
книги / Оборудование литейных цехов
..pdfВ данной части коробки 2 встроены пластины 6, которые перед заполнением смесью из бункера 1 принимают горизонтальное положение, а на позиции разгрузки – вертикальное.
Над опокой 9 установлен жалюзийный разрыхлитель, состоящий из короба 7 и разрыхлителей 8. При работе дозирующая коробка 4 устанавливается под бункер 1, а после ее заполнения перемещается пневмоцилиндром 3 вправо. На позиции засыпки пластины поворачиваются в вертикальное положение с одновременным включением в работу разрыхлителей.
На валу каждого разрыхлителя устроено несколько рядов пальцев – пластин в перпендикулярном направлении. Каждый отдельный разрыхлитель вращается по отношению к соседнему в противоположном направлении. Благодаря такому встречному вращению смесь хорошо разрыхляется, аэрируется и выбрасывается в опоку, заполняя ее.
Вопросы для повторения
1.Чем отличается механизированная формовочная машина от формовочного автомата?
2.Последовательно назовите все технологические операции, выполняемые автоматом в составе АФЛ.
3.Как классифицируются формовочные автоматы по числу позиций?
4.Что означает позиционность формовочного автомата?
5.Как различают формовочные автоматы по характеру движения модельно-опочной оснастки?
6.Каковы преимущества безопочной формовки? Как подразделяются автоматы безопочной формовки по положению разъема формы?
7.Какие наиболее распространенные способы уплотнения применяются в формовочных автоматах?
8.Какие вы знаете способы извлечения моделей из полуформ? Какие силы влияют на отрыв болванов?
21

9.Каковы пути повышения прочности и сохранности болванов при протяжке?
10.Какие способы дозирования смеси и конструкции дозаторов вы знаете?
11.Как устроен коробчатый дозатор с жалюзийным затвором и разрыхлителем? Каковы преимущества этого дозатора?
12.Как классифицируются формовочные машины?
3.ПРЕССОВЫЕ ФОРМОВОЧНЫЕ МАШИНЫ
3.1. Особенности уплотнения форм прессованием
Формовочные и стержневые смеси по характеру физических свойств представляют собой сложные дисперсные тела, или системы, и обладают сыпучестью, связностью, пластичностью, вязкостью, текучестью, упругостью. Однако в различных условиях эти их свойства проявляются по-разному. Поэтому нельзя предложить единую универсальную физическую модель формовочной смеси для всех случаев.
Рис. 3.1. Напряжение |
Рис. 3.2. Схема перетекания смеси |
в элементарном объеме |
в процессе прессования формы: 1 – |
формовочной смеси |
прессовая колодка; 2 – опока; 3 – |
|
смесь; 4 – модель; 5 – стол машины |
В условиях уплотнения на прессовых формовочных машинах формовочные смеси обычного типа можно рассматривать
22
впервом приближении как связные сыпучие тела. Поэтому следует полагать, что при достаточно больших нагрузках на смесь
взамкнутом объеме (опоке) происходит перетекание ее из полостей более уплотненных в полости менее уплотненные, в результате чего форма равномерно уплотняется.
Перетекание заканчивается, и уплотнение завершается при достижении в различных полостях формы так называемого состояния предельного равновесия смеси.
На рис. 3.1 показан элементарный объем смеси, в котором под действием внешних нагрузок возникают главные напряже-
ния σ1 и σ2. На косой площадке m–n, расположенной под углом α к горизонту, возникают нормальные напряжения σα и касательные τα:
σα = σ1 cos2α + σ2 sin2α,
τa = σ1 − σ2 sin2α. 2
При нагружении в смеси (как в сыпучем теле) возникает боковое давление на стенки сосуда (опоки, модели), в который она помещена. Это давление пропорционально меньшему главному напряжению σ2 = kσ1, где k – коэффициент подвижности (сыпучести) смеси,
k= 1− sinφ, 1+ sinφ
здесь φ – угол естественного откоса материала в покое.
При определенных значениях главных напряжений σ1 и σ2 (σ1 > σ2) происходит сдвиг верхней части рассматриваемого объема относительно нижней. Равновесие в системе наступит, когда увеличение σ2 приведет к прекращению деформаций сдвига. Угол, который при этом составляет площадка сдвига с направлением меньшего напряжения для сыпучих тел, 45°+φ/2.
Если такое равновесие наступит не на всех участках формы, в смеси возникнет множество поверхностей скольжения,
23
и она будет перетекать из одних полостей формы в другие до наступления состояния равновесия.
Зависимость между нормальными (сжимающими) и касательными (сдвигающими) напряжениями выражается следующим образом:
τα = σαtgφ+ k1,
где φ – угол внутреннего трения смеси; k1 – сила сцепления, приходящаяся на единицу площади (для формовочных и стерж-
невых смесей), k1 = (0,1…0,2)105 Па.
При перемещениях частицы смеси, кроме внутреннего трения, должны преодолевать еще и силы сцепления k1.
Уравнение состояния предельного равновесия имеет следующий вид:
σ |
2 |
= σ tg2 |
|
45 − |
φ |
− 2k tg |
|
45 − |
φ . |
||
|
1 |
|
|
2 |
|
1 |
|
|
2 |
|
|
|
|
|
|
|
|
|
|
|
|
Схема перетекания смеси в процессе уплотнения формы прессованием может быть представлена следующим образом (рис. 3.2). В начале процесса происходит более сильное сжатие объема A, расположенного выше модели. Здесь раньше наступает состояние предельного равновесия, и происходят деформации сдвига. В результате часть смеси из этого объема перетекает в объемы B, где также приходит в состояние предельного равновесия. Затем в объемах B начинают происходить сдвиговые деформации, и часть смеси из них перетекает в объемы C. Процесс перетекания смеси продолжается до конца внедрения прессовой колодки в объем наполнительной рамки.
Первоначальный объем смеси должен быть больше объема опоки с моделью на величину, размещаемую в наполнительной, рамке, объем которой выбирается из условия обеспечения заданной плотности формы. При данных размерах опоки объем наполнительной рамки определяется ее высотой h, которую можно определить из равенства масс смеси до и после уплотне-
ния (рис. 3.3):
24
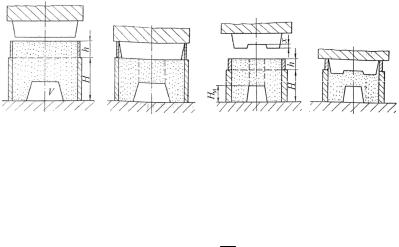
|
0 ( |
H + h |
) |
|
|
0 |
= |
( |
|
0 |
|
) |
δ, |
||
F |
|
− V δ |
|
|
|
F H − V |
|
||||||||
откуда |
|
|
|
|
|
|
|
|
|
|
|
|
|
|
|
|
|
|
|
|
V |
|
|
δ |
|
|
|
|
|||
|
|
h = H − |
|
|
|
|
|
−1 |
, |
|
(3.1) |
||||
|
|
F |
δ |
|
|
|
|||||||||
|
|
|
|
0 |
|
|
|
0 |
|
|
|
|
где F0 – площадь опоки в плане, м2; Н – высота опоки, м; h – высота наполнительной рамки, м; V – объем модели, м3; δ0 и δ – плотность смеси соответственно до и после прессования, кг/м3.
Для более равномерного уплотнения формы часто применяют профильные прессовые колодки (рис. 3.3, б), размеры выступов которых делаются в соответствии с контуром модели.
а |
б |
Рис. 3.3. К определению высоты наполнительной рамки при прессовании: а – плоской колодкой; б – профильной колодкой
Высота наполнительной рамки при этом подсчитывается по формуле
h = (H − Hм ) δδ −1 ,0
авысота выступов профильной колодки
x= H 1− δ0 .
мδ
Уплотнение литейных форм прессованием – наиболее известный способ изготовления литейных песчано-глинистых форм уплотнением. Этот способ имеет ряд преимуществ, в силу
25
которых он и получил широкое распространение. Основные его преимущества: бесшумность и простота процесса; возможность создания давления прессования любой величины; относительно низкая энергоемкость.
Однако этот способ имеет существенный недостаток – значительную неравномерность распределения плотности смеси при уплотнении по высоте опоки, в силу чего он пригоден только для изготовления низких опок (переуплотнение смеси над моделью и недоуплотнение ее вокруг модели).
Прессование нашло широкое применение не как самостоятельный способ, а в комбинации с другими, например со встряхиванием, пескострельным процессом, вибрацией и др. Прессование несет основную силовую нагрузку; другие же процессы играют, хотя и вспомогательную, но чрезвычайно важнуюроль, так как они создают предварительную плотность смеси в околомодельной зоне оснастки и тем самым обеспечивают технологически необходимую равномерность плотности по всей высоте полуформы.
3.2. Классификация прессующих механизмов и элементов прессовых машин
Прессующие механизмы формовочных машин разделяются на группы по следующим признакам:
а) по способу приложения прессующего воздействия – на механизмы с верхним, нижним и двусторонним прессованием; б) по величине прессующего воздействия – на механизмы с низким p ≤ 0,3 МПа (3,0 кгс/см2); средним p = 0,3…0,7 МПа
(3–7 кгс/см2); высоким p = 2…5 МПа (20–50 кгс/см2) и сверхвысоким p > 5 МПа (более 50 кгс/см2) удельными давлениями прессования;
в) по конструктивному выполнению прессовой головки – на механизмы с жесткой плоской и профильной плитой, диафрагменные, многоплунжерные, катковые, рычажные, мундштучные, с решетчатым элементом, лопастные и др.;
26
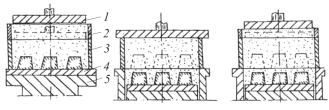
г) по роду привода – на пневматические, гидравлические, пневмогидравлические и электромагнитные;
д) по типу траверсы – на поворотные в виде консольной балки, поворотные в виде балки на двух опорах, в виде тележки и неподвижные.
3.3. Верхнее, нижнее и двустороннее прессование
При уплотнении литейных форм на машинах различают верхнее и нижнее прессование. При верхнем прессовании дополнительный объем смеси вдавливается в опоку прессовой колодкой со стороны, противоположной разъему формы (рис. 3.4, а). При нижнем прессовании этот дополнительный объем вводится со стороны разъемаформы при помощи самоймодели (рис 3.4, б).
При двустороннем прессовании дополнительный объем смеси вдавливается в опоку как со стороны модели, так и со стороны, противоположной разъему формы (рис. 3.4, в).
а |
б |
в |
Рис. 3.4. Способы прессования: а – верхнее; б – нижнее; в – двустороннее; 1 – прессовая колодка; 2 – наполнительная рамка; 3 – опока; 4 – модельная плита; 5 – стол
Распределение плотности смеси по высоте опоки при указанных методах прессования неодинаково. Наибольшая плотность создается в слоях, близких к поверхности, передающей силовое воздействие (прессовой колодке или модели), и по мере удаления от нее уменьшается вследствие торможения смеси о стенки опоки (рис. 3.5).
27
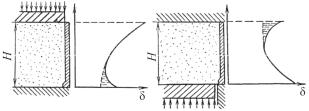
аб
Рис. 3.5. Распределение плотности формовочной смеси по высоте опоки: а – при верхнем прессовании; б – при нижнем прессовании
Чем выше опока, тем больше неравномерность распределения плотности смеси по ее высоте. Величина и характер распределения плотности зависят не только от высоты формы Н, но и от отношения этой высоты к наименьшему поперечному сечению. Для получения равномерного уплотнения это отношение не должно превышать 1–1,25.
Основным фактором уплотняющего воздействия на форму при прессовании является удельное давление прессования p. Исследования, проведенные Н.П. Аксеновым, позволили получить зависимость средней плотности δср (г/см3) литейной формы от удельного давления прессования p (кгс/см2):
|
ср |
|
( |
+ Сp0,25 |
) |
|
|
||||
δ |
|
= |
1 |
|
, |
(3.2) |
|||||
или |
|
|
|
|
|
|
|
|
|
|
|
|
|
δ |
ср |
−1 |
|
4 |
|
|
|
||
p = |
|
|
|
|
|
105 Па, |
(3.2, а) |
||||
|
С |
|
|
||||||||
|
|
|
|
|
|
|
|
|
|
где C – коэффициент уплотняемости смеси, C = 0,4…06. Процесс уплотнения формы прессованием происходит
в условиях внутреннего и внешнего трения смеси. Сила трения зависит от размеров, формы, конфигурации модели, скорости приложения уплотняющего усилия, коэффициента трения смеси о стенки опоки и модели, текучести формовочной смеси и др.
28
Состояние смеси при этом будет характеризоваться: а) боковым давлением, которое вызывает трение смеси о стенки опоки и поверхность модели. Величина этого давления составляет 0,3–0,5 вертикального сжимающего напряжения; б) торцевым трением смеси о прессовую колодку и модельную плиту, которое препятствует перемещению смеси.
Трение смеси о стенки опоки и модели снижает эффект прессования. В силу этого недостатка метод уплотнения форм прессованием ограничен и применяется для сравнительно низ-
ких опок (H = 0,15…0,20 м).
Коэффициент внешнего трения зависит от состояния поверхности опоки, модели и от свойств материала.
Следует отметить, что коэффициент внешнего трения зависит также от скорости прессования, что очень важно при импульсных и высокоскоростных методах уплотнения. При прессовании же, где скорость прессовой колодки низкая и колеблется в незначительных пределах, можно считать, что коэффициент внешнего трения не зависит от скорости и является величиной постоянной (для данной смеси).
При верхнем прессовании формовочная смесь из наполнительной рамки запрессовывается в опоку прессовой колодкой, при этом происходит переуплотнение смеси над моделью и недоуплотнение вокруг нее. При нижнем прессовании смесь обычно запрессовывается моделью и модельной плитой со стороны разъема формы. Рамкой в этом случае служит углубление в неподвижном столе машины. Плотность смеси по высоте опоки при нижнем прессовании значительно более высокая около модели и меньшая со стороны контрлада. Однако это утверждение справедливо, если уплотняется одна модель в опоке. В этом случае внешнее трение (между стенками опоки и смесью) способствует уплотнению смеси в карманах между моделью и стенками опоки. В карманах же формы между несколькими моделями смесь одинаково плохо уплотняется как при верхнем, так и при нижнем прессовании. Точность форм при нижнем прессовании ниже, чем при верхнем.
29
При любом способе уплотнения не удается точно сдозировать необходимый объем смеси в опоку. При верхнем прессовании излишки смеси обычно срезают. При нижнем этого сделать нельзя, и поэтому при сборке полуформы сопрягают не по ладу, как при верхнем прессовании, а по поверхности уплотненной смеси, уровень которой выполняют несколько выше лада опоки.
Таким образом, несмотря на определенные технологические преимущества нижнего прессования, в силу указанных причин оно не нашло широкого применения. Поэтому нижнее прессование рекомендуется применять в специализированных формовочных машинах, предназначенных для изготовления форм, в которых располагается только одна отливка, или в случаях, когда нижнее прессование позволяет получить какой-либо дополнительный эффект.
Двустороннее прессование применяют в том случае, когда необходимо получить одинаковую плотность с обеих сторон (обе стороны рабочие) и когда положение уплотненной смеси относительно опоки (камеры прессования) не оказывает влияния на последующие операции, например в машинах безопочной формовки.
3.4. Прессование жесткой или профильной плитой
При прессовании жесткой плоской плитой неравномерность плотности смеси по высоте полуформы объясняется различной высотой столбов смеси и абсолютно одинаковой их деформацией. Профильная плита устраняет этот недостаток.
Профильные плиты целесообразно использовать только в массовом производстве (см. рис. 3.3, б).
3.5. Прессующий механизм с гибкой диафрагмой
При уплотнении смеси плоской колодкой над моделью и по ладу полуформы получается переуплотнение, а по боковым поверхностям модели – недоуплотнение смеси. Прессование ли-
30