
книги / Электронно-лучевая сварка и смежные технологии
..pdfменее 105—106 К/с) обрабатываемого металла, т. е. эффект само закалки, в том числе из жидкого состояния. С помощью высоко скоростной растровой развертки электронного пучка и цифрового управления формируется программно-управляемый распределен ный источник нагрева. Растр на плоской поверхности можно фор мировать в виде прямоугольника, трапеции, круга, кольца и дру гих фигур. Благодаря этому поверхностное термоупрочнение мож но достигнуть и на малогабаритных, тонкостенных изделиях, а так ж е на изделиях сложной конфигурации.
Процесс электронно-лучевого модифицирования поверхностей осуществляют в двух основных режимах: без оплавления и с оп лавлением. Выбор режима зависит, прежде всего, от требуемой глубины модифицированного слоя материала. Для первого режи ма модифицирования не требуется последующая механическая обработка поверхности. При этом реализуется эффект термоуп рочнения тонкого (до 2-2,5 мм) приповерхностного слоя металла, процесс зонального отжига или локальной термообработки свар ных соединений [78], а также явления фазообразования и струк турных изменений в кристаллах [51]. Второй режим модифициро вания применяют для гомогенизации, рафинирования и облицо вочного оплавления поверхности слитков, перемешивания в жид кой фазе компонентов, не образующих сплавов в равновесных условиях, образования метастабильных соединений и стеклообраз ных сплавов, закалки слоев металла толщиной до 10 мм. Упрочне ние в этом случае можно выполнять и с подачей присадочного материала для ввода легирующих элементов или нанесения амор фного слоя. При термоупрочнении с оплавлением улучшается мик роструктура металла и значительно уменьшается количество мик роликваций. Для сплавов системы железо-углерод повышенную твердость слоя переплава обеспечивает развитая дендритная структура с твердой мартенситно-карбидной основой, по грани цам которой расположена пластичная аустенитная фаза.
Для импульсного упрочнения максимальную температуру по
верхности металла можно оценить по соотношению [60] |
|
T m„ = 2 q 1/rc pA A t. |
<189> |
где q — усредненная длительность импульса, плотность мощности электронного пучка; A t— длительность импульса электронного пуч ка; с; Л — соответственно удельная теплоемкость и теплопроводность металла.
технологические процессы |
211 |
|
|
|
|
|
|
Охлаждение поверхности |
|||
HV, М Па |
|
р Ю 9, см |
металла |
после окончания |
|||||
|
|
|
|
|
|
импульса осущ ествляется |
|||
|
|
|
|
|
|
по закону: |
|
||
|
|
|
|
|
|
T=T maxerf(A t/bAt)1/2- ( 19°) |
|||
|
|
|
|
|
|
Пример распределения |
|||
|
|
|
|
|
|
микротвердости по глубине |
|||
|
|
|
|
|
|
металла при им пульсном |
|||
|
|
|
|
|
|
воздействии электронного |
|||
|
|
|
|
|
|
пучка показан на рис. 92 [32]. |
|||
|
|
|
|
|
|
Р еж им |
возд е й стви я: |
||
|
|
|
|
|
|
At=0,75 м кс, UycK= 6 -2 0 кВ, |
|||
0 |
2 |
4 |
6 |
|
8 |
р=1,33*10-5 Па. Скорость ох |
|||
|
|
Г л уб и н а, м км |
|
|
лаждения поверхности дос |
||||
Рис. |
92. Распределение микротвердости в |
тигает Ю 10 К/с и при удале |
|||||||
нии от поверхности резко па |
|||||||||
сс-железе по глубине (косой шлиф, нагрузка |
|||||||||
дает в |
слое |
толщ иной |
|||||||
9,8-1(Г3 Н :1 |
— исходное состояние; |
||||||||
2 — поток энергии 3,3 Д ж /см 2; |
|
0,2 мкм. |
|
|
|||||
3 — поток энергии 5 ,2 Дж/см? |
|
Поверхностное термоуп |
|||||||
HV, М П а |
|
|
|
|
рочнение без оплавления |
||||
|
|
|
|
эффективно применять для |
|||||
50 0 0 |
|
|
|
|
|
||||
|
|
|
|
ч |
нелегированных и низколе |
||||
|
|
|
|
|
|||||
|
|
|
|
2 |
гированных сталей с содер |
||||
4 5 0 0 |
|
|
|
V |
ж а н и е м |
угл е р о д а более |
|||
|
|
|
|
||||||
|
|
у |
|
|
0,35%, перлитного чугуна с |
||||
4 0 0 0 |
|
|
|
|
пластинчатым |
графитом и |
|||
|
|
|
О |
|
|
перлитного ковкого чугуна. |
|||
|
|
|
|
|
Термоупрочнение с оп |
||||
3 5 0 0 |
|
|
|
|
|
||||
|
|
|
|
|
лавлением р е ко м е н д ую т |
||||
|
|
|
|
|
|
для средне- и высоколеги |
|||
3000 |
|
|
|
|
|
рованных хромистых сталей |
|||
8 |
12 |
16 |
2 0 М п , % |
(для работы при повышен |
|||||
Рис. 93. Зависимость микротвердости |
ной температуре), для чуГу |
||||||||
нов с пластинчатым и сферо |
|||||||||
сталей типа Г10, Г16, Г24 после объемной |
|||||||||
(1) и электронно-лучевой обработки (2) от |
идальны м граф итом, для |
||||||||
содержания марганца |
|
|
|
алюминиевых, титановых и |
|||||
|
|
|
|
|
|
никелевых сплавов. При об |
работке титановых сплавов наибольший эффект повышения твер дости достигают на двухфазных материалах. Влияние на степень
212 |
Смежные |

Температурное поле по глубине металла от воздействия элект ронного пучка с высокочастотной прямоугольной растровой разверт кой без оплавления поверхности описывает следующее выражение:
T (z ,t)= T 0 + Ta J
’05 -4 -11,-05) HJ.JQS-4-"!-^). Ц
0 ,S -p (t-n -0 ,5 ) | |
(191) |
|
где z — координата, направленная перпендикулярно к поверхно сти вглубь металла; Т0 — начальная температура; Ф — интеграл
вероятностей:
Ф (х) ^ ехр( - и % Т а = ^ Г ;
а — коэффициенттемпературопроводности; ау— поперечный раз мер растра; r \= 2 4 a x ja ^ ях — продольный размер растра; то— период вращения кольца подшипника; h=nD/ах; D — диаметр кольца подшипника; $=ajay\ t =t/t0; nt — целая часть \ ; п — целое число.
Учитывая, что материалом подшипника — среднеуглеродистая сталь типа Ш Х15, прошедшая термообработку (47 -4 8 HRC3, а0 2=1440 МПа), а также то, что закалку осуществляют в диапазоне отГ<Т на поверхности кольца до Т>800 °С на глубине упрочнен ного слоя, расчет температурного поля дает оптимальную глубину упрочненного слоя 1,5-1,7 мм при мощности электронного пучка 2,6 кВт, размерах прямоугольного растра ах=5 мм, ау=30 мм и ско рости перемещения растра по изделию 10 мм/с.
Упрочненный слой показан на рис. 96. Твердость упрочненного слоя 63-64 HRC3, что удовлетворяет условию равнонесущей способ ности деталей подшипника 60<66 HRC3. Срок службы радиально упорных подшипников, имеющих детали с электронно-лучевым термоупрочнением и работающих при высоких динамических на грузках в активной среде без смазки, в два раза выше, чем изго
214 |
Смежные |

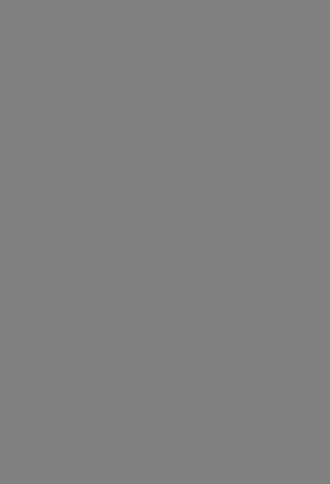
ности изделий из титановых сплавов по сравнению с де талями из других металли ческих материалов обуслов лено, вероятнее всего, низ кой теплопроводностью этих сплавов и, соответственно, большим временем суще ствования жидкой фазы на поверхности.
Из анализа физико-хими ческого состояния поверхностных слоев исходных и облученных
образцов и лопаток следует, что в результате быстрой кристалли зации расплава происходит:
■существенное изменение химического состава поверхност ных слоев толщиной по крайней мере 200 нм (имеет место очистка от примесей углерода и кислорода; с увеличением
числа импульсов происходит повышение однородности рас пределения А1, Мо и Z r по глубине, причем концентрация А1
в приповерхностной зоне возрастает до 15-20 ат. %);
■изменение фазового состава в слое толщиной примерно
10 м км (наблюдается практически полный распад |Н )азы
и образование большого количества а"-фазы (до 30-40%);
■формирование в этом же слое остаточных растягивающих напряжений, что проявляется в смещении рентгеновских ли ний в сторону меньших углов и в снижении значений мик ротвердости, особенно заметном при небольших нагрузках.
На поверхности образцов и лопаток при небольшом числе импуль сов формируется значительное количество микродефектов в виде кратеров диаметром 1-80 мкм и глубиной 0,5-2 мкм. С ростом чис ла импульсов плотность распределения кратеров уменьшается и при я>40 их присутствие практически не регистрируется. Последнее сви детельствует о том, что причиной формирования кратеров является неоднородность химического состава и структурно-фазового состо яния материала в поверхностных слоях, а также формирование не устойчивостей при взаимодействии электронного пучка со случайно ориентированными участками поверхности (риски, царапины, забои ны и др.) и при затенении некоторых поверхностных областей образу ющимся на начальной стадии действия импульса пароплазменным облаком, содержащим преимущественно углеводороды.
технологические процессы |
217 |
Сметные
Таблица 36. Х арактеристики электронно-лучевой закалки металлов в твердом состоянии
М а р ка стали |
Парам етры нагрева |
Ф орм а и разм ер зоны |
Твердость, микротвердость |
Н аибольш ая |
|||
(со д ерж ан ие |
|
|
|
н агрева, врем я |
закаленной зоны, износостойкость |
глубина закалки, |
|
легирую щ их |
и уск- * В |
1п,м Л |
Р, кВ т |
воздействия, скорость |
|
мм |
|
элем ентов, % ) |
п ерем ещ ени я |
|
|
||||
|
|
|
|
||||
15 |
2 5 - 3 0 |
1 0 0 -5 0 0 |
- |
5 - 1 5 0 |
м м /с |
Н =4,65...6 ГПа (иск. 1,5-1,8 ГПа) |
0 ,1 -0 ,4 |
20 |
2 5 - 3 0 |
1 0 0 -5 0 0 |
- |
5 - 1 5 0 |
м м /с |
Н =8,6...11,5 ГПа (4,2-5,2 ГПа) |
0 ,2 5 -0 ,5 7 |
4 5 после |
2 5 - 3 0 |
1 0 0 -5 0 0 |
- |
5 - 1 5 0 |
м м /с |
Н =8,7...9,8 ГПа (5.0...5.7 ГПа) |
0 ,2 4 -0 ,4 0 |
цем ентации |
|
|
|
|
|
|
|
4 0 Х 9 С 2 М , |
2 5 - 3 0 |
1 0 0 -5 0 0 |
— |
5 - 1 5 0 |
м м /с |
Н =8,2...11,0 ГПа (5,5-5,7 ГПа) |
0 ,3 6 -0 ,4 0 |
после закалки |
|
|
|
|
|
|
|
Т В Ч |
|
|
|
|
|
|
|
4 0 Х 1 3 М |
2 5 - 3 0 |
1 0 0 -5 0 0 |
|
5 - 1 5 0 |
м м /с |
Н = 7 ,3 ...9 ,3 Г П а (4 ,8 -5 ,0 Г П а). |
|
|
|
|
|
|
|
П ов ы ш ение износостойкости |
|
|
|
|
|
|
|
об разцов в 3 - 5 раз по срав нен ию |
|
|
|
|
|
|
|
с печной закал кой; клапан ов, |
|
|
|
|
|
|
|
толкателей и кором ы сел в два |
|
|
|
|
|
|
|
раза по срав н ен и ю с серийны м и |
|
|
|
|
|
|
|
деталям и двигателя трактор а |
|
|
|
|
|
|
|
6 1 - 6 5 H R C 3 |
|
4 1 4 0 ,1 0 4 5 , |
52 |
3 2 8 |
— |
Ф о рм иров ани е по точкам |
|
1 .2 ...2 .5 |
|
10 5 0 , 5 1 6 0 |
|
|
|
кр уга и квадрата; 2 с |
Н =8 ГП а |
|
|
(0 ,3 8 - 0 ,5 8 С) |
|
|
|
|
|||
|
|
|
|
|
|
|
|
4 5 |
2 5 |
1 0 - 2 0 |
- |
Точечная, d = 1 ,5 ... 10 м м ; |
57 H R C 3 |
- |
|
|
|
||||||
|
|
|
|
5 м м /с |
|
|
|
4 0 Х |
2 0 |
- |
- |
П иния 3 - 2 0 м м ; |
5 6 0 H V |
0,2 (H V > 5 0 0 ) |
|
|
|
4 - 1 6 м м /с
процессытехнологические |
40Х |
60 |
' |
- |
0,5 -1,5 |
|
1 |
|
|
2 |
|
|
|
|
|
I„, M A |
P, кВт |
|
45 |
60 |
|
|
1,5-1,65 |
|
S45C (0,44 С; 0,19 Si; |
150 |
|
12-22 |
- |
|
0,62 Мп) |
|
|
|
|
|
С45,16М пСг5, |
60 |
|
|
5,0 |
|
90MnV8 |
|
|
|
|
|
50CrV4 |
100 |
|
3 |
|
|
X22CrM oV12.1V, |
100 |
|
35 |
|
|
X20C M 3V, |
|
|
|
|
|
33CrMoV24.12, |
|
|
|
|
|
55NiCrMoV6 |
|
|
|
|
|
41MoC11 (0,4% C, |
9,75 |
|
1900 |
30,0 |
|
1,3% Cr, 0,25% Mo), |
|
|
|
|
,OLC45 (0,45% C)
3 |
4 |
5 |
Линия, 20 мм/с |
59 H R Ca, 700 HV (48 H R C y |
|
|
495 HV после печной |
|
|
закалки), повышение |
|
|
износостойкости в 1,4 раза |
|
|
по сравнению с печной |
|
|
закалкой |
|
Полоса; |
650 -750 HV, 731 HV |
1 .7 (3 0 *) |
5 -5 0 MM/C |
(среднее) |
|
Полоса 10 мм; |
900 HV, 1100 HV |
0,6 (>600 HV) |
3,3 -16,6 MM/C |
|
|
Полоса 50 мм; |
1030 HV. При отклонении |
0,7; производительность |
10 -50 MM/C |
электронного пучка на 45° |
упрочнения |
|
твердость закаленной зоны |
до 4 смг/с |
|
снижается в два раза по |
|
|
сравнению с вертикальным |
|
|
падением |
|
Точечная, |
700 HV; 820 HV |
0,8 |
d=1,5 M M ; |
|
|
t=0,05 c |
|
|
Полоса 30 мм, |
810 HV |
0,5 |
11,5 MM/C |
(исх. 320 HV) 660 HV |
|
|
(исх. 170 HV) 900 HV |
|
|
(исх. 530 HV) |
|
0,3-0,6 с |
158 HV, нагрузка начала |
0.6 (HV>800) |
|
интенсивного износа |
|
|
возрастает до 300-320 Н |
|
|
(после печной закалки 60 Н) |
|
36 .табл Продолжение
*Стали после предварительной объемной закалки и отпуска.
Сметные
Таблица 37. Характеристика электронно-лучевой закалки металлов из ж ид кого состояния
Марка стали |
Параметры нагрева |
Глубина |
Скорость |
Микроструктура оплавленной |
Твердость |
||
(содержание |
|
|
|
оплав- |
охлаждения, |
зоны |
оплавленной зоны, |
основных |
UyCK, кВ |
1п, мА |
V, |
ленной |
°С/с |
|
полученные |
легирующих |
зоны, мм |
|
|
свойства |
|||
элементов, %) |
|
|
мм/с |
|
|
|
|
|
|
|
|
|
|
|
|
Р6М5 (штампы) |
16-60 |
10-125 |
|
1,3-25 |
103—5-105 |
Мелкодендритное строение, |
650-700 HV. |
|
|
|
|
|
|
ширина вторичных ветвей |
Стойкость штампов |
|
|
|
|
|
|
дендритов 1 -7 мкм. |
горячего |
|
|
|
|
|
|
Междендритная фаза состоит |
деформирования |
|
|
|
|
|
|
из эвтектических карбидов |
повысилась |
|
|
|
|
|
|
М(С размером 0,1-1 мкм |
на 40-50% |
Р6М5 |
16-60 |
10-125 |
|
1,3-25 |
103—5-105 |
Мелкодендритная структура с |
900 HV (охлаждение |
|
|
|
|
|
|
шириной вторичных ветвей |
при -1920°С). |
|
|
|
|
|
|
1-3 мкм. Междендритная |
Предел прочности |
|
|
|
|
|
|
фаза-эвтектические карбиды |
при изгибе соста |
|
|
|
|
|
|
размером 0,1-0,5 мкм и |
вил 2-2,5 ГПа по |
|
|
|
|
|
|
полигональные зерна |
сравнению |
|
|
|
|
|
|
размером 2 мкм |
с 1-1,5 ГПа в литом |
|
|
|
|
|
|
|
состоянии. |
|
|
|
|
|
|
|
Стойкость |
|
|
|
|
|
|
|
повысилась на 60% |
Х12 |
16-60 |
10-125 |
|
1,3-25 |
103—5-105 |
Более равномерное |
850-900 HV |
|
|
|
|
|
|
распределение легирующих |
(на 100 HV больше, |
|
|
|
|
|
|
элементов, чем до оплавления, |
чем твердость |
|
|
|
|
|
|
повышенное содержание |
основного металла). |
|
|
|
|
|
|
углерода. Излом характеризует |
Благодаря |
|
|
|
|
|
|
мелкокристаллическое вязкое |
уменьшению |
|
|
|
|
|
|
строение по сравнению с |
износа рабочих |
|
|
|
|
|
|
хрупким (до оплавления) |
кромок значительно |
|
|
|
|
|
|
|
увеличилась |
стойкость
пуансонов