
книги / Резание материалов
..pdf
Сегодня мы можем объяснить наличие клина на режущих инструментах с физической точки зрения. Например, при колке дров применяют режущий инструмент – топор или колун, имеющий форму клина в поперечном сечении (рис. 2).
Рис. 2. Общий вид расколки дров (а) и схема разложения силы удара Р топором на составляющие силы Рн и Рг при внедрении наклонных поверхностей клина в дерево (б)
Входе колки мы можем проследить последовательно несколько стадий процесса разрушения. Сначала режущая кромка топора упруго деформирует деревянный материал. Происходит упругая деформация. Затем наступает пластическая деформация материала со следами врезания топора, а затем под действием клина происходит разрыв межмолекулярных связей обрабатываемого материала. Образуется трещина, и чурка раскалывается на два полена. Наличие наклонных поверхностей клина на топоре и создает силу разрыва межмолекулярных связей и разрушение материала. Эти явления мы можем наблюдать и при резке других материалов
вбытовых условиях с помощью ножа или ножниц и, конечно, при обработке заготовок деталей машин на металлорежущих станках. Здесь с обрабатываемой поверхности заготовки последовательно срезаются тонкие слои материала, называемые стружкой, с целью получения детали необходимой формы и размеров (рис. 3).
Впроцессе механической обработки деталей помимо видоизменения формы и размеров заготовки происходит формирование особых свойств поверхностного слоя, его макро- и микро-
11
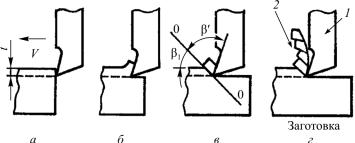
структуры, что непосредственным образом влияет на усталостную прочность, долговечность деталей и, в конечном счете, на надежность и ресурс работы изготавливаемого изделия. Окончательное формирование основных параметров качества поверхностного слоя и усталостной прочности деталей машин происходит на чистовых финишных операциях механической обработки, которые будут рассмотрены далее в данном учебном пособии.
Рис. 3. Схема последовательного врезания клина резца 1 в заготовку с образованием срезаемого слоя – стружки 2
Наука о резании материалов – относительно молодая наука. Первые теоретические работы в этой области знаний появились в конце XIX века в России. Ранее в различных странах Европы и США проводились лишь отдельные чисто экспериментальные работы без объяснения физического смысла процесса резания. Основоположником научного направления в резании материалов является русский профессор Санкт-Петербургского горного института Иван Августович Тиме (1838–1920). В 1870 году он опубликовал монографию «Сопротивление металла и дерева резанию». В ней он впервые показал, что без детального изучения физических основ резания невозможно организовать рациональную и научно обоснованную механическую обработку. Он впервые исследовал характер деформации срезаемого слоя, установил классификацию типов стружек, разработал методы измерения сил резания и предложил формулы для их вычисления. Результаты аналогичных исследований были опубликованыв Англии только спустя55 лет.
12

Иван Августович Тиме
Исследования И.А. Тиме продолжил профессор Харьковского технологического института К.А. Зворыкин (1861–1928). Он в 1893 году опубликовал книгу «Работа и усилие, необходимое для отделения металлических стружек при резании», где представил разработанные конструкции динамометра для определения сил резания, а также вывел формулу для их расчета с учетом сил трения на передней и задней поверхностях инструмента. Необходимо отметить, что лишь спустя 50 лет аналогичную теорию опубликовал профессор из США М.Е. Мерчант, «забыв» сослаться на труды К.А. Зворыкина.
В 1896 году вышла книга профессора Михайловской артиллерийской академии А.А. Брикса (1865–1900) «Резание металлов», в которой анализируются предшествующие исследования стружкообразования, делается попытка обобщить их и систематизировать идеи предшественников. А.А. Брикс ввел более точные формулировки понятий и явлений процесса резания, терминологии режущего инструмента.
Профессор Я.Г. Усачев (1873–1941) в 1912–1915 годах в книге «Явления, происходящие при резании металлов» представил результаты выдающихся исследований в области резания, опере-
13
дившие аналогичные результаты ученых из Германии и США на 30–50 лет. Впервые для изучения процесса стружкообразования Я.Г. Усачев применил металлографический метод вместо ранее применявшегося визуального метода. Это позволило разработать весьма достоверную теорию наростообразования. Особенно ценными являются работы в области теплообразования. Новый калометрический метод и использование искусственных термопар позволили экспериментально установить влияние режимов резания на величину температуры резания. Впервые появилась возможность управления процессом стружкообразования, силами резания, шероховатостью поверхности деталей машин. Эти результаты сегодня подтверждаются с помощью компьютерного моделирования тепловых процессов различными учеными у нас
встране и за рубежом.
Вэтот же период проводились многочисленные стойкостные эксперименты под руководством американского исследователя Ф.У. Тейлора. В 1906 году вышла его книга «Искусство обработки металлов», представляющая собой статистический набор данных по стойкости режущих инструментов для различных обрабатываемых материалов. В книге отрицалось теоретическое изучение процесса резания, а пропагандировалось лишь искусство мастера, создание банка данных, справочников и каталогов без объяснения физической природы явлений при резании. Сегодня это опытно-статистическое направление широко распространено за рубежом. Технологу выдается каталог с режимами резания, а дальше он должен заниматься доводкой режимов самостоятельно. Если возникают проблемы, то технологу нужно обращаться за отдельную плату на фирму, производящую станок или инструмент и выпускающую соответствующие каталоги. Несмотря на относительное удобство пользования каталогами, они не могут учесть все многообразие условий обработки, не могут учесть появление десятков новых обрабатываемых и инструментальных материалов, выбрать наиболее оптимальные режимы резания. Этих недостатков тейлоровской теории были лишены разработки наших ученых. Усилиями И.А. Тиме, К.А. Зворыкина и Я.Г. Уса-
14
чева была создана отечественная школа резания материалов, намного обогнавшая зарубежные исследования в этой области.
Бурное развитие машиностроения в России в 20–30-х годах привело к созданию и открытию в России новых лабораторий резания на заводах, в отраслевых НИИ и в учебных заведениях. В 1936 году при техническом совете Наркомтяжпрома была создана комиссия по резанию металлов под председательством Е.П. Надеинской. Эта комиссия привлекла к научно-исследовательской работе лаборатории резания более 30 вузов, НИИ и заводов. За пять лет работы было выполнено более 300 исследований силовых и стойкостных зависимостей по единой методике. Это позволило значительно усовершенствовать существующие нормативы и почти на порядок увеличить производительность механообработки в годы Великой Отечественной войны.
Такого размаха исследовательской работы в области резания металлов не имела ни одна страна в мире. Накопленный фактический материал одновременно явился источником для дальнейших теоретических обобщений. В результате появился ряд работ большого научного значения. Основы современной науки резания материалов заложили ученые: И.И. Семенченко (металлорежущий инструмент); А.И. Каширин (вибрации при резании); Г.И. Грановский (кинематика резания); Т.Н. Лоладзе (износ инструмента); В.А. Кривоухов, А.И. Исаев (качество поверхностного слоя); Н.Н. Зорев, М.И. Клушин (механика процессов резания); А.М. Даниелян, А.Н. Резников, А.Д. Макаров, С.С. Силин (теплофизика резания); А.А. Маталин, А.М. Сулима, В.Ф. Безъязычный, А.Г. Суслов (влияние качества обработки на эксплуатационные свойства изделий) и др. Таким образом, трудами российских ученых создана современная передовая отечественная школа резания металлов, получившая мировое признание. Ее характеризует глубокое проникновение в суть физических явлений и использование установленных закономерностей на практике.
Сегодня исследования процесса резания продолжаются в связи с появлением новых обрабатываемых материалов и новых изделий, широким применением вычислительной техники, создани-
15
ем нового оборудования с ЧПУ, возможностью виртуального моделирования процесса резания, создания диагностических систем слежения за процессом резания, увеличением скоростей резания, применения новых конструкций режущих инструментов, инструментальных материалов с новыми видами покрытий, новых видов СОТС и т.д. Дальнейшее развитие фундаментальных основ науки о резании материалов связано с широким применением ЭВМ
имикропроцессорной техники и автоматизацией промышленного производства, созданием роботизированного безлюдного производства. Для разработки таких процессов, их наладки, контроля
иуправления требуются высокопрофессиональные специалисты, обладающие глубокими знаниями процессов резания.
Автор данного учебного пособия считает необходимым дать студентам технических вузов современные профессиональные знания о физической сущности и основных теоретических закономерностях и технических особенностях процесса обработки материалов резанием, чтобы затем успешно решать любые проблемы на производстве.
Эти знания необходимы будущему специалисту – технологу, мастеру, конструктору машиностроительного предприятия, для того чтобы технически грамотно назначить режимы резания, геометрию инструмента, смазывающе-охлаждающие технологические средства (СОТС) с целью обеспечения высокой производительности труда, выполнения требований по точности и качеству изготовления деталей, снижения затрат и себестоимости при выполнении различных технологических операций механической обработки.
Вучебном пособии представлен как классический теоретический материал, основанный на разработках основоположников теории резания материалов, так и теоретические и практические материалы современных ученых и материалы исследований автора учебного пособия.
К задачам изучения дисциплины «Резание материалов» относятся понимание и освоение основных закономерностей теории резания, физических явлений, происходящих в процессе резания –
16
кинематики, динамики, теплофизики процесса резания, изнашивания и стойкости режущих инструментов, формирования качества поверхностного слоя. В учебном пособии предоставлена возможность понять особенности влияния технологических условий обработки материалов на формирование качества поверхностного слоя и эксплуатационные характеристики обрабатываемых деталей машин; понять сущность оптимизации и управления процессом резания; научиться выбирать рациональные режимы резания и режущий инструмент; получить знания о современных методах проектирования и применения процессов резания, об эффективном использовании природных ресурсов, материалов и энергии, о разработке и использовании методических, справочных и нормативных материалов, технической документации.
Предметом изучения дисциплины являются следующие объекты: конструктивные элементы режущих инструментов, инструментальные материалы, кинематика и динамика процесса резания, стружкообразование и тепловые явления при резании, износ и стойкость режущих инструментов, моделирование и оптимизация процессов резания, назначение рациональных режимов резания, качество поверхностного слоя обрабатываемых деталей, современные направленияразвития теории и практики процессарезания.
Дисциплина «Резание материалов» относится к циклу специальных дисциплин и федеральному компоненту рабочего учебного плана. Она взаимосвязана с такими специальными дисциплинами, как «Проектирование металлорежущего инструмента», «Металлорежущие станки», «Технология машиностроения», «Проектирование приспособлений», «Автоматизация производственных процессов» и др.
В результате изучения дисциплины студент должен:
иметь представление о сущности процесса резания, о закономерностях и взаимосвязях физических явлений, происходящих в зоне резания;
знать общие закономерности превращения срезаемого слоя
встружку, физические основы износа и прочности режущего инструмента, сущность силового воздействия на процесс резания; те-
17
пловые явления на контактных поверхностях режущей части инструмента и заготовки; основы выбора оптимальных параметров режима резания и их влияние на производительность обработки, обрабатываемость материалов, качество обработанной поверхности, точность размеров обрабатываемой поверхности деталей;
уметь назначать рациональные режимы резания различными способами, выбирать инструментальные материалы и геометрию режущего инструмента, определять силу и мощность резания, пользоваться нормативными справочниками, стандартами
иинструкциями, выбирать СОТС для конкретных условий обработки резанием;
уметь выполнять необходимые измерения геометрии режущего инструмента, проводить контроль геометрии обработан-
ных деталей, измерения и расчеты силы резания, мощности
итемпературы резания;
владеть методами автоматизированного контроля и управления процессом резания;
иметь навыки анализа и устранения причин сбоев в технологическом процессе, организации и проведения необходимых мероприятий по отладке технологии изготовления и внедрению новых технологических процессов.
В учебном пособии в отличие от других изданий приведены результаты исследования автором механических свойств обрабатываемых материалов в широком температурном диапазоне с определением температурных зон провала пластичности, результаты исследования влияния адгезионных явлений при резании на формирование физико-химических свойств поверхностного слоя деталей, приведены результаты исследования износа инструмента и процесса стружкообразования с привлечением электронной микроскопии, микрорентгеноспектрального химического анализа, скоростной киносъемки и т.д. Показана возможность применения статистических методов обработки результатов исследований, применения математического планирования экспериментов, использования методов математического моделирования процессов резания с использованием ПЭВМ.
18
Особенностью данного учебного пособия является и то, что
внем приведены основные результаты теоретических и экспериментальных исследований процесса резания, выполненные под руководством автора в ОАО «Пермский моторный завод» за последние 35 лет при производстве деталей и узлов современных авиационных газотурбинных двигателей. Автор выражает искреннюю признательность руководству завода, инженерам и сотрудникам лабораторий резания и шлифования экспе- риментально-технологического цеха за помощь в организации, постановке экспериментов и внедрении полученных результатов
впроизводство.
19
Глава 1 КИНЕМАТИКА ПРОЦЕССА РЕЗАНИЯ
1.1. Основы кинематики резания
Кинематика процесса резания – это закономерности относительного движения инструмента и заготовки без учета физических явлений, протекающих в зоне резания, но с учетом геометрических параметров режущих инструментов в одной из трех систем координат. При этом кинематическая станочная система считается абсолютно жесткой и независимой от каких-либо физико-химических воздействий. Изучение и анализ кинематики резания имеет важное значение, поскольку при определенном соотношении скоростей абсолютных движений, которые совершаются при резании, кинематика определяет траекторию рабочего движения инструмента и детали. Траектория рабочего движения, геометрические параметры инструментов и скорости абсолютно влияют на силы сопротивления резанию, процесс стружкообразования, теплообразование, характер изнашивания и период стойкости инструмента. Кроме того, совокупность траекторий точек режущей кромки инструмента в процессе резания представляет собой поверхность, возникающую в процессе обработки, т.е. кинематическую форму поверхности резания и, как следствие, качество и геометрию обработанной поверхности.
1.1.1. Виды движений при резании материалов
Кинематика резания (в отличие от кинематики станков) рассматривает движения, необходимые для срезания стружки с заготовки, т.е. только главные движения в момент резания от начала контакта лезвия инструмента до прекращения этого контакта. Для того чтобы инструмент мог удалить с детали припуск, оставленный на обработку, инструменту и детали сообщают движения с определенными направлениями и скоростями. Одно из главных движений, сообщаемых инструменту или детали, называют движением резания, а другое – движением подачи.
20