает реле ИКС-2Н, и конвейер отключается. В качестве регистрирующего прибора могут быть использованы источник: излучения и детектор (рис. 3.19,6). Они расположены под грузонесущей ветвью ленты с двух сторон конвейерного става. При образовании продольного разреза ленты просыпь уменьшает поток излучения, поступающего в детектор. Срабатывает ре лейный блок, и конвейер останавливается. В качестве детекто ров используются газоразрядные счетчики СБМ-19, а релейных блоков — серийно выпускаемые отечественные приборы типа БР-7, БР-8. Устройство прошло опытную проверку. Повышение

надежности контроля возникновения сквозных повреждений до стигается применением специальных роликов с выступами. При взаимодействии ленты с выступами роликов происходит расши рение трещин и порезов, имеющихся в ленте, и более интенсив ное образование просыпи.
Простую конструкцию имеет приспособление в виде наклон
ного листа или лотка, с одной стороны снабженного шарниром, а с другой — пружиной. При попадании просыпи на лист (или лоток) он поворачивается и воздействует на выключатель при вода. Лотки могут быть установлены в сочетании с источником излучения.
Контактные устройства. При сильном повреждении ленты на ее нижней поверхности в средней части или на кромках ленты образуются задиры в виде лоскутов, которые можно использо
вать |
для воздействия на рабочие элементы |
системы защиты. |
В |
контактных устройствах (рис. 3.19, в) |
скользящего типа |
рабочие элементы в виде гибкой пластины закрепляются на
кронштейне и имеют шарнирную тягу, которая соединяется суп ругой консольной балочкой с контактом на конце. При набе гании пластины на выступающий разрыв ленты она увлекается им и поворачивает тягу, в результате чего происходит сраба тывание цепи управления.
На шахте «Западная» производственного объединения «Интауголь» используется приспособление для защиты ленты от по рыва, выполненное из поворотной рамки (рис. 3.19,г). Рамка имеет верхнюю и нижнюю части. К последней прикреплен трос, который сблокирован с реле ИКС-2Н. Выступающий лоскут ленты поворачивает рамку, после чего трос включает реле ИКС-2Н и соответственно систему сигнализации.
В ГДР и Японии широко используются простые по компо новке устройства защиты ленты, выполненные в виде электро проводников. Они изготавливаются из медной или стальной про волоки с малой прочностью на разрыв. Проволока натягивается) под лентой между стойками. Оборвавшийся участок поверхно сти ленты набегает на проволоку и обрывает ее, после чеговключается сигнализация.
Рабочим органом вибрационных устройств (рис. 3.19, (9) служит вибрационный элемент, выполненный, например, в виде эксцентриковой шайбы. Она устанавливается консольно на валу и имеет выступы, взаимодействующие с краем ленты. На дру гом краю ленты располагается диск с приемником колебаний. Лента является «волноводом» для передачи вынужденных ко лебаний от вибрационного элемента приемнику колебаний. При возникновении продольных разрывов ленты амплитуда вынуж денных колебаний ленты в зоне приемника уменьшается. При емник вырабатывает управляющий сигнал, и реле отключает привод конвейера.
Пневматические устройства (рис. 3.19, в) работают при сквозных разрывах ленты по принципу регистрации изменения
106
давления в камере прибора. Камера устанавливается под лен
той и прижимается к ней посредством рычажного механизма с контргрузом через уплотнения. В камеру через форсунку по дается сжатый воздух, давление которого контролируется дат чиком. Рычажный механизм монтируется на подвижном держа теле, установленном на направляющей. Перемещение держа теля осуществляется гидроцилиндром. Держатель совершает возвратно-поступательное перемещение, благодаря чему контро лируются повреждения по всей ширине ленты. Когда камера оказывается под повреждением насквозь участком ленты, дав ление в камере падает и датчик вырабатывает сигнал для сиг нализации. Камера может иметь ширину, равную ширине кон тролируемого участка ленты, и в этом случае монтируется ста ционарно.
Устройства с использованием проникающего излучения. Из устройств данного типа (рис. 3.19, ж) на металлургических пред приятиях широко применяются рентгенодефектоскоп РДЛ-1 и гамма-дефектоскоп УДК. Рентгенодефектоскоп РДЛ-1 основан на проникающем излучении рентгеновских лучей, интенсивность поглощения которых меняется при возникновении дефектов в материале. Выявление повреждений в ленте осуществляется по изменению изображения на экране или фотопленке. Гаммадефектоскоп УДК предназначен для контроля состояния сты ков и отдельных участков ленты. Проведение дефектоскопии требует остановки конвейера.
Принцип контроля основан на регистрации изменения иони зирующего излучения контролируемой среды. Аппаратура вклю чает в себя датчики повреждения ленты, источники ионизирую щего излучения (детектор) и электронный блок. Имеются дат чики для обнаружения повреждений негруженой и груженой ленты. Каждый датчик снабжен источником ионизирующего из лучения. Датчики негруженой ленты срабатывают при резком изменении интенсивности ионизирующего излучения, проходя щего через ленту. Эти изменения возникают при порезах и про
боях ленты. Датчики имеют удлиненную форму. Их число зави сит от ширины ленты, каждый датчик обеспечивает контроль полосы ленты шириной 600 мм. Датчики срабатывают при по явлении повреждений в ленте шириной не менее 2 мм. Поток ионизирующего излучения в датчиках регистрируется газораз рядным счетчиком СБМ-13. Сигнал со счетчиков в блоках де тектирования усиливается, калибруется и через соединительный кабель поступает на один из пяти входов электронного блока. В блоке сигнал проходит соответствующую интегрирующую це почку, подключенную к стрелочному прибору визуального конт роля состояния ленты. С интегрирующих цепей через логиче скую схему сигнал подается в анализатор, который сравнивает его с величиной опорного сигнала. При отклонении значения сигнала от опорного срабатывает реле. Включается сигнализа ция, и отключается привод конвейера. Повторный запуск кон-
вейера осуществляется после устранения повреждения нажа тием кнопки пуска на панели электронного блока. Рассмотрен ную аппаратуру для обнаружения повреждений в ленте реко мендуется применять на мощных конвейерах.
Резкое ухудшение прочностных показателей лент мощных конвейеров связано не только с внешним нарушением целост ности. Нередко процесс разрушения ленты начинается изнутри и связан с разрывом тяговых и грузонесущих элементов (ни тей, тросов, корда, упрочняющих вставок). Такие нарушения целостности ленты также должны контролироваться. Известны следующие устройства для контроля внутренней и внешней це лостности ленты: электромагнитные, электроконтактные, с ис пользованием световодом и пьезоэлектрические.
К электромагнитным устройствам относятся устройства кон троля целостности резинотросовых лент, а также лент специ альной конструкции (со вставками различного типа). Для кон троля резинотросовых лент могут быть эффективно использо ваны магнитные свойства тросов. Феррозондовые датчики весьма чувствительны к изменению магнитного поля в местах повреждения тросов. Контроль повреждений тросов возможен также в режиме остаточного намагничивания, что упрощает процесс контроля лент в подземных условиях.
Гипроуглеавтоматизацией совместно с Днепропетровским за водом шахтной автоматики разработано устройство УКЦТ-1 для профилактического контроля целостности тросов, основан ное на феррозондовой дефектоскопии. Оно содержит электрон ный блок, намагничивающий элемент, магнитомодуляционные датчики для обнаружения повреждений при подвижной ленте и определения места и числа поврежденных тросов на неподвиж ной ленте.
В резинотросовых лентах легко получить замыкание цепи для индуктирования в ней электрических сигналов, которые за тем регистрируются датчиками. Для этого крайние тросы пе ремыкаются проводами и образуют с ними замкнутые контуры (рис. 3.20,а). При возникновении внутренних повреждений в ленте прерывается поступление сигналов, и устройство сраба тывает. В другом варианте получают группу магнитных или электромагнитных контуров, замыкающих несколько тросов, в каждой группе. В более сложных универсальных схемах спе циальный прибор вырабатывает сигнал переменного тока с им пульсной модуляцией. Модулированные сигналы, проходящие через ленту, изменяют свою характеристику при прохождении поврежденных участков ленты (резинотросовой или резинотка невой) и преобразуются в постоянный ток, значение которого сравнивается с эталонным.
К универсальным средствам контроля целостности ленты относятся также схемы, в которых используются специальные самостоятельные элементы, встраиваемые внутрь резинотросо вой или резинотканевой ленты и выполняющие функцию дат-
|
|
|
|
РИС. 3.20. |
|
|
|
|
|
||
Устройства для |
контроля |
внешней |
н внутренней |
целостности |
лент: |
||||||
а — электромагнитное: |
/ — лента; |
2 — тросы; |
3 — провод; б — то |
же: / — передающая* |
|||||||
электромагнитная обмотка; |
2 — лента; |
3 — контур; |
4 — приемная |
электромагнитная об |
|||||||
мотка; |
5 — исполнительный |
механизм; |
в — то |
же: |
/ — лента; |
2 — контур; |
3 — краевой |
||||
проводник; 4 — контроллер; |
г — то |
же: |
/ — лента; |
2 — магнитный резиновый |
элемент; |
||||||
3 — ферромагнитный элемент; д — электроконтактное: / — элсктропроводник; |
2 — кон |
||||||||||
такт; |
3 — контактный |
диск; |
4 — реле; |
в — с |
использованием |
световодов: |
/ — излуча |
||||
|
|
тель; 2 — световод; 3 — светоприемиик |
|
|
|
|
чиков повреждений. Это могут быть групповые контуры из от дельных тросиков или проволоки, встраиваемые в ленту. Кон туры, как правило, имеют многоступенчатую петлеобразную форму (рис. 3.20,6), иногда оснащаются индуктивными катуш ками. С одной стороны ленты монтируется передающая элек-
тромагнитная обмотка, а с другой — приемная с усилителем. При обрыве контура ток в нем не возникает, и система сраба тывает. В США используют медные контуры в виде одной сину соидальной петли, от которой через определенный интервал проходят к краям ленты проводники (рис. 3.20, в). Ток в кон туре возникает под действием переменного внешнего магнит ного потока. При повреждении ленты ток исчезает. Участок по вреждения ленты быстро обнаруживается при включении в цепь контроля краевых проводников. Срабатывает реле, и привод конвейера отключается.
В Японии широкое распространение для контроля целост ности лент получили магнитные элементы. В ленту встраива
ется |
система резиновых магнитов (рис. 3.20, г), |
устанавливае |
мых |
со смещением по ширине ленты. Вплотную |
к магнитикам |
располагаются ферромагнитные элементы, выходящие к поверх ности ленты и служащие для передачи магнитного потока
кдатчикам. При разрыве ленты происходит смещение магнитов
иферромагнитных элементов, в результате чего интенсивность
регистрируемого магнитного потока возрастает. Срабатывает датчик, и привод конвейера отключается.
Электроконтактные устройства (рис. 3.20, (?) редко приме няются для контроля целостности лент, транспортирующих сы пучие грузы. Встраиваемые в ленту элементы выполняются электропроводными, располагаются по всей ширине ленты и взаимодействуют с неподвижными или подвижными (диско выми) контактами (щетками). Последние включаются в элек трическую цепь с исполнительным реле, которое срабатывает при повреждении электропроводника. Целесообразно вместо специальных контактов, взаимодействующих с электропровод ными элементами ленты, использовать роликоопоры. Для этого в обечайку роликов помещаются контакты, взаимодействующие с электропроводными элементами ленты и щетками, включен ными в электрическую цепь управления.
В устройствах с использованием световодов в качестве пер вичных датчиков используются световоды (рис. 3.20, в) из стек
ловолокна, обладающие эластичностью и встраиваемые в ленту вулканизацией. Световоды располагаются поперек ленты под некоторым углом, чтобы излучатель света и светоприемиик •были смещены относительно друг друга для исключения взаим ного воздействия. При отсутствии повреждений в ленте свет от излучателя через световод попадает в светоприемиик. Наруше ние режима подачи световых сигналов свидетельствует о нали чии повреждения в ленте. Световоды могут быть зигзагообраз ной формы и располагаться в виде отдельных отрезков с опре деленным шагом по длине ленты. Концы световодов обычно помещаются в защитные трубки и располагаются в углубле ниях, выполненных на кромках ленты и прикрытых прозрачной пленкой, предохраняющей световоды от загрязнения. Преду сматриваются также очистительные щетки, устанавливаемые
НО
с боков ленты и служащие для удаления грязи с пленок в мо мент прохождения световодов относительно регистрирующей ап паратуры.
3.5.КОНТРОЛЬ СКОРОСТИ И ПРОБУКСОВКИ ЛЕНТ
ВПОДЗЕМНЫХ УСЛОВИЯХ
При эксплуатации мощных ленточных конвейеров в шахтах и рудниках средствам контроля скорости и пробуксовки лент уделяется большое внимание. Значительное проскальзывание ленты относительно приводного барабана ведет к быстрому на греванию пары лента — обечайка (футеровка) барабана и воз можному воспламенению ленты и окружающей газовой среды. Имеет место также интенсивный износ обкладок в виде срывов,, прожогов до каркаса и износ футеровки барабана. Образуются: завалы в загрузочных узлах. Известные средства контроля про буксовки лент можно подразделить на три группы: механиче ские, электрические и электронные, температурные. Для первых двух групп устройств характерна регистрация изменения скоро сти или возникновения пробуксовки ленты при номинальной ча стоте вращения приводного барабана, для третьей группы уст ройств— только пробуксовки.
Механические устройства контроля. В технике измерений применяются многие типы устройств для контроля скорости, движения грузонесущего органа. К ним относятся фрикцион ные, центробежные и гидравлические регуляторы. В устройствах фрикционного типа обычно первичным элементом служит фрик ционный ролик (рис. 3.21,а). Ось ролика устанавливается на поворотном рычаге с противовесом. Ролик на торце имеет по воротную пружинную скобу с тормозной накладкой, с которой взаимодействует ось ролика. В нейтральном положении пру жинную скобу удерживает пластинчатая пружина. Балансир служит для уравновешивания скобы при вращении ролика. Под
роликом и лентой устанавливается опора с некоторым подъемом в сторону движения холостой ветви ленты. При отсутствии про буксовки лента движется с номинальной скоростью и фрикци онный ролик вращается. Под действием центробежных сил скоба преодолевает сопротивление пластинчатой пружины и по ворачивается. Тормозная накладка взаимодействует с осьюролика, возникает повышенное сопротивление вращению ро лика, и рычаг вместе с роликом поворачивается, замыкая цепь управления с реле времени. При возникновении пробуксовки рычаг возвращается в исходное положение, так как уменьша ются действие центробежных сил и сопротивление вращениюроликов. После некоторой выдержки времени, задаваемой релевремени, если пробуксовка не исчезает, привод конвейера от ключается. Чтобы устройство позволяло включать конвейер, ис пользуется соответствующая блокировка.
lit
Устройства для контроля скорости и пробуксовки лент:
а — механическое: |
/ — фрикционный |
ролик; |
2 — рычаг; |
3 — опора; |
4 — балансир; |
5 — |
|||||||||||||||
пружинная |
скоба; |
6 — тормозная |
накладка; |
|
б —электронное |
с |
датчиками |
|
скорости |
||||||||||||
ленты: |
/ — датчик |
скорости |
ленты; |
2 —датчик скорости приводного |
барабана; |
3 — до |
|||||||||||||||
полннтельный |
транзистор; |
4 — усилитель-ограничитель; |
5 — мультивибратор; |
6 — срав |
|||||||||||||||||
нивающее |
устройство; |
7 — измерительный |
прибор; |
8 — интегрирующее устройство; |
9 — |
||||||||||||||||
пороговое |
устройство; |
10 — исполнительный |
|
орган; |
в — то же, |
с |
микрофоном: |
/ — ми |
|||||||||||||
крофон; |
2 — трансформатор |
для микрофона; |
3 — усилитель; |
4 — анализатор; |
5 —транс |
||||||||||||||||
форматор |
исполнительного |
блока; |
|
6 — исполнительные |
реле; |
|
г — температурное с |
би |
|||||||||||||
металлической |
пластиной: |
/ — обечайка |
|
барабана; |
2 — биметаллическая |
пластина; |
|||||||||||||||
3 — рычаг; |
4 — выключатель; д — то же, |
с |
термобаллонами: |
/ — термобаллоны; |
2 — |
||||||||||||||||
капиллярные трубки; |
3 — пружина |
|
манометра; |
4 — выключатель; |
е —то |
же, |
с |
магнит |
|||||||||||||
ным выключателем: / — канал; 2 — оболочка; |
3 — магниты; |
4 — контакт |
магнита; |
5 — |
|||||||||||||||||
|
|
|
|
|
контакт |
выключателя; 6 — пружина |
|
|
|
|
|
|
|
В центробежных устройствах контроля пробуксовки ленты вращательное движение поворотных рычагов преобразуется в поступательное движение скользящей подвижной втулки, ко торая взаимодействует с конечным выключателем. Гидравличе ские устройства представляют собой тихоходный роторный мае-
ляный насос. В процессе нормальной работы конвейера ротор, кинематически связанный с движущейся лентой, вращается и подает под давлением масло в систему управления с поршнями
имеханизмом выдержки времени. При снижении скорости ленты ротор насоса останавливается, включается реле времени
ипривод конвейера после некоторой задержки отключается.
Электрические и электронные устройства контроля. Наи
большее распространение получили электрические и электрон ные устройства контроля скорости и пробуксовки лент. К дат чикам скорости лент тахогенераторного типа относятся датчики УПДС-2, ДС, PC-67, РСА, УКСП. Последний обеспечивает контроль превышения или уменьшения скорости ленты от задан ного значения с дистанционным переключением настройки реле на одну из скоростей ленты. Основной элемент тахогенераторных датчиков — магнитоиндукционный генератор однофазного переменного тока. Статор генератора приводится во вращение фрикционным роликом, поджимаемым пружиной к ленте.
Пробуксовка ленты контролируется с использованием элек трических и электронных средств автоматики. Аппарат АКП-1 предназначен для контроля пробуксовки ленты относительно приводного барабана в период пуска и работы конвейера. Ско рость и пробуксовка ленты контролируются соответственно в пределах 5 м/с и 10—25 %. В состав аппарата входят два тахогенераторных датчика УПДС, один из которых кинематиче ски связан с лентой, а другой с приводным барабаном. Частоты сигналов двух датчиков поступают в электронный блок сравне ния. Если разница в частотах сигналов превышает допустимую, формируется управляющий импульс на отключение привода конвейера.
Особые требования предъявляются к электронным устрой ствам пробуксовки ленты, работающим в период пуска конвей ера, когда скорость привода регулируется. В конструкции устройства, разработанного Ворошиловградским филиалом Гипроуглеавтоматизации, сигнал от датчика скорости ленты поступает на вход усилителя-ограничителя, формулирующего прямоугольные импульсы, длительность которых обратно про порциональна, а частота следования прямо пропорциональна скорости ленты (рис. 3.21,6). При пробуксовке ленты возникает разность в импульсах усилителя-ограничителя и мультивибра тора, значение которой прямо пропорционально величине про буксовке ленты.
При применении для барабана тахогенераторного датчика скорости постоянного тока его выход подсоединяют к базе тран зистора. Если в качестве такого датчика используют тахогенераторный датчик скорости переменного тока, его выход под
соединяют с базой дополнительного транзистора через выпря митель и сглаживающий фильтр.
На ленточных конвейерах карьеров ФРГ успешно применя ется способ контроля пробуксовки ленты, основанный на изме-
рении и сравнивании частоты сигналов, поступающих от при водного и отклоняющего барабанов. Для этой дели исполь зуют два ферромагнитных бесконтактных датчика, устанавли ваемые на приводном и отклоняющем барабанах. Во избежание влияния вытяжки ленты на результаты измерений расстояние между приводным и отклоняющим барабанами выбирается не менее 10 м. Сигналы от датчиков частоты вращения барабанов поступают в счетчики импульсов с диапазоном счета от 1 до 99. По истечении заданного времени счетчики автоматически сбрасывают свои показания и начинают вести счет снова. Сиг налы от счетчиков поступают в блок памяти и сравнения. По следний блок вырабатывает сигнал на отключение привода кон вейера, если проскальзывание ленты составляет более 2% . При задании расчетной разности импульсов учитываются пере даточное отношение редукторов, диаметры барабанов, частота вращения двигателя и скорость движения ленты.
В качестве датчика пробуксовки ленты на приводном бара бане может быть использован микрофон (рис. 3.21, в), установ ленный возле обечайки барабана и реагирующий на частотный сигнал, сопровождающий пробуксовку. Микрофон подключа ется одним концом к части вторичной обмотки трансформатора,, воспринимающего сигналы генератора, а другим через усили тель— к входу анализатора. Последний соединен с исполни тельным блоком, содержащим трансформатор, к вторичной обмотке которого подключены последовательно исполнитель ные реле, настроенные на сигналы микрофона и генератора.
Температурные устройства контроля. Одновременно с про скальзыванием ленты на барабане происходит быстрое их на гревание, которое может достигать больших значений. Это об стоятельство позволяет в качестве средства контроля пробук совки ленты использовать температурные датчики. Достоинство температурных датчиков — регистрация при минимальном числе ложных отключений привода. На подземных ленточных конвейерах используется серийно выпускаемая аппаратура кон троля нагрева обечайки футерованного приводного барабана для защиты ленты от воспламенения при пробусовке. В комп лект аппаратуры входят блок сигнализации температуры БСТ-1, термодатчик ТД-1, токосъемник, генератор высокой ча стоты ТСВ-1, блок питания, усилитель постоянного тока, резо нансный усилитель и исполнительные механизмы. Термодатчик состоит из полой стальной шпильки, внутри которой имеется термочувствительный элемент в виде трехобмоточного транс форматора с ферритовым сердечником; термодатчик встраива ется в обечайку барабана. Принцип работы термочувствитель ного элемента основан на изменении ферромагнитных свойств сердечника в зависимости от температуры. При пробуксовке обечайки барабана, а затем и сердечник трансформатора нагре ваются. Когда температура обечайки достигает 65 °С, происхо дит значительное уменьшение магнитной проницаемости сер
дечника датчика, магнитное сопротивление возрастает, а уро вень сигнала, генерируемого генератором высокой частоты, 1резко снижается. Уменьшение уровня сигнала на входе блока •сигнализации приводит к включению исполнительного реле. Конвейер отключается одновременно с включением световой сиг нализации. Повторно конвейер может включиться только после снижения температуры на 5—7 °С. Аппаратура обеспечивает автоматический контроль неисправности цепей термодатчика и других элементов.
В качестве температурных датчиков в устройствах автома тики успешно применяются биметаллические пластины (рис. 3.21,г). Такая пластина с отогнутым концом монтируется на обечайки барабана. Отогнутый конец пластины в нормальном положении удерживает поворотный рычаг, который стремится повернуться под действием пружины. При буксовке ленты обе чайка барабана и пластина нагреваются. За счет разности ко эффициентов теплового расширения металлов, из которых со стоит пластина, ее свободный конец изгибается и освобождает рычаг. Под действием пружины рычаг поворачивается и нажи мает на выключатель привода конвейера. В ГДР в качестве температурных датчиков пробуксовки ленты применяют прово локу, встраиваемую с натяжением под обечайкой барабана. Проволока состоит из отдельных отрезков, соединенных легко плавкими пайками. Один конец проволоки соединен с подпру жиненным стержнем. При пробуксовке ленты нагреваются •обечайка барабана и места пайки. Проволока обрывается, и пружина поворачивает стержень, который воздействует на вы ключатель привода конвейера. Недостатком конструкции яв ляется необходимость в монтаже новой проволоки после сраба тывания устройства.
Менее трудоемки в регулировке устройства для контроля пробуксовки ленты, выполненные в виде термобаллонов (рис. 3.21,5), заполняемых рабочей жидкостью, расширяю щейся при нагревании. Термобаллоны соединяются капилляр ными трубками и монтируются в пазах футеровки барабана с небольшим превышением над его поверхностью. Капилляр ные трубки подключены к манометру с пружиной, взаимодей ствующей с контактной пластиной. При возникновении про буксовки ленты термобаллоны под действием сил трения на греваются. Тепло сообщается рабочему веществу, при расши рении которого в капиллярных трубках повышается давление. Пружина манометра выпрямляется и при вращении барабана набегает на контактную пластину и отклоняет ее. Устройство вырабатывает сигнал о возникновении пробуксовки и в случае необходимости отключает привод. Манометр с пружиной и кон тактная пластина могут быть заменены магнитным выключа телем (рис. 3.21, е). В таком устройстве к внутренней поверх ности обечайки приводного барабана прикрепляется отрезок трубы, выполняющий роль полости термодатчика с жидкостью,
не замерзающей при отрицательной температуре. Один конец канала служит для наполнения и слива жидкости из его по лости и закручивается герметичной пробкой. Другой конец соединяется с упругой оболочкой с постоянным магнитом. Вы ключатель привода конвейера содержит постоянный магнит с контактом, прижатым к контактам цепи отключения пружи ной. При появлении проскальзывания ленты по барабану тем пература жидкости в канале увеличивается, что приводит к де формированию упругой оболочки, полость которой сообщена* с полостью канала, и перемещению магнита. Приближение маг
нита |
оболочки одноименным полюсом к магниту выключа |
теля |
вызывает усиление их магнитного отталкивания. Маг |
нит выключателя размыкает контакты и отключает привод кон вейера. В таком положении контакты магнита удерживаются стопором. Чтобы возвратить устройство в исходное положение* стопор сдвигается и контакты магнита под действием пружины снова замыкают контакты цепи выключателя.
3.6.ОБЕСПЕЧЕНИЕ ЦЕНТРИРОВАННОГО
ИНАПРАВЛЕННОГО ДВИЖЕНИЯ ЛЕНТЫ
Чем сложнее условия эксплуатации мощных ленточных кон вейеров (особенно при доставке налипающих грузов по искрив ленной в пространстве трассе, повышенных длинах ставов и скоростях движения ленты) вопросы центрирования, направле ния движения и контроля схода ленты приобретают первосте пенное значение. Причинами децентрированного хода ленты яв ляются: нарушение в правильности установки става и роликоопор, «серповидность» ленты, воздействие устройств загрузки* разгрузки, очистки и натяжения барабанов при перекосе, ветра, выход из строя подшипниковых узлов роликоопор, попадание посторонних предметов и заклинивание. Сход ленты в сторону часто приводит к тяжелым последствиям: быстро изнашива ются борта ленты при трении о металлоконструкции, возни кает заклинивание и разрывы ленты, значительные просыпи груза и перегрузки в приводе. Из-за неустойчивого попереч ного движения ленты работоспособность конвейера резко сни жается.
3 . 6 . 1. ЦЕНТРИРОВАНИЕ ЛЕНТЫ НА РАБОЧЕЙ И ХОЛОСТОЙ
ВЕТВЯХ
Чем труднее условия эксплуатации ленты, тем сложнее по* составу и компоновке механизмов центрирующие средства. К последним относятся дефлекторные ролики, линейные роликоопоры (жесткие, подвесные) с центрирующими свойствами, спе циальные центрирующие роликоопоры (бесприводные и привод ные), центрирующие барабаны, комбинации перечисленных средств.
Лб
Дефлекторные ролики. Даже кратковременные поперечные смещения ленты приводят к тому, что борта ленты трутся о стойки и быстро изнашиваются. Дефлекторные ролики не только предохраняют борта от износа, но и способствуют воз вращению ленты в исходное положение. Во многих случаях дефлекторные ролики являются единственным средством для предохранения бокового схода ленты на холостой ветви. Поло жение роликов (рис. 3.22, а) может изменяться переставкой
а. б, |
|
Центрирующие |
ролики |
и роликоопоры: |
|
||
в — компоновка |
дефлекторных |
роликов: |
/ — дефлекторные ролики; |
2 — лента;. |
|||
3 — роликоопора; г — роликоопора |
с балансиром: |
/ — балансир; |
2 — ролик; |
д — магнит |
|||
ная |
роликооопора: |
/ — магниты; |
2 — ферромагнитные кольца; |
3 — поворотная опора |
ИГ
оси в соответствующие пазы. Дефлекторные ролики могут иметь реборды различного диаметра, ограничивающие смеще ние ленты в боковом и вертикальном направлениях. При этом в подшипниках используются конические элементы качения или цилиндрические с наклонным расположением элементов каче ния (рис. 3.22,6). Дефлекторные ролики активного действия устанавливаются над лентой, вплотную и наклонно своими бо ковыми участками к ней. Обычно такие ролики поворачивают крайним концом в направлении движения ленты, при этом ро лики препятствуют сходу последней (рис. 3.22, б).
Линейные роликоопоры. Обычная желобчатая роликоопора, благодаря своей геометрии, способствует центрированию ленты. На холостой ветви центрирующая роликоопора монтируется из двух наклонно расположенных роликов (сплошных или дисковых), увеличивающих сопротивление движению холостой ветви ленты. Натяжение ленты на холостой ветви значительно меньше, поэтому центрирующую желобчатую роликоопору за крепляют в перевернутом положении для увеличения натяже ния ленты на участке центрирования. На рабочей или холо стой ветви ленты обычно предусматривается возможность креп ления роликоопор в отверстиях прогонов под заданным углом к продольной оси. В процессе эксплуатации конвейера необ ходимо изменять положение таких роликоопор в плане. Однако при этом следует избегать излишних установок центрирующих роликоопор, так как центрирующее воздействие роликоопорь1 на ленту чаще всего связано с ее проскальзыванием и дополнительным износом.
Повышенным центрирующим воздействием обладают вин товые роликоопоры с парными встречными и противополож ными направлениями витков, оснащаемые дефлекторными ро ликами. Такая компоновка роликоопоры обеспечивает центри рованное движение ленты при несимметричной загрузке ленты вдоль продольной оси. Спиральные (полые) роликоопоры из готовляются из пружинной стали, имеют цилиндрическую илц двустороннюю коническую поверхность и оборудуются подшип никовыми узлами на концах оси. Одновременно с центрирую щими функциями спиральные роликоопоры хорошо очищаю^ ленту на холостой ветви. По сравнению с центрирующими роликоопорами со сплошной конической поверхностью аналогич ные по конфигурации спиральные роликоопоры меньше загряз няются и изнашивают ленту.
К группе центрирующих относятся также подвесные (гир, ляндные) роликоопоры, особенно с подвеской к канатному ставу. В ленточных конвейерах 1ЛБТ-100 конструкции Донн/, проуглемаша жесткое крепление прямых роликоопор холосто^ ветви к канатному ставу, подвешиваемому к кровле на цепях заменено подвеской их осей или рамок роликов к цепям. При’ боковом сходе ленты на роликоопору действует вращаюни^ момент, разворачивающий ее так, что возникает усилие, кот<^
рое стремится вернуть ленту в центральное положение. Чем больше сход ленты, тем на больший угол поворачивается роликоопора. Таким образом обеспечивается автоматическое цент рирование ленты. Однако подвеска роликоопор к цепям при водит к их смещению и возможному раскачиванию [22].
Специальные центрирующие роликоопоры. Мощные ленточ ные конвейеры, как правило, оснащаются специальными цент рирующими роликоопорами активного действия, изменяющими свое положение при движении ленты и действующими авто матически. Распространены роликоопоры с центральной пово ротной осью (или втулкой) в комбинации с дефлекторными роликами, служащими для сообщения роликоопоре вращаю щего момента при сходе ленты. Общим недостатком самоустанавливающихся в плане роликоопор является сложность в ре гулировке и неустойчивость в работе.
Более устойчивы в работе приводные центрирующие ролико опоры с гидроприводом и дефлекторными роликами. Дефлекторные ролики выполняют роль датчиков, которые через систему рычагов управляют золотником гидроцилиндров, пово рачивающих центрирующую роликоопору. По мере центрирова ния ленты дефлекторные ролики, золотник и гидроцилиндры возвращаются в исходное положение. На конвейерах с канат ными ставами и лентами шириной более 1600 мм, используе мыми на карьерах ГДР, эффективно эксплуатируются гирляндные роликоопоры, объединяемые в центрирующие группы. Концы таких роликоопор соединяются канатами, связанными с лебедкой. Включением лебедки производят смещение кана тов относительно друг друга, в результате чего роликоопоры одновременно поворачиваются на угол, необходимый для воз врата ленты в исходное положение. Для своевременного пово рота роликоопоры в заданное положение служат конечные вы ключатели.
Известны конструкции, в которых центрирующая роликоопора не изменяет своего положения, однако при этом изме няется ее геометрия (опорный контур) в вертикальной плоско сти. Это достигается креплением роликов на шарнирах и ка чающемся балансире (рис. 3.22, г). При поперечном сдвиге ленты, благодаря ее повышенному давлению на встречный бо ковой ролик, происходит одновременное смещение в сторону и изменение углов наклона всех роликов. В результате обра зуется опорный профиль с несимметричной желобчатостью, смещенный в сторону сдвига ленты. Такая роликоопора нахо дится в состоянии постоянно изменяющегося равновесия, благадаря чему она автоматически приспосабливается к положе нию ленты.
Кузбасским политехническим институтом разработана и
испытана для |
криволинейных участков трассы |
конвейеров |
|||
1Л80, |
1Л80К, |
1ЛБ8 0 |
центрирующая |
магнитная |
роликоопора |
(рис. |
3.22,3). |
Область |
использования |
такой роликоопоры ог |
раничена резинотросовыми лентами и лентами, имеющими маг нитомягкую обкладку. Роликоопора включает в себя поворот ное на подпятнике основание с роликами и дефлекторные ро лики с рычагами. Ролики снабжены обращенными одноимен ными полюсами друг к другу кольцевыми магнитами, между которыми установлены ферромагнитные кольца из магнитомяг кого материала. Ферромагнитные к^ьц а уменьшают сопротив ление магнитному потоку. Работает роликоопора на криволи нейном участке ленточного конвейера следующим образом. При смещении ленты она взаимодействует с дефлекторным роли ком, благодаря чему рычаг отклоняется в сторону действия ленты. Рычаг поворачивает роликоопору. Центрирующее дей ствие роликоопоры повышается за счет магнитного притяже ния ленты к роликам.
Центрирующие барабаны. Боковой сход ленты часто проис ходит на барабанах. Этот вид смещения ленты опасен, так как нарушается режим передачи тягового усилия, возникает вероят ность возникновения аварийной ситуации при полном сбегании ленты. Устранение смещения ленты на барабанах произ водится регулированием положения и подбором формы обечайки барабана, а также дополнительными средствами ак тивного действия. Регулирование положения барабана осущест вляется чаще поворотом его в плане. При этом уменьшаются расстояние между концевыми барабанами и натяжение ленты на стороне, противоположной сходу ленты (рис. 3.23, а). Лента смещается (центрируется) в сторону меньшего натяжения. Для поворота барабана ослабляются болты крепления подшипни ковых узлов, которые затем переставляются, и барабан мон тируется с перекосом в плане. Однако этот способ регулировки трудоемок. Для устранения этого недостатка механизм регу-
Центрирующие барабаны:
-а — схема центрирования ленты при повороте барабанов; б — барабаны специальная
формы
лировки смещения барабана компонуют совместно с устрой ством для натяжения.
Хорошие результаты получены при использовании бараба нов, имеющих отличную от обычных конфигурацию обечайки. Разные участки таких барабанов (рис. 3.23,6) имеют мень ший, больший или изменяющийся по их длине диаметр. Ленты на барабанах о изменяющейся геометрией, прилегая к обе чайке, приобретают соответствующий профиль. При возникно вении децентрчрующих усилий лента стремится сместиться в сторону, однако этому препятствует поверхность обечайки. Известны также барабаны с винтовой поверхностью, витки ко торого направлены встречно к середине барабана. Смещению ленты препятствуют витки на барабане, которые, кроме того* способствуют очистке поверхности ленты.
3.6.2. НАПРАВЛЕНИЕ ДВИЖЕНИЯ ЛЕНТЫ
Направление движения лент производится на конвейерах с криволинейным профилем, у которых направление тягового усилия на приводном барабане и натяжение на натяжном ба рабане не совпадают с направлением движения ленты. Криво линейный ленточный конвейер большой протяженности со стан дартной лентой способен заменить систему, состоящую из боль шого числа конвейеров, перегрузочных узлов, приводных, блоков. При этом уменьшаются затраты на ленту за счет умень шения ее износа в узлах перегрузки, оборудования, количества обслуживающего персонала. Такие конвейеры длиной до 1500 мм уже широко применяются на открытых разработках ЧССР, ГДР, ФРГ, Франции, США. Эксплуатируются и проек тируются сверхдлинные криволинейные ленточные конвейеры. В Новой Зеландии, например, фирмами Франции построен в 1980 г. криволинейный ленточный конвейер протяженностью 11 км, имеющий четыре горизонтально изогнутых участка с ра диусами 2000, 1500, 1500 и 1100 м. Конвейер транспортирует никелевую руду от рудника до морского порта при перепаде высот 560 м, имеет производительность 520 т/ч при ширине ре зинотросовой ленты 800 мм и скорости ее движения до 3,6 м/с. Протяженность криволинейных ленточных конвейеров по про ектным данным французских фирм может достигнуть 40 км, однако при этом целесообразно использовать промежуточные барабанные или ленточные приводы.
В криволинейных ленточных конвейерах должно обеспечи ваться устойчивое направленное движение плоской ленты на всех участках трассы без вредного фрикционного и растяги вающего воздействия на борта ленты и сохранении устойчи вого положения груза. Заданное направление движения ленты достигается в основном за счет фрикционного взаимодействия ленты и роликоопор, определенно расположенных на криволи нейных участках конвейера. В конструкциях криволинейных
а
ленточных конвейеров ВНИИПТМАШа на прямолинейных, го*, ризонтальных и наклонных участках конвейера роликоопорь* имеют обычное расположение. При повороте ленты роликоопоры на рабочей и холостой ветвях устанавливаются не со смещением в горизонтальной плоскости (как, например, при
центрировании ленты), а наклонно в вертикальной плоскости. Внутренняя кромка ленты оказывается выше внешней. При наклонном расположении роликоопоры она препятствует смещению ленты, образуя упор. Лента движется без проскальзывания относительно направляющих роликоопор. Чтобы устранит*, смещение ленты вниз при увеличении нагрузки, угол наклон^ роликоопоры должен уменьшаться с увеличением нагрузки. Силы отталкивания при этом уменьшаются, однако лента дви жется устойчиво, так как нагрузка на роликоопору и силы тре ния возрастают. С уменьшением загрузки ленты наклон ро.
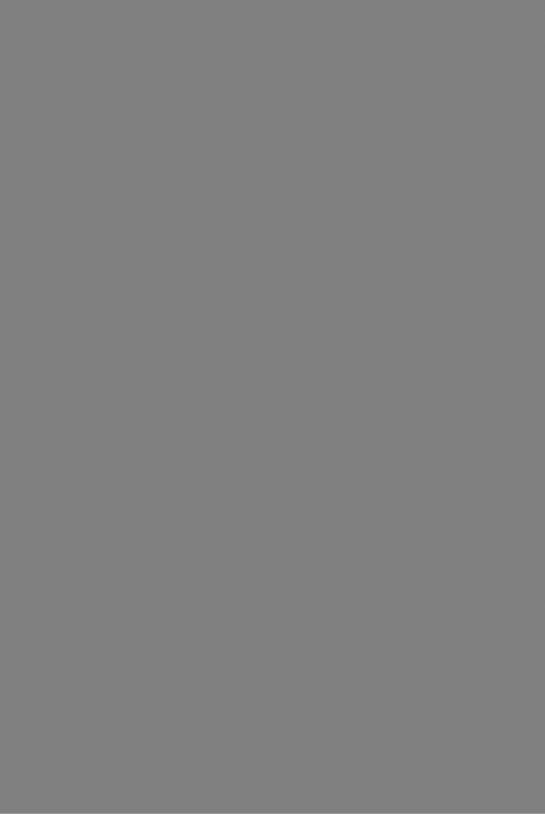
ляющими роликами минимально. При изменении величины на тяжения ленты на участке поворота ленты в пределах 10— S0 % допускаемого натяжения радиус поворота става конвей ера может быть (по данным ВНИИПТмаша) для резиноткане вых лент равным 60—270 5, для резинотросовых — 450— 2000 В (где В — ширина ленты). При таком условии растяже ние кромок ленты не превышает допустимого. Чтобы лента не сдвигалась на трехроликовой желобчатой опоре с углом желобчатости в 30° и при угле наклона всей роликоопоры 5е; должна соблюдаться определенная зависимость между отно шением натяжения ленты к весу 1 м ее на участке поворота (табл. 3.8) и радиусом поворота става.
Расчетные зависимости для определения радиуса поворота Яи става конвейера при различных роликоопорах и парамет рах лент приведены в табл. 3.9, где Sn— наибольшее натяже ние ленты на участке поворота, Н; А — коэффициент, характе ризующий расположение роликов роликоопоры; Ф — коэффици ент, характеризующий распределение нагрузки на рамки: ап — угол наклона прямой роликоопоры к горизонтальной плоско сти, градус; fP — коэффициент трения ленты о поверхность роликоопоры, равен 0,20—0,35 для роликоопор со стальной обе чайкой и 0,30—0,45 для роликоопор с резиновой футеровкой; *7л — вес 1 м ленты; Н; В — ширина ленты, м; ел — допускаемое относительное удлинение ленты при рабочем натяжении; Еп— модуль упругости одной прокладки ленты, Н/см; i — число прокладок в ленте; п — запас прочности ленты; оп— прочность
прокладки, |
Н/см; Ет— модуль упругости |
резинотросовой |
ленты, Н/см; |
ат — прочность резинотросовой |
ленты, Н/см. |
В проектах принимается наибольшее значение радиуса по ворота става, полученное расчетным путем, причем одинако вое для рабочей и холостой ветвей ленты. С учетом результа тов исследований ВНИИПТмашем разработана техническая документация на криволинейный ленточный конвейер для до ставки гравийной массы из карьера на бетонный завод на рас стояние 1000 м. Производительность конвейера 1100 т/ч при
ширине резинотканевой |
ленты |
1200 мм |
и скорости ее |
движе- |
|||
|
|
|
|
|
|
ТАБЛИЦА 3.8 |
|
Отношение |
Коэффициент трения |
Отношение |
Коэффициент трения |
||||
натяжения |
ленты о роликоопоры |
натяжения |
ленты роликоопоры |
||||
ленты к весу |
|
|
|
ленты к весу |
|
|
|
1 м ленты |
|
|
|
1 м ленты |
|
|
|
на участке |
0.25 |
0.30 |
0.35 |
на участке |
0.25 | |
о.:о |
0.35 |
поворота |
поворота |
||||||
100 |
200 |
160 |
140 |
400 |
765 |
630 |
520 |
200 |
385 |
315 |
2G5 |
500 |
960 |
785 |
660 |
300 |
575 |
470 |
400 |
|
|
|
|
Требования к режиму работы ленты
Отсутствие поперечного сдвига:
на желобчатой роликоопоре
на прямой роликоопоре
По допускаемому удлинению кромки ленты
По допускаемому напряжению в кромках лент:
резинотканевых
резинотросовых
На холостой ветви ленты с примене нием батареи вертикальных прямых ролнкоопор
Расчетная формула
|
п |
^ |
О А |
|
|
|
5 пЛ |
|
|||
|
Rn^ |
ф |
|
|
|
р . |
S„(cosan — /psinan) |
||||
" " |
4л (sinan + |
/pcosocn) |
|||
|
„ |
В(2 + |
ел) |
|
|
|
|
|
2ел |
|
|
|
В |
г |
2<Е„ое» |
1 |
|
|
200 |
L (ani)BS„n |
^ J |
||
_ |
в |
Г |
2£тВл |
1 |
|
■п > |
200 |
LaTB — Snn |
+1J |
Яп > 20 В
ния 2,26 м/с, радиус поворота ленты в горизонтальной пло скости 700 м. Конвейер имеет три приводных блока: один го ловной барабанный и два промежуточных ленточных при об щей установленной мощности 3x320 кВт.
Криволинейные ленточные конвейеры с узкими лентами и небольшой протяженностью особенно перспективны в подзем ных условиях. Украинским заочным политехническим институ том и объединением «Донецкуголь» разработан и испытан кри волинейный ленточный конвейер КЛ-150 длиной 90 м, имею щий производительность 120 т/ч при ленте шириной 800 мм и радиусе поворота 150 м. Особенностью его является примене ние на рабочей и холостой ветвях ленты роликов с коническими поверхностями по краям, препятствующими сходу ленты. Од нако в процессе эксплуатации замечен повышенный износ ленты (на 28,5%), происходящий в результате скольжения ленты на фигурных роликах (рис. 3.24, б ).
Криволинейный конвейер изготовлен на базе серийного кон вейера 1Л80 и оснащен магнитными самоцентрирующимн роликоопорами, повернутыми постоянно на угол 10—12° в гори зонтальной плоскости и взаимодействующими с лентой БКНЛ-150, имеющей магнитомягкую нерабочую обкладку, В центрирующих роликоопорах, установленных с шагом 2,8 м, имеются постоянные кольцевые магниты, исключающие сдвиг ленты за счет сил притяжения и обеспечивающие поворот
ленты |
по радиусу, равному 80 м при общем угле поворотаг |
в 23° |
Конвейер имеет длину 344 м, производительность по углк> |
252 т/ч при ширине ленты 800 мм и скорости ее движения
1,6—2,0 м/с. |
изготовлено |
и |
испытано |
в комплексе- |
Гипроуглегормашем |
||||
с ленточным конвейером 1Л80 устройство типа |
УП-80 для |
|||
поворота ленты шириной 800 мм |
на |
криволинейных участ |
||
ках с радиусом 50 |
м. Высокая |
эффективность |
устройства |
связана с выполнением его по типу приводного поддерживаю щего ходового контура, применяемого в ленточных конвейерах: на ходовых опорах. Цепной контур с траверсами глубокой желобчатости и ходовыми роликами имеет регулируемый привод. Траверсы на участке поворота располагаются наклонно на расстоянии 1280 мм друг от друга. На холостой ветви устанав ливаются желобчатые роликоопоры с соответствующим накло ном. Максимальный угол поворота составляет 30° при скоро сти движения ленты 1,6 м/с и мощности привода 17 кВт. Уста новлено, что при радиусе поворота, равном более 75 м, можно использовать бесприводной цепной контур с ходовыми травер сами. Чтобы повысить надежность направленного движения ленты при действии больших сдвигающих усилий используют элементы, центрирующие ленту силами отталкивания. Для этой
цели |
ленту |
выполняют |
с трапециевидными |
выступами |
(рис. |
3.24, в) |
в средней или |
краевых частях. При |
этом на ба |
рабанах имеются аналогичные по форме проточки, в которые входят выступы ленты. Выступы не только центрируют ленту, но и повышают тяговые возможности приводных барабанов.
Особую группу конвейеров с повышенной способностью на правления движения лент (в том числе специальных) состав ляют конвейеры с опорами скольжения (рис. 3.24,г). Опоры скольжения могут быть сплошными в виде полос или проме жуточными. Для них характерно отсутствие вращающихся частей на линейной части конвейера, а значит, повышается устойчивость движения ленты и кускового крупностью до 1500 мм груза. Применение антифрикционных материалов для опор скольжения и лент позволяет уменьшить коэффициент трения между лентой и опорами до 0,05 и менее. Ленточные конвейеры с желобчатыми опорами скольжения, обладаю щими направляющими свойствами, наиболее эффективны в ус ловиях подземных работ, где требования по пылеобразованию, шуму, компоновке оборудования в пространстве высоки. При повышенных скоростях движения ленты рекомендуются смазка опор скольжения, использование в опорах скольжения и опорной обкладке ленты антифрикционных материалов, на правляющих дефлскторных роликов, направляющих элементов на ленте, линейной и приводной частях конвейера.
В процессе эксплуатации конвейера возможна потеря устой чивости движения ленты, когда самостоятельно дествующие средства центрирования или направления движения ленты не обеспечивают возвращение ее в исходное положение (напри мер, при выходе из строя дефлекторных роликов, центрирующих роликоопор и др.). В этом случае для предотвращения возник новения аварийной ситуации необходимо оперативное отклю чение привода конвейера. Эта задача решается устройствами, контролирующими величину схода ленты.
Днепропетровским заводом шахтной автоматики серийно выпускается датчик контроля схода ленты типа КСЛ-2 с маг нитными элементами управления. При сходе лента нажимает на подпружиненный гибкий стержень, который, перемещаясь совместно с магнитной системой, изменяет магнитное сопро тивление в цепи управляющего реле с контактом. Последний замыкается, и привод конвейера отключается. После устране ния причины, вызвавшей чрезмерный сход ленты, магнитная система и подпружиненный элемент возвращаются в исходное положение. В устройстве с маятниковым механизмом переме щения первичного элемента, взаимодействующего с кромками ленты, обеспечивается контроль поперечного схода ленты в обе стороны. Оно включает два дефлекторных ролика, поворотные основания которых через тросики соединены с поворотным фер ромагнитным сердечником (рис. 3.25 а), имеющим обмотку воз буждения. Под поворотным сердечником установлены два не подвижных сердечника с сигнальными обмотками. Сигнальные обмотки включены через диод в цепь управления тиристором. В анодной цепи тиристора имеются конденсатор и исполни тельное реле. При набегании ленты на дефлекторный ролик один из тросиков увлекает поворотный сердечник. Изменяется магнитное сопротивление одной из сигнальных обмоток, в цепи которой возникает ток. Включается в работу тиристор, и сраба тывает исполнительное реле, электрически связанное с приво дом конвейера. После центрирования ленты схема возвращается
висходное положение.
Вустройствах для контроля схода резинотросовых лент {рис. 3.25, б) на уровне образующей бокового ролика ролико-
опоры монтируется датчик в виде управляемого магнитным по лем контакта с постоянным магнитом. Контакт включен в цепь управления приводом конвейера. При сходе ленты кромки ее приближаются к корпусу датчика. Ферромагнитные боковые тросы ленты изменяют магнитное поле датчика, контакт замы кается, и срабатывает цепь управления. Весьма эффективны в работе устройства с использованием световой техники, рабо тающие на принципе бесконтактных элементов автоматики. В корпусе С-образной формы имеются оптический прибор с ис точником света и фотореле (рис. 3.25, в). В момент схода
(N3 t'O
ленты ее кромка заходит в проем корпуса и закрывает луч света. Срабатывает фотореле, и привод конвейера отключа ется.
Срабатывание устройства можно получить и путем исполь зования с отраженного от кромки ленты луча света при ее сходе (рис. 3.25, г). Устройства контроля схода лент могут служить для автоматического включения в работу центрирую щих и направляющих устройств.
Эффективность применения центрирующих и направляющих устройств зависит от того, в какой мере по своим техническим данным они соответствуют характеру смещений ленты в кон кретных условиях. В зависимости от качества изготовления и стыковки ленты, связанного с ее «серповидностыо», и монтажа величина и характер смещений ленты могут существенно изме няться. Практическое значение приобретает также оценка хо довых качеств ленты для определенной группы конвейеров, ос новными параметрами выбора которых являются длина кон вейера, ширина и скорость движения ленты, тип роликоопор и условия установки (в шахте, карьере, помещении). Такая оценка движения ленты осуществляется специальным механиз мом (рис. 3.25, (3). Он включает в себя дефлекторный ролик, выполняющий функцию датчика перемещений и установлен ный на подвижной штанге. Штанга шарнирно прикреплена к пишущему элементу двуплечим рычагом. Барабан с пишущей лентой своей осью через муфту соединен с вариатором, кото рый связан с фрикционным роликом, футерованным резиной. Перемещение дефлекторного ролика и штанги преобразуется в перемещение пишущего элемента с помощью двуплечего ры чага, соотношение плеч которого можно изменять для выбора масштаба записи смещения ленты. Барабан приводится во вра щение через вариатор от ролика. Передаточное отношение ва риатора подбирается так, что за один оборот ленты барабан также совершает один оборот. Это отношение длины ленты конвейера к длине окружности барабана. Таким образом, ча стота вращения регистрирующего барабана равна числу обо ротов ленты конвейера за определенный промежуток времени. На пишущей ленте получается синхронная запись хода ленты конвейера, по которой можно рассчитать проектируемые пре делы регулирующей способности центрирующих и направляю щих устройств.
|
|
|
|
|
|
|
РИС. |
3.25. |
|
|
|
|
|
|
|
|
|
|
|
|
Средства контроля схода |
ленты: |
|
|
|
|
|||||
а — устройство контроля |
схода |
ленты |
с |
поворотным |
ферромагнитным |
сердечником: |
|||||||||
/ — схема |
устройства; |
// — электрическая схема; |
/ — дефлекторный |
ролик; |
2 — осно |
||||||||||
вание; |
3 — трос; |
4 — поворотный |
магнитный сердечник; 5 — неподвижные |
сердечники; |
|||||||||||
6 — обмотка возбуждения; |
7 — обмотка |
сигнальная; |
в —диод; 9 — тиристор; |
10 —реле; |
|||||||||||
б — то |
же, |
для |
резннотросовой |
ленты: |
/ — контакт; |
2 — магнит; |
3 — корпус; |
в, г — |
|||||||
то |
же, |
с |
фотореле: |
/ — лента; |
2 — корпус; |
3 — луч света; д — механизм |
для |
оценки |
|||||||
ходовых |
качеств |
ленты: |
/ — дефлекторный |
ролик; |
2 — штанга; 3 — рычаг; |
4 — вариа |
|||||||||
|
|
|
|
|
|
тор; 5 — пишущий барабан |
|
|
|
|
|||||
5 |
Заказ № 1462 |
|
|
|
|
|
|
|
|
|
|
|
129 |
Контроль производительности конвейера позволяет: измерять количество перевезенного груза отдельным конвей
ером или конвейерной линией за отчетный период времени; проверять загрузку конвейера с целью возможного регули
рования скорости движения ленты, при которой износ конвейер ного оборудования минимальный;
обеспечить заданную технологию переработки сырья путем строгого дозирования исходных компонентов;
учитывать интенсивность и количество подачи груза с целью автоматического управления работой всей транспортной си стемы в заданном режиме.
К средствам контроля производительности относят конвейер ные весы — самостоятельные устройства, монтируемые на кон вейере; дозаторы — механизмы, сочетающие одновременно функ ции взвешивания и передачи груза на короткое расстояние от загружающего устройства к конвейеру или аппарату технологи ческой линии; вспомогательные элементы контроля (датчики, аппаратура переработки информации и выдачи управляющего сигнала, исполнительные механизмы).
Необходимо отметить особую техническую сложность кон троля производительности конвейера или конвейерной системы. Это связано с тем, что измеряемый грузопоток, как правило, Не стабилен, неоднороден по составу. Кроме того, измерения дол жны осуществляться непрерывно с учетом возможного откло
нения важных |
(с точки зрения оценки количества груза) пара |
||||
метров. Монтаж и настройка измерительных |
средств |
должны |
|||
быть выполнены высококвалифицированным |
персоналом. |
||||
Основные |
средства |
контроля |
производительности |
конвей |
|
ера — конвейерные весы |
в целях |
высокой точности измерений |
должны удовлетворять ряду требований: точность измерения должна соответствовать заданной при изменении количества груза на ленте от 20 до 100%; оптимальная загрузка ленты равна 60—80 % максимальной; загрузка ниже минимальной до пускается только в течение короткого времени (рекомендуется принимать не более 2% полного времени взвешивания). Для конвейерных весов должна быть установлена минимальная масса груза, которая может быть взвешена за один раз. Должны строго соблюдаться условия по однородности свойств состава взвешиваемого груза (особенно по плотности, кусковатости> влажности), температуре и влажности окружающей среды, ко лебанию напряжения в сети (по величине и частоте).
Проверку и тарировку весов необходимо проводить непо
средственно на конвейере с использованием транспортируемого материала при номинальной загрузке весов.
Принцип действия конвейерных весов основан на непрерЬ1В. ном суммировании (интегрировании) произведения сигналов, пропорциональных массе груза и скорости движения лен^ы*
При постоянной загрузке конвейера
Q = qrvt,
где Q — количество перевезенного груза; qT— масса груза на 1 м длины ленты; v — скорость движения ленты; t — время ра боты конвейера.
При переменной загрузке конвейера
Q = f 4vvdt,
|
|
<0 |
|
|
|
|
|
где to — начало |
отсчета времени |
взвешивания; |
tK— конечное |
||||
время взвешивания. |
|
|
|
|
|
|
|
При проектировании конвейерных весов к одним из основ |
|||||||
ных расчетных |
параметров |
относится нагрузка |
(давление) |
от |
|||
груза и ленты |
на грузоприемное устройство (например, на |
из |
|||||
мерительную роликоопору), которая составляет |
|
|
|
||||
|
Р = g?n/y cos ф + |
2,1PSJL. , |
|
|
|
||
|
|
|
1У |
|
|
|
|
Р — нагрузка на роликоопору от груза |
и ленты; g — ускорение |
||||||
свободного падения; qn— масса груза |
на 1 м длины ленты и |
||||||
1 м ленты [24]; |
/у — длина |
измеряемого |
участка; |
ср — угол нак |
|||
лона конвейера; hp— смещение вверх |
измерительной |
ролико- |
|||||
опоры относительно смежных; S H— натяжение ленты |
на изме |
||||||
рительной роликоопоре. |
|
|
|
|
|
|
Под действием ленты с грузом измерительная роликоопора смещается на
hp = h0— knP9
где hQ— смещение измерительной роликоопоры, связанное с мон тажом грузоприемной площадки конвейерных весов; kn— коэф фициент пропорциональности.
В табл. 3.10 даны значения масс груза на 1 м ленты и 1 м ленты для ленточных конвейеров.
Конвейерные весы оснащаются специальными измеритель ными (взвешивающими) роликоопорами, воздействующими на датчики силы. Чем большее количество измерительных роликоопор участвует в регистрации массы груза, тем точнее конвей ерные весы. Рама взвешивающих роликоопор должна быть жесткой и устанавливается на жестком фундаменте для устра нения излишних деформаций. Наиболее широко распространены как наиболее простые одно- и двухроликовые схемы компоновки измерительных роликоопор (рис. 3.26, а, /, //). Для увеличения чувствительности грузоприемной площадки весов применяется консольная шарнирная схема компоновки измерительных роли коопор (рис. 3.26, а, III). На конвейерах повышенной произво дительности устанавливаются конвейерные весы с двухрычаж ной системой и четырьмя измерительными роликоопорами

Тип конвейера |
Скорость |
Производи |
Диаметр |
Масса |
Масса груза |
||||
движения |
тельность, |
роликов, мм |
1 м лен |
на 1 м ленты, |
|||||
|
|
ленты, м,с |
т,ч |
|
ты, |
кг |
кг |
||
К Л 1 |
|
1,5 |
2 5 0 |
127 |
12 |
|
4 6 ,3 |
||
1 Л 8 0 К , |
1Л 80 |
1,6 |
2 7 0 |
89 |
9 ,7 |
47 |
|
||
2 Л 8 0 |
|
1,6 |
2 7 0 |
89 |
11 |
|
47 |
|
|
З Л 8 0 |
|
1,6 |
2 7 0 |
127 |
11 |
|
47 |
|
|
1 Л Т 8 0 |
|
1,6 |
2 7 0 |
89 |
10,5 |
47 |
|
||
К Л 1 5 0 У |
|
1,6 |
2 0 0 |
127 |
9 ,7 |
45 |
|
||
К Р У 2 6 0 |
|
1,58 |
2 6 0 |
89 |
2 3 |
|
4 5 |
,7 |
|
1 Л Б 8 0 , |
2 Л Б 8 0 |
1,6 |
2 7 0 |
89 |
9 |
,7 |
4 7 |
,0 |
|
К Р У 3 5 0 |
|
1,5 |
3 5 0 |
159 |
3 1 |
,0 |
6 2 |
,5 |
|
К Л А 2 5 0 |
|
1,85 |
2 5 0 |
127 |
12,0 |
39 |
|
||
К Л А 1 5 0 А |
1,6 |
2 5 0 |
89 |
9 |
,7 |
4 3 |
,5 |
||
К Л А 2 5 0 |
|
1,25 |
2 5 0 |
127 |
12 |
|
55 |
|
|
2 Л У 1 2 0 |
|
3 |
,5 |
1200 |
159 |
37 |
|
100 |
|
К Р У 9 0 0 |
|
3 |
,2 5 |
9 0 0 |
159 |
36 |
|
7 7 ,2 |
|
Л 1 0 0 , 2 Л У 1 2 0 |
2 |
|
5 0 0 |
133 |
3 7 |
|
6 9 ,5 |
||
2 Л У 1 0 0 |
|
2 |
|
5 0 0 |
133 |
30 |
|
6 9 ,5 |
|
1 Л У 1 2 0 |
|
2 |
|
8 5 0 |
159 |
30 |
|
118 |
|
2 Л Т 8 0 |
|
2 |
|
3 4 0 |
127 |
12 |
|
47 |
|
С Р С /К /4 7 0 |
4 |
|
2 0 0 0 |
159 |
20 |
|
140 |
||
С Р С /К /2 0 0 0 |
5 |
|
4 0 0 0 |
159 |
20 |
|
2 2 0 |
|
(рис. 3.26, а, IV). Рычаги соединяются с датчиком силы посред ством тяги. Устройства для взвешивания, включающие в себя дозаторы, монтируются на раме, выполняющей функцию грузо приемной площадки. Рама с грузоприемной площадкой устанав ливается подвижно в вертикальной плоскости (рис. 3.26, б, I) либо поворотно со стороны натяжного или приводного барабана (рис. 3.26, б, II, III).
Производительность конвейера прямо пропорциональна сече нию грузопотока на ленте и зависит от конфигурации сечения. По этому принципу работают измерители сечения (массы) груза контактного типа (рис. 3.26, в). В зоне измерения над лентой на раме подвешивается система поворотных планок. Угол пово рота последних зависит от высоты сечения груза в точке кон такта. Планки соединены с шарнирным параллелограммом, пе ремещение одной из сторон которого прямо пропорционально перемещению планки по высоте. Эти перемещения преобразу ются в сигналы потенциометрами, число которых соответствует
РИС. 3.26.
Средства контроля производительности конвейера:
а — измерительные |
роликоопоры: / — линейная |
роликоопора; 2 — измерительная |
ролико- |
|||||||
опора; |
3 —датчик |
силы; б —дозаторы; |
в — измеритель |
сечения |
груза |
контактного |
||||
типа: |
/ — параллелограмм; 2 — планка; |
г — индуктивный |
датчик |
силы: |
/ — измери |
|||||
тельная роликоопора; 2 — пластина; 3 — индуктивный датчик; |
д — конвейерные весы |
|||||||||
с радиоактивным |
излучением: |
/ — основание; |
2 — излучатель; |
3 — детектор; |
е — весы- |
|||||
|
дозатор: / — затвор; |
2 —дозатор; |
3 — тахогенераторный |
датчик |
|
|
числу планок. Изменение величины сигналов происходит при пе ремещении подвижных контактов, соединенных с одной из сто рон параллелограмма. Запись суммарного сигнала производится самопишущим миллиамперметром на диаграммной бумаге. По скольку скорость установившегося движения ленты принимается постоянной (в схеме отсутствует датчик скорости), то произво дительность конвейера в любой промежуток времени пропор циональна площади, контролируемой системой планок. Рассмот ренная схема устройства позволяет проводить исследования ди намики грузопотока на конвейере за рабочий цикл. Хорошие результаты получены при использовании индуктивных датчиков силы (рис. 3.26, г). Измерительная роликоопора устанавлива ется на пружинных пластинах, к нижней из которых подвешен сердечник. Последний перемещается относительно катушек мос товой схемы с миллиамперметром, показания которого соответ ствуют перемещениям сердечника и, следовательно, измеряемой производительности конвейера.
Повышенной точностью измерений обладают конвейерные весы с применением радиоактивного излучения. В отличие от других устройств они не имеют механической связи (за исклю чением тахогенераторного датчика скорости ленты) с лентой и роликоопорами. Благодаря этому значительно снижается трудо емкость работ по тарировке, контролю работы и обслуживанию весов. Принцип действия таких устройств основан на поглоще нии слоем груза радиоактивного излучения (обычно гамма-из лучения) и регистрации уже измененного излучения детектором (рис. 3.26, д). Источник излучения устанавливается на основа нии, расположенном над лентой, а детектор — под лентой. Лучи проходят через слой груза и ленту и попадают в детектор, ко торый преобразует их в электрические импульсы. В усилителе происходит преобразование сигнала в ток, который затем уве личивается пропорционально сигналу, вырабатываемому тахогенераторным датчиком скорости ленты. Результирующий ток поступает в прибор для измерения грузопотока. Основной недо статок радиоактивных весов — особые требования к технике безопасности, связанные с обеспечением защиты обслуживаю щего персонала от радиоактивного облучения. На аналогичном принципе работы построены конвейерные весы с применением ультразвука, однако при этом измеряется не проникающее, а отраженное излучение.
Для конвейеров, устанавливаемых наклонно или изменяю щих угол наклона в процессе эксплуатации, в измерительную схему весов (величина давления груза зависит от величины угла наклона конвейера) вводится дополнительный датчик угла по ворота в виде поворотного трансформатора. Выходное напряже ние трансформатора, изменяющееся в зависимости от его угла поворота, равного или пропорционального углу наклона конвей ера, подается в электрическую схему и корректирует сигнал от датчика массы.
В производствах, где потребуется дозированная подача
сырья, применяют конвейерные весы-дозаторы |
(рис. 3.26, е). |
|||
Они представляют собой |
короткие |
конвейеры, |
работающие |
|
в комплексе с подающим |
грузопоток устройством |
(обычно |
||
бункер с затвором). Достоинством |
весов-дозаторов |
с цик |
лической подачей порции груза является то, что они сглажи вают неравномерности грузопотока. Груз поступает через зат вор бункера на приемную часть дозатора, скорость движения ленты которого постоянна. При подходе груза к месту раз грузки затвор бункера автоматически закрывается. Таким об разом, взвешивание груза осуществляется при отсутствии по мех, связанных с падением груза и неравномерностью загрузки. После окончания взвешивания затвор открывается и начинается новый цикл загрузки и взвешивания дозатора. Период загрузки выбирают так, чтобы до фиксации каждого показания счетчика разгрузка материала с головного барабана не происходила. При этом незагруженным остается участок длиной не более 15 % длины дозатора. Некоторое снижение общей скорости подачи груза можно компенсировать соответствующим подбором ши рины ленты дозатора.
Регулирование скорости конвейера, связанное с показаниями весов, чаще применяется при изменении производительности за грузочных устройств. Контроль производительности и регулиро вание скорости движения ленты позволяет уменьшить расход электроэнергии, износ оборудования и улучшить в целом экс плуатационные показатели работы конвейеров. Конвейерные весы при этом выполняют роль датчиков, регулирующих произ водительность загрузочных устройств.
В СССР разработаны, испытаны и выпускаются различные типы конвейерных весов. Конвейерные весы типа УУП конструк ции УкрНИИпроекта могут устанавливаться на наклонных шахтных и карьерных конвейерах; работают они по принципу контроля мощности, потребляемой двигателями. При необходи мости они включаются в систему автоматического регулирова ния и измеряют мгновенную производительность в фиксирован ный промежуток времени. Данные о количестве груза, пере везенного за час, смену, сутки, фиксируются интегрирующим счетчиком. Отсутствие в весах сложных датчиков силы упро щает их эксплуатацию. Основная область применения — ротор ные экскаваторы. Погрешность измерений составляет до 2% .
Электронно-гидравлические весы ЭГВ-2 с грузоподъемным устройством в виде секции с роликоопорами, датчиками силы и скорости движения ленты, формирователем сигналов и счетным устройством имеют нормальное или взрывобезопасное исполне ние. Применяются для лент шириной 800—1400 мм.
Электронные тензорезисторные весы ЭТВР нормального ис полнения устанавливаются на конвейерах роторных экскавато ров, имеют грузоприемник в виде коромысла с качалкой и двумя роликоопорами, датчики силы и скорости движения ленты, дат
чик угла наклона конвейера. Грузоприемник обеспечивает за щиту датчика силы от ударных нагрузок. Датчик угла наклона включает в себя отвес с маховиком и вращающийся трансфор маторный преобразователь. Приборный блок выполняет мате матические операции по вычислению массы груза и передачи сигналов в счетчик суммарного учета. Весы могут регистриро вать производительность в пределах 111—1111 кг/с при угле наклона конвейера до 20°, ширине ленты 1200 мм и скорости ее движения 0,4—4 м/с, массе устройства 600 кг.
Конвейерные весы типа 4219 ВКГ160 и 4219 ВКГ200 имеют взрывобезопасное исполнение, обеспечивают цифровую индика цию массы взвешиваемого грузопотока и формирование дис кретного сигнала на замыкание реле при достижении заданной дозы груза. Грузоприемная платформа, опирающаяся на гид равлическую мессдозу, снабжена опорным лотком из полос ан тифрикционного капролона, по которому скользит лента с гру зом. Благодаря этому уменьшается влияние динамических на грузок на точность измерений. Давление на выходе измеряется манометром. Стрелка манометра и датчик скорости движения ленты связаны с кодирующим диском, с помощью которого и оптической считывающей головки формируются сигналы для счетчика. Возможна дистанционная настройка нуля весов и де шифратора груза. Бесконтактное оптическое считывание инфор мации повышает надежность работы весов. Взвешивание может осуществляться для лент шириной 1600 и 2000 мм и скорости их движения 0,5—3,5 м/с при массе груза на 1 м ленты 210—- 530 кг и точности измерений 1 %. Весы изготавливаются Одес ским ПО «Точмаш».