
книги / Технология машиностроения.-1
.pdfДля проверки рассчитаем верхнее предельное отклонение замыкающего звена:
∆SAΣ = +0,25 – (–0,21 – 0,15 – 0,21) = 0,82.
0,6 < 0,82 → сумма допусков составляющих звеньев превышает допуск замыкающего звена на 0,22 мм. Необходимо одно из звеньев размерной цепи назначить регулировочным, т.е. уменьшить допуск на 0,22 мм, но таких звеньев нет.
Вопрос: можно ли выполнить все размеры звеньев размерной цепи по 12-му квалитету и при этом обеспечить заданную точность
(Т = 0,6) замыкающего звена АƩ1?
Ответ: да, возможно методом пригонки. В качестве звена для пригонки можно взять размер А2 (шайба), размер которой можно подогнать для обеспечения точности замыкающего звена.
Выводы:
1.Определены все исполнительные размеры и допуски деталей (позиции 4, 5, 6), входящих в сборочную единицу и находящиеся
всвободном состоянии на пальце (позиция 7) (см. рис. 5.6).
2.Это позволяет разработать рабочие характеристики деталей, входящих в сборочную единицу (позиции 4, 5, 6, 7) (см. рис. 5.6).
В качестве примера проверки правильности простановки размеров приведем рабочий чертеж пальца (рис. 5.8.) позиции 7 на рис. 5.6 и проанализируем его с точки зрения правильности простановки размеров.
Рассмотрим размерную цепь, возникающую при простановке размеров.
Баланс размерной цепи
30 + АΣ2 + 49 + 15 = 100.
Уравнение цепи
АΣ2 = 100 – (30 + 49 + 15).
→←
увел. уменьш.
61
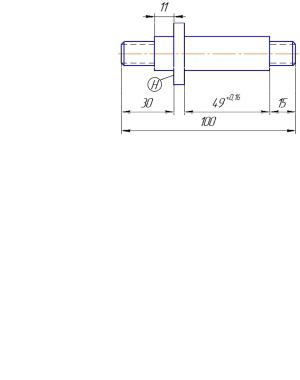
Рис. 5.8. Рабочий чертеж детали «Палец»
Решение цепи (обратная задача):
∆SАΣ2 = 0 – (0 + 0 + 0) = 0,
∆IАΣ2 = –0,87 – (0,43 + 0,16 + 0,43) = –1,89.
Ответ: АΣ2 = 6–1,89 (Т = 1,89).
В этом случае (при данном способе простановки размеров) может происходить смещение (в сборке) всей правой части детали от
|
опорной плоскости (поверхности) Н в |
|
пределах почти 2 мм, что недопустимо. |
|
Для обеспечения минимального до- |
Рис. 5.9. Частная размерная |
пуска на замыкающее звено необходимо |
ввести в рассмотрение частную размер- |
|
цепь |
ную (сборочную) цепь II (рис. 5.9). |
Целесообразно принять размер 55 по 12-му квалитету, т.е. 55–0,25. Баланс размерной цепи
АΣ2 + 49 = 55.
Уравнение цепи
АΣ2 = 55 – 49 = 6 мм,
→←
увел. уменьш.
∆SАΣ2 = 0 – (0) = 0,
∆IАΣ2 = –0,25 – (0,16) = – 0,41,
Ответ: АΣ2 = 6–0,41.
62
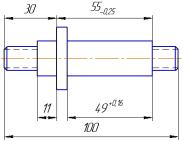
Такое значение допуска замыкающего звена вполне приемлемо, допуск значительно ниже: 0,41 вместо 1,89. Принимаем следующий вариант задания размеров (рис. 5.10).
Рис. 5.10. Окончательный вариант простановки размеров
Выводы (после рассмотрения примера):
1.Рассмотрена и освоена методика построения размерных цепей, как сборочной, так и подетальной.
2.С помощью теории размерных цепей решены конструкторские и метрологические задачи:
• установлены геометрические связи между размерами деталей, входящих в сборочную единицу (после выявления размерных цепей);
• установлены геометрические связи между размерами конкретной детали после выявления размерных цепей;
• выполнен расчет номинальных значений размеров, отклонений и допусков размеров звеньев;
• приведен расчет норм точности на составные части сборочного узла;
• проведен анализ правильности простановки размеров и отклонений на рабочем чертеже пальца.
Контрольные вопросы по главе
1. Понятие размерной цепи.
63
2.Отличия между конструкторской, технологической и сборочной размерными цепями.
3.Понятие составляющего и замыкающего звеньев.
4.Увеличивающие и уменьшающие звенья размерной цепи.
5.Методы обеспечения точности замыкающего звена.
6.Способ расчета размерных цепей «максимум-минимум».
7.Вероятностный способ расчета размерных цепей.
8.Последовательность выявления звеньев размерной цепи.
9.Прямая и обратная задачи размерного анализа.
10.Баланс и уравнение размерной цепи.
64
6. РАЗМЕРНЫЙ АНАЛИЗ И ОБОСНОВАНИЕ ПРИНЯТИЯ ТЕХНОЛОГИЧЕСКИХ РЕШЕНИЙ
Размерным анализом технологического процесса называют выявление и фиксирование размерных связей между операциями и переходами конкретного технологического процесса. Для решения проектной задачи, когда есть только чертежи деталей, необходима разработка первоначального, так называемого стартового варианта технологического процесса.
Целью размерного анализа является прежде всего обеспечение точности указанных на чертеже размерных связей поверхностей деталей.
С помощью размерного анализа выявляется наиболее эффективная (рациональная) структура технологического процесса, гарантирующая достижение поставленной цели.
В результате размерного анализа наиболее рационально формируются технологические операции и переходы, проверяются и уточняются принятые схемы базирования, определяются все операционные размеры и размеры исходной заготовки.
При разработке технологического процесса обработки деталей на каждую операцию составляется операционный эскиз, на котором указываются: обрабатываемые поверхности с размерами и допусками на них и необходимыми базами. Эти размеры могут быть промежуточными или окончательными. Они устанавливаются технологами и называются технологическими в отличие от конструкторских. С базами ситуация аналогичная. Окончательные технологические размеры могут не совпадать с конструкторскими, так как конструктор не всегда имеет возможность учитывать технологию изготовления и вид оборудования. Кроме того, конструктор не имеет права диктовать технологу технологические методы обработки и методы достижения точности (качества) обработанных поверхностей.
Однако технология изготовления и применяемое оборудование существенно влияют на простановку размеров на детали.
65
Технологу часто вместо конструкторских размеров приходится устанавливать технологические размеры и допуски на них. При этом при выполнении технологических размеров должны обеспечиваться размеры и допуски, установленные конструктором.
Определение технологических размеров и допусков производится на основе расчета технологических размерных цепей по мере выполнения технологического процесса.
Врезультате расчета может получиться, что принятая последовательность обработки (маршрут обработки) является нерациональной, так как допуски на технологические размеры получаются трудновыполнимыми.
Вэтом случае необходимо пересмотреть маршрут обработки
иустановить такую последовательность, при которой предусматривается максимальное совмещение технологических и конструкторских баз.
Таким образом, в задачу размерного анализа входит определение:
1) технологических размеров и допусков на них для каждого технологического перехода (операции) на основе расчета размерных цепей;
2) наиболее рациональной последовательности (маршрута) обработки отдельных поверхностей деталей, обеспечивающей требуемую точность размеров;
3) предельных отклонений размеров припусков и расчет размеров исходной заготовки.
Рассмотрим примеры:
I вариант примера (рис. 6.1).
Конструкторская размерная цепь (рис. 6.1, б): баланс размерной цепи
60 = АƩ + 20,
уравнение размерной цепи АƩ = 60 – 20 = 40,
→←
увел. уменьш.
66

Рис. 6.1. Первый вариант задания размеров: а – эскиз детали; б – конструкторская размерная цепь
∆SАƩ = 0 – (–0,52) = +0,52,
∆IАƩ = –0,72 – 0 = –0,74,
AΣ = 40−+0,520,74 (Т = 1,26).
67

II вариант примера (рис. 6.2).
Конструкторская размерная цепь (рис. 6.2, б): 60 = АƩ + 40,
АƩ = 60 – 40 = 20,
→←
увел. уменьш.
∆SАƩ = –0,74 – (+0,62) = –1,36, АƩ = 20– 1,36 (Т = 1,36).
Рис. 6.2. Второй вариант задания размеров: а – эскиз детали; б – конструкторская размерная цепь
68
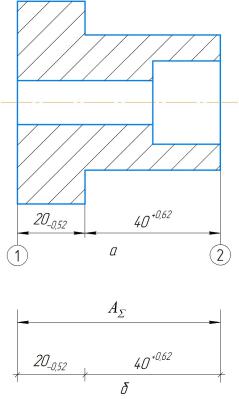
Рис. 6.3. Третий вариант задания размеров: а – эскиз детали;
б– конструкторская размерная цепь
IIIвариант примера (рис. 6.3).
Конструкторская размерная цепь (рис. 6.3, б):
|
АƩ = 40 + 20 |
= 60, |
|
|
→ → |
|
|
|
увел. |
увел. |
|
∆SАƩ = 0 + 0,62 |
= +0,62, |
||
∆IАƩ = –0,52 + 0 = –0,52, |
|||
А = 60+0,62 |
(Т = 1,14). |
||
Σ |
−0,52 |
|
|
69
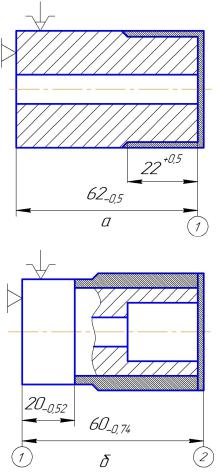
Рассмотрим варианты маршрута обработки детали с каждым из представленных вариантов простановки размеров. Технологическое решение без смены конструкторских баз, простановка размеров по 1-му варианту (рис. 6.4).
Рис. 6.4. Способ обработки детали с первым вариантом задания размеров с сохранением конструкторских баз: а – первый установ; б – второй установ
70