
книги / Сварка плавлением
..pdfОсновные типы сварных швов и конструктивные элементы подготовки кромок под автоматическую и полуавтоматическую сварку под флюсом установлены ГОСТ 8713–70.
Двусторонние стыковые швы без скоса кромок применяются для металла со свариваемой толщиной от 2 до 20 мм. Основным условием получения качественного шва при сварке с одной стороны является точная сборка, чтобы зазор в стыке для толщин более 4 мм не превышал 1 мм, а для более малых толщин был бы еще меньше. Если указанное условие не соблюдается, то сварку следует выполнять на технологических подкладках.
Односторонние стыковые швы без разделки кромок допустимо выполнять на металле толщиной до 12 мм.
V-образная разделка рекомендуется для толщин 8–30 мм, U-образная 16–50 мм и выше, K- и Х-образные > 20 мм.
Притупление в стыках под автоматическую сварку должно быть больше (часто 6–10 мм), чем при ручной дуговой сварке, что связано с более глубоким проплавлением.
Некоторые виды разделок предназначены для автоматической сварки по предварительной ручной подварке корня шва с одной или двух сторон. Ручная подварка должна быть определенной величины, иначе она не сможет предотвратить прожог. В связи с этим под ручную подварку иногда требуется разделка кромок, особенно при односторонней сварке неповоротных стыков.
Флюсовая подушка при односторонней сварке нужна не только для удержания металла от вытекания, но и для формирования обратной стороны шва, поэтому подушки для односторонней сварки обычноимеютпневматическийприжимфлюсаккромкам.
Подготовка кромок угловых, тавровых и нахлесточных соединений не имеет специфических особенностей.
Основными параметрами режима являются сварочный ток, напряжение дуги, скорость сварки, диаметр электрода, скорость подачи проволоки и вылет электрода. Влияние параметров режима на форму и размеры швов при сварке под флюсом в основном такое же, как и при ручной дуговой сварке.
31
Можно отметить следующие особенности:
1.Применение токов большой величины заметно влияет на величину вылета электродной проволоки. Это необходимо принимать во внимание при регулировании длины дуги и напряжения на дуге.
2.На размеры и форму шва влияют марка и структура флюса. С повышением стабилизирующих свойств флюса увеличиваются длина дуги и напряжение дуги, вследствие чего возрастает ширина шва. Структура, грануляция и насыпной вес флюса влияют на его газопроницаемость, объем флюсового пузыря
идавление газов в пузыре. Например, чем больше насыпной вес флюса, тем меньше объем газовой полости, что приводит к уменьшению блуждания дуги, возрастанию давления газов и более интенсивному вытеснению жидкого металла из-под дуги. В результате ширина шва уменьшается, а глубина провара увеличивается.
3.В автоматах с постоянной подачей электродной проволоки этот параметр (величина подачи) определяет величину сварочного тока и поэтому является одним из основных.
Влияние параметров режима сварки под флюсом на химический состав металла шва качественно такое же, как и при ручной электродуговой сварке. Здесь можно выделить следующие особенности:
1.Доля основного металла в металле шва значительно больше, чем при ручной электродуговой сварке (РДС), поэтому химический состав основного металла больше влияет на состав шва, чем при РДС.
2.Сварочная ванна под флюсом имеет больший объем и существует дольше, чем при РДС, поэтому реакции взаимодействия жидкого металла со шлаком протекают более полно и состав флюса оказывает большее влияние на состав металла шва.
3.При сварке под керамическими флюсами изменение параметров режима (особенно напряжения дуги) влечет за собой значительное изменение химического состава металла шва.
32
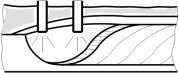
Многоэлектродная и многодуговая сварка под флюсом
В большинстве случаев сварку под флюсом выполняют одним электродом. Однако для повышения производительности процесса и качества сварных соединений применяют сварку двумя и более электродами многоэлектродную и многодуговую. При этом сварка может выполняться по двум схемам:
1)в общую ванну, когда расплавляемый всеми дугами металл образует единую ванну;
2)в раздельные ванны (раздвинутыми дугами), когда последующая дуга расплавляет уже закристаллизовавшуюся часть шва, полученную предыдущей дугой.
Сварка в общую ванну. Сварка производится сдвоенным (рис. 2) или расщепленным электродом на специальных много-
электродных автоматах: А 609, А 330, ДТС39. К этому методу прибегают главным образом для регулирования формы и размеров швов.
При электродуговой сварке (ЭДС) можно в довольно широких пределах регулировать ширину шва и глубину провара, не изменяя режима сварки, за счет различных траекторий перемещения конца электрода. Автоматическая сварка также может выполняться
с колебаниями электрода поперек шва. При этом чем больше амплитуда колебаний, тем шире шов и меньше глубина провара. Но сварка в общую ванну является более эффективным способом регулирования.
Сварка может выполняться при параллельном или последовательном расположении электродов (рис. 3).
33

а |
|
б |
|
|
|
Рис. 3. Расположение электродов: а параллельное; б последовательное
Параллельное расположение электродов. Этот способ по-
зволяет изменять форму шва в широких пределах при неизменных значениях сварочного тока и напряжения дуги (цифры на рисунке расстояние между электродами).
Чем больше расстояние между проволоками (электродами), тем шире шов и меньше глубина провара (рис. 4). Для проволоки диаметром 3 мм при оптимальном расстоянии 8–12 мм шов получается широким с минимальной высотой. Дальнейшее увеличение расстояния между электродами приводит к образованию «седловин». При увеличении диаметра электрода и сварочного тока оптимальное расстояние может быть несколько бóльшим. Этот способ находит наибольшее применение при сварке легированного слоя двухслойных сталей и при наплавке.
Рис. 4. Влияние расстояния между проволоками на ширину шва и глубину провара
Последовательное расположение. Такое расположение по-
зволяет увеличить количество наплавляемого в единицу времени электродного металла при неизменной или уменьшенной глубине
34

провара. Метод целесообразно применять тогда, когда увеличение сварочного тока при однодуговой сварке невозможно из-за опасности прожога. Например, при сварке по зазору при двухсторонней сварке для уменьшения высоты наплавленного металла первого слоя, при многослойном заполнении швов и т.д.
Сварка в раздельные ванны, или сварка раздвинутыми ду-
гами. Этот способ может быть двух- и многодуговым (рис. 5).
Рис. 5. Сварка в раздельные ванны
По сравнению с многоэлектродной сваркой в общую ванну она обладает бóльшими технологическими возможностями, так как параметры режима на каждом электроде могут регулироваться самостоятельно, причемпервыйэлектродможетбытьрасщепленным.
Сварка последующей дугой должна вестись по жидкому шлаку, в противном случае процесс становится неустойчивым и возможны зашлаковки. Исходя из этого минимальное расстояние между дугами определяется длиной сварочной ванны, а максимальное расстояние длинойслояжидкого шлакаотпредыдущейдуги.
Этот способ сварки (раздвинутыми дугами) обладает двумя основными преимуществами: повышает производительность сварки и улучшает качество сварных соединений. Производительность сварки повышается за счет большей суммарной мощности дуг и увеличения количества наплавляемого металла.
Качество сварных соединений повышается за счет следующих факторов:
снижения скорости охлаждения металла шва и зоны термического влияния и, следовательно, повышения пластичности металла, склонного к закалке;
35
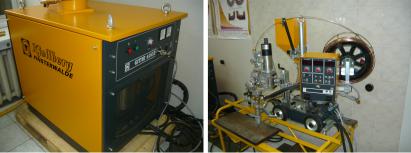
повышения стойкости металла шва против горячих трещин, так как предшествующая дуга создает предварительный подогрев, а последующая почти полностью переплавляет предыдущий слой и устраняет трещины, которые могли в нем возникнуть.
Сварка раздвинутыми дугами применяется для выполнения многослойных швов и при сварке закаливающихся сталей.
Цель работы – освоить принцип работы автомата для сварки под флюсом и технологию выполнения сварочного процесса.
Оборудование, материалы, инструмент:
1)автомат для сварки под флюсом;
2)пластина из низкоуглеродистой стали;
3)сварочная проволока Св-08А;
4)штангенциркуль.
Задания для лабораторной работы:
1. Изучить устройство и принцип работы автомата для сварки под флюсом. Сварка под флюсом проводится на автомате фирмы Kjellberg (рис. 6).
а |
б |
Рис. 6. Автомат фирмы Kjellberg: а – внешний вид автомата для сварки под флюсом; б – внешний вид источника питания автомата для сварки под флюсом
36
2.Зачистить пластины.
3.Подготовить автомат к работе.
4.Записать в отчет исходные данные и параметры режима
сварки. Сварочные материалы: dэ = 4 мм, флюс АН-348А, толщина металла 16 мм, сварочный ток 400–500 А, напряжение дуги 34–40 В, скорость сварки 35–45 м/ч.
5.Провести наплавку под флюсом, изменяя режимы сварки.
6.Установить влияние силы сварочного тока на форму и размеры валиков, коэффициент наплавки и производительность.
7.Установить влияние напряжения дуги на форму и размеры валика, коэффициент наплавки, расход флюса и производительность.
8.Установить влияние скорости перемещения дуги на форму и размерывалика, коэффициентнаплавкиипроизводительность.
9.Оценить визуально характер влияния изменения режимов сварки на форму и размеры сварного шва.
10.Составить отчет по результатам работы.
Лабораторная работа № 3 Расчет проплавляющей способности дуги
сучетом технологических особенностей сварки углеродистых и низколегированных сталей автоматической аргонодуговой сваркой
(сварочный робот Fanuc) по заданным режимам
Краткие теоретические сведения
Для сварки в защитных газах применяют три группы газов: инертные (аргон, гелий); активные (углекислый газ, азот, водород и др.); смеси газов инертных, активных или первой и второй групп. Выбор защитного газа определяется химическим составом свариваемого металла, требованиями, предъявляемыми к свойствам сварного соединения; экономичностью процесса и другими факторами.
37
Смесь аргона с 10–25 % углекислого газа применяют при сварке плавящимся электродом. Добавка углекислого газа при сварке углеродистых сталей позволяет избежать образование пор, несколько повышает стабильность дуги и надежность защиты зоны сварки при наличии сквозняков, улучшает формирование шва при сварке тонколистового металла.
Преимущества сварки в аргоне:
1.Можно сваривать на малых токах (например, на 10 А), что очень помогает при работе с тонкими металлами и работах, где требуется высокая точность и аккуратность.
2.Процесс сварки в среде аргона происходит без флюса и электродных обмазок, что уменьшает количество отходов и грязи
впомещении.
3.Возможность получать самые эстетичные и высокопрочные швы при выполнении сварки только с одной стороны.
4.Абсолютная изоляция от воздуха и окружающей среды, что в несколько раз повышает качество сварных соединений.
5.Малая область нагрева основного металла (швы получаются очень узкими и аккуратными), что предотвращает изменение формы свариваемой детали.
6.Аргонодуговая сварка позволяет соединять разнородные металлы.
7.С помощью больших мощностей можно очень быстро резать металл, при этом края изделий получатся сравнительно ровными и на них будут отсутствовать окислы и оксидные пленки.
8.Различные отходы и примеси в процессе дуговой сварки тут же выдуваются струей аргона из зоны сварки.
9.Можно выполнять наплавку для того, чтобы, например, восстановить изношенную часть изделия, при этом делать это очень удобно.
10.Сваривать аргоном можно детали самых различных габаритов – от маленьких деталей до очень больших металлоконструкций.
11.Выделение различных вредных газов и аэрозолей мини-
мально.
38
12. Сварка в аргоне – это относительно безопасный вид дуговой сварки. Отсутствие брызг металла и искр способствует использованию такого вида сварки в бытовых условиях без опасности повредить имущество.
Недостатки сварки в аргоне:
1.Сложное и дорогое оборудование.
2.Требуется высокая квалификация сварщика. Обусловлено это тем, что применяемое оборудование весьма сложно и его точная настройка требует определенных знаний и навыков.
3.Если производить сварку на высоких токах (свыше 180 А), то появляется необходимость в водяном охлаждении, а это дополнительноегромоздкоеоборудование.
4.При работе на открытом воздухе или в помещениях, где присутствует движение воздуха, аргон не сможет обеспечить надежной и эффективной защиты швов, так как он будет сдуваться и, как следствие, не будет выполнять своих функций.
5.В процессе сварки наблюдается очень сильное ультрафиолетовое излучение, особенно если в качестве защитного газа используется гелий.
Свариваемые кромки и прилегающие к ним поверхности перед сваркой зачищают от окалины и загрязнений и обезжиривают. Ввиду ограниченных возможностей металлургической обработки при сварке в защитных газах зачистка и обезжиривание должны проводиться более тщательно, чем при других способах сварки. Способ очистки выбирают в зависимости от марки свариваемого металла и производственных условий.
Сборку узлов под сварку обычно выполняют в специальных приспособлениях без предварительной прихватки. При отсутствии приспособлений сборку ведут на прихватках небольшой длины с расстоянием между прихватками 15–50 мм в зависимости от свариваемой толщины.
При аргонодуговой сварке в зону дуги подается защитный газ, струя которого, обтекая электрическую дугу и сварочную ванну, предохраняет расплавленный металл от воздействия атмосферного воздуха, окисления и азотирования.
39
Аргон – одноатомный инертныйгаз безцвета и запаха, тяжелее воздуха. Получают аргон из воздуха. Аргон поставляется двух сортов: высшего и первого. Высший сорт содержит 99,992 % аргона, не более 0,006 % азота и не более 0,0007 % кислорода. Первый сорт содержит 99,987 % аргона, азота – до 0,01 % и кислорода – не более 0,002 %. Аргон поставляется в газообразном виде в баллонах типа А под давлением 15 MПa. Баллоны окрашены в серый цвет с зеленой полосойизеленойнадписью «Аргончистый».
Аргон применяют при сварке ответственных сварных швов и при сварке высоколегированных сталей, титана, алюминия, магния и их сплавов.
Особенности сварки углеродистых и низколегированных сталей
Для этих сталей технологию сварки выбирают из условий обеспечения комплекса требований, главные из которых – достижение равнопрочности сварного соединения с основным металлом и отсутствие дефектов в сварном соединении. Дляэтого механические свойства металла шва, околошовной зоны и сварного соединения в целом должны быть не ниже минимальных механических свойств основного металла. В ряде случаев с учетом конкретных условий работы конструкции допускается снижение требований к отдельным показателям механических свойств сварного соединения по сравнениюстребованиями, предъявляемымикосновному металлу.
В металле швов не должно быть трещин, непроваров, пор, подрезов и других дефектов, они должны иметь требуемые по чертежу размеры и форму. Сварное соединение должно быть стойким к переходу в хрупкое состояние. В некоторых случаях дополнительно вводят требования высокой коррозионной стойкости сварных соединений, их работоспособности в условиях вибрационных и ударных нагрузок, повышенных или пониженных температур и другие специальные требования
Механические свойства металла шва и сварного соединения зависят от его структуры, определяемой химическим составом,
40