
книги / Напряженное состояние и прочность оболочек из хрупких неметаллических материалов
..pdfн а торцовую |
поверхность стенки стеклоэлемента (рис 52, б). Послед |
нее ж е, как |
правило, приводит к полному имплозионному разруше |
нию конструкции и ее внутреннего насыщения в целом. На основании данного опробирования сделан вывод о недопустимости применения рассмотренного конструктивного решения узла соединения для проч ных оболочек из хрупких неметаллических материалов типа стекол, ситаллов, керамики.
Разработка разъемных соединений с цилиндрическим шарниром качения между контактирующими подвижными поверхностями пока зала лиш ь некоторый положительный эффект такой реализации гра ничных условий. Согласно расчету в стеклоэлементе хотя и не удается в полную меру использовать явление эффекта обоймы, как и в преды дущем случае, но при этом в наиболее напряженной зоне хрупкогоэлемента — зоне ожидаемого разрушения, концентрация меридиональ ных напряж ений уменьшена на 25 %; коэффициенты концентрации главных напряж ений для этой зоны, например, в сферическом стекло
элементе |
составили а г = 0,5 р; а 2 = —4,3р; а 3 = —7 ,0 р. Одновре |
менно на |
торце стеклоэлемента отмечен существенный, до —6,4р,. |
рост меридиональных напряжений, что на 25 % выше аналогичных, действующих в безмоментной области. Окружные напряжения в рас сматриваемой локальной зоне тем не менее на 16 % ниже таковых, действующих на расстоянии 2,2 h в оболочке. Концентрация сжимаю щих напряж ений в стальном кольце-обрамлении составила порядка 10— 11 р и охватила практически весь объем материала опорной стенки последнего. Н апряженность хрупких элементов оболочки падает по мере удаления от узла разъема; на расстоянии порядка 2 ,2 h локальное возмущение напряженного состояния полностью затухает.
В целом, как видно на рис. 53, напряженное состояние сферической оболочки с экваториальным разъемным соединением типа цилиндри ческого шарнира можно считать условно удовлетворительным. Прида ние новой формы опорной поверхности стеклоэлемента, когда его кром ки округлены по радиусу в виде, копирующем форму разъемной поверхности металлического кольца-обрамления, не только не позво лило улучшить напряженное состояние хрупкого элемента, а значи тельно ухудшило последнее: зафиксирован ощутимый рост главных растягивающ их напряжений, действующих по всей скругленной по верхности стеклоэлемента. Именно поэтому последнее решение не пред ставляется возможным для реализации. В соответствии с расчетными данными получены результаты экспериментов: минимальная несущая способность сферической оболочки с таким соединением элементов составила более 147 МПа; ни одна из оболочек не разруш иласьи не получила опасного повреждения при нагружении допредельной в дан ном опыте нагрузки. В момент действия максимальной нагрузки в стен ке оболочки действовали как растягивающие (порядка 74 МПа), так и сжимающие (—942 МПа) напряжения, а в кольце-обрамлении осевые напряж ения ощутимо превышали предел текучести стали. При раз грузке, начиная с давлений 23—9 МПа, стеклоэлементы всех оболочек получили значительные повреждения (см. рис. 52, в), практически не позволяющие использовать их в дальнейшем. Нагружение таких
Рис. 53. Напряженно-деформированное состояние в зоне механического соеди нения полусферических стеклоэлементов, разъем которых выполнен между ци линдрическими (а) и коническими (б) поверхностями колец-обрамлений.
конструкций повторно-статической нагрузкой с максимальным давле нием в цикле 98 МПа подтвердило ранее полученные результаты и пока зало абсолютную неработоспособность последних: при разгрузке на пер вом цик левее обол очки получили повреждения (см. рис. 52, г), которые обусловили их полное имплозионное разрушение на мелкие осколки на втором цикле нагружения во время повышения давления до 12—27 МПа. В дополнение отметим, что непрерывное нагружение составных обо
лочек с разъемным |
механическим |
соединением типа цилиндрического |
ш арнира качения |
в течение 300 ч |
наружным гидростатическим дав |
лением 10, 20, 29 МПа (по 100 ч каждым) не вызывало накопления по вреждений и разруш ения стеклоэлементов сборки и клеевых швов. По следнее позволяет отметить надежную работоспособность шарнирного соединения при длительном действии гидростатического давления.
Введение в разъем между цилиндрическими опорами дополнитель ного элемента — стального кольца малой жесткости — вызвало при действии однократной кратковременной статической нагрузки неко торое понижение давления разрушения конструкций до 127— 148 МПа; существенное увеличение жесткости этого кольца еще более снижает несущую способность составных оболочек, которая теперь составляет 27— 70 МПа (см. табл. 18). Экспериментальное изучение работоспособ ности таких узлов соединений при действии повторно-статических на грузок, соответственно равных 98 и 39 МПа, показало низкую долго вечность последних: оболочки всегда начинали разрушаться при раз грузке на 1— 2 циклах нагружения в условиях действия внешнего давления 26— 14 МПа и максимальных напряжений: растягивающих
— 6,9— 3,9 М Па, сжимающих — 177— 157 МПа (см. рис. 52, 5). Абсо лютная неработоспособность составных оболочек с соединениями эле ментов типа цилиндрического шарнира качения с незначительнымскольжением деталей в разъеме объясняется относительно удовлетвори тельной работой такого узла только в период повышения нагрузки, действующей на конструкцию. Ограниченная подвижность элементов ш арнирного узла соединения при разгрузке, вследствие схватывания перемещающихся поверхностей в зоне контакта, из-за локального пластического деформирования металлических вставок не позволяет вернуться подвижным деталям в свое исходное положение, что приводит к возникновению обратного момента на торце стенки стеклоэлемента, который и вызывает действие растягивающих напряжений вследствие изгиба. Последние обусловливают развитие трещин в ло кальной зоне оболочки. Катастрофические трещины, зарождающиеся в зоне соединения стеклоэлемента и направленные эквидистантно срединной поверхности, инициируют отколы наружных волокон этой области в глубь стенки вплоть до полного исчерпания ее толщины от стыка в сторону полюса на расстояние, равное четырем — шести толщинам стенки оболочки. В момент сквозного разрушения стенки хрупкого элемента происходит полное разрушение оболочки на мел кие осколки (см. рис. 52, ё).
В результате комплексного изучения составных оболочек из стек ла, в которых использованы два типа соединений, обеспечивающих разъем между металлическими узлами по конической поверхности
(рис. 54), оценена реальная возможность реализации таких конструк тивных решений и высказано мнение о нерациональности использо вания последних вследствие низкой эффективности. Сферические обо лочки, стеклоэлементы которых состыкованы с кольцом-обрамлением по горизонтальной поверхности (рис. 54, а, б), разруш ались при внеш нем давлении 88—92 МПа, в то время как составные сферические и цилиндрические оболочки с более сложным соединением второго типа (рис. 54, в) теряли несущую способ ность при нагрузке 104— 129 МПа.
Смазка
Рис. 54. Два типа механического соединения в составной оболочке из стекла со сталь ным кольцом-обрамлением, реализующим разъем по конической поверхности.
Низкий уровень несущей способности конструкций с соединением эле ментов первого типа вызван применением в процессе нагруж ения условий взаимодействия по поверхности разъема, происходящих в ре зультате потери подвижности деталей в узле соединения. Возникаю щая непрерывность поведения сопрягаемых в разъеме элементов обус ловлена уменьшением (на 40 %) площади контакта кольца-обрамления с опорным кольцом и вызвана действием больших сил трения между скользящими поверхностями, препятствующими взаимному перемеще нию деталей. Изменение в процессе повышения внешней нагрузки условий на границах состыкованных деталей резко ухудш ает напря женно-деформированное состояние оболочки в зоне соединения: во внутренних слоях стеклоэлемента появляются значительные по вели чине радиальные растягивающие напряжения (см. рис. 53, б), которые вызывают его разрушение (см. рис. 52, ж, з). Подтверждение этому получено в результате фиксирования зон, стадийности накопления
повреждений и разрушения конструкций, а также в результате изу чения фрактографий характерных зон на поверхностях излома в раз рушенных соединениях стеклоэлементов (см. следующий параграф). Кроме того, повышенная жесткость внутреннего опорного участка обрамляющего кольца, не позволяет создать благоприятное распреде
ление |
напряжений в торце стенки стеклоэлемента, что также опреде |
л я ет |
низкий уровень разрушающих нагрузок. Повторно-статические |
испытания оболочки с рассматриваемым соединением элементов по той же причине не позволили добиться удовлетворительной работо способности конструкции.
Применение второго типа соединения, в котором опорные поверх ности стенки стеклоэлемента и кольца-обрамления имеют конические поверхности, а жесткости соединяемых деталей соизмеримы (приве денная жесткость стального кольца не превышает 2,0) позволило не сколько повысить предельную несущую способность оболочек. Раз рушение оболочек с таким соединением (см. рис. 52, и) происходило вследствие исчерпания прочности стекла от действия сжимающих на пряжений в стенке хрупкого элемента, примыкающей к узлу соединения. Положительным в опробованном решении узла разъема является полное •отсутствие растягивающих напряжений в стеклоэлементе на всех этапах работы конструкции. Пластическое деформирование кольца-обрамле ния в момент повышения нагрузки, когда напряжения превышали предел текучести стали, следует отнести к отрицательным явлениям.
Данные по работоспособности этого соединения, полученные для составных оболочек последовательным нагружением по блочной схе ме до максимальных давлений в цикле 39 и 59 МПа, позволяют гово рить, что узел разъема обладает минимальным ресурсом — порядка 100 циклов. Накопление повреждений в стенке стеклоэлемента не поз в о л я е т е высокой степенью надежности гарантировать использование данного конического разъема в оболочечных системах, когда макси мальное давление в цикле равняется или превышает 0,45 кратковре менной разрушающей нагрузки. Последнее указывает на неэффектив ное использование неорганического стекла в аналогичных конструк циях, предназначенных для эксплуатации на предельных глубинах океана.
Долговечность нового узла конического разъема оценена также при длительном (более 300 ч) действии внешнего гидростатического давле ния 10, 20, 29 МПа, изменяемого ступенями через каждые 100 ч. Вслед ствие действия низкого уровня внешней нагрузки ни в одной из обо лочек не зафиксировано повреждение стеклоэлементов. Таким образом, ресурс долговечности данного механического соединения элементов составляет более 300 ч работы под нагрузкой.
Низкий уровень максимального давления в цикле при повторно статических нагружениях из-за относительно высокой напряженности стеклоэлемента в зоне соединения элементов, а такж е усложненная технология обработки и сборки сопрягаемых поверхностей не позволя ют в конечном итоге рекомендовать его к широкому использованию.
Всестороннее практическое использование составных оболочечных систем из стекла, эксплуатируемых под действием высокого внешнего
давления, тормозится из-за отсутствия надежного работоспособного разъемного соединения элементов существенно различной жесткости. В данном случае имеется в виду торцовое соединение стеклянного обо лочечного элемента осесимметричной формы, который опирается на металлическую вставку — плиту существенных размеров.
Две предыдущие конструкции соединения хрупких элементов оди наковой жесткости, опробованных только в виде срединного сты ка, решено изучить применительно к новым условиям. В качестве вариан тов рассмотрены конструкции, в которых стеклянный сферический сег мент с телесным углом п ср вклеен эпоксидным компаундом в стальное кольцо-обрамление, опирающееся на жесткую опорную плиту толщ и ной 25 мм. Представленные типы стыков имеют некоторое сходство в реализации граничных условий; разъем осуществлен по конической поверхности. Различие этих соединений в том, что стеклоэлементы омоноличены с кольцами-обрамлениями в первом случае по горизон тальной поверхности, во втором — по конической. Учитывая то, что соотношения конструктивных жесткостей края стенки оболочки и ме таллического обрамления, толщины клеевых прослоек на торцовой и боковых поверхностях и их соотношения, несовершенства м акрогео метрии торца стенки стеклоэлементов, а такж е технология склейки и монтажа для этих узлов соединений практически одинаковы, различие в напряженности конструкций определяется стабильностью реализа ции принятых граничных условий по поверхности разъема деталей в процессе всего периода работы рассматриваемых узлов.
Численные исследования полусферических сегментов с описан ными узлами соединений позволили проанализировать зависимости напряженно-деформированного состояния торца стенки оболочки от условий конструктивной реализации стыков и указать по уровню на пряженности оболочки в зоне соединения элементов степень приемле мости таковых. Оба разъема подвижных соединений вызывают суще ственную концентрацию главных напряжений, неравномерность их распределения по толщине стенки стеклоэлемента в наиболее нагру женной зоне оболочки, причем последнее конструктивное решение все же ближе к оптимальному. Затем в расчетных схемах были учтены ре зультаты предварительных экспериментов, поставленных для уяснения характера работы рассмотренных узлов соединений вплоть до предель ных нагрузок. Согласно этим данным оба типа конструкций теряю т подвижность элементов в узлах соединений: давление потери подвиж ности элементов в узлах соединений конструкций различно — соот ветственно порядка 39 и 45 МПа.
Учитывая то, что разрабатываемые конструкции предназначены для эксплуатации при предельных давлениях, далее рассматривали измененные условия работы последних. Оба типа соединения в резуль тате больших сил трения, которые возникают между кольцами-обрам лениями и опорными плитами и препятствуют относительному переме щению элементов, образовывают непрерывность поведения сопрягаемых элементов конструкции. В дополнение к этому усугубляю т процесс взаимодействия элементов под нагрузкой существенные деформации опорной плиты. Анализ напряженно-деформированного состояния

ним рассмотренных узлов разъемных соединений, работаю щ их в реаль ных условиях нагружения, следует использовать кольцевые резиновые уплотнители, уложенные в канавки, проточенные на контактирую щ их поверхностях, а также в некоторых случаях другие специальны е меры типа замкнутых герметизирующих покрытий и кож ухов.
В целом полученные в данном параграфе результаты нельзя считать удовлетворительными из-за относительно низких предельной несущей •способности и ресурса надежной работы конструкций, вы званны х от сутствием работоспособного соединения, которое может эффективно реализовать высокую прочность хрупкого материала в составной си стеме путем искусственного создания благоприятного напряж енного состояния локальных зон элементов сборки в разъеме.
5.Анализ разрушения узла соединения
воболочечной конструкции из стекла методом ф рактограф ии
Разрушение составных оболочек из стекла при предельных кратко временных нагрузках представляет особый интерес для разработчи ков новых конструкций с точки зрения изучения причин и самого про цесса накопления повреждений и нарушений сплошности м атериала в наиболее напряженных зонах, знание которых поможет выработке рекомендаций по конструированию соединений в таких системах. Цель настоящего исследования — разработать методику анализа поверхности излома стеклоэлемента как критерия оценки составных оболочек.
Численное исследование с помощью МКЭ локальных зон соеди нений в оболочках, экспериментально подтвержденное с помощью малобазной тензометрии до нагрузки 25 МПа, позволило изучить н ап ря женно-деформированное состояние составных систем, исходя из пред
положения упругой работы элементов сборки в |
процессе нагруж е |
ния, не изменяющего условия сопряжения узлов. |
П оскольку экспе |
риментальное изучение конструкций методом |
тензометр ирования |
при значительных ( > 59 МПа) нагрузках, возрастающих вплоть до разрушения оболочки, затруднено по техническим причинам, эти испы тания обеспечили получение только ориентировочных оценок совмест ной работы элементов и значений нагрузки разруш ения конструкций. Анализ экспериментальных и расчетных данных позволил отметить изменение условий работы узлов некоторых конструкций при относи тельно низких нагрузках, превышающих 69 МПа, которые приводили к преждевременному разрушению стеклоэлементов в неудачно скон струированных разъемных соединениях. При этом результаты числен ных исследований, осуществленных по новым расчетным схемам, в которых учтены эти изменения, требуют экспериментального под тверждения, проведенного по новой методике.
В результате действия создавшихся условий сопряжения деталей соединения (в дальнейшем рассмотрим одну из конструкций, в которой стеклоэлемент склеен с кольцом-обрамлением по горизонтальной по верхности площадью 6,4 1СГ3 м2, а разъем осуществлен между ме
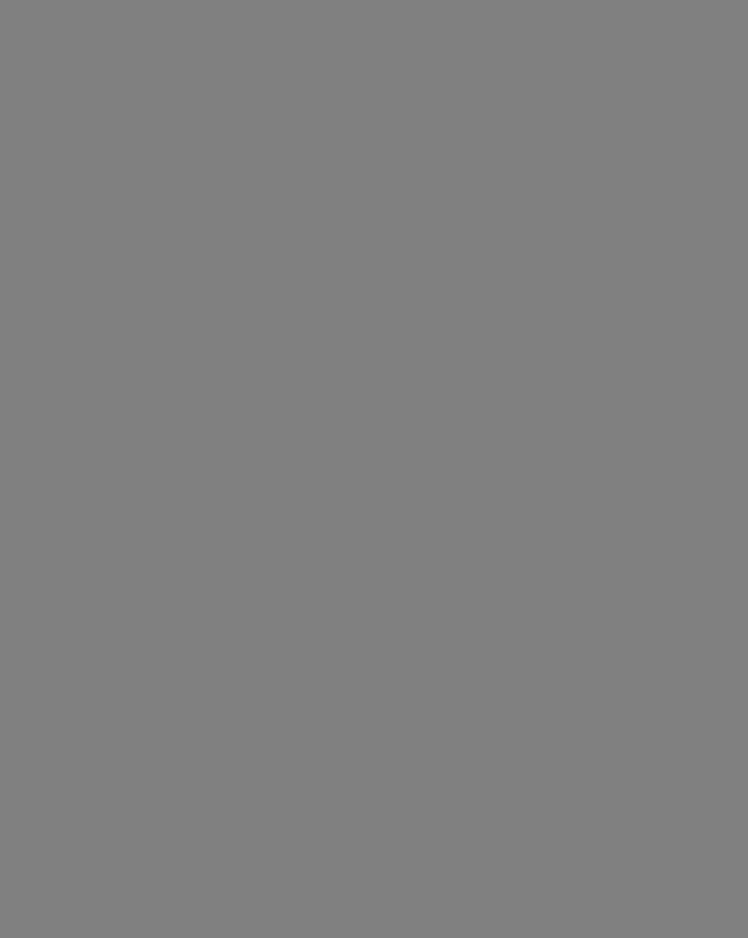
ного состояния, продолжительности нагруж ения. Кроме того, испыта ния на образцах позволили получить механические характеристики материала элементов сборки оболочки при сжатии и изгибе, предста вительно отражающих работу стекла в конструкции.
Согласно предложенной программе испытаний образцы разделили на две группы: первая включала 40, вторая — 5 образцов. О бразцы вырезали с помощью алмазных отрезных кругов из штампованных
стеклянных колпаков-заготовок, используемых для |
изготовления |
со |
||||||||
ставных оболочечных конструкций. Стержни прямоугольного |
попереч |
|||||||||
ного сечения |
размером 10 X 10 X 110 мм и цилиндрические |
образцы |
||||||||
Т а б л и ц а |
19. |
Прочность |
стекла |
МКР-1 при испытаниях |
на изгиб и |
сжатие |
||||
В ид напряж ен ного |
со |
Ч и сл о |
о б р а з |
Р азб р о с зн ач е |
С р ед н ее |
зн а К о эф ф и ц и ен т |
в а |
|||
стояни я |
|
|
цов» |
ш т. |
ний. М П а |
чение, |
М П а |
ри ац и и , |
% |
|
Поперечный изгиб |
|
40 |
40,5—71,1 |
56 |
|
1 2 ,8 2 |
|
|||
Одноосное сжатие |
|
|
5 |
1484— 1608 |
1537 |
|
3,16 |
|
||
с площадью сечения, равной 10 X 30 мм, изготовляли для |
испытаний |
|||||||||
соответственно при |
поперечном |
изгибе и одноосном сжатии. О бразцы |
после механического шлифования алмазным инструментом, позволив шим получить примерно восьмой класс шероховатости поверхностей, готовили к испытаниям. Подготовка включала визуальный отбор, а также обмер образцов, который производили с помощью микрометра с точностью до ± 0 ,01 мм. Образцы, имеющие видимые дефекты струк туры и поверхности, выбраковывали.
Испытания образцов на поперечный изгиб проводили по схеме чистого изгиба приложением двух перерезывающих сил в центре про лета; расстояние между крайними опорами составляло 80 мм, между линиями приложения поперечных сил — 40 мм. Д ля сохранения кар тины разруш ения и облегчения изучения его истории образцы с двух противоположных боковых сторон покрывали липкой полиэтиленовой пленкой. Максимальные растягивающ ие напряж ения при изгибе рассчитывали по известной формуле сопротивления материалов [126]. Обращали внимание на аккуратность и идентичность установки образ цов на опоры.
Подготовку и проведение испытаний образцов на одноосное сжатие вели по ранее описанной методике.
Механические испытания образцов при действии поперечного из гиба и одноосного сжатия проводили на универсальных испытатель
ных машинах, соответственно ЦД-4 и ЦД-40. Скорость |
роста напря |
|||
жений при |
испытаниях |
выдерживали |
постоянной, |
составляющей |
2—3 МПа/ с |
в первом |
случае и 25— |
29 М Па/с — во |
втором. Точ |
ность замера разрушающих нагрузок составляла ± 0 ,5 % их величины. Результаты испытания образцов двух групп (табл. 19) показали, что прочность стекла МКР-1 на изгиб составляет 1/28 часть их проч ности при одноосном сжатии (1537 МПа — среднее значение); при этом разброс отдельных значений, характеризуемый коэффициентом ва-