
книги / Напряженное состояние и прочность оболочек из хрупких неметаллических материалов
..pdf4.Напряженно-деформированное состояние
инесущ ая способность различных типов
разъемных соединений
Необходимость устранения прямого контакта стекла с металлом по поверхности разъема и дальнейшее развитие конструктивных ре шений, опробованных при проектировании составных стеклянных оболочек с неразъемными клеевыми соединениями, включающими ино родные вставки, привели к разработке новых типов узлов соедине ний, в которых предложены вклейка торцовых зон стеклоэлементов в металлические кольца-обрамления и создание разъема между метал лическими поверхностями. При таком способе соединения взаимные перемещения стекла по металлу исключены. Установочные модельные эксперименты по изучению предельной несущей способности составных оболочечных конструкций с новыми типами срединных и торцовых разъемов хрупких элементов сопоставимой и существенно различной жесткости показали, что их прочность определяется напряженным состоянием стеклоэлемента в окрестностях стыковой поверхности, которое, в свою очередь, зависит от соотношения конструктивных жесткостей края оболочечного элемента и металлического обрамле ния, конструкции кольца-обрамления, толщины клеевых омоноличивающих прослоек на торцовой и боковых поверхностях и их соотноше
ний, а |
такж е от несовершенств макрогеометрии края стеклоизделия |
||
и технологических |
дефектов опорных поверхностей |
и кромок в виде |
|
сколов, |
вскрытых |
газовых пузырей и др. В то же |
время отсутствие |
систематизированной информации о влиянии жесткости и конфигура ции кольца-обрамления, условий его взаимодействия с сопрягаемыми подвижными деталями соединения на распределение напряжений в стеклоэлементах и в целом на прочность составной оболочки не позво ляет применять последние. Научно обоснованный подбор выделенных конструктивных параметров и наложение ограничений на технологи ческие факторы сборки узла соединения позволяет надежно обеспе чить высокую предельную несущую способность составных оболочек из хрупких неметаллических материалов данного класса.
В связи о этим поставлены и требуют решения следующие конкрет ные задачи .
1. Исследование напряженно-деформированного состояния некото рых типов подвижных разъемных срединных соединений элементов в составных сферических и цилиндрических оболочках из стекла с целью снижения уровня напряженности в локальной зоне последних за счет реализации благоприятных граничных условий по поверхности разъе ма в условиях действия высокого внешнего давления.
2. Изучение влияния конструктивно-технологических параметров разъемных соединений на напряженно-деформированное состояние и несущую способность составных оболочек из стекла с целью рацио нального конструирования последних. Выявление специфики разруше ния составных стеклянных оболочек с новыми узлами срединных и торцовых соединений хрупких элементов одинаковой и существенно различной жесткости и установление возможности их использования.
При изучении различных типов разъемных механических соеди нений элементов использована разработанная авторами методика ра ционального конструирования работоспособных соединений в состав ных системах из хрупких материалов — стекол, ситаллов, керамики. Комплексное решение задачи предусматривает применение расчет ного и экспериментального методов исследования таких объектов.
Предмет апробирования возможных схем стыковки элементов — изучение напряженно-деформированного состояния локальны х обла стей и предельной несущей способности составных оболочечных систем в зависимости от конструктивно-технологических факторов соеди нений элементов, а также установление зон максимальной концентра ции напряжений в таких системах. Основой для реализации поставлен ной цели являлось применение численного метода решения смешанной задачи линейной теории упругости в новых конструкциях [109] в со
четании с исследованиями опытных образцов |
в лабораторны х |
усло |
виях. Достоверность полученных результатов |
подтверж далась |
сопо |
ставлением последних. |
|
|
Лабораторные эксперименты проводили на |
опытных сферических |
и цилиндрических с монолитными полусферическими оконцовками оболочках с одним разъемным узлом соединения, в которых использо ваны стеклоэлементы, полученные из стеклоизделий-заготовок с наруж
ным диаметром порядка 200+l мм, длиной 250 мм, толщиной стенки
11+6 мм. Собираемые опытные конструкции имели типичные для стеклоизделий, выработанных методом прессования, несовершенства: при относительно правильной геометрической форме наруж ной поверх ности существенную разнотолщинность стенок (10,9— 16,6 мм). Д опол нительная механическая шлифовка алмазным инструментом торцовых зон стеклоэлементов для сведения до минимума их разнотолщ инности проведена по 3-му классу точности обработки. После этого толщ ина •стенок стеклоэлементов в зоне соединения изменялась от 10,90 до 11.05 мм; среднее арифметическое отклонение профиля торцовых по
верхностей составляло |
0,63 |
• 10_6м. Торцовые кромки притуплялись |
|
фасками порядка 0,5 |
• 45°. |
М еталлические вставки изготавливали |
|
из стали 40Х |
и стали 45, термообработанных до 28— 32 HRC; отклоне |
||
ния размеров |
находились в |
пределах ± 0 ,0 5 мм, а класс ш ероховато |
сти посадочных поверхностей составлял 8—9.
Склейку конструкций проводили по единой технологии с помощью клея-компаунда Д -9 холодного отвердения, приготовленного на осно ве эпоксидной смолы ЭД-16 и отвердителя — полиэтиленполиамина. Площадь опорной поверхности стеклоэлементов, омоноличиваемых с металлическими вставками, для сферических оболочек составляла 6.5 10~3 м2, для цилиндрических — 6,9 10” 3 м2. Поверхности для склейки предварительно обезжиривали ацетоном и обезвоживали спир том. Этой операции предшествовала тщ ательная промывка стеклоэле ментов в воде с применением кальцинированной соды. П олучение ка чественного соединения достигалось нанесением тонкого слоя клея на все омоноличиваемые поверхности. Отверждение клея происходило в течение 20—24 ч при температуре 291—298 К. Д л я получения не-
обходимых толщин склеивающих прослоек соединяемые элементы дополнительно прижимали друг к другу усилием 196 Н. После отверждения клеевые швы термообрабатывали при температуре 343 К в течении 8 ч.
Сборка конструкций состояла в обеспечении посадочных зазоров и герметичности внутреннего объема оболочек во время проведения испытаний. Неразборность достигалась применением четырех стяжек, равномерно распределенных по периметру оболочки в зоне узла сое динения. Герметичность оболочек создавали применением кольцевых резиновых уплотнителей в стыках и последующим заключением кон струкций в герметичные гибкие полиэтиленовые оболочки-кожухи.
Срок хранения конструкций (в комнатных условиях) после изго товления от двух дней до четырнадцати месяцев.
Опытные конструкции испытывали внешним давлением в масля ной среде при температуре 289—307 К на ранее описанных установках высокого давления. Программа испытаний конструкций включала изу чение действия однократного кратковременного гидростатического давления вплоть до разрушения (пять оболочек на тип соединения), повторно-статического нагружения 100 циклами систем с наиболее перспективными техническими решениями (пять оболочек на тип со единения) и длительного приложения нагрузки, изменяемой 100 ч ступенями: 10, 20, 29 МПа (по три оболочки с лучшими типами узлов соединений).
Наибольш ее давление в цикле нагружения конструкций с тем или другим узлом соединения выбиралось исходя из результатов установоч ного кратковременного испытания последних так, чтобы максималь ное давление в режиме повторно-статического нагружения составляло 0,5— 0,98 максимального давления при однократном нагружении. Оценку зарождения и развития повреждаемости узлов соединений оболочек проводили визуально в ходе испытаний после 1,5, 10 циклов,
азатем через каждые 30 циклов.
Постановка представленных в данном параграфе численных и ла бораторных экспериментов вызвана необходимостью обоснованного выбора граничных условий по поверхности разъема деталей, что в свою очередь позволяет изменять податливость подвижного соединения и концентрацию напряжений в хрупком элементе составной системы.
Первоначально изучали составные оболочки из стекла с разъемными механическими соединениями элементов в форме шарнирного узла качения. Конструктивная реализация таких соединений достигается путем вклейки торцовых зон стеклоэлементов в кольцевой паз метал лического кольца-обрамления, которое впоследствии шарнирно стыку
ется с подобным кольцом или с другими деталями в узле |
соединения. |
Т ак создается неразъемное клеевое соединение двух |
разнородных |
элементов, а разъем организуется между металлическими поверхно стями. Клеевой омоноличивающий шов между дном, внутренними бо ковыми стенками паза кольца-обрамления и опорной, боковыми поверх ностями торца стенки хрупкого элемента образует прочную, с хороши ми деформационными свойствами прослойку, выбирающую во время нагруж ения все несовершенства сопрягаемых поверхностей. Обладая
1 3 2 - 2 8 5 8 |
193 |
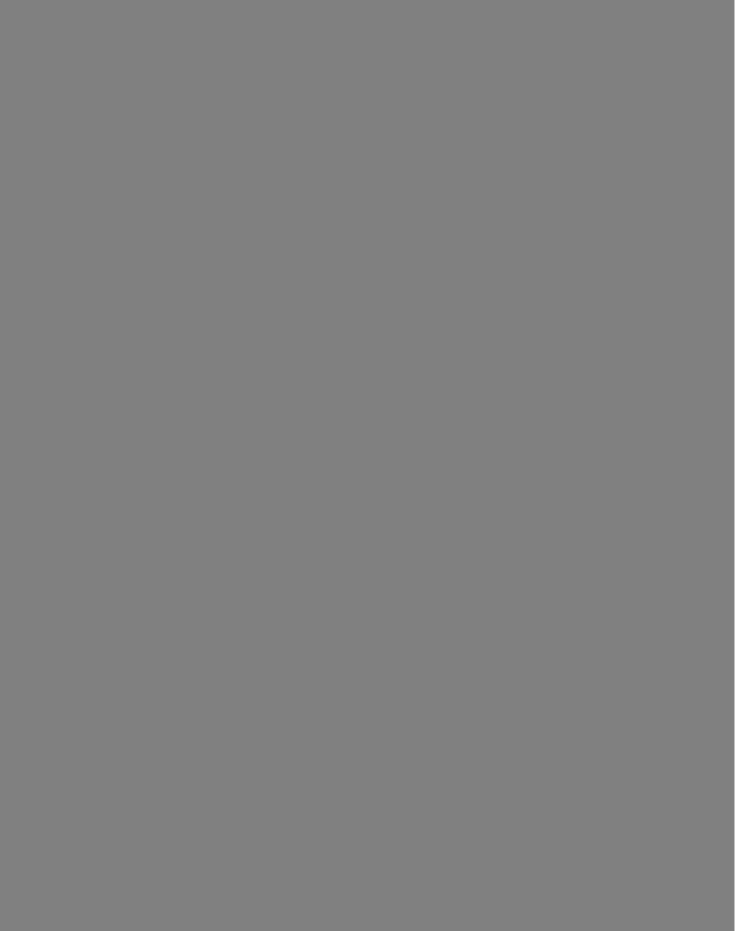
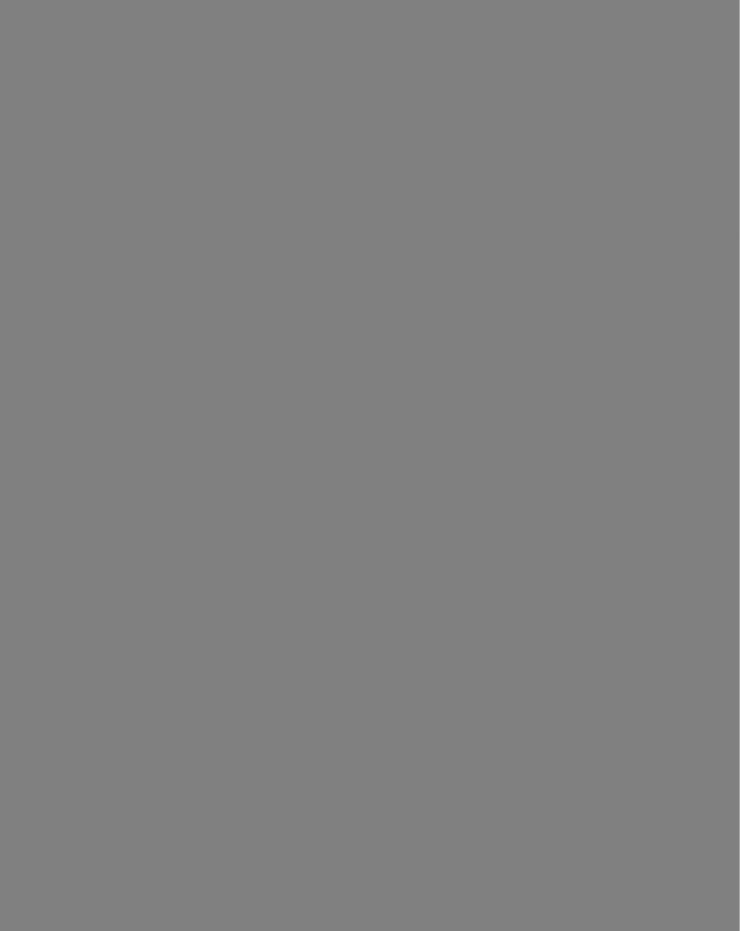
|
|
М атериал |
|
|
|
|
|
<с |
|
|
|
|
д |
|
|
|
|
д |
|
|
|
к |
O g |
3 |
|
|
я |
|
|
|
|
Ж |
|
ай |
|
|
V |
2 § |
|
Я |
Тип соеди нения |
4 |
0) |
|
|
о |
|||
|
2 |
i s |
||
* |
|
03 |
4 |
|
fp |
|
О. |
Я о |
|
о |
|
Н ® |
О |
|
4 |
|
О |
VO |
|
о |
|
О |
|
о |
о |
|
а |
а о |
о |
о |
|
Я |
||
|
|
л |
Е |
4 |
Ж |
|
4 |
о Я |
и |
|
о |
с я |
я |
|
|
|
я |
5* |
|
С ф ери |
|
|
|
|
ческая |
|
С таль |
|
5 |
|
|
|
||
|
|
40Х |
|
|
Та ж е |
— |
5 |
|
|
5 |
» » |
— |
5 |
X С т ал ь |
5 |
40Х
5
Ц и |
» » Та ж е |
5 |
|
а н и д - |
|||
риче- |
|
|
|
ская |
|
|
|
С фери |
|
|
5 |
ческая |
|
|
|
|
С тал ь |
С т а л ь |
о |
|
45 |
45 |
|
|
С тал ь |
С т ал ь |
5 |
|
4ОХ |
40Х |
|
П ар ам етр ы |
к р ат к о в р ем е н н ы х |
одн ократны х |
||||
|
|
|
и сп ы тан и и , М П а |
|
|
|
|
|
М а к си м ал ьн о е р а сч ет н о е н а п р я |
||||
Д а в л е |
ж ен и е в м ом ен т д е й с т в и я п р е |
|||||
д е л ь н о й |
н а г р у з к и |
или |
р а з р у |
|||
ние |
н а |
|
|
ш ени я |
|
|
г р у ж е |
|
|
|
|
|
|
ния |
или |
|
|
|
|
|
р а з р у |
|
|
|
в |
кольце- |
|
ш ения |
в с т е к л о э л е м е н т е |
|||||
|
|
сб р л м л е - |
||||
|
|
|
|
|
|
шш |
17— 22 |
72— 91. — 240 --------302 |
|
— 670 — |
|||
19 |
|
|
— 841 |
|||
|
81 |
’ |
— 271 |
|
||
|
|
|
— 753 |
|||
|
|
|
|
|
|
147 |
74; |
—942 |
П р ев ы ш ал о |
|
|
|
п р е д е л |
|
|
|
т е к у ч е |
|
|
|
сти с тал и |
|
|
тштщ |
|
|
|
|
“ |
147 |
44; |
— 1013 |
П р ев ы ш ало |
|
|
|
п р е д е л |
|
|
|
т е к у ч е |
|
|
|
сти стал и |
127— 148 |
38— |
44 |
— 7 3 --------1020 |
То ж е |
138 |
41 |
1 |
— 952 |
|
|
|
|
|
— |
47— 70 |
14— 21, |
- 5 1 2 --------771 |
|
56 |
17 |
' |
- 6 1 5 |
—■ |
- |
|
- |
27— 60 |
7,8— 18. |
—304 ------- 657 |
|
49 |
15.7 |
' |
—539 |
88— 92 |
37— 101 |
—768 ------- 802 |
|
90 |
39 |
’ |
—784 |
|
—460 —
—687 __
—594
—
-2 8 0 -
—6 1 0 __
—498
Пр е в ы ш а
л о |
пр£* |
д е л |
т е ’ |
к у ч ести с тал и
|
П а р ам е тр ы |
п овто р н о -стати ч ески х испы таний |
|
------------------------------- -— |
|
|
к |
|
|||
|
|
|
|
|
|
п |
£ |
Р асчетн ое н ап ряж ен и е в ц и кл е или при |
5 |
|
|
я |
Я |
разруш ении , М П а |
* |
|
|
о |
|
||||
х |
ч |
|
|
и |
|
R |
о |
|
|
|
|
§ |
|
|
2 |
|
|
а |
|
|
|
|
|
U |
<и |
|
|
а |
Примечания |
со |
а» |
|
|
||
Я са |
НГ |
|
|
о |
|
« с |
|
в кольце- |
К |
|
|
2 |
в стекло эл ем ен те |
* |
|
||
я -5 |
СО |
обрамленин |
S |
|
|
а> . |
s |
|
я |
|
|
= ® |
схга |
|
|
о |
|
s g |
|
|
5 . |
||
п С |
|
|
|||
|
a S |
|
|
я |
н |
|
|
|
t r |
a |
0— 147— 0 |
17—22 |
8,3— 10,8 |
. |
— 107— 212 |
— 167------- |
216 |
i |
||
|
19 |
9,6 |
|
1 |
— 123 |
— 192 |
|
|
|
0— 98— 0 |
12— 27 |
5,9— 13,7 . |
|
—7 6 ------- |
176 |
— 118 ------- |
275 |
1— 2 |
|
|
19 |
9.7 |
' |
|
— 125 |
— 194 |
|
|
|
0— 147— 0 |
9— 23 |
2,9— 6,9. |
— 6 1 ------- |
159 |
—9 1 ------- |
237 |
1 |
||
|
15 |
4,9 |
' |
|
- 1 0 6 |
|
- 1 5 9 |
|
|
О— 98— 0 |
14—26 |
3,0— |
6,9. |
— 9 8 ------- 177 |
— 146------- 263 |
1 |
|
20 |
5,9 |
1 |
- 1 3 7 |
—206 |
|
Локальн ое разруш ение оболочек в виде сквозного отверстия
Разруш ение |
оболочек |
в процессе |
р а згр у з |
ки
То ж е
*
Разруш ение |
оболочек |
в процессе |
р а зг р у з |
ки |
|
— |
|
— |
— |
|
- |
- |
— |
- |
|
|
|
|
|
||||
0—39 |
— 0 |
14— 19 |
3,9— 5,9 |
— 157------- 20G |
— 139------- 182 |
i— 2 |
- |
|
— 157 |
|
|
||||||
|
|
16 |
4 |
.9 ' |
- 1 7 7 |
|
|
|
|
|
|
|
|
||||
— |
|
|
|
’ |
|
|
|
|
——
о
ч
а
>о
о
fct
Я
0
С ф ери ческая
Ц и лин - дриче ская
С ф ери ческая
М атери ал
|
|
я |
|
|
|
л |
н |
|
|
§§ |
|
|
X |
a |
|
|
|
я |
|
|
о» |
25 |
|
Тип соединения |
ч |
0> |
|
2 |
§ о |
ЕГ |
|
|
О |
||
|
со |
гр (-• |
ч |
|
а |
|
|
|
«о |
£ 1 |
о |
|
о |
о |
|
|
|
S о |
о |
|
|
Я В |
о |
|
ч |
S ° |
ч |
|
о я |
о |
|
|
о |
£§ |
я |
|
* |
ЙР |
|
|
С т а л ь .С т а л ь |
|
|
|
40Х |
| 40Х |
|
П ар ам етр ы |
к р атк о вр ем ен н ы х |
о д н о к р атн ы х |
|
|
и спы тани й, |
М П а |
|
|
М ак си м ал ьн о е |
р а сч етн о е н а п р я |
|
Д а в л е |
ж ен и е в м омент д е й с т в и я п р е |
||
д е л ь н о й н а гр у зк и и л и р а з р у |
|||
ни е н а |
ш ени я |
|
|
г р у ж е |
|
|
|
ния или |
|
|
|
р а з р у |
|
|
п к о л ь ц е - |
ш ени я |
в с т е к л о э л е м е н т е |
||
|
о б р а м л е - |
||
|
|
|
нии |
— |
— |
— |
— |
_
Та ж е Та ж е |
125— 129 |
— 9 7 2 ------- ЮОЗ |
То ж е |
|
127 |
— 987 |
|
С тал ь |
С тал ь |
104 -113 |
—9 1 5 ------- 993 |
То же |
45 X |
45 X |
108 |
||
|
|
- 9 5 3 |
|
С тал ь |
Та ж е |
3 7 - 4 9 |
88— |
108. |
—4 3 1 ------- 628 |
- 6 2 3 - |
40 X |
|
|||||
|
|
42 |
93 |
’ |
- 5 4 9 |
------- 811 |
|
|
|
|
|
|
— 706 |
Та ж е |
43—54 |
- П 8 7 ------- 1491 |
- 6 9 5 — |
|
|||
|
48 |
— 1334 |
------- 869 |
|
|
|
— 778 |
П р и м е ч а н и е . Под чертой указано ср ед н ее значение.
|
П а р а м е т р ы |
п о в то р н о -ст а ти ч ес к и х испы таний |
||
в |
аГ |
Р а сч етн о е |
н ап ряж ен и е в |
ц и кл е или при |
|
X |
|||
и |
|
разруш ении , |
М П а |
|
4> |
|
|||
зк |
m |
|
|
|
р у |
та |
|
|
|
с* |
|
|
|
|
а г |
а» |
|
|
|
н а |
о |
|
|
|
3 |
|
|
|
|
и е М П |
|
|
в к о л ьц е - |
|
2 |
|
|
||
та |
в стек л о эл ем ен те |
обрам лении |
||
ен , |
э * |
|
|
|
ен ле |
. s i |
|
|
|
змИ ицк |
|
|
|
|
|
" С |
|
|
|
0—39— 0 |
— |
43; |
—341 |
- 6 5 5 |
0—49— 0 |
|
54; |
—426 |
—818 |
0—49— 0 |
35— 46 |
39— 51. |
—3 0 7 ------- 401 |
—5 9 0 ------- 770 |
|
41 |
45 1 |
—354 |
- 6 8 0 |
1—39 — 1 |
— |
- |
—306 |
|
- 6 3 6 |
|
1______ 1 |
|
|
— 459 |
В |
локальн ом |
|
|
|
|
|
об ъ ем е |
п р е |
|
|
|
|
|
вы ш ало |
п р е |
|
|
|
|
|
д е л |
текучести |
|
|
|
|
|
|
стали |
- |
- |
— |
— |
— |
|
|
о?
К
35
£
О.
U
Я
Примечания
а |
|
|
|
|
о |
|
|
|
|
«ч |
|
|
|
|
о F- |
|
|
|
|
а |
|
|
|
|
10J |
Все |
оболочки |
получи |
|
|
ли |
сущ ественны е по |
||
|
вреж дения |
стекло- |
||
|
элементов |
|
||
100 |
|
То |
ж е |
|
2—19 |
Разруш ение стеклоэле- |
|||
|
мента в |
зоне соеди |
||
|
нения и потеря не |
|||
|
сущ ей |
способности |
||
|
оболочки |
|
|
100 |
Н агруж ен и е |
оболочек |
||
|
повторно-статистиче |
|||
|
ским |
давлением |
по |
|
|
блочной схеме |
че |
||
|
рез |
14 месяцев |
|
|
100 |
Д в е оболочки |
п олучи |
||
|
ли |
незначительны е |
повреж дени я стекло - элементов
- |
- |
— |
— |
- |
|
|
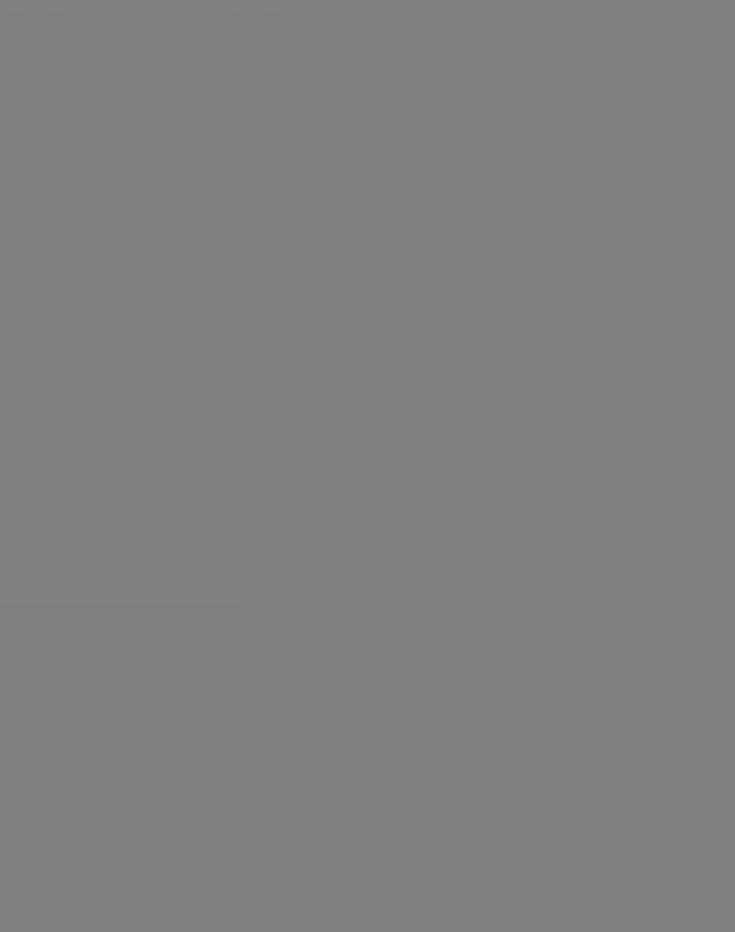