
книги / Редукторы. Атлас конструкций
.pdf3. КОНСТРУКЦИИ ЗУБЧАТЫХ И ЧЕРВЯЧНЫХ КОЛЕС
Конструкции зубчатых и червячных колес зависят от размеров колес, объемов производства и технологических возможностей завода-изготовителя. В учебном проекте проектант вправе выбрать любое производство: единичное, мелко-, крупносерийное или массовое, если это не задано в техническом задании, то же самое относится и к технологическим возможностям изготовления зубчатых колес.
В современных редукторах шестерни делают за одно целое с валами, в этом случае деталь называют валом-шестерней, и только при значительных отличиях по диаметру её выполняют насадной как и колесо. В единичном и мелкосерийном производстве заготовки для зубчатых колес небольших диаметров получают отрезкой из прутков, а при больших – свободной ковкой, с последующей механической обработкой на станках (рис. 3.1, а). При крупносерийном и массовом производстве заготовки получают штамповкой.
В штампованных заготовках (рис. 3.1, б), в отличие от кованых, ступицы и ободы делают с уклоном ≈1:8, что соответствует углу γ=7°; в литых колесах диаметром da ≤ 800 мм уклон делают таким же (см. рис. 3.1, б), большего диаметра (da > 800 мм) с симметрично расположенным диском уклон делают меньшим – 1:20 (рис. 3.1, г). Уклоны необходимы для свободного извлечения колеса-заготовки из штампа и литьевой модели из формы.
Сопряжение диска с ободом и ступицей в штампованных заготовках делается по радиусу, который должен быть не менее 5 мм, с увеличением радиуса закругления улучшаются условия пластической деформации металла, поверхность диска и часть обода при этом не обрабатываются.
Диск между ободом и ступицей колеса следует размещать посредине зубчатого венца, так как при этом уменьшается коробление колеса при термообработке, это же относится и к коническим колесам.
Несимметричное расположение диска делается при ковке заготовок в подкладных штампах, применяемых при серийном производстве (число заготовок в год более 50 штук), когда формообразуется только одна часть колеса, а вторая делается сплошной гладкой; технология ковки облегчается, если диск смещен к одному из торцов колёс, колесо имеет вид, подобный изображению на рис. 3.1, в, только без спиц, которые делаются только в литых колёсах.
31
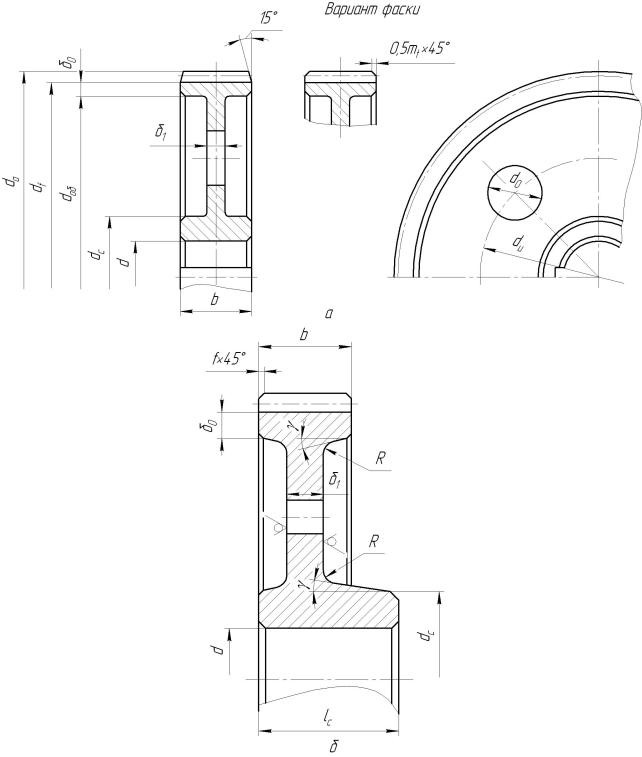
32
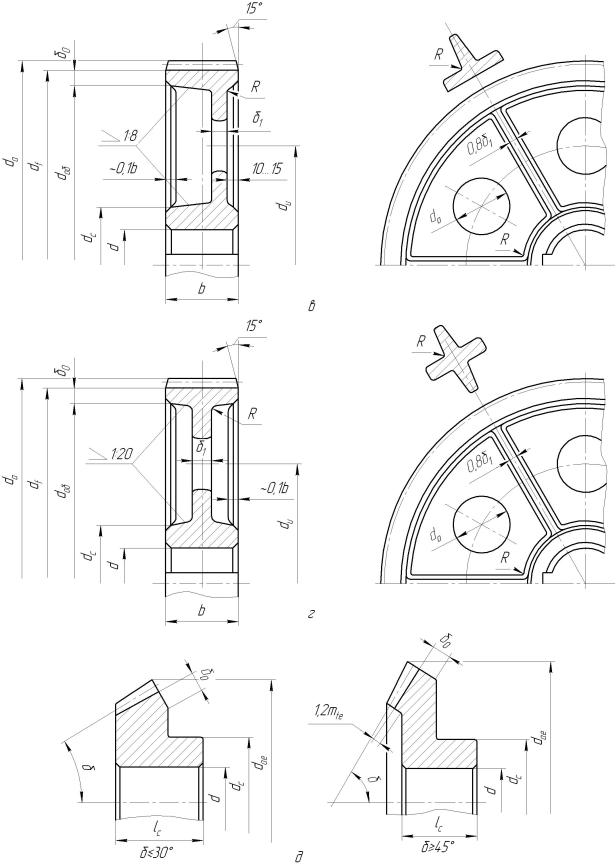
33
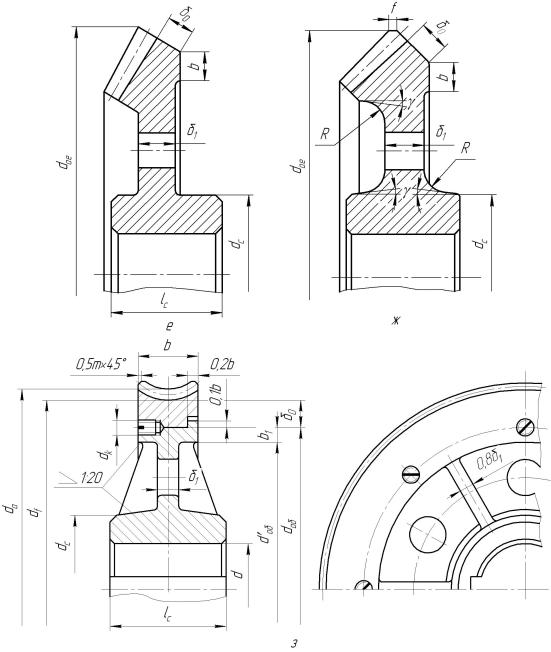
Рис. 3.1. Конструкции зубчатых цилиндрических, конических и червячных колес (табл. 3.1):
а– кованое с длиной ступицы, равной ширине зубчатого венца (da < 400 ... 600 мм);
б– штампованное с длиной ступицы, большей ширины зубчатого венца; в – литое
однодисковое несимметричное (dа1 < 800 мм, b < 150 мм); г – литое однодисковое симметричное (dа = 800 ... 2000 мм, b < 250 мм); д – коническое (daе_< 120 мм);
е– коническое кованое (daе > 120 мм): ж – коническое штампованное (daе > 120 мм);
з– червячное
Длину ступицы колеса желательно выполнять равной ширине зубчатого венца, в этом случае упрощаются базирование и установка колеса-заготовки на стол зуборезного станка и увеличивается производительность нарезания зубьев, так как при этом можно одновременно крепить на станке несколько заготовок,
34
но при твердых зубьях ( ~ 60 HRC ) расчетная ширина зубчатого венца получается меньше длины ступицы (см. рис. 3.1, б).
В дисках штампованных и кованых колес выполняют отверстия, которые являются технологическими и используются для транспортировки и для прижатия заготовки к столу зуборезного станка.
Зубчатые колеса диаметрами da от 400…600 мм выполняют литыми из стали или серого чугуна, диски выполняют со спицами, количество которых обычно 6, на рис. 3.1 в, г приведены примеры конструкций литых деталей.
Несмотря на большое конструктивное многообразие зубчатых колес, на основе теории и практики отработаны некоторые усреднённые рекомендации по их выполнению, основные из которых приведены в табл. 3.1.
Таблица 3.1
Размеры конструктивных элементов штампованных и кованых цилиндрических и конических зубчатых колес, червячных колес (см. рис. 3.1)
Размер конструктивного |
Обозначе- |
Расчетное значение |
|
||
|
|
|
|||
Цилиндрические |
Конические |
Червячные |
|||
элемента |
ние |
||||
колеса |
колеса |
колеса |
|||
|
|
||||
|
|
|
|
|
|
Длина ступицы |
lc |
(0,8…1,5) d* 1) |
≈ 1,2d |
≈1,2 d |
|
Диаметр ступицы |
dc |
(1,5…1,6) d |
(1,5…1,6)d |
1,6 d |
|
Толщина обода |
δ0 |
2,5m + 2 мм |
2,5me+2 мм |
≥ 2 m |
|
(зубчатого венца) |
|
(0,25…0,3) b** 2) |
(0,2…0,4) b |
|
|
Толщина диска |
δ1 |
0,3b≥10 мм |
|||
Угол штамповоч- |
γ |
(0,35…0,4) b*** 3) |
|
|
|
7° |
7° |
|
|||
ного уклона |
R |
не менее 5 мм**** 4) |
|
|
|
Радиус закругления |
неменее5 мм**** |
≥20 мм |
|||
Диаметр отверстия |
d0 |
15…25 мм 5) |
15…25 мм |
15…25 мм 3) |
Примечание:
1)Длина ступицы с увеличением твердости зубьев уменьшается, в азотированных и нитроцементованных колесах lc ≤ d.
2)В улучшенных колесах (НВ ≤ 350).
3)В азотированных и нитроцементованных колесах (57…63 HRC).
4)Относится только к штампованным колесам.
5)В литых колесах диаметр отверстий может быть больше для облегчения деталей.
Шевронные зубчатые колеса отличаются увеличенной шириной. Так как обычно зубья в них нарезают червячными фрезами, то для выхода инструмента посередине венца делается канавка (рис. 3.2), размеры которой определяются по табл. 3.2.
35
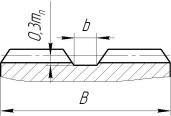
Таблица 3.2
Канавки для выхода червячных фрез при нарезании шевронных колес [4]
Модуль m, |
Ширина канавки b, мм, при угле наклона |
|
|||
зубьев по делительному диаметру |
|
||||
мм |
|
|
|
|
|
св. 15 до 25° |
св.25 до 35° |
св.35 до 45° |
|
||
|
|
||||
|
|
|
|
|
|
1 |
20 |
22 |
24 |
|
|
1,5 |
24 |
26 |
28 |
|
|
2 |
28 |
30 |
34 |
|
|
2,5 |
34 |
36 |
40 |
|
|
3 |
38 |
40 |
45 |
|
|
3,5 |
45 |
50 |
55 |
|
|
4 |
50 |
55 |
60 |
|
|
4,5 |
55 |
60 |
65 |
|
|
5 |
60 |
65 |
70 |
Рис. 3.2. Канавки для выхода |
|
6 |
70 |
75 |
80 |
||
червячных фрез при нарезании |
|||||
7 |
75 |
80 |
85 |
||
шевронных колес (см. табл. 3.2) |
|||||
8 |
85 |
90 |
95 |
||
9 |
95 |
105 |
110 |
|
|
10 |
100 |
110 |
115 |
|
При определении конструктивных элементов в конических колесах в основном приемлемы те же рекомендации (см. табл. 3.1), что и для цилиндрических. Конические колеса с внешним диаметром вершин зубьев dae≤120 мм имеют вид, показанный на рис. 3.1, д и изготовляют их из прутка, при dae>120 мм – свободной ковкой или штамповкой с последующей токарной обработкой (см. рис. 3.1, е, ж), в зависимости от серийности производства.
При серийном отлаженном производстве вершины зубьев притупляют фаской f≈0,5m (см. рис. 3.1, ж) со стороны внешнего торца зубчатого венца параллельно оси посадочного отверстия, на наличие фаски затрудняет контроль высоты зуба зубомером.
Червячные колеса (см. рис. 3.1, з) обычно выполняют составными – венец из бронзы, а центр из чугуна или стали, и только в малогабаритных редукторах
смежосевым расстоянием a ≤ 40 мм применяют бронзовые и латунные цельные сплошные конструкции. Существуют различные способы соединения венца
сцентром [3]. В индивидуальном и мелкосерийном производствах венец запрессовывают на центр колеса по посадкам с натягом, для предохранения от осевого смещения венец дополнительно скрепляют с центром винтами (3…8 шт.), количество которых определяется расчетом на срез, приблизительно можно прини-
мать dк = m + 2 мм, длину винта ≈2,5dк, где m – модуль зацепления. Конструктивные элементы ориентировочно можно определять по табл. 3.1.
36
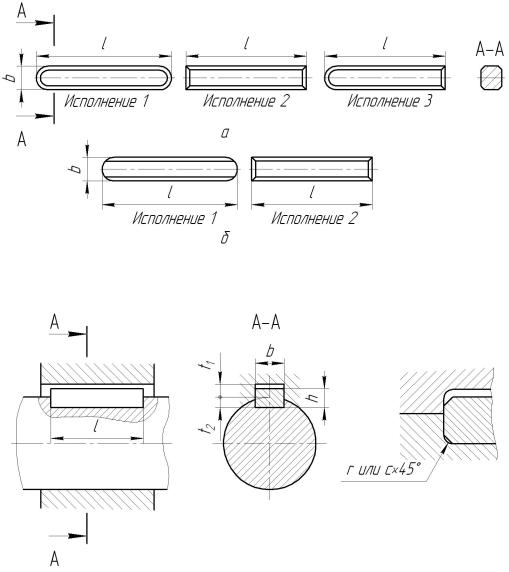
4.ШПОНОЧНЫЕ СОЕДИНЕНИЯ
Вредукторах обычно применяют шпонки призматические по ГОСТ 23360-78,
ав тяжелонагруженных редукторах и в редукторах с узкими колесами, имею-
щими высокую твердость зубьев (≈ 60 HRC) и короткие ступицы, как, например, в редукторах Ижевского АО «Редуктор», применяются призматические высокие шпонки по ГОСТ 10748-79.
Шпонки бывают различных исполнений (рис. 4.1), чаще применяют шпонки исполнений 2 как более простые в изготовлении.
Рис. 4.1. Исполнения: а – призматических шпонок по ГОСТ 23360-78; б – призматических высоких по ГОСТ 19748-79
Рис. 4.2. Вид шпоночного соединения и его основные размеры
37
Таблица 4.1
Размеры шпонок призматических исечений для них, мм
(из ГОСТ 23360-78) (рис. 4.2)
Диаметр |
Сечение |
Глубина паза |
Пред. откл. ширины b |
Пред. отклон. |
Радиус r1 или |
|||||||
|
|
Нормальное |
Плотное |
глубины па- |
||||||||
вала d |
шпонки |
вал |
втулка |
фаска s1 |
||||||||
|
|
|
|
|
|
соединение |
соедин. |
зов |
|
|
||
|
|
|
|
|
|
|
|
|
|
|
|
|
св. |
до |
b |
h |
t1 |
t2 |
Вал |
Втулка |
Вал и втул- |
t1 и |
от |
до |
|
(N9) |
(Is9) |
ка (Р9) |
t2 |
|||||||||
|
|
|
|
|
|
|
|
|||||
8 |
10 |
3 |
3 |
1,8 |
1,4 |
–0,004 |
± 0,012 |
–0,006 |
|
|
|
|
–0,029 |
|
–0,031 |
|
0,08 |
0,16 |
|||||||
|
|
|
|
|
|
|
|
|||||
10 |
12 |
4 |
4 |
2,5 |
1,8 |
0 |
± 0,015 |
–0,012 |
+ 0,1 |
|
|
|
12 |
17 |
5 |
5 |
3 |
2,3 |
0 |
|
|
||||
–0,030 |
|
–0,042 |
0,16 |
|
||||||||
17 |
22 |
6 |
6 |
3,5 |
2,8 |
|
|
0,25 |
||||
|
|
|
|
|||||||||
|
|
|
|
|
|
|
|
|
|
|
||
22 |
30 |
8 |
7 |
4 |
3,3 |
0 |
± 0,018 |
–0,015 |
|
|
|
|
30 |
38 |
10 |
8 |
5 |
3,3 |
–0,036 |
|
–0,051 |
|
0,25 |
|
|
38 |
44 |
12 |
8 |
5 |
3,3 |
|
|
|
|
|
||
44 |
50 |
14 |
9 |
5,5 |
3,8 |
0 |
± 0,021 |
–0,018 |
+ 0,2 |
|
0,4 |
|
50 |
58 |
16 |
10 |
6 |
4,3 |
–0,043 |
|
–0,061 |
|
|
||
58 |
65 |
18 |
11 |
7 |
4,4 |
|
|
|
0 |
|
|
|
65 |
75 |
20 |
12 |
7,5 |
4,9 |
|
|
|
|
|
|
|
75 |
85 |
22 |
14 |
9 |
5,4 |
0 |
± 0,026 |
–0,022 |
|
|
|
|
85 |
95 |
25 |
14 |
9 |
5,4 |
–0,052 |
|
–0,074 |
|
0,4 |
0,6 |
|
95 |
110 |
28 |
16 |
10 |
6,4 |
|
|
|
|
|
|
|
110 |
130 |
32 |
18 |
11 |
7,4 |
0 |
± 0,031 |
–0,026 |
|
|
|
|
|
|
|
|
|
|
–0,062 |
|
–0,088 |
|
|
|
Примечания:
1.Допускаются для ширины паза и втулки любые сочетания полей допусков, указанных в табл. 4.1, под втулкой понимается охватывающая деталь.
2.В ответственных шпоночных соединениях сопряжения дно паза с боковыми сторонами выполняется по радиусу, величина и предельные отклонения которого должны указываться на рабочем чертеже.
3.Допускается в обоснованных случаях (пустотелые и ступенчатые валы, при передаче пониженных крутящих моментов) применять меньшие размеры сечений стандартных шпонок на валах больших диаметров, за исключением выходных концов валов.
4.Материал – сталь чистотянутая для шпонок с временным сопротивлением разрыву не менее 600 Н/мм2 (МПа).
5.Ряд длин l : 6, 8, 10, 12, 14, 16, 18, 20, 22, 25, 28, 32, 36, 40, 45, 50, 56, 63, 70, 80, 90, 100, 110, 125, 140, 160, 180, 200, …, 450.
6.Пример условного обозначения шпонки исполнения 2 с размерами b= 18 мм, h = 11 мм, l = 100 мм: «Шпонка 18х11х100». То же исполнения В: «Шпонка В – 18х11х100 ГОСТ 23360-78». То же исполнения 1: «Шпонка 18х11х100 ГОСТ 23360-78».
7.На рабочих чертежах предпочтительно указывать размеры: для вала t1, для втулки d + t2.
38
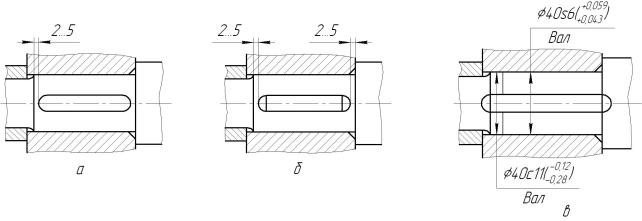
Таблица 4.2
Размеры шпонок призматических высоких и сечений пазов для них, мм
(из ГОСТ 10748-79) (рис. 4.2)
Диаметр вала d |
Сечение шпонки |
Глубина паза |
Радиус r |
|||||
|
|
|||||||
вал |
втулка |
|||||||
|
|
|
|
|
|
|||
|
|
|
|
|
|
|
|
|
свыше |
до |
b |
h |
t1 |
t2 |
от |
до |
|
30 |
38 |
10 |
9 |
5,5 |
3,8 |
|
|
|
38 |
44 |
12 |
11 |
7 |
4,4 |
|
|
|
44 |
50 |
14 |
12 |
7,5 |
4,9 |
0,25 |
0,4 |
|
50 |
58 |
16 |
14 |
9 |
5,4 |
|
|
|
58 |
65 |
18 |
16 |
10 |
6,4 |
|
|
|
65 |
75 |
20 |
18 |
11 |
7,4 |
|
|
|
75 |
85 |
22 |
20 |
12 |
8,4 |
|
|
|
85 |
95 |
25 |
22 |
13 |
9,4 |
0,4 |
0,6 |
|
95 |
110 |
28 |
25 |
15 |
10,4 |
|
|
|
110 |
130 |
32 |
28 |
17 |
11,4 |
|
|
Примечания:
1.Предельные отклонения для шпоночного паза на валу и втулке: +0,2 мм для d ≤ 75 мм, +0,3 для d > 75 мм.
2.См. примечания к табл. 4.1.
Обычно длина шпонки берется близкой к ширине ступицы зубчатого колеса, при этом длина паза не доводится на 2...5 мм до галтелей, чтобы меньше ослаблять вал и не увеличивать концентрацию напряжений у галтели (рис. 4.3, а, б). При необходимости увеличения длины шпонки концентрацию напряжений под прессовой посадкой уменьшают за счет выполнения части сопрягаемой поверхности по посадке с зазором (см. рис. 4.3), это облегчает также сборку, так как вал со шпонкой легко направляется по шпоночному пазу в отверстии ступицы. Прочность шпонки всегда проверяют расчетом по напряжениям смятия.
Рис. 4.3. Расположение и исполнение шпоночных пазов и валов: а – соединение шпонкой со скругленными торцами; б – то же с плоскими торцами; в – соединение с удлиненным шпоночным пазом и участком вала, соединяемым со ступицей по посадке с зазором
39
5.ОПОРНЫЕ УЗЛЫ РЕДУКТОРОВ
5.1.Типы подшипников, применяемые в редукторах,
иих условные обозначения
Внастоящее время в редукторах в качестве опор в основном применяются подшипники качения. В спецификации на сборочный чертеж редуктора указывается тип подшипника качения, его условное обозначение и номер ГОСТа.
Вредукторах применяются стандартные подшипники, каждый типоразмер которого имеет свой номер.
5.1.1.Условные обозначения подшипников
Полное условное обозначение подшипника по ГОСТ 3189-89 буквенноцифровое и включает в себя основное и дополнительное обозначения. Основное обозначение подшипников состоит из 2…7 цифр, характеризующих внутренний диаметр подшипника, серию, тип и конструктивные особенности подшипника. Две первые цифры основного обозначения, считая справа налево, условно обозначают диаметр подшипника (исключая подшипники с внутренним диаметром до 9 мм). Для подшипников с внутренним диаметром от 20 до 495 мм эти цифры являются частными от деления внутреннего диаметра отверстия на пять. Внутренний диаметр подшипников от 10 до 17 мм обозначается условными данными, приведенными в табл. 5.1.
|
Таблица 5.1 |
Условное обозначение внутренних диаметров от 10 до 17 мм |
|
|
|
Номинальный диаметр отверстия подшипника, мм |
Обозначение диаметра |
|
|
10 |
00 |
12 |
01 |
15 |
02 |
17 |
03 |
Третья и седьмая цифры, также считая справа налево, характеризуют габаритные размеры подшипника и обозначают серию подшипника. Основные габаритные размеры d×D×B, где d – внутренний диаметр, D – наружный диаметр, B – ширина подшипника. В редукторах применяются серии: 1 – особо легкая, 2 – легкая, 3 – средняя, 4 – тяжелая, 5 – легкая широкая, 6 – средняя широкая.
40